Introduction
Total Page:16
File Type:pdf, Size:1020Kb
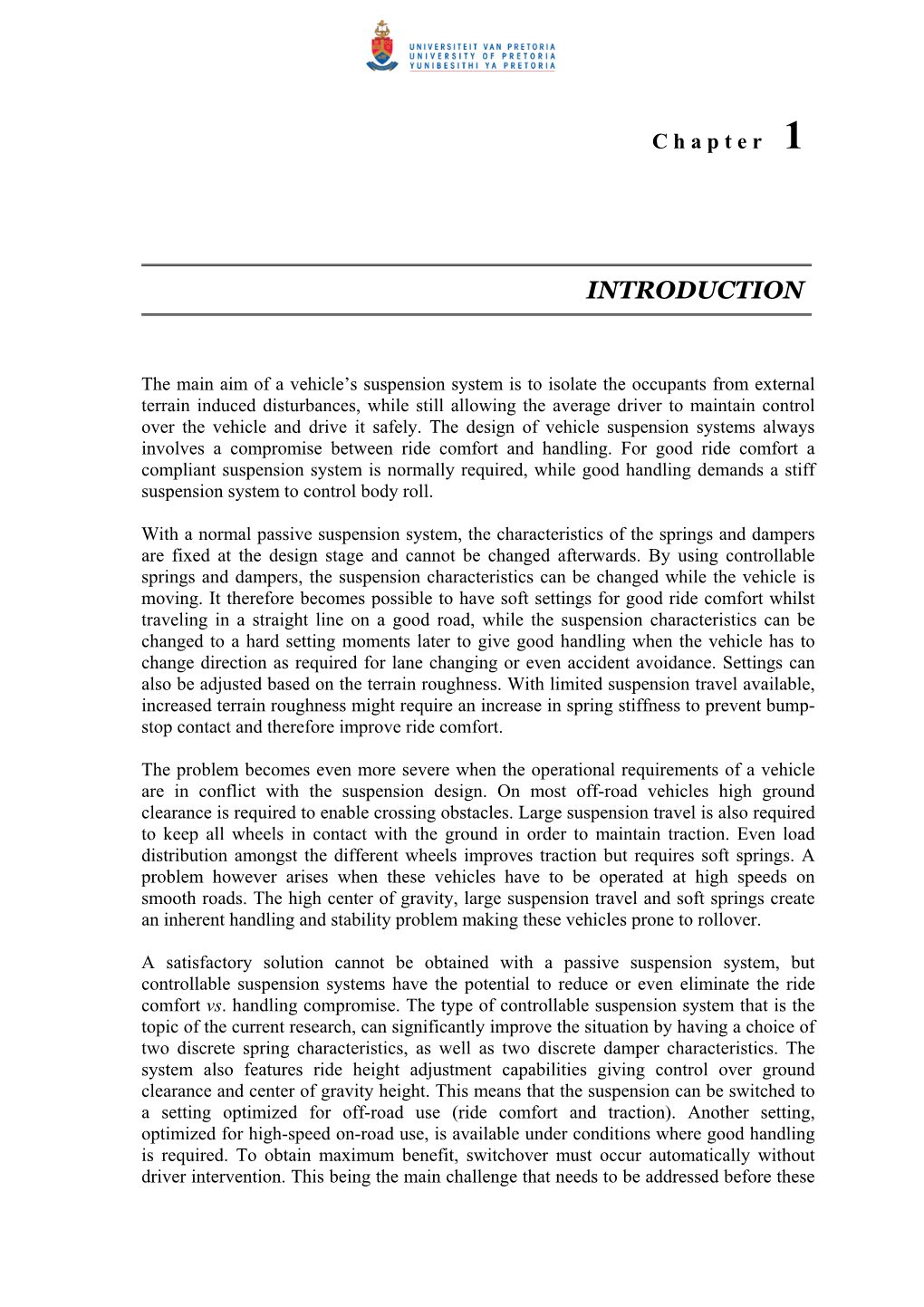
Load more
Recommended publications
-
Variable Dynamic Testbed Vehicle Dynamics Analysis
Variable Dynamic Testbed Vehicle Dynamics Analysis Allan Y. Lee Jet Propulsion Laboratory Nhan T. Le University of California, Los Angeles March 1996 Jet Propulsion Laboratory California Institute of Technology JPL D-13461 Variable Dynamic Testbed Vehicle Dynamics Analysis Allan Y. Lee Jet Propulsion Laboratory Nhan T. Le University of California, Los Angeles March 1996 JPL Jet Propulsion Laboratory California Institute of Technology Table of Contents Page Table of Contents ............................................................ 2 Abstract .................................................................... 3 Introduction................................................................. 4 Scope and Approach.......................................................... 5 Vehicle Dynamic Simulation Program........................................... 6 Selected Production Vehicle Models............................................. 8 Steady-state and Transient Lateral Response Performance Metrics .................. 9 The Selected Baseline Variable Dynamic Vehicle ................................. 12 Sensitivity Analyses .......................................................... 13 Four Wheel Steering Control Algorithms........................................ 16 Results obtained from Consumer Union Obstacle Course .......................... 20 Concluding Remarks.......................................................... 21 References................................................................... 22 Acknowledgments ........................................................... -
P 01.Qxd 6/30/2005 2:00 PM Page 1
p 01.qxd 6/30/2005 2:00 PM Page 1 June 27, 2005 © 2005 Crain Communications GmbH. All rights reserved. €14.95; or equivalent 20052005 GlobalGlobal MarketMarket DataData BookBook Global Vehicle Production and Sales Regional Vehicle Production and Sales History and Forecast Regional Vehicle Production and Sales by Model Regional Assembly Plant Maps Top 100 Global Suppliers Contents Global vehicle production and sales...............................................4-8 2005 Western Europe production and sales..........................................10-18 North America production and sales..........................................19-29 Global Japan production and sales .............30-37 India production and sales ..............39-40 Korea production and sales .............39-40 China production and sales..............39-40 Market Australia production and sales..........................................39-40 Argentina production and sales.............45 Brazil production and sales ....................45 Data Book Top 100 global suppliers...................46-50 Mary Raetz Anne Wright Curtis Dorota Kowalski, Debi Domby Senior Statistician Global Market Data Book Editor Researchers [email protected] [email protected] [email protected], [email protected] Paul McVeigh, News Editor e-mail: [email protected] Irina Heiligensetzer, Production/Sales Support Tel: (49) 8153 907503 CZECH REPUBLIC: Lyle Frink, Tel: (49) 8153 907521 Fax: (49) 8153 907425 e-mail: [email protected] Tel: (420) 606-486729 e-mail: [email protected] Georgia Bootiman, Production Editor e-mail: [email protected] USA: 1155 Gratiot Avenue, Detroit, MI 48207 Tel: (49) 8153 907511 SPAIN, PORTUGAL: Paulo Soares de Oliveira, Tony Merpi, Group Advertising Director e-mail: [email protected] Tel: (35) 1919-767-459 Larry Schlagheck, US Advertising Director www.automotivenewseurope.com Douglas A. Bolduc, Reporter e-mail: [email protected] Tel: (1) 313 446-6030 Fax: (1) 313 446-8030 Tel: (49) 8153 907504 Keith E. -
