Achieving Optimal Shrinkage of Cotton Spandex Woven Fabrics by Apposite Heat Setting Temperature
Total Page:16
File Type:pdf, Size:1020Kb
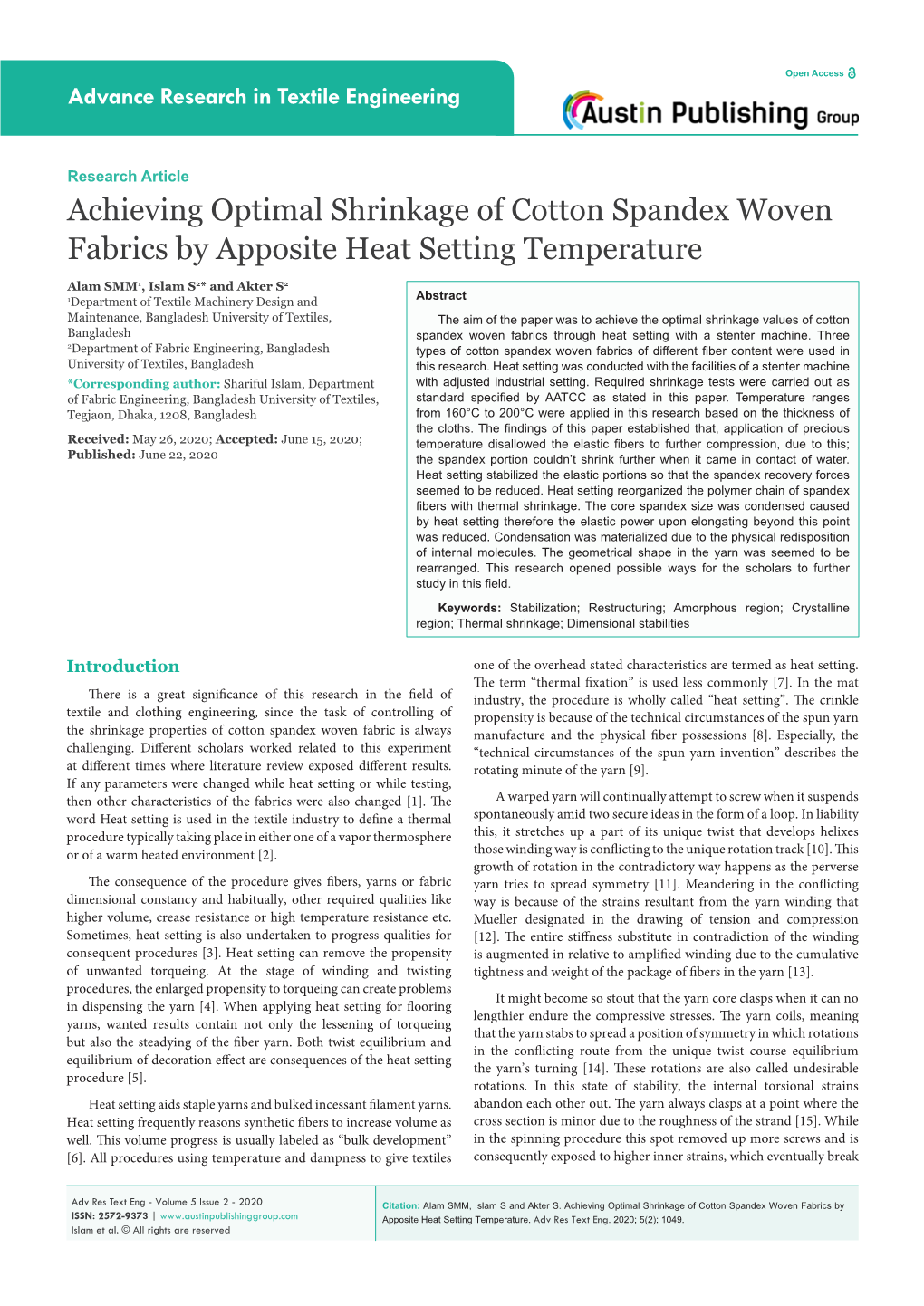
Load more
Recommended publications
-
Processing Problems of Polyester and Its Remedies
International Journal of Engineering Research & Technology (IJERT) ISSN: 2278-0181 Vol. 1 Issue 7, September - 2012 Processing Problems Of Polyester And Its Remedies Dr.Chinta S.K*. and Rajesh Kumar singh D.K.T.E.S Textile and Engineering Institute, Ichalakaranji. ABSTRACT Polyester is predominantly used synthetic fiber in textile fiber industry since 1950. Today there are varieties of commercial forms of polyester available in market viz. Texturized polyester, Bright polyester, Dull polyester, Cationic dyeable polyester, Cot look polyester, Microfiber polyester, Air punched polyester, Staple fiber polyester & its blends. The extensive use of polyester in textile industry & High rate of growth of polyester fibers is due to their outstanding physical properties, resistance to moth, mildew and microorganism, ease of handle, easy to dye & easy to care during use. Also they can be successfully blended with cotton with various proportions either in fiber form or yarn in fabric form. It has high durability compared to other fibers used in apparel industry. In spite of its outstanding performance, there are some shortcomings in polyester fabric & its blends for example: Hydrophobic nature, ease of soiling, static charge builds up, Tendency to pill, some problems may occur due to improper processing sequence such as Shrinkage, due to improper heat setting dyeability varies, colour fading in checks & strip fabrics. Therefore it is necessary to analyze different physical & chemical properties of polyester available in varies commercial forms, so we can understand reasons for problems occurring in its wet processing & to eliminate this problems. INTRODUCTION Polyester is a synthetic fiber derived from coal, air, water, and petroleum. -
Fibre Blends with Elastane
FibreFibre blendsblends withwith elastaneelastane Recommendations for pretreatment and dyeing PrecautionsPrecautions ! Long term storage of fabrics should be avoided - if unavoidable seal in airtight, opaque plastic foil ( to protect from degrading oxides of nitrogen, and sunlight) ! High amounts of silicone oils and other lubricants are used in spinning and winding ! During weaving and knitting further oils and auxiliaries are applied to ensure good running properties. ! Degradation of these products can lead to yellowing or loss of elasticity. ! ‘Cold setting’ can cause permanent crease marks. Circular knits are best slit on knitting machine and rolled open width. ProcessingProcessing Elastanes are knitted/woven under tension which : ! allows “jamming” or compaction of the fabric. ! “buckles” the hard fibre in “jammed” fabric. The fabric should be relaxed prior to heat-setting to avoid rope marks and puckering during dyeing, and ensure good dimensional stability in the final garment. RELAXATIONRELAXATION 11 The process of “settling” the tension in the fabric, to allow full development of the elasticity. The fabric will become fully “jammed”. RelaxationRelaxation == HotHot ++ WetWet ! Benefits of Relaxation ! Reduces potential distortion or deformation of the fabric from residual uneven tension. (e.g. : slits, islands, uneven puckering ) ! Pre-shrinks the goods ready for correct setting. ! Develops full “power” and recovery. ! Required for Desizing woven goods before Heat Set. Relaxation before long storage is preferred. RELAXATIONRELAXATION 22 Relaxation Methods for Elastanes ! Steaming ! Steam Table or Steam Frame in front of Stenter ( Steaming and drying in a stenter should be a separate step before Heat Setting. ) ! Hot wash or scour e.g on a Softflow machine This can be coupled with a scouring step. -
