Comparisons of the Aerodynamic Performance of Two Silver Arrows from the Thirties -An Analysis with Computational Fluid Dynamics
Total Page:16
File Type:pdf, Size:1020Kb
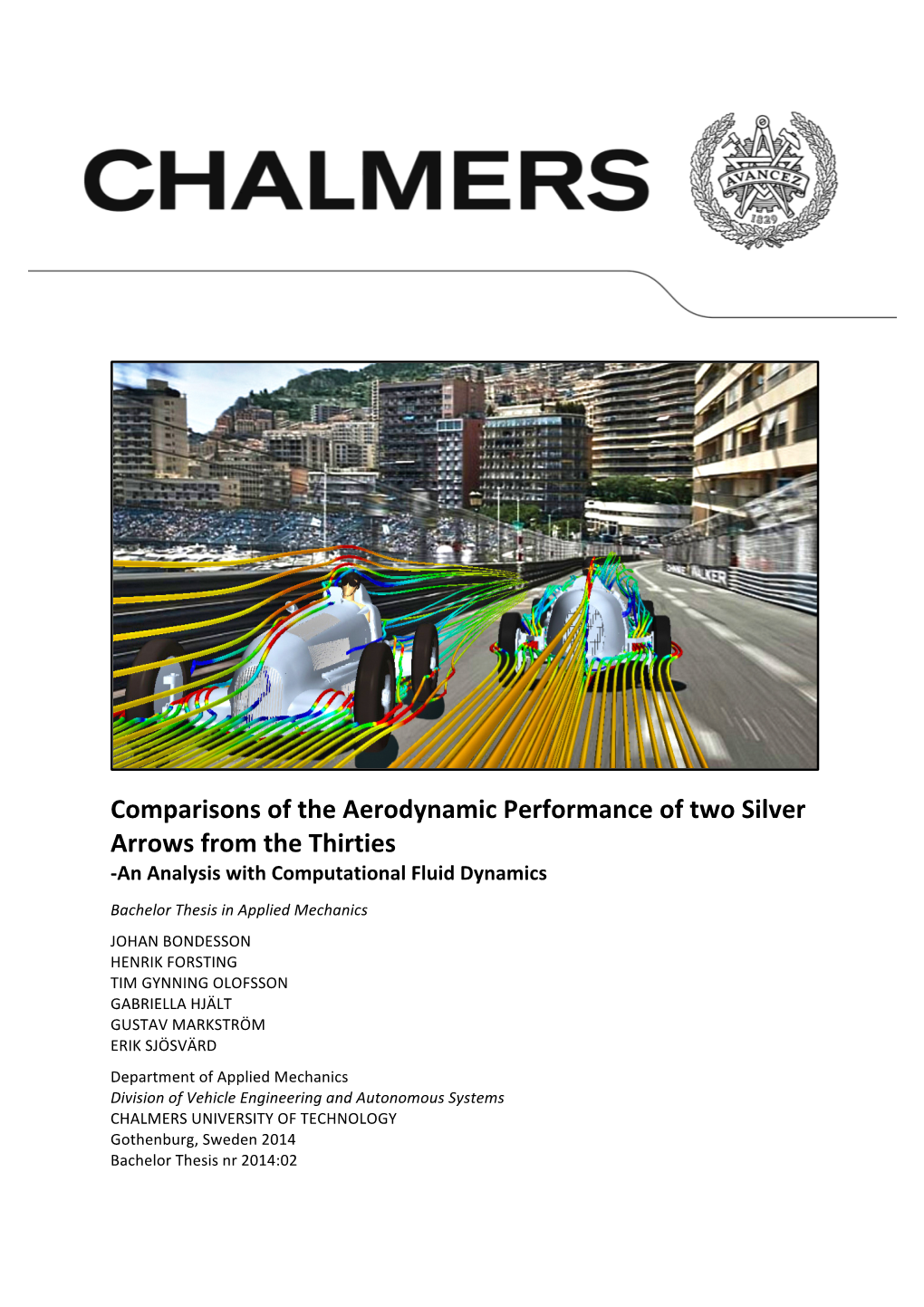
Load more
Recommended publications
-
The Engine Wizard Behind 14 Le Mans Wins in the Modern Era Also Tends
24 ENGINE TECHNOLOGY Auto Union T’S HARD to imagine what people must have thought when Auto Union racing cars burst Ionto the grand prix scene in 1934. Clad in gleaming silver aluminium, with a shape honed in the wind tunnel, a revolutionary mid-engined The time layout and a powerplant of fearsome power and complexity, they were decades ahead of their time. In an era where horses still outnumbered cars, they might as well have teleported in from traveller another galaxy. Since then, few moments in motor racing have The engine wizard behind 14 Le Mans even come close to the shock generated by the arrival of the Auto Unions. Ironically, Audi – one wins in the modern era also tends of the four companies that grouped together to the ground-breaking Auto Union form Auto Union – perhaps came closest, when it brought diesel technology to sports car racing powerplants in Audi’s heritage division. in 2006. Since then, every single Le Mans 24 And he can’t hide his admiration for what Hours winner has been powered by a diesel he has found. Chris Pickering reports engine and all bar one of them has come from Photos: Stefan Warter the German manufacturer. 24 Issue 2 ENGINE TECHNOLOGY 25 BELOW By 1939, the Type D featured a twin- stage supercharger and four carburettors Fittingly, the man behind these incredible engines (not to mention those used in the petrol-powered Audi R8 and the Bentley Speed 8 which won previously) is also charged with looking after the Auto Unions on Audi’s heritage fleet. -
The C-Class Coupé the C-Class Coupé Instantly Seductive
The C-Class Coupé The C-Class Coupé Instantly seductive. 100 milliseconds– that’s how fast we form our first impression. When glimpsing a coupé from Mercedes-Benz it happens even faster. And gets even deeper under the skin. The most emotive way of transforming attraction into fascination. The most intelligent way of transforming desire into power. The new C-Class Coupé. InstANT INFORMATION. Discover the new C-Class Coupé on your iPad®. The Mercedes-Benz brochure app with lots of additional content is available free of charge in the iTunes Store®. The seducers. The arts of seduction. 2 | Mercedes-Benz C-Class Coupé C 300 22 | Mercedes me selenite grey metallic 26 | Services AMG Line, AMG multi-spoke light-alloy wheels, panoramic 30 | Engines and 9G-TRONIC sliding roof, saddle brown leather upholstery, black 32 | AIRMATIC Agility package open-pore ash/light longitudinal-grain aluminium trim 34 | COMAND Online 36 | Burmester® surround sound system 12 | Mercedes-Benz C-Class Coupé C 250 d 38 | Mercedes-Benz Intelligent Drive designo hyacinth red metallic 40 | Equipment and packages 5-twin-spoke light-alloy wheels, panoramic sliding sunroof, 46 | Wheels porcelain leather upholstery, trim in black piano-lacquer 48 | Mercedes-AMG look/light longitudinal-grain aluminium 62 | Technical data 65 | Upholstery and paintwork 48 | Mercedes-AMG C 63 S Coupé designo diamond white bright AMG performance 5-twin-spoke forged wheels, painted matt black and high-sheen rim flange, AMG Night package, AMG Exterior Carbon-Fibre package I + II, AMG red pepper/black nappa leather upholstery, AMG carbon-fibre/ light longitudinal-grain aluminium trim The illustrations may show accessories and optional extras which are not part of the standard specification. -
