Design of a Power Screw
Total Page:16
File Type:pdf, Size:1020Kb
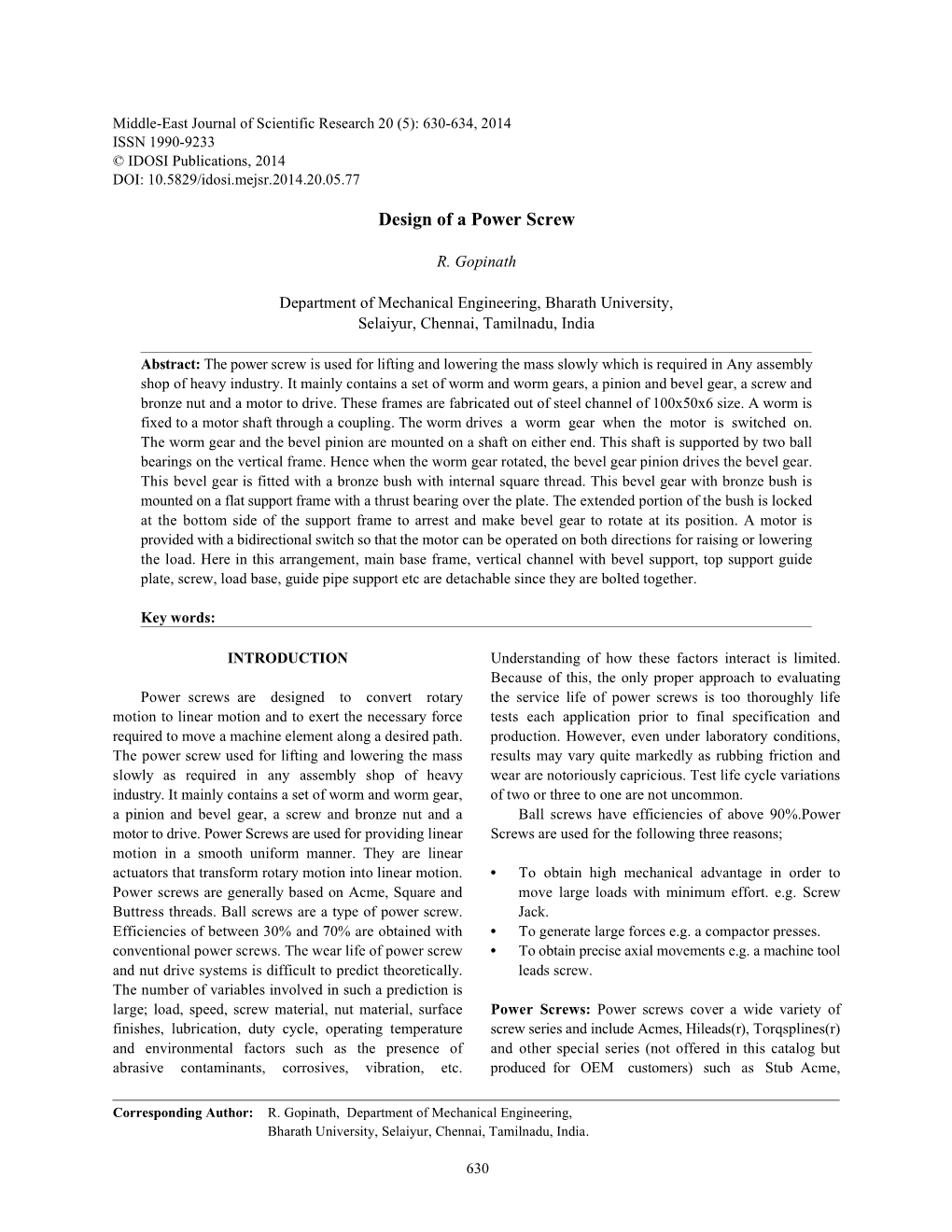
Load more
Recommended publications
-
The Tinkerer's Pendulum for Machine System's Education
Session 2566 The Tinkerer’s Pendulum for Machine System’s Education: Creating a Basic Hands-On Environment with Mechanical “Breadboards” John J. Wood*, Kristin L. Wood** *Department of Mechanical Engineering, Colorado State University **Department of Mechanical Engineering, The University of Texas at Austin Abstract The pendulum of engineering education is swinging from an emphasis of theoretical material to a balance between theory and hands-on activities. This transformation is motivated, in part, by the changing students entering engineering programs. Instead of a tinkering background with the dissection of machines and use of tools, students are now entering with computer, video games, and other “virtual” experiences. This focus has left a void in the ability to relate engineering principles to real-world devices and applications. In this paper, we introduce a new approach for filling this void in a mechanical engineering curriculum. In particular, we describe modifications and extensions to machine design courses to include hands-on exercises. Through the application of “mechanical breadboards,” clear relationships between machine design principles and the reality of machine components are established. These relationships reduce the number of topics covered in the courses, but greatly increase the interest of the students and their potential retention of the material. 1. OVERTURE: INTRODUCTION 1.1 Motivation: Engineering education is transforming from a theoretical emphasis to a balance between applied mathematics and science material and hands-on activities. Design components in courses are helping to provide this balance. Instead of relegating design courses to the last two semesters of an engineering program, many universities are spreading the experiences across the entire 4-5 year curriculum. -
Design of Eccentric Load Carrying Lead Screw Mechanism: an Application of Auxiliary Rolling Shutter System Ajay N
International Journal of Management, Technology And Engineering ISSN NO : 2249-7455 Design of Eccentric Load Carrying Lead Screw Mechanism: An Application of Auxiliary Rolling Shutter System Ajay N. Patil1, Abhinav B. Patil2, Sumesh S. Narkhede3, Pandurang D. Mane4. 1-4Students, Mechanical Engineering Department, Dr. D. Y. Patil School of Engineering, Pune, (India) Abstract Now days, we see rolling shutters near about in every Shop, Garage, Workshops, etc. Some of them are Automatic, some are opened by Mechanical arrangements, & most of this are manually opened. Small scale industries & shops owners can’t afford the automatic shutters because of the high installation cost. Manual operation requires more manpower & more time. In this project we are going to design the auxiliary system for the opening of shutters. We providing more typeof openings in one system. In this system the shutter can be open by using mechanical arrangement, by using switches, & by using the remote control, & manual opening is also provided. This mechanism consists Lead screw, Bearing, Lead screw nut and assembly, Lead screw driving mechanism, Motor, Supporting structure, Lead screw selection. Lead screw for this application is placed on side due to this lead screw contains eccentric load. So in this research paper we design and analyse the lead screw against eccentric load. Keywords: Automatic Shutter, Auxiliary System, Eccentric Load, Lead Screw, Rolling Shutter. Nomenclature A = Cross-sectional area (mm2) dc = Core diameter e = Eccentricity = 400 mm = Factor of safety I = moment of inertia of the cross-section about the neutral axis (mm4) l = lead M= Applied bending moment (N-mm) =Torque required to raise the load (N-mm) W = Load required to raise the shutter= 34.11 Kg 335N p = pitch P = effort required to raise the load. -
