1 Pre-Disaster Events and Conditions Contributing to the Crandall
Total Page:16
File Type:pdf, Size:1020Kb
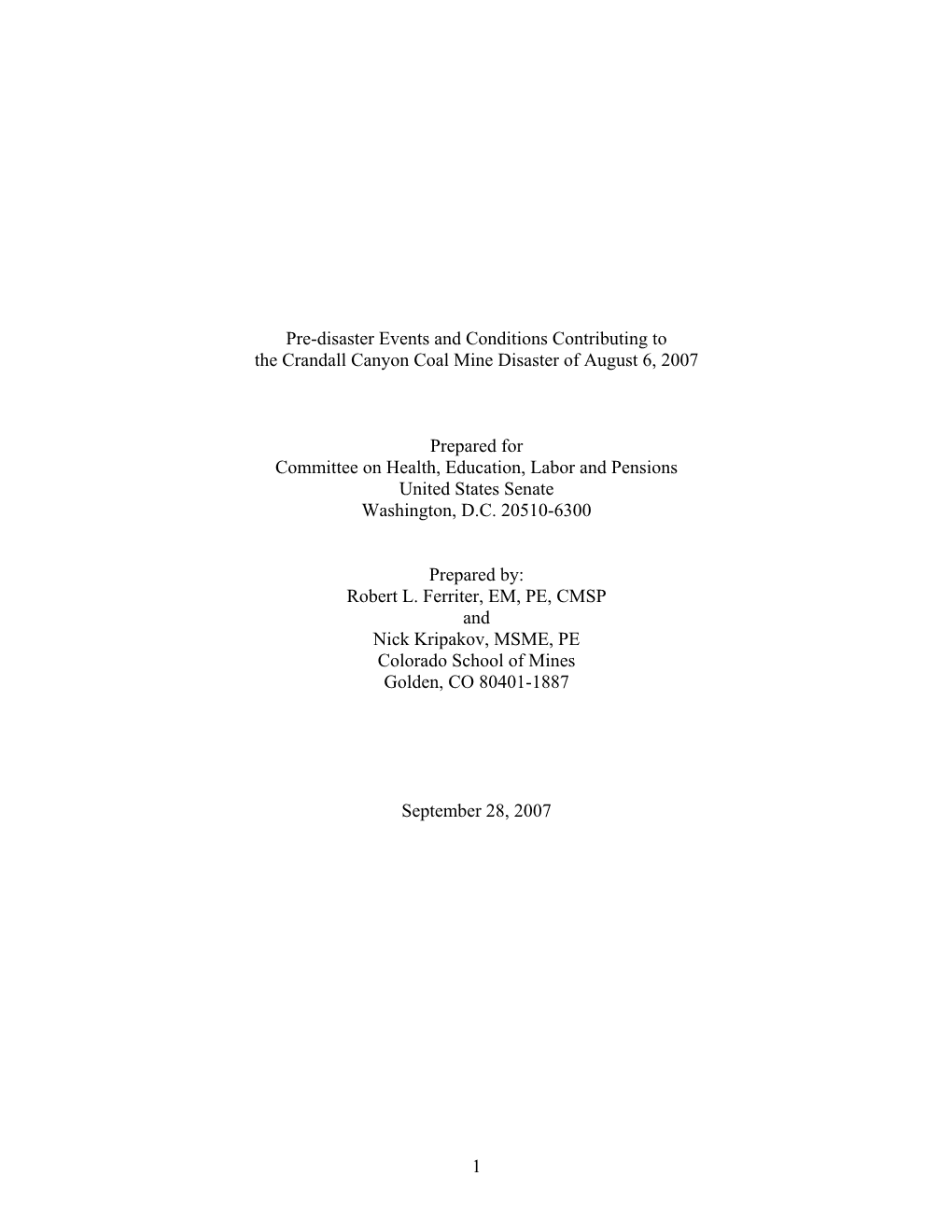
Load more
Recommended publications
-
In the Supreme Court of Ohio
Supreme Court of Ohio Clerk of Court - Filed February 23, 2015 - Case No. 2015-0127 IN THE SUPREME COURT OF OHIO ROBERT E. MURRAY, et al., : Ohio Supreme Court Case No. 15-0127 : Plaintiffs-Appellants, : : v. : On appeal from Cuyahoga County Court of : Appeals, Eighth Appellate District THE CHAGRIN VALLEY PUBLISHING : COMPANY, et al., : Court of Appeals Case No. 101394 : Defendants-Appellees. : : MEMORANDUM IN RESPONSE TO APPELLANTS’ MEMORANDUM IN SUPPORT OF JURISDICTION OF APPELLEES THE CHAGRIN VALLEY PUBLISHING COMPANY; H. KENNETH DOUTHIT, III; TODD NIGHSWONGER; DAVID C. LANGE; DOUTHIT COMMUNICATIONS, INC.; SALI A. MCSHERRY; AND RON HILL J. MICHAEL MURRAY (0019626) (COUNSEL OF RECORD) [email protected] LORRAINE R. BAUMGARDNER (0019642) [email protected] BERKMAN, GORDON, MURRAY & DeVAN 55 Public Square, Suite 2200 Cleveland, OH 44113 (216) 781-5245 / (216) 781-8207 (facsimile) Attorneys for Defendants-Appellees The Chagrin Valley Publishing Company, H. Kenneth Douthit, III, Todd Nighswonger, David C. Lange, Douthit Communications, Inc., Sali A. McSherry, and Ron Hill Mark S. Stemm (0023146) (COUNSEL OF RECORD) [email protected] L. Bradfield Hughes (0070997) [email protected] PORTER WRIGHT MORRIS & ARTHUR LLP 41 South High Street, Suite 3200 Columbus, Ohio 43215 (Continued) J. Philip Calabrese (0072709) [email protected] Tracy S. Francis (0080879) [email protected] PORTER WRIGHT MORRIS & ARTHUR LLP 950 Main Avenue, Suite 500 Cleveland, Ohio 44113 Kevin Anderson, pro hac vice PHV Registration No. 3507-2015 Ohio Admission Pending (0092847) [email protected] FABIAN & CLENDENIN, PC 215 South State Street, Suite 1200 Salt Lake City, Utah 84111 Michael O. McKown (0013378) [email protected] Gary M. Broadbent (0083876) [email protected] 46226 National Road St. -
Robert C. Byrd Miner Safety and Health Act of 2010
111TH CONGRESS REPT. 111–579 " ! 2d Session HOUSE OF REPRESENTATIVES Part 1 ROBERT C. BYRD MINER SAFETY AND HEALTH ACT OF 2010 JULY 29, 2010.—Committed to the Committee of the Whole House on the State of the Union and ordered to be printed Mr. GEORGE MILLER of California, from the Committee on Education and Labor, submitted the following R E P O R T together with SUPPLEMENTAL AND MINORITY VIEWS [To accompany H.R. 5663] [Including cost estimate of the Congressional Budget Office] The Committee on Education and Labor, to whom was referred the bill (H.R. 5663) to improve compliance with mine and occupa- tional safety and health laws, empower workers to raise safety con- cerns, prevent future mine and other workplace tragedies, establish rights of families of victims of workplace accidents, and for other purposes, having considered the same, report favorably thereon with an amendment and recommend that the bill as amended do pass. The amendment is as follows: Strike all after the enacting clause and insert the following: SECTION 1. SHORT TITLE; TABLE OF CONTENTS. (a) SHORT TITLE.—This Act may be cited as the ‘‘Robert C. Byrd Miner Safety and Health Act of 2010’’. (b) TABLE OF CONTENTS.—The table of contents for this Act is as follows: Sec. 1. Short title; table of contents. Sec. 2. References. TITLE I—ADDITIONAL INSPECTION AND INVESTIGATION AUTHORITY Sec. 101. Independent accident investigations. Sec. 102. Subpoena authority and miner rights during inspections and investigations. Sec. 103. Designation of miner representative. Sec. 104. Additional amendments relating to inspections and investigations. -
