Foam Transport in Porous Media – a Review
Total Page:16
File Type:pdf, Size:1020Kb
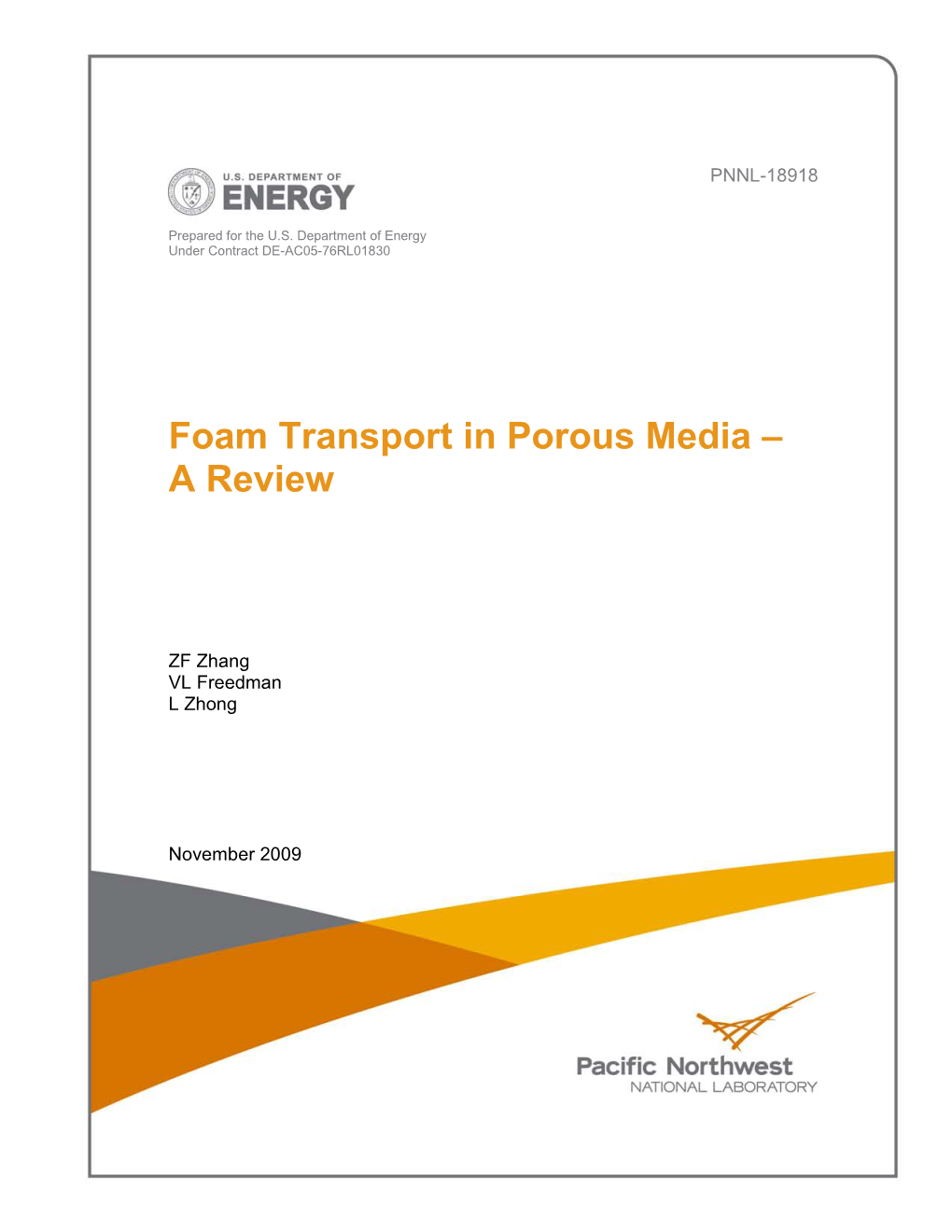
Load more
Recommended publications
-
Numerical Modeling of Capillary-Driven Flow in Open Microchannels: an Implication of Optimized Wicking Fabric Design
Scholars' Mine Masters Theses Student Theses and Dissertations Summer 2018 Numerical modeling of capillary-driven flow in open microchannels: An implication of optimized wicking fabric design Mehrad Gholizadeh Ansari Follow this and additional works at: https://scholarsmine.mst.edu/masters_theses Part of the Environmental Engineering Commons, Mathematics Commons, and the Mechanical Engineering Commons Department: Recommended Citation Ansari, Mehrad Gholizadeh, "Numerical modeling of capillary-driven flow in open microchannels: An implication of optimized wicking fabric design" (2018). Masters Theses. 7792. https://scholarsmine.mst.edu/masters_theses/7792 This thesis is brought to you by Scholars' Mine, a service of the Missouri S&T Library and Learning Resources. This work is protected by U. S. Copyright Law. Unauthorized use including reproduction for redistribution requires the permission of the copyright holder. For more information, please contact [email protected]. NUMERICAL MODELING OF CAPILLARY-DRIVEN FLOW IN OPEN MICROCHANNELS: AN IMPLICATION OF OPTIMIZED WICKING FABRIC DESIGN by MEHRAD GHOLIZADEH ANSARI A THESIS Presented to the Faculty of the Graduate School of the MISSOURI UNIVERSITY OF SCIENCE AND TECHNOLOGY In Partial Fulfillment of the Requirements for the Degree MASTER OF SCIENCE IN ENVIRONMENTAL ENGINEERING 2018 Approved by Dr. Wen Deng, Advisor Dr. Joseph Smith Dr. Jianmin Wang Dr. Xiong Zhang 2018 Mehrad Gholizadeh Ansari All Rights Reserved iii PUBLICATION THESIS OPTION This thesis has been formatted using the publication option: Paper I, pages 16-52, are intended for submission to the Journal of Computational Physics. iv ABSTRACT The use of microfluidics to transfer fluids without applying any exterior energy source is a promising technology in different fields of science and engineering due to their compactness, simplicity and cost-effective design. -
Measurement of Dynamic Capillary Pressure and Viscosity Via the Multi-Sample Micro-Slit Rheometer Doyoung Moon, Kalman B
ARTICLE IN PRESS Chemical Engineering Science ( ) -- Contents lists available at ScienceDirect Chemical Engineering Science journal homepage: www.elsevier.com/locate/ces Measurement of dynamic capillary pressure and viscosity via the multi-sample micro-slit rheometer Doyoung Moon, Kalman B. Migler ∗ Polymers Division, 100 Bureau Drive, NIST, Gaithersburg, Maryland 20899, USA ARTICLE INFO ABSTRACT Article history: We develop two direct methods to simultaneously measure the dynamic capillary pressure and the vis- Received 14 October 2008 cosity of fluids by application of differential forces during flow into micro-channels. In the first method, Received in revised form 30 January 2009 a series of external pressures is applied in conjunction with the dynamic capillary pressure and a “Bagley Accepted 18 February 2009 analysis” is applied to the flow front velocity, and in the second, we utilize differential gravitational forces. By explicitly measuring the dynamic capillary pressure, the measurement window of the recently Keywords: developed multi-sample micro-slit rheometer is extended to the regime where capillary forces are signif- Imbibition Dynamic capillary pressure icant. These measurement methods will be useful in understanding filling flows encountered in diverse Contact angle areas such as microfluidics, oil recovery and biological transport. Microfluidics Published by Elsevier Ltd. Viscosity Rheometer 1. Introduction (for the case of a rectangular capillary) where is the surface tension, is the contact angle, and h and w are -
