Panhard Rod Assembly for Mgb, Mgbv8 & Mgc Fitting
Total Page:16
File Type:pdf, Size:1020Kb
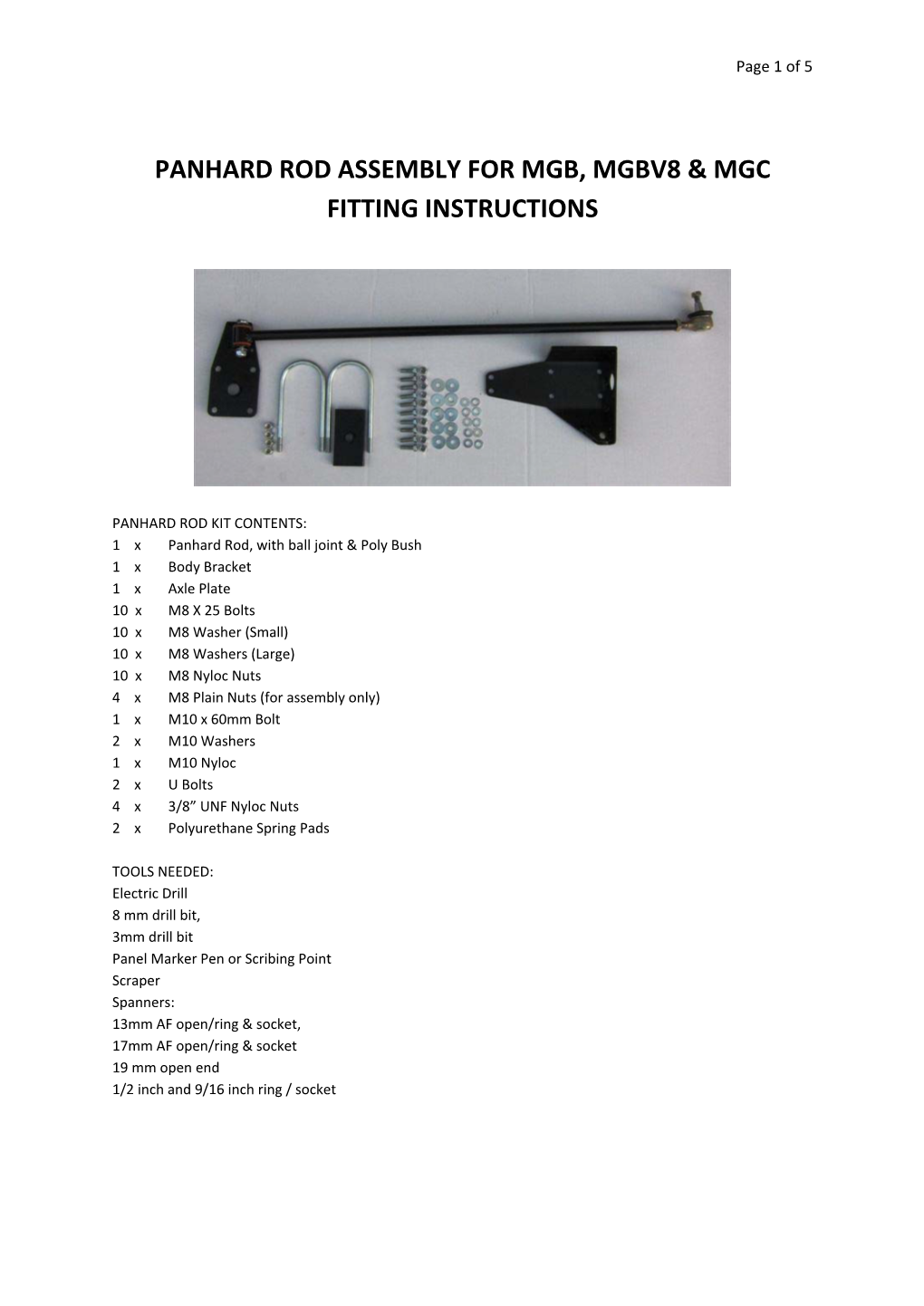
Load more
Recommended publications
-
Design and Analysis of Suspension System for an All Terrain Vehicle
International Journal of Scientific & Engineering Research, Volume 7, Issue 3, March-2016 164 ISSN 2229-5518 DESIGN AND ANALYSIS OF SUSPENSION SYSTEM FOR AN ALL TERRAIN VEHICLE Shijil P, Albin Vargheese, Aswin Devasia, Christin Joseph, Josin Jacob Abstract—In this paper our work was to study a. Study the static and dynamic parameters of the the static and dynamic parameter of the suspension system chassis. of an ATV by determining and analyzing the dynamics of b. Workout the parameters by analysis, design, and the vehicle when driving on an off road racetrack. Though, optimization of suspension system. there are many parameters which affect the performance of c. Study of existing suspension systems and the ATV, the scope of this paper work is limited to parameters affecting its performance. optimization, determination, design and analysis of d. Determination of design parameters for suspension systems and to integrate them into whole vehicle suspension system. systems for best results. The goals were to identify and optimize the parameters affecting the dynamic performance suspension systems Index terms—All terrain vehicle, suspension, caster angle, within limitations of time, equipment and data from camber angle, toe angle, roll centre manufacturer. In this paper we will also come across the following aspects IJSER negotiate a wider variety of terrain than most other vehicles. Although it is a street-legal vehicle in some countries, it is not legal within most states and provinces of Australia, the United States and 1.INTRODUCTION Canada and definitely not in India. By the current An All-Terrain Vehicle (ATV) is defined ANSI definition, it is intended for use by a single by the American National Standards Institute operator, although a change to include 2-seaters is (ANSI) as a vehicle that travels on low pressure under consideration. -
Download Article
addendum Setting a Hundred-Year Standard Remembering Panhard and Levassor, the company that invented the first manual transmission. Alex Cannella, Associate Editor 20th century French automobile to Bordeaux and back, before the hobby company Panhard and Levassor ultimately claimed his life in 1897 in a fatal were always unconventional. racing accident. Panhard, the other mind Sometimes, their deviations from the norm of the pair, would pass on, as well, a decade didn’t quite pan out. For example, one car, later. the Panhard and Levassor Dynamic, fea- The company’s innovations didn’t stop tured the driver seat in the middle of the car, after its two founders had passed, however. with passengers on either side, for a few years Most notably, they eventually developed the before the design was scrapped as awkward and “Panhard rod,” an early suspension rod that you impractical. can still find on some cars today. But while Panhard and Levassor’s innovations But here again, Panhard and Levassor the com- sometimes ended in a few evolutionary dead ends, pany continued to put out less well-known innova- some also resulted in a lot of the automotive industry’s first big tions for transmission systems. It was never anything huge or steps that are still standard practice today. flashy, but fundamental steps forward towards what we com- They were the first to start mounting the engine on the front monly recognize today as a modern transmission. Enclosed of the car. Before the turn of the 20th century, when automo- gearboxes in 1895. Quadrant changing four-speed transmis- biles were more still mostly motor buggies, the engine was often sions in 1903. -
TJM 4X4 Performance Suspension Parts Brochure