Democrats Content to Let Gonzales Twist in Wind
MN_A_8_A8_LA_1_08-07-07_tu_2_CMYK 2007:08:06:23:30:19_ A8 TUESDAY, AUGUST 7, 2007 , LOS ANGELES TIMES THE NATION Desperate effort to aid miners A predawn collapse Trapped underground trapped 6 men 1,500 Hundreds of rescuers dug through a collapsed underground shaft Monday in an attempt to rescue six feet underground in a miners trapped in a Utah coal mine. Here’s an approximate boundary of the Crandall Canyon Mine: Utah coal mine. Provo 191 Detailed NEV. By Ashley Powers UTAH CALIF. and Janet Wilson Price Times Staff Writers Huntington Electric Lake UTAH Reservoir 6 huntington, utah — Res- cuers drilled and smashed Cleveland through solid rock Monday in an Reservoir Miners attempt to reach six coal miners trapped 31 Huntington trapped deep underground by a Miller Flat 10 15 MILES massive predawn cave-in. Reservoir 29 Searchers said they were within 1,700 feet of the miners but their initial approach failed. Workers could not contact the miners. Authorities were uncer- tain whether the men were still Miners trapped 1,500 Mine entrance alive. feet below ground A top mining company official said the collapse was caused by 31 an earthquake, but seismolo- gists said they suspected the re- Main shaft verse. Company officials and hun- Rescuers dig dreds of workers at the Crandall through cave-in Canyon Mine — 140 miles south of Salt Lake City — focused on trying to reach the six men, who were believed to be about 1,500 feet below the surface and 3.4 miles from the mine entrance. Mine rescue teams from around Utah were arriving Mon- day night as other miners, ex- Digital image from Google Earth hausted and covered in black Retreat mining dust, promised to return after a The miners may have been using a technique called retreat mining, which involves gleaning the coal in few hours’ sleep. -
Msha Could Not Show It Made the Right Decision in Approving the Roof Control Plan at Crandall Canyon Mine
MINE SAFETY AND HEALTH ADMINISTRATION MSHA COULD NOT SHOW IT MADE THE RIGHT DECISION IN APPROVING THE ROOF CONTROL PLAN AT CRANDALL CANYON MINE Office of Inspector General—Office Audit Date: March 31, 2008 Report Number: 05-08-003-06-001 U.S. DEPARTMENT OF LABOR March 2008 Office of Inspector General Office of Audit WHAT OIG FOUND MSHA was negligent in carrying out its BRIEFLY… responsibilities to protect the safety of miners. Specifically, MSHA could not show that it made the Highlights of Report Number: 05-08-003-06-001, right decision in approving the Crandall Canyon MSHA Could Not Show It Made the Right Decision Mine roof control plan or that the process was free In Approving the Roof Control Plan At Crandall from undue influence by the mine operator. MSHA Canyon Mine, to the Assistant Secretary for Mine did not have a rigorous, transparent review and Safety and Health, dated March 31, 2008. approval process for roof control plans consisting of explicit criteria and plan evaluation factors, WHY READ THE REPORT appropriate documentation, and active oversight In August 2007, "a major coal bump/bounce" and supervision by Headquarters and District 9 occurred in the Crandall Canyon Mine (Emery management. Further, MSHA did not ensure that County, Utah) precipitating a tragedy in which nine subsequent inspections assessed compliance men lost their lives: six miners, and three rescue with, and the effectiveness of, approved plans in workers who died attempting to save the miners. continuing to protect miners. At the time of the incident, the mine operator was conducting a high-risk mining technique known as MSHA and mine operator officials worked together retreat mining in which pillars of coal previously left to develop rescue plans related to the August 2007 to support the mine roof are removed to maximize tragedy, with MSHA exercising final approval resource recovery. -