Investigation of Fluid Wicking Behavior in Micro- Channels and Porous Media by Direct Numerical Simulation
Investigation of Fluid Wicking Behavior in Micro- Channels and Porous Media by Direct Numerical Simulation Ph.D. Dissertation By An Fu Master of Science, Mechanical Engineering, University of Cincinnati, 2016 April. 12th, 2019 Committee Chair: Dr. Milind Jog 1 A B S T R A C T Capillary transport phenomenon in porous media can be found in numerous natural processes and industrial applications such as inkjet printing, filtration, and enhanced oil recovery. In many of these applications, fluid penetration can be categorized into two orientations, viz., unidirectional (linear) and radial. In this thesis, the wicking process for both orientations has been investigated. Direct numerical simulation with Volume-of-Fluid (VOF) method has been implemented at pore scale (micro-scale simulation) to solve the transient governing equations, and global properties such as meniscus displacement and capillary pressure have been calculated to investigate macroscopic spontaneous imbibition (wicking) process. Linear fluid penetration kinetics within the viscous stage is first considered to investigate if the pore size and distribution are contributing factors which shift the overall kinetics, and how interface mobility is influenced by geometry layout. Various cases are simulated with increasing geometric complexity; from simple pore space connection with uniform pore size to complicated connection with random pore sizes. Average meniscus location, capillary pressure and other global variables are examined. The results indicate that within the viscous regime, the Lucas-Washburn behavior is valid in homogeneous porous media, even with random pore size and connection. However, in non-homogeneous structure, the wicking kinetic does depend on the distribution of pore spaces, and Lucas-Washburn equation fails to describe the linear macroscopic capillarity. -
Capillary Phenomena in Porous Media: Pore and Grain Scale Studies
CAPILLARY PHENOMENA IN POROUS MEDIA: PORE AND GRAIN SCALE STUDIES A Dissertation Presented to The Academic Faculty by Zhonghao Sun In Partial Fulfillment of the Requirements for the Degree Doctor of Philosophy in the School of Civil and Environmental Engineering Georgia Institute of Technology August 2018 COPYRIGHT © 2018 BY ZHONGHAO SUN CAPILLARY PHENOMENA IN POROUS MEDIA: PORE AND GRAIN SCALE STUDIES Approved by: Dr. J. Carlos Santamarina, Advisor Dr. Sheng Dai School Civil and Environmental School of Civil and Environmental Engineering Engineering Georgia Institute of Technology Georgia Institute of Technology Dr. J. David Frost Dr. Guillermo Goldsztein School of Civil and Environmental School of Mathematics Engineering Georgia Institute of Technology Georgia Institute of Technology Dr. Susan E. Burns School of Civil and Environmental Engineering Georgia Institute of Technology Date Approved: May 4, 2018 ACKNOWLEDGEMENTS Many people have offered support and suggestions over the last five years; I own thanks to you all. I want to thank my Ph.D. advisor, Carlos Santamarina, for providing me such a great opportunity and wonderful time in my life. I am deeply grateful for his persevering guidance and support. Experiences of working with him taught me valuable lessons, both professional and personal. I thank my thesis committee members, Dr. Susan E. Burns, Dr. J. David Frost, Dr. Sheng Dai, and Dr. Guillermo Goldsztein, for valuable comments and suggestions. Special thanks to Dr. J. David Frost for generous support. I am grateful to Qi Liu and Junbong Jang for the time we worked together. The collaboration helped me deepen my insight of capillary phenomena and broaden my thinking of doing research. -
