Profile of the Metal Mining Industry
Total Page:16
File Type:pdf, Size:1020Kb
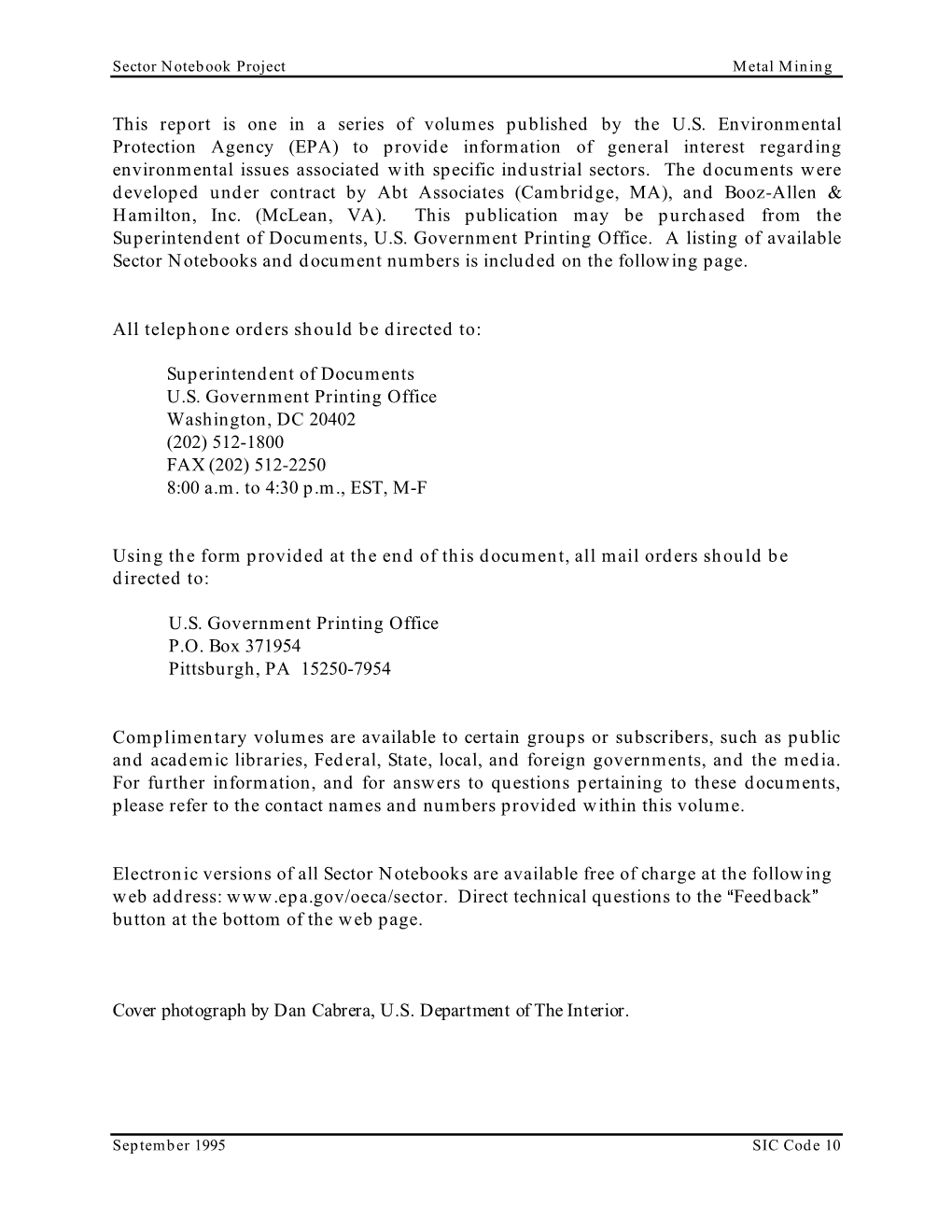
Load more
Recommended publications
-
Results of Reconnaissance for Radioactive Minerals in Parts of The
GEOLOGICAL SURVEY CIRCULAR 294 RESULTS OF RECONNAISSANCE FOR RADIOACTIVE MINERALS IN PARTS OF THE ALMA DISTRICT PARK COUNTY, COLORADO UNITED STATES DEPARTMENT OF THE INTERIOR Douglas McKay, Secretary GEOLOGICAL SURVEY W. E. Wrather, Director GEOLOGICAL SURVEY CIRCULAR 294 RESULTS OF RECONNAISSANCE FOR RADIOACTIVE MINERALS IN PARTS OF THE ALMA DISTRICT, PARK COUNTY, COLORADO By C. T. Pierson and Q. D. Singewald This report concerns work done on behalf of the U. S. Atomic Energy Commission and is published with the permission of the Commission. Washington, D. Free on application to the Geological Survey, Washington 25, D. C. RESULTS OF RECONNAISSANCE FOR RADIOACTIVE MINERALS IN PARTS OF THE ALMA DISTRICT, PARK COUNTY, COLORADO By C. T. Pierson and Q. D. Singewald CONTENTS Page Page Abstract.................................... 1 Occurrences of uranium Continued Introduction................................. 1 Veins in pre-Cambrian rocks............ 3 Field work and acknowledgments......... 1 London vein system..................... 7 Location and accessibility............... 2 Veins east of Cooper Gulch fault.......... 7 General geology and ore deposits.............. 2 Disequilibria in the uranium occur Method of reconnaissance for radioactive rences............................. 7 minerals.................................. 3 Nonradioactive localities................ 7 Radioactivity measurements.................. 3 Origin................................. 7 Occurrences of uranium...................... 3 Literature cited............................ -
Mining Index To
MINING INDEX TO HENDERSON, HOLLISTER, AND CANFIELD HISTORIES DENVER PUBLIC LIBRARY WESTERN HISTORY DEPARTMENT Typed and edited by Rita Torres February, 1995 MINING INDEX to Henderson, Hollister, and Canfield mining histories. Names of mines, mining companies, mining districts, lodes, veins, claims, and tunnels are indexed with page number. Call numbers are as follows: Henderson, Charles. Mining in Colorado; a history of discovery, development and production. C622.09 H38m Canfield, John. Mines and mining men of Colorado, historical, descriptive and pictorial; an account of the principal producing mines of gold and silver, the bonanza kings and successful prospectors, the picturesque camps and thriving cities of the Rocky Mountain region. C978.86 C162mi Hollister, Orvando. The mines of Colorado. C622.09 H72m A M W Abe Lincoln mine p.155c, 156b, 158a, 159b, p.57b 160b Henderson Henderson Adams & Stahl A M W mill p.230d p.160b Henderson Henderson Adams & Twibell A Y & Minnie p.232b p.23b Henderson Canfield Adams district A Y & Minnie mill p.319 p.42d, 158b, 160b Hollister Henderson Adams mill A Y & Minnie mines p.42d, 157b, 163b,c, 164b p.148a, 149d, 153a,c,d, 156c, Henderson 161d Henderson Adams mine p.43a, 153a, 156b, 158a A Y mine, Leadville Henderson p.42a, 139d, 141d, 147c, 143b, 144b Adams mining co. Henderson p.139c, 141c, 143a Henderson 1 Adelaide smelter Alabama mine p.11a p.49a Henderson Henderson Adelia lode Alamakee mine p.335 p.40b, 105c Hollister Henderson Adeline lode Alaska mine, Poughkeepsie gulch p.211 p.49a, 182c Hollister Henderson Adrian gold mining co. -
General Index
