Deformation of Hexagonal Boron Nitride
Total Page:16
File Type:pdf, Size:1020Kb
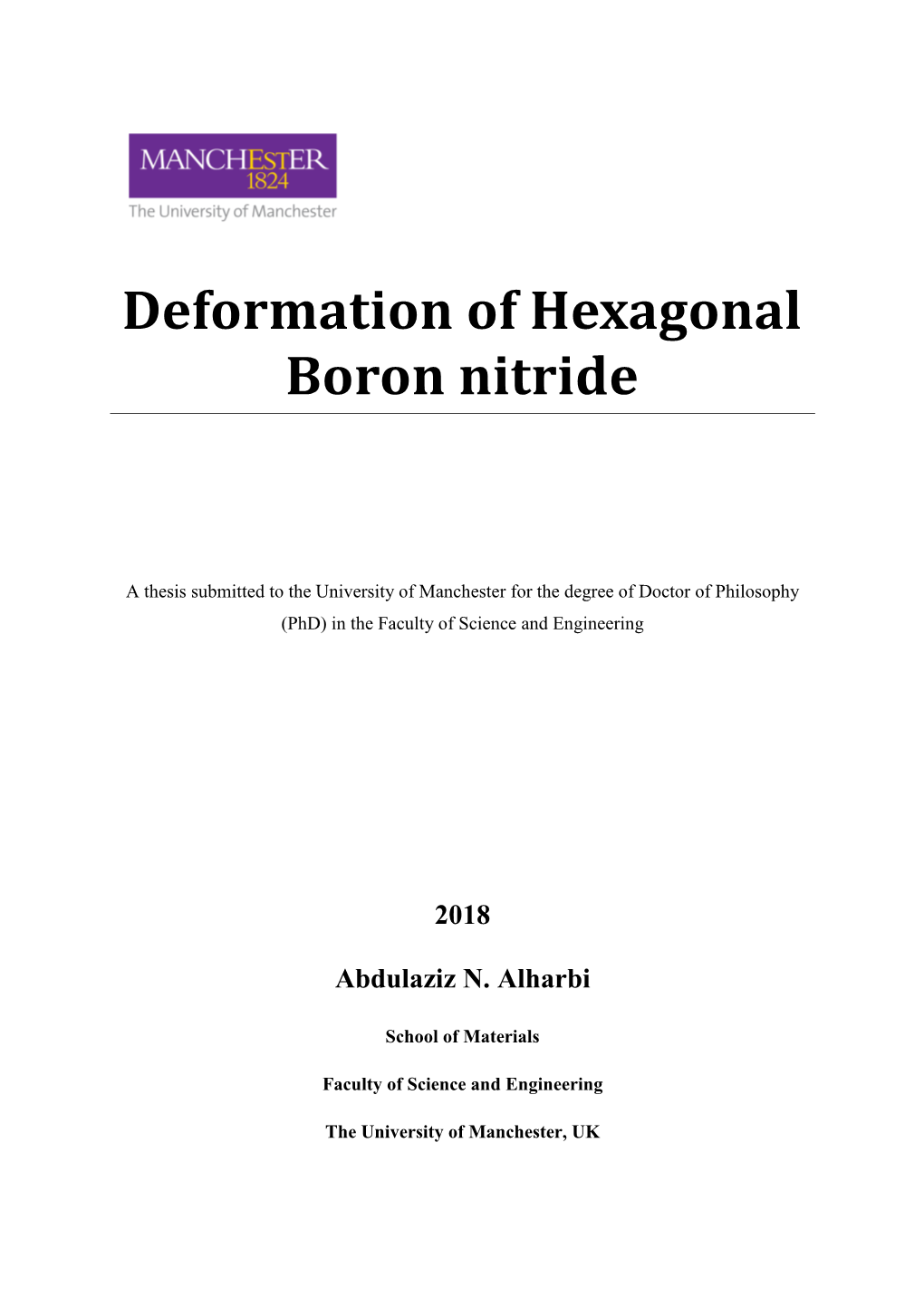
Load more
Recommended publications
-
BN Nanosheet/Polymer Films with Highly Anisotropic Thermal Conductivity for Thermal Management Applications Yuanpeng Wu Deakin University
University of Wollongong Research Online Australian Institute for Innovative Materials - Papers Australian Institute for Innovative Materials 2017 BN Nanosheet/Polymer Films with Highly Anisotropic Thermal Conductivity for Thermal Management Applications Yuanpeng Wu Deakin University Ye Xue Rowan University Si Qin Deakin University Dan Liu Deakin University Xuebin Wang Nanjing University See next page for additional authors Publication Details Wu, Y., Xue, Y., Qin, S., Liu, D., Wang, X., Hu, X., Li, J., Wang, X., Bando, Y., Golberg, D., Chen, Y., Gogotsi, Y. & Lei, W. (2017). BN Nanosheet/Polymer Films with Highly Anisotropic Thermal Conductivity for Thermal Management Applications. ACS Applied Materials and Interfaces, 9 (49), 43163-43170. Research Online is the open access institutional repository for the University of Wollongong. For further information contact the UOW Library: [email protected] BN Nanosheet/Polymer Films with Highly Anisotropic Thermal Conductivity for Thermal Management Applications Abstract The development of advanced thermal transport materials is a global challenge. Two-dimensional nanomaterials have been demonstrated as promising candidates for thermal management applications. Here, we report a boron nitride (BN) nanosheet/polymer composite film with excellent flexibility and toughness prepared by vacuum-assisted filtration. The mechanical performance of the composite film is highly flexible and robust. It is noteworthy that the film exhibits highly anisotropic properties, with superior in-plane thermal conductivity of around 200 W m -1 K -1 and extremely low through-plane thermal conductivity of 1.0 W m -1 K -1 , making this material an excellent candidate for thermal management in electronics. Importantly, the composite film shows fire-resistant properties. -
Carbon and Boron Nitride Nanostructures for Hydrogen Storage Applications Through a Theoretical Perspective
CARBON AND BORON NITRIDE NANOSTRUCTURES FOR HYDROGEN STORAGE APPLICATIONS THROUGH A THEORETICAL PERSPECTIVE Y. T. Singha,b, B. Chettria,b, A. Banikc , K. O. Obodod and D. P. Raia,* aPhysical Science Research Center (PSRC), Department of Physics, Pachhunga University College, Mizoram University, Aizawl 796001, India bDepartment of Physics, North-Eastern Hill University, Shillong 793022, India cDepartment of Electrical Engineering, National Institute of Technical Teachers' Training & Research (NITTTR), Kolkata, India dHySA Infrastructure Centre of Competence, Faculty of Engineering, North-WestUniversity (NWU), P. Bag X6001, Potchefstroom, 2520, South Africa Abstract: The recent progress in the field of hydrogen storage in carbon and boron nitride nanostructures has been summarized. Carbon and boron nitride nanostructures are considered advantageous in this prospect due to their lightweight and high surface area. Demerits of pristine structures to hold hydrogen molecules for mobile applications have been highlighted by many researchers. In such cases, weak van der Waals interaction comes into account, hence, the hydrogen molecules are weakly bonded with the host materials and hence weak adsorption energy and low hydrogen molecules uptake. So, to tune the adsorption energy as well as overall kinetics, methods such as doping, light alkali-alkaline earth metals decoration, vacancy, functionalization, pressure variation, application of external electric field, and biaxial strain has been adopted by many researchers. Physisorption with atoms decoration is promising for hydrogen storage application. Under this condition, the host materials have high storage capacity with considerable average adsorption energy, feasible adsorption/desorption kinetics. Keywords: Density Functional Theory; hydrogen storage; boron nitride; graphene; carbon nanotube; adsorption energy; desorption temperature; physisorption; chemisorption; temperature; pressure. -
