A P =Σ L L L Ll ∆ = − =Ε
Total Page:16
File Type:pdf, Size:1020Kb
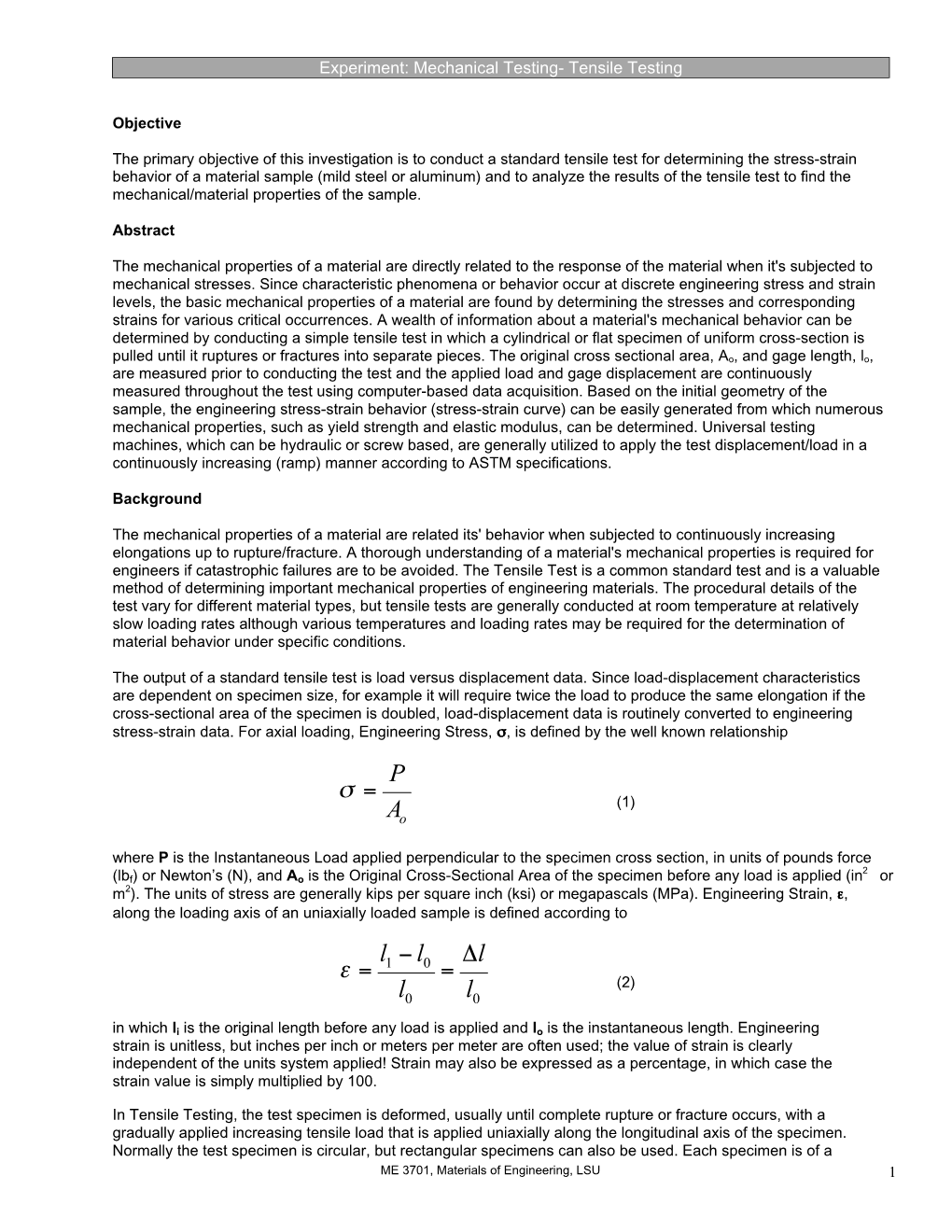
Load more
Recommended publications
-
Definition of Brittleness: Connections Between Mechanical
DEFINITION OF BRITTLENESS: CONNECTIONS BETWEEN MECHANICAL AND TRIBOLOGICAL PROPERTIES OF POLYMERS Haley E. Hagg Lobland, B.S., M.S. Dissertation Prepared for the Degree of DOCTOR OF PHILOSOPHY UNIVERSITY OF NORTH TEXAS August 2008 APPROVED: Witold Brostow, Major Professor Rick Reidy, Committee Member and Chair of the Department of Materials Science and Engineering Dorota Pietkewicz, Committee Member Nigel Shepherd, Committee Member Costas Tsatsoulis, Dean of the College of Engineering Sandra L. Terrell, Dean of the Robert B. Toulouse School of Graduate Studies Hagg Lobland, Haley E. Definition of brittleness: Connections between mechanical and tribological properties of polymers. Doctor of Philosophy (Materials Science and Engineering), August 2008, 51 pages, 5 tables, 13 illustrations, 106 references. The increasing use of polymer-based materials (PBMs) across all types of industry has not been matched by sufficient improvements in understanding of polymer tribology: friction, wear, and lubrication. Further, viscoelasticity of PBMs complicates characterization of their behavior. Using data from micro-scratch testing, it was determined that viscoelastic recovery (healing) in sliding wear is independent of the indenter force within a defined range of load values. Strain hardening in sliding wear was observed for all materials—including polymers and composites with a wide variety of chemical structures—with the exception of polystyrene (PS). The healing in sliding wear was connected to free volume in polymers by using pressure- volume-temperature (P-V-T) results and the Hartmann equation of state. A linear relationship was found for all polymers studied with again the exception of PS. The exceptional behavior of PS has been attributed qualitatively to brittleness. -
(BME 541) Mechanical Prosperities of Biomaterials Experiment #1 Tensile Test
BioMechanics and BioMaterials Lab (BME 541) Mechanical Prosperities of Biomaterials Experiment #1 Tensile Test Objectives 1. To be familiar with the universal testing machine(810LE4) and provide a practical exercise for using it to determine the mechanical properties of different materials. 2. To understand the principle of tensile test. 3. To understand the Stress-Strain curve and learn how to use it in determining various mechanical properties of different materials (Aluminum, Copper and PMMA): modulus of elasticity, yield strength, ultimate tensile strength and elongation (ductility). Background Mechanical properties are of interest to engineers utilizing materials in any application where forces are applied. Three fundamental mechanical properties of materials are the elastic modulus (E), the yield point ( σy), and the ultimate strength ( σult ). A tensile test, also known as tension test, is probably the most fundamental type of mechanical test you can perform on material to recognize its strength and its mechanical behavior. Tension test, in which a strip or cylinder of the material, having length L and cross-sectional area A, is anchored at one end and subjected to an axial load P (a load acting along the specimen’s long axis) at the other (uniaxial tensile load). As the load is increased gradually, the axial deflection δ of the loaded end will increase also. Eventually the test specimen breaks or does something else catastrophic, often fracturing suddenly into two or more pieces. The strain resulting from the stress applied is proportional to the stress and is directly related to it with a proportionality constant called the Elastic Modulus/ Young’s Modulus. -
