André-Jacob Roubo
Total Page:16
File Type:pdf, Size:1020Kb
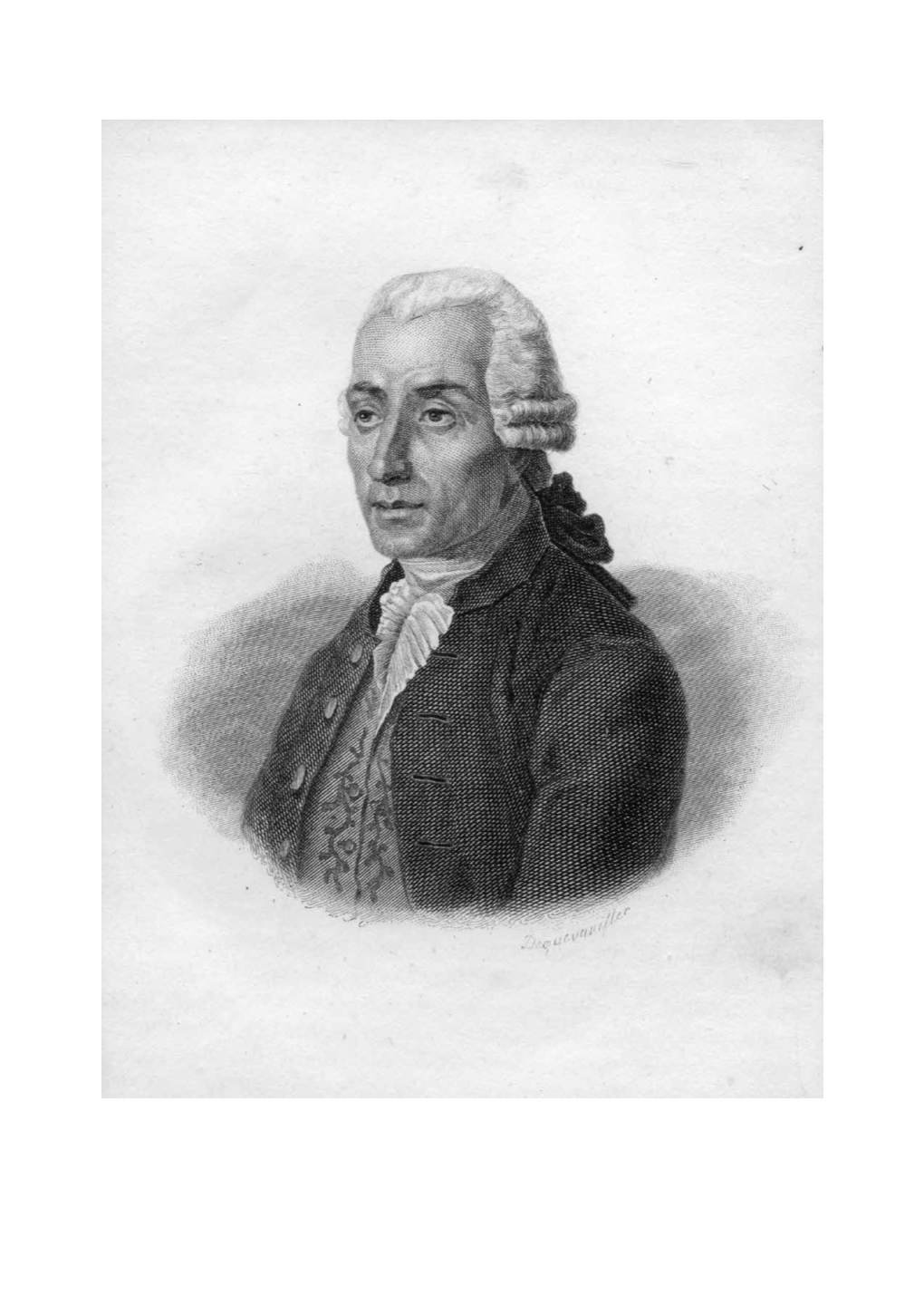
Load more
Recommended publications
-
1 Corrected and Approved by B.T.E on Dated 17.01.2018
CURRICULUM FOR THREE YEAR SIX Semester DIPLOMA COURSE IN ===================================== : PAPER & PULP TECHNOLOGY : : Effective from Session : ===================================== ==================== UNDER DEVELOPMENT ==================== ==================== : Semester System : ==================== Prepared By ================================= : Curriculum Development Cell : ================================= INSTITUTE OF RESEARCH DEVELOPMENT & TRAINING, U.P., KANPUR APPROVED BY ================================= : BOARD OF TECHNICAL EDUCATION : : U.P. LUCKNOW, : :CORRECTED AS SYLLABUS COMMITTEE OF: : B.T.E. MEETING HELD ON 17.01.2018: ================================= 1 CORRECTED AND APPROVED BY B.T.E ON DATED 17.01.2018 STUDY AND EVALUATION SCHEME FOR THREE YEAR(Six Semeter) DIPLOMA COURSE IN PAPER AND PULP TECHNOLOGY (Effective From Session ) I SEMESTER ------------------------------------------------------------------------------------------------------------- Curriculum | | Scheme of Examination | ----------------------| |-----------------------------------------------------| Periods Per Week | S U B J E C T | Theory | Practical |Gra-| ----------------------| |-----------------------|------------------------|nd | Le|Tut|Dr|Lab|Work|Tot| |Examination|Sess.|Total|Examination|Sess.| Total|Tot-| c.|ori|aw| |Shop|al | |----------| Marks|Marks|-----------|Marks| Marks|al | |al | | | | | |Dur.|Marks| | |Dur.| Marks| | | | --|---|--|---|----|---|-------------------------------|----|-----|------|-----|----|------|-----|------|----| -
Household Use of Maritime Resources in 18Th-Century Connecticut
“Providence Brings to our Doors, the Delicious Treasures of the Sea”: Household Use of Maritime Resources in 18th-Century Connecticut Ross K. Harper Abstract Many families in 18th-century Connecticut combined farming and maritime activities in their household economies. While they raised crops and livestock, they also caught fish, harvested shellfish, and hunted waterfowl and game animals in the rivers and along the coastline. Families made salt by boiling seawater in large kettles, used seaweed for fertilizer and insulation, and burned shells to extract lime to make building mortar. Much of this work was done by sharing labor, equipment and boats among family and neighbors. Simple boats, such as dugout canoes and scows, were commonly used. This paper uses archaeological data from five house sites excavated in Connecticut, and a variety of documentary sources, such as probate records, diaries, journals, and newspapers, to reconstruct historic household use of maritime resources. Introduction Connecticut’s inland waterways and off-shore saltwater bodies are known today as recreational beach and sport-fishing areas. Few Connecticut residents now make or supplement their living from maritime resources. But before over-fishing, the damming of rivers, and industrial pollution decimated the state’s fish and shellfish supplies, generations of families relied on Connecticut’s maritime resources for a myriad of uses in everyday life. This paper draws on historical documents and archaeological data derived from the excavation of five buried 18th-century European American sites to examine how colonial families used maritime resources in their household economies. The house-site excavations were conducted by Archaeological and Historical Services, Inc. -
