Volume 2 2017
Total Page:16
File Type:pdf, Size:1020Kb
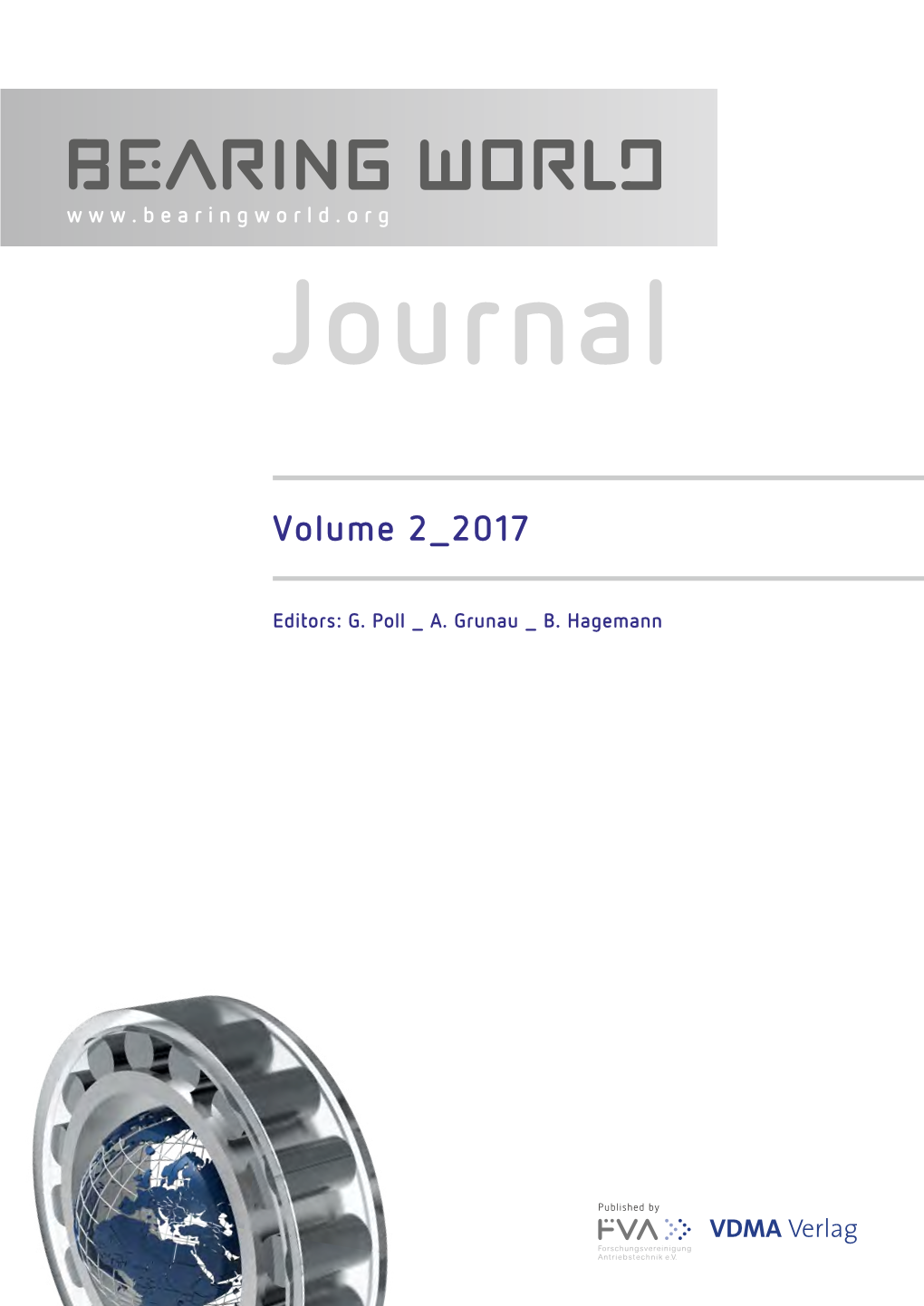
Load more
Recommended publications
-
Wednesday Program Overview
Overview Wednesday, May 19, 2021 8:30 – 10 am 2 – 6 pm Wednesday Keynote Session Wednesday Technical Sessions: Keynote Speaker: • 6A – Biotribology II • Dr. Armit Parikh, Research Manager, Smith & Nephew, Inc. • 6B – 2D Materials/Superlubricity: Material Tribology & Nanotribology Joint Session II 10 – 10:30 am • 6C – Engine & Drivetrain II Networking Break & Special Programming • 6D – Lubrication Fundamentals III: Additives II 10 am – 3:30 pm • 6E – Wear II Virtual Exhibits and Student Posters • 6F – Tribotesting II 10:30 am – 1 pm • 6G – Rolling Element Bearings IV Wednesday Technical Sessions: • 6H – Tribochemistry – Materials Tribology & Nanotribology • 5A – Biotribology I Joint Session I • 5B – 2D Materials/Superlubricity: Material Tribology & • 6I – Grease I Nanotribology Joint Session II • 6J – Commercial Marketing Forum V1 • 5C – Engine & Drivetrain I • 5D – Lubrication Fundamentals II: Additives I 3 – 3:30 pm Networking Break & Special Programming • 5E – Wear I • 5F – Tribotesting I • 5G – Rolling Element Bearings III • 5H – Nonferrous Metals III • 5I – Commercial Marketing Forum V Trade Show Hours: • Monday, May 17: 10 am – 4 pm 1 – 2 pm Plenary Program – Session #1 • Tuesday, May 18: 10 am – 3:30 pm • Wednesday, May 19: 10 am – 3:30 pm Plenary Speaker: • Thursday, May 20: 10 am – 3:30 pm • Dr. Jack Zakarian, Consultant, JAZTech Consulting LLC (All times listed are Eastern Daylight Time) www.stle.org | STLE 2021 Virtual Annual Meeting & Exhibition | 47 Technical Sessions Time Grids – Wednesday, May 19, 2021 TIME SESSION 5A SESSION 5B SESSION 5C Biotribology I 2D Materials/Superlubricity II Engine & Drivetrain I Virtual Meeting Room 1 Virtual Meeting Room 2 Virtual Meeting Room 3 10:30 – 11 am Impact of Metal Release on Chondrocytes Due to The Fascinating Frictional Properties of Layered Component Wear in Diesel Engine High Pressure Fuel Biotribocorrosion in CoCrMo Sliding Against Articular Materials, M. -
2016 STLE Tribology Frontiers Conference
2016 STLE Tribology Frontiers Conference Tribology: The Interface of Physics, Chemistry, Materials and Mechanical Science and Engineering November 13-15, 2016 Historic Drake Hotel on Chicago’s “Magnificent Mile” Chicago, Illinois 2016 Preliminary Technical Program as of 8/2/16 Preliminary TABLE OF CONTENTS Program-at-a-Glance ............................................................................................3 Program with Abstracts Sunday ......................................................................................................4 Monday ......................................................................................................17 Tuesday .....................................................................................................47 Author Index .........................................................................................................64 2016 STLE Tribology Frontiers November 13-15, 2016 Historic Drake Hotel Chicago, Illinois (USA) Preliminary Program-at-a-Glance As of 8/2/16 – Subject to Change Sunday, November 13, 2016 Berkeley – 1:20 pm – 2:00 pm – Grand Ballroom AFM and TEM Studies of Friction and Wear in Pt- Welcome and Introductions – 1:00 pm – 1:20 pm Graphene and Pt-SiO2 Systems Invited Talk – J. Edward Colgate. PhD, Technical Sessions – 2:00 – 6:00 pm Northwestern University – 1:20 pm – 2:00 pm – 3A – Materials Tribology III – Walton North Grand Ballroom 3B – Surfaces & Interfaces III - Walton South Surface Haptics: How Friction Modulation Lets Us 3C – Machine Elements & Systems -
