Nail Coil Gun
Total Page:16
File Type:pdf, Size:1020Kb
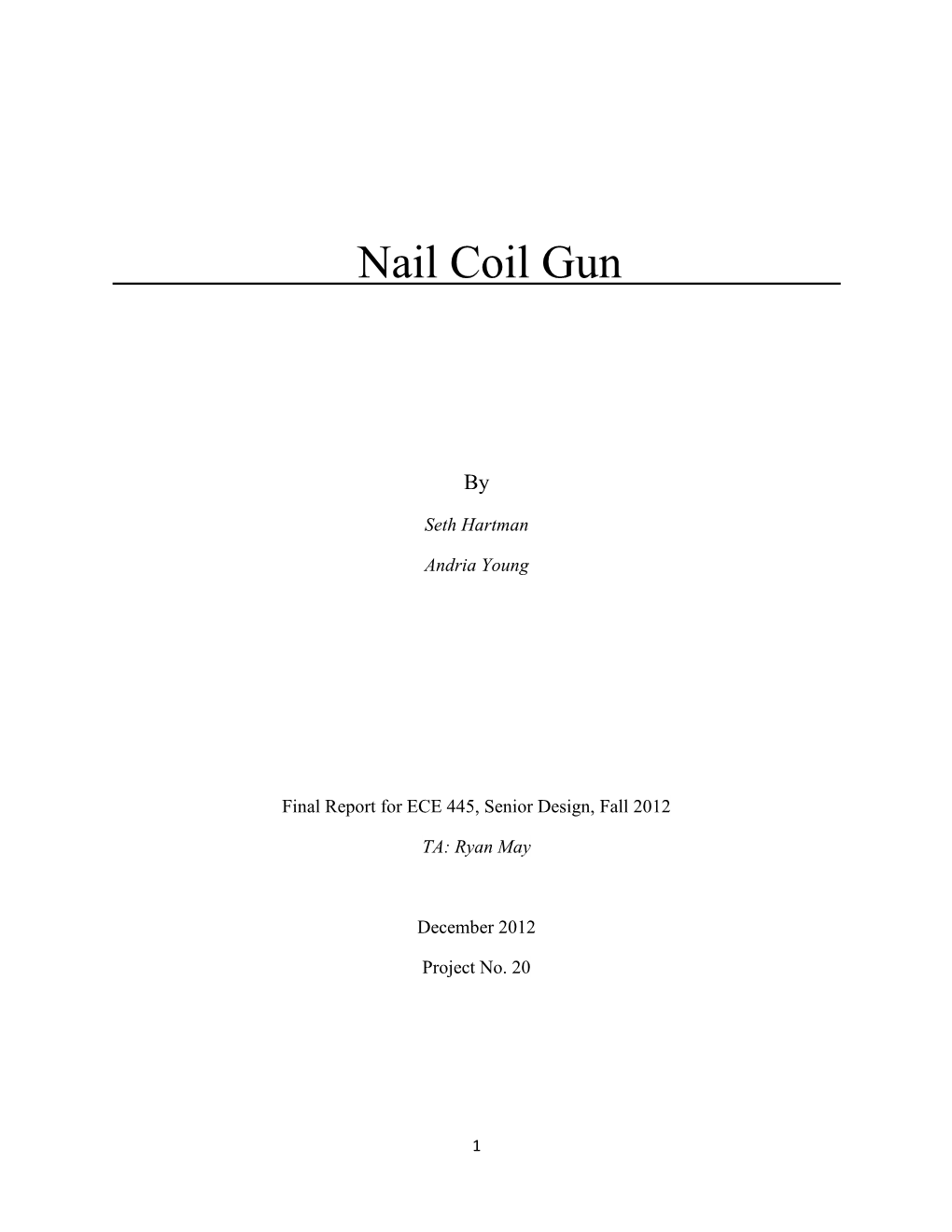
Load more
Recommended publications
-
Lyall Cooper Dr. Dann ASR – D Block 10 May 2012 the Mighty Railgun I. Abstract the Idea of This Project Is to Build a Railgun
Lyall Cooper Dr. Dann ASR – D Block 10 May 2012 The Mighty Railgun (All Bark no Bite) I. Abstract The idea of this project is to build a railgun capable of firing a small metal projectile at substantial velocity. The original plan was to build iterative prototypes capable of firing small projectiles, and using them to figure out the ideal design for the final version, but the smaller versions were not very successful due to their relative lack of power, so it was difficult to use them to learn what to do. The final, largest scale railgun is powered by a bank of capacitors with an equivalent capacitance of 24.6mF charged to around 350V. This produces 3013.5J of energy discharged over approximately 58.75 µs (it varies for each firing), drawing a peak of about 1425A when firing a projectile (it once again varies) and about 1600A when not firing a projectile (short circuiting the rails). The railgun is capable of consistently firing a small piece of metal (usually aluminum or copper); however the projectile does not usually travel very far, although this is hard to measure due to the nature of the gun and the speed at which the firing takes place. II. Introduction Electricity is often seemingly mysterious, but we have come to accept and understand how through the interaction of electric and magnetic fields we can create a simple motor, as we did in the first semester. A railgun is just a linear electric motor, at very high speeds. What makes it different, however, is that it uses neither magnets nor coils of wire, and relies entirely on the induced magnetic field in the rails due to the extremely large current to produce a Lorentz Force to propel the projectile (which will be discussed in greater depth in the theory section). -
Overlapped Electromagnetic Coilgun for Low Speed Projectiles
ISSN (Print) 1226-1750 ISSN (Online) 2233-6656 Journal of Magnetics 20(3), 322-329 (2015) http://dx.doi.org/10.4283/JMAG.2015.20.3.322 Overlapped Electromagnetic Coilgun for Low Speed Projectiles Hany M. Mohamed1, Mahmoud A. Abdalla2*, Abdelazez Mitkees, and Waheed Sabery Electrical Engineering Branch, MTC College, Cairo, Egypt [email protected] [email protected] (Received 20 February 2015, Received in final form 16 June 2015, Accepted 16 June 2015) This paper presents a new overlapped coilgun configuration to launch medium weight projectiles. The proposed configuration consists of a two-stage coilgun with overlapped coil covers with spacing between them. The theoretical operation of a multi-stage coilgun is introduced, and a transient simulation was conducted for projectile motion through the launcher by using a commercial transient finite element software, ANSOFT MAXWELL. The excitation circuit design for each coilgun is reported, and the results indicate that the overlapped configuration increased the exit velocity relative to a non-overlapped configuration. Different configurations in terms of the optimum length and switching time were attempted for the proposed structure, and all of these cases exhibited an increase in the exit velocity. The exit velocity tends to increase by 27.2% relative to that of a non-overlapped coilgun of the same length. Keywords : electromagnetic launch, excitation circuit, lorentz force, overlapped coilgun 1. Introduction is not easy to obtain the main performance parameters and optimize the design [3]. Electromagnetic (EM) launch technology is a strong Sandia National Laboratories has succeeded in coilgun candidate to launch objects with high velocities over long design and operations by developing four guns with distances. -
An Introductory Electric Motors and Generators Experiment for a Sophomore Level Circuits Course
