A Study on the Manufacturing of Energetically-Modified Reject Fly Ash and the Characteristics of Mortar
Total Page:16
File Type:pdf, Size:1020Kb
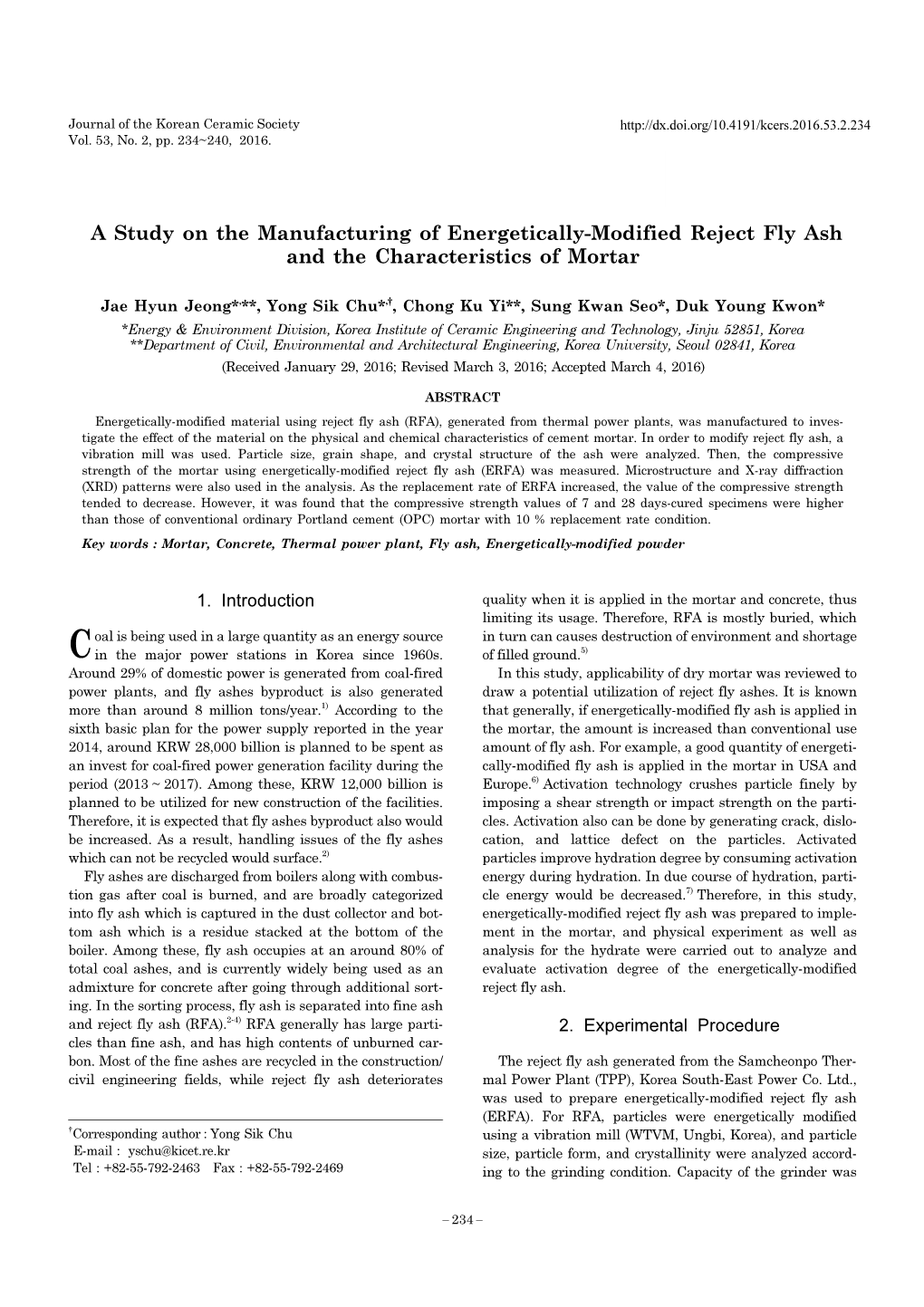
Load more
Recommended publications
-
Assessment of Wood-Based Fly Ash As Alternative Cement Replacement
sustainability Article Assessment of Wood-Based Fly Ash as Alternative Cement Replacement Jan Foˇrt 1,2,* , Jiˇrí Šál 2, Jaroslav Žák 2 and Robert Cernˇ ý 1 1 Department of Materials Engineering and Chemistry, Faculty of Civil Engineering, Czech Technical University in Prague, Thákutova 7, 166 29 Prague, Czech Republic; [email protected] 2 Institute of Technology and Business in Ceskˇ é Budˇejovice,Okružní 10, 370 01 Ceskˇ é Budˇejovice, Czech Republic; [email protected] (J.Š.); [email protected] (J.Ž.) * Correspondence: [email protected] Received: 16 October 2020; Accepted: 15 November 2020; Published: 17 November 2020 Abstract: The abandonment of coal energy plants in the near future will result in a substantially reduced availability of the coal fly ash broadly used as an efficient supplementary material. In line with the growth of alternative and renewable energy resources, the amount of biomass-based ash rises substantially. Nevertheless, a diverse chemical composition prevents a broader utilization of biomass-based fly ash compared to coal ash on an industrial scale. On this account, the present work is aimed at investigating the basic physical and mechanical properties of concrete mortars modified by a high volume of biomass fly ash (BFA) from wood combustion. Delivered results confirm a significant potential of BFA in the building industry. Experimental analysis of concrete mortars with BFA reveals preservation or even improvement of compressive and bending strength up to 30 wt.% cement replacement. On the contrary, higher dosages induce a gradual decrease in mechanical performance. The performed Life Cycle Assessment analysis reveals the perspective of BFA incorporation taking into account environmental issues considering the ratio between preservation of mechanical performance per normalized endpoint environmental score that allows a direct comparison with other alternatives. -
Alkali-Silica Reactivity: an Overview of Research
SHRP-C-342 Alkali-Silica Reactivity: An Overview of Research Richard Helmuth Construction Technology Laboratories, Inc. With contributions by: David Stark Construction Technology Laboratories, Inc. Sidney Diamond Purdue University Micheline Moranville-Regourd Ecole Normale Superieure de Cachan Strategic Highway Research Program National Research Council Washington, DC 1993 Publication No. SHRP-C-342 ISBN 0-30cL05602-0 Contract C-202 Product No. 2010 Program Manager: Don M. Harriott Project Maxtager: Inam Jawed Program AIea Secretary: Carina Hreib Copyeditor: Katharyn L. Bine Brosseau May 1993 key words: additives aggregate alkali-silica reaction cracking expansion portland cement concrete standards Strategic Highway Research Program 2101 Consti!ution Avenue N.W. Washington, DC 20418 (202) 334-3774 The publicat:Lon of this report does not necessarily indicate approval or endorsement by the National Academy of Sciences, the United States Government, or the American Association of State Highway and Transportation Officials or its member states of the findings, opinions, conclusions, or recommendations either inferred or specifically expressed herein. ©1993 National Academy of Sciences 1.5M/NAP/593 Acknowledgments The research described herein was supported by the Strategic Highway Research Program (SHRP). SHRP is a unit of the National Research Council that was authorized by section 128 of the Surface Transportation and Uniform Relocation Assistance Act of 1987. This document has been written as a product of Strategic Highway Research Program (SHRP) Contract SHRP-87-C-202, "Eliminating or Minimizing Alkali-Silica Reactivity." The prime contractor for this project is Construction Technology Laboratories, with Purdue University, and Ecole Normale Superieure de Cachan, as subcontractors. Fundamental studies were initiated in Task A. -
