Breakdown of Native Oxide Enables Multifunctional, Free-Form Carbon Nanotube−Metal Hierarchical Architectures † ‡ † Kehang Cui*, , and Brian L
Total Page:16
File Type:pdf, Size:1020Kb
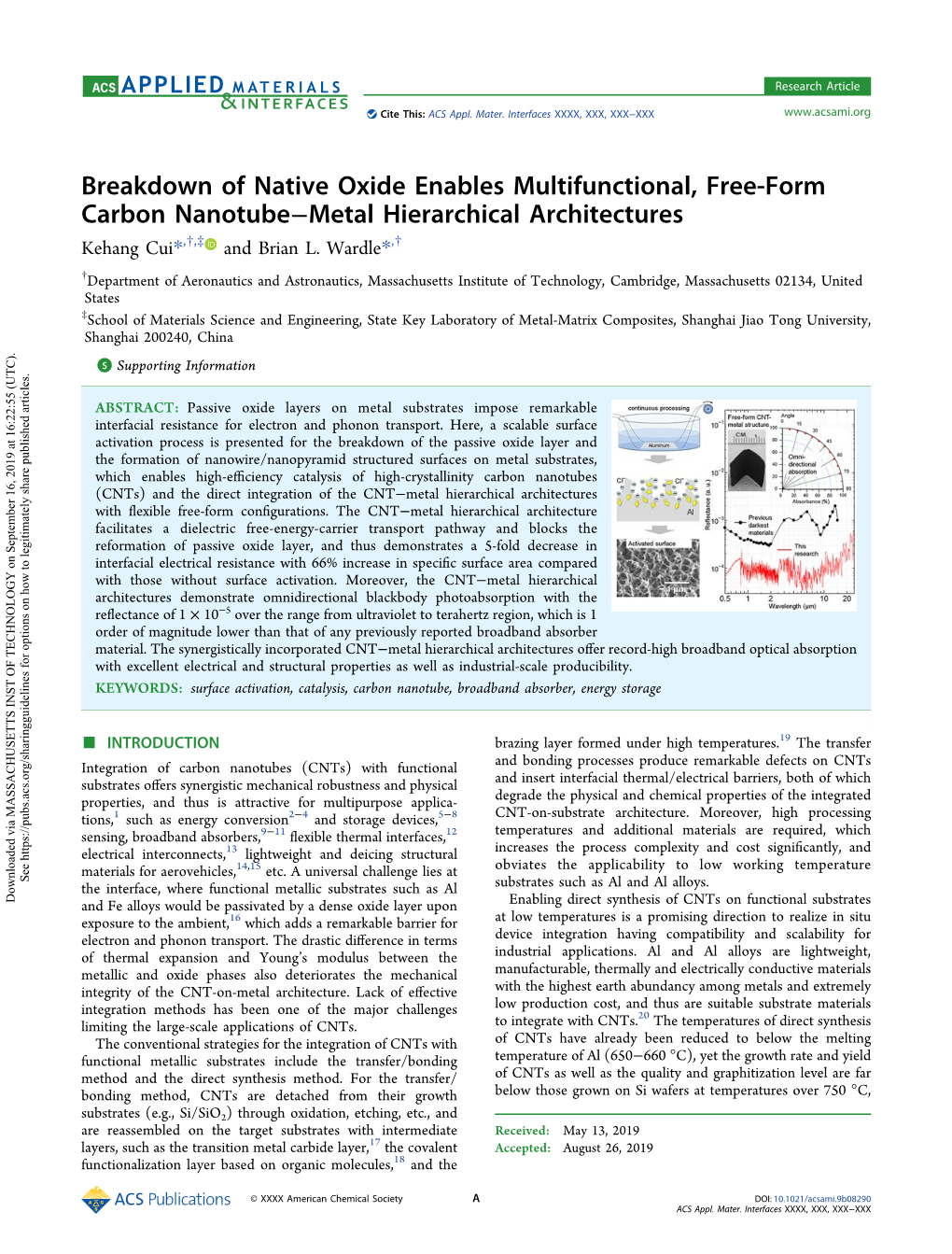
Load more
Recommended publications
-
In This Issue NIOSH Not Issuing New Recommended Exposure Limit For
Volume 11, No. 2 • Summer 2016 Environmental Protection Agency (US EPA) and the Food and In This Issue Drug Administration (FDA) to require companies to submit data on worker exposures to nanosilver before products con- • Recent Government Briefs taining nanosilver are allowed into the marketplace. These • Reports, Reviews, White Papers, and Books groups also supported implementing controls to mitigate ex- • Hot-off-the-Presses: Peer-reviewed Research posures (e.g., eliminating exposure to nanosilver or using less- Articles of Note hazardous substances) and recommended that companies be • Upcoming Meetings and Conferences required to submit safety data on potential risks to workers • New Product Review (e.g., liver and lung effects). Specifically, these groups noted the need to address women's exposures to nanosilver (e.g., for reproductive endpoints), because most occupational studies Recent Government Briefs of this substance have focused on men. Link to the Risk Policy Report, by Reynolds: http://insideepa.com/risk-policy-report/niosh-for- goes-novel-limit-nanosilver-citing-insufficient-risk-da- NIOSH Not Issuing New Recommended ta Exposure Limit for Nanosilver The docket, including comments and supporting documenta- tion, can be accessed here: Based on the comments it received on the draft document https://www.regulations.gov/#!docketDetail;D=C "Health Effects of Occupational Exposure to Silver Nanomate- DC-2016-0001 rials," the National Institute for Occupational Safety and Health (NIOSH) has decided it will not issue a specific -
EPIC Members Directory In
clionixumotL88 EPIC Consortium Members Directory: 737 members Questions/Comments, please contact [email protected] This directory is updated every month. Latest revision: 15 September 2021 Table of contents 1. II-VI Incorporated ................................................................................................................ 20 2. III-V Lab ................................................................................................................................ 21 3. 3D AG................................................................................................................................... 21 4. 3photon ............................................................................................................................... 21 5. 3SP Technologies ................................................................................................................. 21 6. 4isp ...................................................................................................................................... 22 7. 4JET Group ........................................................................................................................... 22 8. 603OPTX .............................................................................................................................. 22 9. 8photonics ........................................................................................................................... 23 10. Aarhus University ............................................................................................................... -
Photoacoustic Characteristics of Carbon-Based Infrared Absorbers
