Characterization of the Stress and Refractive-Index Distributions in Optical Fibers and Fiber-Based Devices
Total Page:16
File Type:pdf, Size:1020Kb
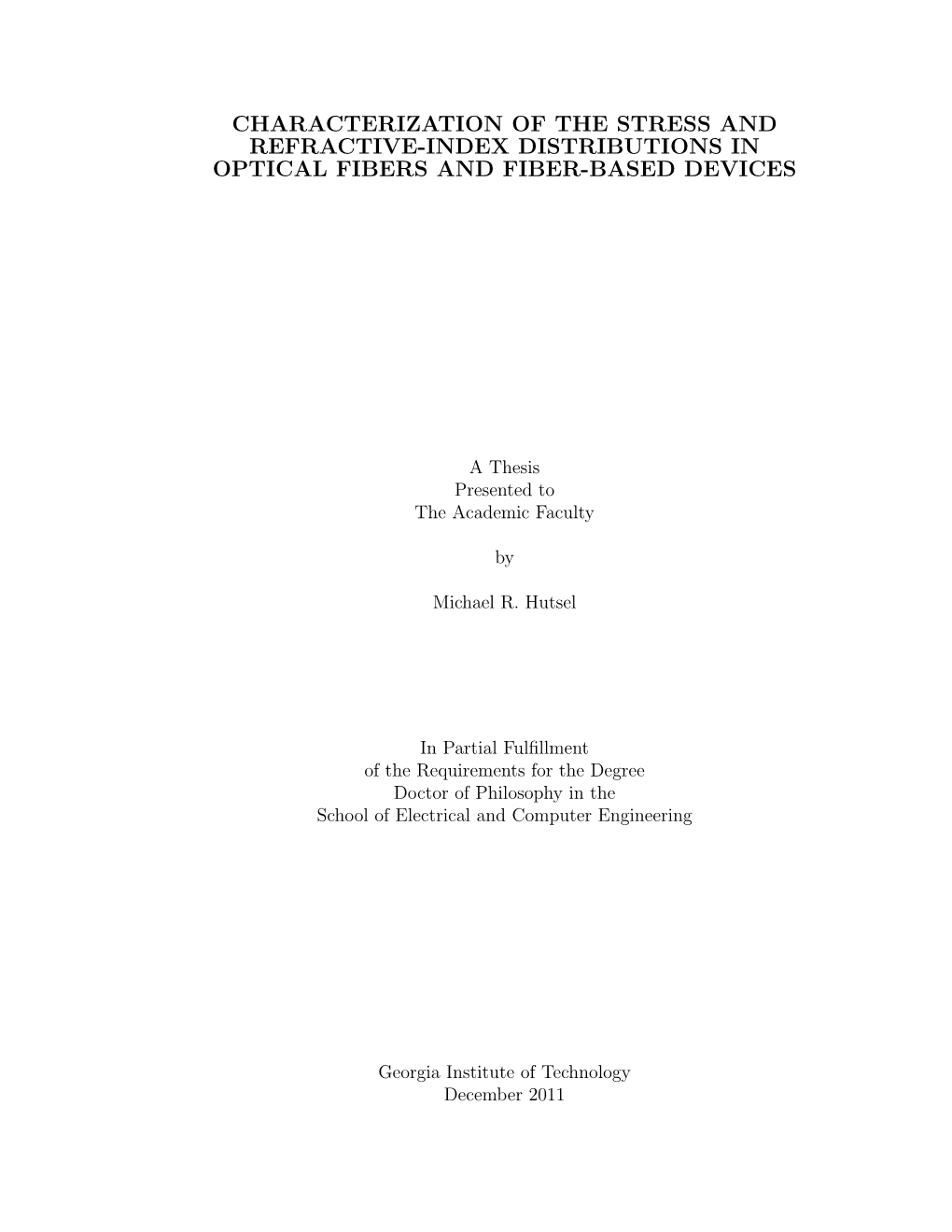
Load more
Recommended publications
-
Negative Refractive Index in Artificial Metamaterials
1 Negative Refractive Index in Artificial Metamaterials A. N. Grigorenko Department of Physics and Astronomy, University of Manchester, Manchester, M13 9PL, UK We discuss optical constants in artificial metamaterials showing negative magnetic permeability and electric permittivity and suggest a simple formula for the refractive index of a general optical medium. Using effective field theory, we calculate effective permeability and the refractive index of nanofabricated media composed of pairs of identical gold nano-pillars with magnetic response in the visible spectrum. PACS: 73.20.Mf, 41.20.Jb, 42.70.Qs 2 The refractive index of an optical medium, n, can be found from the relation n2 = εμ , where ε is medium’s electric permittivity and μ is magnetic permeability.1 There are two branches of the square root producing n of different signs, but only one of these branches is actually permitted by causality.2 It was conventionally assumed that this branch coincides with the principal square root n = εμ .1,3 However, in 1968 Veselago4 suggested that there are materials in which the causal refractive index may be given by another branch of the root n =− εμ . These materials, referred to as left- handed (LHM) or negative index materials, possess unique electromagnetic properties and promise novel optical devices, including a perfect lens.4-6 The interest in LHM moved from theory to practice and attracted a great deal of attention after the first experimental realization of LHM by Smith et al.7, which was based on artificial metallic structures -
Chapter 19/ Optical Properties
Chapter 19 /Optical Properties The four notched and transpar- ent rods shown in this photograph demonstrate the phenomenon of photoelasticity. When elastically deformed, the optical properties (e.g., index of refraction) of a photoelastic specimen become anisotropic. Using a special optical system and polarized light, the stress distribution within the speci- men may be deduced from inter- ference fringes that are produced. These fringes within the four photoelastic specimens shown in the photograph indicate how the stress concentration and distribu- tion change with notch geometry for an axial tensile stress. (Photo- graph courtesy of Measurements Group, Inc., Raleigh, North Carolina.) Why Study the Optical Properties of Materials? When materials are exposed to electromagnetic radia- materials, we note that the performance of optical tion, it is sometimes important to be able to predict fibers is increased by introducing a gradual variation and alter their responses. This is possible when we are of the index of refraction (i.e., a graded index) at the familiar with their optical properties, and understand outer surface of the fiber. This is accomplished by the mechanisms responsible for their optical behaviors. the addition of specific impurities in controlled For example, in Section 19.14 on optical fiber concentrations. 766 Learning Objectives After careful study of this chapter you should be able to do the following: 1. Compute the energy of a photon given its fre- 5. Describe the mechanism of photon absorption quency and the value of Planck’s constant. for (a) high-purity insulators and semiconduc- 2. Briefly describe electronic polarization that re- tors, and (b) insulators and semiconductors that sults from electromagnetic radiation-atomic in- contain electrically active defects. -