Students, Police Clash
Push Atlantic Highlands Renewal SEE STORY BELOW Weather HOME •Mostly Many and cod today, THEMW Ugh SMt. Clear «oa coot to- night, low Is aid 4h Pair, lit. T Red Bank, Freehold 7" tie milder, tomorrow1! high la FINAL mid Mi. Sunday's outlook, le|r (^ Long Branch J ud seasonable, > MONMOUTH COUNTY'S HOME NEWSPAPER FOR 89 YEARS DIAL 741-0010 VOL 00, NO. 82 RED BANK, N. J., FRIDAY, OCTOBER 20, 1967 10c PER COPY PAGE ONE Middletown Still Hoping to Get New Library By LEE STARNES the complex is built. layout and style of the main library "leave much to be The reading room is exceptionally well stocked with the MIDDLETOWN — The trustees of the township library The township may acquire part or all of an estimated 50- desired." latest magazines and best sellers, but can accommodate three caid yesterday they had very little knowledge of what was acre tract on die north side of Kings Hwy. Mr. Makely headed The library, located on Kings Hwy. is filled to an overflow persons seated and only one person standing. happening-regarding the proposed new library building that the committee that recommended the site. Negotiations are capacity of 15,000 books. Because of the crowded conditions, locating a title in the has become a minor controversy here. being handled by Richard Seuffert, business administrator. "We have to get rid of books because we just can't find • card catalogue, waiting to get through the aisles and locating Committeeman Edward Makely told The Register "every- If the township acquires the plot, 10 acres will be for space for them here," he said. -
SATURDAY, AUGUST 28, 2021 at 10:00 AM
www.reddingauction.com 1085 Table Rock Road, Gettysburg, PA PH: 717-334-6941 Pennsylvania's Largest No Buyers Premium Gun Auction Service Your Professional FireArms Specialists With 127+ Combined Years of Experience Striving to Put Our Clients First & Achieving Highest Prices Realized as Possible! NO RESERVE – NO BUYERS PREMIUM If You Are Interested in Selling Your Items in an Upcoming Auction, Email [email protected] or Call 717- 334-6941 to Speak to Someone Personally. We Are Consistently Bringing Higher Prices Realized Than Other Local Auction Services Due to Not Employing a Buyer’s Premium (Buyer’s Penalty). Also, We Consistently Market Our Sales Nationally with Actual Content For Longer Periods of Time Than Other Auction Services. SATURDAY, AUGUST 28, 2021 at 10:00 AM PLEASE NOTE: -- THIS IS YOUR ITEMIZED LISTING FOR THIS PARTICULAR AUCTION PLEASE BRING IT WITH YOU WHEN ATTENDING Abbreviation Key for Ammo Lots: NIB – New in Box WTOC – Wrapped at Time of Cataloging (RAS Did Not Unwrap the Lots With This Designation in Order to Verify the Correctness & Round Count. We depend on our consignor’s honesty and integrity when describing sealed boxes. RAS Will Offer No Warranties or No Guarantees Regarding Count or the Contents Inside of These Boxes) Any firearms with a “R” after the lot number means it is a registrable firearm. Any firearms without the “R” is an antique & Mfg. Pre-1898 meaning No registration is required. Lot #: 1. Winchester – No. W-600 Caged Copper Room Heater w/Cord – 12½” Wide 16” High w/Gray Base (Excellent Label) 2. Winchester-Western – “Sporting Arms & Ammunition” 16” Hexagon Shaped Wall Clock – Mfg. -