Photoacoustic characteristics of carbon-based infrared absorbers Jussi Rossi1, Juho Uotila2, Sucheta Sharma3, Toni Laurila3, Roland Teissier4, Alexei Baranov4, Erkki Ikonen3,5 and Markku Vainio1,6 1 Photonics Laboratory, Physics Unit, Tampere University, Tampere, Finland 2 Patria Aviation Oy, Tampere, Finland 3 Metrology Research Institute, Aalto University, Espoo, Finland 4 IES, University of Montpellier, CNRS, 34095 Montpellier, France 5 VTT MIKES, Espoo, Finland 6 Department of Chemistry, University of Helsinki, Helsinki, Finland Contact: [email protected] or [email protected] Abstract We present an experimental comparison of photoacoustic responsivities of common highly absorbing carbon-based materials. The comparison was carried out with parameters relevant for photoacoustic power detectors and Fourier-transform infrared (FTIR) spectroscopy: we covered a broad wavelength range from the visible red to far infrared (633 nm to 25 µm) and the regime of low acoustic frequencies (< 1 kHz). The investigated materials include a candle soot-based coating, a black paint coating and two different carbon nanotube coatings. Of these, the low-cost soot absorber produced clearly the highest photoacoustic response over the entire measurement range. Keywords: Candle soot, carbon nanotubes, photoacoustic response Introduction In addition to its many applications in spectroscopy [1-4] and imaging [5,6], the photoacoustic (PA) effect is useful for electromagnetic power detection due to its wavelength independency and high detection sensitivity. In a typical photoacoustic optical power detector, the incident radiation is first modulated by a chopper and then directed through a window to a PA cell. The cell contains an optical absorber to generate an acoustic wave at the chopping frequency. -
Defense 2045: Assessing the Future Security Environment And
NOVEMBER 2015 1616 Rhode Island Avenue NW Washington, DC 20036 202-887-0200 | www.csis.org Defense 2045 Lanham • Boulder • New York • London 4501 Forbes Boulevard Assessing the Future Security Environment and Implications Lanham, MD 20706 301- 459- 3366 | www.rowman.com for Defense Policymakers Cover photo: Shutterstock.com A Report of the CSIS International Security Program AUTHOR ISBN 978-1-4422-5888-4 David T. Miller 1616 Rhode Island Avenue NW FOREWORD Washington,Ë|xHSLEOCy258884z DC 20036v*:+:!:+:! Joseph S. Nye Jr. 202-887-0200 | www.csis.org Blank Defense 2045 Assessing the Future Security Environment and Implications for Defense Policymakers AUTHOR David T. Miller FOREWORD Joseph S. Nye Jr. A Report of the CSIS International Security Program November 2015 Lanham • Boulder • New York • London 594-62791_ch00_3P.indd 1 11/6/15 7:13 AM hn hk io il sy SY ek eh About CSIS hn hk io il sy SY ek eh For over 50 years, the Center for Strategic and International Studies (CSIS) has worked to hn hk io il sy SY ek eh develop solutions to the world’s greatest policy challenges. Today, CSIS scholars are hn hk io il sy SY ek eh providing strategic insights and bipartisan policy solutions to help decisionmakers chart hn hk io il sy SY ek eh a course toward a better world. hn hk io il sy SY ek eh CSIS is a nonprofit organ ization headquartered in Washington, D.C. The Center’s 220 full- time staff and large network of affiliated scholars conduct research and analy sis and hn hk io il sy SY ek eh develop policy initiatives that look into the future and anticipate change. -
Technological Change 2013-2016 Change Technological Publication of the Committee for the Future 2/2016