World of Textiles Euorpe
world of textiles Europe References Special Issue www.monforts.com T Competence in Technical Textiles AHEAD OF PROGRESS Our Product Range Suitable for Stretching Ranges Ⅲ Ⅲ Glas Fibre Fabrics Flow Through Dryers Ⅲ Ⅲ Light Protection Belt Dryers Ⅲ Ⅲ Tarpaulins High Temperature Stenters Ⅲ Ⅲ Billboards Vertical Dryers Ⅲ Ⅲ Artificial Leather Finishing Ranges Ⅲ Ⅲ Floor Coverings Universal Dryers Ⅲ Ⅲ Artificial Grass TwinTherm Dryers Ⅲ Ⅲ Nonwovens Thermobonding Ranges Ⅲ Ⅲ Spacers Coating Lines Ⅲ Ⅲ Membranes A. Monforts Textilmaschinen GmbH & Co. KG Germany | A member of CHTC Fong’s Group www.monforts.com Retaining a lead in Europe In this special publication for Of this 181 billion value, 33% ITMA 2019 in Barcelona, we are is achieve€d by clothing, 17% by celebrating the achievements of conventional trading in fabrics, Monforts customers here in our 15% by home textiles and 17% European markets. by industrial and technical In attempting to convey the textiles. importance of the European All these market segments are textiles and clothing industry to its served by Monforts products, overall economy, Lutz Walter, and at ITMA 2019 you’ll find director of innovation and skills at innovations built on Industry 4.0 Euratex – the European Textile possibilities and our long history and Apparel Council – notes that of accumulated expertise across the list price of a new Airbus all clusters of the textile chain. A350-900 wide-body jet airliner is Virtual and remote control of around 275 million. our plant technologies, including This m€eans that EU exports of digital twinning and complete textiles and clothing outside the automation, are just a few of the block alone are the annual concepts you can find out about equivalent of purchasing over 350 for our advanced textile finishing of these latest Airbus planes, so and coating systems, by visiting A. -
Finishing, Dyeing, Quality, Textile, Softener
International Journal of Textile Science 2016, 5(5): 110-118 DOI: 10.5923/j.textile.20160505.03 Finishing Effects on Coloured Knit Fabrics through Implementation of Effective Parameters Md. Mostafizur Rahman1,*, Muhammad Abu Taher1, Mst. Zakia Sultana1, Ashaduzzaman1, Md. Shipan Mia1, Mohammad Sohel Rana2,* 1School of Textile Chemistry & Chemical Engineering, Wuhan Textile University, Wuhan, China 2School of Textile Science & Engineering, Southeast University, Dhaka, Bangladesh Abstract Finishing is used to improve the appearance, imparting functionality and enhancing durability as well as process ability of the textile products. Different processes are associated with the complete production of Coloured fabrics to get the finished fabric. Finishing processes are carried out to improve the natural properties or attractiveness of the fabric and to increase its serviceability. Every natural fiber is noted for some properties but it lacks some other properties which are essential during its end-use. The term finishing, in a broad sense, covers all the processes which the fabric undergoes after leaving the loom or the knitting machine to the stage at which it enters the market. Thus the term also includes bleaching, dyeing, mercerizing etc. but normally the term is restricted to the final stage in the sequence of treatment of Knit fabrics after bleaching and dyeing. Major processes control parameters in all machines are discussed briefly to optimizing the faults through this machine control process and some visible hindrance. Based on the overall performance it can be said that this paper gathers all the information’s related to knit-finishing factory and analyze the fault’s, causes and some ideas are suggested which can meet modern textile trends and customer demand. -
