Externally Blown Flap Noise Research '
Total Page:16
File Type:pdf, Size:1020Kb
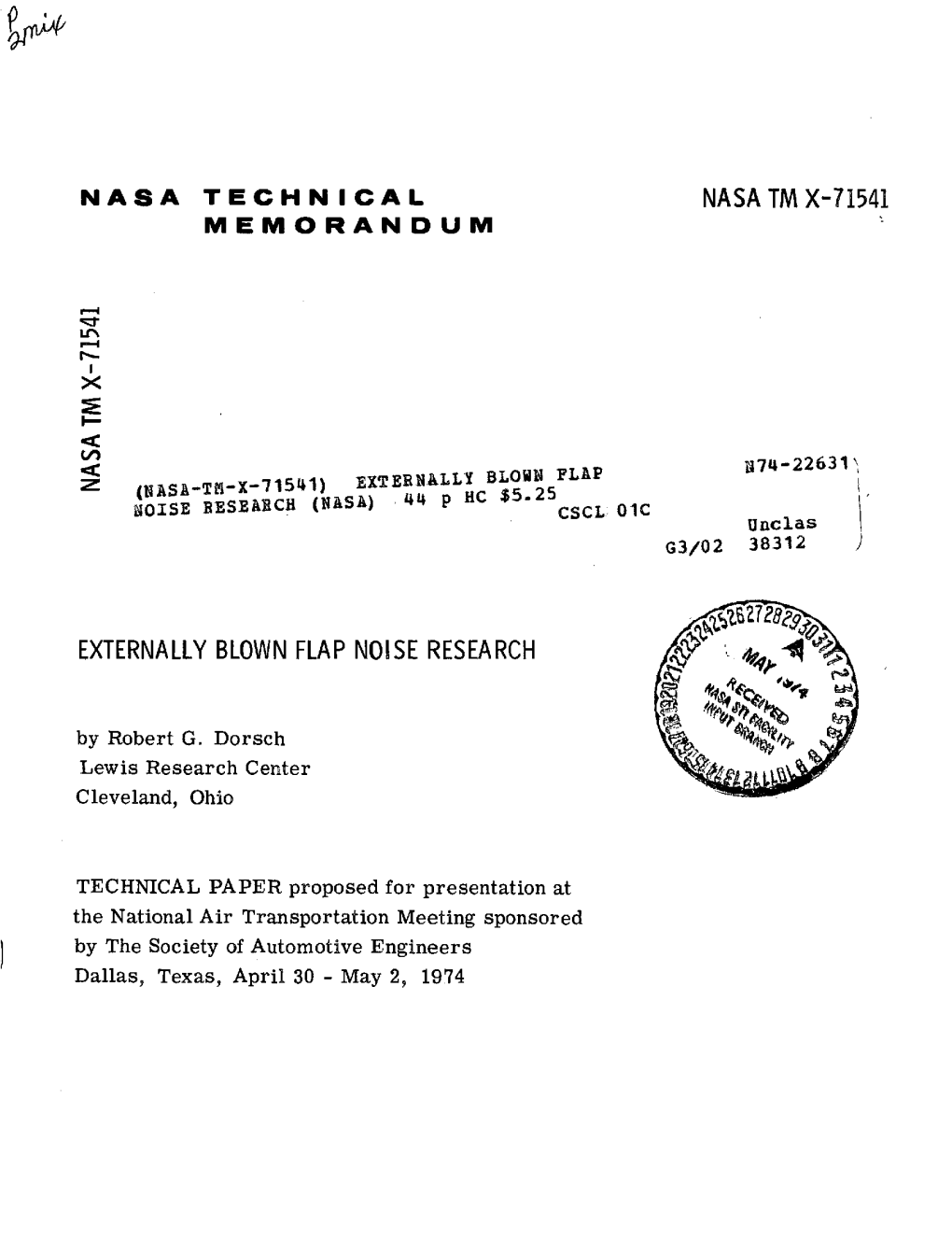
Load more
Recommended publications
-
A Flight Simulation Study of the Simultaneous Non-Interfering
A FLIGHT SIMULATION STUDY OF THE SIMULTANEOUS NON-INTERFERING AIRCRAFT APPROACH A Thesis presented to the Faculty of California Polytechnic State University, San Luis Obispo In Partial Fulfillment of the Requirements for the Degree Master of Science in Aerospace Engineering by Brian Reel May 2009 © 2009 Brian Hogan Reel ALL RIGHTS RESERVED ii COMMITTEE MEMBERSHIP TITLE: A Flight Simulation Study of the Simultaneous Non-Interfering Aircraft Approach AUTHOR: Brian Hogan Reel DATE SUBMITTED: May 2009 COMMITTEE CHAIR: Dr. Daniel Biezad, Cal Poly Aerospace Engineering COMMITTEE MEMBER: Craig Hange, NASA AMES COMMITTEE MEMBER: Dr. Eric Mehiel, Cal Poly Aerospace Engineering COMMITTEE MEMBER: Dr. Frank Owen, Cal Poly Mechanical Engineering COMMITTEE MEMBER: Dr. Kurt Colvin, Cal Poly Industrial/Manufacturing Engineering iii ABSTRACT A Flight Simulation Study of the Simultaneous Non-Interfering Aircraft Approach Brian Hogan Reel Using a new implementation of a NASA flight simulation of the Quiet Short-Haul Research Aircraft, autopilots were designed to be capable of flying both straight in (ILS) approaches, and circling (SNI) approaches. A standard glideslope coupler was sufficient for most conditions, but a standard Proportional-Integral-Derivative (PID) based localizer tracker was not sufficient for maintaining a lateral track on the SNI course. To track the SNI course, a feed-forward system, using GPS steering provided much better results. NASA and the FAA embrace the concept of a Simultaneous, Non-Interfering (SNI) approach as a way to increase airport throughput while reducing the noise footprints of aircraft on approach. The NASA concept for the SNI approach for Short Takeoff and Landing (STOL) aircraft involves a straight in segment flown above the flight path of a normal approach, followed by a spiraling descent to the runway. -
Propulsion and Flight Controls Integration for the Blended Wing Body Aircraft
Cranfield University Naveed ur Rahman Propulsion and Flight Controls Integration for the Blended Wing Body Aircraft School of Engineering PhD Thesis Cranfield University Department of Aerospace Sciences School of Engineering PhD Thesis Academic Year 2008-09 Naveed ur Rahman Propulsion and Flight Controls Integration for the Blended Wing Body Aircraft Supervisor: Dr James F. Whidborne May 2009 c Cranfield University 2009. All rights reserved. No part of this publication may be reproduced without the written permission of the copyright owner. Abstract The Blended Wing Body (BWB) aircraft offers a number of aerodynamic perfor- mance advantages when compared with conventional configurations. However, while operating at low airspeeds with nominal static margins, the controls on the BWB aircraft begin to saturate and the dynamic performance gets sluggish. Augmenta- tion of aerodynamic controls with the propulsion system is therefore considered in this research. Two aspects were of interest, namely thrust vectoring (TVC) and flap blowing. An