The Use of a High Limestone Content Mining Waste As a Sorbent for Co2 Capture
Total Page:16
File Type:pdf, Size:1020Kb
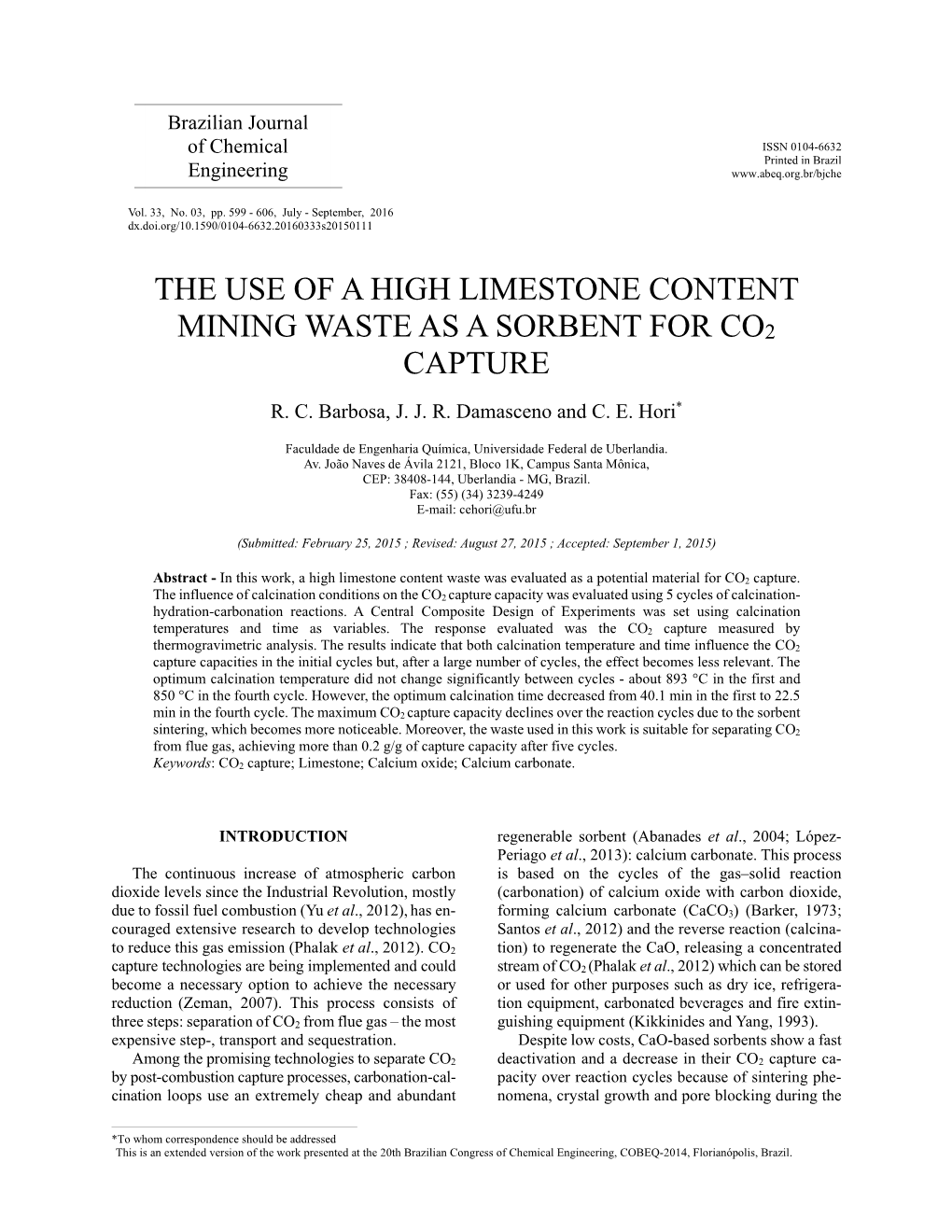
Load more
Recommended publications
-
The Combination of Calcium Oxide and Cu/Zro2 Catalyst and Their Selective Products for CO2 Hydrogenation
Article The Combination of Calcium Oxide and Cu/ZrO2 Catalyst and their Selective Products for CO2 Hydrogenation Soipatta Soisuwan1,a,b,*, Wilasinee Wisaijorn1, Chalida Nimnul1, Orawan Maunghimapan1, and Piyasan Praserthdam2 1 Department of Chemical Engineering, Faculty of Engineering, Burapha University, 169 Long-Hard Bangsaen Road, Saensuk Sub-District, Muang District, Chonburi, 20130, Thailand 2 Center of Excellence in Catalysis and Catalytic Reaction Engineering, Department of Chemical Engineering, Faculty of Engineering, Chulalongkorn University, Phayathai Road, Pathuwan District, Bangkok 10330, Thailand E-mail: [email protected] (Corresponding author), [email protected] Abstract. The catalytic activities of Cu/ZrO2_CaO catalysts were investigated on CO2 hydrogenation. The CO2 hydrogenations were carried out over combination of calcium oxide and Cu/ZrO2 catalyst. Two calcination temperatures were chosen at 300 and 650 oC according to thermal decomposition results. The catalysts were characterized by means of N2 adsorption-desorption, H2 temperature programmed reduction and X-ray diffraction. The CO2 hydrogenation under atmospheric pressure and at 250 oC was carried out over copper-based catalysts combined with calcium oxide namely i.e. Cu/ZrO 2 _CaO300, Cu/ZrO 2 _CaO650, Cu/ZrO2_Cu/CaO and Cu/ZrO2+CaO. The catalytic activities over all catalysts were consistent for 4 hours. The catalytic reaction rates over copper-based catalysts were in the range of 21.8 – 47.4 mol L-1 s-1 g cat-1. The modification of calcium oxide can improve the catalytic activity of copper-based catalysts to 47.4 mol L-1 s-1 g cat-1. The calcination temperature can cause a difference in active species that impact on product selectivity. -
Calcium Oxide
CALCIUM OXIDE Prepared at the 19th JECFA (1975), published in NMRS 55B (1976) and in FNP 52 (1992). Metals and arsenic specifications revised at the 59th JECFA (2002). An ADI ‘Not limited’ was established at the 9th JECFA (1965). SYNONYMS Lime; INS No. 529 DEFINITION Chemical names Calcium oxide C.A.S. number 1305-78-8 Chemical formula CaO Formula weight 56.08 Assay Not less than 95.0% after ignition DESCRIPTION Odourless, hard, white or greyish white masses or granules, or white to greyish white powder FUNCTIONAL USES Alkali, dough conditioner, yeast food CHARACTERISTICS IDENTIFICATION Solubility (Vol. 4) Slightly soluble in water, insoluble in ethanol, soluble in glycerol (Caution: Protect eyes when adding water) Reaction with water Moisten the sample with water; heat is generated (Caution: Protect eyes when adding water). Test for alkali The sample is alkaline to moistened litmus paper Test for calcium (Vol. 4) Passes test PURITY Loss on ignition (Vol. 4) Not more than 10% (1 g, about 800o to constant weight) Barium Not more than 0.03% Cautiously mix 1.5 g of the sample with 10 ml water, add 15 ml of dilute hydrochloric acid TS, dilute to 30 ml with water and filter. To 20 ml of the filtrate add 2 g of sodium acetate, 1 ml of dilute acetic acid TS and 0.5 ml of potassium chromate TS and allow to stand for 15 min. The turbidity of the solution is not greater than that of a control prepared by adding water to 0.3 ml of barium standard solution (1.779 g barium chloride in 1000 ml of water) to make to 20 ml, adding 2 g of sodium acetate, 1 ml of dilute acetic acid TS and 0.5 ml of potassium chromate TS and allowing to stand for 15 min. -