Effective Mechanical Properties and Thickness Determination of Boron Nitride Nanosheets Using Molecular Dynamics Simulation
nanomaterials Article Effective Mechanical Properties and Thickness Determination of Boron Nitride Nanosheets Using Molecular Dynamics Simulation Venkatesh Vijayaraghavan and Liangchi Zhang * Laboratory for Precision and Nano Processing Technologies, School of Mechanical and Manufacturing Engineering, The University of New South Wales, Sydney, NSW 2052, Australia; [email protected] * Correspondence: [email protected]; Tel.: +61-2-9385-6078 Received: 3 July 2018; Accepted: 17 July 2018; Published: 19 July 2018 Abstract: Research in boron nitride nanosheets (BNNS) has evoked significant interest in the field of nano-electronics, nanoelectromechanical (NEMS) devices, and nanocomposites due to its excellent physical and chemical properties. Despite this, there has been no reliable data on the effective mechanical properties of BNNS, with the literature reporting a wide scatter of strength data for the same material. To address this challenge, this article presents a comprehensive analysis on the effect of vital factors which can result in variations of the effective mechanical properties of BNNS. Additionally, the article also presents the computation of the correct wall thickness of BNNS from elastic theory equations, which is an important descriptor for any research to determine the mechanical properties of BNNS. It was predicted that the correct thickness of BNNS should be 0.106 nm and the effective Young’s modulus to be 2.75 TPa. It is anticipated that the findings from this study could provide valuable insights on the true mechanical properties of BNNS that could assist in the design and development of efficient BN-based NEMS devices, nanosensors, and nanocomposites. Keywords: boron nitride nanosheet; molecular dynamics; thickness; mechanical strength; vacancy defects 1. -
Enhanced Thermal Conductivity of Polyimide Composites with Boron
www.nature.com/scientificreports OPEN Enhanced Thermal Conductivity of Polyimide Composites with Boron Nitride Nanosheets Received: 2 November 2017 Ting Wang1, Mengjie Wang1, Li Fu2, Zehui Duan3, Yapeng Chen1, Xiao Hou1, Yuming Wu1, Accepted: 10 January 2018 Shuangyi Li1, Liangchao Guo1, Ruiyang Kang1, Nan Jiang1 & Jinhong Yu1 Published: xx xx xxxx A strategy was reported to prepare boron nitride nanosheets (BNNSs) by a molten hydroxide assisted liquid exfoliation from hexagonal boron nitride (h-BN) powder. BNNSs with an average thickness of 3 nm were obtained by a facile, low-cost, and scalable exfoliation method. Highly thermally conductive polyimide (PI) composite flms with BNNSs fller were prepared by solution-casting process. The in-plane thermal conductivity of PI composite flms with 7 wt% BNNSs is up to 2.95 W/mK, which increased by 1,080% compared to the neat PI. In contrast, the out-of plane thermal conductivity of the composites is 0.44 W/mK, with an increase by only 76%. The high anisotropy of thermal conductivity was verifed to be due to the high alignment of the BNNSs. The PI/BNNSs composite flms are attractive for the thermal management applications in the feld of next-generation electronic devices. With the rapid development of electronics industry, there is an increasing demand for electrically insulating polymer-based materials with enhanced capability of heat dissipation1–5. Furthermore, low cost and light weight polymer-based materials for next-generation electronic device, power systems, and communication equipment are needed. Polymers such as polyimide (PI) has been widely used as an electronic packaging material due to good thermal and mechanical properties6,7. -