Bendix ABS-6 Advanced with ESP Stability System
Bendix® ABS-6 Advanced with ESP® Stability System Frequently Asked Questions to Help You Make an Intelligent Investment in Stability Contents: Key FAQs (Start here!)………….. Pg. 2 Stability Definitions …………….. Pg. 6 System Comparison ……………. Pg. 7 Function/Performance ………….. Pg. 9 Value ………………………………. Pg. 12 Availability/Applications ……….. Pg. 14 Vehicle System Integration …….. Pg. 16 Safety ………………………………. Pg. 17 Take the Next Step ………………. Pg. 18 Please note: This document is designed to assist you in the stability system decision process, not to serve as a performance guarantee. No system will prevent 100% of the incidents you may experience. This information is subject to change without notice © 2007 Bendix Commercial Vehicle Systems LLC, a member of the Knorr-Bremse Group. All Rights Reserved. 03/07 1 Key FAQs What is roll stability? Roll stability counteracts the tendency of a vehicle, or vehicle combination, to tip over while changing direction (typically while turning). The lateral (side) acceleration creates a force at the center of gravity (CG), “pushing” the truck/tractor-trailer horizontally. The friction between the tires and the road opposes that force. If the lateral force is high enough, one side of the vehicle may begin to lift off the ground potentially causing the vehicle to roll over. Factors influencing the sensitivity of a vehicle to lateral forces include: the load CG height, load offset, road adhesion, suspension stiffness, frame stiffness and track width of vehicle. What is yaw stability? Yaw stability counteracts the tendency of a vehicle to spin about its vertical axis. During operation, if the friction between the road surface and the tractor’s tires is not sufficient to oppose lateral (side) forces, one or more of the tires can slide, causing the truck/tractor to spin. -
Ride Control Defined
RIDE CONTROL DEFINED According to Newton's First Law, a moving body will continue moving in a straight line until it is acted upon by another force. Newton's Second Law states that for each action there is an equal and opposite reaction. In the case of the automobile, whether the disturbing force is in the form of a wind-gust, an incline in the roadway, or the cornering forces produced by tires, the force causing the action and the force resisting the action will always be in balance. Many things affect vehicles in motion. Weight distribution, speed, road conditions and wind are some factors that affect how vehicles travel down the highway. Under all these variables however, the vehicle suspension system including the shocks, struts and springs must be in good condition. Worn suspension components may reduce the stability of the vehicle and reduce driver control. They may also accelerate wear on other suspension components. Replacing worn or inadequate shocks and struts will help maintain good ride control as they: Control spring and suspension movement Provide consistent handling and braking Prevent premature tire wear Help keep the tires in contact with the road Maintain dynamic wheel alignment Control vehicle bounce, roll, sway, dive and acceleration squat Reduce wear on other vehicle systems Promote even and balanced tire and brake wear Reduce driver fatigue Suspension concepts and components have changed and will continue to change dramatically, but the basic objective remains the same: 1. Provide steering stability with good handling characteristics 2. Maximize passenger comfort Achieving these objectives under all variables of a vehicle in motion is called ride control 1 BASIC TERMINOLOGY To begin this training program, you need to possess some very basic information. -