Chain & Pulley Tensioners
CHAIN & PULLEY TENSIONERS Engineering Data Tensioner Arms idler Sprocket Sets Idler Roller Pulley Sets ENGINEERING DATA TENSIONING TECHNOLOGY Chain & V-Belt Tensioning Roller chains are power transmission components with positive transmission which, by virtue of their design are subject, depending on quality, to elongation as a result of wear of 1 to 3% of their total length. Inspite of this elongation, due to aging, a roller chain transmits the occurring torques effectively providing it is periodically retensioned. Without tension adjustment, the slack side of the chain becomes steadiliy longer, ascillates and reduces the force transmitting wrap angle of the chain on the sprockets. The chain no longer runs smoothly off the teeth of the sprockets, producing uneven running of the entire drive and supporting wear. The service life of the chain drive can be extended considerably by the use of an automatic chain tension adjuster. The tensioning element prevents the slack side of the chain from 'sagging' or 'slapping' by its automatic operation and very wide tensioning range for compensating this given elongation. The DUNLOP tensioning element is based on the rubber spring principle. According to application it is supplemented with the appropriate idler sprocket for chain drives or with a belt roller pulley in belt tensioner applications. Pretensioning With the tensioning element the necessary travel and simultaneously the corresponding initial tension force can be accurately adjusted by a torsion angle scale and indicating arrow. Excessive initial pretensioning of the chain should be avoided in order to reduce the tensile force and surface pressure on the links. Vibration Damping The DUNLOP tensioning element, based on a system of rubber springs, absorbs considerably the chain vibration due to internal molecular friction in the rubber inserts. -
Design and Analysis of Chain Drive Power Transmission from Stationary to Oscillating Devices
International Research Journal of Engineering and Technology (IRJET) e-ISSN: 2395-0056 Volume: 06 Issue: 03 | Mar 2019 www.irjet.net p-ISSN: 2395-0072 DESIGN AND ANALYSIS OF CHAIN DRIVE POWER TRANSMISSION FROM STATIONARY TO OSCILLATING DEVICES P. Ramesh1, T. Abinesh2, R. Aravind Babu2, P.R. Jagadeesh Babu2 1Asst Professor, R.M.K. Engineering College, Chennai, Tamil Nadu, India 2UG Student, R.M.K. Engineering College, Chennai, Tamil Nadu, India ---------------------------------------------------------------------***--------------------------------------------------------------------- Abstract - A conventional transmission system consists of situations, the second gear is placed and the power is the driver and driven in same axis. If driver axis is changed to recovered by attaching the shafts or hubs to this gear. Though 15° the axis of driven also must be changed to 15° or else drive chains are often being a simple oval loops, they can also failure of the machine element will take place. This work be going around the corners by placing more than two gears modifies the chain so which the driver can be placed along the chain; gears that does not gives power into the stationary and driven can be oscillated by -45° to +45°. Here, system or transmit it out are generally known as the idler- the power can be transmitted from a stationary source to wheels. By varying the diameter of input and output gears some of the oscillating devices like steering. This has a wide with respect to each other, the gear ratio can be altered. For range of application where machine containing multi drives example, the pedals of a normal bicycle can spin all the way can be replaced with the single drive. -