Interaction of Water with the Cao(001) Surface † ‡ † § ‡ † ∥ Yuichi Fujimori, Xunhua Zhao, Xiang Shao, , Sergey V
Article pubs.acs.org/JPCC Interaction of Water with the CaO(001) Surface † ‡ † § ‡ † ∥ Yuichi Fujimori, Xunhua Zhao, Xiang Shao, , Sergey V. Levchenko, Niklas Nilius, , † ⊥ † Martin Sterrer,*, , and Hans-Joachim Freund † ‡ Department of Chemical Physics and Theory Department, Fritz-Haber-Institut der Max-Planck-Gesellschaft, Faradayweg 4-6, 14195 Berlin, Germany ∥ Institute of Physics, Carl-von-Ossietzky University, 26111 Oldenburg, Germany ⊥ Institute of Physics, University of Graz, Universitatsplatz̈ 5, 8010 Graz, Austria *S Supporting Information ABSTRACT: The interaction of water with the CaO(001) surface has been studied from ultrahigh-vacuum to submillibar water vapor pressures and at temperatures of 100 and 300 K using well-structured CaO(001)/Mo(001) thin-film model systems. Infrared reflection absorption spectroscopy (IRAS), X-ray photoelectron spectroscopy (XPS), and scanning tunneling microscopy (STM) in combination with density functional theory (DFT) calculations have been employed to reveal the correlation between the vibrational frequencies of the hydroxyl groups and the distinct hydroxylated surface phases that develop as a function of water exposure. In the low-coverage regime, water monomers, small water clusters, and one-dimensional water chains are formed on the CaO(001) surface. At increasing water coverages, water-induced structural disorder is observed, indicating 2+ partial solvation of Ca ions. Partial transformation of CaO(001) into a Ca(OH)2-like phase occurs upon dosing of water at submillibar water pressure. In addition, it was found that interfacial hydroxyl groups formed on the CaO(001) surface during water exposure at temperatures as low as 100 K shift the temperatures for ice desorption and for the transition from amorphous solid water to crystalline ice by 10 K as compared to those for the nonhydroxylated MgO surface. -
Material Safety Data Sheet for Calcium Oxide ------Section I - Identity
Flammability 0 Health Reactivity 1 1 Specific Hazard Calcium Oxide Material Safety Data Sheet for Calcium Oxide --------------------------------------------------------------------------------------------------------------------------- Section I - Identity --------------------------------------------------------------------------------------------------------------------------- Manufacturer's name and address: Ash Grove Cement Company 8900 Indian Creek Parkway P. O. Box 25900 Overland Park, KS 66225 Emergency Telephone Number: (913) 451-8900 Information Telephone Number: (913) 451-8900 Chemical Name and Synonyms: Calcium oxide, CaO, quicklime, lime, unslaked lime Trade Name and Synonyms: Pebble Quicklime, Cal-Max CAS No.: 1305-78-8 Date Revised: July 2000 --------------------------------------------------------------------------------------------------------------------------- Section II - Hazardous Ingredients --------------------------------------------------------------------------------------------------------------------------- CAS Number OSHA PEL ACGIH TLV Quicklime, CaO 1305-78-8 5 mg/m3 2 mg/m3 PEL = 10mg/m3 3 Quartz, crystalline silica 14808-60-7 % SiO2*+2 0.05 mg/m * Calcium oxide may contain greater than 0.1% quartz, crystalline silica. Chronic exposure above the allowed limit to the respirable dust of materials containing crystalline silica or quartz may cause silicosis. *Respirable fraction ACGIH American Conference of Governmental Industrial Hygienists OSHA Occupational Safety and Health Administration PEL Permissible Exposure -