Study on the Effect of Energy-Input on the Joint Mechanical Properties of Rotary Friction-Welding
metals Article Study on the Effect of Energy-Input on the Joint Mechanical Properties of Rotary Friction-Welding Guilong Wang 1,2, Jinglong Li 1, Weilong Wang 1, Jiangtao Xiong 1 and Fusheng Zhang 1,* 1 Shaanxi Key Laboratory of Friction Welding Technologies, Northwestern Polytechnical University, Xi’an 710072, China; [email protected] (G.W.); [email protected] (J.L.); [email protected] (W.W.); [email protected] (J.X.) 2 State Key Laboratory of Solidification Processing, Northwestern Polytechnical University, Xi’an 710072, China * Correspondence: [email protected]; Tel.: +86-029-8849-1426 Received: 17 October 2018; Accepted: 3 November 2018; Published: 6 November 2018 Abstract: The objective of the present study is to investigate the effect of energy-input on the mechanical properties of a 304 stainless-steel joint welded by continuous-drive rotary friction-welding (RFW). RFW experiments were conducted over a wide range of welding parameters (welding pressure: 25–200 MPa, rotation speed: 500–2300 rpm, welding time: 4–20 s, and forging pressure: 100–200 MPa). The results show that the energy-input has a significant effect on the tensile strength of RFW joints. With the increase of energy-input, the tensile strength rapidly increases until reaching the maximum value and then slightly decreases. An empirical model for energy-input was established based on RFW experiments that cover a wide range of welding parameters. The accuracy of the model was verified by extra RFW experiments. In addition, the model for optimal energy-input of different forging pressures was obtained. To verify the accuracy of the model, the optimal energy-input of a 170 MPa forging pressure was calculated. -
Mechanical Properties of Biomaterials
Mechanical Properties of Biomaterials Academic Resource Center Determining Biomaterial Mechanical Properties • Tensile and Shear properties • Bending properties • Time dependent properties Tensile and Shear properties • Types of forces that can be applied to material: a) Tensile b) Compressive c) Shear d) Torsion Tensile Testing • Force applied as tensile, compressive, or shear. • Parameters measured: Engineering stress (σ) and Engineering strain (ԑ). • σ = F/A0 : Force applied perpendicular to the cross section of sample • ԑ = (li-l0)/l0: l0 is the length of sample before loading, li is the length during testing. Compression Testing • Performed mainly for biomaterials subjected to compressive forces during operation. E.g. orthopedic implants. • Stress and strain equations same as for tensile testing except force is taken negative and l0 larger than li. • Negative stress and strain obtained. Shear Testing • Forces parallel to top and bottom faces • Shear stress (τ) = F/A0 • Shear strain (γ)= tanθ ; θ is the deformation angle. • In some cases, torsion forces may be applied to sample instead of pure shear. Elastic Deformation • Material 1: Ceramics • Stress proportional to strain. • Governed by Hooke’s law: σ = ԑE; τ=Gγ • E :Young’s modulus G: Shear modulus - measure of material stiffness. • Fracture after applying small values of strain: ceramics are brittle in nature. Elastic and Plastic deformation. • Material 2: Metal • Stress proportional to strain with small strain; elastic deformation. • At high strain, stress increases very slowly with increased strain followed by fracture: Plastic deformation. Elastic and Plastic deformation. • Material 3: Plastic deformation polymer • Stress proportional to strain with small strain; elastic deformation. • At high strain, stress nearly independent of strain, shows slight increase: Plastic deformation. -
