Matrix Conversion of Natural and Associated Petroleum Gases to Syngas – New Developments and Possibilities
Total Page:16
File Type:pdf, Size:1020Kb
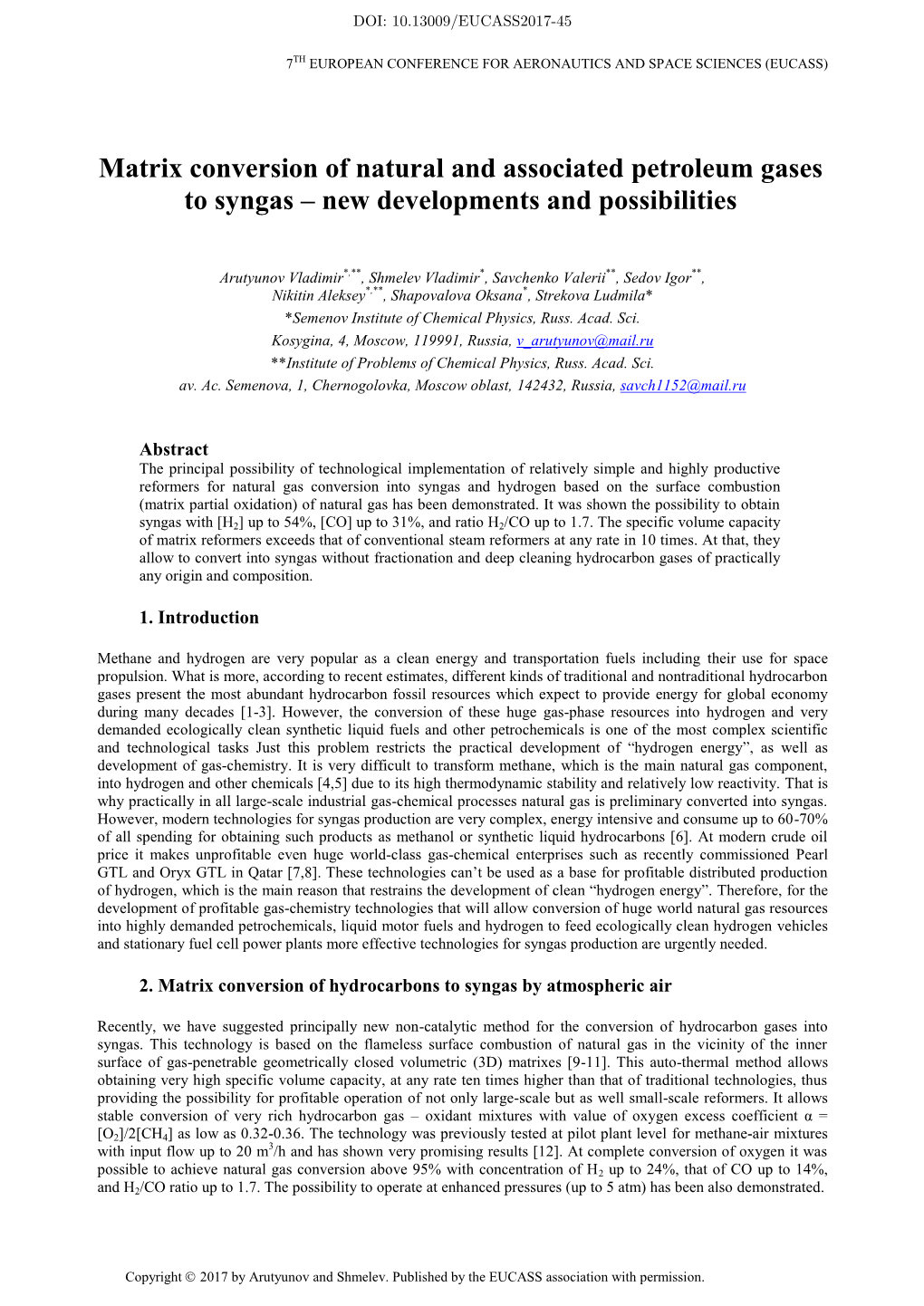
Load more
Recommended publications
-
Storing Syngas Lowers the Carbon Price for Profitable Coal Gasification
Carnegie Mellon Electricity Industry Center Working Paper CEIC-07-10 www.cmu.edu/electricity Storing syngas lowers the carbon price for profitable coal gasification ADAM NEWCOMER AND JAY APT Carnegie Mellon Electricity Industry Center, Tepper School of Business, and Department of Engineering and Public Policy, 254 Posner Hall, Carnegie Mellon University, Pittsburgh, Pennsylvania 15213 Integrated gasification combined cycle (IGCC) electric power generation systems with carbon capture and sequestration have desirable environmental qualities, but are not profitable when the carbon dioxide price is less than approximately $50 per metric ton. We examine whether an IGCC facility that operates its gasifier continuously but stores the syngas and produces electricity only when daily prices are high may be profitable at significantly lower CO2 prices. Using a probabilistic analysis, we have calculated the plant-level return on investment (ROI) and the value of syngas storage for IGCC facilities located in the US Midwest using a range of storage configurations. Adding a second turbine to use the stored syngas to generate electricity at peak hours and implementing 12 hours of above ground high pressure syngas storage significantly increases the ROI and net present value. Storage lowers the carbon price at which IGCC enters the US generation mix by approximately 25%. 1 Carnegie Mellon Electricity Industry Center Working Paper CEIC-07-10 www.cmu.edu/electricity Introduction Producing electricity from coal-derived synthesis gas (syngas) in an integrated gasification combined cycle (IGCC) facility can improve criteria pollutant performance over other coal-fueled technologies such as pulverized coal (PC) facilities [1-5] and can be implemented with carbon capture and sequestration. -
Harmon of Energ THIRD REVIS Onisation of Definitions Rgy
Harmononisation of Definitions of Energrgy Products and Flows THIRD REVISISION OF THE DEFINITIOIONS Part 1: Flows IEA,A, Paris, 21 December 2009 Table of Contents Page Note by Tim Simmons ............................................................................................................................. 5 Flow Structure ......................................................................................................................................... 7 Definition of National Territory (not in flow classification) ................................................................... 9 Supply .................................................................................................................................................... 11 Production .............................................................................................................................................. 13 Receipts from Other Sources ................................................................................................................. 16 Imports and Exports .............................................................................................................................. 18 International Marine Bunkers ................................................................................................................ 21 International Aviation Bunkers ............................................................................................................. 22 Stocks (not in flow classification) ........................................................................................................ -