Friction Modifier Additives
FRICTION MODIFIER ADDITIVES Hugh Spikes Tribology Group, Imperial College London, UK ABSTRACT The need for energy efficiency is leading to the growing use of additives that reduce friction in thin film boundary and mixed lubrication conditions. Several classes of such friction modifier additive exist, the main ones being organic friction modifiers, functionalised polymers, soluble organo-molybdenum additives and dispersed nanoparticles. All work in different ways. This paper reviews these four main types of lubricant friction modifier additive and outlines their history, research and the mechanisms by which they are currently believed to function. Aspects of their behaviour that are still not yet fully understood are highlighted. Keywords: Friction; lubricant additives; OFM; molybdenum additives; functionalised polymers; nanoparticles; boundary lubrication 1. INTRODUCTION In order to reduce energy consumption and thus CO2 emissions it is necessary to increase the energy efficiency of mechanical systems and an important way to achieve this is to design lubricants that give low friction in machine components. One design approach is to optimise liquid lubricant rheology so as to minimise hydrodynamic shear, churning and pumping losses. In practice this often means reducing lubricant viscosity to the lowest possible value consonant with maintaining fluid or mixed film lubrication. Another approach is to add small proportions of friction modifier additives to the lubricant in order to reduce friction in the boundary and mixed lubrication regimes. In practice both of these approaches are best applied concurrently since, as lubricant viscosity is progressively reduced, contacts are separated by thinner and thinner hydrodynamic films and so operate increasingly the regimes where friction modifier additives are effective. -
Materials Scie Materials
Imperial College Inaugur <\\ liHt'JJAVHvin s^ 1111n Materials Scie IlVb iilll Materials Eng IJIfifi»JIJILT Editor: Don W. P SJA&/ mperiaJ College Pre^a Imperial College Inaugural Lectures in Materials Science and Materials Engineering Imperial College Inaugural Lectures in Materials Science and Materials Engineering Editor Don W. Pashley Imperial College, UK Imperial College Press Published by Imperial College Press 57 Shelton Street Covent Garden London WC2H 9HE Distributed by World Scientific Publishing Co. Pte. Ltd. P O Box 128, Farrer Road, Singapore 912805 USA office: Suite IB, 1060 Main Street, River Edge, NJ 07661 UK office: 57 Shelton Street, Covent Garden, London WC2H 9HE British Library Cataloguing-in-Publication Data A catalogue record for this book is available from the British Library. IMPERIAL COLLEGE INAUGURAL LECTURES IN MATERIALS SCIENCE AND MATERIALS ENGINEERING Copyright © 2001 by Imperial College Press All rights reserved. This book, or parts thereof, may not be reproduced in any form or by any means, electronic or mechanical, including photocopying, recording or any information storage and retrieval system now known or to be invented, without written permission from the Publisher. For photocopying of material in this volume, please pay a copying fee through the Copyright Clearance Center, Inc., 222 Rosewood Drive, Danvers, MA 01923, USA. In this case permission to photocopy is not required from the publisher. ISBN 1-86094-106-0 Printed in Singapore. PREFACE Newly appointed or newly promoted professors at Imperial College are required to give an inaugural lecture on a subject of their choosing. The professors inevitably talk about areas of their subject on which they are expert, but the lectures are presented in such a way that they appeal to a wide ranging audience, from those who have little knowledge of the subject to those who are comparatively expert in the field. -