CAL – CAL GENERAL INDEX CACOXENITE United States Prospect quarry (rhombs to 3 cm) 25:189– Not verified from pegmatites; most id as strunzite Arizona 190p 4:119, 4:121 Campbell shaft, Bisbee 24:428n Unanderra quarry 19:393c Australia California Willy Wally Gully (spherulitic) 19:401 Queensland Golden Rule mine, Tuolumne County 18:63 Queensland Mt. Isa mine 19:479 Stanislaus mine, Calaveras County 13:396h Mt. Isa mine (some scepter) 19:479 South Australia Colorado South Australia Moonta mines 19:(412) Cresson mine, Teller County (1 cm crystals; Beltana mine: smithsonite after 22:454p; Brazil some poss. melonite after) 16:234–236d,c white rhombs to 1 cm 22:452 Minas Gerais Cripple Creek, Teller County 13:395–396p,d, Wallaroo mines 19:413 Conselheiro Pena (id as acicular beraunite) 13:399 Tasmania 24:385n San Juan Mountains 10:358n Renison mine 19:384 Ireland Oregon Victoria Ft. Lismeenagh, Shenagolden, County Limer- Last Chance mine, Baker County 13:398n Flinders area 19:456 ick 20:396 Wisconsin Hunter River valley, north of Sydney (“glen- Spain Rib Mountain, Marathon County (5 mm laths donite,” poss. after ikaite) 19:368p,h Horcajo mines, Ciudad Real (rosettes; crystals in quartz) 12:95 Jindevick quarry, Warregul (oriented on cal- to 1 cm) 25:22p, 25:25 CALCIO-ANCYLITE-(Ce), -(Nd) cite) 19:199, 19:200p Kennon Head, Phillip Island 19:456 Sweden Canada Phelans Bluff, Phillip Island 19:456 Leveäniemi iron mine, Norrbotten 20:345p, Québec 20:346, 22:(48) Phillip Island 19:456 Mt. St-Hilaire (calcio-ancylite-(Ce)) 21:295– Austria United States -
Bioremediation of Acid Mine Drainage Using Sulfate-Reducing Bacteria
Bioremediation of Acid Mine Drainage Using Sulfate-Reducing Bacteria August 2006 Prepared by Sheela M. Doshi National Network of Environmental Management Studies Fellow University of Indiana for U.S. Environmental Protection Agency Office of Solid Waste and Emergency Response Office of Superfund Remediation and Technology Innovation Washington, D.C. www.epa.gov www.clu-in.org Bioremediation of Acid Mine Drainage Using Sulfate-Reducing Bacteria NOTICE This document was prepared by a National Network of Environmental Management studies grantee under a fellowship from the U.S. Environmental Protection Agency. This report was not subject to EPA peer review or technical review. The EPA makes no warranties, expressed or implied, including without limitation, warranty for completeness, accuracy, or usefulness of the information, warranties as to the merchantability, or fitness for a particular purpose. Moreover, the listing of any technology, corporation, company, person, or facility in this report does not constitute endorsement, approval, or recommendation by the EPA. The report contains information attained from a wide variety of currently available sources, including project documents, reports, periodicals, Internet websites, and personal communication with both academically and commercially employed sources. No attempts were made to independently confirm the resources used. It has been reproduced to help provide federal agencies, states, consulting engineering firms, private industries, and technology developers with information on the current status of this project. About the National Network for Environmental Management Studies The National Network for Environmental Management Studies (NNEMS) is a comprehensive fellowship program managed by the Environmental Education Division of EPA. The purpose of the NNEMS Program is to provide students with practical research opportunities and experiences. -
