LED Lighting in Museums: Conservation and Color of Textiles
Total Page:16
File Type:pdf, Size:1020Kb
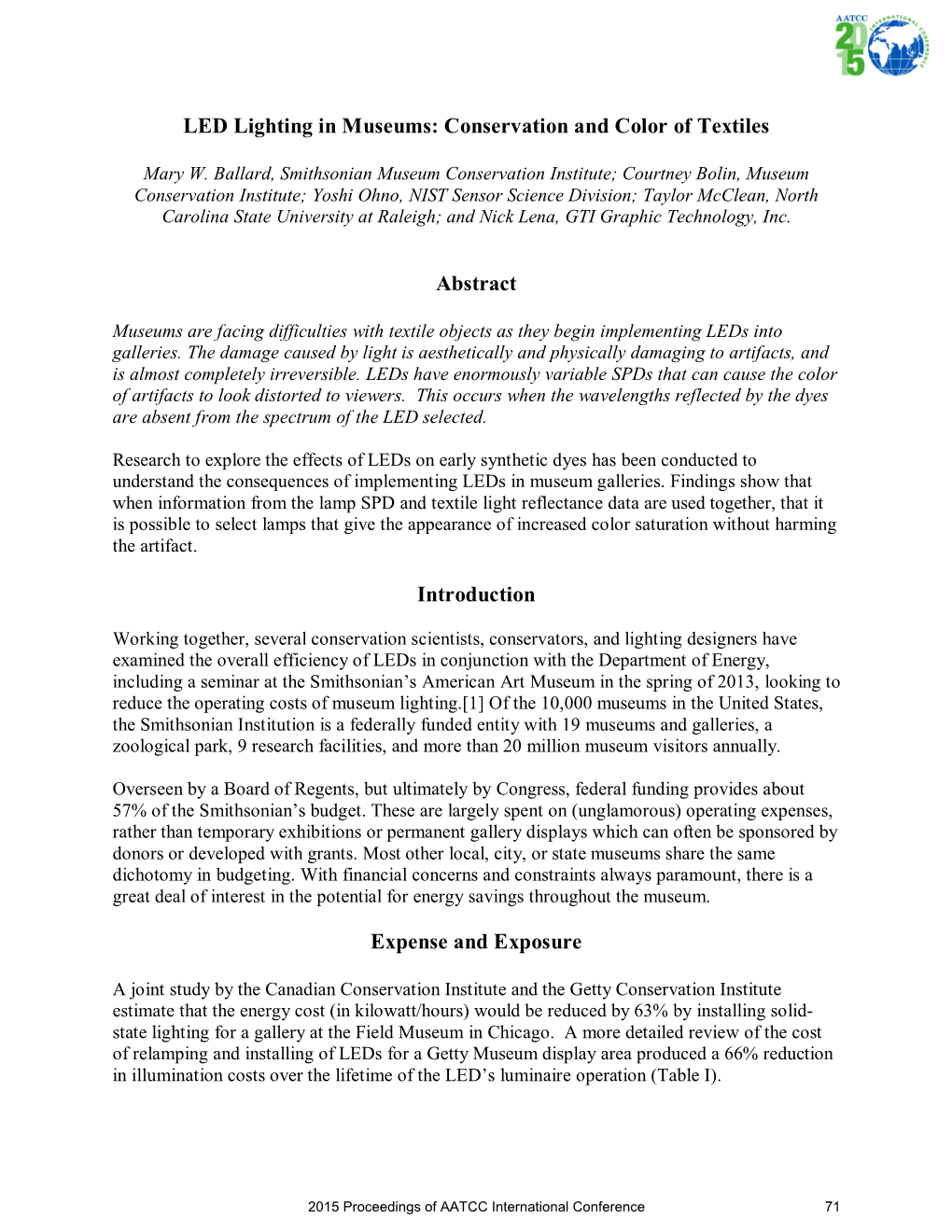
Load more
Recommended publications
-
Review of Measures for Light-Source Color Rendition and Considerations for a Two-Measure System for Characterizing Color Rendition
Review of measures for light-source color rendition and considerations for a two-measure system for characterizing color rendition Kevin W. Houser,1,* Minchen Wei,1 Aurélien David,2 Michael R. Krames,2 and Xiangyou Sharon Shen3 1Department of Architectural Engineering, The Pennsylvania State University, University Park, PA, 16802, USA 2Soraa, Inc., Fremont, CA 94555, USA 3Inno-Solution Research LLC, 913 Ringneck Road, State College, PA 16801, USA *[email protected] Abstract: Twenty-two measures of color rendition have been reviewed and summarized. Each measure was computed for 401 illuminants comprising incandescent, light-emitting diode (LED) -phosphor, LED-mixed, fluorescent, high-intensity discharge (HID), and theoretical illuminants. A multidimensional scaling analysis (Matrix Stress = 0.0731, R2 = 0.976) illustrates that the 22 measures cluster into three neighborhoods in a two- dimensional space, where the dimensions relate to color discrimination and color preference. When just two measures are used to characterize overall color rendition, the most information can be conveyed if one is a reference- based measure that is consistent with the concept of color fidelity or quality (e.g., Qa) and the other is a measure of relative gamut (e.g., Qg). ©2013 Optical Society of America OCIS codes: (330.1690) Color; (330.1715) Color, rendering and metamerism; (230.3670) Light-emitting diodes. References and links 1. CIE, “Methods of measuring and specifying colour rendering properties of light sources,” in CIE 13 (CIE, Vienna, Austria, 1965). 2. W. Walter, “How meaningful is the CIE color rendering index?” Light Design Appl. 11(2), 13–15 (1981). 3. T. Seim, “In search of an improved method for assessing the colour rendering properties of light sources,” Lighting Res. -
Comparing Measures of Gamut Area
Comparing Measures of Gamut Area Michael P Royer1 1Pacific Northwest National Laboratory 620 SW 5th Avenue, Suite 810 Portland, OR 97204 [email protected] This is an archival copy of an article published in LEUKOS. Please cite as: Royer MP. 2018. Comparing Measures of Gamut Area. LEUKOS. Online Before Print. DOI: 10.1080/15502724.2018.1500485. PNNL-SA-132222 ▪ November 2018 COMPARING MEASURES OF GAMUT AREA Abstract This article examines how the color sample set, color space, and other calculation elements influence the quantification of gamut area. The IES TM-30-18 Gamut Index (Rg) serves as a baseline, with comparisons made to several other measures documented in scientific literature and 12 new measures formulated for this analysis using various components of existing measures. The results demonstrate that changes in the color sample set, color space, and calculation procedure can all lead to substantial differences in light source performance characterizations. It is impossible to determine the relative “accuracy” of any given measure outright, because gamut area is not directly correlated with any subjective quality of an illuminated environment. However, the utility of different approaches was considered based on the merits of individual components of the gamut area calculation and based on the ability of a measure to provide useful information within a complete system for evaluating color rendition. For gamut area measures, it is important to have a reasonably uniform distribution of color samples (or averaged coordinates) across hue angle—avoiding exclusive use of high-chroma samples—with sufficient quantity to ensure robustness but enough difference to avoid incidents of the hue-angle order of the samples varying between the test and reference conditions. -