aerodynamic model for the BWB aircraft with blown flap effects was formulated using empirical and vortex lattice methods and then integrated with a three spool Trent 500 turbofan engine model. The objectives were to estimate the effect of vectored thrust and engine bleed on its performance and to ascertain the corresponding gains in aerodynamic control effectiveness. To enhance control effectiveness, both internally and external blown flaps were sim- ulated. For a full span internally blown flap (IBF) arrangement using IPC flow, the amount of bleed mass flow and consequently the achievable blowing coefficients are limited. For IBF, the pitch control effectiveness was shown to increase by 18% at low airspeeds. -
The Influence of Wing Loading on Turbofan Powered Stol Transports with and Without Externally Blown Flaps
https://ntrs.nasa.gov/search.jsp?R=19740005605 2020-03-23T12:06:52+00:00Z NASA CONTRACTOR NASA CR-2320 REPORT CXI CO CNI THE INFLUENCE OF WING LOADING ON TURBOFAN POWERED STOL TRANSPORTS WITH AND WITHOUT EXTERNALLY BLOWN FLAPS by R. L. Morris, C. JR. Hanke, L. H. Pasley, and W. J. Rohling Prepared by THE BOEING COMPANY WICHITA DIVISION Wichita, Kans. 67210 for Langley Research Center NATIONAL AERONAUTICS AND SPACE ADMINISTRATION • WASHINGTON, D. C. • NOVEMBER 1973 1. Report No. 2. Government Accession No. 3. Recipient's Catalog No. NASA CR-2320 4. Title and Subtitle 5. Reoort Date November. 1973 The Influence of Wing Loading on Turbofan Powered STOL Transports 6. Performing Organization Code With and Without Externally Blown Flaps 7. Author(s) 8. Performing Organization Report No. R. L. Morris, C. R. Hanke, L. H. Pasley, and W. J. Rohling D3-8514-7 10. Work Unit No. 9. Performing Organization Name and Address The Boeing Company 741-86-03-03 Wichita Division 11. Contract or Grant No. Wichita, KS NAS1-11370 13. Type of Report and Period Covered 12. Sponsoring Agency Name and Address Contractor Report National Aeronautics and Space Administration Washington, D.C. 20546 14. Sponsoring Agency Code 15. Supplementary Notes This is a final report. 16. Abstract The effects of wing loading on the design of short takeoff and landing (STOL) transports using (1) mechanical flap systems, and (2) externally blown flap systems are determined. Aircraft incorporating each high-lift method are sized for Federal Aviation Regulation (F.A.R.) field lengths of 2,000 feet, 2,500 feet, and 3,500 feet, and for payloads of 40, 150, and 300 passengers, for a total of 18 point-design aircraft. -
QUIET CLEAN SHORT-HAUL EXPERIMENTAL ENGINE (QCSEE) Preliminary Under the Wing Flight Propulsion System Analysis Report
NASA CR-134868 QUIET CLEAN SHORT-HAUL EXPERIMENTAL ENGINE (QCSEE) Preliminary Under the Wing Flight Propulsion System Analysis Report February 1976 by Advanced Engineering & Technology Programs Department General Electric Company (IASA-CR-134868) QUIET CLEAN SHORT-HAUL NS0-15088 EXPERIMENTAL ENGINE (QCSEE) PRELIMINARY 1UNDER THE WING FLIGHT PROPULSION SYSTEM lANALYSIS REPORT '(General Electric Co.) "nclas '1261 p HC A12/MF A01 CSCL 21E G3/07 33465 Prepared For National Aeronautics and Space Admiistrati Contract NAS3-18021 FOR EARLY DOMESTIC