CHARACTERIZATION of GRANITE and SUBSEQUENT GROUND CONTROL MANAGEMENT PLAN at ORPHAN BOY MINE – BUTTE, ONTM ANA Emily Rose Montana Tech
Montana Tech Library Digital Commons @ Montana Tech Graduate Theses & Non-Theses Student Scholarship Spring 2017 CHARACTERIZATION OF GRANITE AND SUBSEQUENT GROUND CONTROL MANAGEMENT PLAN AT ORPHAN BOY MINE – BUTTE, ONTM ANA Emily Rose Montana Tech Follow this and additional works at: http://digitalcommons.mtech.edu/grad_rsch Part of the Geology Commons, and the Mining Engineering Commons Recommended Citation Rose, Emily, "CHARACTERIZATION OF GRANITE AND SUBSEQUENT GROUND CONTROL MANAGEMENT PLAN AT ORPHAN BOY MINE – BUTTE, MONTANA" (2017). Graduate Theses & Non-Theses. 122. http://digitalcommons.mtech.edu/grad_rsch/122 This Thesis is brought to you for free and open access by the Student Scholarship at Digital Commons @ Montana Tech. It has been accepted for inclusion in Graduate Theses & Non-Theses by an authorized administrator of Digital Commons @ Montana Tech. For more information, please contact [email protected]. CHARACTERIZATION OF GRANITE AND SUBSEQUENT GROUND CONTROL MANAGEMENT PLAN AT ORPHAN BOY MINE – BUTTE, MONTANA by Emily Rose A thesis submitted in partial fulfillment of the requirements for the degree of Master of Science in Mining Engineering Montana Tech 2017 ii Abstract The Underground Mine Education Center (UMEC) and World Museum of Mining facilities began as shallow underground mines in the 1880’s during the mining boom that populated Butte, Montana. The UMEC is a multi-disciplinary facility that provides an on-campus underground laboratory environment and a place for students to learn and practice practical underground mining techniques; therefore, the longevity of the facility is important to Montana Tech. The goal of this project is to develop a Ground Control Management Plan (GCMP) for the UMEC and World Museum of Mining facilities. -
Flume, and That Has Prompted a Look Exceeded $20 Per Ounce, Said William Back at the Mine's Rich History
Parked in the Past Early days at the Orphan Boy 2011 fire not a first; gold production $583.5 million in today's dollars Laura Van Dusen, Correspondent Januery 27, 2012 A fire of unknown origin occurred Dec. 23 About $7 million in gold was taken from at the historic Orphan Boy Mine in the Orphan Boy over the years it was in Mosquito Gulch, according to the Jan. 6 operation, a time when gold never Flume, and that has prompted a look exceeded $20 per ounce, said William back at the mine's rich history. Jeffries in a report written in 1990 and A 20-foot-tall ore house, one of three stored at the Park County Local History structures that had survived the passing Archives. His great-uncle was James years, was destroyed in the Dec. 23 fire. Moynahan, owner and later manager of The structures remaining at the site are a the Orphan Boy. collapsed tool shed and the mine portal. Assuming the weight of 350,000 ounces But that was not the only fire that has and knowing that the value of gold per been reported at the Orphan Boy. ounce as of Jan. 22 of this year was $1,667.19, the gold taken out of the In October 1907, a bunkhouse burned to Orphan Boy in today's dollars would be the ground. Miners were asleep when it worth about $583.5 million. That figure started. does not include the value of other "The bunkhouses on the Orphan Boy minerals taken from the Orphan Boy in its mine burned down last week. -