Families of Mine Disaster Victims Seek Accountability Angie Robertson
Public Interest Law Reporter Volume 13 Article 13 Issue 2 Spring 2008 2008 Families of Mine Disaster Victims Seek Accountability Angie Robertson Follow this and additional works at: http://lawecommons.luc.edu/pilr Part of the Oil, Gas, and Mineral Law Commons Recommended Citation Angie Robertson, Families of Mine Disaster Victims Seek Accountability, 13 Pub. Interest L. Rptr. 200 (2008). Available at: http://lawecommons.luc.edu/pilr/vol13/iss2/13 This Article is brought to you for free and open access by LAW eCommons. It has been accepted for inclusion in Public Interest Law Reporter by an authorized administrator of LAW eCommons. For more information, please contact [email protected]. Robertson: Families of Mine Disaster Victims Seek Accountability Loyola Public Interest Law Reporter FAMILIES OF MINE DISASTER VICTIMS SEEK ACCOUNTABILITY by ANGIE ROBERTSON twelve miners, in West Virginia, which killed T andhe 2006 the 2007Sago minemine disasterdisaster at Crandall Canyon in Utah, which killed nine miners, once again revealed the dangerous working conditions in coal mines and brought renewed national attention to the need for thorough mine inspections.1 Mining remains one of the most dangerous occupations in America, with a fatality rate more than seven times higher than the average for all private indus- tries.2 Because coal remains the source of 50 percent of the energy used in the United States, and energy use continues to rise, this fatality rate could poten- tially increase. 3 200 Published by LAW eCommons, 2008 1 Public Interest Law Reporter, Vol. 13, Iss. 2 [2008], Art. 13 No. 2 * Spring 2008 U.S. -
Deep Cover Pillar Recovery in the US
Deep Cover Pillar Recovery in the US Chris Mark, PrincipalMark, C.Research Engineer NIOSH Pittsburgh Research Laboratory Pittsburgh, PA ABSTRACT • Conditions under which retreat mining is used, including In the wake of the Crandall Canyon mine disaster, the U.S. conditions relating to seam thickness, depth of cover, strength Congress asked the National Institute for Occupational Health and of the mine roof, floor, and pillars, and the susceptibility of the Safety (NIOSH) to study the safety of deep cover pillar recovery mine to seismic activity, and; operations in the US. The legislation defined “deep cover” to • Procedures used to ensure miner safety during retreat mining. be greater than 1,500 ft, but NIOSH is also evaluating mines at depths greater than 1,000 ft when multiple seam interactions are NIOSH will submit a report to Congress on December 31, 2009, encountered. By these definitions, there about 35 active mines that containing the results of the study. The report will also include engage in deep cover pillar recovery, in the states of UT, CO, VA, recommendations to enhance the safety of miners on retreat mining WV, and KY. To date, NIOSH has documented ground conditions sections and recommendations for future research. and ground control experience at nearly all of them. This paper provides an overview of current deep cover pillar recovery practice. The study is being conducted in collaboration with the University Specific ground control issues that are discussed include: of Utah (U of UT) and West Virginia University (WVU). At WVU, a team led by Prof. Keith Heasley is investigating pillar design for • Pillar recovery sequences, deep cover retreat mining, focusing on the LaModel numerical • Pillar and barrier pillar design, modeling program. -