Impacts on Oil Recovery from Capillary Pressure and Capillary Heterogeneities
IMPACTS ON OIL RECOVERY FROM CAPILLARY PRESSURE AND CAPILLARY HETEROGENEITIES by Thomas Bognø A dissertation submitted to the Department of Physics and Technology at the University of Bergen in partial fulfilment of the requirements for the degree doctor scientiarum. Pau, France, March, 2008. ISBN 978-82-308-0588-6 Bergen, Norway 2008 Printed by Allkopi Tel: +47 55 54 49 40 ii SUMMARY This thesis summarises the findings made in NFR-funded project “Capillary Pressure and Capillary Heterogeneities”. The focus has been to determine the impact on oil recovery from wettability and fractures in carbonate rocks. Secondly a new method for measuring capillary pressure has been developed. The results of this work are reported in this thesis. The work presented in this thesis has improved the understanding of the interaction between wettability and fractures on the production mechanisms in carbonate reservoirs, in different directions. Figure 1 gives an overview of the project “Capillary Pressures and Capillary Heterogeneities”, its fundamental building blocks and the interaction between them to better understand how main conclusions in this study may be drawn; Building block 1: A reproducible method for altering wettability has been developed, and continuously improved throughout the study. Feed-back from the large scale block experiments have actively been used to improve the wettability alteration technique, in particular when it comes to radial and lateral wettability heterogeneity. This is further described in Paper 1 and 2. Building block 2: The study of fracture crossing mechanisms at different wettabilities has improved the understanding of the production mechanisms in fractured chalk. The observations in the large scale block experiments have been used to understand the results of the fracture crossing experiments and vice versa. -
Microfluidics Toward a Lab-On-A-Chip
13 Dec 2003 18:58 AR AR203-FL36-15.tex AR203-FL36-15.sgm LaTeX2e(2002/01/18) P1: IBD 10.1146/annurev.fluid.36.050802.122124 Annu. Rev. Fluid Mech. 2004. 36:381–411 doi: 10.1146/annurev.fluid.36.050802.122124 Copyright c 2004 by Annual Reviews. All rights reserved ENGINEERING FLOWS IN SMALL DEVICES: Microfluidics Toward a Lab-on-a-Chip H.A. Stone,1 A.D. Stroock,2 and A. Ajdari3 1Division of Engineering and Applied Sciences, Harvard University, Cambridge, Massachusetts 02138; email: [email protected] 2School of Chemical and Biomolecular Engineering, Cornell University, Ithaca, New York 14853; email: [email protected] 3Physico-Chimie Theorique,´ UMR CNRS-ESPCI 7083, ESPCI, 10 rue Vauquelin, 75005 Paris, France; email: [email protected] Key Words low-Reynolds-number hydrodynamics, electro-osmosis, nanofluidics, microdevices, mixing ■ Abstract Microfluidic devices for manipulating fluids are widespread and finding uses in many scientific and industrial contexts. Their design often requires unusual geometries and the interplay of multiple physical effects such as pressure gradients, electrokinetics, and capillarity. These circumstances lead to interesting variants of well-studied fluid dynamical problems and some new fluid responses. We provide an overview of flows in microdevices with focus on electrokinetics, mixing and dispersion, and multiphase flows. We highlight topics important for the description of the fluid dynamics: driving forces, geometry, and the chemical characteristics of surfaces. 1. INTRODUCTION Microfluidics refers to devices and methods for controlling and manipulating fluid flows with length scales less than a millimeter. Studies of such fluid-related phe- nomena have long been part of the fluid mechanical component of colloid science (e.g., Russel et al. -