Comparison Between Hydrogen and Syngas Fuels in an Integrated Micro Gas Turbine/Solar Field with Storage
energies Article Comparison between Hydrogen and Syngas Fuels in an Integrated Micro Gas Turbine/Solar Field with Storage Maria Cristina Cameretti, Alessandro Cappiello, Roberta De Robbio * and Raffaele Tuccillo Department of Industrial Engineering, University of Naples Federico II, 80125 Naples, Italy; [email protected] (M.C.C.); [email protected] (A.C.); raff[email protected] (R.T.) * Correspondence: [email protected] Received: 9 June 2020; Accepted: 3 September 2020; Published: 12 September 2020 Abstract: In recent years, the use of alternative fuels in thermal engine power plants has gained more and more attention, becoming of paramount importance to overcome the use of fuels from fossil sources and to reduce polluting emissions. The present work deals with the analysis of the response to two different gas fuels—i.e., hydrogen and a syngas from agriculture product—of a 30 kW micro gas turbine integrated with a solar field. The solar field included a thermal storage system to partially cover loading requests during night hours, reducing fuel demand. Additionally, a Heat Recovery Unit was included in the plant considered and the whole plant was simulated by Thermoflex® code. Thermodynamics analysis was performed on hour-to-hour basis, for a given day as well as for 12 months; subsequently, an evaluation of cogeneration efficiency as well as energy saving was made. The results are compared against plant performance achieved with conventional natural gas fueling. After analyzing the performance of the plant through a thermodynamic analysis, the study was complemented with CFD simulations of the combustor, to evaluate the combustion development and pollutant emissions formation, particularly of NOx, with the two fuels considered using Ansys-Fluent code, and a comparison was made. -
Russian Associated Gas Utilization: Problems And
Russian Associated Gas Utilization: Problems and Prospects А. Knizhnikov, N. Poussenkova Annual Report within the Framework of the Project Environment and Energy: International Context Issue 1 Moscow • 2009 Russian Associated Gas Utilization: Problems and Prospects A.Yu. Knizhnikov – WWF-Russia N.N. Poussenkova – Institute of World Economy and International Relations of the Russian Academy of Sciences Issue 1 (working materials) for the annual review within the framework of the joint project of the Institute of World Economy and International Relations of the Russian Academy of Sciences and WWF-Russia “Environment and Energy. International Context” Please, send your comments on the Review to WWF-Russia: 19-3 Nikoloyamskaya Street, Moscow, 109240 e-mail: [email protected] Moscow, 2009 TABLE OF CONTENTS Russian Associated Gas Utilization: Problems and Prospects ..................................................................................... 2 1. Russian associated gas flaring volumes ....................................................................................................................... 2 2. Environmental and climatic implications of large-scale associated gas flaring .............................................................. 4 3. Financial implications of large-scale associated gas flaring .......................................................................................... 4 4. Potential ways to utilize associated gas ........................................................................................................................ -
Catalytic Upgrading Nitrogen-Riched Wood Syngas to Liquid Hydrocarbon Mixture Over a Feepd/ZSM-5 Catalyst