Novel Porous Boron Nitride Nanosheet with Carbon Doping: Potential Metal-Free Photocatalyst for Visible-Light-Driven Overall Water Splitting
FULL PAPER Photocatalysis www.advtheorysimul.com Novel Porous Boron Nitride Nanosheet with Carbon Doping: Potential Metal-Free Photocatalyst for Visible-Light-Driven Overall Water Splitting Qiang Wan, Fenfei Wei, Zuju Ma,* Masakazu Anpo, and Sen Lin* materials are suitable as photocatalysts ow- The band gap of hexagonal boron nitride (h-BN) is far too wide for efficiently ing to their appropriate band structures.[6] utilizing visible light, limiting its application in photocatalysis. The present For example, Wang et al.[4a] had reported study employs first principles calculations to demonstrate that the band gap that g-C3N4, with a band gap of 2.70 eV, energies of porous h-BN (p-BN) can be tuned by carbon doping to levels could be used to photocatalyze hydrogen and oxygen from water under visible light appropriate for the absorption of visible-light, and that the conduction band irradiation. This opens an entirely new di- and valence band match well with the potentials of both hydrogen and oxygen rection for developing metal-free photocat- evolution reactions. Importantly, a strategy of carbon doping to improve the alysts for overall water splitting. energy level of valence band maximum is also proposed. Moreover, the Among the several 2D materials avail- carbon-doped p-BN exhibits good separation between photogenerated able, h-BN, an analogue of graphene, has electrons/holes and structural stability at high temperatures. The DFT results attracted tremendous interest recently due to its electronic properties that are distinct help the design of high-performance two-dimensional photocatalysts that from those of graphene and its superior avoid the use of metals. -
Highly Efficient Electrochemical Hydrogen Evolution Reaction At
www.nature.com/scientificreports OPEN Highly Efficient Electrochemical Hydrogen Evolution Reaction at Insulating Boron Nitride Nanosheet Received: 19 May 2016 Accepted: 03 August 2016 on Inert Gold Substrate Published: 25 August 2016 Kohei Uosaki1,2,3, Ganesan Elumalai1,3, Hung Cuong Dinh2, Andrey Lyalin1, Tetsuya Taketsugu1,3,4 & Hidenori Noguchi1,2,3 It is demonstrated that electrochemical hydrogen evolution reaction (HER) proceeds very efficiently at Au electrode, an inert substrate for HER, modified with BNNS, an insulator. This combination has been reported to be an efficient electrocatalyst for oxygen reduction reaction. Higher efficiency is achieved by using the size controlled BNNS (<1 μm) for the modification and the highest efficiency is achieved at Au electrode modified with the smallest BNNS (0.1–0.22 μm) used in this study where overpotentials are only 30 mV and 40 mV larger than those at Pt electrode, which is known to be the best electrode for HER, at 5 mAcm−2 and at 15 mAcm−2, respectively. Theoretical evaluation suggests that some of edge atoms provide energetically favored sites for adsorbed hydrogen, i.e., the intermediate state of HER. This study opens a new route to develop HER electrocatalysts. Hydrogen is considered to be the cleanest fuel and a recent announcement of a commercial fuel cell car opened a new era of hydrogen-based economy. One must, however, realize that although CO2 is not emitted when hydro- gen is used as a fuel, it is emitted during the hydrogen production since current hydrogen source is fossil fuels such as natural gas. Therefore, for hydrogen to be truly a clean fuel, it must be generated from water using renew- able energy. -