Investigation of Industrial Gear Oils: Insights from Complementary Surface and Subsurface Characterisation
Investigation of industrial gear oils: insights from complementary surface and subsurface characterisation A thesis submitted to the University of Manchester for the degree of Doctor of Philosophy in the Faculty of Science and Engineering 2018 Aduragbemi J. Adebogun School of Materials Contents List of Tables ................................................................................................................. 7 List of Figures ............................................................................................................... 8 Abstract ...................................................................................................................... 13 Declaration ................................................................................................................. 14 Copyright Statement .................................................................................................. 14 Acknowledgments ...................................................................................................... 15 1 Introduction ....................................................................................................... 16 1.1 Research motivation and objectives ........................................................... 16 1.2 Structure of the thesis ................................................................................. 18 2 Literature review ................................................................................................ 20 2.1 Tribology as a scientific field ...................................................................... -
Karya Ilmiah : Jurnal Ilmiaii
LEMBAR I{ASIL PENILAIAN SAJAWAT SEBIDANG ATAU PEER REYIEW KARYA ILMIAH : JURNAL ILMIAII Judul Jumal Ikniah (Artikel) Multiphase computational fluid dynamics analysis of hydrodynamic journal bearing under the combined influence of texture and slip Jumlah Penulis 5 orang (Mohammad Tauviqirrnhman, J. Jamari, Bayu Siswo Wibowo, Hilmy Muhammad Fauzan dan M. Muchammad) Status Pengusul Penulis Pertama sekaligus Penulis Korespondensi Identitas Jumal Ilmiah a. Nama Jurnal Lubricants b. Nomor ISSN ISSN:2075-4442 c. Vol, No., Bln Thn Volume 7, Nomor I l, 2019 d. Penerbit Multidisciplinary Digital Publishing Institute (MDP[) e. DOI artikel (ika ada) 1 0.3390/lubricantsT 1 I 0097 f. Alamat web jurnal https: I lwyw.mdpi.canl71T 5 -444?17 I 1 1 197 Alamat Atikel https : //res. mdni, com/djrttachmenViubricants/lubricants- 0L000g7/articl p deplov/lu,brb g. Terindex Scopus (Q1, SJR 0,71) Kategori Publikasi Jumal Ilmiah Jurnal Ilmiah Intemasional Bereputasi @en lpadakategori yang tepat) Jumal llmiah Intemasional Jurnal Ilmiah Nasional Terakreditasi Jurnal Ilmiatr Nasional Tidak Terakrcditasi Hasil Penilaian Peer Review : Nilai Reviewer Komponen yang dinilai Nilai rntr-rata Reviewer 1 Reviewer2 a. Kelengkapan unsur isi jurnal (10%) 3,50 4,00 3,75 b. Ruang lingkup dan kedalaman pembahasan(30%) 11,00 12,00 11,50 c. Kecukupan dan kemutahiran datalinformasi dan 12,00 12.00 12,00 metodologi (30%) d. Kelengkapan unsur dan kualitas terbitan/jumal (30%) 12,00 12,00 12,00 Total = (100%) 38,50 40,00 39,25 Nilai Pengusul = 607o x 39,25 = 23155 Semarang,2T Maret2020 Reviewer I Reviewer 2 tt.\ \N,\y Ir. Eflita Yoh{na,M.T., Ph.D Ojo Kuidi, S.T. -
Research Collection