Abandoned Mine Site Characterization and Cleanup Handbook, Epa 910-B-00-001
Table of Contents v APPENDICES Appendix A: Acronym List and Glossary of Mining Terms Appendix B: Acid Mine Drainage Appendix C: Mining Sites on the NPL Appendix D: General Discussion of Applicable or Relevant and Appropriate Requirements at Superfund Mining Sites Appendix E: X-Ray Florescence Appendix F: Risk Assessment Scoping, Problem Formulation, and Additional Risk Assessment Guidance Appendix G: Detailed Information on Mine Remediation Technologies Appendix H: Innovative Technologies Appendix I: EPA Mining Contacts Appendix J: Internet Resources Appendix K: Land Disposal Restrictions Overview and Bibliography Appendix L: Mine Waste Technology Program Appendix M: Remediation References APPENDIX A ACRONYM LIST and GLOSSARY OF MINING TERMS Appendix A: Acronym List and Glossary of Mining Terms (This Page Intentionally Blank) A - 2 Appendix A: Acronym List and Glossary of Mining Terms NPS National Park Service OSC On-Scene Coordinator OPPTS Office of Prevention Pesticides and Toxic Substances ORD Office of Research and Development O&M Operating and maintenance OSM Office of Surface Mining OSHA Occupational Safety and Health Act OSW Office of Solid Waste OSWER Office of Solid Waste and Emergency Response OU Operable Units OW Office of Water PAHs Poly Aromatic Hydrocarbons PCBs Polychlorinated Biphenols PRG Preliminary Remediation Goals PRP Potentially Responsible Party QAPP Quality Assurance Project Plan RAGS Risk Assessment Guidance for Superfund RAOs Remedial Action Objectives RCRA Resource Conservation and Recovery Act RI/FS Remedial -
Reclamation Work Plan Lilly/Orphan Boy Mine Powell County, Montana
FINAL Phase II - Reclamation Work Plan Lilly/Orphan Boy Mine Powell County, Montana Prepared for: Montana Department of Environmental Quality P.O. Box 200901 Helena, MT 59620-0901 Prepared By: TerraGraphics Environmental Engineering, Inc. 15 W 6th Avenue, Power Block 3rd Floor W Helena, MT 59601 406.441.5441 ph 406.441.5443 fx September 24, 2010 Lilly/Orphan Boy Reclamation Work Plan Table of Contents Section 1.0 INTRODUCTION ....................................................................................................... 1 1.1 Purpose of the Phase II Reclamation Work Plan.................................................................. 1 1.2 Organization of Phase II Reclamation Work Plan................................................................ 2 1.3 Project Team......................................................................................................................... 3 1.4 Project Schedule ................................................................................................................... 4 Section 2.0 ENVIRONMENTAL SETTING ................................................................................. 5 2.1 Setting and Climate............................................................................................................... 5 2.2 Geology and Soils................................................................................................................. 5 2.3 Hydrogeology ...................................................................................................................... -
9:30 AM ADMINISTRATIVE SESSION Video to Join the Meeting, Click on the Link Below Or Copy and Paste Into Your Preferred Web Brow