OCCASION This Publication Has Been Made Available to the Public on The
OCCASION This publication has been made available to the public on the occasion of the 50th anniversary of the United Nations Industrial Development Organisation. DISCLAIMER This document has been produced without formal United Nations editing. The designations employed and the presentation of the material in this document do not imply the expression of any opinion whatsoever on the part of the Secretariat of the United Nations Industrial Development Organization (UNIDO) concerning the legal status of any country, territory, city or area or of its authorities, or concerning the delimitation of its frontiers or boundaries, or its economic system or degree of development. Designations such as “developed”, “industrialized” and “developing” are intended for statistical convenience and do not necessarily express a judgment about the stage reached by a particular country or area in the development process. Mention of firm names or commercial products does not constitute an endorsement by UNIDO. FAIR USE POLICY Any part of this publication may be quoted and referenced for educational and research purposes without additional permission from UNIDO. However, those who make use of quoting and referencing this publication are requested to follow the Fair Use Policy of giving due credit to UNIDO. CONTACT Please contact [email protected] for further information concerning UNIDO publications. For more information about UNIDO, please visit us at www.unido.org UNITED NATIONS INDUSTRIAL DEVELOPMENT ORGANIZATION Vienna International Centre, P.O. Box 300, 1400 Vienna, Austria Tel: (+43-1) 26026-0 · www.unido.org · [email protected] v. v. t«»l< Jt-caat #•* .M ^OZHOf i>i. .. i r-.r .'••; T ì) /v; ; . -
Ingilizce-T.Türkcesi Sözlüğü 6300.Başlıq
Ingilizce-T.Türkcesi Sözlüğü 6300.Başlıq aba aba abaca fiber manila elyafı abdominal bandage karın kuşağı abegg frame abegg bankosu abietic reçineli ( çam sakızına benzer ). ability vasıf ( özellik ). ablution yıkama. abmixture emici maddeler abnormal anormal ( olağanüstü ) abrade aşındırmak ( kazımak ). perdahlama abrasion aşınma ( aşındırma ). sürtünerek aşınma abrasion proof aşınmaya dayanıklı abrasion resistance aşınma direnci aşındırma dayanıklılığı abrasion resistant aşınmaya dayanıklı abrasion test aşındırma deneyi aşınma deneyi abrasion tester aşınma deneyici abrasion wear test machine aşınmayı deneme makinesi abrasive zımpara abrasive cloth zımpara bezi ( taşlama bezi ) abrasive coated fabrics zımpara bezi dokuma abrasive paper zımpara kağıdı abrasive products taşlama malzemesi mamulü absence of voltage gerilimsiz ( voltajsız ). absolute mutlak, salt absolute dryness of the yarn elyafın mutlak kuru ağırlığı absolute rotary encoder mutlak değerli döner sensör absorb emme ( emilme, masetme ) absorb power enerji emme absorbability emebilme absorbate emici maddeler absorbed substance emici maddeler absorbencey emicilik. soğurganlık absorbent emen ( emici, massedici, emici maddeler absorbent capacity soğurma yeteneği absorbent cotton emici pamuk absorbent gauze emici tül absorbing emici maddeler emme ( emilme, masetme ) absorbing agent emici maddeler absorbing capacity emme kabiliyeti absorbing device emme tertibatı absorbing filter emme filtresi absorbing medium emici maddeler absorbing plant emme tesisatı absorbing power emme kabiliyeti -