Tensile Testing of Metallic Materials: a Review
TENSTAND - WORK PACKAGE 1 - FINAL REPORT CONTRACT N° : G6RD-CT-2000-00412 PROJECT N° : GRD1-2000-25021 ACRONYM : TENSTAND TITLE : Tensile Testing of Metallic Materials: A Review PROJECT CO-ORDINATOR : NPL Management Ltd PARTNERS : National Physical Laboratory, Teddington, UK INSTRON, High Wycombe, UK BAM, Berlin, Germany ZWICK, Ulm, Germany Denison Mayes Group, Leeds, UK Thyssen Krupp Stahl, Duisburg, Germany ARCELOR, Florange, France ISQ-Instituto de Soldadura e Qualidade, Oeires, Portugal University of Strathclyde, Glasgow, UK Trinity College, Dublin, Ireland AGH, Kraków, Poland AUTHORS : Malcolm S Loveday, Tom Gray and Johannes Aegerter REPORTING PERIOD: From 1st February 2001 TO 30th April 2004 PROJECT START DATE : 1st February 2001 DURATION : 39 months Date of issue of this report : April 2004 Project funded by the European Community under the ‘Competitive and Sustainable Growth’ Programme (1998- 2002) 07/10/05 Rev 10 by LOVEDAY,GRAY & Aegerter Tensile test of Metallic Materials : A Review TENSTAND (M.S.L) 1 Tensile Testing of Metallic Materials: A Review. By Malcolm S Loveday,1 Tom Gray2 and Johannes Aegerter3 (April 2004) 1. Beta Technology Consultant, c/o National Physical Laboratory, Teddington, Middlesex, TW11 0LW, UK 2. Dept. Mechanical Engineering, University of Strathclyde, Glasgow, Scotland, G1 1XJ 3. Hydro Aluminium RDB, Georg-von-Boeselager Str 21, 53117 Bonn Postfach 24 68, 53014 Bonn, Germany [ See Foreword] Abstract The strength of a material under tension has long been regarded as one of the most important characteristics required for design, production quality control and life prediction of industrial plant. Standards for tensile testing are amongst those first published and the development of such Standards continues today. -
Tensile Testing Experiment Sheet
BURSA TECHNICAL UNIVERSITY FACULTY OF NATURAL SCIENCES, ARCHITECTURE AND ENGINEERING DEPARTMENT OF MECHANICAL ENGINEERING MECHANICAL ENGINEERING LABORATORY TENSILE TESTING EXPERIMENT SHEET Asst. Prof. Dr. Onur SARAY Asst. Prof. Dr. Sukhwinder Kaur BHULLAR Res. Asst. Emre DEMİRCİ BURSA, 2017 TENSILE TESTING 1. OBJECTIVES The purpose of this laboratory is to determine characteristic mechanical properties of metals, by performing uniaxial tensile tests using given specimens. 2. GENERAL INFORMATION Tensile Tests are performed for several reasons. Tensile properties frequently are included in material specifications to ensure quality. Tensile properties often are measured during development of new materials and processes, so that different materials and processes can be compared. Also, tensile properties often are used to predict the behavior of a material under forms of loading other than uniaxial tension. Material selection is a central task of the overall design process. Engineers must decide which materials are the most appropriate for a particular design. The tensile test is an important standard engineering procedure useful to characterize some relevant elastic and plastic variables related to the mechanical behaviour of materials. Elastic Properties: When a solid material is subjected to small stresses, the bonds between the atoms are stretched. When the stress is removed, the bonds relax and the material returns to its original shape. This reversible deformation is called elastic deformation. In the elastic region, stress and strain are related to each other linearly and characterized by Young’s modulus, 퐸 and the Poisson’s ratio 푣. 휎푎푥푖푎푙(푒푙푎푠푡푖푐) 퐸 = 휀푎푥푖푎푙(푒푙푎푠푡푖푐) 휎푎푥푖푎푙: engineering stress along the loading axis, 휀푎푥푖푎푙: engineering strain. 퐹 휎푎푥푖푎푙 = 퐴0 where 퐹 is the tensile force and 퐴0 is the initial cross-sectional area of the gage section. -