AC 2008-310: AN INTRODUCTORY ELECTRIC MOTORS AND GENERATORS EXPERIMENT FOR A SOPHOMORE-LEVEL CIRCUITS COURSE Thomas Schubert, University of San Diego Thomas F. Schubert, Jr. received his B.S., M.S., and Ph.D. degrees in electrical engineering from the University of California, Irvine, Irvine CA in 1968, 1969 and 1972 respectively. He is currently a Professor of electrical engineering at the University of San Diego, San Diego, CA and came there as a founding member of the engineering faculty in 1987. He previously served on the electrical engineering faculty at the University of Portland, Portland OR and Portland State University, Portland OR and on the engineering staff at Hughes Aircraft Company, Los Angeles, CA. Prof. Schubert is a member of IEEE and ASEE and is a registered professional engineer in Oregon. He currently serves as the faculty advisor for the Kappa Eta chapter of Eta Kappa Nu at the University of San Diego. Frank Jacobitz, University of San Diego Frank G. Jacobitz was born in Göttingen, Germany in 1968. He received his Diploma in physics from the Georg-August Universität, Göttingen, Germany in 1993, as well as M.S. and Ph.D. degrees in mechanical engineering from the University of California, San Diego, La Jolla, CA in 1995 and 1998, respectively. He is currently an Associate Professor of mechanical engineering at the University of San Diego, San Diego, CA since 2003. From 1998 to 2003, he was an Assistant Professor of mechanical engineering at the University of California, Riverside, Riverside, CA. He has also been a visitor with the Centre National de la Recherche Scientifique at the Université de Provence (Aix-Marseille I), France. -
An Engineering Guide to Soft Starters
An Engineering Guide to Soft Starters Contents 1 Introduction 1.1 General 1.2 Benefits of soft starters 1.3 Typical Applications 1.4 Different motor starting methods 1.5 What is the minimum start current with a soft starter? 1.6 Are all three phase soft starters the same? 2 Soft Start and Soft Stop Methods 2.1 Soft Start Methods 2.2 Stop Methods 2.3 Jog 3 Choosing Soft Starters 3.1 Three step process 3.2 Step 1 - Starter selection 3.3 Step 2 - Application selection 3.4 Step 3 - Starter sizing 3.5 AC53a Utilisation Code 3.6 AC53b Utilisation Code 3.7 Typical Motor FLCs 4 Applying Soft Starters/System Design 4.1 Do I need to use a main contactor? 4.2 What are bypass contactors? 4.3 What is an inside delta connection? 4.4 How do I replace a star/delta starter with a soft starter? 4.5 How do I use power factor correction with soft starters? 4.6 How do I ensure Type 1 circuit protection? 4.7 How do I ensure Type 2 circuit protection? 4.8 How do I select cable when installing a soft starter? 4.9 What is the maximum length of cable run between a soft starter and the motor? 4.10 How do two-speed motors work and can I use a soft starter to control them? 4.11 Can one soft starter control multiple motors separately for sequential starting? 4.12 Can one soft starter control multiple motors for parallel starting? 4.13 Can slip-ring motors be started with a soft starter? 4.14 Can soft starters reverse the motor direction? 4.15 What is the minimum start current with a soft starter? 4.16 Can soft starters control an already rotating motor (flying load)? 4.17 Brake 4.18 What is soft braking and how is it used? 5 Digistart Soft Starter Selection 5.1 Three step process 5.2 Starter selection 5.3 Application selection 5.4 Starter sizing 1. -
Electric Motors
SPECIFICATION GUIDE ELECTRIC MOTORS Motors | Automation | Energy | Transmission & Distribution | Coatings www.weg.net Specification of Electric Motors WEG, which began in 1961 as a small factory of electric motors, has become a leading global supplier of electronic products for different segments. The search for excellence has resulted in the diversification of the business, adding to the electric motors products which provide from power generation to more efficient means of use. This diversification has been a solid foundation for the growth of the company which, for offering more complete solutions, currently serves its customers in a dedicated manner. Even after more than 50 years of history and continued growth, electric motors remain one of WEG’s main products. Aligned with the market, WEG develops its portfolio of products always thinking about the special features of each application. In order to provide the basis for the success of WEG Motors, this simple and objective guide was created to help those who buy, sell and work with such equipment. It brings important information for the operation of various types of motors. Enjoy your reading. Specification of Electric Motors 3 www.weg.net Table of Contents 1. Fundamental Concepts ......................................6 4. Acceleration Characteristics ..........................25 1.1 Electric Motors ...................................................6 4.1 Torque ..............................................................25 1.2 Basic Concepts ..................................................7 -