technological change 2013-2016 publication of the committee for the future 2/2016 technological change 2013-2016 Preliminary investigation of the development of radical technologies after the 2013 review 2/2016 isbn 978-951-53-3616-3 (paperback) • isbn 978-951-53-3617-0 (pdf) issn 2342-6594 (printed) • issn 2342-6608 (web) TECHNOLOGICAL CHANGE 2013–2016 Preliminary investigation: Development of radical technologies after the review in 2013 (100 Opportunities For Finland And The World, Publication Of The Committee For The Future 11/2014) Risto Linturi publication of the committee for the future 2/2016 Cover: freeimageslive.com Back cover: Part of the Artwork Tulevaisuus, Väinö Aaltonen (1932), photo Vesa Lindqvist. Committee for the Future FI-00102 Parliament of Finland www.parliament.fi Helsinki 2016 ISBN 978-951-53-3616-3 (paperback) ISBN 978-951-53-3617-0 (PDF) ISSN 2342-6594 (printed) ISSN 2342-6608 (web) Contents Foreword ......................................................................................................................... 5 1 Introduction, summary of observations and recommendations ................................ 8 1.1 A Hundred New Opportunities for Finland: Radical Technological Solutions ...... 8 1.2 Crowdsourcing after the publication of TuVRad9/2013 and acknowledgements ..................................................................................................... 9 1.3 Objectives of the preliminary investigation ...................................................... 11 1.4 The fastest-progressing baskets in the TuvRad9/2013 Top 25 category .......... 12 1.5 The fastest-progressing baskets in the TuVRad9/2016 Top 26–100 category . 13 1.6 New baskets and fields of technology that are proposed for monitoring ........ 14 1.7 Structural improvements to the report ............................................................ 15 1.8 Regional and international application of the four-level model ....................... 16 1.9 Interactive updating of the report with the help of database ......................... -
Surface Modification of Metal-Organic Framework Nanoparticles for Biomedical Applications
Dissertation zur Erlangung des Doktorgrades der Fakultät für Chemie und Pharmazie der Ludwig-Maximilians-Universität München Surface modification of metal-organic framework nanoparticles for biomedical applications Andreas Zimpel aus Rosenheim, Deutschland 2018 Preface Erklärung Diese Dissertation wurde im Sinne von § 7 der Promotionsordnung vom 28. November 2011 von Herrn Prof. Dr. Thomas Bein betreut. Eidesstattliche Versicherung Diese Dissertation wurde eigenständig und ohne unerlaubte Hilfe bearbeitet. München, den 03. August 2018 ____________________________ Andreas Zimpel Dissertation eingereicht am 28.06.2018 1. Gutachter: Prof. Dr. Thomas Bein 2. Gutachter: Dr. Stefan Wuttke Mündliche Prüfung am 24.07.2018 I Preface Danksagung Zu Beginn meiner Dissertation möchte ich einigen Leuten danken, ohne die das Erlangen meines Doktorgrades niemals zu Stande gekommen wäre. Als erstes möchte ich mich bei meinem Chef, Mentor und Freund Dr. Stefan Wuttke bedanken, ohne den ich ziemlich sicher nie zu diesem, sehr interessanten Forschungsgebiet der „Metall-organischen Gerüstverbindungen“ gekommen wäre. Danke, dass du mich auf meinem wissenschaftlichen Weg, von unserer ersten Begegnung und Zusammenarbeit als F- Praktikant von Christian Dietl in der organischen Chemie, über das PC-F-Praktikum und die Masterarbeit bis hin zu meiner Doktorarbeit, immer angetrieben und unterstützt hast. Besonders herzlicher Dank gilt meinem Doktorvater, Prof. Dr. Thomas Bein für die Möglichkeit meine Dissertation in seiner Arbeitsgruppe anfertigen zu dürfen, für all die finanzielle und wissenschaftliche Unterstützung über die Jahre meiner Promotion, sowie bereits während meiner Masterarbeit. Bei beiden möchte ich mich auch speziell für die Chancen bedanken, meine Forschungsarbeiten auf diversen nationalen und internationalen Konferenzen präsentieren zu dürfen. Diese haben mich nicht nur durch interessante Diskussionen mit anderen Doktoranden wissenschaftlich neu inspiriert, sondern auch menschlich gefestigt, indem ich gezwungen war dadurch meine Kontaktscheu Fremden gegenüber abzulegen. -