Delayed Ettringite Formation
Ettringite Formation and the Performance of Concrete In the mid-1990’s, several cases of premature deterioration of concrete pavements and precast members gained notoriety because of uncertainty over the cause of their distress. Because of the unexplained and complex nature of several of these cases, considerable debate and controversy have arisen in the research and consulting community. To a great extent, this has led to a misperception that the problems are more prevalent than actual case studies would indicate. However, irrespective of the fact that cases of premature deterioration are limited, it is essential to address those that have occurred and provide practical, technically sound solutions so that users can confidently specify concrete in their structures. Central to the debate has been the effect of a compound known as ettringite. The objectives of this paper are: Fig. 1. Portland cements are manufactured by a process that combines sources of lime (such as limestone), silica and • to define ettringite and its form and presence in concrete, alumina (such as clay), and iron oxide (such as iron ore). Appropriately proportioned mixtures of these raw materials • to respond to questions about the observed problems and the are finely ground and then heated in a rotary kiln at high various deterioration mechanisms that have been proposed, and temperatures, about 1450 °C (2640 °F), to form cement compounds. The product of this process is called clinker • to provide some recommendations on designing for durable (nodules at right in above photo). After cooling, the clinker is concrete. interground with about 5% of one or more of the forms of Because many of the questions raised relate to cement character- calcium sulfate (gypsum shown at left in photo) to form portland cement. -
A Study on Physical Properties of Mortar Mixed with Fly-Ash As Functions of Mill Types and Milling Times
Journal of the Korean Ceramic Society http://dx.doi.org/10.4191/kcers.2016.53.4.435 Vol. 53, No. 4, pp. 435~443, 2016. Communication A Study on Physical Properties of Mortar Mixed with Fly-ash as Functions of Mill Types and Milling Times Sung Kwan Seo*,**, Yong Sik Chu*,†, Kwang Bo Shim**, and Jae Hyun Jeong* *Energy & Environmental Division, Korea Institute of Ceramic Engineering and Technology, Jinju 52851, Korea1) **Division of Materials Science and Engineering, Hanyang University, Seoul 04763, Korea2) (Received January 27, 2016; Revised May 9, July 4, 2016; Accepted July 7, 2016) ABSTRACT Coal ash, a material generated from coal-fired power plants, can be classified as fly ash and bottom ash. The amount of domes- tic fly ash generation is almost 6.84 million tons per year, while the amount of bottom ash generation is 1.51 million tons. The fly ash is commonly used as a concrete admixture and a subsidiary raw material in cement fabrication process. And some amount of bottom ash is used as a material for embankment and block. However, the recyclable amount of the ash is limited since it could cause deterioration of physical properties. In Korea, the ashes are simply mixed and used as a replacement material for cement. In this study, an attempt was made to mechanically activate the ash by grinding process in order to increase recycling rates of the fly ash. Activated fly ash was prepared by controlling the mill types and the milling times and characteristics of the mortar containing the activated fly ash was analyzed. -