Mineral Carbonation and Industrial Uses of Carbon Dioxide 319 7
Chapter 7: Mineral carbonation and industrial uses of carbon dioxide 319 7 Mineral carbonation and industrial uses of carbon dioxide Coordinating Lead Author Marco Mazzotti (Italy and Switzerland) Lead Authors Juan Carlos Abanades (Spain), Rodney Allam (United Kingdom), Klaus S. Lackner (United States), Francis Meunier (France), Edward Rubin (United States), Juan Carlos Sanchez (Venezuela), Katsunori Yogo (Japan), Ron Zevenhoven (Netherlands and Finland) Review Editors Baldur Eliasson (Switzerland), R.T.M. Sutamihardja (Indonesia) 320 IPCC Special Report on Carbon dioxide Capture and Storage Contents EXECUTIVE SUMMARY 321 7.3 Industrial uses of carbon dioxide and its emission reduction potential 330 7.1 Introduction 322 7.3.1 Introduction 330 7.3.2 Present industrial uses of carbon dioxide 332 7.2 Mineral carbonation 322 7.3.3 New processes for CO2 abatement 332 7.2.1 Definitions, system boundaries and motivation 322 7.3.4 Assessment of the mitigation potential of CO2 7.2.2 Chemistry of mineral carbonation 323 utilization 333 7.2.3 Sources of metal oxides 324 7.3.5 Future scope 334 7.2.4 Processing 324 7.2.5 Product handling and disposal 328 References 335 7.2.6 Environmental impact 328 7.2.7 Life Cycle Assessment and costs 329 7.2.8 Future scope 330 Chapter 7: Mineral carbonation and industrial uses of carbon dioxide 321 EXECUTIVE SUMMARY This Chapter describes two rather different options for carbon and recycled using external energy sources. The resulting dioxide (CO2) storage: (i) the fixation of CO2 in the form of carbonated solids must be stored at an environmentally suitable inorganic carbonates, also known as ‘mineral carbonation’ or location. -
Thermal and Combined Thermal and Radiolytic Reactions Involving
PNL-10490 Thermal and Combined Thermal and Radiolytic Reactions Involving Nitrous Oxide, Hydrogen, and Nitrogen in the Gas Phase; Comparison of Gas Generation Rates in Supernate and Solid Fractions of Tank 241-SY-101 Simulated Waste S. A. Bryan L R. Pederson March 1995 Prepared for the U.S. Department of Energy under Contract DE-AC06-76RL0 1830 Pacific Northwest Laboratory Richland, Washington 99352 DISTRIBUTION OF THIC DOCUMENT IS UNLIMITED IT DISCLAIMER Portions of this document may be illegible in electronic image products. Images are produced from the best available original document. Executive Summary This report summarizes progress made in evaluating mechanisms by which flammable gases are generated in Hanford double-shell tank wastes, based on the results of laboratory tests using simulated waste mixtures. Work described in this report was conducted at Pacific Northwest Laboratory (PNL)(a) for the Flammable Gas Safety Project, the purpose of which is to develop information needed to support Westinghouse Hanford Company (WHC) in their efforts to ensure the safe interim storage of wastes at the Hanford Site. This work is related to gas generation studies being performed at Georgia Institute of Technology (GIT), under subcontract to PNL, using simulated wastes, and to studies being performed at WHC using actual wastes. Described in this report are 1) the results of tests to evaluate the rates of thermal and combined thermal and radiolytic reactions involving flammable gases, and 2) the results of experiments intended to compare gas generation rates in a homogeneous liquid with those in a heterogeneous slurry. Flam• mable gases generated by the radiolysis of water and by the thermal and radiolytic decomposition of organic waste constituents may themselves participate in further reactions. -