E GE Enhanced Color Lamps
e GE Enhanced Color Lamps TRANSFORM YOUR BUSINESS... WITH THE CHANGE OF A LIGHT BULB GE enhanced GE ENHANCED color lighting can... ■ Render colors in a natural way. COLOR LIGHTING ■ Highlight and accent objects as never before. ■ Allow you to choose light sources that enhance colors, giving furnishings, merchandise and even people a rich, vibrant look. CAN TRANSFORM ■ Give your surroundings a “warm” or “cool” tone, or somewhere in between. ■ Provide a pleasing light that improves visual A FACILITY FROM appeal, enhances productivity and overall satisfaction of the occupants of the space. ■ Permit more accurate determination of THE ORDINARY color differences. In addition to color enhancement, many of these GE products can also significantly reduce your energy costs and save lamp INTO THE replacement and labor costs. Evaluating light source color. EXTRAORDINARY. Two common ways of specifying light source color are: color temperature and color rendering index. Color Temperature indicates the atmosphere created WITH THE SIMPLE by the light source. • The higher the color temperature, the “cooler” the color. • Color temperatures... – Of 2000K-3000K create a “warm” atmosphere. CHANGE OF A – Above 4000K are “cool” appearance. – Between 3000K and 4000K are considered intermediate and tend to be preferred. LIGHT BULB, YOUR Color Rendering Index (CRI) rates a light source’s ability to render colors in a natural and normal way, based on a scale from 0 to 100. • In general, light sources with high CRI (80-100) BUSINESS CAN will make people and things look better than those with lower CRIs. TAKE ON A VIBRANT NEW LOOK. Color Rendering and 7000K Overcast C75 Sky Color Temperature Starcoat™ The chart at right shows both dimensions of light source SP65 SP65 color—color temperature and color rendering—for the most popular light sources. -
Optimizing Color Rendering Index Using Standard Object Color Spectra Database and CIECAM02
Optimizing Color Rendering Index Using Standard Object Color Spectra Database and CIECAM02 Pei-Li Sun Department of Information Management, Shih Hsin University, Taiwan Abstract is an idea reference for developing new CRIs. On the As CIE general color rending index (CRI) still uses other hand, CIE TC8-01 recommended CIECAM02 obsolete color space and color difference formula, it color appearance model for cross-media color 3 should be updated for new spaces and new formulae. reproduction. As chromatic adaptation plays an * * * The aim of this study is to optimize the CRI using ISO important role on visual perception, U V W should standard object color spectra database (SOCS) and be replaced by CIECAM02. However, CIE has not yet CIECAM02. In this paper, proposed CRIs were recommended any color difference formula for 3 optimized to evaluate light sources for four types of CIECAM02 applications. The aim of this study is object colors: synthetic dyes for textiles, flowers, paint therefore to evaluate the performance of proposed (not for art) and human skin. The optimization was CRI based on the SOCS and CIECAM02. How to based on polynomial fitting between mean color evaluate its performance also is a difficult question. variations (ΔEs) and visual image differences (ΔVs). The answer of this study is to create series of virtual TM The former was calculated by the color differences on scene using Autodesk 3ds Max to simulate the color SOCS’s typical/difference sets between test and appearance of real-world objects under test reference illuminants. The latter was obtained by a illuminants and their CCT (correlated color visual experiment based on four virtual scenes under temperature) corresponding reference lighting 15 different illuminants created by Autodesk 3ds Max. -