DISSEMNATION-f9, < %,tj64 Because of its significant early commercial potential, th'is information, which has been developed under a U. S. Government program, is being disseminated within the United States in advance of general publication. This information may be dupli cated and used by the recipient with the express limitation that it not be published. Release of this information to other domestic parties by the recipient shall be made subject to these limitations. Foreign release may be made only with prior NASA approval and appropriate export licenses. This legend shall be marked on any reproduction of this information in whole or in Datepart. forfa general rel ease,)- 0A16/Zyj/ 1.Rep No. 2. Government Accession No. 3. Recipient's Catalog No: NASA CR-134868 4 Titleand Subtitle 5.Report Date QUIET CLEAN SHORT-HAUL EXPERIMENTAL ENGINE PRELIMINARY February 1976 UNDER-THE-WING FLIGHT PROPULSION SYSTEM ANALYSIS REPORT 6. Performing Organization Code 7. Author(s) D. F. Howard, et al 8.Performing Organization Report No. Advanced Engineering and Technology Programs Dept R75AEG349 Group Engineering Division 10. Work Unit No 9 Performing Organization Name and Address General Electric Company 1 Jimson Road 11. -
Synergistic Airframe-Propulsion Interactions and Integrations
NASA/TM-1998-207644 Synergistic Airframe-Propulsion Interactions and Integrations A White Paper Prepared by the 1996-1997 Langley Aeronautics Technical Committee Steven F. Yaros, Matthew G. Sexstone, Lawrence D. Huebner, John E. Lamar, Robert E. McKinley, Jr., Abel 0. Torres, Casey L. Burley, Robert C. Scott, and William J. Small Langley Research Center, Hampton, Virginia National Aeronautics and Space Administration Langley Research Center Hampton, Virginia 23681-2199 March 1998 Available from the following: NASA Center for AeroSpace Information (CASH National Technical Information Service (NTIS) 800 Elkridge Landing Road 5285 Port Royal Road Linthicum Heights, MD 21090-2934 Springfield, VA 22161-2171 (703) 487-4650 (301) 621-0390 Executive Summary This white paper documents the work of the NASA Langley Aeronautics Technical Committee from July 1996 through March 1998 and addresses the subject of Synergistic Airframe-Propulsion Interactions and Integrations (SnAPII). It is well known that favorable Propulsion Airframe Integration (PAD is not only possible but Mach number dependent -- with the largest (currently utilized) benefit occurring at hypersonic speeds. At the higher speeds the lower surface of the airframe actually serves as an external precompression surface for the inlet flow. At the lower supersonic Mach numbers and for the bulk of the commercial civil transport fleet, the benefits of SnAPII have not been as extensively explored. This is due primarily to the separateness of the design process for airframes and propulsion systems, with only unfavorable interactions addressed. The question 'How to design these two systems in such a way that the airframe needs the propulsion and the propulsion needs the airframe?' is the fun- damental issue addressed in this paper. -
Nasa Technical Note Nasa Tn D-7497 a Compilation And