Emission of Dislocations from Grain Boundaries and Its Role in Nanomaterials
crystals Review Emission of Dislocations from Grain Boundaries and Its Role in Nanomaterials James C. M. Li 1,*, C. R. Feng 2 and Bhakta B. Rath 2 1 Department of Mechanical Engineering, University of Rochester, Rochester, NY 14627, USA 2 U.S. Naval Research Laboratory, 4555 Overlook Ave SW, Washington, DC 20375, USA; [email protected] (C.R.F.); [email protected] (B.B.R.) * Correspondence: [email protected] Abstract: The Frank-Read model, as a way of generating dislocations in metals and alloys, is widely accepted. In the early 1960s, Li proposed an alternate mechanism. Namely, grain boundary sources for dislocations, with the aim of providing a different model for the Hall-Petch relation without the need of dislocation pile-ups at grain boundaries, or Frank-Read sources inside the grain. This article provides a review of his model, and supporting evidence for grain boundaries or interfacial sources of dislocations, including direct observations using transmission electron microscopy. The Li model has acquired new interest with the recent development of nanomaterial and multilayers. It is now known that nanocrystalline metals/alloys show a behavior different from conventional polycrystalline materials. The role of grain boundary sources in nanomaterials is reviewed briefly. Keywords: dislocation emission; grain boundaries; nanomaterials; Hall-Petch relation; metals and alloys 1. Introduction To explain the properties of crystalline aggregates, such as crystal plasticity, Taylor [1,2] provided a theoretical construct of line defects in the atomic scale of the crystal lattice. Citation: Li, J.C.M.; Feng, C.R.; With the use of the electron microscope, the sample presence of dislocations validated Rath, B.B. -
The Influence Mechanism of Ettringite Crystals and Microstructure
materials Article The Influence Mechanism of Ettringite Crystals and Microstructure Characteristics on the Strength of Calcium-Based Stabilized Soil Youmin Han 1,2,3 , Junwu Xia 1,3,* , Hongfei Chang 1 and Jun Xu 4,5 1 State Key Laboratory for Geomechanics and Deep Underground Engineering, China University of Mining and Technology, Daxue Road, Xuzhou 221116, China; [email protected] (Y.H.); [email protected] (H.C.) 2 School of Architecture and Civil Engineering, Anhui Polytechnic University, Beijing Road, Wuhu 241000, China 3 Jiangsu Collaborative Innovation Center for Building Energy Saving and Construction Technology, Xueyuan Road, Xuzhou 221116, China 4 School of Civil Engineering and Architecture, Jiangsu University of Science and Technology, Changhui Road, Zhenjiang 212100, China; [email protected] 5 School of Materials Science and Engineering, Southeast University, Southeast University Road, Nanjing 211189, China * Correspondence: [email protected] or [email protected] Abstract: To reveal the influence mechanism of ettringite (AFt) crystals and microstructure character- istics on the strength of calcium-based stabilized soil, the strengths and microscopic properties of seven groups of stabilized soil samples were studied systematically through unconfined compressive strength, scanning electron microscope (SEM), X-ray diffraction (XRD), thermogravimetry (TG), and Fourier transform infrared spectroscopy (FTIR) testing methods. The results indicate that the strength of the cement-stabilized soil is relatively high because abundant calcium silicate hydrate (CSH) gels Citation: Han, Y.; Xia, J.; Chang, H.; coat the outer surface of soil particles to cement together. For the cement–gypsum-stabilized soil, Xu, J. The Influence Mechanism of Ettringite Crystals and superabundant thick and long AFt crystals make the pores in soil particles larger, and the sample Microstructure Characteristics on the becomes looser, resulting in lower strength than that of the cement-stabilized soil. -