PARK COUNTY BOARD OF COMMISSIONERS WORK SESSION VITRUAL MEETING WEDNESDAY, JANUARY 6, 2021 9:30 AM ADMINISTRATIVE SESSION Video To join the meeting, click on the link below or copy and paste into your preferred web browser: https://zoom.us/j/632627219? pwd=Q2gvUVEwd0JuQ0R3TE9qWE9LTk9kQT09 Audio Upon joining the meeting, you will have the option to use either your computer mic and speakers for audio interaction, or participate by phone. If you are not using your computer speakers and mic to interact in the meeting, you may use the dial- option below: Dial by your location (669) 900-6833 US (Western US) (929) 205-6099 US (Eastern US) Meeting ID: 632 627 219 Password: 04408 * At the start of the meeting enter your name when prompted * 9:30 AM ADMINISTRATIVE SESSION (OPEN) . DISCUSSION RELATED TO THE PROPOSED REVISION TO PARK COUNTY PUBLIC HEALTH ORDER 20-09 . DISCUSSION RELATED TO APPROVAL OF THE NATIONAL NOMINATION FOR THE SPRING HOUSE / MOYNIHAN HOUSE Documents: NR Nomination Review Form.pdf Tentative Agenda_CLG mailing.pdf CLG_NR_Mtg_Commission_virtual_Spring House.pdf CO_Park County_Spring House_NR_11.9.20.pdf The purpose of a work session is to provide for a free and open dialogue. Discussions are not limited to those items being on the agenda. NOTE: This WORK SESSION agenda may be modified with items either being added or deleted. Please check Website "parkco.us" for most updated agendas. If you need further information, please contact the BOCC (Board of County Commissioners) office at 719-836-4201. COLORADO CERTIFIED LOCAL GOVERNMENT NATIONAL REGISTER NOMINATION REVIEW REPORT FORM Property Name: Address: Certified Local Government: Date of public meeting at which nomination was reviewed: Eligibility Criteria: (Check applicable boxes) Criterion A Criterion C Criterion B Criterion D Please check the boxes below appropriate to the nomination review: Commission/Board The commission/board recommends that the nomination meets the criteria checked above. -
PRR' S Were. Seri-Tttl:F•::Tlle ~Ejeum)
NarES PRR -•('Prellminary;,~nha±ssanc.e Reports) reports may not be canplete in the -fonn Bendi:.K sent·'.them to u5Th:~e;:hlaY also be a copy microfilmed by NTIS or Oak Ridge which is··· IIDre -Ji.xxnplete 'Siia'-'tb·lli>copies · should. be kept together. ('IDe origirial copies'· of the PRR' s were. seri-tttl:f•::tlle ~EJeum). - ' ,):-!-.~ . ,.-: PGJ rePGJfus w~e:.:f.;plac~,,byPGJ/F andG.JQ reports. All PGJ's should be discarded. Note·:itmt-.the:•£i;liil}i,:p.K.tl:ies.erepdrts differs frcm the usual date/number pattern. 'lll.ey are filed.nilriieriEally/'disregarding the date. - .. ; ---·. '- ' :; . ·.•.-..·~ -..~. : ,,., ~-~' f _J,· ..·:£~~~ ,-·- --~~( ) The reports listed in this Bibliography are available, as of August 1, 1984, from the u.s. Geological Survey, Open-File Services Section. Inquiries should be sent to U.S. Geological Survey, Open-File Services Section, Building 41, · MS 306, P.o. Box 25046, Federal Center, Denver, Colorado 80225, Telephone (303,) 236-7476. ,) ACC0-40 "A Pilot Plant Test of the Electrolytic. Uranium Recovery ) Process," G. w. Clevenger, June 17, 1954, 36. P• AEC-PED-1 "Uranium Mine Operations Data," Production Evaluation Division," u.S. Atomic. Energy Commission, January 1, 1959, 363 p.; PR No. 79-119; 9/24/79. Res.o<.J..te :::t:;.I(,H:.~J .(...;s~+-alo.- -c,•v, .)i (/'\. AEC-RID-1 "Summary and Tabulation of Sulfur-Isotope Work", s. R. Austin, January 1968, 30 p.; PR No. 68-486, 5/16/68. AEC-RID-2 "Thorium, Yttrium and Rare-earth Analyses, Lemhi Pass, Idaho and Montana," s. R. Austin, April 1968, 12 p.; PR No. -