Electromagnetic Flyer Plate Technology and Development of a Novel Current Distribution Sensor
Electromagnetic Flyer Plate Technology and Development of a Novel Current Distribution Sensor A doctoral thesis by Kaashif A. M. Omar (MPhys. Physics with Astrophysics, University of Leicester, 2007) Submitted in partial fulfilment of the requirements for the award of the degree of Doctor of Philosophy of Loughborough University November 2014 To the School of Electronic, Electrical and Systems Engineering, Loughborough University, Loughborough, UK © British Crown Owned Copyright 2014/AWE Acknowledgements With the grace and blessing of Allah (SWT), I have been able to complete this work, and I hope to continue in the pursuit of knowledge as is commanded by him… Completing this research project and writing up this thesis has been full of ups and downs and it has been a very long journey, I can vaguely recall a young(er) single scientist who began this work not knowing where it would lead to; now, I am happily married to my wife Humna, having just celebrated our first wedding anniversary, and about to start the next big chapter in my life, which is to become a father… On that note I would like to take this opportunity to firstly thank my father, Mr Abdul Majid Omar and my mother, Mrs Shenaz A M Omar; who have always encouraged me to push myself and instilled within me the confidence that I can achieve anything I put my mind to. Without their constant support I would never have even been able to complete my first degree In physics with Astrophysics at Leicester University, let alone have the opportunity to complete a PhD. -
Electromagnetic Launcher: Review of Various Structures
Published by : International Journal of Engineering Research & Technology (IJERT) http://www.ijert.org ISSN: 2278-0181 Vol. 9 Issue 09, September-2020 Electromagnetic Launcher : Review of Various Structures Siddhi Santosh Reelkar Prof. Dr. U. V. Patil Department of Electrical Engineering, Department of Electrical Engineering, Government College of Engineering, Government College of Engineering, Karad Karad Prof. Dr. V. V. Khatavkar Department of Electrical Engineering, P.E.S. Modern college of Engineering, Pune Hrishikesh Mehta Utkarsh Alset Aethertec Innovative Solutions, Aethertec Innovative Solutions, Bavdhan, Pune Bavdhan, Pune Abstract— A theoretic review of electromagnetic coil-gun This paper is mainly focusing the basic principle of launcher and its types are illustrated in this paper. In recent electromagnetic coil-gun launcher, inductance and resistance years conventional launchers like steam launchers, chemical calculations, construction and modeling concept of different launchers are replaced by electromagnetic launchers with coil-gun launcher. auxiliary benefits. The electromagnetic launchers like rail- gun and coil-gun elevated with multi pole field structure delivers II. WORKING PRINCIPLE great muzzle velocity and huge repulse force in limited time. Rail gun has two parallel rails from which object is launched. Various types of coil-gun electromagnetic launchers are When current passes through the rails to the object it compared in this paper for its structures and characteristics. The paper focuses on the basic formulae for calculating the produces arc. Because of high current pulse it has more values of inductance and resistance of electromagnetic contact friction losses [4]. Compare to the rail-gun launcher, launchers. Coil-gun launchers have no contact friction losses as there is no electrical contact between coils and object. -
Unit VI Superconductivity JIT Nashik Contents