Better Colour Rendering Offers Many Benefits
TYRI CASE STUDY BETTER COLOUR RENDERING OFFERS MANY BENEFITS Caravan Mill provides its environment. The result was both customers with gravel and better working conditions and sand which they refine “ increased productivity. ...Drivers have a hard time dealing from blasted stone. A job with the big differences between that requires precision and “For us, good lighting is primarily a white bright light from the headlights work environment and safety issue. powerful machines. The work and the dark environment next to the We work long days and for large environment is dusty and often machine. parts of the year it is dark both in dark so the lighting on their the morning and in the afternoons. machines is crucial for both the ...With TYRI´s new work lights, it Drivers have a hard time dealing with employee’s health and safety the big differences between white has become much better. Today, we as well as the productivity at bright light from the headlights have significantly better lighting that work. and the dark environment next makes our drivers feel better and to the machine. When the eye is To meet the challenges of with that, safety and productivity forced to switch between white light reflections, color rendering and increases.” and darkness for many hours, the a safe work environment for the consequence is often headaches - Pierre Jakobsson, Caravan Mill. operators, TYRI has spent four and fatigue. With TYRI´s new work years developing a LED work light lights, it has become much better. that now measures 90-95 CRI Today, we have significantly better (color rendering index). -
Development of the IES Method for Evaluating the Color Rendition of Light Sources
Development of the IES method for evaluating the color rendition of light sources Aurelien David Paul T. Fini Kevin W. Houser Yoshi Ohno Michael P. Royer Kevin A.G. Smet Minchen Wei Lorne Whitehead We have developed a two-measure system for evaluating light sources’ color rendition that builds upon conceptual progress of numerous researchers over the last two decades. The system quantifies the color fidelity and color gamut (i.e. change in object chroma) of a light source in comparison to a reference illuminant. The calculations are based on a newly developed set of reflectance data from real samples uniformly distributed in color space (thereby fairly representing all colors) and in wavelength space (thereby precluding artificial optimization of the color rendition scores by spectral engineering). The color fidelity score Rf is an improved version of the CIE color rendering index. The color gamut score Rg is an improved version of the Gamut Area Index. In combination, they provide two complementary assessments to guide the optimization of future light sources and allow lighting specifiers to appropriately match sources with applications. 1. Introduction Limitations of the general color rendering index (CRI) [CIE95], developed by the International Lighting Commission (CIE), have been extensively documented [e.g., Worthey03, CIE07, DiLaura11]. Despite many past efforts to develop complimentary or alternative ways for evaluating light sources’ color rendition1 [Guo04, Smet11b, Houser13b], a suitable alternative has not yet been widely adopted; efforts by the CIE to revise the CRI in the 1980s-90s did not succeed [CIE99]. Yet, with the proliferation of solid- state lighting—a family of light sources with tremendous opportunities for spectral engineering and optimization—the need for a method to evaluate color rendition is greater than ever [Houser13a]. -