Surface Protection of Mg Alloys in Automotive Applications: a Review
AIMS Materials Science, 6(4): 567–600. DOI: 10.3934/matersci.2019.4.567 Received: 15 February 2019 Accepted: 04 May 2019 Published: 04 July 2019 http://www.aimspress.com/journal/Materials Review Surface protection of Mg alloys in automotive applications: A review Jie Wang1, Xin Pang2 and Hamid Jahed1,* 1 Department of Mechanical & Mechatronics Engineering, University of Waterloo, Waterloo, ON, Canada N2L 3G1 2 CanmetMATERIALS, Natural Resources Canada, Hamilton, ON, Canada L8P 0A5 * Correspondence: Email: [email protected]. Abstract: Mg alloys find widespread applications in transportation industries especially in cars and trucks because of their edges in light-weight design, which can greatly help improve the fuel efficiency and decrease the gas emissions of vehicles; However, Mg alloys’ high sensitivity to the corrosive environments limit their penetration in automotive applications. Surface coating is one of the most effective and economic ways to protect Mg alloys from corrosion. Presently, the currently researched and commercial coatings that are specifically applied to Mg alloys in the automotive industry are reviewed in this paper. With some Mg automotive components subjected to corrosion and repeated load simultaneously, corrosion fatigue of coated Mg alloys are reviewed as well. Additionally, a part of attention in this review is given to the assessment approaches of corrosion and corrosion fatigue performance of coated Mg alloys for the purpose of material/surface coating system selection. Finally, some corrosion-related -
Less Mower Deck) Equipment for Base Machine
JOHN DEERE TURF & UTILITY PRODUCTS COMMERCIAL FRONT MOWERS AND EQUIPMENT 1550 TerrainCut Commercial Front Mower (Less Mower Deck) Equipment for Base Machine 24.2 HP (17.8 kW), gross SAE mounted) Low Oil Pressure Warning Light J1995, PS 23x10.50-12 In. 4PR Turf (std) Hydraulic Oil Temp. Light and Rated at 3000 rpm Drive Tires Alarm PTO Shutdown Diesel Engine 77 cu. in. (1.27 18x8.50-8 In. 4PR Turf Folding Two Post ROPS (Roll- L) Steering Tires (2WD) or Over Protective Structure) Three Cylinder Liquid-Cooled 18x8.50-10 In. 4PR Turf and Retractable Seat Belt Dual Element Air Cleaner Steering Tires (4WD) Cast Iron Rear Bumper Air Restriction Indicator Transmission Oil Cooler Operator Training Video 12V Electric Start Individual Turn Assist Brakes 12V Auxilary Power Outlet Internal Wet Disk Brakes 75 AMP Automotive Alternator Master Stop Brake 16 U.S. Gallon Fuel Capacity Dual Hydraulic Implement Two Pedal Hydrostatic Foot Lift Cylinders Control Less Mower Deck Hydrostatic Transmission Hourmeter Hydrostatic Front Wheel Drive Fuel Gauge Hydrostatic Power Steering Tilt Steering Wheel Differential Front Wheel Lock PTO Drvien Implements Front Lights (steering column Operator Presence System List Price Attachment Suggested Code Identifier Description USD ($) Select One Code From Each Required Category BASE MACHINE F.O.B. Raleigh, North Carolina 2400TC 1550 TerrainCut Commercial Front Mower (Less Mower Deck) 19,899.00 DESTINATION North America 001A United States and Canada In Base Price DRIVE SYSTEM 1190 Two Wheel Drive In Base Price 1191 Four Wheel Drive (Full Time or On Demand) 2,913.00 Standard on the 1575, 1580, and 1585 TerrainCut Commercial Front Mowers. -