Machine Elements: Connecting Elements Gunt
Engineering design 5 Machine elements: connecting elements gunt Machine elements Components of a technical application that fulfi l certain func- Simple machine elements such as screws, cylinder pins, This section presents the following machine elements: tions in structures are known as machine elements. Machine feather keys or seals are defi ned according to standards and • various connecting elements elements can be both single components and assemblies: therefore can be exchanged without diffi culty. More complex • roller bearings machine elements such as bearings, couplings, gears or shafts • various types of gears • individual parts such as screws, bolts or gears are standardised in only certain important properties, such as • assemblies consisting of individual machine elements, such main dimensions or fl anges, and as such are not fully inter- Connecting elements as couplings, ball bearings, transmissions or valves changeable. An individual machine element always performs the same func- Connecting elements are used when the components in the machine are intended to tion, even though it is used in very different structures. be fi xed fi rmly to each other. Fixing screws, rivets and studs are discrete elements that are usually detachable and can be reused. Screws are the most commonly used machine elements and are classifi ed according to Classifi cation of machine elements their function: fastening screws connect two or more parts fi rmly to each other and can be detached. Motion screws convert rotary motion into linear motion and are used Some machine elements can perform different tasks. For example, couplings can be used as linking and/or transmission elements under load following assembly. -
1.0 Simple Mechanism 1.1 Link ,Kinematic Chain
SYLLABUS 1.0 Simple mechanism 1.1 Link ,kinematic chain, mechanism, machine 1.2 Inversion, four bar link mechanism and its inversion 1.3 Lower pair and higher pair 1.4 Cam and followers 2.0 Friction 2.1 Friction between nut and screw for square thread, screw jack 2.2 Bearing and its classification, Description of roller, needle roller& ball bearings. 2.3 Torque transmission in flat pivot& conical pivot bearings. 2.4 Flat collar bearing of single and multiple types. 2.5 Torque transmission for single and multiple clutches 2.6 Working of simple frictional brakes.2.7 Working of Absorption type of dynamometer 3.0 Power Transmission 3.1 Concept of power transmission 3.2 Type of drives, belt, gear and chain drive. 3.3 Computation of velocity ratio, length of belts (open and cross)with and without slip. 3.4 Ratio of belt tensions, centrifugal tension and initial tension. 3.5 Power transmitted by the belt. 3.6 Determine belt thickness and width for given permissible stress for open and crossed belt considering centrifugal tension. 3.7 V-belts and V-belts pulleys. 3.8 Concept of crowning of pulleys. 3.9 Gear drives and its terminology. 3.10 Gear trains, working principle of simple, compound, reverted and epicyclic gear trains. 4.0 Governors and Flywheel 4.1 Function of governor 4.2 Classification of governor 4.3 Working of Watt, Porter, Proel and Hartnell governors. 4.4 Conceptual explanation of sensitivity, stability and isochronisms. 4.5 Function of flywheel. 4.6 Comparison between flywheel &governor. -