Xenolux LED Headlights Brochure
LED HL70 XENALUX LED HL30 Headlights XenaLux™ and LED HL70 & HL30 Comfortable, lightweight, high quality headlights that help you go the distance. Headlights Headlights XenaLux™ LED HL70 & HL30 (Xenon Lamp Illuminator) • 225,000 lux at 16" (40.64 cm) diameter • Adjustable light field diameter • 300 Watt Illuminator Headlamp Features: • Extremely bright light at working distance • Variable spot with flawless circular beam • Very light weight, right angle headlamp • Preferred for comfort • Compact optical system • Fully-adjustable, uniquely-designed linkage arm allows for vertical adjustment of the optical module • Wolf port fitting provided on fiber optic cable • Rear cranial headband support improves comfort along with front to back crown support, providing superior light module adjustment and stable placement • Headband construction diminishes fatigue that occurs in extended surgical procedures Illuminator Features: • Produces highest intensity white light of any 300 Watt Xenon source LED HEADLIGHT HL70 LED HEADLIGHT HL30 • Quiet, cool venting system (Battery on Belt Holster) (Battery on Headlight) • Rotary turret for Wolf, Storz, Olympus, ACMI • For Pilling port in Rotary Turret, contact • 30,000 lux at 16" (40.64 cm) diameter • 70,000 lux at 16" (40.64 cm) diameter Burton Customer Service • Adjustable light field diameter • Variable light output control • Adjustable light field diameter • Battery life 2.5 hours at max light output • Battery life 2.5 hours at max light output • Dimensions: 5" (12.7 cm) x 10" (25.4 cm) x 14" (35.5 cm) -
Spectral Design Considerations for White LED Color Rendering
Optical Engineering 44͑11͒, 111302 ͑November 2005͒ Spectral design considerations for white LED color rendering Yoshi Ohno Abstract. White LED spectra for general lighting should be designed for National Institute of Standards and Technology high luminous efficacy as well as good color rendering. Multichip and 100 Bureau Drive phosphor-type white LED models were analyzed by simulation of their Gaithersburg, Maryland 20899 color characteristics and luminous efficacy of radiation, compared with E-mail: [email protected] those of conventional light sources for general lighting. Color rendering characteristics were evaluated based on the CIE Color Rendering Index ͑CRI͒, examining not only Ra but also the special color rendering indices ⌬ * Ri, as well as on the CIELAB color difference Eab for the 14 color samples defined in CIE 13.3. Several models of three-chip and four-chip white LEDs as well as phosphor-type LEDs are optimized for various parameters, and some guidance is given for designing these white LEDs. The simulation analysis also demonstrated several problems with the current CRI, and the need for improvements is discussed. © 2005 Society of Photo-Optical Instrumentation Engineers. ͓DOI: 10.1117/1.2130694͔ Subject terms: color rendering; colorimetry; CRI; lighting; luminous efficacy; solid- state lighting; LED; white LED. Paper SS040576 received Aug. 24, 2004; accepted for publication Jun. 13, 2005; published online Nov. 30, 2005. This paper is a revision of a paper presented at the SPIE conference on Solid State Lighting, Aug. 2004, Denver, Colorado. The paper presented there appears ͑unrefereed͒ in SPIE Proceedings Vol. 5530. 1 Introduction The main driving force for solid-state lighting is the po- tential of huge energy savings on the national or global One of the most important characteristics of light sources scale.6 Thus, when considering spectra of light sources for for general lighting is color rendering. -