Catching up with Carbon Japan Fights to Stay on Top of a Field It Pioneered
NANOCARBON IN JAPAN SPOTLIGHT Catching up with carbon Japan fights to stay on top of a field it pioneered. BY TIM HORNYAK n September last year, a handful of Nagoya University. “It was the most exciting the stability and strength to build complex researchers were sitting around a com- moment I ever had in my life.” molecules — into new materials with useful puter monitor in chemist Kenchiro Itami’s Itami thinks he has good reason to be so properties, and it has built a strong industrial Ilab at Japan’s Nagoya University as one loaded excited. “The discovery of a new form of car- sector from those basic research efforts. a file showing the results of an X-ray crystal- bon has always opened up new science and But in the past decade or so, Japan has found lography scan. Within seconds, the room technology — fullerenes are a great example,” itself beset by international competition, as erupted: scientists were on their feet, cheering he says, referring to the all-carbon molecular progress in the field has shifted abroad. Now, and exchanging high fives. In front of them spheres created by scientists at Rice University Japanese researchers are fighting to maintain was a 3D representation of a carbon nanobelt in Houston, Texas, in 1985. their global prominence. — a new molecule of carbon that the team Chemists have indeed tried many things had successfully synthesized after 12 years of when it comes to constructing exotic forms, NO SMALL PEDIGREE ILLUSTRATION BY PETER HORVATH; PHOTOS: GETTY PHOTOS: HORVATH; PETER BY ILLUSTRATION painstaking effort. -
Bioinspired Microstructured Polymer Surfaces with Antireflective Properties
nanomaterials Article Bioinspired Microstructured Polymer Surfaces with Antireflective Properties Alexandre Emmanuel Wetzel 1 , Nuria del Castillo Iniesta 1, Einstom Engay 1, Nikolaj Kofoed Mandsberg 2,3, Celine Schou Dinesen 1, Bilal Rashid Hanif 1 , Kirstine Berg-Sørensen 3, Ada-Ioana Bunea 1,* and Rafael Taboryski 1 1 National Centre for Nano Fabrication and Characterization (DTU Nanolab), Technical University of Denmark, Ørsted Plads 347, 2800 Kongens Lyngby, Denmark; [email protected] (A.E.W.); [email protected] (N.d.C.I.); [email protected] (E.E.); [email protected] (C.S.D.); [email protected] (B.R.H.); [email protected] (R.T.) 2 Center for Intelligent Drug Delivery and Sensing Using Microcontainers and Nanomechanics (IDUN), Technical University of Denmark, Ørsted Plads 345C, 2800 Kongens Lyngby, Denmark; [email protected] 3 Department of Health Technology (DTU Health Tech), Technical University of Denmark, Ørsted Plads 345C, 2800 Kongens Lyngby, Denmark; [email protected] * Correspondence: [email protected]; Tel.: +45-29404623 Abstract: Over the years, different approaches to obtaining antireflective surfaces have been explored, such as using index-matching, interference, or micro- and nanostructures. Structural super black colors are ubiquitous in nature, and biomimicry thus constitutes an interesting way to develop antireflective surfaces. Moth-eye nanostructures, for example, are well known and have been successfully replicated using micro- and nanofabrication. However, other animal species, such as Citation: Wetzel, A.E.; del Castillo birds of paradise and peacock spiders, have evolved to display larger structures with antireflective Iniesta, N.; Engay, E.; Mandsberg, features. In peacock spiders, the antireflective properties of their super black patches arise from N.K.; Schou Dinesen, C.; Hanif, B.R.; relatively simple microstructures with lens-like shapes organized in tightly packed hexagonal arrays, Berg-Sørensen, K.; Bunea, A.-I.; which makes them a good candidate for cheap mass replication techniques. -