The News Director's Balance of Business and News: an Oral History Exploration of Salt Lake Television News, 1948 - 2008
Brigham Young University BYU ScholarsArchive Theses and Dissertations 2010-03-16 The News Director's Balance of Business and News: An Oral History Exploration of Salt Lake Television News, 1948 - 2008 Andrew Miles Tyler Brigham Young University - Provo Follow this and additional works at: https://scholarsarchive.byu.edu/etd Part of the Communication Commons BYU ScholarsArchive Citation Tyler, Andrew Miles, "The News Director's Balance of Business and News: An Oral History Exploration of Salt Lake Television News, 1948 - 2008" (2010). Theses and Dissertations. 2104. https://scholarsarchive.byu.edu/etd/2104 This Thesis is brought to you for free and open access by BYU ScholarsArchive. It has been accepted for inclusion in Theses and Dissertations by an authorized administrator of BYU ScholarsArchive. For more information, please contact [email protected], [email protected]. The News Director’s Balance of Business and News: An Oral History Exploration of Salt Lake Television News, 1948 - 2008 AnDrew M. Tyler A thesis submitted to the faculty of Brigham Young University in partial fulfillment of the requirements for the degree of Master of Arts Dale Cressman, Chair Ed Adams Brad Rawlins Department of Communications Brigham Young University April 2010 Copyright © 2010 AnDrew Tyler All Rights Reserved ABSTRACT The News Director’s Balance of Business and News: An Oral History Exploration of Salt Lake Television News, 1948-2008 AnDrew M. Tyler Department of Communications Master of Arts News directors fill, perhaps, one of the most difficult roles within the drama of the news room. In an environment where objectivity and trust are paramount, and where bias must be kept at an absolute minimum, the news director exists as the arbiter, balancing these journalistic ideals with the necessities for financial survival. -
Coal Mine Safety and Health
Order Code RL34429 Coal Mine Safety and Health March 31, 2008 Linda Levine Specialist in Labor Economics Domestic Social Policy Division Coal Mine Safety and Health Summary Safety in the coal mining industry is much improved compared to the early decades of the twentieth century, a time when hundreds of miners could lose their lives in a single accident and more than 1,000 fatalities could occur in a single year. Fatal injuries associated with coal mine accidents fell almost continually between 1925 and 2005, when they reached an all-time low of 23. As a result of 12 deaths at West Virginia’s Sago mine and fatalities at other coal mines in 2006, however, the number of fatalities more than doubled to 47. Fatalities declined a year later to 33, which is comparable to levels achieved during the late 1990s. In addition to the well above-average fatal injury rates they face, coal miners suffer from occupationally caused diseases. Prime among them is black lung (coal workers’ pneumoconiosis, CWP), which still claims about 1,000 fatalities annually. Although improved dust control requirements have led to a decrease in the prevalence of CWP, there is recent evidence of advanced cases among miners who began their careers after the stronger standards went into effect in the early 1970s. In addition, disagreement persists over the current respirable dust limits and the degree of compliance with them by mine operators. In the wake of the January 2006 Sago mine accident, the U.S. Department of Labor’s Mine Safety and Health Administration (MSHA) was criticized for its slow pace of rulemaking earlier in the decade. -