Our Workshop
OUR WORKSHO P : B E I N G A P RACTI CAL GU I DE To TH E AMATEU R ENTRY ANDJ I NE Y OFCAR P O { . P R O FU S ELY I L R AT ED. Y D N E W Y O R ] . ’ T T E 1 30 N A S S A U S T R E E . H O MA S O K AN , C O N TEN TS C H A P . CARP ENTRY AND TH E BENCH H O W TO U S E THE ~ R EMAR H S ON THE S EASONING AND C HOI CE O F THE W OODS V ARIOU S METHODS O F JO I N I N G TIMBER V S IMP LE V O R H S IN W OOD G V P L E TC . ROO ING ANES, MORTISING AND TENONING DOV ETAI LING V ENEER I NG V ARNISHING AND FRENCH P OLISHING A m1 2240 1 O U R W O R K S H O P . D Y CARP ENTRY AN JOINER . obli e d are sorry to be g to admit, that t o enter into a scientific investi gat ion O f the mechanical principles on of C which the art arpentry depends , ul . s o wo d be worse than useless By doing, we w should only be occupying valuable space, ith o u t f imparting instruction, or a fording pleasure f r to many o ou readers . W e in should fail the first, Simply because a m a teu rs would not peru se such unpalatable matter f or so it wou ld be considered by the - of every day reader light literature . -
Frameless Cabinet Construction
Wolverine Brand Cabinetry Econ Line - Frameless Cabinet Specifications Cabinet and Door Design: Overlay doors and drawer fronts with 3/16” reveal Doors and drawers are soft close Wood options are Soft Maple, Red Oak, Knotty Oak, and Cherry in a variety of stain options Painted doors are MDF with 5 paint color options 4 door style options: Richmond, Madison, and Harvest door styles are 2 ¼” frame Reno door style is a slab door Slab drawer fronts – outside profile will match outside profile of door selected Cabinets up to 36” wide have bi-parting doors, no partition or center stile Base Cabinets: 18mm cabinet grade plywood sides, top, and bottom in birch with UV coating and PVC edge-banding ¼” birch plywood back with UV coating and ¾” hanging rail ¾” birch plywood full depth adjustable shelf with metal shelf pins Dovetail joined 5/8” solid maple drawer box with ½” bottom Blum full extension, soft close, under mount drawer slides Blum 3-way adjustable soft close hinges Cabinet sides are ¾” wide loose panels to be installed on site to sit flush with face of door / drawer Wall Cabinets: 18mm cabinet grade plywood sides, top, and bottom in birch with UV coating and PVC edge-banding ¼” birch plywood back with UV coating and ¾” hanging rail ¾” maple plywood full depth adjustable shelf with metal shelf pins Standard 12” deep wall cabinets Blum 3-way adjustable soft close hinges Cabinet sides are ¾” wide loose panels to be installed on site to sit flush with face of door / drawer Wall cabinet bottoms are natural birch . -
Dura Supreme Cabinet Comparison