Plant Surfaces: Structures and Functions for Biomimetic Innovations
Nano-Micro Lett. (2017) 9:23 DOI 10.1007/s40820-016-0125-1 REVIEW Plant Surfaces: Structures and Functions for Biomimetic Innovations Wilhelm Barthlott1 . Matthias Mail1,2 . Bharat Bhushan3 . Kerstin Koch4 Received: 21 October 2016 / Accepted: 4 December 2016 Ó The Author(s) 2016. This article is published with open access at Springerlink.com Abstract An overview of plant surface structures and their evolution is presented. It combines surface chemistry and architecture with their functions and refers to possible biomimetic applications. Within some 3.5 billion years biological species evolved highly complex multifunctional surfaces for interacting with their environments: some 10 million living prototypes (i.e., estimated number of existing plants and animals) for engineers. The complexity of the hierarchical structures and their functionality in biological organisms surpasses all abiotic natural surfaces: even superhydrophobicity is restricted in nature to living organisms and was probably a key evolutionary step with the invasion of terrestrial habitats some 350–450 million years ago in plants and insects. Special attention should be paid to the fact that global environmental change implies a dramatic loss of species and with it the biological role models. Plants, the dominating group of organisms on our planet, are sessile organisms with large multifunctional surfaces and thus exhibit particular intriguing features. Superhydrophilicity and superhydrophobicity are focal points in this work. We estimate that superhydrophobic plant leaves (e.g., grasses) comprise in total an area of around 250 million km2, which is about 50% of the total surface of our planet. A survey of structures and functions based on own examinations of almost 20,000 species is provided, for further references we refer to Barthlott et al. -
Design, Applications, and Processing of Synthetic Protein Nanoparticles
Design, Applications, and Processing of Synthetic Protein Nanoparticles by Daniel F. Quevedo A dissertation submitted in partial fulfillment of the requirements for the degree of Doctor of Philosophy (Biomedical Engineering) in the University of Michigan 2020 Doctoral Committee: Professor Joerg Lahann, Chair Professor Lola Eniola-Adefeso Assistant Professor Colin F. Greineder Professor Blanca H. Lapizco-Encinas, Rochester Institute of Technology Professor Peter Tessier Daniel F. Quevedo [email protected] ORCID iD: 0000-0001-5892-364X © Daniel F. Quevedo 2020 Dedication To Ma, Pa, and Miguel for their love and support and To Shannon, who is my everything, and without whom this thesis would not exist ii Acknowledgements First and foremost, I would like to convey my deepest thanks and gratitude to my advisor, Professor Joerg Lahann, for guidance, kindness, patience, and support, and without whom nothing contained in this dissertation would be possible. His keen scientific insight, gentle guiding hand, and uncanny ability to calm and reassure any student as soon as they enter his office, no matter what the problem is, got me through the last 5 years. I am honored and proud to have joined his lab and worked with him, from my time at the Karlsruhe Institute of Technology, all the way to being locked up in my apartment for the last few months of my PhD. I would also like to thank my committee members, Professor Lola Eniola-Adefeso, Professor Peter Tessier, Professor Colin F. Greineder, and Professor Blanca H. Lapizco-Encinas, for their help and guidance over the years. Whether it was classes, constantly asking for a meeting to check up on my progress, working with me to design experiments, or even having insightful conversations while driving me to the airport, their contributions have shaped me, my thoughts, and the contents of this dissertation. -