biomass and bioenergy 47 (2012) 469e473 Available online at www.sciencedirect.com http://www.elsevier.com/locate/biombioe Catalytic upgrading nitrogen-riched wood syngas to liquid hydrocarbon mixture over a FeePd/ZSM-5 catalyst Qiangu Yan a,*, Fei Yu a,*, Zhiyong Cai b, Jilei Zhang c a Department of Agricultural & Biological Engineering, Box 9632, Mississippi State University, Starkville, MS 39762, USA b USDA Forest Service, Forest Products Laboratory, Madison, WI, USA c Department of Forest Products, Mississippi State University, Mississippi State, MS, USA article info abstract Article history: Biomass like wood chips, switchgrass and other plant residues are first converted to syngas Received 14 October 2011 through gasification process using air, oxygen or steam. A downdraft gasifier is performed Received in revised form for syngas production in Mississippi State. The syngas from the gasifier contains up to 49% 24 May 2012 (vol) N2. High-level nitrogen-containing (nitrogen can be up to 60%) synthesis gas is con- Accepted 1 September 2012 verted to liquid hydrocarbon mixture through a one-stage catalytic process with a FeePd/ Available online 13 October 2012 ZSM-5 catalyst. The FeePd/ZSM-5 catalyst shows relatively high activity and selectivity in producing liquid hydrocarbons when running with nitrogen-rich syngas. The CO conver- Keywords: sion, hydrocarbon selectivity and hydrocarbon distribution as a function of temperature, Biomass to liquid (BTL) fuels pressure, GHSV, composition of the feed, and reaction time are examined. Gasification ª 2012 Elsevier Ltd. All rights reserved. Nitrogen-riched Catalytic upgrading FeePd/ZSM-5 catalyst 1. Introduction stage processes of synthesis gas conversion to gasoline [9,10]. -
A Comparative Exergoeconomic Evaluation of the Synthesis Routes for Methanol Production from Natural Gas
applied sciences Article A Comparative Exergoeconomic Evaluation of the Synthesis Routes for Methanol Production from Natural Gas Timo Blumberg 1,*, Tatiana Morosuk 2 and George Tsatsaronis 2 ID 1 Department of Energy Engineering, Zentralinstitut El Gouna, Technische Universität Berlin, 13355 Berlin, Germany 2 Institute for Energy Engineering, Technische Universität Berlin, 10587 Berlin, Germany; [email protected] (T.M.); [email protected] (G.T.) * Correspondence: [email protected]; Tel.: +49-30-314-23343 Received: 30 October 2017; Accepted: 20 November 2017; Published: 24 November 2017 Abstract: Methanol is one of the most important feedstocks for the chemical, petrochemical, and energy industries. Abundant and widely distributed resources as well as a relative low price level make natural gas the predominant feedstock for methanol production. Indirect synthesis routes via reforming of methane suppress production from bio resources and other renewable alternatives. However, the conventional technology for the conversion of natural gas to methanol is energy intensive and costly in investment and operation. Three design cases with different reforming technologies in conjunction with an isothermal methanol reactor are investigated. Case I is equipped with steam methane reforming for a capacity of 2200 metric tons per day (MTPD). For a higher production capacity, a serial combination of steam reforming and autothermal reforming is used in Case II, while Case III deals with a parallel configuration of CO2 and steam reforming. A sensitivity analysis shows that the syngas composition significantly affects the thermodynamic performance of the plant. The design cases have exergetic efficiencies of 28.2%, 55.6% and 41.0%, respectively. -
The Future of Gas in Europe: Review of Recent Studies on the Future of Gas Mihnea Cătuţi, Christian Egenhofer & Milan Elkerbout