Dura Supreme Cabinet Comparison Crestwood Designer Bria Alectra 4 Frameless or Frameless or “Full-Access” 3/4” X 1-1/2” Solid Hardwood Face “Full-Access” 6 Construction with 1 Construction Frames with I-Beam Construction Construction with coordinating PVC wood edge banding 2 edge banding 1/2” thick 3/4” thick 3/4” thick 2 End Panels Furniture Board or 1/2” Plywood Furniture Board or Furniture Board or 5 Plywood upgrade Plywood upgrade Plywood upgrade 1/2” thick 3/4” thick 3/4” thick 3 3 Top/Bottom Furniture Board or 1/2” Plywood Furniture Board or Furniture Board or Plywood upgrade Plywood upgrade Plywood upgrade 1 7 1/2” thick 1/4” MDF core 1/4” MDF core Furniture Board or 1/2” Plywood 4 Back with Hanging Rail with Hanging Rail Plywood upgrade Adjustable 3/4” thick 3/4” thick 3/4” thick Crestwood and Designer 5 Furniture Board or 3/4” Plywood Furniture Board or Furniture Board or Shelves Plywood upgrade Plywood upgrade Plywood upgrade Premium 5/8” solid Premium 5/8” solid 5/8” hardwood box 5/8” hardwood Drawer box Maple box with Maple box with 4 with furniture box with furniture dovetailed joints dovetailed joints 6 & Roll-out dovetailed joints dovetailed joints sanded & finished - sanded & finished - Shelves 6 eased top edge eased top edge Blumotion Soft Close Full Extension Undermount Glides Glides for drawers and roll-out shelves 2 7 Toe Kick 4 1/2” High x 3” Recess Finished to Match Maple Woodgrain Maple Woodgrain Maple Woodgrain 5 Cabinet Print or Maple Veneer Print or Print or Interior Maple Veneer with Natural Finish Maple Veneer Maple Veneer 3 with Natural Finish with Natural Finish with Natural Finish 7 Matching Wood Matching Wood Matching Wood Matching Wood 1 Finished Ends Veneer Veneer Veneer Veneer Fully Adjustable Fully Adjustable Fully Adjustable Fully Adjustable with Optional Soft with Optional Soft Hinges with Soft Close with Soft Close Bria and Alectra Close Close ©Dura Supreme Inc. -
Understanding Western Backsaws
Understanding Western Backsaws The Western backsaw has almost vanished. But a few toolmakers are trying to turn back the clock to when this One of the earliest tool catalogs we have, “Smith’s Key,” shows the four types The saw on the bottom is a typical pistol-grip dovetail saw from sawmaker of backsaws available in 1816 from makers in Sheffield, England. Note how Mike Wenzloff of Wenzloff & Sons. Also shown (at top) is a straight-handled saw was in every toolbox. this tool catalog shows the blades as tapered – they are narrower at the toe dovetail saw known as a gent’s saw, so named (we’re told) because it was than at the heel. There’s a likely reason for that. used by gentlemen hobbyist woodworkers in the 19th century. Why Use Western Handsaws? For some woodworkers, the above reasons blade is straight up and down. However, using The backsaws that built nearly every piece of If you do the math, mass-produced high-qual- are a compelling reason to use Western saws. a straight-handled “gent’s saw” isn’t difficult. It antique English and American furniture almost ity Japanese saws are a bargain. You can buy a If you are one of those, read on. If you still pre- just takes a little more getting used to. became extinct, thanks to the universal motor and Japanese dovetail saw for $35 that works just as fer Japanese saws and want to learn more about The teeth of a dovetail saw are quite fine, the Japanese obsession with quality. -
Demystifying the Traditional Backsaw © 2014, by Mark D