Rotary Friction Welding of Inconel 718 to Inconel 600
metals Article Rotary Friction Welding of Inconel 718 to Inconel 600 Ateekh Ur Rehman * , Yusuf Usmani, Ali M. Al-Samhan and Saqib Anwar Department of Industrial Engineering, College of Engineering, King Saud University, Riyadh 11451, Saudi Arabia; [email protected] (Y.U.); [email protected] (A.M.A.-S.); [email protected] (S.A.) * Correspondence: [email protected]; Tel.: +966-1-1469-7177 Abstract: Nickel-based superalloys exhibit excellent high temperature strength, high temperature corrosion and oxidation resistance and creep resistance. They are widely used in high temperature applications in aerospace, power and petrochemical industries. The need for economical and efficient usage of materials often necessitates the joining of dissimilar metals. In this study, dissimilar welding between two different nickel-based superalloys, Inconel 718 and Inconel 600, was attempted using rotary friction welding. Sound metallurgical joints were produced without any unwanted Laves or delta phases at the weld region, which invariably appear in fusion welds. The weld thermal cycle was found to result in significant grain coarsening in the heat effected zone (HAZ) on either side of the dissimilar weld interface due to the prevailing thermal cycles during the welding. However, fine equiaxed grains were observed at the weld interface due to dynamic recrystallization caused by severe plastic deformation at high temperatures. In room temperature tensile tests, the joints were found to fail in the HAZ of Inconel 718 exhibiting good ultimate tensile strength (759 MPa) without a significant loss of tensile ductility (21%). A scanning electron microscopic examination of the fracture surfaces revealed fine dimpled rupture features, suggesting a fracture in a ductile mode. -
Tension Testing of Metallic Materials1
Designation: E8/E8M − 13a American Association State Highway and Transportation Officials Standard AASHTO No.: T68 An American National Standard Standard Test Methods for Tension Testing of Metallic Materials1 This standard is issued under the fixed designation E8/E8M; the number immediately following the designation indicates the year of original adoption or, in the case of revision, the year of last revision. A number in parentheses indicates the year of last reapproval. A superscript epsilon (´) indicates an editorial change since the last revision or reapproval. This standard has been approved for use by agencies of the Department of Defense. 1. Scope* 2. Referenced Documents 1.1 These test methods cover the tension testing of metallic 2.1 ASTM Standards:2 materials in any form at room temperature, specifically, the A356/A356M Specification for Steel Castings, Carbon, Low methods of determination of yield strength, yield point Alloy, and Stainless Steel, Heavy-Walled for Steam Tur- elongation, tensile strength, elongation, and reduction of area. bines 1.2 The gauge lengths for most round specimens are re- A370 Test Methods and Definitions for Mechanical Testing quired to be 4D for E8 and 5D for E8M. The gauge length is of Steel Products the most significant difference between E8 and E8M test B557 Test Methods for Tension Testing Wrought and Cast specimens. Test specimens made from powder metallurgy Aluminum- and Magnesium-Alloy Products (P/M) materials are exempt from this requirement by industry- B557M Test Methods for Tension Testing Wrought and Cast wide agreement to keep the pressing of the material to a Aluminum- and Magnesium-Alloy Products (Metric) specific projected area and density. -