Experimental Study on Influence of Al2o3, Cao and Sio2 On
minerals Article Experimental Study on Influence of Al2O3, CaO and SiO2 on Preparation of Zinc Ferrite Jinlin Yang 1,2, Shuo Xu 1, Wentao Zhou 3 , Pengyan Zhu 1, Jiguang Liu 1 and Shaojian Ma 1,2,* 1 College of Resources, Environment and Materials, Guangxi University, Nanning 530004, China; [email protected] (J.Y.); [email protected] (S.X.); [email protected] (P.Z.); [email protected] (J.L.) 2 Guangxi Key Laboratory of Processing for Nonferrous Metallic and Featured Materials, Guangxi University, Nanning 530004, China 3 College of Resources and Civil Engineering, Northeastern University, Shenyang 110819, China; [email protected] * Correspondence: [email protected]; Tel.: +86-0771-3232200 Abstract: Gossan ore of sulfide zinc deposit contains abundant zinc, iron, and other metal elements, which is a significant resource with complex components and can be utilized. In this study, a new technology of preparing zinc ferrite from zinc sulfide deposit gossan was proposed. The effects of Al2O3, CaO, and SiO2 in gossan on the formation of zinc ferrite were investigated by X-ray diffraction (XRD), scanning electron microscopy (SEM), and specific surface area and pore size analysis (BET). The results show that the presence of Al2O3 and CaO could hinder the formation of zinc ferrite, while silica had no effect on the formation of zinc ferrite. Under the conditions of the molar ratio of ZnO and Fe2O3 to Al2O3, CaO, and SiO2 of 1:1:1, an activation time of 60 min, and a roasting temperature of 750 ◦C for 120 min, the products, which had good crystallinity, smooth particle surface, and uniform particle size could be obtained. -
New Kinetic Model for the Rapid Step of Calcium Oxide Carbonation by Carbon Dioxide Lydie Rouchon, Loïc Favergeon, Michèle Pijolat
New kinetic model for the rapid step of calcium oxide carbonation by carbon dioxide Lydie Rouchon, Loïc Favergeon, Michèle Pijolat To cite this version: Lydie Rouchon, Loïc Favergeon, Michèle Pijolat. New kinetic model for the rapid step of calcium oxide carbonation by carbon dioxide. Journal of Thermal Analysis and Calorimetry, Springer Verlag, 2014, 116 (3), pp.1181-1188. 10.1007/s10973-013-3544-y. hal-01009674 HAL Id: hal-01009674 https://hal.archives-ouvertes.fr/hal-01009674 Submitted on 18 Jun 2014 HAL is a multi-disciplinary open access L’archive ouverte pluridisciplinaire HAL, est archive for the deposit and dissemination of sci- destinée au dépôt et à la diffusion de documents entific research documents, whether they are pub- scientifiques de niveau recherche, publiés ou non, lished or not. The documents may come from émanant des établissements d’enseignement et de teaching and research institutions in France or recherche français ou étrangers, des laboratoires abroad, or from public or private research centers. publics ou privés. New kinetic model for the rapid step of calcium oxide carbonation by carbon dioxide Authors: Lydie Rouchon, Loïc Favergeon, Michèle Pijolat Affiliations: École Nationale Supérieure des Mines, SPIN-EMSE, PRESSIC Department, CNRS:UMR5307, LGF F-42023 Saint-Étienne, France Corresponding author: Loïc Favergeon, École Nationale Supérieure des Mines de Saint-Étienne, 158 Cours Fauriel, 42023 Saint-Étienne, Cedex 2, France, e-mail address: [email protected] ; phone number: +33 4 77 42 02 93 ; fax number : +33 4 77 49 96 94. Keywords: Carbonation, Calcium oxide, Kinetic modeling, TG Abstract Carbonation of solid calcium oxide by gaseous carbon dioxide was monitored by thermogravimetry (TG). -