Unit VI Superconductivity JIT Nashik Contents 1 Superconductivity 1 1.1 Classification ............................................. 1 1.2 Elementary properties of superconductors ............................... 2 1.2.1 Zero electrical DC resistance ................................. 2 1.2.2 Superconducting phase transition ............................... 3 1.2.3 Meissner effect ........................................ 3 1.2.4 London moment ....................................... 4 1.3 History of superconductivity ...................................... 4 1.3.1 London theory ........................................ 5 1.3.2 Conventional theories (1950s) ................................ 5 1.3.3 Further history ........................................ 5 1.4 High-temperature superconductivity .................................. 6 1.5 Applications .............................................. 6 1.6 Nobel Prizes for superconductivity .................................. 7 1.7 See also ................................................ 7 1.8 References ............................................... 8 1.9 Further reading ............................................ 10 1.10 External links ............................................. 10 2 Meissner effect 11 2.1 Explanation .............................................. 11 2.2 Perfect diamagnetism ......................................... 12 2.3 Consequences ............................................. 12 2.4 Paradigm for the Higgs mechanism .................................. 12 2.5 See also ............................................... -
High-Performance Specialty Motors & Application-Specific Motion Systems
Motion Solutions That Change the Game Aerospace & Defense Automation Commercial-Consumer Industrial High-Performance Specialty Motors Medical & Application-Specific Motion Systems Pumps Robotics Vehicles A World of Solutions Allied Motion products are in use around the globe in a wide range of demanding applications. Our companies possess the expertise, products, and global presence to provide you with the motion solutions you need in today’s globally competitive world. Aerospace & Defense Automation Commercial-Consumer Industrial Medical Pumps Robotics Vehicles www.alliedmotion.com 2 [email protected] Motion Solutions That Change the Game The Allied Motion Culture “VIA” – Value, Integrity, AST – encapsulates the Allied Motion culture. It means we work to create tangible Value for our customers and stakeholders; we maintain the highest Integrity in all of our business relationships; and we utilize Allied Systematic Tools to continuously improve Quality, Delivery, Cost and Innovation. Why Choose Allied Motion to be Your Motion Solution Provider? Global Reach Solution Centers Three strategically located Solution Centers – North America, Europe, Asia – offer local application engineering and sales support to make it easy to do business with us. “We speak your language.” Advanced Technology Products Allied Motion develops advanced-technology products that enable our customers to “change the game.” We strive to produce the most compact, innovative products with the highest performance at a competitive price. Allied Motion Solutions Brushless Torque Motors 4-5 Lean Enterprise: Allied Systematic Tools (AST) Brushless Servo Motors 6-7 Allied Systematic Tools (AST) is our set of lean enterprise business tools that drive continuous improvement. AST insures that our Brushless & PMDC Gear Motors 8-9 customers receive the highest quality products and service at the Brushless Motors with Integrated Controllers 10-11 best possible price. -
Linear Induction Motor
Linear Induction Motor Electrical and Computer Engineering Tyler Berchtold, Mason Biernat and Tim Zastawny Project Advisor: Professor Steven Gutschlag 4/21/2016 2 Outline of Presentation • Background and Project Overview • Microcontroller System • Final Design • Economic Analysis • Hardware • State of Work Completed • Conclusion 3 Outline of Presentation • Background and Project Overview • Microcontroller System • Final Design • Economic Analysis • Hardware • State of Work Completed • Conclusion 4 Alternating Current Induction Machines • Most common AC machine in industry • Produces magnetic fields in an infinite loop of rotary motion • Current-carrying coils create a rotating magnetic field • Stator wrapped around rotor [1] [2] 5 Rotary To Linear [3] 6 