Few-Atomic-Layered Hexagonal Boron Nitride: CVD Growth, Characterization, and Applications Majharu Haque Khan University of Wollongong, [email protected]
University of Wollongong Research Online Australian Institute for Innovative Materials - Papers Australian Institute for Innovative Materials 2017 Few-atomic-layered hexagonal boron nitride: CVD growth, characterization, and applications Majharu Haque Khan University of Wollongong, [email protected] Hua-Kun Liu University of Wollongong, [email protected] Xudong Sun Northeastern University Yusuke Yamauchi University of Wollongong, [email protected] Yoshio Bando National Institute For Materials Science, [email protected] See next page for additional authors Publication Details Khan, M., Liu, H. Kun., Sun, X., Yamauchi, Y., Bando, Y., Golberg, D. & Huang, Z. (2017). Few-atomic-layered hexagonal boron nitride: CVD growth, characterization, and applications. Materials Today, 20 (10), 611-628. Research Online is the open access institutional repository for the University of Wollongong. For further information contact the UOW Library: [email protected] Few-atomic-layered hexagonal boron nitride: CVD growth, characterization, and applications Abstract Two-dimensional (2D) materials have shown outstanding properties that make them the materials of choice for future semiconductor and flexible nanoelectronics. Hexagonal boron nitride nanosheet (BNNS) is one of the most studied 2D materials due to its extraordinary properties and potential applications. The synthesis of large, homogeneous, and few-layered BNNS, however, remains challenging. Among the various synthetic routes, chemical vapour deposition (CVD) is preferred on the grounds of its potential to yield large BNNS with controllable atomic layers and minimal contamination. We thus devote this review to the CVD growth of BNNS, and its characterization and applications. The er cent progresses in the CVD growth of BNNS is firstly summarized from the aspects of precursors, substrates, growth mechanisms, and transfer techniques. -
Facile 3D Boron Nitride Integrated Electrospun Nanofibrous
nanomaterials Article Facile 3D Boron Nitride Integrated Electrospun Nanofibrous Membranes for Purging Organic Pollutants 1,2,3, 1, 1 1 Dai-Hua Jiang y, Pei-Chi Chiu y, Chia-Jung Cho , Loganathan Veeramuthu , Shih-Huang Tung 2, Toshifumi Satoh 3 , Wei-Hung Chiang 4 , Xingke Cai 5 and Chi-Ching Kuo 1,* 1 Institute of Organic and Polymeric Materials, Research and Development Center of Smart Textile Technology, National Taipei University of Technology, Taipei 10608, Taiwan; [email protected] (D.-H.J.); [email protected] (P.-C.C.); [email protected] (C.-J.C.); [email protected] (L.V.) 2 Institute of Polymer Science and Engineering, National Taiwan University, Taipei 106, Taiwan; [email protected] 3 Faculty of Engineering, Hokkaido University, Sapporo 060-8628, Japan; [email protected] 4 Department of Chemical Engineering, National Taiwan University of Science and Technology, Taipei 10607, Taiwan; [email protected] 5 Institute for Advanced Study, Shenzhen University, Shenzhen 518060, Guangdong, China; [email protected] * Correspondence: [email protected]; Tel.: +886-2-27712171 (ext. 2407) These authors contributed equally to this work. y Received: 25 August 2019; Accepted: 24 September 2019; Published: 27 September 2019 Abstract: Elegant integration of three-dimensional (3D) boron nitride (BN) into the porous structure of a polymer nanofiber (NF) membrane system results in a surface with enhanced absorption capacity for removal. Various BN-based applications were designed and developed successfully, but BN-based absorption systems remain relatively unexplored. To develop a reusable absorption strategy with high removal efficiency, we used a composite of 3D BN and polyacrylonitrile (PAN) to prepare a NF membrane with a porous structure by using electrospinning and spray techniques (BN-PAN ES NFs). -