Engineering Design
A111D3 Qfifi^3H NATL INST OF STANDARDS & TECH R.I.C. gineering design : }77 C.1 NBS-PUB-C 19 NBS SPECIAL PUBLICATION 487 U.S. DEPARTMENT OF COMMERCE / National Bureau of Standards Engineering Design MFPG 25th Meeting - r»iT--ti>ii-J'fittMni i;f iiff ii i>i<tiiii m NATIONAL BUREAU OF STANDARDS The National Bureau of Standards^ was established by an act of Congress March 3, 1901. The Bureau's overall goal is strengthen and advance the Nation's science and technology and facilitate their effective application for public benefit. To this end, the Bureau conducts research and provides: (1) a basis for the Nation's physical measurement system, (2) scientific and technological services for industry and government, (3) a technical basis for equity in trade, and (4) technical services to pro- mote public safety. The Bureau consists of the Institute for Basic Standards, the Institute for Materials Research, the Institute for Applied Technology, the Institute for Computer Sciences and Technology, the Office for Information Programs, and the Office of Experimental Technology Incentives Program. THE INSTITUTE FOR BASIC STANDARDS provides the central basis within the United States of a complete and consist- ent system of physical measurement; coordinates that system with measurement systems of other nations; and furnishes essen- tial services leading to accurate and uniform physical measurements throughout the Nation's scientific community, industry, and commerce. The Institute consists of the Office of Measurement Services, and the following center and divisions: Applied Mathematics — Electricity — Mechanics — Heat — Optical Physics — Center for Radiation Research — Lab- oratory Astrophysics^ — Cryogenics^ — Electromagnetics'' — Time and Frequency". -
Design for Functional Requirements Enabled by a Mechanism and Machine Element Taxonomy
INTERNATIONAL CONFERENCE ON ENGINEERING DESIGN, ICED13 19-22 AUGUST 2013, SUNGKYUNKWAN UNIVERSITY, SEOUL, KOREA DESIGN FOR FUNCTIONAL REQUIREMENTS ENABLED BY A MECHANISM AND MACHINE ELEMENT TAXONOMY Szu-Hung LEE, Pingfei JIANG, Peter RN CHILDS Imperial College London, United Kingdom ABSTRACT A process providing an option for engineers and designers to separate the consideration of functional requirements and movement requirements to encourage diverse thinking has been developed and implemented in a graphical interface. In order to assist in consideration of attributes, a database, mechanism and machine element taxonomy (MMET), has been constructed. MMET is composed of the functional attributes, movement attributes, and advantages and disadvantages of machine elements and mechanisms. It provides engineers and designers a wide range of component selection to fulfil design requirements and reliable references to make decisions. Three different interfaces such as hierarchy, functional-oriented and movement-oriented are defined to allow users to explore different options and purposes. This taxonomy also provides comparative information between elements, mechanisms with the same main technical functions. With this information contained in MMET and with the additional aid of a functional analysis diagram (FAD) approach, engineers and designers are able to explore flaws in current designs and deliver alternative solutions by following a proposed creative optimizing process. Keywords: conceptual design, design process, optimisation, process modelling, functional analysis Contact: Szu-Hung Lee Imperial College London Mechanical Engineering London SW7 2AZ United Kingdom [email protected] ICED13/373 1 1 INTRODUCTION As a multi-disciplinary subject, engineering design involves not only technological but also human- interactive and organisational issues. Competition to develop products with enriched functions and improved quality in a time and resource efficient manner drives an interest in design process research. -