Download but Meet the Buick Terraza
MOTOR page- 11/8/04 3:26 PM Page 1 Chevy Corvette 20 November 2004 MOTOR page- 11/8/04 3:27 PM Page 2 CARS ARE BACK! Tech Preview of the 2005 Domestics BY PAUL WEISSLER Chrysler 300 After a multiyear infatuation with SUVs, the domestic automakers have ‘rediscovered’ the automobile. Our annual report covers several all-new models that have resulted from this new marketing direction. ord is calling 2005 the Year of the Car, and is introduc- ing brand-new cars and carlike “crossover” vehicles. But Fit’s not alone, as General Motors and the Chrysler Group also are focusing on the passenger car for 2005. At Ford, the new Mustang gets the most head-turning looks, of course, but the new Ford 500 and Mercury Montego sedans, and the Freestyle “almost SUV,” are a higher volume group. At Chrysler, the in-your-face 300 and Dodge Magnum wagon are getting plenty of attention. And GM has several significant new Dodge Magnum cars—the compact Chevrolet Cobalt (which replaces the Cava- lier), Pontiac G6 (replacing the Grand Am), Buick LaCrosse (replacing the Regal and Century), Cadillac STS (replacing the Seville) and the Corvette, which is irreplaceable. Let’s delve further into it and see what the three domestic camps are offering for 2005. Ford The Ford 500 and its sister Mercury Montego clearly are cars, but what’s the Freestyle? The North American Car of the Year jury placed it in the truck/SUV category (it has suspension modifications to increase ride height and a wagon-type body with three-row seating), but it’s technically very close to the 500. -
2009 Cadillac Xlr Warranty.Pdf
IMPORTANT: This booklet contains important information about the vehicle’s warranty coverage. It also explains owner assistance information and GM’s participation in an Alternative Dispute Resolution Program. Keep this booklet with your vehicle and make it available to a Cadillac dealer if warranty work is needed. Be sure to keep it with your vehicle if you sell it so future owners will have the information. Owner’s Name: Street Address: City & State: Vehicle Identification Number (VIN): Date Vehicle First Delivered or Put In Use: Odometer Reading on Date Vehicle First Delivered or Put In Use: Have you purchased the Genuine GM Protection Plan? The GM Protection Plan may be purchased within specific time/mileage limitations. See the information request form in the back of this booklet. Remember, if the service contract you are considering for purchase does not have the GM Protection Plan emblem shown above on it, then it is not the Genuine GM Protection Plan from GM. ©2008 Cadillac Motor Car Division, General Motors Corporation. All rights reserved. Printed in the U.S.A. GENERAL MOTORS, GM, CADILLAC, and the CADILLAC emblem are registered trademarks of General Motors Corporation. Part No. 15911414 B Second Printing 2009 Cadillac Limited Warranty and Owner Assistance Information An Important Message to Cadillac Owners... .........1 Tire Service ....................................................14 Cadillac’s Commitment to You ............................1 6.6L DURAMAX® Diesel Engine Owner Assistance .............................................1 -