AND NASA TECHNICAL NOTE NASA TN D-7497 N74-196 7 1 (NASA-TN-D-7497 ) A COMPILATION AND ANALYSIS OF TYPICAL APPEOACH AND LANDING FOR A SIMULATOR STUDY OF AN DATA Unclas EXTERNALLY BLOWN FLAP STOL AIRCRAFT CSCL 01C H1/02 34586 <r (NASA) 24 p BC $3.00 A COMPILATION AND ANALYSIS OF TYPICAL APPROACH AND LANDING DATA FOR A SIMULATOR STUDY OF AN EXTERNALLY BLOWN FLAP STOL AIRCRAFT by David B. Middleton and Hugh P. Bergeron Langley Research Center oWo10o Hampton, Va. 23665 NATIONAL AERONAUTICS AND SPACE ADMINISTRATION * WASHINGTON, D. C. * APRIL 1974 1. Report No. 2. Government Accession No. 3. Recipient's Catalog No. NASA TN D-7497 4. Title and Subtitle 5. Report Date A COMPILATION AND ANALYSIS OF TYPICAL APPROACH April 1974 AND LANDING DATA FOR A SIMULATOR STUDY OF AN 6. Performing Organization Code EXTERNALLY BLOWN FLAP STOL AIRCRAFT Report No. 7. Author(s) 8. Performing Organization David B. Middleton and Hugh P. Bergeron L-9142 10. Work Unit No. 9. Performing Organization Name and Address 501-29-13-01 NASA Langley Research Center 11. Contract or Grant No. Hampton, Va. 23365 13. Type of Report and Period Covered 12. Sponsoring Agency Name and Address Technical Note National Aeronautics and Space Administration 14. Sponsoring Agency Code Washington, D.C. 20546 15. Supplementary Notes 16. Abstract A piloted simulation study has been made of typical landing approaches with an externally blown flap STOL aircraft to ascertain a realistic dispersion of parameter values at both the flare window and touchdown. The study was performed on a fixed-base simulator using standard cockpit instrumentation. -
Externally Blown Flap Impingenent Parameter
EXTERNALLY BLOWN FLAP IMPINGENENT PARAMETER Danny R. Hoad Langley Directorate, U.S. Army Air Mobility R&D Laboratory -q4 SUMMARY This paper presents a comparison of the performance of two externally .:I blown flap (EBF) wind-tunnel models with an engine-exhaust flap impinge- ment correlation parameter. One model was a four-engine EBF triple- slotted flap transport. Isolated engine wake surveys were conducted to define the wake properties of give separate engine configurations for which performance data were available. The other model was a two-engine EBF trans- port for which the engine wake properties were estimated. The ccrrelation parameter was a function of engine-exhaust dynamic pressure at the flap location, area of engine-exhaust flap impingement, total exhaust area at the flap location, and engice thrust. The distribution of dynamic pressure for the first model was measured ; however, the distribution for the second model was assumed to be uniform. ;:.J ;:.J ., -,w --:.-. Numerous concepts have been developed for achieving short-take-off-and- .,:.:i landing (STOL) performance. One approach which was selected for an ~dvanced .i medium STOL transport (AMST) configuration, the YC--15, is the externally >'*.- I blown flap (EBF). Most EBF concept development h~.sbeen achieved with experimental investigations (refs. 1 to 8) of various engine and airframe conf iguratians. While very limited acdyses (refs. 9 to 11) of these config- urations have been attempted, some work has been done with an empirical analysis using a correlation parameter (impingement parameter) based on the vertical distance that the fls~trailing edge extends into the jet exhaust from the engine center line and the radius of the jet exhaust at the flap trailing edge. -
