Waste Heat Recovery and Conversion Into Electricity: Current Solutions and Assessment
Total Page:16
File Type:pdf, Size:1020Kb
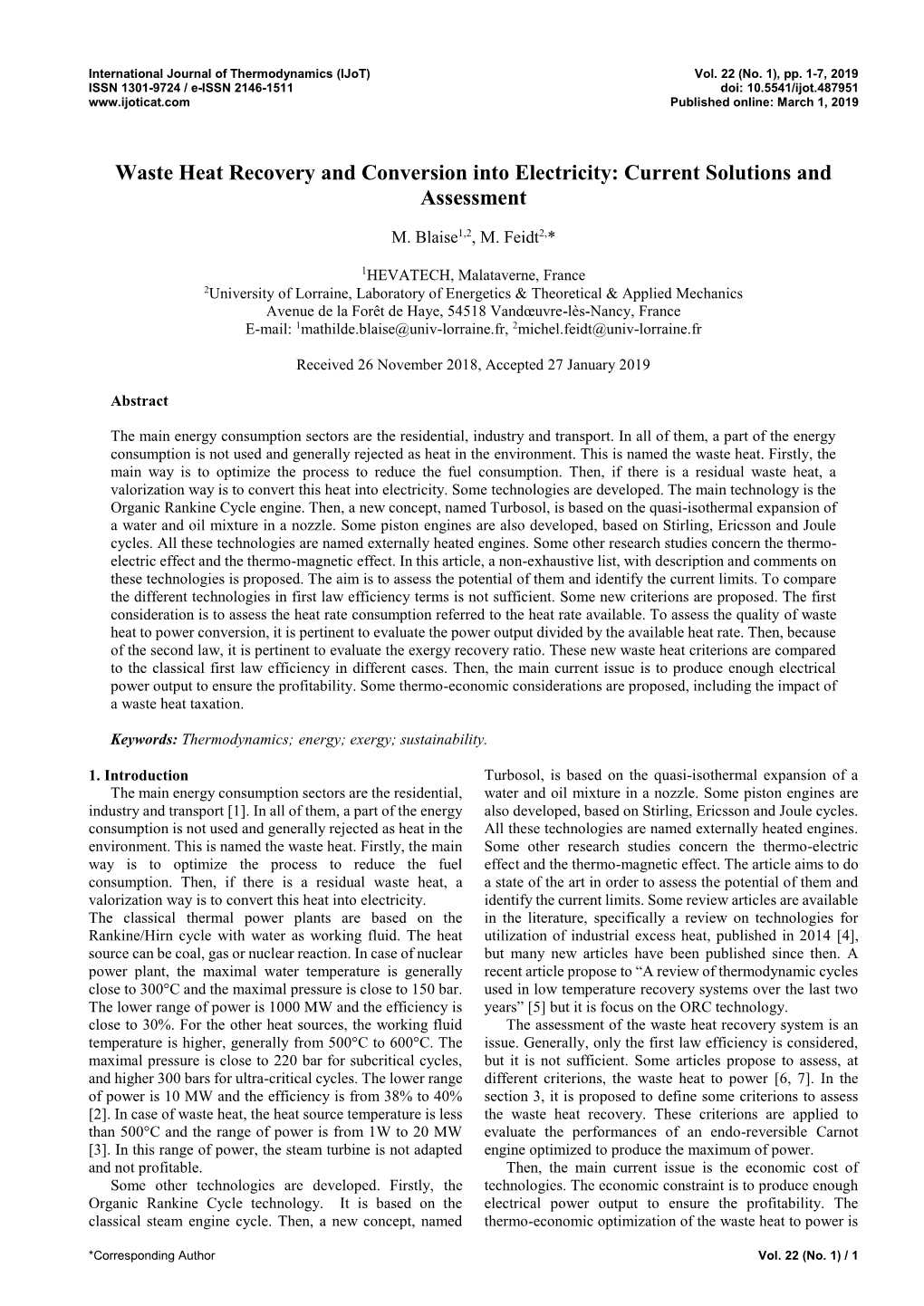
Load more
Recommended publications
-
Recording and Evaluating the Pv Diagram with CASSY
LD Heat Physics Thermodynamic cycle Leaflets P2.6.2.4 Hot-air engine: quantitative experiments The hot-air engine as a heat engine: Recording and evaluating the pV diagram with CASSY Objects of the experiment Recording the pV diagram for different heating voltages. Determining the mechanical work per revolution from the enclosed area. Principles The cycle of a heat engine is frequently represented as a closed curve in a pV diagram (p: pressure, V: volume). Here the mechanical work taken from the system is given by the en- closed area: W = − ͛ p ⋅ dV (I) The cycle of the hot-air engine is often described in an idealised form as a Stirling cycle (see Fig. 1), i.e., a succession of isochoric heating (a), isothermal expansion (b), isochoric cooling (c) and isothermal compression (d). This description, however, is a rough approximation because the working piston moves sinusoidally and therefore an isochoric change of state cannot be expected. In this experiment, the pV diagram is recorded with the computer-assisted data acquisition system CASSY for comparison with the real behaviour of the hot-air engine. A pressure sensor measures the pressure p in the cylinder and a displacement sensor measures the position s of the working piston, from which the volume V is calculated. The measured values are immediately displayed on the monitor in a pV diagram. Fig. 1 pV diagram of the Stirling cycle 0210-Wei 1 P2.6.2.4 LD Physics Leaflets Setup Apparatus The experimental setup is illustrated in Fig. 2. 1 hot-air engine . 388 182 1 U-core with yoke . -
Novel Hot Air Engine and Its Mathematical Model – Experimental Measurements and Numerical Analysis
POLLACK PERIODICA An International Journal for Engineering and Information Sciences DOI: 10.1556/606.2019.14.1.5 Vol. 14, No. 1, pp. 47–58 (2019) www.akademiai.com NOVEL HOT AIR ENGINE AND ITS MATHEMATICAL MODEL – EXPERIMENTAL MEASUREMENTS AND NUMERICAL ANALYSIS 1 Gyula KRAMER, 2 Gabor SZEPESI *, 3 Zoltán SIMÉNFALVI 1,2,3 Department of Chemical Machinery, Institute of Energy and Chemical Machinery University of Miskolc, Miskolc-Egyetemváros 3515, Hungary e-mail: [email protected], [email protected], [email protected] Received 11 December 2017; accepted 25 June 2018 Abstract: In the relevant literature there are many types of heat engines. One of those is the group of the so called hot air engines. This paper introduces their world, also introduces the new kind of machine that was developed and built at Department of Chemical Machinery, Institute of Energy and Chemical Machinery, University of Miskolc. Emphasizing the novelty of construction and the working principle are explained. Also the mathematical model of this new engine was prepared and compared to the real model of engine. Keywords: Hot, Air, Engine, Mathematical model 1. Introduction There are three types of volumetric heat engines: the internal combustion engines; steam engines; and hot air engines. The first one is well known, because it is on zenith nowadays. The steam machines are also well known, because their time has just passed, even the elder ones could see those in use. But the hot air engines are forgotten. Our aim is to consider that one. The history of hot air engines is 200 years old. -
Arxiv:2003.07157V1 [Cond-Mat.Stat-Mech] 10 Mar 2020 Oin Ti on Htteiiilvlmso H Odadho Engine