Are We Ready for Spray-On Carbon Nanotubes?
SUBMITTED TEXT Nature Nanotechnology Thesis column, June 2016 Are we ready for spray-on carbon nanotubes? As artists and manufacturers explore the use of spray-on carbon nanotube coatings, Andrew Maynard explores the state of the science around nanotube safety. Andrew D. Maynard Director, Risk Innovation Lab. School for the Future of Innovation in Society, Arizona State University, Tempe AZ, USA. Email: [email protected] Earlier this year, British sculptor, Anish Kapoor was given exclusive rights to use a new spray-on carbon nanotube-based paint. The material – produced by UK-based Surrey NanoSystems and marketed as Vantablack S-VIS – can be applied to a range of surfaces, and absorbs well over 99% of the light that falls onto it.1 It is claimed to be the world’s blackest paint, and there is growing interest in its use in works of art and high- end consumer products. It’s easy to see the appeal of Vantablack S-VIS. Apart from technical applications where stray reflections need to be suppressed, this is a material that potentially enables manufacturers and artists to give their products a unique aesthetic edge. Yet, having worked on carbon nanotube safety for some years, I was intrigued to see the material in a spray-paint designed to coat objects that people may possibly come into contact with. It was, after all, only a few years ago that journalists were asking if carbon nanotubes were the next asbestos.2 And while this is unlikely, concerns over the possible health impacts of the material persist. Safety concerns of purposely manufactured carbon nanotubes began in the 1990’s. -
BLACK MAGIC Military Material to Optical Machines, As Well As Luxury Items Such As Can
Stare into the void that is Vantablack: ry to imagine something so black that it sucks up light. Surprisingly, Vantablack isn’t the creation of NASA, CERN or some other a nanoparticle coating that could soon be T Sounds like science fiction, doesn’t it? It’s not. It’s Vantablack, large international scientific research centre or company. It was, in fact, the world’s darkest man-made substance, which absorbs more developed by a small British company called Surrey NanoSystems, and is coming to a satellite or art gallery near you... than 99.6 per cent of radiation in the visible spectrum. Basically, it’s the produced on an industrial park in Newhaven, East Sussex. ‘We’re doing closest thing you’ll find on Earth to a black hole. some really exciting work here,’ explains Ben Jensen, the company’s The coating was originally developed for use on satellites, but since its founder and chief technical officer, showing us around the facility. ‘With launch in 2014 it has been applied to a wide range of products, from barely 20 full-time staff, we are achieving results nobody else in the world BLACK MAGIC military material to optical machines, as well as luxury items such as can. It’s been a whirlwind few years but we’re not resting on our laurels watches and cars. In April, a spray version was released, and will be used yet. We’re continually trying to push the limits of possibility.’ for projects by Turner Prize-winning artist Anish Kapoor, who is famous The company has a long list of projects still under embargo.