Trl6 Lunar Resource Prospector Drill
Total Page:16
File Type:pdf, Size:1020Kb
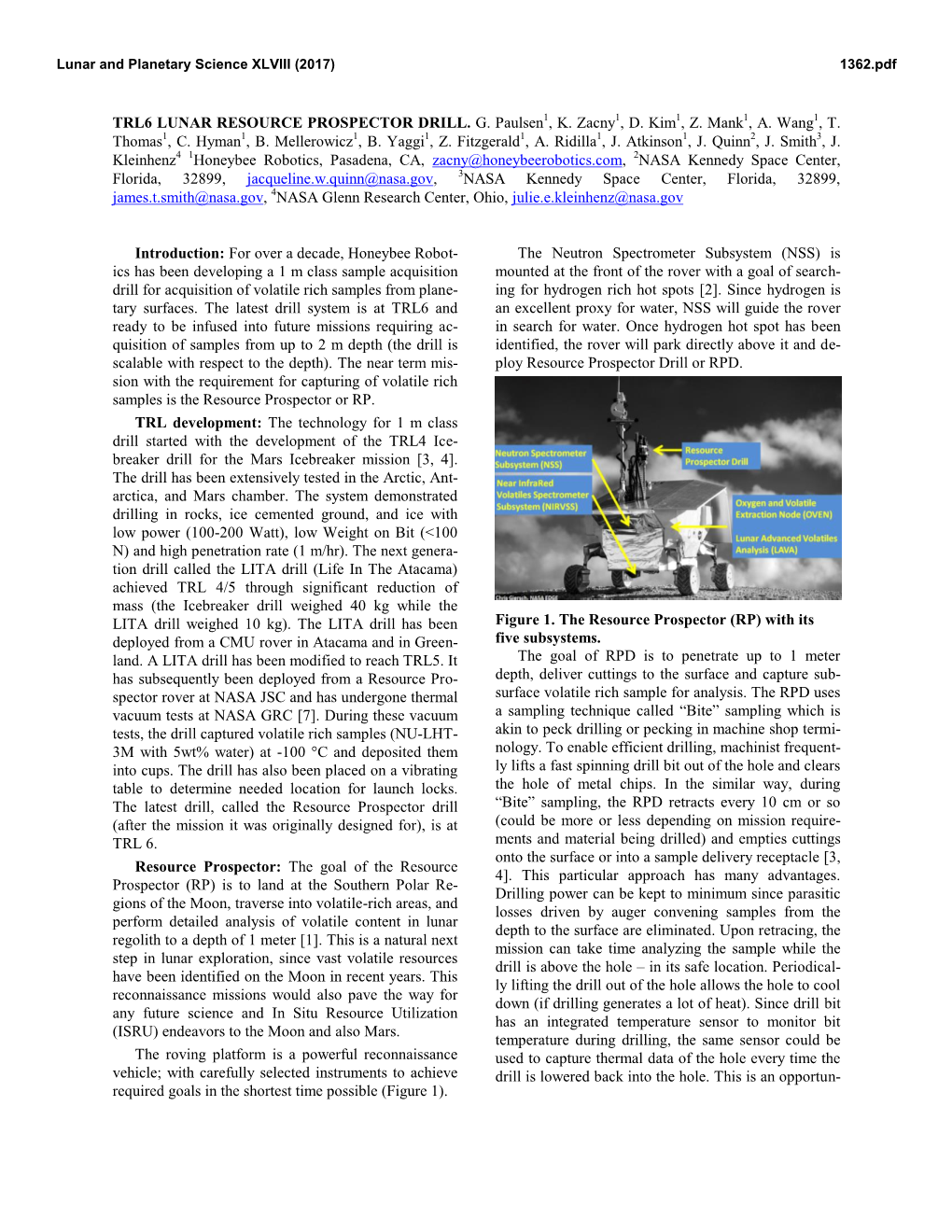
Load more
Recommended publications
-
Return to the Moon Mission Overview
Return to the Moon Mission Overview The new millennium is still young, but humans using the lastest in transport technology to are preparing to Return to the Moon, reduce the travel time. In addition to verifying spurred on by the verification of ice water on the best site for the establishment of the the lunar surface by Lunar Prospector in lunar base, during the course of the mission, 1998. Composed of hydrogen and oxygen – the crew will recover a probe that is the elements that make up water – the lunar stranded in space and access the damage to ice provides a core resource for long-term the probe, and then build and launch an human presence on the lunar surface. equipment module to the lunar surface. Lunar Prospector was followed by a series of Some information has been previously successful robotic missions designed to obtained from the potential lunar base sites. probe the concept that the ice water could A detailed study has determined that the be harvested. Once collected, the ice water base site must contain solid, metals, and can be turned into drinking water, oxygen for potentially useful resources such as helium-3. life support of a lunar base, nutrients as the Rock and soil samples, soil composition, and basis for agriculture, components needed for seismic information have been gathered by rocket fuel, or when combined with lunar soil, previous missions from a portion of the the basics for construction materials. Not potential sites. Experiments on soil and rock only did those robotic missions successfully samples from other possible sites must be prove that concept, but since then, additional performed in order to determine the best robotic staging missions have landed and site for the lunar base. -
Conceptual Human-System Interface Design for a Lunar Access Vehicle
Conceptual Human-System Interface Design for a Lunar Access Vehicle Mary Cummings Enlie Wang Cristin Smith Jessica Marquez Mark Duppen Stephane Essama Massachusetts Institute of Technology* Prepared For Draper Labs Award #: SC001-018 PI: Dava Newman HAL2005-04 September, 2005 http://halab.mit.edu e-mail: [email protected] *MIT Department of Aeronautics and Astronautics, Cambridge, MA 02139 TABLE OF CONTENTS 1 INTRODUCTION..................................................................................................... 1 1.1 THE GENERAL FRAMEWORK................................................................................ 1 1.2 ORGANIZATION.................................................................................................... 2 2 H-SI BACKGROUND AND MOTIVATION ........................................................ 