Demystifying the Traditional Backsaw © 2014, by Mark D. Harrell Introduction Introduction Talking Points • Is it worth saving? • Disassembly • Cleaning • Handle Work • Reassembly & retensioning • Truing up • Clock-sharpening • Safety • The Continuum of a Toothline Is it worth saving? • Pitting (know when it’s too bad • Badly bent sawbacks • Handle repair (you be the judge) • Sentimental value • Handsaw flex test 9 times out of ten, the traditional folded sawback saves the saw Disassembly • Leather-lined wood clamp • Angle iron • 12” mill file • Sharpening files • Dead-blow mallet • Stout screwdriver • Small crowbar • Ruler • Sharpie • Brass hammer • Leather patches • Canning wax • Whetstone • Masking tape • Stout vise These are tools you’ll likely have in your shop already Disassembly (cont.) Step 1: this is how we get our frozen nuts off in Wisconsin. It doesn’t even have to be winter. Disassembly (cont.) Step 2: lay your handle aside—secure your fasteners inside the pistol grip so they don’t get lost. Disassembly (cont.) Step 3: cinch your plate/back assembly into a your leather-lined angle iron and pry of back with crowbar. “Warning, Will Robinson! don’t do this with static backs!” Disassembly (cont.) Step 3a: know the difference between a static back and a traditional folded back—again, don’t attempt to pull off a static-back or you’ll ruin your saw. More on this later. Disassembly (cont.) Step 4: repeat this procedure gradually, then pull off back. Disassembly (cont.) Completely disassembling a traditional backsaw is no different than disassembling a hand plane; easier, in fact. Typical Cleaning Supplies (what Bad Axe Uses, anyway!) • Sunshine Polishing cloths • 3M Abrasive Pads • Cordless Dremel • Sandflex Eraser blocks • Plastic Safety Razor • Brass toothbrush • Dental Pick • Exacto Knife • Wizard's Power Seal • Nitrile Gloves • Spraybees • Wizard's Metal • Renew • Dust mask(s) & safety goggles • Dry t-shirt/cloth diaper cloth • Your child's old toothbrush. -
CX202 10” CONTRACTORS TABLE SAW with RIVING KNIFE User Manual
CX202 10” CONTRACTORS TABLE SAW WITH RIVING KNIFE User Manual TABLE OF CONTENTS General Safety Instructions ..................................................................................... 3 Specific Safety Instructions ..................................................................................... 4 CX202 Features ...................................................................................................... 5 Physical Features ................................................................................................... 6 Set Up ..................................................................................................................... 7 Un-Packing & Inventory .......................................................................................... 7 Proper Grounding ................................................................................................... 8 Assembly ................................................................................................................ 9 Installing the Saw Blade .......................................................................................... 12 Blade Guard Spreader ............................................................................................ 13 Table Insert ............................................................................................................. 13 Installing the Blade Guard ....................................................................................... 13 Basic Controls ........................................................................................................ -