Development of Advanced High Lift Leading Edge Technology for Laminar Flow Wings
Development of Advanced High Lift Leading Edge Technology for Laminar Flow Wings Michelle M. Bright*, Andrea Korntheuer†, Steve Komadina‡ Northrop Grumman Aerospace Systems, El Segundo, CA, 90245, USA John C. Lin§ NASA Langley Research Center, Hampton, VA, 23681, USA Abstract This paper describes the Advanced High Lift Leading Edge (AHLLE) task performed by Northrop Grumman Systems Corporation, Aerospace Systems (NGAS) for the NASA Subsonic Fixed Wing project in an effort to develop enabling high-lift technology for laminar flow wings. Based on a known laminar cruise airfoil that incorporated an NGAS- developed integrated slot design, this effort involved using Computational Fluid Dynamics (CFD) analysis and quality function deployment (QFD) analysis on several leading edge concepts, and subsequently down-selected to two blown leading-edge concepts for testing. A 7-foot-span AHLLE airfoil model was designed and fabricated at NGAS and then tested at the NGAS 7’ x 10’ Low Speed Wind Tunnel in Hawthorne, CA. The model configurations tested included: baseline, deflected trailing edge, blown deflected trailing edge, blown leading edge, morphed leading edge, and blown/morphed leading edge. A successful demonstration of high lift leading edge technology was achieved, and the target goals for improved lift were exceeded by 30% with a maximum section lift coefficient (Cl) of 5.2. Maximum incremental section lift coefficients (ΔCl) of 3.5 and 3.1 were achieved for a blown drooped (morphed) leading edge concept and a non-drooped leading edge blowing concept, respectively. The most effective AHLLE design yielded an estimated 94% lift improvement over the conventional high lift Krueger flap configurations while providing laminar flow capability on the cruise configuration. -
Technische Universität München a Method for the Comparison Of
Technische Universität München Institut für Luft-und Raumfahrt A Method for the Comparison of Transport Aircraft with Blown Flaps Corin Gologan Vollständiger Abdruck der von der Fakultät für Maschinenwesen der Technischen Universität München zur Erlangung des akademischen Grades eines Doktor-Ingenieurs (Dr.-Ing.) genehmigten Dissertation. Vorsitzender: Univ.-Prof. Dr.-Ing. Mirko Hornung Prüfer der Dissertation: 1. Hon.-Prof. Dr.-Ing. Dr. h.c. Dieter Schmitt 2. Univ.-Prof. Dr.-Ing. Horst Baier Die Dissertation wurde am 10.12.2009 bei der Technischen Universität München eingereicht und durch die Fakultät für Maschinenwesen am 07.09.2010 angenommen. Für Alina, Daniela und Stefan V VI Vorwort Diese Arbeit entstand während meiner Zeit als wissenschaftlicher Mitarbeiter am Bauhaus Luftfahrt. Die ausgezeichneten Rahmenbedingungen am Bauhaus Luftfahrt waren eine wesentliche Grundlage für den Erfolg dieser Arbeit. Besonders bedanke ich mich bei Herrn Hon.-Prof. Dr.-Ing. Dieter Schmitt, der mir als Doktorvater mit stets kompetenten und hilfreichen Ratschlägen zur Seite stand. Ebenso danke ich Frau Dr. Anita Linseisen für ihre Unterstützung in sämtlichen nicht-technischen Angelegenheiten. Bei Herrn Prof. Dr.