CB Training Lighting
Third-Party Certification Training for EPA-Recognized Lighting Certification Bodies Kathleen Vokes and Alex Baker ENERGY STAR® Labeling Branch December 3, 2010 (Updated pages 7-19 for accuracy/clarity on December 13, 2010) Farragut Center, Washington, DC Training Design • Training addresses existing lighting specifications and EPA-recognized CB requirements • Training also informs CBs of near term specification changes and key implications ENERGY STAR Lighting Specifications Today Near Future (2011-2012) Residential Light Fixtures (RLF) Luminaires SSL Luminaires CFLs Lamps Integral LED Lamps Decorative Light Strings (DLS) Decorative Light Strings 2 Today’s Agenda • Lab Accreditation and Recognition by EPA • Product Certification • Private Labeling • Verification Testing • Common Problems with Lighting Submissions • Upcoming Specification Changes 3 Lab Accreditation and Recognition by EPA 4 Category Approach to EPA- Recognized Laboratories • Category Approach: Defined groups of test methods (mainly photometric) relevant to a category/specification – Lighting Categories: Recognize labs for a lighting category, based on a defined group of test methods required in a specification – Component Categories: Ballasts, Lamps and LED Package, Module or Array will need to be tested and labs will be recognized based on relevant test(s) 5 Category Approach to EPA- Recognized Laboratories (cont.) • Categories do not include EVERY test in a specification • Test reports may come from multiple EPA-recognized labs • EPA-recognized CBs must verify that all relevant test reports come from an EPA-recognized lab • EPA-recognized CBs use specifications to identify additional test reports/information (e.g., safety, warranty, product labeling) a partner needs to submit to determine if a product qualifies as ENERGY STAR 6 Lab Recognition by Lighting Category • The purpose of the following slides is to clarify for laboratories, ABs, and CBs the test methods to which a laboratory must be accredited to gain EPA recognition for testing one or more lighting product types. -
Surgical Lights SURGICAL LIGHTS • • • • • • • • • • • • • FHC Iceledsurgicallight • • • • • • • • • • • • • FHC Miraledsurgicallight
Surgical Lights FHC iCE LED Surgical Light • Illuminance: available in 160,000, and 130,000 lux • Color Temperature: 4500°K • Diameter of Lighthead: 30in. and 25in. (for iCE 25 LED) • Light Field Diameter: 7.6 - 12” (7.5-11” for iCE 25 LED) • Focusing: Adjustable by rotating focus handle • CRI (Color Rendering Index): 95 • Rotation: 360° (limitless) on single ceiling models • Sterilizable Handle: Removable • Number of Bulbs: 80 main (52 main for iCE 25 LED) • Light Source: LED • Rated life of LED Lamp: 50,000 hours • Mounting Options: ceiling, wall AML-ILED-30 • Warranty: 5 year limited warranty The iCE LED Surgical Lighting System brings the newest LED technology to the Operating Room. The iCE LED Surgical Lights are designed for superior shadow control, increased depth of field and light intensity. The iCE Surgical Lighting System comes standard with an in-light HD camera. Each iCE LED is upgradable and customizable and can be ordered in a variety of configurations. FHC Mira LED Surgical Light • Illuminance: available in 50,000, 65,000, and 90,000 lux • Color Temperature: 4500°K • Diameter of Lighthead: 18” • Light Field Diameter: 6.5 - 12” • Focusing: Twist handle • CRI (Color Rendering Index): 95 • Rotation: 360° (limitless) on single ceiling models • Sterilizable Handle: Removable AML-MLED-65 • Number of Bulbs: 36 • Light Source: LED • Rated life of LED Lamp: 50,000 hours • Mounting Options: ceiling, wall, or roll stand As the latest advancement in minor surgery and diagnostic lighting technology, the Mira Series LED • Warranty: 5 year limited warranty Surgical Light’s precisely positioned LED’s ensure superior shadow control, depth of field, and light intensity. -