Loading of Agnps Onto the Surface of Boron Nitride Nanosheets For
www.nature.com/scientificreports OPEN Loading of AgNPs onto the surface of boron nitride nanosheets for determination of scopoletin in Received: 13 November 2018 Accepted: 18 February 2019 Atractylodes macrocephala Published: xx xx xxxx Yinzi Yue1, Li Zeng2, Xiaopeng Wang3, Lianlin Su4, Mingming Sun3, Bensheng Wu3 & Shuai Yan3,4 In this work, silver nanoparticles prepared by a molten salt method were deposited onto the surface of hexagonal boron nitride nanosheet (NS/AgNP) to from a composite. The synthesized nanocomposite was applied for surface modifcation of screen-printed electrode (SPE). The modifed electrode showed a superior performance for electrochemical detection of scopoletin. The electrochemical behaviour of NS/AgNP/SPE was studied in detail. An electrocatalytic oxidation was observed and used for analytical determination of scopoletin concentration. The response of the proposed electrochemical sensing platform was linear over a wide detection range of 2 μM to 0.45 mM with a low limit of detection (LOD) of 0.89 μM. The NS/AgNP/SPE also showed excellent reproducibility and anti-interference property. In addition, the proposed scopoletin sensor was successfully used for the determination of scopoletin in Atractylodes macrocephala herb samples. Hexagonal boron nitride (h-BN) nanosheets, also known as “white graphene”, have a layered structure of hex- agonal boron nitride planes1,2. Tey have unique properties that are diferent from graphene, including a wide bandwidth, insulative characteristics, UV photoluminescence, high thermal conductivity and stability, oxidation resistance and chemical inertness3–9. In addition, the polarity of the nitrogen-boron bond and the high surface area of the h-BN nanosheets enable them to adsorb a variety of substances from aqueous solutions. -
Boron Nitride Nanosheet Veiled Gold Nanoparticles for Surface
ACS Applied Materials & Interfaces 8, 15630, 2016 (DOI: 10.1021/acsami.6b04320) Boron Nitride Nanosheet Veiled Gold Nanoparticles for Surface Enhanced Raman Scattering Qiran Cai,1 Srikanth Mateti,1 Kenji Watanabe,2 Takashi Taniguchi,2 Shaoming Huang,3 Ying Chen1* and Lu Hua Li1* 1. Institute for Frontier Materials, Deakin University, Geelong Waurn Ponds Campus, VIC 3216, Australia 2. National Institute for Materials Science, Namiki 1-1, Tsukuba, Ibaraki 305-0044, Japan 3. Nanomaterials and Chemistry Key Laboratory, Wenzhou University, Wenzhou 325027, China. ABSTRACT Atomically thin boron nitride (BN) nanosheets have many properties desirable for surface enhanced Raman spectroscopy (SERS). BN nanosheets have a strong surface adsorption capability towards airborne hydrocarbon and aromatic molecules. For maximized adsorption area and hence SERS sensitivity, atomically thin BN nanosheet covered gold nanoparticles have been prepared for the first time. When placed on top of metal nanoparticles, atomically thin BN nanosheets closely follow their contours so that the plasmonic hot spots are retained. Electrically insulating BN nanosheets also act as a barrier layer to eliminate metal-induced disturbance in SERS. Moreover, the SERS substrates veiled by BN nanosheets show an outstanding reusability in the long term. As the result, the sensitivity, reproducibility and reusability of SERS substrates can be greatly improved. We also demonstrate that large BN 1 ACS Applied Materials & Interfaces 8, 15630, 2016 (DOI: 10.1021/acsami.6b04320) nanosheets produced by chemical vapor deposition can be used to scale up the proposed SERS substrate for practical application. KEYWORDS: boron nitride nanosheets, surface enhanced Raman spectroscopy (SERS), plasmonic metal particles, reusability, surface adsorption. -