Mine Waste Technology Program in Situ Source Control of Acid
MWTP-298 June 2008 Mine Waste Technology Program In Situ Source Control Of Acid Generation Using Sulfate-Reducing Bacteria By: Suzzann Nordwick MSE Technology Applications, Inc. Mike Mansfield Advanced Technology Center Butte, Montana 59702 Under Contract No. DE-AC09-96EW96405 Through EPA IAG No. DW89938870-01-0 Diana Bless, EPA Program Manager Sustainable Technology Division National Risk Management Research Laboratory Cincinnati, Ohio 45268 This study was conducted in cooperation with U.S. Department of Energy Environmental Management Consolidated Business Center Cincinnati, Ohio 45202 National Risk Management Research Laboratory Office of Research and Development U.S. Environmental Protection Agency Cincinnati, Ohio 45268 Disclaimer This publication is a report of work conducted under the Mine Waste Technology Program that was funded by the Environmental Protection Agency and managed by the Department of Energy under the authority of an Interagency Agreement. Because the Mine Waste Technology Program participated in EPA’s Quality Assurance Program, the project plans, laboratory sampling and analyses, and final report of all projects were reviewed to ensure adherence to the data quality objectives. The views expressed in this document are solely those of the performing organization. The views and opinions of authors expressed herein do not necessarily state or reflect those of the United States Government or any agency thereof. Reference herein to any specific commercial product, process, or service by trade name, trademark, manufacturer, -
Anderson-Carlisle Technical Society Annual Report May 5Th, 2020
Anderson-Carlisle Technical Society A Student Chapter of the Society for Mining, Metallurgy, and Exploration Annual Report May 5th, 2020 Table of Contents ACTS Membership ..............................................................................................................3 2019-2020 SME Chapter Officers ...................................................................................3 2019-2020 Mining Team: ................................................................................................4 2019-2020 Mine Rescue Team Officers ..........................................................................4 2019-2020 Geological Club Officers ...............................................................................4 2019-2020 Club Metallurgy Officers ..............................................................................4 2019-2020 ISEE Chapter Officers ...................................................................................4 2019-2020 WIM Chapter Officers ...................................................................................5 History..................................................................................................................................5 President Report ...................................................................................................................6 Treasurer Report ..................................................................................................................9 Secretary Report.................................................................................................................10