TRACTOR 4100 Serial # 1001-1501
OWNER/OPERATOR’S MANUAL TRACTOR 4100 Serial # 1001-1501 REVISED 04-18-07 2ND EDITION 09.10026 Venture Products Inc. Orrville, OH Orrville, OH www.ventrac.com TO THE OWNER Congratulations on the purchase of a new VENTRAC 4100! The purpose of this manual is to assist you in its safe and effective operation and maintenance. With proper usage and care, the Tractor will provide many years of service. Please read and understand this manual entirely before using the Tractor. Keep this manual on file for future reference. Always give Model and Serial # when ordering service parts. Please fill in the following information for future reference: Date of Purchase: Month _________________ Day __________ Year ____________ Model Number: _______________________________________________________ Serial Number: ________________________________________________________ Dealer: ______________________________________________________________ Dealer Address: _______________________________________________________ _______________________________________________________ Dealer Phone Number: _________________________________________________ Dealer FAX Number: ___________________________________________________ Venture Products Inc. reserves the right to make changes in design or specifications without incurring obligation to make like changes on previously manufactured products. ii TABLE OF CONTENTS INTRODUCTION SECTION A Description .....................................A-1 Specifications ...................................A-2 SAFETY SECTION B Safety Symbols ..................................B-1 -
Vehicle Load Transfer
Vehicle Load Transfer Wm Harbin Technical Director BND TechSource 1 Vehicle Load Transfer Part I General Load Transfer 2 Factors in Vehicle Dynamics . Within any modern vehicle suspension there are many factors to consider during design and development. Factors in vehicle dynamics: • Vehicle Configuration • Vehicle Type (i.e. 2 dr Coupe, 4dr Sedan, Minivan, Truck, etc.) • Vehicle Architecture (i.e. FWD vs. RWD, 2WD vs.4WD, etc.) • Chassis Architecture (i.e. type: tubular, monocoque, etc. ; material: steel, aluminum, carbon fiber, etc. ; fabrication: welding, stamping, forming, etc.) • Front Suspension System Type (i.e. MacPherson strut, SLA Double Wishbone, etc.) • Type of Steering Actuator (i.e. Rack and Pinion vs. Recirculating Ball) • Type of Braking System (i.e. Disc (front & rear) vs. Disc (front) & Drum (rear)) • Rear Suspension System Type (i.e. Beam Axle, Multi-link, Solid Axle, etc.) • Suspension/Braking Control Systems (i.e. ABS, Electronic Stability Control, Electronic Damping Control, etc.) 3 Factors in Vehicle Dynamics . Factors in vehicle dynamics (continued): • Vehicle Suspension Geometry • Vehicle Wheelbase • Vehicle Track Width Front and Rear • Wheels and Tires • Vehicle Weight and Distribution • Vehicle Center of Gravity • Sprung and Unsprung Weight • Springs Motion Ratio • Chassis Ride Height and Static Deflection • Turning Circle or Turning Radius (Ackermann Steering Geometry) • Suspension Jounce and Rebound • Vehicle Suspension Hard Points: • Front Suspension • Scrub (Pivot) Radius • Steering (Kingpin) Inclination -
Skid Pad Project