Super-Resolution Imaging by Dielectric Superlenses: Tio2 Metamaterial Superlens Versus Batio3 Superlens
hv photonics Article Super-Resolution Imaging by Dielectric Superlenses: TiO2 Metamaterial Superlens versus BaTiO3 Superlens Rakesh Dhama, Bing Yan, Cristiano Palego and Zengbo Wang * School of Computer Science and Electronic Engineering, Bangor University, Bangor LL57 1UT, UK; [email protected] (R.D.); [email protected] (B.Y.); [email protected] (C.P.) * Correspondence: [email protected] Abstract: All-dielectric superlens made from micro and nano particles has emerged as a simple yet effective solution to label-free, super-resolution imaging. High-index BaTiO3 Glass (BTG) mi- crospheres are among the most widely used dielectric superlenses today but could potentially be replaced by a new class of TiO2 metamaterial (meta-TiO2) superlens made of TiO2 nanoparticles. In this work, we designed and fabricated TiO2 metamaterial superlens in full-sphere shape for the first time, which resembles BTG microsphere in terms of the physical shape, size, and effective refractive index. Super-resolution imaging performances were compared using the same sample, lighting, and imaging settings. The results show that TiO2 meta-superlens performs consistently better over BTG superlens in terms of imaging contrast, clarity, field of view, and resolution, which was further supported by theoretical simulation. This opens new possibilities in developing more powerful, robust, and reliable super-resolution lens and imaging systems. Keywords: super-resolution imaging; dielectric superlens; label-free imaging; titanium dioxide Citation: Dhama, R.; Yan, B.; Palego, 1. Introduction C.; Wang, Z. Super-Resolution The optical microscope is the most common imaging tool known for its simple de- Imaging by Dielectric Superlenses: sign, low cost, and great flexibility. -
Realization of an All-Dielectric Zero-Index Optical Metamaterial
Realization of an all-dielectric zero-index optical metamaterial Parikshit Moitra1†, Yuanmu Yang1†, Zachary Anderson2, Ivan I. Kravchenko3, Dayrl P. Briggs3, Jason Valentine4* 1Interdisciplinary Materials Science Program, Vanderbilt University, Nashville, Tennessee 37212, USA 2School for Science and Math at Vanderbilt, Nashville, TN 37232, USA 3Center for Nanophase Materials Sciences, Oak Ridge National Laboratory, Oak Ridge, Tennessee 37831, USA 4Department of Mechanical Engineering, Vanderbilt University, Nashville, Tennessee 37212, USA †these authors contributed equally to this work *email: [email protected] Metamaterials offer unprecedented flexibility for manipulating the optical properties of matter, including the ability to access negative index1–4, ultra-high index5 and chiral optical properties6–8. Recently, metamaterials with near-zero refractive index have drawn much attention9–13. Light inside such materials experiences no spatial phase change and extremely large phase velocity, properties that can be applied for realizing directional emission14–16, tunneling waveguides17, large area single mode devices18, and electromagnetic cloaks19. However, at optical frequencies previously demonstrated zero- or negative- refractive index metamaterials require the use of metallic inclusions, leading to large ohmic loss, a serious impediment to device applications20,21. Here, we experimentally demonstrate an