Research Collection Doctoral Thesis Surface modifications for improved aqueous lubrication under low-contact-pressure conditions Author(s): Heeb, Raphael Emanuel Publication Date: 2009 Permanent Link: https://doi.org/10.3929/ethz-a-006001889 Rights / License: In Copyright - Non-Commercial Use Permitted This page was generated automatically upon download from the ETH Zurich Research Collection. For more information please consult the Terms of use. ETH Library DISS. ETH No. 18431 Surface Modifications for Improved Aqueous Lubrication under Low-Contact-Pressure Conditions A dissertation submitted to ETH ZURICH for the degree of Doctor of Sciences (Dr. sc. ETH Zurich) presented by RAPHAEL EMANUEL HEEB Dipl. Werkstoff-Ing. ETH born on January 16, 1980 citizen of Altst¨atten(SG) accepted on the recommendation of Prof. Dr. Nicholas D. Spencer, examiner Prof. Dr. Seunghwan Lee, co-examiner Prof. Dr. Hugh Spikes, co-examiner 2009 FOR KATHRIN AND MY FAMILY The scientist is not a person who gives the right answers, he's one who asks the right questions. CLAUDE LEVI-STRAUSS´ Abstract The reduction of the interfacial friction between two surfaces in relative motion is a prerequisite for the proper functioning of many systems, ranging from machine parts to human joints. While the lubrication of two contacting surfaces primarily aims at the reduction of friction and wear, either by a separation of the surfaces by means of a fluid film or by introducing a layer of low shear strength between them, additional requirements such as the environmental compatibility of a lubricant or the energy efficiency of tribological systems have become important during recent years. -
PREDICTION of POWER LOSSES in an AUTOMOTIVE GEARBOX INCORPORATING a THERMALLY COUPLED LUBRICATION MODEL’ and the Work Presented in It Are My Own
PREDICTION OF POWER LOSSES IN AN AUTOMOTIVE GEARBOX INCORPORATING A THERMALLY COUPLED LUBRICATION MODEL by Athanasios Christodoulias This dissertation is submitted in fulfilment of the requirements for the degree of Doctor of Philosophy (PhD) and Diploma of Imperial College (DIC) in the Tribology group Department of Mechanical Engineering Imperial College London June 2017 ABSTRACT The continuous tightening of environmental standards, and in particular the stricter vehicle CO2 emission regulations, have put increased pressure on passenger vehicle manufacturers to develop more efficient components. One way of improving fuel consumption and reducing emissions in a vehicle is by reducing the friction-related power loss in major components such as the engine and the transmission. Between 5% and 6% of the total fuel energy that the car converts is lost through friction in the transmission and ends up as heat being absorbed by the transmission lubricant. The principal aim of this project was developing a method to accurately predict power losses in the gearbox -the main transmission component- while at the same time having the ability to assess the influence of lubricant properties on the gearbox efficiency. For this purpose, a thermally coupled numerical model was developed, incorporating lubricant parameters extracted from rheological tests. The model calculates the friction coefficient in gear elastohydrodynamic (EHL) contacts and then uses it in an iterative scheme to predict in-contact and bulk temperatures as well as power losses. Finally, the model’s predictions for gears are coupled to current experimentally derived models for bearing and churning losses. The method has been applied to a single speed gearbox and a manual six speed automotive gearbox. -
2016 STLE Tribology Frontiers Conference