Machine Elements – Coordination with Design Science
AEDS 2005 WORKSHOP 3 – 4 November 2005, Pilsen - Czech Republic MACHINE ELEMENTS – COORDINATION WITH DESIGN SCIENCE W. Ernst Eder Keywords: Machine element, function structure, organ structure, constructional part 1. Introduction This paper is a continuation of a paper delivered in 2004 [Eder 2004]. Machine elements has long been a staple subject for mechanical engineering education, and an extensive literature exists, e.g. [Doughtie 1964, Faires 1965, Spotts 1985, Juvinall 2000]. Nevertheless, there is a general lack of a systematic classification, the literature presents partly-ordered listings, examples of existing machine elements, and extensive engineering science analysis, with little attempt at revealing the underlying principles. Such a classification would be useful in the context of design engineering. For teaching engineering, it provides an ‘advanced organizer’ for the information about machine elements [Bruner 1960 and 1966], as a pedagogic aid to help students build that information into their own mental schemata [Eder 2005a and 2005b]. It also provides a basis for applying machine elements to solve problems of design engineering. Technical Systems are tangible products of an enterprise that have a substantial engineering content. They are intended to be used, as operators of a transformation process, see figure 1, working together with the other operators. Figure 1 General Model of a Transformation System Figure 1 shows a generalized model of a transformation system (TrfS), with its processes (TrfP) and their technologies (Tg), its operators: human systems (HuS), technical systems (TS), information systems (IS), management systems (MgtS), and environment systems (EnvS). Inputs to the transformation system include the operands that are to be transformed in the process from their initial state (Od1), assisting inputs (to the process, and to the operators), and secondary inputs (mostly disturbances). -
Topic 3 Fundamental Principles
Topic 3 Fundamental Principles Topics • Occam’s Razor: KISS & MISS • Saint-Venant’s Principle • Abbe’s Principle • Maxwell’s Reciprocity • Self-Principles • Stability • Symmetry • Superposition • Golden Rectangle • Parallel Axis Theorem • Accuracy, Repeatability, Resolution Y • Sensitive Directions • Reference Features θ Y • Structural Loop • Free Body Diagram θ • Centers of Action Z X • Exact Constraint Design Z θX • Elastic Averaging • Dimensional Analysis © 2000 Alexander Slocum • Stick Figures 3-1 Occam’s Razor: KISS & MISS • William of Occam (or Ockham) (1284-1347) was an English philosopher and theologian – Ockham stressed the Aristotelian principle that entities must not be multiplied beyond what is necessary – “Ockham wrote fervently against the papacy in a series of treatises on papal power and civil sovereignty. The medieval rule of parsimony, or principle of economy, frequently used by Ockham came to be known as Ockham's razor. The rule, which said that plurality should not be assumed without necessity (or, in modern English, keep it simple, stupid), was used to eliminate many pseudo-explanatory entities” (http://wotug.ukc.ac.uk/parallel/www/occam/occam-bio.html) • A problem should be stated in its basic and simplest terms • The simplest theory that fits the facts of a problem is the one that should be selected • Limit Analysis is an invaluable way to identify and check simplicity • Use fundamental principles as catalysts to help you – Keep It Super Simple – Make It Super Simple – Because “Silicon is cheaper than cast iron…”(Don -