Stirling engine operating at low temperature difference Alejandro Romanelli∗ Instituto de F´ısica, Facultad de Ingenier´ıa Universidad de la Rep´ublica C.C. 30, C.P. 11000, Montevideo, Uruguay (Dated: March 17, 2020) Abstract The paper develops the dynamics and thermodynamics of Stirling engines that run with tem- perature differences below 100 0C. The working gas pressure is analytically expressed using an alternative thermodynamic cycle. The shaft dynamics is studied using its rotational equation of motion. It is found that the initial volumes of the cold and hot working gas play a non-negligible role in the functioning of the engine. arXiv:2003.07157v1 [cond-mat.stat-mech] 10 Mar 2020 1 I. INTRODUCTION In the field of energy efficiency, the use of waste energy is one of the keys to improve the performance of facilities, whether industrial or domestic. In general the waste energy arises as heat, from some thermal process, that it is necessary to remove. Therefore the use of the waste energy is usually conditioned by the difficulty of converting heat into other forms of energy.1,2 The Stirling engines, being external combustion machines, have the potential to take advantage of any source of thermal energy to convert it into mechanical energy. This makes them candidates to be used in heat recovery systems. The Stirling engine is essentially a two-part hot-air engine which operates in a closed regenerative thermodynamic cycle, with cyclic compressions and expansions of the working fluid at different temperature levels.3,4 The flow of the working fluid is controlled only by the internal volume changes; there are no valves and there is a net conversion of heat into work or vice-versa. -
Gamma-Type Stirling Engine Prototype
MODELLING AND OPTIMIZATION OF HIGH TEMPERATURE DIFFERENCE (HTD) GAMMA- TYPE STIRLING ENGINE PROTOTYPE By Suliman Alfarawi A thesis submitted to the University of Birmingham for the Degree of Doctor of Philosophy School of Mechanical Engineering College of Engineering and Physical Sciences The University of Birmingham September - 2017 University of Birmingham Research Archive e-theses repository This unpublished thesis/dissertation is copyright of the author and/or third parties. The intellectual property rights of the author or third parties in respect of this work are as defined by The Copyright Designs and Patents Act 1988 or as modified by any successor legislation. Any use made of information contained in this thesis/dissertation must be in accordance with that legislation and must be properly acknowledged. Further distribution or reproduction in any format is prohibited without the permission of the copyright holder. ABSTRACT Finding solutions for increasing energy demands is being globally pursued. One of the promising solutions is the utilization of renewable forms of energy with thermo-mechanical conversion systems such as Stirling engines. Nowadays, effort is made in industry and academia to promote the development of Stirling technology. In this context, this thesis was first focused on modelling of High Temperature Difference (HTD) gamma-type Stirling engine prototype (ST05-CNC) and investigating means of improving its performance. Secondly, newly parallel- geometry mini-channel regenerators (with hydraulic diameters of 0.5, 1, 1.5 mm) and their test facility were developed and fabricated to enhance engine performance. Both thermodynamic and CFD models were comprehensively developed to simulate the engine and have been successfully validated against experimental data. -
Stirling Engine)