Press Information
Brackley Press Information 2015 Italian Grand Prix – Preview 01 September 2015 The 2015 Formula One World Championship season continues with Round Twelve, the Italian Grand Prix, from Monza Contents • Driver / Senior Management Quotes o Lewis Hamilton o Nico Rosberg o Toto Wolff o Paddy Lowe • Silver Arrows Statistics • Italian Grand Prix Week: Calendar • #GlobalGrandstand • Contacts Driver / Senior Management Quotes Lewis Hamilton Spa was a really positive weekend for me. I felt comfortable right the way through and it was great to finally get another win at one of the real classic F1 circuits. Now, we head to another of those in Monza. It’s an awesome track – so fast and with some of the most passionate fans you’ll see anywhere in the world. I was actually at this circuit with Sir Stirling Moss earlier this year, driving the banking in his old Mercedes W 196, which was just awesome. Having that taste of what it was like for those guys back in the day really gives you a feel for the history of this place and why it became so legendary. It’s still a big challenge today, too. Fast, but really technical at the same time with some heavy braking and big kerbs to ride for the best line. Racing in Italy brings back a lot of good memories for me and I’d love to add to those this weekend, so that’s the aim. Nico Rosberg Page 2 The race in Spa was definitely disappointing. My start was not good so I need to work on that and also on finding those extra tenths in qualifying to get back on top there. -
Formula E Finale Buemi Survives Clash to Take the Crown #%%'.'4#6' +0018#6+10
AUSTRIAN GP WHAT MERC CRASH TANAK DENIED SURPRISE 16-PAGE REPORT MEANS FOR FORMULA 1 WORLD RALLY VICTORY HAMILTON WINS… ROSBERG FUMES As Wolff threatens team orders “I don’t want contact anymore” FORMULA E FINALE BUEMI SURVIVES CLASH TO TAKE THE CROWN #%%'.'4#6' +0018#6+10 ÜÜܰ>Û°VÉÀ>V} 5+/7.#6' '0)+0''4 /#-' 6'56 4#%' AUSTRIAN GP WHAT MERC CRASH TANAK DENIED SURPRISE 16-PAGE REPORT MEANS FOR FORMULA 1 WORLD RALLY VICTORY HAMILTON WINS… ROSBERG FUMES COVER IMAGES As Wolff threatens team orders “I don’t want contact anymore” Etherington/LAT; FORMULA E FINALE Charniaux/XPB; BUEMI SURVIVES CLASH TO TAKE THE CROWN Rajan Jangda/e-racing.net COVER STORY 4 Austrian Grand Prix report and analysis PIT+PADDOCK 20 FIA aims to boost motorsport worldwide 22 New manufacturers for Formula E 25 Feedback: your letters 27 Ian Parkes: in the paddock REPORTS AND FEATURES XPB IMAGES 28 Buemi takes Formula E title as Prost wins 34 Heartache for Tanak in Rally Poland 40 Suzuki: the sleeping giant of MotoGP Nico still struggling to RACE CENTRE 46 GP2; GP3; Blancpain Sprint Cup; NASCAR Sprint Cup; Formula get the balance right Renault Eurocup; IMSA SportsCar NICO ROSBERG JUST CAN’T QUITE GET IT RIGHT. WHEN CLUB AUTOSPORT it comes to wheel-to-wheel battles, he is either too soft or overly 65 Will Palmer to race in BRDC F3 at Spa robust. He usually comes off worst too, particularly when fi ghting 66 Crack Mercedes squad for British GT Mercedes ‘team-mate’ and title rival Lewis Hamilton. -