A Comparison of the Tensile and Bending Properties of Dental Gold Wires D
A COMPARISON OF THE TENSILE AND BENDING PROPERTIES OF DENTAL GOLD WIRES D. F. TAYLOR, M.S.E.,* AND F. A. PEYTON, D.Sc. School of Dentistry, University of Michigan, Ann Arbor, Mich. INTRODUCTION M ODERN dental practice makes wide use of precious metal alloys in wire form as partial denture clasps and as orthodontic appliances. When used in such applications, these alloys are subject only to bend loading and never to pure tensile loading. For this reason, there has long been a feeling within the dental profession that the tensile test for wires was somewhat in- appropriate and might be replaced advantageously by a bend test. However, the absence of any previous correlation between the test values obtained from the two types of loading, as well as the large amount of effort represented by collected tensile data on these alloys, has heretofore prevented any serious consideration of a possible change of standards from one test to the other. The technical representatives of several manufacturers have displayed a con- tinuing interest in the development of possible relationships between tension and bend tests. This interest was expressed through the loan, by these manu- facturers, of gold alloy wires of high intrinsic value for use in this investiga- tion. Further support was received from the Office of Naval Research which sponsored the project as a part of its program of research on the properties of restorative dental materials. The specific purpose of this investigation was to determine what correla- tion, if any, existed between the mechanical properties of wrought gold alloys as found in a standard tensile test and those as found in a bend test. -
Enghandbook.Pdf
785.392.3017 FAX 785.392.2845 Box 232, Exit 49 G.L. Huyett Expy Minneapolis, KS 67467 ENGINEERING HANDBOOK TECHNICAL INFORMATION STEELMAKING Basic descriptions of making carbon, alloy, stainless, and tool steel p. 4. METALS & ALLOYS Carbon grades, types, and numbering systems; glossary p. 13. Identification factors and composition standards p. 27. CHEMICAL CONTENT This document and the information contained herein is not Quenching, hardening, and other thermal modifications p. 30. HEAT TREATMENT a design standard, design guide or otherwise, but is here TESTING THE HARDNESS OF METALS Types and comparisons; glossary p. 34. solely for the convenience of our customers. For more Comparisons of ductility, stresses; glossary p.41. design assistance MECHANICAL PROPERTIES OF METAL contact our plant or consult the Machinery G.L. Huyett’s distinct capabilities; glossary p. 53. Handbook, published MANUFACTURING PROCESSES by Industrial Press Inc., New York. COATING, PLATING & THE COLORING OF METALS Finishes p. 81. CONVERSION CHARTS Imperial and metric p. 84. 1 TABLE OF CONTENTS Introduction 3 Steelmaking 4 Metals and Alloys 13 Designations for Chemical Content 27 Designations for Heat Treatment 30 Testing the Hardness of Metals 34 Mechanical Properties of Metal 41 Manufacturing Processes 53 Manufacturing Glossary 57 Conversion Coating, Plating, and the Coloring of Metals 81 Conversion Charts 84 Links and Related Sites 89 Index 90 Box 232 • Exit 49 G.L. Huyett Expressway • Minneapolis, Kansas 67467 785-392-3017 • Fax 785-392-2845 • [email protected] • www.huyett.com INTRODUCTION & ACKNOWLEDGMENTS This document was created based on research and experience of Huyett staff. Invaluable technical information, including statistical data contained in the tables, is from the 26th Edition Machinery Handbook, copyrighted and published in 2000 by Industrial Press, Inc. -