Heat Cycles Hot air engine (Stirling engine) OPERATE A FUNCTIONAL MODEL OF A STIRLING ENGINE AS A HEAT ENGINE Operate the hot-air engine as a heat engine Demonstrate how thermal energy is converted into mechanical energy Measure the no-load speed as a function of the thermal power UE2060100 04/16 JS BASIC PRINCIPLES The thermodynamic cycle of the Stirling engine While the working piston is in its top dead centre posi- (invented by Rev. R. Stirling in 1816) can be pre- tion: the displacement piston retracts and air is dis- sented in a simplified manner as the processes placed towards the top end of the large cylinder so that thermal input, expansion, thermal output and com- it cools. pression. These processes have been illustrated by The cooled air is compressed by the working piston schematic diagrams (Fig. 1 to Fig. 4) for the func- extending. The mechanical work required for this is tional model used in the experiment. provided by the flywheel rod. A displacement piston P1 moves upwards and displac- If the Stirling engine is operated without any mechanical es the air downwards into the heated area of the large load, it operates with at a speed which is limited only by cylinder, thereby facilitating the input of air. During this internal friction and which depends on the input heating operation the working piston is at its bottom dead centre energy. The speed is reduced as soon as a load takes position since the displacement piston is ahead of the up some of the mechanical energy. This is most easily working piston by 90°. -
HOT AIR ENGINE, DEVELOPED and PATENTED by TRAIAN VUIA, a ROMANIAN PERFORMANCE for 21St CENTURY
HOT AIR ENGINE, DEVELOPED AND PATENTED BY TRAIAN VUIA, A ROMANIAN PERFORMANCE FOR 21st CENTURY DUMITRU MIHALCEA1 Abstract. After thoroughly researching data from national archives, libraries, and important technical studies from Romania and abroad, I concluded that the hot air and closed-circuit engine built, tested, and patented by Romanian engineer Traian Vuia (1872–1950), is superior in its thermodynamic performances to similar engines investigated today. For this engine, almost as perfect thermodynamic Carnot engine, Traian Vuia has achieved ten (10) patents, during 1908-1916 years. Therefore, this engine unjustified forgotten or ignored over a century should be considered a wealth, which belongs (inter) national technical heritage. It represents a great challenge to bring this engine back to the scientific and industrial circuit and, in order to do so, this paper clarifies the following issues: • How evolved over time thermal cycling of different engines, as target perfect thermodynamic engine Carnot; • Which was the thermal process used at Vuia engine for isothermation of compression and expansion; • Today “isodiabate heat release and receipt” at Vuia engine can be qualified as an isentropic process for ideal conditions or adiabatic process for real conditions, with irreversibility, or others; • Which device used Traian Vuia for “isodiabate heat release and receipt”; • Which is the construction and operation of Vuia engine; • If thermal cycle and engine Vuia has been recognized internationally. Key words: Carnot, Stirling, Ericsson, Joule, Brayton, engines, almost perfect thermo- dynamic engines Vuia and Pomojnicu, engines with external combustion, isothermate compression and expansion, isentropic, adiabatic, isodiabatic heat release and receipt, regenerator, recuperator. 1. INTRODUCTION At a time when the steam engine showed signs of technical ageing, causing numerous accidents due to explosion of boilers and high consumption of coal, experts turned their attention to regenerative engines with open or closed circuits, 1Corresponding address: str. -