Skid Pad Project Lewis-Clark State College Workforce Training Workforce Training Facility 2 Excavation and Paving Skid Pad Project Lewis-Clark State College Workforce Training Phase 1: Excavate and Pave Existing Gravel Area 4 The following slides depict the area prior to paving 5 Location for staging area and garage 6 Perspective of the area from southwest corner of property 7 Engineers observing the test pass 8 The project used local contractors and provided jobs for the valley. 9 Excavation and paving took less than one month 10 Skid Pad paving completed 11 Phase 2: Skid Pad Garage and Security Fence Skid Pad Project Lewis-Clark State College Workforce Training Pole Building design with electrical conduits 13 Local contractor was awarded the bid contract 14 Materials purchased from local suppliers 15 Project provided labor jobs 16 Completed Garage is 54x32 feet 17 Perspective from front gate to Skid Pad 18 Phase 3: Skid Truck Skid Pad Project Lewis-Clark State College Workforce Training Skid Truck was manufactured by International Co. 20 Installation of flat-bed 21 Skid Truck 22 Phase 4: Technology Skid Pad Project Lewis-Clark State College Workforce Training Technology installed to the Truck 24 Skid Truck 25 Lewis-Clark State College invested funds to expand the program Skid Pad Project Lewis-Clark State College Workforce Training Skid SUV 27 The Lewis-Clark State College Skid Fleet 28 Use Of A Skid Pad For Training Truck Drivers: The Lewis-Clark State College Project Driver Development Course Achieving Accountability Through Advanced Understanding and Techniques Driver Accountability 2 Keepin’ it between the lines OUR GOAL: To help you become a more proactive driver To develop advanced insight as a driver A proactive driver is defined as one who uses superior knowledge to avoid situations that require superior skill. -
Cranfield University
CRANFIELD UNIVERSITY KONSTANTINOS ZARKADIS MODEL PREDICTIVE TORQUE VECTORING CONTROL WITH ACTIVE TRAIL-BRAKING FOR ELECTRIC VEHICLES SCHOOL OF AEROSPACE, TRANSPORT AND MANUFACTURING Transport Systems MSc by Research Academic Year: 2016–2017 Supervisor: Dr E. Velenis and Dr S. Longo February 2018 CRANFIELD UNIVERSITY SCHOOL OF AEROSPACE, TRANSPORT AND MANUFACTURING Transport Systems MSc by Research Academic Year: 2016–2017 KONSTANTINOS ZARKADIS Model Predictive Torque Vectoring Control with Active Trail-Braking for Electric Vehicles Supervisor: Dr E. Velenis and Dr S. Longo February 2018 This thesis is submitted in partial fulfilment of the requirements for the degree of MSc by Research. © Cranfield University 2018. All rights reserved. No part of this publication may be reproduced without the written permission of the copyright owner. Abstract In this work we present the development of a torque vectoring controller for electric ve- hicles. The proposed controller distributes drive/brake torque between the four wheels to achieve the desired handling response and, in addition, intervenes in the longitudinal dynamics in cases where the turning radius demand is infeasible at the speed at which the vehicle is traveling. The proposed controller is designed in both the Linear and Nonlin- ear Model Predictive Control framework, which have shown great promise for real time implementation the last decades. Hence, we compare both controllers and observe their ability to behave under critical nonlinearities of the vehicle dynamics in limit handling conditions and constraints from the actuators and tyre-road interaction. We implement the controllers in a realistic, high fidelity simulation environment to demonstrate their performance using CarMaker and Simulink. Keywords torque vectoring; MPC; nonlinear predictive control; FEV.