impedance matched zero-index metamaterial at optical frequencies based on purely dielectric constituents. Formed from stacked silicon rod unit cells, the metamaterial possesses a nearly isotropic low-index response leading to angular selectivity of transmission and directive emission from quantum dots placed within the material. Over the past several years, most work aimed at achieving zero-index has been focused on epsilon-near-zero metamaterials (ENZs) which can be realized using diluted metals or metal waveguides operating below cut-off. -
Refractive Index and Dispersion of Liquid Hydrogen
&1 Bureau of Standards .ifcrary, M.W. Bldg OCT 11 B65 ^ecknlcciL ^iote 9?©. 323 REFRACTIVE INDEX AND DISPERSION OF LIQUID HYDROGEN R. J. CORRUCCINI U. S. DEPARTMENT OF COMMERCE NATIONAL BUREAU OF STANDARDS THE NATIONAL BUREAU OF STANDARDS The National Bureau of Standards is a principal focal point in the Federal Government for assuring maximum application of the physical and engineering sciences to the advancement of technology in industry and commerce. Its responsibilities include development and maintenance of the national stand- ards of measurement, and the provisions of means for making measurements consistent with those standards; determination of physical constants and properties of materials; development of methods for testing materials, mechanisms, and structures, and making such tests as may be necessary, particu- larly for government agencies; cooperation in the establishment of standard practices for incorpora- tion in codes and specifications; advisory service to government agencies on scientific and technical problems; invention and development of devices to serve special needs of the Government; assistance to industry, business, and consumers in the development and acceptance of commercial standards and simplified trade practice recommendations; administration of programs in cooperation with United States business groups and standards organizations for the development of international standards of practice; and maintenance of a clearinghouse for the collection and dissemination of scientific, tech- nical, and engineering information. The scope of the Bureau's activities is suggested in the following listing of its four Institutes and their organizational units. Institute for Basic Standards. Applied Mathematics. Electricity. Metrology. Mechanics. Heat. Atomic Physics. Physical Chemistry. Laboratory Astrophysics.* Radiation Physics. Radio Standards Laboratory:* Radio Standards Physics; Radio Standards Engineering. -
4.4 Total Internal Reflection
n 1:33 sin θ = water sin θ = sin 35◦ ; air n water 1:00 air i.e. ◦ θair = 49:7 : Thus, the height above the horizon is ◦ ◦ θ = 90 θair = 40:3 : (4.7) − Because the sun is far away from the fisherman and the diver, the fisherman will see the sun at the same angle above the horizon. 4.4 Total Internal Reflection Suppose that a light ray moves from a medium of refractive index n1 to one in which n1 > n2, e.g. glass-to-air, where n1 = 1:50 and n2 = 1:0003. ◦ If the angle of incidence θ1 = 10 , then by Snell's law, • n 1:50 θ = sin−1 1 sin θ = sin−1 sin 10◦ 2 n 1 1:0003 2 = sin−1 (0:2604) = 15:1◦ : ◦ If the angle of incidence is θ1 = 50 , then by Snell's law, • n 1:50 θ = sin−1 1 sin θ = sin−1 sin 50◦ 2 n 1 1:0003 2 = sin−1 (1:1487) =??? : ◦ So when θ1 = 50 , we have a problem: Mathematically: the angle θ2 cannot be computed since sin θ2 > 1. • 142 Physically: the ray is unable to refract through the boundary. Instead, • 100% of the light reflects from the boundary back into the prism. This process is known as total internal reflection (TIR). Figure 8672 shows several rays leaving a point source in a medium with re- fractive index n1. Figure 86: The refraction and reflection of light rays with increasing angle of incidence. The medium on the other side of the boundary has n2 < n1. -