Finished Guide.Indd
The SAN RAFAEL COUNTRY Travel Guide Experience The Roads Less Traveled SAN RAFAEL COUNTRY E M E R Y C O U N T Y ® ®® ® www.sanrafaelcountry.com TABLE OF CONTENTS AREA INFORMATION Emergency Numbers Introduction, Precautions, & Important Info. p. 3 Calendar of Events p. 4 Emery County Sheri! : Emergency 911 San Rafael Country App p. 5 Green River 435-564-8111 Museums & Information Centers p. 6 Castle Dale 435-381-2404 Golf Courses p. 7 State Parks p. 8 & 9 Utah Highway Patrol: Emergency 911 Utah State Route 10 p. 10-12 Green River 435-564-3474 Huntington Canyon p. 13 Miller Flat p. 14 Medical Centers: Green River 435-564-3434 Joe’s Valley p. 15 Castle Dale 435-381-2305 Cleveland - Lloyd Dinosaur Quarry p. 16 Cedar Mountain p. 17 Hospital: Old Rail Road Grade Road p. 18 Price 435-637-4800 Wedge Overlook p. 19 Bureau of Land Management: Cottonwood Wash/Buckhorn Wash p. 20 & 21 Price 435-636-3600 Interstate 70 p. 22 Black Dragon Wash p. 23 Forest Service: Ferron 435-384-2372 Little Wild Horse Road p. 24 Price 435-637-2817 Goblin Valley State Park Road p. 25 Heart of Sinbad Road p. 26 Road Department: Behind the Reef Road p. 27 Green River 435-564-3574 Castle Dale 435-381-2550 McKay Flat/Hondu Arch Road p. 28 Hidden Splendor Road p. 29 Reds Canyon Road p. 30 Rod’s Valley p. 31 Swasey’s Cabin p. 32 Dutchman’s Arch/Head of Sinbad p. 33 Moore Cuto! Road p. 34 Rochester Creek Rock Art p. -
Underground Mine Refuge Chamber Expectations Training: Program Development and Evaluation ⇑ Katherine A
Underground mine Refuge Chamber Expectations Training: Program development and evaluation ⇑ Katherine A. Margolis, Catherine Y. Kingsley Westerman , Kathleen M. Kowalski-Trakofler National Institute for Occupational Safety and Health, P.O. Box 18070, Pittsburgh, PA, United States abstract Refuge chambers are new devices for underground coal mines that provide approximately 96 h of breath able air, water, food, and supplies in the event of an emergency where miners are unable to escape. Researchers at the National Institute for Occupational Safety and Health (NIOSH) developed a training program to prepare miners for what to expect psychologically and physiologically inside of a refuge chamber. The field tests of this training revealed that it was received very positively by miners and helped impart realistic views about the physical discomforts and psychological stresses of being inside a refuge chamber. 1. Introduction (2007) suggested that psychological factors relevant during emer gencies, such as reducing anxiety and improving morale, are In 2006, several major incidents occurred at underground coal important design considerations for refuge chambers. However mines in the United States (US), resulting in 19 worker fatalities. well-designed a refuge chamber is, those inside are inevitably These included an explosion at the Anker West Virginia Mining going to experience some negative psychological effects because Company Sago Mine in Upshur County, West Virginia, in which of the situation. One way to help miners deal with these effects 12 miners died; a fire at the Aracoma Coal Company, Inc., Alma is to make them aware in advance of the potential reactions to No. 1 Mine in West Virginia, in which two miners died; and an such an experience. -