-Ing. Klaus Broichhausen bedanke ich mich dafür, dass er mich davon überzeugt hat, am Bauhaus Luftfahrt anzufangen und für die Unterstützung bei der anfänglichen Themenfindung. Herrn Univ.-Prof. Dr.-Ing. Horst Baier, sei gedankt für die freundliche Übernahme der zweiten Begutachtung dieser Arbeit und Herrn Univ.-Prof. Dr.-Ing. Mirko Hornung für die freundliche Übernahme des Prüfungsvorsitzes. Am Bauhaus Luftfahrt war es mir möglich, mit sehr erfahrenen Experten aus der Industrie und Wissenschaft zusammenzukommen. Ich danke Herrn Jan van Toor von der EADS dafür, dass er sich regelmäßig an Reviews beteiligt hat und mit seiner Expertise wichtige Impulse für diese Arbeit gegeben hat. -
Numerical Simulation of Transonic Circulation Control
AIAA 2015-1709 53rd AIAA Aerospace Sciences Meeting, AIAA Science and Technology Forum, 5-9 Jan 2015, Kissimee, Florida Numerical Simulation of Transonic Circulation Control M. Forster∗ and R. Steijly School of Engineering, University of Liverpool, L69 3GH, U.K. Simulations of circulation control via blowing over Coanda surfaces at freestreams up to Mach 0.8 are presented. Validation was conducted against experiments performed at NASA on a 6 percent thick elliptical circulation control aerofoil, which demonstrates the necessary grid requirements and compares between two-equation turbulence models of the k − ! family. It is found that simplifications to the experimental set up are detrimental to the results. In addition, the performance and sensitivity of several circulation control devices applied to a supercritical aerofoil are presented. It is shown that circulation control has the ability to match the performance of traditional control surfaces during regimes of attached flow at transonic speeds. Nomenclature α Angle of Attack, degrees y+ Non-Dimensional Wall Distance αAIL Aileron Deflection, degrees A Wing Surface Area, m2 Acronyms c Chord Length, m AOA Angle of Attack Cd Sectional Drag Coefficient CC Circulation Control Cl Sectional Lift Coefficient CFD Computational Fluid Dynamics Cm Sectional Pitching Moment Coefficient EARSM Explicit Algebraic Reynolds Stress Model m_j Vj Cµ Momentum Coefficient, EXP Experiment q1A Cp Pressure Coefficient FAST-MAC Fundamental Aerodynamics Subsonic/ M Mach Number Transonic-Modular Active Control m_j Jet Mass Flow Rate, kg/s GTRI Georgia Tech Research Institute q1 Freestream Dynamic Pressure, Pa HMB Helicopter Multi-Block CFD Code Re Reynolds Number PR Pressure Ratio U Velocity Component in Streamwise Direction, RANS Reynolds Averaged Navier-Stokes m/s SARC Spalart-Allmaras Rotation/Curvature UE Velocity at Boundary Layer Edge, m/s TDT Transonic Dynamics Tunnel Vj Jet Velocity, m/s UAV Uninhabited Air Vehicle ∗Ph.D. -
Aircraft Systems.Pdf