Analysis of the Kinetic Slowing Down During Carbonation of Cao by CO2 Lydie Rouchon, Loïc Favergeon, Michèle Pijolat
Analysis of the kinetic slowing down during carbonation of CaO by CO2 Lydie Rouchon, Loïc Favergeon, Michèle Pijolat To cite this version: Lydie Rouchon, Loïc Favergeon, Michèle Pijolat. Analysis of the kinetic slowing down during carbon- ation of CaO by CO2. Journal of Thermal Analysis and Calorimetry, Springer Verlag, 2013, 113 (3), pp. 1145-1155. 10.1007/s10973-013-2950-5. hal-00858783 HAL Id: hal-00858783 https://hal.archives-ouvertes.fr/hal-00858783 Submitted on 27 Sep 2013 HAL is a multi-disciplinary open access L’archive ouverte pluridisciplinaire HAL, est archive for the deposit and dissemination of sci- destinée au dépôt et à la diffusion de documents entific research documents, whether they are pub- scientifiques de niveau recherche, publiés ou non, lished or not. The documents may come from émanant des établissements d’enseignement et de teaching and research institutions in France or recherche français ou étrangers, des laboratoires abroad, or from public or private research centers. publics ou privés. Analysis of the kinetic slowing down during carbonation of CaO by CO2 Lydie Rouchon, Loïc Favergeon, Michèle Pijolat École Nationale Supérieure des Mines, SPIN-EMSE, CNRS:FRE3312, LPMG F-42023 Saint- Étienne, France Corresponding author: Loïc Favergeon, École Nationale Supérieure des Mines de Saint-Étienne, 158 Cours Fauriel, 42023 Saint-Étienne, Cedex 2, France, e-mail address: [email protected] ; phone number: +33 4 77 42 02 93 ; fax number : +33 4 77 49 96 94. Keywords: Carbonation, Calcium oxide, Kinetics, Porosity, TG Abstract: In order to improve the capture capacity of CaO-based sorbents, it appears important to understand the mechanism of calcium oxide carbonation and to get details on kinetic law controlling the reaction, which has not been really studied up to now. -
Production of Chlorine Dioxide Release Material
(19) TZZ 574598A_T (11) EP 2 574 598 A1 (12) EUROPEAN PATENT APPLICATION (43) Date of publication: (51) Int Cl.: 03.04.2013 Bulletin 2013/14 C01B 11/02 (2006.01) (21) Application number: 11183505.4 (22) Date of filing: 30.09.2011 (84) Designated Contracting States: (72) Inventors: AL AT BE BG CH CY CZ DE DK EE ES FI FR GB • Rahkola, Risto GR HR HU IE IS IT LI LT LU LV MC MK MT NL NO 32730 Sastamala (FI) PL PT RO RS SE SI SK SM TR • Vainio, Pirjo Designated Extension States: 32700 Huittinen (FI) BA ME (74) Representative: Björk, Frida Magdalena (71) Applicant: Kemira Oyj Awapatent AB 00180 Helsinki (FI) Bellevuevägen 46 P.O. Box 5117 200 71 Malmö (SE) (54) Production of chlorine dioxide release material (57) The present invention relates to a process for mixture; and to a chlorine dioxide release material ob- the production of a chlorine dioxide release material com- tainable by said process. Further a process for the pro- prising the steps of: a) admixing a metal chlorite salt so- duction of chlorine dioxide from chlorine dioxide release lution or suspension and a dehydrating agent; b) admix- material comprising contacting at least one chlorine di- ing a dry and/or anhydrous acid source capable of do- oxide release material with a water containing liquid is nating protons to chlorine dioxide generation reactions, disclosed. with said metal chlorite salt and dehydrating agent to a EP 2 574 598 A1 Printed by Jouve, 75001 PARIS (FR) EP 2 574 598 A1 Description Field of the invention 5 [0001] The present invention relates to a process for the production of chlorine dioxide release materials, a process for the production of chlorine dioxide and a chlorine dioxide release material. -