Introduction and Theory of Finishing
Introduction and theory of finishing Contemporary wool dyeing and finishing Dr Rex Brady Deakin University Topics 1. Introduction 2. Wet and dry finishing 3. The theory of setting wool 4. Temporary set 5. Permanent set 6. Relaxation shrinkage 7. Hygral expansion 8. Setting in finishing processes 1. Introduction The aims of finishing § Finishing is the use of a series of processes to develop the properties of fabrics to meet customer requirements. The desired fabric properties are only achieved if each of the steps in a sequence of processes is carried out in a precise order and in an appropriate manner. § Unfinished fabrics are referred to as being ‘greige’ (grey) fabrics, or when appropriate, as ‘loomstate’ fabrics. Finishing converts these into ‘finished’ fabrics. Finishing routines In finishing fabric, a sequence of operations needs to be followed: § to remove unwanted contaminants, mainly lubricants and anti-static agents introduced during yarn and fabric production § to prepare fabrics for dyeing, if it is to be carried out in piece or garment form § to add functional finishes as required, to produce the required handle, shrink-resistance, flame-retardancy, water-proofing, smooth drying, anti-microbial and antistatic properties § to modify the dimensional properties of the fabric (relaxation shrinkage and hygral expansion) and bring these within desired limits § to develop the required fabric handle and appearance. Limitations on finishing § The general character of a fabric is determined by the diameter of the fibres, yarn structure, yarn linear density (count), yarn twist, knit or weave structure and cover factor. These variables are not under the direct control of the finisher. -
15. Principles of Wool Fabric Finishing
15. Principles of Wool Fabric Finishing Mike Pailthorpe and Errol Wood Learning objectives On completion of this topic you should be able to: • Explain the various types of dimensions change that can occur in fabrics • Describe the finishing methods used to remove contaminants from greige state wool fabrics • Outline the finishing methods used to stabilise the dimensions of wool fabrics • Describe the methods used for drying wool fabrics • Describe the finishing processes employed to modify the handle and appearance of wool fabrics Key terms and concepts Inspection, burling, mending, scouring, crabbing, carbonizing, milling, shrink proofing, bleaching, hydroextraction, scutching, drying, conditioning, raising, shearing, singeing, pressing, decatizing, perching. Introduction to the topic The objective of wool fabric finishing is to develop the desired properties in woollen and worsted fabrics that meet the specified end use requirements of consumers. Finishing is a sequence of dry and wet processes that is carried out in a logical order. There are four main objectives to be achieved from the finishing of wool fabrics. • The removal, by scouring, of contaminants from the fabric. These contaminants may include lubricants and antistatic agents employed in yarn and fabric production, warp sizes and lubricants, machine oil stains, etc. In some cases the wool fabric may also contain vegetable matter (VM), in which case the process known as carbonising may be used to remove the VM • The development of the required handle, softness, fullness, drape, etc. • The control of the dimensional stability of the fabric, e.g. relaxation shrinkage, felting shrinkage, and hygral expansion • The application of functional finishes, e.g. -