Electromagnetism - Lecture 13
Electromagnetism - Lecture 13 Waves in Insulators Refractive Index & Wave Impedance • Dispersion • Absorption • Models of Dispersion & Absorption • The Ionosphere • Example of Water • 1 Maxwell's Equations in Insulators Maxwell's equations are modified by r and µr - Either put r in front of 0 and µr in front of µ0 - Or remember D = r0E and B = µrµ0H Solutions are wave equations: @2E µ @2E 2E = µ µ = r r r r 0 r 0 @t2 c2 @t2 The effect of r and µr is to change the wave velocity: 1 c v = = pr0µrµ0 prµr 2 Refractive Index & Wave Impedance For non-magnetic materials with µr = 1: c c v = = n = pr pr n The refractive index n is usually slightly larger than 1 Electromagnetic waves travel slower in dielectrics The wave impedance is the ratio of the field amplitudes: Z = E=H in units of Ω = V=A In vacuo the impedance is a constant: Z0 = µ0c = 377Ω In an insulator the impedance is: µrµ0c µr Z = µrµ0v = = Z0 prµr r r For non-magnetic materials with µr = 1: Z = Z0=n 3 Notes: Diagrams: 4 Energy Propagation in Insulators The Poynting vector N = E H measures the energy flux × Energy flux is energy flow per unit time through surface normal to direction of propagation of wave: @U −2 @t = A N:dS Units of N are Wm In vacuo the amplitudeR of the Poynting vector is: 1 1 E2 N = E2 0 = 0 0 2 0 µ 2 Z r 0 0 In an insulator this becomes: 1 E2 N = N r = 0 0 µ 2 Z r r The energy flux is proportional to the square of the amplitude, and inversely proportional to the wave impedance 5 Dispersion Dispersion occurs because the dielectric constant r and refractive index -
Monte-Carlo Path Tracing Transparency/Translucency
Monte-Carlo Path Tracing Transparency/Translucency Max Ismailov, Ryan Lingg Light Does a Lot of Reflecting ● Our raytracer only supported direct lighting ● Objects that are not light sources emit light! ➔ We need more attention to realism than direct light sources can offer Global Illumination: Shrek Tools to Solve this Problem 1. Appropriate model of reflectance for objects 2. A way to aggregate incoming light sources Formally: We’re Solving the Rendering Equation! Reflectance Models - BRDF’s ● To properly globally illuminate, we need accurate models of light reflectance ○ “Bidirectional Reflectance Distribution Function” ● We already have a few of these! ○ Lambertian ○ Blinn-Phong ○ Many more exist Basic Ingredients of a BRDF Microfaceted Surfaces Subsurface Scattering Aggregating Light Sources ● Ideally, we want to integrate over the light functions contributing to a point. ○ Integrals require an integrand, a function that we can integrate! ■ ...we don’t have this ○ We need something we can do in practice numerically Approximating an Integral ● Recall: an integral is the area under the curve of a function along interval [a,b] ● Rough Area Under a Curve: evaluate the function at a point that looks good, multiply it by the difference in the interval ○ You get a very crude approximation of the integral! Approximating an Integral ● Like most things in calculus: do it a lot, and you get closer to the truth! ● Sample random variable, X ∈ [a,b], from a uniform distribution ● Keep evaluating f(X), average the results, you get a better approximation of the integral ○ This is a “Basic Monte-Carlo Estimator” Approximating an Integral: Non-Uniform Distributions ● In practice, we often sample our random variable from a non-uniform distribution. -