Class 74 Machine Element Or Mechanism 1 R 1 Ss 1.5 2 3
CLASS 74 MACHINE ELEMENT OR MECHANISM 74 - 1 1 R MISCELLANEOUS 9 .Cam operated 1 SS .High frequency vibratory devices 10 R SHAFT OPERATORS (RADIO TUNER 1.5 ESCAPEMENTS TYPE) 2 AUTOMATIC OPERATION OR CONTROL 10.1 .Preselected position (E.G., TRIPS) 10.15 ..Step by step 3 .Speed controlled 10.2 ..Rotatable stop and projectable 3.2 ..Valve gear trips (e.g., steam abutment engine "Corliss" type) 10.22 ..Digital dial type 3.5 .Retarded 10.27 ..Plural operator 3.52 ..Plural, sequential, trip 10.29 ...Cam and follower actuations 10.31 ....Adjustable cam 3.54 ..Clock train 10.33 .....Sliding operator 3.56 ...Winding knob trip (e.g., alarm 10.35 ....Adjustable follower mechanism) 10.37 .....Sliding operator 4 .Hit and miss 10.39 ...Rack and pinion 5 R GYROSCOPES 10.41 ..With detent or clicker 5.1 .With caging or parking means 10.45 .Plural shafts 5.12 ..Rotor spin and cage release 10.5 .Plural speed type 10.52 ..Planetary 5.14 ..And resetting means 10.54 ..Separate operators 5.2 .With gimbal lock preventing 10.6 .Cam and follower means 10.7 .Tensioned flexible operator 5.22 .Combined 10.8 .Gear drive 5.34 .Multiple gyroscopes 10.85 ..Worm or screw 5.37 ..With rotor drives 10.9 .Lever and linkage drive 5.4 .Gyroscope control 10 A .Remote control 5.41 ..Erecting 813 R ROTARY MEMBER OR SHAFT INDEXING, 5.42 ...By plural diverse forces E.G., TOOL OR WORK TURRET 5.43 ...By jet 814 .With safety device or drive 5.44 ...By weight disconnect 5.45 ...By friction 815 .With locating point adjusting 5.46 ...By magnetic field 816 .Preselected indexed position -
Fundamentals of Design Topic 9 Structural Connections & Interfaces
FUNdaMENTALS of Design Topic 9 Structural Connections & Interfaces © 2008 Alexander Slocum 9-0 1/1/2008 Structural Connections & Interfaces There are many different ways of forming con- nections & interfaces, and each has its own set of heuris- Take a close look at a bridge or a building as it is tic rules that enable a designer to layout a joint quickly being built and compare what you see to the structure of and conservatively. The mechanics of different joints a large crane, automobile, or machine tool. What simi- are also well understood, so the detailed design of the larities and differences do you observe? Can you close joint can then be done deterministically your eyes and visualize how loads transfer through the system? At every connection or interface, power, loads, Consider a three legged chair, and its interface or data are transferred, and it is the job of the design with the ground. For a three legged chair, leg length and engineer to determine the best way to accomplish the compliance are nominally not critical. Three legs will connector or interface for minimum cost. Remember, always contact the ground. However, the chair is more cost is not just the initial (fixed) cost, but includes the prone to tipping because the load must be applied within cost of ownership (variable cost). the bounds of a triangle. On the other hand, consider a five legged chair where each leg has modest compliance All mechanical things have a structure, and the so when a person sits on it, all the legs deform a little bit structure is often made up of parts.