No. 2019/03, August 2019 The future of gas in Europe: Review of recent studies on the future of gas Mihnea Cătuţi, Christian Egenhofer & Milan Elkerbout Abstract In the context of the EU transition to a low-carbon economy, the gas industry will face significant transformations over the next decades up to 2050 and beyond. A substantial number of studies on the future of gas have been published recently, which each come to different outcomes and projections, in some cases even to radically different conclusions. This report reviews the findings of the most recent reports on the evolution of the EU gas market foreseen up to 2030 and 2050 with the aim of identifying the different outcomes and examining the reason for divergent results. Up until 2030, the demand for natural gas is projected to remain stable or to decrease slightly. Switching to natural gas-fired power plants can represent a short and medium-term solution for countries going through a coal phase-out. Gas can also contribute to the flexibility in the power sector necessitated by the increasing share of variable renewables such as wind and solar. The demand projections for 2050 show more significant differences between results. The higher the assumed 2050 GHG emissions reduction target in the scenario, the lower the projected demand for natural gas will be. As the EU moves towards its 2050 targets, a mix of low and zero-carbon gaseous fuels, such as biogas, biomethane, (blue and green) hydrogen, and synthetic methane, are expected to replace natural gas. Biogas and biomethane are currently the most commercially ready alternatives to natural gas and require no major infrastructural upgrades. -
Syngas Obtainment from the Gasification of Asphaltenes of the San Fernando Crude Oil
SYNGAS OBTAINMENT FROM THE GASIFICATION OF ASPHALTENES OF THE SAN FERNANDO CRUDE OIL Ciencia, Tecnología y Futuro SYNGAS OBTAINMENT FROM THE GASIFICATION OF ASPHALTENES OF THE SAN FERNANDO CRUDE OIL Laura-Smith Moreno-Arciniegas2*, Fabio-Ernesto Rodríguez-Corredor2*, Luz-Edelmira Afanador-Rey1* and Jorge-Luis Grosso-Vargas2 ¹ Ecopetrol S.A-Instituto Colombiano del Petróleo, P. O. Box 4185, Bucaramanga, Santander, Colombia ² Universidad Industrial de Santander (UIS), Bucaramanga, Santander, Colombia e-mail: [email protected] e-mail: [email protected] e-mail: [email protected] (Received April 30, 2008; Accepted July 17, 2009) n this work, we developed the first study in Colombia to obtain and evaluate syngas compositions derived from asphaltenes gasification. These asphaltenes came from the implementation of a Deasphalting process to San IFernando crude oil, with the purpose of looking for technological options for their utilization. We performed the design, installation and commissioning of facilities for the gasification of asphaltenes at laboratory scale, it fol- lowing an experimental methodology, performing nine tests and considering temperature and agent gasification quantity (oxygen) as independent variables. The syngas derived from gasification was analyzed by two chromato- graphic techniques, which reported the presence of refinery gases and sulfur. We evidenced a growth tendency of CO, H2 and sulfur composition and a decrease in CH4 and CO2 composition with temperature. The composition of the syngas was evaluated with different quantities of gasification agent (33%, 40% and 47% the amount of oxygen theoretically required for complete combustion) at each temperature levels operated. It was established that when using a 40% of gasification agent, you get greater average content of CO and H2, which are the interest gases in the gasification process. -
The Future of Gasification