›› › SUSPEN SUSPENSUSPENSSSIONIONION Suspension Information 2 | Suspension We started it Founded on mateship in 1973, TJM is the Aussie pioneer of 4WD equipment. We’re tried and proven Australia’s rugged, yet diverse landscape has provided the ideal testing ground. Whether your journey takes you on or off road, for work or play, TJM has the gear you can depend on. We’re tough, yet sophisticated Using the latest engineering and manufacturing technology, our products are exposed to stringent testing and thorough quality assurance procedures to guarantee our customers receive nothing but the best. Everybody wants a piece of us Our research and development team brings leading-edge and performance-driven products. We’re the experts not just on our home turf but also offshore, so it’s not surprising TJM’s Aussie innovations are exported around the globe. Suspension | 3 IF YOU’RE GOING BUSH, BOUNDING OVER A BUMPY BUILDING SITE OR HAULING A CARAVAN ACROSS THE COUNTRY, TJM HAS A SUSPENSION SYSTEM TO SUIT YOUR 4WD. If wheels were your car’s feet, then suspension would be the legs. Just as the strength, length and flexibility of your legs impact on the way in which you move and the way you connect to the ground, different types of suspension determine the functionality, safety and comfort of your vehicle on different terrain. Made up of several parts that work together like joints and bones, suspension affects absolutely every aspect of driving. TJM XGS GOLD SUSPENSION Given the importance of suspension, it’s surprising how frequently people place priority on installing bull bars, roof racks and other 4WD accessories without even considering their suspension needs. -
Wl002 Installation Instructions
WL002 INSTALLATION INSTRUCTIONS 1993-2002 Camaro, Firebird TOOLS REQUIRED: Hydraulic jack and stands or service lift Die grinder with cutoff wheel or similar cutting tool (See Step 12 below) Tin snips Wrenches and sockets: 7mm, 13mm, 15mm, 18mm, 21mm, 9/16”, ¾”, 15/16” INSTALLATION: 1. Lift vehicle and safely support with jack stands under the frame rails. 2. Position the jack under the center of the axle once the car is secure. 3. Using an 18mm and 21mm wrench, remove the factory panhard rod. 4. Locate the heat shield directly over the muffler. There are two small screws that connect the heat shield to the upper panhard rod support. Using a 7mm wrench or socket, remove these screws as shown in IMAGE 1. 5. Remove the upper panhard rod support bolt on the passenger side using an 18mm and 21mm wrench. Due to rearend/spring interference, you may need to lift or lower the rear end in order to get the bolt all the way out. (IMAGE 2) 6. Using a 15mm socket, remove the (3) bolts on the drivers’ side that connect the upper panhard rod support to the frame rail. Remove the upper panhard rod support. 7. Using the 7mm socket, remove the remaining 3 screws that retain the heat shield to the floor. Remove the heat shield by sliding out the rear. 8. Install the BMR Watts Link cross-member with the supplied spacers installed where the panhard rod and upper panhard rod support was originally bolted. See IMAGE 3). Use the factory mounting hardware to install the cross-member. -
Morgan Roadster Lightweight
MSCC Techniques Speed Championship If you are thinking of sprinting your Morgan, you may be surprised to find that very little work is necessary to comply with the regulations to enable you to compete. The fitting of a roll over bar, timing strut and identifying the ignition key is all that is required! Race suit, helmet and gloves, apply for your licence and you’re off…! Below is a list of work that will improve safety and performance, but most is not compulsory. Why not give it a try. Contact Chris Bailey on 07889 722 333, 01924 201086 or via email [email protected] for further information about the Techniques Speed Championship. Roll Over Bars (Compulsory) Stainless Steel Braided Brake Hose A Roll Over Bar is compulsory for the Speed Championship. (Recommended but not compulsory) We can supply and fit Roll Over Bars or full racing ‘cages’ For a firmer brake pedal and better protection of the according to MSA and FIA regulations. brake hoses we recommend the fitting of stainless braided brake lines. Fire Extinguishers (Recommended but not compulsory) We fit our extinguisher systems either in the passenger Adjustable Shock Absorbers (Recommended but not compulsory) footwell or under the rear parcel shelf on the Challenge race Morgans. However for Sprinting a hand held The fitting of adjustable shock absorbers from the leading extinguisher is suitable. makers AVO, SPAX and Koni will enable you to fine tune the suspension for all weather conditions. Race Seats (Recommended but not compulsory) Brake Reaction Bars (Recommended but not compulsory) A correctly installed race seat tailored to the drivers needs is often the most noticed improvement by a Race driver and These bars are fitted between the top of the front frame can be measured by quicker lap times. -
M-2300-T 6-Piston Mustang Brake Kit INSTALLATION INSTRUCTIONS
M-2300-T 6-Piston Mustang Brake Kit INSTALLATION INSTRUCTIONS NO PART OF THIS DOCUMENT MAY BE REPRODUCED WITHOUT PRIOR AGREEMENT AND WRITTEN PERMISSION OF FORD RACING PERFORMANCE PARTS. Please visit www.fordracingparts.com for the most current instruction information ! ! ! PLEASE READ ALL OF THE FOLLOWING INSTRUCTIONS CAREFULLY PRIOR TO INSTALLATION. AT ANY TIME YOU DO NOT UNDERSTAND THE INSTRUCTIONS, PLEASE CALL THE FORD RACING TECHLINE AT 1-800-367-3788 ! ! ! Component Number Component Description Qty BRAKE KIT 6 Piston Brake Kit 1 DR3V-1125-CC Front Rotor Assembly 2 DR3V-2078-FA RH Brake Hose 1 DR3V-2B118-EB RH Front Caliper 6 Piston 1 DR3V-2B119-EB LH Front Caliper 6 Piston 1 DR3V-2B557-FA LH Brake Hose 1 DR3V-2C026-BA Rear Rotor 2 DR3V-2K004-CA RH Disk Brake Shield 1 DR3V-2K005-CA LH Disk Brake Shield 1 DR3V-2K327-AA LH Rear Caliper 1 DR3V-2K328-AA RH Rear Caliper 1 W500020-S439 Bolt, Backing Plate 4 W705821-S439 Caliper Bolt to Adaptor Brake Kit 1 W710233-S439 Caliper Mount Bolt M12X1.75X65 4 DR3Z-2C100-A RH Rear Support Bracket 1 DR3Z-2C101-A LH Rear Support Bracket 1 Material Item Specification High Performance DOT 3 WSS-M6C62-A or Motor Vehicle Brake Fluid WSS-M6C65-A1 PM-1-C (US); CPM-1-C (Canada) Factory Ford shop manuals are available from Helm Publications, 1-800-782-4356 Techline 1-800-367-3788 Page 1 of 29 IS-1850-0418 M-2300-T 6-Piston Mustang Brake Kit INSTALLATION INSTRUCTIONS NO PART OF THIS DOCUMENT MAY BE REPRODUCED WITHOUT PRIOR AGREEMENT AND WRITTEN PERMISSION OF FORD RACING PERFORMANCE PARTS. -
Suspension and Steering Inspection Proceedure.PDF
ELECTRICAL AND MECHANICAL VEHICLE G 188-1 ENGINEERING INSTRUCTIONS Issue 2, Aug 09 TRUCK, LIGHTWEIGHT, MC2, LAND ROVER 110 4X4 – ALL TYPES TRUCK, LIGHT, MC2, LAND ROVER 110 6X6 SUSPENSION AND STEERING INSPECTION PROCEDURE EQUIPMENT INSPECTION AND EXAMINATION DATA This instruction is authorised for use by command of the Chief of the General Staff. It provides direction, mandatory controls and procedures for the operation, maintenance and support of equipment. Personnel are to carry out any action required by this instruction in accordance with GENERAL A 001. Introduction 1. This instruction details the criteria for the inspection of the suspension and the steering on the Land Rover 110 4x4 and 6x6 to assess wear in suspension and steering components. Associated Publications 2. Reference may be necessary to the latest issue of the following documents: a. EMEI Vehicle A 291-1 – Tyres and Tubes – Care and Maintenance of B Vehicles; b. EMEI Vehicle A 291-5 – Tyres and Tubes – General Service B Vehicle Tyre Guide; c. EMEI Vehicle A 298-2 – Tyres and Tubes – Inspection for Useability; d. EMEI Vehicle G 103 – Truck, Utility, Lightweight And Truck, Utility, Lightweight, Winch, Mc2 - Land Rover 110 4x4 – Light Grade Repair; e. EMEI Vehicle G 104-1 – Truck, Utility, Lightweight And Truck, Utility, Lightweight, Winch, Mc2 - Land Rover 110 4x4 – Medium Grade Repair; f. EMEI Vehicle G 109 – Truck, Utility, Lightweight And Truck, Utility, Lightweight, Winch, Mc2 - Land Rover 110 4x4 – Servicing Schedule; g. EMEI Vehicle G 189-11 – Reclamation of Panhard Rod, Rear Lower Link and Radius Arm Mounts; h. EMEI Vehicle G 197-13 – Fitting of Coil Spring Retainers; i. -