Mechanical Testing of Plastic, Rubber, Elastomer, and Composite Materials by Steven Tysoe Ph
Discover The Answers ™ Mechanical Testing of Plastic, Rubber, Elastomer, and Composite Materials By Steven Tysoe Ph. D. and Jim Zwynenburg Associated Polymer Labs (APL) adds another electromechanical Universal Testing Machine (UTM) to the Mechanical Properties Testing Laboratory. The new Shimadzu AGS-X 500mm extended frame UTM is perfect for testing polymeric materials including plastics, rubbers, elastomers, and composites. The Shimadzu AGS-X 10kN load frame with Trapezium Control Software allows the operator to stretch (tensile), bend (flexural), compress or squash (compression), or pull (shear) a specimen until it moves, yields or to the breaking point. Tensile testing is performed in accordance with American Society for Testing and Materials (ASTM) Methods D882, D638, D412, D1708 and other custom test methods designed to meet your requirements and needs. Tensile properties are key indicators of the strength of a material. Results from tensile testing include the yield point, tensile (Young’s) modulus, tensile strength, elongation, break point, and toughness. Flexural testing is performed in accordance with ASTM Method D790 to measure the flexural modulus. Many brittle materials are flexed to the breaking point in order to measure the flexural strength. The test is stopped when the specimen reaches 5% deflection or the specimen breaks before 5% deflection is reached. The flexural test measures the force required to bend a beam at a specific rate. Flexural modulus is an indication of a material’s stiffness when bent on a three-point apparatus. The three point bending fixture supports the specimen and the load is applied to the center by the loading nose producing three point bending at a specified rate. -
Bending Tests Impact Strength Test Tensile/Compression Machine Universal Testing Machine
STEEL 18 UNIVERSAL TESTING MACHINE 18.1 TENSILE/COMPRESSION MACHINE 18.2 IMPACT STRENGTH TEST 18.3 BENDING TESTS 2.4 INDEX ITEMS PAGE Universal testing machine page 471 Alternate folding testing machine....................... 496 Bending and straightening test machine............ 493-495 Calibration load cell............................................ 481 "Charpy" Pendulum............................................ 490-492 Cut-off machine.................................................. 496 Eurotronic........................................................... 486-487 Tensile/compression Extensometer..................................................... 475 Graph recorder................................................... 475 machine page 485 Machine for tensile and compression test (100 kN)................................. 488-489 Machine for tensile and compression test (500 kN)................................. 485-487 Machine for tensile test (600 kN)....................... 479-481 Impact strength test page 490 Machine for tensile test (1000 kN)..................... 482-484 Set for testing at low temperatures.................... 492 Universal testing machine 600 kN..................... 471-475 Tracing machine................................................ 496 Bending tests page 493 470 18.1 UNIVERSAL TESTING MACHINE HYDRAULIC UNIVERSAL TESTING MACHINES "F 060/U - F 060" The F 060/U essentially comprises a pair of vertical columns The software supplied with the machine serves for testing and an inversion frame supported by a hydraulic