Lab on a Chip PAPER
View Article Online / Journal Homepage / Table of Contents for this issue Lab on a Chip Dynamic Article Links Cite this: Lab Chip, 2012, 12, 2858–2864 www.rsc.org/loc PAPER Pinned films and capillary hysteresis in microfluidic channels Yihong Liu,a David D. Noltea and Laura J. Pyrak-Nolteabc Received 11th March 2012, Accepted 20th April 2012 DOI: 10.1039/c2lc40247e Pinned water films in a microfluidic channel act as elastic membranes under tension that increase capillary pressures while preserving the mechanical work dissipated around capillary pressure- saturation, Pc–Sw, hysteresis cycles. High-resolution two-photon laser micromachining of SU-8 photoresist was used to fabricate wedge-shaped microfluidic channels that included sharp edge features to pin wetting films during drainage. The films were measured using confocal fluorescence microscopy. The tension in the film acts as an elastic tether that shifts the Pc–Sw hysteresis cycle higher in pressure relative to the hysteresis cycle in the same sample when films are not pinned. The film tension is strongly nonlinear as the restoring force decreases with increasing displacement. The contribution of elastic forces to hysteresis has important consequences for pressure and saturation control in microfluidics. 1. Introduction where ul is the position of the interface that is not pinned, um is the position of the pinned interface and k is the effective spring The hysteresis of saturations and pressures is ubiquitous in all constant of the contact line. As the distance between the bulk 1–7 complex pore geometries that support multiple fluid phases. A fluid-fluid interface moves farther from the site of pinning, the complete understanding of capillary hysteresis in micro-fluidic elastic force increases, similar to the increase in force that occurs devices and other porous media containing immiscible fluids by stretching a spring, which defines Hookean behaviour. -
Capillary Biochip for Point of Use Biomedical Application
Capillary Biochip for point of use biomedical application Joana de Carvalho Rodrigues Mesquita Chim Thesis to obtain the Master of Science Degree in Biomedical Engineering Supervisors: Prof. João Pedro Estrela Rodrigues Conde and Dr. João Garcia da Fonseca Examination Committee Chairperson: Prof. Raúl Daniel Lavado Carneiro Martins Members of the Committee: Dr. Nuno Alexandre Esteves Reis Prof. Frederico Castelo Alves Ferreira October 2015 Abstract Microfluidic devices have become an attractive technology in terms of point of care use, due to reduction of sample and reagents consumption, time and also costs of analysis. These devices allow to simplify laboratory protocols and perform them in a single chip of small dimensions. However, some of the devices developed require combining the chip with external equipment that can be complex for handling and difficult the PoC application. In order to solve these issues, capillary chips come into play. Capillary-driven microfluidics introduce a wide range of benefits, including being user friendly and portability, owed to the fact that fluid flow is only controlled by the surface wetting properties of the device. Taking advantage of these benefits this work proposes a capillary chip for a specific biomedical application, namely an immunoassay or the detection of the mycotoxin OTA. PDMS and glass were the materials chosen for the fabrication of the capillary chips. In addition an intensive study of the work conditions is presented. Namely the effect that different capillary pumps can have in fluid motion. Since surface properties are determinant in capillarity, the influence of the UV/Ozone treatment was also tested. In terms of application, the chip was shown to be capable of providing the required conditions for performing the OTA immunoassay. -