Class a Color Classification for Light Sources Used in General Illumination
www.lrc.rpi.edu/programs/solidstate/assist/recommends/lightcolor.asp www.lrc.rpi.edu/programs/solidstate/assist/whitelight.asp Class A Color Classification for Light Sources Used in General Illumination Mark Rea, PhD Jean Paul Freyssinier October 2012 © 2012 Rensselaer Polytechnic Institute. All rights reserved. www.lrc.rpi.edu/programs/solidstate/assist/recommends/lightcolor.asp www.lrc.rpi.edu/programs/solidstate/assist/whitelight.asp Introduction Color rendering and the color of illumination are two key factors that support architectural lighting (e.g., retail lighting). However, presently accepted metrics used to describe color properties (CRI and CCT) often are not perfectly predictive of people’s assessments of illumination from a light source. Amerlux Amerlux photos.com 2 © 2012 Rensselaer Polytechnic Institute. All rights reserved. www.lrc.rpi.edu/programs/solidstate/assist/recommends/lightcolor.asp www.lrc.rpi.edu/programs/solidstate/assist/whitelight.asp Color Rendering of Illumination © 2012 Rensselaer Polytechnic Institute. All rights reserved. www.lrc.rpi.edu/programs/solidstate/assist/recommends/lightcolor.asp www.lrc.rpi.edu/programs/solidstate/assist/whitelight.asp Basic issues CRI is used almost exclusively for color rendering January 2004 survey of 242 lighting professionals http://www.lrc.rpi.edu/programs/nlpip/lightinganswers/lightsources/abstract.asp 4 © 2012 Rensselaer Polytechnic Institute. All rights reserved. www.lrc.rpi.edu/programs/solidstate/assist/recommends/lightcolor.asp www.lrc.rpi.edu/programs/solidstate/assist/whitelight.asp Color rendering index (CRI) Measure of the degree of color shift objects undergo when illuminated by CRI = 90 the light source as compared with the color of those same objects when illuminated by a CRI = 70 reference source of comparable color temperature. -
Efficacy, Color Rendering, and Color Temperature by Uwe Happek
Basics of Lighting: Efficacy, Color Rendering, and Color Temperature by Uwe Happek f you are environmentally conscious, or value around 10 lm/W. Increasing the temperature of a black simply thrifty, you probably would have body source improves the efficacy; at T = 6,620 K we reach I replaced your incandescent lamps (the 95 lm/W for the simple fact that the peak of the emission Edison type) with more efficient devices. (If spectrum moves into the range of human vision. As a reference you happen to live in Europe, you cannot even buy the point, sunlight gives, on a clear day, 93 lm/W. incandescent any more!) What you are looking for when Fluorescent lighting and solid state lamps (LED- or OLED- deciding on a new lamp is the “luminous efficacy,” measured based) can achieve higher values by emitting distinct bands in lumens/watt. We know what a watt is: it is the unit of in the blue, green, and red region, without significant power, a well-defined physical property, given in absorbed radiation outside of the human eye’s response. By adjusting or emitted energy per time, measured in joules per second. the relative ratio of the spectral components, we can achieve Lumens are a different matter; here the human comes into the perception of sun light or incandescent lamps. Fluorescent the picture: lumen is the unit of luminous flux, which is a lamps can reach 100 lm/W, experimental versions of solid measure of the human eye’s signal level sent to the brain, or state lighting are in the range of 150 lm/W.