Underground Coal Mine Disasters 1900 - 2010: Events, Responses, and a Look to the Future
Underground Coal Mine Disasters 1900 - 2010: Events, Responses, and a Look to the Future Michael J. Brnich, Jr., BS, CMSP NIOSH Office of Mine Safety and Health Pittsburgh, PA, USA Kathleen M. Kowalski-Trakofker, Ph.D. NIOSH Office of Mine Safety and Health Pittsburgh, PA, USA ABSTRACT: This paper captures almost 110 years of history of underground coal mine disasters in the United States. The deadly disasters of the first ten years of the twentieth century led to the U.S. Congress founding the U.S. Bureau of Mines (USBM) in 1910. The authors examine the changing trends in mine disasters including the frequency of fatalities, causal types, the responses to those disasters and most importantly, the growing body of research on human behavior in mine emergencies. Emphasis is on the future - integrating the research on human behavior in disasters into the mining industry. This research includes the integration of the judgment decision- making process, communication, leadership in escape, expectations training, incident command center issues including fatigue, shifts and leadership, plus issues concerning the introduction of refuge chambers into U.S. mines. The authors suggest that a key factor in meeting the goal of increasing successful mine escape and rescue while decreasing fatalities and injuries lies in the field of social-psychological research and human behavior interventions. INTRODUCTION Mine disasters have been a focal point among mine operators, safety and health personnel, and miners, as well as mine safety and health researchers in the United States for decades. Hundreds of disasters, resulting in thousands of mine worker deaths, have occurred in mines since 1900. -
Utah Mine Disaster and Preventing Future Tragedies
S. HRG. 110–471 UTAH MINE DISASTER AND PREVENTING FUTURE TRAGEDIES HEARING BEFORE A SUBCOMMITTEE OF THE COMMITTEE ON APPROPRIATIONS UNITED STATES SENATE ONE HUNDRED TENTH CONGRESS FIRST SESSION SPECIAL HEARING SEPTEMBER 5, 2007—WASHINGTON, DC Printed for the use of the Committee on Appropriations ( Available via the World Wide Web: http://www.gpoaccess.gov/congress/index.html U.S. GOVERNMENT PRINTING OFFICE 43–788 PDF WASHINGTON : 2008 For sale by the Superintendent of Documents, U.S. Government Printing Office Internet: bookstore.gpo.gov Phone: toll free (866) 512–1800; DC area (202) 512–1800 Fax: (202) 512–2250 Mail: Stop SSOP, Washington, DC 20402–0001 COMMITTEE ON APPROPRIATIONS ROBERT C. BYRD, West Virginia, Chairman DANIEL K. INOUYE, Hawaii THAD COCHRAN, Mississippi PATRICK J. LEAHY, Vermont TED STEVENS, Alaska TOM HARKIN, Iowa ARLEN SPECTER, Pennsylvania BARBARA A. MIKULSKI, Maryland PETE V. DOMENICI, New Mexico HERB KOHL, Wisconsin CHRISTOPHER S. BOND, Missouri PATTY MURRAY, Washington MITCH MCCONNELL, Kentucky BYRON L. DORGAN, North Dakota RICHARD C. SHELBY, Alabama DIANNE FEINSTEIN, California JUDD GREGG, New Hampshire RICHARD J. DURBIN, Illinois ROBERT F. BENNETT, Utah TIM JOHNSON, South Dakota LARRY CRAIG, Idaho MARY L. LANDRIEU, Louisiana KAY BAILEY HUTCHISON, Texas JACK REED, Rhode Island SAM BROWNBACK, Kansas FRANK R. LAUTENBERG, New Jersey WAYNE ALLARD, Colorado BEN NELSON, Nebraska LAMAR ALEXANDER, Tennessee CHARLES KIEFFER, Staff Director BRUCE EVANS, Minority Staff Director SUBCOMMITTEE ON DEPARTMENTS OF LABOR, HEALTH AND HUMAN SERVICES, AND EDUCATION, AND RELATED AGENCIES TOM HARKIN, Iowa, Chairman DANIEL K. INOUYE, Hawaii ARLEN SPECTER, Pennsylvania HERB KOHL, Wisconsin THAD COCHRAN, Mississippi PATTY MURRAY, Washington JUDD GREGG, New Hampshire MARY L.