2016 STLE Tribology Frontiers Conference Nov. 13-15, 2016 Drake Hotel • Chicago PROGRAM GUIDE TFC Meeting App Society of Tribologists and Lubrication Engineers Exclusive Discount for STLE TLT Magazine Subscribers: ISBN:: 978-0-8493-2095-8 ISBN: 978-0-8247-0574-9 ISBN: 978-1-4200-8935-6 Catalog no. 2095 Catalog no. DK1815 Catalog no. 89358 ••••• SAVE 25% when you enter code STL73 at checkout ••••• ISBN: 978-1-4200-6908-2 ISBN: 978-1-4665-8726-7 ISBN: 978-1-4665-6774-0 Catalog no. 6908X Catalog no. K20335 Catalog no. K16355 ••••• Enjoy FREE Shipping when you order online at www.crcpress.com ISBN: 978-0-8493-3903-5 ISBN: 978-1-5744-4689-0 ISBN: 978-1-4398-5537-9 ••••• Catalog no. 3903 Catalog no. DK4179 Catalog no. K12581 www.crcpress.com Table of Contents 2} Message from the Chair – Dr. Ashlie Martini 8} Time Grid: Sunday Technical Sessions 3} General Information and Policies 9} Abstracts: Sunday Technical Sessions • Exhibition Hours 17} Time Grid: Monday Technical Sessions • Registration Information • Badge Policy 20} Abstracts: Monday Technical Sessions • TFC Mobile App 40} Time Grid: Tuesday Technical Sessions • Recording Policy • Cellular Phone Policy 42} Abstracts: Tuesday Technical Sessions • Future Industry Meeting Dates 52 Student Posters • 2016 Conference Planning Committee } • TFC and Social Media 55} TFC General Posters 4 Schedule at a Glance } 59} Participant Index 5 The Drake Hotel Floor Plans } 62} Notes Pages 6} Special Events and Networking • Sunday Speakers Luncheon • Sunday Student Career Mentoring Program • Sunday Student Networking Event • Monday Speakers Breakfast • Monday General Attendee Breakfast • Monday Networking Reception • Tuesday Speakers Breakfast • Tuesday General Attendee Breakfast • Networking Breaks (All Days) • Invited Speakers • Sponsors and Exhibitors 7} ASME Tribology Division Awards STLE is the premier technical society serving the needs of more than 13,000 individuals and 250 organizations that comprise the tribology and lubrication engineering business sector. -
The Mechanisms of Wet Clutch Friction Behaviour
The Mechanisms of Wet Clutch Friction Behaviour by Marc Philip Ingram A thesis submitted to Imperial College London for the degree of Doctor of Philosophy and Diploma of Imperial College (D.I.C.) January 2010 Tribology Section Department of Mechanical Engineering Imperial College London Abstract Wet clutches are used in automatic transmissions to bring about gear changes and also to reduce energy loss in the torque converter. These friction devices are susceptible to stick-slip effects, which result in the vehicle giving an unsteady ride. Stick-slip effects can be avoided by ensuring the wet clutch and lubricant combination produces a friction coefficient that increases with sliding speed. This friction characteristic is achieved by using a specific material on one of the two clutch surfaces and by using certain surface active chemicals, which are added to the lubricant. Although wet clutches have been studied throughout the industry for many decades, the mechanism of the generated friction is still not fully understood. In this thesis the friction mechanisms are clarified by the experimental study of the wet clutch in terms of its real area of contact, its flash temperatures and the friction characteristics, which are measured over a broad range of conditions. These results are used along with theoretical calculations to first clarify the lubrication regime, which is found to be predominantly boundary due to the roughness of the friction material and the small size of the contact units formed. The generated friction is then attributed to surface active additives, which form solid-like films on the clutch surfaces. These friction characteristics can be modified by varying the nature of the solid-like film, and when a close-packed film is formed, this displays the friction increasing with speed characteristic due to an activated shearing mechanism, which is linked to the speed of molecular rearrangement at the surface. -