STRATEGIC ANALYSIS The Future of Gasification By DeLome Fair coal gasification projects in the U.S. then slowed significantly, President and Chief Executive Officer, with the exception of a few that were far enough along in Synthesis Energy Systems, Inc. development to avoid being cancelled. However, during this time period and on into the early 2010s, China continued to build a large number of coal-to-chemicals projects, beginning first with ammonia, and then moving on to methanol, olefins, asification technology has experienced periods of both and a variety of other products. China’s use of coal gasification high and low growth, driven by energy and chemical technology today is by far the largest of any country. China markets and geopolitical forces, since introduced into G rapidly grew its use of coal gasification technology to feed its commercial-scale operation several decades ago. The first industrialization-driven demand for chemicals. However, as large-scale commercial application of coal gasification was China’s GDP growth has slowed, the world’s largest and most in South Africa in 1955 for the production of coal-to-liquids. consistent market for coal gasification technology has begun During the 1970s development of coal gasification was pro- to slow new builds. pelled in the U.S. by the energy crisis, which created a political climate for the country to be less reliant on foreign oil by converting domestic coal into alternative energy options. Further growth of commercial-scale coal gasification began in “Market forces in high-growth the early 1980s in the U.S., Europe, Japan, and China in the coal-to-chemicals market. -
Technical Report
TECHNICAL REPORT Nov 30, Potential Cost-Effective Flare & Vent Gas Reduction Opportunities 2015 at Selected Production Facilities in Colombia (Operator No. 1) Prepared For: Petroleum Technology Alliance Canada (PTAC) Suite 400, 500-5th Avenue S.W. Calgary, AB, T2P 3L5 Prepared By: Clearstone Engineering Ltd. 700, 900-6th Avenue S.W. Calgary, AB, T2P 3P2 DISCLAIMER While reasonable effort has been made to ensure the accuracy, reliability and completeness of the information presented herein, this report is made available without any representation as to its use in any particular situation and on the strict understanding that each reader accepts full liability for the application of its contents, regardless of any fault or negligence of Clearstone Engineering Ltd. i EXECUTIVE SUMMARY A limited flare and vent gas measurement program was conducted during the period of 14 to 16 August 2015 at the following selected Operator No. 1 facilities in Colombia: • CCAC.3 Oilfield (Conventional Oil Production) • CCAC.1 Oilfield (Thermal Heavy Oil Production) Supplemental information was provided by the operations centre for each oilfield, including activity data, commodity pricing and production decline rates. The overall purpose of this study was, for the surveyed facilities, to identify and conduct a pre-feasibility assessment of practicable flare and vent gas reduction opportunities in terms of their magnitude, most suitable control option, feasibility, greenhouse gas (GHG) emissions reductions, secondary environmental benefits and energy conservation. The surveyed facilities were selected by Operator No. 1 as being representative of sites likely to offer such opportunities. Key Environmental and Economic Analysis Assumptions All technical, environmental and economic analyses were performed using Clearstone’s web- based source-simulation and data-management application, CSimOnline. -
Selected Aspects of Hydrogen Production Via Catalytic Decomposition of Hydrocarbons