The Effect of Surface-Active Solutes on Water Flow and Contaminant Transport in Variably Saturated Porous Media with Capillary Fringe Effects
Journal of Contaminant Hydrology 56 (2002) 247–270 www.elsevier.com/locate/jconhyd The effect of surface-active solutes on water flow and contaminant transport in variably saturated porous media with capillary fringe effects E.J. Henry a, J.E. Smith b,* aDepartment of Hydrology and Water Resources, University of Arizona, Tucson, AZ, 85721 USA bSchool of Geography and Geology, McMaster University, 1280 Main St. West, Hamilton, ON, Canada L8S 4L8 Received 20 December 2000; received in revised form 12 October 2001; accepted 23 October 2001 Abstract Organic contaminants that decrease the surface tension of water (surfactants) can have an effect on unsaturated flow through porous media due to the dependence of capillary pressure on surface tension. We used an intermediate-scale 2D flow cell (2.44 Â 1.53 Â 0.108 m) packed with a fine silica sand to investigate surfactant-induced flow perturbations. Surfactant solution (7% 1-butanol and dye tracer) was applied at a constant rate at a point source located on the soil surface above an unconfined synthetic aquifer with ambient groundwater flow and a capillary fringe of f 55 cm. A glass plate allowed for visual flow and transport observations. Thirty instrumentation stations consist of time domain reflectometry probes and tensiometers measured in-situ moisture content and pressure head, respectively. As surfactant solution was applied at the point source, a transient flow perturbation associated with the advance of the surfactant solution was observed. Above the top of the capillary fringe the advance of the surfactant solution caused a visible drainage front that radiated from the point source. -
An Abstract of the Thesis Of
AN ABSTRACT OF THE THESIS OF Diba Behnoudfar for the degree of Master of Science in Chemical Engineering presented on April 27, 2020. Title: Exploring the Wettability States and Contact Angle Variation in Porous Media Multi-Phase Flow Systems. Abstract approved: ______________________________________________________ Dorthe Wildenschild The wetting of a surface by a liquid is a crucial part of many natural and industrial processes. Despite numerous existing studies, some elements of wetting-dewetting such as contact angle variation are still poorly understood. Knowledge of contact angle behavior during the flow is necessary for modeling fluid displacements in capillary-dominated flows. In the context of multi-phase flow in porous medium, the lack of direct contact angle measurements inside pores (in-situ), adds to the ambiguity. This work consists of performing in-situ contact angle measurements on X-ray micro-computed tomography images of multi-phase fluid systems during quasi-static flow and investigating the effects of pore geometry and interfacial forces on contact angle. An algorithm enabled automated analysis of contact angle throughout the three-dimensional images. Observations revealed two unique contact angle variation patterns for oil (dodecane)-water and air-water systems with larger hysteresis for the oil-water. Introduction of a third phase (air) and altering surface chemistry (wettability) of a portion of solid phase, influenced oil-water contact angle near unaltered surfaces, but the overall trend remained the same. Results -