Suspension by Design
Version 5.114A June 2021 SusProg3D - Suspension by Design Robert D Small All rights reserved. No parts of this work may be reproduced in any form or by any means - graphic, electronic, or mechanical, including photocopying, recording, taping, or information storage and retrieval systems - without the written permission of the publisher. Products that are referred to in this document may be either trademarks and/or registered trademarks of the respective owners. The publisher and the author make no claim to these trademarks. While every precaution has been taken in the preparation of this document, the publisher and the author assume no responsibility for errors or omissions, or for damages resulting from the use of information contained in this document or from the use of programs and source code that may accompany it. In no event shall the publisher and the author be liable for any loss of profit or any other commercial damage caused or alleged to have been caused directly or indirectly by this document. Printed: June 2021 Contents 3 Table of Contents Foreword 0 Part 1 Overview 12 1 SusProg3D................................................................................................................................... - Suspension by Design 12 2 PC hardware................................................................................................................................... and software requirements 14 3 To run the.................................................................................................................................. -
J&M Mustang Adjustable Panhard Rod (05-09)
J&M Mustang Adjustable Panhard Rod (05-09) - Installation Instructions The below installation instructions work for the following products: • J&M Mustang Adjustable Panhard Rod (05-09) Please read through the instructions carefully before starting this project. Take the time to get all the materials together as well as all the safety equipment. Overview: The suspension of the 05+ Mustang went through some changes when compared to the earlier versions of the Mustang. The move to a three link suspension, necessitates the use of a panhard bar to center the rear axle under the car. Previous suspension arrangements kept the rear axle in a fixed spot, but the use of the panhard bar means that the rear axle’s position will shift slightly as the car is lowered. In fact, many owners may find their rear axle isn’t perfectly centered, even under stock conditions. In my case, the rear end not being perfectly centered was apparent once I installed 18x10 wheels and tires to fit them on the rear of my 2006 convertible. The Goodyear Supercar F1’s I had mounted on my wheels had a width of 285mm, and were considerably wider than the stock tires. While my test mounting of the wheels alone had the wheel safely tucked inside the quarter panel, with the tires mounted the center bulge of the sidewall was sitting nearly a half inch outside of the rear quarter panel on the driver’s side tire. It was readily apparent that, after comparing the rear wheels, the axle was off center. The cure was the J&M Adjustable Panhard Rod, which I promptly ordered. -
Mgb 5-Link Rear Suspension Conversion
MGB 5-LINK REAR SUSPENSION CONVERSION The Frontline 5-link rear suspension has been developed in conjunction with Harvey Bailey Engineering and is designed to completely replace the original rear suspension. We have used state-of-the-art processes and technology to produce a bolt-on conversion that transforms the ride quality, handling and traction of your car. The conversion consists of parallel trailing arms, axle and body locating brackets, coil over gas dampers and a panhard rod Before starting we recommend that you familiarise yourself with the components by laying them out in their correct positions. Spring hanger bracket Sub frame Twin trailing arms Coil over dampers Panhard rod body Top axle bracket mounting bracket Lower axle bracket Panhard rod Fitting instructions (See pictures A to O on separate sheet) 1. Jack the rear of the vehicle and support on axle stands. With the axle hanging, remove the rear wheels. Then position the jack under the diff so it just supports the weight of the rear axle. Ensure the axle stands are stable and wheel chocks are in place at the front. 