Holy Halls”: This Is the Home of the Spectacular Mercedes-Benz Vehicle Collection
Mercedes-Benz Classic Press Information 22 October 2019 Presented for the first time in book format: The Mercedes-Benz treasure chambers The “Holy Halls”: This is the home of the spectacular Mercedes-Benz vehicle collection. The book entitled “Holy Halls. The Secret Car Collection of Mercedes-Benz” offers breathtaking views and insights: with well-researched texts and brilliant photos, it is not only an exciting ramble through the brand’s treasure troves, in addition, 50 selected vehicles tell their own very special stories. Stuttgart. The Mercedes-Benz Classic collection comprises more than 1000 vehicles. No less than 160 of them can be admired at the museum in Untertürkheim. Many others are regularly showcased to the public at exhibitions and events around the globe. By far the largest part of the collection, however, is not freely accessible to the public: it is housed carefully in twelve inconspicuous commercial buildings in and around Stuttgart – the “Holy Halls”. However, the company did make an exception for a special occasion: the renowned specialist journalist and author of several books, Christof Vieweg, who also had the original idea to write the first book about Mercedes-Benz’s exclusive vehicle collection, had the opportunity to inspect the cars extensively and captured his impressions in informative texts. The photos in the “Holy Halls” were taken by photographer Igor Panitz, who is known above all for his automotive and architectural photos. The result is this mesmerising stroll through the unique treasure troves of Mercedes-Benz. Additional studio shots of 50 selected vehicles from the collection were taken under the direction of Harry Ruckaberle in the Sindelfingen photo studio that belongs to Akka Concept GmbH. -
90 Years of Nürburgring
STAGES ............................................. 16 MILESTONES ...................................... 18 NEWS IN THE WEST: EARLY HISTORY AND OPENING ................. 24 FROM THE SOUTH SIDE OF THE SLOPE: OPENING OF THE NEW RACETRACK . 34 KEY RACES ........................................ 36 PRAGUE IMPRESSIONS: 1927 GERMAN GRAND PRIX ................ 38 LIKE ARROWS SHOT FROM A BOW: 1934 EIFEL RACE ................ 42 BITTER LAURELS: 1937 GERMAN GRAND PRIX ..................... 50 RETURN OF THE SILVER ARROWS: 1954 GERMAN GRAND PRIX ........ 58 SURVIVAL OF THE FITTEST: 1957 1,000-KILOMETRE RACE ............ 64 HAIL THE KING: 1957 GERMAN GRAND PRIX ...................... 66 STROKE OF GENIUS: 1961 EUROPEAN GRAND PRIX ................. 68 GALA IN THE WETLANDS: 1968 GERMAN GRAND PRIX ............... 70 BITTER ENDING: 1976 GERMAN GRAND PRIX ...................... 74 THE DUEL: 1980 GERMAN MOTORCYCLE GRAND PRIX ................ 78 MICHAEL TURNER POETRY IN MOTION ............................. 80 CHAMPIONS ....................................... 88 A GERMAN ICON: BERND ROSEMEYER ............................ 90 WoUNDED HERO: RUDOLF CARACCIOLA .......................... 94 ALL-TIME GREAT: JUAN MANUEL FANGIO ......................... 98 MONUMENT OF HIMSELF: SIR STIRLING MOSS .................... 102 MAN OF MANY HATS: JOHN SURTEES ........................... 108 THE KILTED EVANGELIST: SIR JACKIE STEWART ................... 114 MASTER IN THE RAIN: JACKY ICKX ............................. 122 ONCE BURNT, TWICE CAUTIOUS. OR NOT? NIKI LAUDA .............. -