We Now Know That the Maximum Level That Avoids
Using ash in concrete is nothing new. h e Romans rials derived from coal combustion products, includ- used volcanic ash in their spectacular construction ing fly ash, nationwide. projects long before the introduction of Portland cement, “Fly ash is composed of the non-combustible mineral having discovered its value as a hardening agent when portion of coal. When coal is consumed in a power plant, mixed with lime. h e ancient Romans used volcanic ash it’s i rst ground to the i neness of powder. Blown into as an admix to erect buildings such as the Pantheon and the power plant’s boiler, the carbon is consumed – leav- Coliseum, roads, and aqueducts. Remember, these struc- ing molten particles rich in silica, alumina, and calcium. tures are more than 2,000 years old. h ese particles solidify as microscopic, glassy spheres Fly ash concrete was first used in the U.S. in the that are collected from the power plant’s exhaust before 1920s for dam construction, when engineers found that it reduced the total cement requirement. Today, as more projects seek LEED certification, ash is resurfac- WE NOW KNOW THAT THE ing as a popular environmentally-friendly alternative MAXIMUM LEVEL THAT AVOIDS to Portland cement. No longer are we using volcanic COMPLICATIONS IN ADHERING FLOOR ash, of course, but coal fly ash is gaining ground as the COVERING IS 15% FLY ASH. green alternative of choice for LEED projects. Many of the projects and the millions of square yards of LEED flooring we’ve installed in recent years used ash in the they can “l y” away – hence the product’s name: l y ash,” cement mixture. -
Brownmillerite Ca2(Al, Fe )2O5 C 2001-2005 Mineral Data Publishing, Version 1
3+ Brownmillerite Ca2(Al, Fe )2O5 c 2001-2005 Mineral Data Publishing, version 1 Crystal Data: Orthorhombic. Point Group: mm2. As square platelets, to about 60 µm; massive. Physical Properties: Hardness = n.d. D(meas.) = 3.76 D(calc.) = 3.68–3.73 Optical Properties: Semitransparent. Color: Reddish brown. Optical Class: Biaxial (–). Pleochroism: Distinct; X = Y = yellow-brown; Z = dark brown. Orientation: Y and Z lie in the plane of the platelets; extinction in that plane is diagonal. α = < 2.02 β = > 2.02 γ = > 2.02 2V(meas.) = n.d. Cell Data: Space Group: Ibm2. a = 5.584(5) b = 14.60(1) c = 5.374(5) Z = 2 X-ray Powder Pattern: Near Mayen, Germany. 2.65 (vs), 7.19 (s), 2.78 (s), 1.93 (s), 2.05 (ms), 3.65 (m), 1.82 (m) Chemistry: (1) (2) (3) TiO2 1.5 1.9 Al2O3 17.2 22.3 13.1 Fe2O3 30.5 27.6 41.9 Cr2O3 0.1 n.d. MgO n.d. n.d. CaO 46.2 44.8 43.7 insol. 4.0 LOI 0.5 Total 94.4 100.3 100.6 (1) Near Mayen, Germany; by semiquantitative spectroscopy. (2) Hatrurim Formation, Israel; corresponds to Ca1.99(Al1.09Fe0.86Ti0.05)Σ=2.00O5. (3) Do.; corresponds to Ca1.95(Fe1.31Al0.64 Ti0.06)Σ=2.01O5. Occurrence: In thermally metamorphosed limestone blocks included in volcanic rocks (near Mayen, Germany); in high-temperature, thermally metamorphosed, impure limestones (Hatrurim Formation, Israel). Association: Calcite, ettringite, wollastonite, larnite, mayenite, gehlenite, diopside, pyrrhotite, grossular, spinel, afwillite, jennite, portlandite, jasmundite (near Mayen, Germany); melilite, mayenite, wollastonite, kalsilite, corundum (Kl¨och, Austria); spurrite, larnite, mayenite (Hatrurim Formation, Israel). -