2. Remove the lever arm top mounts. 3. Undo the U bolts securing the leaf springs and lever arm plates to the axle and remove along with the bump stop plates on top of the axle. 4. Undo the front spring hanger bolts to remove the spring eyes. 5. Remove the rear shackle bolts to complete the removal of the leaf springs from the car. 6. On rubber bumper models a stiffening web is found inside the front spring hangers and needs to be removed to give clearance for the lower trailing arm brackets. -
1967 Mustang Rear Suspension Redesign
1967 Mustang Rear Suspension Redesign A Baccalaureate thesis submitted to the Department of Mechanical and Materials Engineering College of Engineering and Applied Science University of Cincinnati in partial fulfillment of the requirements for the degree of Bachelor of Science in Mechanical Engineering Technology By Nicholas Crall April, 2016 Thesis Advisor: Professor Ahmed Elgafy, Ph.D. ii TABLE OF CONTENTS 1967 MUSTANG REAR SUSPENSION REDESIGN ............................................................ II TABLE OF CONTENTS ........................................................................................................ III LIST OF FIGURES ................................................................................................................ IV LIST OF TABLES .................................................................................................................. IV ABSTRACT ............................................................................................................................. V INTRODUCTION - PROBLEM STATEMENT AND INTERVIEW .................................... 6 PROBLEM STATEMENT........................................................................................................................................ 6 INTERVIEW ......................................................................................................................................................... 6 ORIGINAL DESIGN............................................................................................................... -
Suspension Systems Suspension Systems
Suspension systems Suspension systems To understand vehicle performance and cornering, it is essential to have an in-depth understanding of the basic geometric properties of roads and suspensions, Including characteristics such as bump steer, roll steer, the various kinds of roll centre, and the relationships between them. 2 Suspension system 3 Suspension system 1. To provide good ride and handling performance – 2. To ensure that steering control is maintained during maneuvering 3. To ensure that the vehicle responds favorably to control forces produced by the tires as a result of longitudinal braking and accelerating forces, lateral cornering forces and braking and accelerating torques 4. To provide isolation from high frequency vibration arising from tire excitation The wheels, through the suspension linkage, must propel, steer, and stop the vehicle, and support the associated forces. 4 Suspension systems Langensperger’s independent steering of 1816 5 Suspension systems Ackermann steering effect achieved with parallel steering arms, by using angled drive points at the inner end of the track rods: ‘La Mancelle’, 1878. Ackermann steering effect achieved by two cams on L’Obeissante, designed by 6 Amedee Bollee in 1873. Suspension systems 7 Suspension systems leaf spring • To increase the compliance, a pair of leaf springs were mounted back-to-back • They were curved, and so then known, imprecisely, as elliptical springs, or elliptics for short • Single ones were called semi-elliptics 8 Suspension systems leaf spring 9 Suspension systems