Friction Modifier Additives
Tribol Lett (2015) 60:5 DOI 10.1007/s11249-015-0589-z ORIGINAL PAPER Friction Modifier Additives Hugh Spikes1 Received: 4 August 2015 / Accepted: 25 August 2015 Ó Springer Science+Business Media New York 2015 Abstract The need for energy efficiency is leading to the modifier additives to the lubricant in order to reduce fric- growing use of additives that reduce friction in thin film tion in the boundary and mixed lubrication regimes. In boundary and mixed lubrication conditions. Several classes practice, both of these approaches are best applied con- of such friction modifier additive exist, the main ones being currently since, as lubricant viscosity is progressively organic friction modifiers, functionalised polymers, soluble reduced, contacts are separated by thinner and thinner organo-molybdenum additives and dispersed nanoparticles. hydrodynamic films and so operate increasingly the All work in different ways. This paper reviews these four regimes where friction modifier additives are effective. main types of lubricant friction modifier additive and out- Although in practice many polar organic species and lines their history, research and the mechanisms by which solid particles dissolved or dispersed in base oils produce they are currently believed to function. Aspects of their measurable reductions in boundary friction, there are four behaviour that are still not yet fully understood are main classes of material that have been deliberately highlighted. developed and applied as additives in liquid lubricants to reduce friction and may thus be formally termed friction Keywords Friction Á Lubricant additives Á OFM Á modifier additives. Molybdenum additives Á Functionalised polymers Á One class is the group of compounds based on amphi- Nanoparticles Á Boundary lubrication philic surfactants now usually called organic friction modifiers (OFMs). -
Issue 20 | Autumn 2016
AUTUMN 2016 ISSUE 20 DEPARTMENT OF ENGINEERING NEWS Science behind remarkable new Wall of Death motorcycle world record Page 3 Could future buildings be made with bone and eggshells? Page 5 Smart glass goes from clear to opaque and back again – 27 million times Page 21 Laser technique promises super-fast and super-secure quantum cryptography Page 24 In this issue Welcome The upcoming book by Haroon Ahmed, Cambridge Science behind remarkable new Wall 3 of Death motorcycle world record Engineering: The First 150 Years, is nearing Sir James Dyson opens invention 4 completion. Spanning the breadth of research powerhouse at the University of Cambridge and the history of the Department and looking Dreaming big with biomimetics 5 toward the future, the book commemorates the Student projects find a home as new 6 achievements of all of the notable figures who have Oatley Garage opens studied, researched and worked in Cambridge to PhD student Sakthy Selvakumaran 7 advance the field of engineering. is on the Forbes 30 under 30 list Venice Architecture Biennale 2016 8 Turning through the pages of the book, I was struck Think small: Diminishing returns 9 by the many contrasts and parallels I find between the in neuroscience current Department and its history. We have always Interview with Dr Jenni Sidey 10 emphasised greatness, of course, but it’s clear that our Women in engineering celebrated 11 focus on excellence won’t slow down any time soon! IfM Design Show 2016 12-13 Cambridge spin-out secures $3m 14 A very striking contrast is seeing the increasing diversity to improve oil recovery efficiency of the students and researchers as we move through Alumna Anya Jones Receives 15 history.