A Computational Model for the Capillary Flow Between Parallel
Naghashnejad and Shabgard/ Preprint submitted to peer reviewed international journal A Computational Model for the Capillary Flow between Parallel Plates Mohammad Naghashnejad, Hamidreza Shabgard* School of Aerospace and Mechanical Engineering, University of Oklahoma, Norman, OK, USA *Corresponding Author Phone: +1-405-3255753, E-mail: [email protected] Abstract A computational fluid dynamics (CFD) model is developed to simulate the dynamics of meniscus formation and capillary flow between vertical parallel plates. The arbitrary Lagrangian-Eulerian (ALE) approach was employed to predict and reconstruct the exact shape of the meniscus. The model was used to simulate the rise of water and the evolution of the meniscus in vertical channels with various spacing values of 0.5 mm, 0.7 mm, and 1 mm. The validity of the model was established by comparing the steady-state capillary height and the meniscus profile with analytical solutions. The developed model presents a novel approach for simulation of capillary flow accounting for the detailed hydrodynamic phenomena that cannot be captured by analytical models. Keywords: Capillary flow, Meniscus, Dynamic Mesh, Parallel Plates, CFD 1. Introduction Liquid flows driven by capillary action appear in a wide range of applications in natural and industrial systems, including water transport in plants, heat pipes and spacecraft Propellant Management Devices (PMDs) [1]. Capillary action is the spontaneous movement of liquid within the voids formed by solid surfaces due to the interaction of adhesion, cohesion, and surface tension forces. The adhesion between the liquid and solid walls along with the surface tension force (cohesion between the liquid molecules) at the liquid-gas interface create the driving force for penetration of the liquid column inside the capillary conduit. -
Chapter 2 FLUID INTERFACES and CAPILLARITY
Chapter 2 FLUID INTERFACES AND CAPILLARITY A. Fluid interfaces: Young’s Membrane Model 1. The thinness of interfaces Fluid-fluid interfaces are a good place to start because they are far simpler to describe than fluid-solid or solid-solid interfaces. The molecular mobility in fluids makes it reasonable to assume that they will be in internal mechanical and diffusional equilibrium. Thus when the composition and the required number of thermodynamic state variables are set, the system is uniquely defined. In solids, non-equilibrium structures are frozen in place over time scales of practical interest. Fluid interfaces are smooth (as opposed to generally rough), morphologically and energetically homogeneous (as opposed to heterogeneous) and free of all internal shear stresses when at rest (as opposed to supporting un-relaxed internal stresses). Consider first the simplest case of all, viz., the interface between a pure liquid (water) and its equilibrium vapor at 20°C. The pressure is then the vapor pressure of water at 20°C, i.e., 2.33 kPa. As noted earlier, the interface is not a mathematical discontinuity, but rather a thin stratum of material whose intensive properties vary across it from those of the liquid phase to those of the gas phase, as suggested in Fig. 1-1. In going from the liquid phase to the gas phase in the present case, the density decreases by a factor of approximately 58,000! It is known that, except when one is very near to the critical point, the stratum of inhomogeneity at a liquid surface is very very thin, usually of the order of a few Ångströms.