Schenker Deutschland AG
CMC GmbH & Co. KG Classic Model Cars Stuttgarter Str. 106 70736 Fellbach Tel.: +49-(0)711-4400799-0 Press Release Fax: +49-(0)711-454378 [email protected] www.cmc-modelcars.de CMC Models 2016 Datum : 22.01.2016 Bearbeiter: Wuerschum E-Mail: [email protected] Tel.: 0711-4400799-0 Ladies and Gentlemen, CMC GmbH & Co. KG Classic Model Cars is pleased to present to you its recent and forthcoming releases at the 2016 Nuremberg Toy Fair. You are looking at a multitude of new, innovative items that cover a wide range. We would like each collector to find his or her “dream model(s)" below. CMC GmbH & Co. KG, Amtsgericht Stuttgart HRA 724294 Volksbank Esslingen Postbank Stuttgart Deutsche Bank AG Esslingen Pers. Haft. Gesellschafter: BLZ 611 901 10 BLZ 600 100 70 BLZ 611 700 76 CMC Verwaltung GmbH, Denkendorf Konto 3 808 009 Konto 275 424 700 Konto 152 882 700 Amtsgericht Stuttgart HRB 729170 IBAN: DE75611901100003808009 IBAN: DE19600100700275424700 IBAN: DE90611700760152882700 Geschäftsführerin: Shuxiao Jia BIC: GENODES1ESS BIC: PBNKDEFF BIC :DEUTDESS611 -2- Mercedes-Benz 300 SL Panamericana, 1952 Scale 1:18 Item No. M-023 The recommended retail price per model is 315.- €. For Alfred Neubauer, the head of the Mercedes-Benz racing department, only one victory was miss- ing – winning the Carrera Panamericana, a long-distance race in Latin America. With four competi- tion cars and a team of 35 service people, the crew flew to Mexico in November 1952. The engine displacement of the 300 SL had been increased to 3.1 liters, producing 177 hp. -
How a Bribe Saved an Auto Union Type C/D from Soviet Destruction the Soviets Were Ready to Destroy This Car
3/28/2020 How This Historic Auto Union Race Car Was Saved SUBSCRIBE SIGN IN How a Bribe Saved an Auto Union Type C/D From Soviet Destruction The Soviets were ready to destroy this car. Now—thanks to Viktors Kulbergs—it sits in the Audi Museum. BY HARRY VEROLME MAR 27, 2020 AUDI The Bikernieki race track lies not far from the center of Riga, Latvia’s capital. Tucked between a swarm of Soviet buildings and an idyllic forest, the one-mile loop is the crown jewel of the race complex. The Riga Motor Museum, which overlooks the course, is less well-known. Home to many wonderful machines, its centerpiece is an Auto Union Type C/D. The museum is literally built around the silver bullet. The hill- climber rests on an aluminum platform hanging from the ceiling of the main hall. It is an impressive sight, made more so by the story of how it ended up there. Following the fall of the Nazi regime at the end of World War II, Soviet leaders ordered the KGB on a special mission. The goal: empty Horch’s Zwickau factory of all of its technology, including over a dozen Auto Union race cars. The Soviet Union put https://www.roadandtrack.com/car-culture/classic-cars/a31931698/how-a-bribe-saved-an-auto-union-type-cd-from-soviet-destruction/?source=nl&utm… 1/10 3/28/2020 How This Historic Auto Union Race Car Was Saved the cars on a train, squishing them together like sardines to make room for other equipment. -
Mercedes 2019