Method of Determining the Optical Properties of Ceramics and Ceramic Pigments: Measurement of the Refractive Index
CASTELLÓN (SPAIN) METHOD OF DETERMINING THE OPTICAL PROPERTIES OF CERAMICS AND CERAMIC PIGMENTS: MEASUREMENT OF THE REFRACTIVE INDEX A. Tolosa(1), N. Alcón(1), F. Sanmiguel(2), O. Ruiz(2). (1) AIDO, Instituto tecnológico de Óptica, Color e Imagen, Spain. (2) Torrecid, S.A., Spain. ABSTRACT The knowledge of the optical properties of materials, such as pigments or the ceramics that contain these, is a key feature in modelling the behaviour of light when it impinges upon them. This paper presents a method of obtaining the refractive index of ceramics from diffuse reflectance measurements made with a spectrophotometer equipped with an integrating sphere. The method has been demonstrated to be applicable to opaque ceramics, independently of whether the surface is polished or not, thus avoiding the need to use different methods to measure the refractive index accor- ding to the surface characteristics of the material. This method allows the Fresnel equations to be directly used to calculate the refractive index with the measured diffuse reflectance, without needing to measure just the specular reflectance. Al- ternatively, the method could also be used to measure the refractive index in transparent and translucent samples. The technique can be adapted to determine the complex refractive index of pigments. The reflectance measurement would be based on the method proposed in this paper, but for the calculation of the real part of the refractive index, related to the change in velocity that light undergoes when it reaches the material, and the imaginary part, related to light absorption by the material, the Kramers-Kronig relations would be used. -
Refractive Index Formulae for Radio Waves
Refractive Index Formulae for Radio Waves Jean M. RÜEGER, Australia Key words: Refractive Index of Air, Radio Waves, Electronic Distance Measurement, Global Positioning System, very long Baseline Interferometry, Microwaves ABSTRACT The radio refractive index formula adopted in 1963 by the International Union of Geodesy and Geophysics (IUGG) and the International Association of Geodesy (IAG) is being reviewed. Forty years ago, this formula was essential for the reduction of distances measured with microwave EDM instruments. Since then, long-range EDM has been replaced by the Global Positioning System (GPS). Today, the formulae are important for accurate measurements using radio waves, including GPS and VLBI (Very Long Baseline Interferometry). The new radio wave refractive index formulae of the last decades are discussed and the inherent problems of some of them are pointed out. State-of-the art formulae for routine and precise measurements in the radio wave spectrum are discussed as are computer programs that model the influences of resonance lines. Two formulae for hand calculations of the radio refractive index Nr (in ppm, for infinite wavelengths) have been designed, one based on 'best available' coefficients and one based on 'best average' coefficients. For air with 0.0375% (375 ppm) content of CO2, the latter is: pd pw pw N = 77.6890 + 71.2952 + 375463 r T T T2 where pd (= ptot - pw) is the partial dry air (including 375 ppm carbon dioxide) pressure (in hPa), pw is the partial water vapour pressure (in hPa), and T is the temperature (in K). The accuracy of the dry air refractivity component Nd (first term on right hand side) is, conservatively, 0.02% of Nd. -