Section 400: Architectural Cabinets
Standing & Running Trim Section 300 ARCHITECTURAL CABINETS ARCHITECTURAL 300 SECTION © 2003 AWI/AWMAC - 8th Edition Quality Standards 400 116 Architectural Cabinets Section 400 Architectural Cabinets Architectural Cabinets Section 400 Section 400 Section 400 Selection and Specification Checklist Because most architecture, specification, and design firms have electronic master specifications in place, the AWI and AWMAC offer this quick checklist. A review of these items may help the design and specification team issue a complete and accurate contract document and avoid missing things vital to the successful completion of the project. The checklists are not considered a part of the Quality Standards for the purposes of compliance. Part 1. GENERAL 1.1. REFERENCES A. AWI/AWMAC Quality Standards Illustrated (QSI), current edition 1.2 SUBMITTALS A. Shop drawings: • Submit two copies; one of which will be returned with reviewed notations prior to commencement of work under this section. • Indicate plans and elevations, materials, surface grain directions, profiles, assembly methods, joint details, fastening methods, accessories, hardware, compliance with specified fire-retardant treatments, preservative treatments, and 400 schedule of finishes. 400 B. Finish samples: • When appropriate, submit one or more samples of veneer-on-substrate, 200 x 250 mm [8 x 10"] illustrating expected range of component finish color and/or grain. • When appropriate, submit one or more samples of solid lumber, 300 square centimeters [50 square inches] illustrating expected range of component finish color and/or grain. • The sample shall bear identification of the project, architect or designer, general contractor, woodwork manufacturer, items to which the finish applies and the system utilized to attain the finish. -
1. Hand Tools 3. Related Tools 4. Chisels 5. Hammer 6. Saw Terminology 7. Pliers Introduction
1 1. Hand Tools 2. Types 2.1 Hand tools 2.2 Hammer Drill 2.3 Rotary hammer drill 2.4 Cordless drills 2.5 Drill press 2.6 Geared head drill 2.7 Radial arm drill 2.8 Mill drill 3. Related tools 4. Chisels 4.1. Types 4.1.1 Woodworking chisels 4.1.1.1 Lathe tools 4.2 Metalworking chisels 4.2.1 Cold chisel 4.2.2 Hardy chisel 4.3 Stone chisels 4.4 Masonry chisels 4.4.1 Joint chisel 5. Hammer 5.1 Basic design and variations 5.2 The physics of hammering 5.2.1 Hammer as a force amplifier 5.2.2 Effect of the head's mass 5.2.3 Effect of the handle 5.3 War hammers 5.4 Symbolic hammers 6. Saw terminology 6.1 Types of saws 6.1.1 Hand saws 6.1.2. Back saws 6.1.3 Mechanically powered saws 6.1.4. Circular blade saws 6.1.5. Reciprocating blade saws 6.1.6..Continuous band 6.2. Types of saw blades and the cuts they make 6.3. Materials used for saws 7. Pliers Introduction 7.1. Design 7.2.Common types 7.2.1 Gripping pliers (used to improve grip) 7.2 2.Cutting pliers (used to sever or pinch off) 2 7.2.3 Crimping pliers 7.2.4 Rotational pliers 8. Common wrenches / spanners 8.1 Other general wrenches / spanners 8.2. Spe cialized wrenches / spanners 8.3. Spanners in popular culture 9. Hacksaw, surface plate, surface gauge, , vee-block, files 10.