2019 Perfection of ursuit MERCEDES P No. 7 2019 Pursuit of Perfection: Roger Federer DUBAI, 28 MARCH 2018 Roger Federer headed to Dubai just weeks after clinching his 20th Grand Slam title. Why? For a film shoot with Mercedes-Benz and an exclusive interview with CIRCLE magazine. There he also drew his perfectly imperfect circle for the cover of this issue and wrote a personal comment for each of his Grand Slam wins – with the same hand that made him a tennis legend. MERCEDES CIRCLE No. 7 DEAR READERS, Particularly when it comes to human interaction, it’s the qualities Welcome to the new issue of CIRCLE magazine! that make us unique that enable us to establish connections with friends, family members and partners. We all have our very At Mercedes-Benz, every day is about meeting your high demands. own character. After all, it is often these very aspects of our Exemplary of our efforts is the Mercedes-Maybach S-Class, personalities that endear us to others. which, with its superior technology and sublime fittings, is rightfully considered one of the world’s foremost luxury cars. Character can also be found in abundance in Mercedes-Benz cars. Or the new Mercedes-Benz EQC. The EQC isn’t just the first And developing this character – guided by your needs and fully electric vehicle by Mercedes-Benz, it is also an important our ideas – to make it ever more unique, ever more unmistakable, milestone for our EQ brand, and indeed for mobility of the future. is a mission we dedicate ourselves to each and every day. -
The Joy of Motoring
AHA 2019: The Joy of Motoring Proceedings of Automotive Edited by Historians Australia Inc. Volume 3 Harriet Edquist Volume 3 The papers in this volume were presented at the 4th annual conference of Automotive Historians Australia Inc. held in Proceedings of Automotive August 2019 at RMIT University, Melbourne. It was supported by RMIT Design Archives and RMIT School of Design and Historians Australia Inc. convened by Harriet Edquist and Simon Lockrey. Other than for fair dealing for the purposes of private study, research, criticism or review, as permitted under the Copyright Act 1968 and Copyright Amendment Act 2006, no part of this volume may be reproduced by any process without the prior permission of the editors, publisher and author/s. Edited by Harriet Edquist ↑ Ye Old Hot Rod Shopp. Life Magazine November 5, 1945 ← Street Rod Centre of Australia sign 2015 Copyright of the volume belongs to AHAInc. Copyright of The Proceedings are a record of papers presented at the the content of individual contributions remains the property annual conference of Automotive Historian Australia Inc. of the named author/s. All effots have been made to ensure Publication of the research documented in these Proceedings that authors have secured appropriate permissions to underscores AHA's commitment to academic freedom and ac- ISBN: 978-0-6487100-1-1 reproduce the images illustrating individual contributions. ademic integrity. The conclusions and views expressed in the Published in Melbourne, Australia, by Automotive Historians Australia Inc. 2020 Proceedings do no necessarily reflect the views of the AHA. 2 AHA 2019 The Joy of Motoring 3 AHA 2019 The Joy of Motoring Foreword historical figures or their personal experiences in some aspect of the motor industry. -