Achieving Optimal Shrinkage of Cotton Spandex Woven Fabrics by Apposite Heat Setting Temperature
Open Access Advance Research in Textile Engineering Research Article Achieving Optimal Shrinkage of Cotton Spandex Woven Fabrics by Apposite Heat Setting Temperature Alam SMM1, Islam S2* and Akter S2 1Department of Textile Machinery Design and Abstract Maintenance, Bangladesh University of Textiles, The aim of the paper was to achieve the optimal shrinkage values of cotton Bangladesh spandex woven fabrics through heat setting with a stenter machine. Three 2Department of Fabric Engineering, Bangladesh types of cotton spandex woven fabrics of different fiber content were used in University of Textiles, Bangladesh this research. Heat setting was conducted with the facilities of a stenter machine *Corresponding author: Shariful Islam, Department with adjusted industrial setting. Required shrinkage tests were carried out as of Fabric Engineering, Bangladesh University of Textiles, standard specified by AATCC as stated in this paper. Temperature ranges Tegjaon, Dhaka, 1208, Bangladesh from 160°C to 200°C were applied in this research based on the thickness of the cloths. The findings of this paper established that, application of precious Received: May 26, 2020; Accepted: June 15, 2020; temperature disallowed the elastic fibers to further compression, due to this; Published: June 22, 2020 the spandex portion couldn’t shrink further when it came in contact of water. Heat setting stabilized the elastic portions so that the spandex recovery forces seemed to be reduced. Heat setting reorganized the polymer chain of spandex fibers with thermal shrinkage. The core spandex size was condensed caused by heat setting therefore the elastic power upon elongating beyond this point was reduced. Condensation was materialized due to the physical redisposition of internal molecules. -
Heat Setting Polyamides with Shape Retention
Technical brief: heat setting Heat setting polyamides with shape retention By Dr Naresh M Saraf and Dr Priti B Tayade, Sarex,India Heat-setting is a heat treatment by which their dimensions during use. This process is for up to the heat setting temperature. shape retention, crease resistance, resilience the stabilisation of synthetic fibres so they do White or light-coloured textiles made and elasticity are imparted to the fibres. It not shrink when subject to heat. from nylon or elastic fibers, as well as related also brings change in strength, stretch ability, Heat setting operation is crucial for fabrics combination fabric, becomes yellow easily. softness, dye-ability and sometimes on the made up of synthetic fibres since it grants Yellowing may happen at every stage, such colour of the material. excellent dimensional stabilisation and as during the dyeing and finishing process, All these changes are connected with the crease-proof properties, maintained till the storing or hanging in the showcase, or even structural and chemical modifications occurring fabric is exposed to temperatures exceeding at home. There are many factors that can in the fibre. Heat setting is the process the heat setting one. The setting temperature cause yellowing - the material itself may be applicable to fabrics made from synthetic fibres used is above Tg. susceptible to yellowing, or the chemicals used like nylon and polyester in which the fabric is In heat setting, inter-chain bonds, such as on the fabric (residual oil or softener) may subjected to the action of high temperature for hydrogen and dipole bonds, break.