Multidisciplinary Design Project Engineering Dictionary Version 0.0.2
Multidisciplinary Design Project Engineering Dictionary Version 0.0.2 February 15, 2006 . DRAFT Cambridge-MIT Institute Multidisciplinary Design Project This Dictionary/Glossary of Engineering terms has been compiled to compliment the work developed as part of the Multi-disciplinary Design Project (MDP), which is a programme to develop teaching material and kits to aid the running of mechtronics projects in Universities and Schools. The project is being carried out with support from the Cambridge-MIT Institute undergraduate teaching programe. For more information about the project please visit the MDP website at http://www-mdp.eng.cam.ac.uk or contact Dr. Peter Long Prof. Alex Slocum Cambridge University Engineering Department Massachusetts Institute of Technology Trumpington Street, 77 Massachusetts Ave. Cambridge. Cambridge MA 02139-4307 CB2 1PZ. USA e-mail: [email protected] e-mail: [email protected] tel: +44 (0) 1223 332779 tel: +1 617 253 0012 For information about the CMI initiative please see Cambridge-MIT Institute website :- http://www.cambridge-mit.org CMI CMI, University of Cambridge Massachusetts Institute of Technology 10 Miller’s Yard, 77 Massachusetts Ave. Mill Lane, Cambridge MA 02139-4307 Cambridge. CB2 1RQ. USA tel: +44 (0) 1223 327207 tel. +1 617 253 7732 fax: +44 (0) 1223 765891 fax. +1 617 258 8539 . DRAFT 2 CMI-MDP Programme 1 Introduction This dictionary/glossary has not been developed as a definative work but as a useful reference book for engi- neering students to search when looking for the meaning of a word/phrase. It has been compiled from a number of existing glossaries together with a number of local additions. -
Report No. REC-ERC-82-1. Fly Ash and Fly Ash Concrete
May 1984 Engineering and Research Center U. S. Department of the Interior Bureau of Reclamation Bureau ot Reclamation TECHNICAL REPORT STANDARD TITLE PAGE Fly Ash and Fly Ash Concrete May 1984 6. PERFORMING ORGANIZATION CODE 7. AUTHOR(S)-. 8. PERFORMING ORGANIZATION Edwin R. Dunstan, Jr. REPORT NO. I REC-ERC-82-1 9. PERFORMING ORGANIZATION NAME AND ADDRESS 10. WORK UNIT NO. Bureau of Reclamation, Engineering and Research Center 11. CONTRACT OR GRANT NO. Denver, Colorado 80225 10781 V0195 13. TYPE OF REPORT AND PERIOD COVERED 2. SPONSORING AGENCY NAME AND ADDRESS Same 14. SPONSORING AGENCY CODE DlBR 15. SUPPLEMENTARY NOTES Microfiche and/or hard copy available at the Engineering and Research Center. Denver. Colorado. Editor: RNW 16. ABSTRACT Fly ash is a residue that results from the combustion of ground or powdered coal. Historically, fly ash has been referred to as a ponolan and is used to reduce the amount of portland cement in concrete. However, in many Western States fly ashes have cementitious properties as well as pozzolanic properties, and they are capable of producing good strengths without portland cement. This study discusses test results of several ashes according to ASTM: C 6 18. Standard Specification for Fly Ash and Raw or Calcined Natural Pozzolan for Use as a Mineral Admixture in Portland Cement Concrete. Many changes are suggested. The replacement of 15 to 25 percent by mass of portland cement in concrete is examined. A few highly cementitious ashes were used to make concrete without portland cement. A new cement was developed that consists of over 90-percent fly ash and anhydrous CaS04.Test data for most concretes include: mix proportions, compressive strength, elasticity, drying shrinkage. -
Atomic Resolution Electron Tomography for 3D Imaging of Dislocations in Nanoparticles