Racing Silver Arrows: Mercedes-Benz Versus Auto Union 1934-1939 Racing Silver Arrows: Mercedes-Benz Versus Auto Union 1934-1939
(Free download) Racing Silver Arrows: Mercedes-Benz Versus Auto Union 1934-1939 Racing Silver Arrows: Mercedes-Benz Versus Auto Union 1934-1939 ls3ISJJmy DNQ7R6P0q Ynu3MPmb1 UyCqLRcLr khj8zQ05I FlYmArBc2 IJE5ABbKg pPOqwnZ7E uvvSozBTC Racing Silver Arrows: Mercedes-Benz Versus Auto Union 1934-1939 x6iD5vtXQ WI-19435 Q7z8AFkuZ US/Data/Engineering-Transportation rZcbEYr5K 4/5 From 426 Reviews FZx7MbORV Chris Nixon YJXhP63rK ebooks | Download PDF | *ePub | DOC | audiobook LvZyEmTcn xo5LZECPb I4mpVpOl3 4GE1QAc3p TZzLXgDxC AVyewpVRi 0 of 0 people found the following review helpful. Brilliantly researched, endlessly YkWEg8SOL fascinatingBy Ricardo MioIf there is a single photo that sums up The Age of kfXltcWxo Titans, its the photo Chris Nixon has chosen for the cover of this book. It shows AieZJE4Xk the Mercedes Benz and Auto Union streamliners on the banks of AVUS in Berlin, NCPiV3n6j the capital and showcase city of Hitlers Third Reich and, by extension, the C8145XZpG showcase for the fastest and most technologically advanced racing cars in the pnjYGVSRk world. Hitler was a megalomaniac with dreams of Germany dominating sports, gunDQ3D8r the arts, architecture, engineering, motor racing, and eventually the world. By Vwc0hqqNN 1937, the year this photo was taken, he had partly fulfilled his dream with the all- conquering Silver Arrows. By this time, the German cars had thoroughly steamrolled all foreign competition, and what better place to demonstrate their superiority than in Berlin on the AVUS super speedway? It was, as some have said, a foretaste of things to come, of Germanys mechanized army crushing Europe into submission.Chris Nixon did an incredible job of researching and writing this book. -
Star Bulletin
Mercedes- Benz Club of America More than a Car Club. We're a Community. TM MBCA SAN DIEGO SECTION OFFICERS Victoria Mazelli, President 858-229-3380 [email protected] Star Bulletin Michael Cooper, Vice President 760-599-0629 AUGUST 2019 [email protected] Carol Kruse-Ross, Treasurer 858-245-1991 [email protected] EVENTS SCHEDULE & SPECIAL ANNOUNCEMENTS Diana Kruse, Secretary Director of FirstImpressions [email protected] Joanne Barnard, Director of Spirits MERCEDES-BENZ IN SAN DIEGO [email protected] Bob Gunthorp, Historian & Photographer Fun in the sun continues unabated in San Diego. Inside this issue [email protected] of the STAR BULLETIN read and see what has been going on and Gary Jarvis, Director what is planned for your future Mercedes-Benz world of fun. 619-670-1375 Rudy Hradecky, We just finished racing some of the world famous Mercedes-Benz Director of Procedures [email protected] Silver Arrows, photos inside, and this month we are going to the thoroughbred races in "Old Steve Ross, Membership Chair, Del Mar". Truly sorry if you missed it. Star Bulletin Editor, Website & e-Mail Distribution 619-508-3925 Several have signed up for the Idyllwild trip [email protected] and it is not too late to join us. It is a nice drive up through the mountains and of course the scenery is not bad wither. Anthony Ockuzzi Director of Culinary Arts and Sommelier [email protected] Join us for one of our functions and if you don't have any Bud Cloninger, fun I will personally reimburse you for your cost.