Beta Type Stirling Engine. Schmidt and Finite Physical Dimensions Thermodynamics Methods Faced to Experiments
entropy Article Beta Type Stirling Engine. Schmidt and Finite Physical Dimensions Thermodynamics Methods Faced to Experiments Cătălina Dobre 1 , Lavinia Grosu 2, Monica Costea 1 and Mihaela Constantin 1,* 1 Department of Engineering Thermodynamics, Engines, Thermal and Refrigeration Equipments, University Politehnica of Bucharest, Splaiul Independent, ei 313, 060042 Bucharest, Romania; [email protected] (C.D.); [email protected] (M.C.) 2 Laboratory of Energy, Mechanics and Electromagnetic, Paris West Nanterre La Défense University, 50, Rue de Sèvres, 92410 Ville d’Avray, France; [email protected] * Correspondence: [email protected] Received: 10 September 2020; Accepted: 9 November 2020; Published: 11 November 2020 Abstract: The paper presents experimental tests and theoretical studies of a Stirling engine cycle applied to a β-type machine. The finite physical dimension thermodynamics (FPDT) method and 0D modeling by the imperfectly regenerated Schmidt model are used to develop analytical models for the Stirling engine cycle. The purpose of this study is to show that two simple models that take into account only the irreversibility due to temperature difference in the heat exchangers and imperfect regeneration are able to indicate engine behavior. The share of energy loss for each is determined using these two models as well as the experimental results of a particular engine. The energies exchanged by the working gas are expressed according to the practical parameters, which are necessary for the engineer during the entire project, namely the maximum pressure, the maximum volume, the compression ratio, the temperature of the heat sources, etc. The numerical model allows for evaluation of the energy processes according to the angle of the crankshaft (kinematic–thermodynamic coupling). -
Determining the Efficiency of the Hot-Air Engine As a Refrigerator
LD Heat Physics Thermodynamic cycle Leaflets P2.6.2.3 Hot-air engine: quantitative experiments Determining the efficiency of the hot-air engine as a refrigerator Objects of the experiments Measuring the heat Q2 extracted from the cylinder head during one revolution. Measuring the heat Q1 transferred to the cooling water during one revolution. Determining the efficiency of the refrigerator. Principles During one revolution, the hot-air engine, operated as a re- The efficiency is determined experimentally by driving the frigerator, extracts the heat Q2 from the cylinder head and flywheel of the hot-air engine with an electric motor at an transfers the heat Q1 to the cooling water. As heat is transferred angular speed f and determining the electric calorific power from the colder to the warmer reservoir, that is, in the opposite that permanently keeps the cylinder head at room temperature direction of spontaneous heat transfer, a certain amount of in a compensation measurement. The electric work supplied mechanical work W has to be supplied during one revolution. per revolution is equal to the heat Q2 extracted from the The refrigerator thus is a heat engine operated in the reverse cylinder head, that is direction. If there are no losses, the following relation between U ⋅ I the quantities involved holds: Q = (III) 2 f Q1 = Q2 + W (I). U: heating voltage, I: heating current The efficiency of a refrigerator is defined as the ratio In addition, the increase in temperature ⌬ of the cooling water Q is measured and the power transferred to the cooling water = 2 (II) ⌬V W P = c ⋅ ⋅ ⋅ ⌬ (IV) ⌬t c = 4.185 J g–1 K–1: specific heat capacity of water, = 1 g cm–3: density of water ⌬V : volume flow rate of the cooling water Determining the efficiency of the refrigerator ⌬t is determined. -