Measurement of the Refractive Index and Dispersion of Optical Glass For
• U. S. DEPARTMENT OF COMMERCE NATIONAL BUREAU OF STANDARDS RESEARCH PAPER RP1572 Part of Journal of Research of the National Bureau of Standards, Volume 32, January 1944 MEASUREMENT OF THE REFRACTIVE INDEX AND DIS~ PERSION OF OPTICAL GLASS FOR CONTROL OF PRODUCT By Helen L. Gurewitz and Leroy \V. Tilton ABSTRACT Commercial critical-angle refractometers are inadequate for acceptance tests on optical glass for precision uses. To facilitate spectrometer determinations. coefficients 1 have been devised which, together with a table of natural sines and slide-rule operations, permit the computation of refractive indices of glass with an accuracy of ± 3 X 10-6 from minimum-deviation data taken on prisms having angles of 60° ± 30'. The refractive index and dispersion of optical glass that is used for lenses and for other refmctive purposes are the most important char acteristics of such glass, and considerable attention should be given by the manufacturer to their appropriate measurement. Adequate measurements of dispersion are more difficult than those of refractive index as such. The value 11= (n D -1)/(N,-Nc), used for expressing the dispersion of optical glass, is often specified by purchasers with tolerances of two or three tenths of a unit. The critical factor in its determination is the partial dispersion (N,-Nc ) , which ranges from 0.00800 for borosilicate crown with n D = 1.517 and 11=64, to 0.02100 for extra-dense flint with n n=1.671 and 11=32. It is evident that the difficulties exist chiefly for crown glass, where errors of ±0.000012 in measuring both no and n, can result in errors of ±0.2 in II value. -
Index of Refraction: Glass Plates
Index of Refraction - T 1 of 11 Index of Refraction: Treasure at the Bottom of the Sea Artwork by Shelly Lynn Johnson When light moves from one material to another, the speed of the light changes. Refraction is the bending of a light ray when it moves from one medium (like air) to another (like glass or water). The amount of bending depends on the difference in speed of the light in the two different media. Snell’s Law describes this relationship. The refractive index of a material is an important optical property and is used to calculate the focusing power of lenses and the dispersive power of prisms. Refractive index is an important physical property of a substance that can be used for identification, purity determination or measurement of concentration. This activity is designed for the Nspire handheld and intends to help students understand the refraction of light as it moves from one medium to another. Students will discover Snell’s Law using an interactive diagram. Index of Refraction - T 2 of 11 Introduction 1.1.Open the IRefracT.tns file. Read the first three pages of the document. 1.2 Reflection and refraction describe the behavior of waves. Students answer questions on handout. Use a think, pair, share strategy to invite students to respond. Q1. How are they similar? Both are properties of waves. Both describe a change in direction of waves. Q2. How are they different? Reflection describes the response of a wave when it cannot pass into a new medium. Refraction describes the response of a wave when it enters a new medium.