Atomic Resolution Electron Tomography for 3D Imaging of Dislocations in Nanoparticles Chien-Chun Chen1,2, Chun Zhu1,2, Edward R. White1,2, Chin-Yi Chiu2,3, M. C. Scott1,2, B. C. Regan1,2, Laurence D. Marks4, Yu Huang2,3 and Jianwei Miao1 1Department of Physics and Astronomy, University of California, Los Angeles, CA 90095, USA. 2California NanoSystems Institute, University of California, Los Angeles, CA 90095, USA. 3Department of Materials Science and Engineering, University of California, Los Angeles, CA 90095, USA. 4Department of Materials Science and Engineering, Northwestern University, Evanston, IL 60201, USA. Dislocations and their interactions strongly influence many of the properties of materials, ranging from the strength of metals and alloys to the efficiency of light-emitting diodes and laser diodes. Although various experimental methods have been used to image dislocations in materials since 1956, a 3D technique for visualizing dislocations at atomic resolution has not previously been demonstrated. Here we report the development of atomic resolution electron tomography and achieve 3D imaging of dislocation core structures of a Pt nanoparticle at atomic resolution. Compared to conventional electron tomography, our atomic resolution imaging method incorporates three novel developments. First, the conventional alignment approach used in electron tomography either relies on fiducial markers or is based on the cross-correlation between neighboring projections. To our knowledge, neither of these alignment approaches can achieve atomic level precision. To overcome this limitation, we have developed a method based on the center of mass (CM), which is able to align the projections of a tilt series at atomic level accuracy. Second, we have implemented a data acquisition and tomographic reconstruction method, termed equally sloped tomography (EST). -
How to Make Concrete More Sustainable Harald Justnes1
Journal of Advanced Concrete Technology Vol. 13, 147-154, March 2015 / Copyright © 2015 Japan Concrete Institute 147 Scientific paper How to Make Concrete More Sustainable Harald Justnes1 A selected paper of ICCS13, Tokyo 2013. Received 12 November 2013, accepted 16 February 2015 doi:10.3151/jact.13.147 Abstract Production of cement is ranking 3rd in causes of man-made carbon dioxide emissions world-wide. Thus, in order to make concrete more sustainable one may work along one or more of the following routes; 1) Replacing cement in con- crete with larger amounts of supplementary cementing materials (SCMs) than usual, 2) Replacing cement in concrete with combinations of SCMs leading to synergic reactions enhancing strength, 3) Producing leaner concrete with less cement per cubic meter utilizing plasticizers and 4) Making concrete with local aggregate susceptible to alkali silica reaction (ASR) by using cement replacements, thus avoiding long transport of non-reactive aggregate. 1 Introduction SCMs, also uncommon ones like calcined marl 2. Replacing cement in concrete with combinations of The cement industry world-wide is calculated to bring SCMs leading to synergic reactions enhancing about 5-8% of the total global anthropogenic carbon strength dioxide (CO2) emissions. The general estimate is about 3. Producing leaner concrete with less cement per cubic 1 tonne of CO2 emission per tonne clinker produced, if meter utilizing plasticizers. fossil fuel is used and no measures are taken to reduce it. 4. Making concrete with local aggregate susceptible to The 3rd rank is not because cement is such a bad mate- alkali silica reaction (ASR) by using cement re- rial with respect to CO2 emissions, but owing to the fact placements, thus avoiding long transport of non- that it is so widely used to construct the infrastructure reactive aggregate and buildings of modern society as we know it.