Hexagonal Boron Nitride Nanosheets Synthesis and Applications
University of Wollongong Research Online University of Wollongong Thesis Collection 1954-2016 University of Wollongong Thesis Collections 2016 Hexagonal boron nitride nanosheets synthesis and applications Feng Xiao University of Wollongong Follow this and additional works at: https://ro.uow.edu.au/theses University of Wollongong Copyright Warning You may print or download ONE copy of this document for the purpose of your own research or study. The University does not authorise you to copy, communicate or otherwise make available electronically to any other person any copyright material contained on this site. You are reminded of the following: This work is copyright. Apart from any use permitted under the Copyright Act 1968, no part of this work may be reproduced by any process, nor may any other exclusive right be exercised, without the permission of the author. Copyright owners are entitled to take legal action against persons who infringe their copyright. A reproduction of material that is protected by copyright may be a copyright infringement. A court may impose penalties and award damages in relation to offences and infringements relating to copyright material. Higher penalties may apply, and higher damages may be awarded, for offences and infringements involving the conversion of material into digital or electronic form. Unless otherwise indicated, the views expressed in this thesis are those of the author and do not necessarily represent the views of the University of Wollongong. Recommended Citation Xiao, Feng, Hexagonal boron nitride nanosheets synthesis and applications, Doctor of Philosophy thesis, Institute for Superconducting and Electronic Materials, University of Wollongong, 2016. https://ro.uow.edu.au/theses/4838 Research Online is the open access institutional repository for the University of Wollongong. -
Boron Vacancy
Nanoscale Advances View Article Online PAPER View Journal | View Issue Boron vacancy: a strategy to boost the oxygen reduction reaction of hexagonal boron nitride Cite this: Nanoscale Adv.,2021,3,4739 nanosheet in hBN–MoS2 heterostructure† Dipayan Roy,‡a Karamjyoti Panigrahi, ‡a Bikram K. Das,b Uday K. Ghorui, d Souvik Bhattacharjee, b Madhupriya Samanta,ac Sourav Sarkara and Kalyan K. Chattopadhyay *ab The incorporation of vacancies in a system is considered a proficient method of defect engineering in general catalytic modulation. Among two-dimensional materials, the deficiency of surface active sites and a high band gap restrict the catalytic activity of hexagonal boron nitride (hBN) material towards the oxygen reduction reaction (ORR), which hinders its applicability in fuel cells. A bane to boon strategy has been introduced here by coupling two sluggish ORR materials (hBN & MoS2) by a probe-sonication method to form a heterostructure (termed HBPS) which fosters four electron pathways to assist the Creative Commons Attribution-NonCommercial 3.0 Unported Licence. reduction of oxygen. Theoretical and experimental studies suggest the kinetically and thermodynamically favorable formation of boron vacancies (B-vacancies) in the presence of MoS2, which act as active sites for oxygen adsorption in HBPS. B-vacancy induced uneven charge distribution together with band gap depression promote rapid electron transfer from the valance band to the conduction band which prevails over the kinetic limitation of pure hBN nanosheets towards ORR kinetics. The formed B-vacancy Received 25th April 2021 À induced HBPS further exhibits a low Tafel slope (66 mV dec 1), and a high onset potential (0.80 V vs.