AERONAUTICAL ENGINEERING MRCET (UGC Autonomous) AIRCRAFT SYSTEMS COURSE FILE IV yr B.Tech I Sem (2019-2020) Prepared By Mr. Sachin Srivastava, Assist. Prof Department of Aeronautical Engineering MALLA REDDY COLLEGE OF ENGINEERING & TECHNOLOGY (Autonomous Institution UGC, Govt. of India) Affiliated to JNTU, Hyderabad, Approved by AICTE Accredited by NBA & NAAC, A Grade – ISO9001:2015Certified) Maisammaguda, Dhulapally (Post Via. Kompally), Secunderabad 500100, Telangana State, India. IV I B. Tech Aircraft Systems by Sachin Srivastava I AERONAUTICAL ENGINEERING MRCET (UGC Autonomous) MRCET VISION To become a model institution in the fields of Engineering, Technology and Management. To have a perfect synchronization of the ideologies of MRCET with challenging demands of International Pioneering Organizations. MRCET MISSION To establish a pedestal for the integral innovation, team spirit, originality and competence in the students, expose them to face the global challenges and become pioneers of Indian vision of modern society. MRCET QUALITY POLICY To pursue continual improvement of teaching learning process of Undergraduate and Post Graduate programs in Engineering & Management vigorously. To provide state of art infrastructure and expertise to impart the quality education. IV I B. Tech Aircraft Systems by Sachin Srivastava II AERONAUTICAL ENGINEERING MRCET (UGC Autonomous) PROGRAM OUTCOMES (PO s) Engineering Graduates will be able to: 1. Engineering knowledge: Apply the knowledge of mathematics, science, engineering fundamentals, and an -
Feasibility Study of Short Takeoff and Landing Urban Air Mobility Vehicles Using Geometric Programming
View metadata, citation and similar papers at core.ac.uk brought to you by CORE provided by DSpace@MIT FEASIBILITY STUDY OF SHORT TAKEOFF AND LANDING URBAN AIR MOBILITY VEHICLES USING GEOMETRIC PROGRAMMING Christopher Courtin, Michael Burton, Patrick Butler, Alison Yu, Parker D. Vascik and R. John Hansman This report presents research originally published under the same title at the 18th AIAA Aviation Technology, Integration, and Operations Conference in Atlanta, GA. Citations should be made to the original work with DOI: https://doi.org/10.2514/6.2018-4151 Report No. ICAT-2018-06 June 2018 MIT International Center for Air Transportation (ICAT) Department of Aeronautics & Astronautics Massachusetts Institute of Technology Cambridge, MA 02139 USA Feasibility Study of Short Takeo↵ and Landing Urban Air Mobility Vehicles using Geometric Programming Christopher Courtin⇤, Michael Burton†, Patrick Butler‡, Alison Yu§, Parker Vascik¶, John Hansmank Massachusetts Institute of Technology, Cambridge, 02139, USA Electric Short Takeo↵ and Landing (eSTOL) vehicles are proposed as a path towards implementing an Urban Air Mobility (UAM) network that reduces critical vehicle certifi- cation risks and o↵ers advantages in vehicle performance compared to the widely proposed Electric Vertical Takeo↵ and Landing (eVTOL) aircraft. An overview is given of the sys- tem constraints and key enabling technologies that must be incorporated into the design of the vehicle. The tradeo↵sbetweenvehicleperformanceandrunwaylengthareinves- tigated using geometric programming, a robust optimization framework. Runway lengths as short as 100-300 ft are shown to be feasible, depending on the level of technology and the desired cruise speed. The tradeo↵sbetweenrunwaylengthandthepotentialtobuild new infrastructure in urban centers are investigated using Boston as a representative case study.