Article Selected Aspects of Hydrogen Production via Catalytic Decomposition of Hydrocarbons Aleksey A. Vedyagin 1,2,* , Ilya V. Mishakov 1,2, Denis V. Korneev 3 , Yury I. Bauman 1,2 , Anton Yu. Nalivaiko 2 and Alexander A. Gromov 2 1 Department of Materials Science and Functional Materials, Boreskov Institute of Catalysis SB RAS, Lavrentieva Ave 5, 630090 Novosibirsk, Russia; [email protected] (I.V.M.); [email protected] (Y.I.B.) 2 Catalysis Lab, National University of Science and Technology MISIS, Leninskiy Prospect 4, 119049 Moscow, Russia; [email protected] (A.Y.N.); [email protected] (A.A.G.) 3 School of Biological Sciences, Monash University, 25 Rainforest Walk, Clayton, VIC 3800, Australia; [email protected] * Correspondence: [email protected] Abstract: Owing to the high hydrogen content, hydrocarbons are considered as an alternative source for hydrogen energy purposes. Complete decomposition of hydrocarbons results in the formation of gaseous hydrogen and solid carbonaceous by-product. The process is complicated by the methane formation reaction when the released hydrogen interacts with the formed carbon deposits. The present study is focused on the effects of the reaction mixture composition. Variations in the inlet hydrogen and methane concentrations were found to influence the carbon product’s morphology and the hydrogen production efficiency. The catalyst containing NiO (82 wt%), CuO (13 wt%), and Al2O3 (5 wt%) was prepared via a mechanochemical activating procedure. Kinetics of the catalytic Citation: Vedyagin, A.A.; Mishakov, process of hydrocarbons decomposition was studied using a reactor equipped with McBain balances. I.V.; Korneev, D.V.; Bauman, Y.I.; The effects of the process parameters were explored in a tubular quartz reactor with chromatographic Nalivaiko, A.Y..; Gromov, A.A. -
Natural Gas Annual Questionnaire 2017-2021
NATURAL GAS ANNUAL QUESTIONNAIRE 2017-2021 AND HISTORICAL REVISIONS August 2018 Attached is the annual questionnaire for natural gas which provides for the submission of 2017-2021 data and historical revisions where applicable. Countries reporting to the IEA are requested to complete the questionnaire at the latest by 30 September. Earlier submissions are welcome. Countries reporting to Eurostat are requested to complete the questionnaire by 30 November (Regulation (EC) No 1099/2008 on energy statistics). Earlier submissions are welcome. Please send your questionnaire to: International Energy Agency (IEA/OECD), Energy Data Centre (the IEA will forward the data to the United Nations Economic Commission for Europe in Geneva). European Commission, Eurostat, Energy Statistics (for EU Member States, European Economic Area countries, EU Candidate Countries and Potential Candidates, Energy Community Contracting Parties) United Nations Statistics Division, Energy Statistics Section Transmission details are provided in the “Data communication procedures” section. ANNUAL GAS QUESTIONNAIRE Data communication procedures IEA 31-35, rue de la Fédération, 75739, Paris, Cedex 15, France Please complete data for your country on the Energy Validation Outlet: https://evo.iea.org Alternatively send the completed questionnaire in a CSV or Excel file as an e-mail attachment. to [email protected] For questions regarding the questionnaire, contact [email protected] * * * * * * * * * * * * * * * * * * * * * * * * * * * * * * * * * Eurostat European Commission – Eurostat, Unit E.5: Energy, L-2920 Luxembourg (for EU Member States, European Economic Area countries, EU Candidate Countries and Potential Candidates, Energy Community Contracting Parties) The completed MS Excel questionnaire should be transmitted via the Single Entry Point following the implementing procedures of EDAMIS (Electronic Data Files Administration And Management Information System): https://webgate.ec.europa.eu/edamis/ selecting the electronic data collection ENERGY_NTGAS_A.