Thermodynamic Study of a Low Temperature Difference Stirling Engine at Steady State Operation
Int. J. of Thermodynamics ISSN 1301-9724 Vol. 10 (No. 4), pp. 165-176, December 2007 Thermodynamic Study of a Low Temperature Difference Stirling Engine at Steady State Operation Nadia MARTAJ *, Lavinia GROSU 1*, Pierre ROCHELLE *,** * Laboratoire d’Energétique et d’Economie d’Energie 50, rue de sèvres, 92 410 Ville d’Avray ** Laboratoire de Mécanique Physique 2, av. de la Gare de Ceinture 78310 Saint Cyr l’Ecole [email protected] Abstract In the current energy economy context, the use of renewable energies and the valuation of lost energies are the subject of many studies. From this point of view, the Stirling engine draws attention of the researchers for its many advantages. This paper presents a thermodynamic analysis of a low temperature Stirling engine at steady state operation; energy, entropy and exergy balances being presented at each main element of the engine. A zero dimensional numerical model describing the variables evolution (pressure, volumes, masses, exchanged energies, irreversibilities...) as function of the crankshaft angle is also presented. The calculated irreversibilities are due to imperfect regeneration and temperature differences between gas and wall in the hot and cold exchangers. A favourable comparison was made with experimental results obtained on an small size engine. Keywords: Stirling engine, numerical model, thermodynamic analysis, imperfect regeneration. 1. Introduction Cold Sink In the past few yars the understanding of the Stirling engine has shown considerable growth. Vc TDC Many new applications were developed, one of y these applications being the low temperature lr y0+l r difference Stirling engine. This new type of Vh Stirling engine is able to operate with very low BDC temperature difference between the source and the TDC sink of the engine. -
The Stirling Engine
THE STIRLING ENGINE STUDENT BOOKLET January 2009 Table of contents Once upon a time a surprising machine! ......................................................................................3 Let's warm up a little ......................................................................................................................4 Kinetic theory of gases...................................................................................................................6 Number of molecules and volume of a gas..................................................................................9 The effect of temperature on the volume of a gas (Charles Law) .................................... 15 The effect of pressure on the volume of a gas (Boyle-Mariotte’s Law) .......................... 21 Function of a liquid column pressure gauge (optional)...........................................................27 The effect of temperature on the pressure of a gas (Gay-Lussac's Law) ......................36 Questionnaire on the general laws of gases ............................................................................43 Back to the Stirling engine .........................................................................................................44 Nomenclature of the Stirling engine .........................................................................................45 Stirling engine operating guide ...................................................................................................46 Analysis of the laboratory Stirling -