Pressure-Stabilized Divalent Ozonide Cao3 and Its Impact on Earth╎s
Physics & Astronomy Faculty Publications Physics and Astronomy 9-17-2020 Pressure-stabilized Divalent Ozonide CaO3 and Its Impact on Earth’s Oxygen Cycles Yanchao Wang Jilin University Meiling Xu Jiangsu Normal University Liuxiang Yang Center for High Pressure Science and Technology Advanced Research Bingmin Yan Center for High Pressure Science and Technology Advanced Research Qin Qin Center for High Pressure Science and Technology Advanced Research Follow this and additional works at: https://digitalscholarship.unlv.edu/physastr_fac_articles See next page for additional authors Part of the Biological and Chemical Physics Commons Repository Citation Wang, Y., Xu, M., Yang, L., Yan, B., Qin, Q., Shao, X., Zhang, Y., Huang, D., Lin, X., Lv, J., Zhang, D., Gou, H., Mao, H., Chen, C., Ma, Y. (2020). Pressure-stabilized Divalent Ozonide CaO3 and Its Impact on Earth’s Oxygen Cycles. Nature Communications, 11 1-7. http://dx.doi.org/10.1038/s41467-020-18541-2 This Article is protected by copyright and/or related rights. It has been brought to you by Digital Scholarship@UNLV with permission from the rights-holder(s). You are free to use this Article in any way that is permitted by the copyright and related rights legislation that applies to your use. For other uses you need to obtain permission from the rights-holder(s) directly, unless additional rights are indicated by a Creative Commons license in the record and/ or on the work itself. This Article has been accepted for inclusion in Physics & Astronomy Faculty Publications by an authorized administrator of Digital Scholarship@UNLV. For more information, please contact [email protected]. -
Advanced Materials Oxides Brochure
ADVANCED MATERIALS Oxides Oxides The Challenge Materion Advanced Materials, formerly CERAC, Inc., offers complete reproducibility BENEFITS to assure consistent high performance of all oxide compounds. Our integrated We offer a full range of inorganic oxide technologies and manufacturing capabilities allow us to deliver exact compositions, in optical coating materials whatever your application. the exact form you require, exactly where and when you need it! n Variety of forms including granules, pellets & powders n Purity levels up to 99.999% n Supporting various optical wavelength ranges from UV to Far IR GLOBAL MANUFACTURING PROCESSES Custom oxide compositions to your exact specifications provide high yield and less down time. n Oxide Synthesis n Controlled Atmosphere Handling n Chemical Analysis n Custom Particle Sizing OXIDE MATERIALS FOR OPTICAL COATING DEPOSITION n n n n n Aluminum Oxide, Al2O3 Europium Oxide, Eu2O3 Lithium Manganese Oxide, Samarium Oxide, Sm2O3 Titanium Monoxide, TiO LiMn O n n 2 4 n n Antimony Oxide, Sb2O3 Gadolinium Oxide, Gd2O3 Scandium Oxide, Sc2O3 Titanium Sesquioxide, Ti2O3 n Magnesium-Aluminum n Barium Titanate, BaTiO n Gallium Oxide, Ga O n Silicon Dioxide, SiO n Tungsten Oxide, WO 3 2 3 Oxide (spinel) 2 3 n Bismuth Oxide, Bi O n Germanium Oxide, GeO n Silicon Monoxide, SiO n Ytterbium Oxide, Yb O 2 3 2 n Magnesium-Aluminum- 2 3 n n Zirconium Oxide (spinel) n n Boron Oxide, B2O3 Hafnium Oxide, HfO2 Strontium Oxide, SrO Yttrium Oxide, Y2O3 n n n Magnesium Oxide, MgO n n Cadmium Oxide, CdO Indium Oxide, In2O3