Linear Induction Motor Background • Alternating Current (AC) electric motor • Powered by a three phase voltage scheme • Force and motion are produced by a linearly moving magnetic field • Used in industry for linear motion and to turn large diameter wheels [4] 7 Project Overview • Design, construct, and test a linear induction motor (LIM) • Powered by a three-phase voltage input • Rotate a simulated linear track and cannot exceed 1,200 RPM • Monitor speed, output power, and input frequency • Controllable output speed [5] 8 Initial Design Process • Linear to Rotary Model • 0.4572 [m] diameter 퐿 = 훳푟 (1.1) • 0.3048 [m] arbitrary stator length • Stator contour designed for a small air gap • Arc length determined from stator length and diameter • Converted arc length from a linear motor to the circumference of a rotary motor • Used rotary equations to determine required [6] frequency and verify number of poles 9 Rotational to Linear Speed (1.2) (1.3) 10 Pole Pitch and Speed (1.4) • For fixed length stator τ= L/p • L = Arc Length τ A B C A B C [7] 11 Linear Synchronous Speed Ideal Linear Synchronous Speed vs. -
DC Motor Workshop
DC Motor Annotated Handout American Physical Society A. What You Already Know Make a labeled drawing to show what you think is inside the motor. Write down how you think the motor works. Please do this independently. This important step forces students to create a preliminary mental model for the motor, which will be their starting point. Since they are writing it down, they can compare it with their answer to the same question at the end of the activity. B. Observing and Disassembling the Motor 1. Use the small screwdriver to take the motor apart by bending back the two metal tabs that hold the white plastic end-piece in place. Pull off this plastic end-piece, and then slide out the part that spins, which is called the armature. 2. Describe what you see. 3. How do you think the motor works? Discuss this question with the others in your group. C. Mounting the Armature 1. Use the diagram below to locate the commutator—the split ring around the motor shaft. This is the armature. Shaft Commutator Coil of wire (electromagnetic) 2. Look at the drawing on the next page and find the brushes—two short ends of bare wire that make a "V". The brushes will make electrical contact with the commutator, and gravity will hold them together. In addition the brushes will support one end of the armature and cradle it to prevent side- to-side movement. 1 3. Using the cup, the two rubber bands, the piece of bare wire, and the three pieces of insulated wire, mount the armature as in the diagram below. -
Green Energy Based Electrical Power Generation System
ISSN (Print) : 2320 – 3765 ISSN (Online): 2278 – 8875 International Journal of Advanced Research in Electrical, Electronics and Instrumentation Engineering (An ISO 3297: 2007 Certified Organization) Vol. 5, Issue 2, February 2016 Green Energy Based Electrical Power Generation System Ronak .L Tandel1, Dipen .D Patel2, Akash .M Tandel3, Keyur .M Mistry4, Shani .M Vaidya5 UG Student, Dept. of Electrical Engineering, Valia Institute of Technology, Bharuch, Gujarat, India1-4 Assistant Professor, Dept. of Electrical Engineering, Valia Institute of Technology, Bharuch, Gujarat, India5 ABSTRACT: Due to the rapid growth in the usage electricity and the price combustion fuel, motivate us to use natural air as a fuel to generate electricity, this paper shows a natural air and industrial waste gases power driven electricity generating system, Which can produced electricity at very low cost using air or waste gas as a fuel, This system will be extremely handy at the place where we have to control only ON and OFF switches for operating and charging purpose of the system, The main aim of this work is to minimize the running cost, charging time, pollution, recover losses of electrical generator and also to maximize it efficiency so that it can run for maximum time as possible to the each and every user, so in this paper we have described a nature air driven electricity generating system. KEYWORDS:Waste gas, Compressed air, Air motor, Alternator, Dynamo, AutoCAD. I. INTRODUCTION Electric power is basic necessity of any industries and it can be very costly