Comparative Study of Stirling Engine
International Journal of Technical Research and Applications e-ISSN: 2320-8163, www.ijtra.com Volume 6, Issue 2 (MARCH-APRIL 2018), PP. 72-75 COMPARATIVE STUDY OF STIRLING ENGINE Amit Baghel1, Rajesh Yadav2, Manish Rajput3, Mayank Agrawal4, Department of Mechanical Engineering 1Student, Dayalbagh Educational Institute Agra, India 2Student, Dayalbagh Educational Institute Agra, India 3Student, Dayalbagh Educational Institute Agra, India 4Lecturer, Dayalbagh Educational Institute Agra, India Abstract—A Stirling engine is a heat engine operating by cycle the energies and high initial capital cost to install the compression and expansion of air or other gas stirling engine is a conversion technologies new generation of stirling engine that has been born to increase A Stirling engine is a heat engine that operates by cyclic the effectiveness of stirling engine .this engine is noted for its high compression and expansion of air or other gas at different efficiency compared to another engines. This compatibility with temperatures, such that there is a net conversion of heat energy alternative and renewable energy sources in which it has become increasingly significant as the price of conventional fuels rises, to mechanical work More specifically, the Stirling engine is a and also in light of concerns such as peak oil and climate change . closed-cycle regenerative this paper is mainly aimed to analyze stirling engine as a LTD or heat engine with a permanently gaseous working fluid. practical engine which has high efficiency almost nearer to the Closed-cycle,in this context, means a thermodynamic cycle in carnot cycle based engine .As a result , this study indicates how which the working fluid specific type of internal heat stirling engines work and give the higher efficiency than present exchanger and thermal store, known as the renerator The time engine. -
The Hot-Air Engine As a Heat Engine: Recording and Evaluating the Pv Diagram with CASSY
Heat LEYBOLD Physics Thermodynamic cycle Leaflets P2.6.2.4 Hot-air engine: quantitative experiments The hot-air engine as a heat engine: Recording and evaluating the pV diagram with CASSY Objects of the experiment Recording the pV diagram for different heating voltages. Determining the mechanical work per revolution from the enclosed area. Principles The cycle of a heat engine is frequently represented as a closed curve in a pV diagram ( p: pressure, V: volume). Here the mechanical work taken from the system is given by the en- closed area: W = − ͛ p ⋅ dV (I) The cycle of the hot-air engine is often described in an idealised form as a Stirling cycle (see Fig. 1), i.e., a succession of isochoric heating (a), isothermal expansion (b), isochoric cooling (c) and isothermal compression (d). This description, however, is a rough approximation because the working piston moves sinusoidally and therefore an isochoric change of state cannot be expected. In this experiment, the pV diagram is recorded with the computer-assisted data acquisition system CASSY for comparison with the real behaviour of the hot-air engine. A pressure sensor measures the pressure p in the cylinder and a displacement sensor measures the position s of the working piston, from which the volume V is calculated. The measured values are immediately displayed on the monitor in a pV diagram. Fig. 1 pV diagram of the Stirling cycle 0210-Wei 1 P2.6.2.4 LEYBOLD Physics Leaflets Setup Apparatus The experimental setup is illustrated in Fig. 2. 1 hot-air engine . 388 182 1 U-core with yoke .