3 2.1 APOLLO VS. LAV H-SI........................................................................................ 3 2.2 APOLLO VS. LUNAR ACCESS REQUIREMENTS ...................................................... 4 3 THE LAV CONCEPTUAL PROTOTYPE............................................................ 5 3.1 HS-I DESIGN ASSUMPTIONS ................................................................................ 5 3.2 THE CONCEPTUAL PROTOTYPE ............................................................................ 6 3.3 LANDING ZONE (LZ) DISPLAY............................................................................. 8 3.3.1 LZ Display Introduction................................................................................. -
Reviewing the Contribution of GRAIL to Lunar Science and Planetary Missions Maria T
EPSC Abstracts Vol. 12, EPSC2018-575, 2018 European Planetary Science Congress 2018 EEuropeaPn PlanetarSy Science CCongress c Author(s) 2018 Reviewing the contribution of GRAIL to lunar science and planetary missions Maria T. Zuber and David E. Smith Department of Earth, Atmospheric and Planetary Sciences, Massachusetts Institute of Technology, Cambridge, MA 02139- 4307, USA. ([email protected], [email protected]) Abstract Q of the Moon determined to be 41±4 at the monthly frequency. The GRAIL Discovery mission to the Moon in 2011 provided an unprecedentedly accurate gravity field model for the Moon. The goal of the mission was to provide insight into the structure of the Moon from its interior to the surface but it also made significant contributions to lunar spacecraft operations for all future lunar missions to the Moon. We discuss the science and the broader contributions from this mission that completed its objectives in December 2012 when the spacecraft impacted the lunar surface. 1. Introduction Figure 1: Free-air gravity of the Moon from GRAIL. GRAIL was a mission designed to measure the Full uniform resolution spherical harmonic models gravity field of the Moon with both high accuracy were obtained out to degree & order 1200 with and high resolution. The measurement goal was to special fields with higher resolutions over certain obtain the gravity at resolutions that would enable areas to degree and order 1800. interpretation of the crust at fractions of its thickness, estimated at the time of launch to be about 45 km. To 3. Mission Operations obtain a surface resolution of less than 10 km required the spacecraft to orbit the Moon at less than The significant improvement in our knowledge of the 20 km, an altitude that was considered dangerous at gravity field of the Moon by GRAIL enabled the re- that time without an accurate gravity field model. -
Robotic Asteroid Prospector
Robotic Asteroid Prospector Marc M. Cohen1 Marc M. Cohen Architect P.C. – Astrotecture™, Palo Alto, CA, USA 94306-3864 Warren W. James2 V Infinity Research LLC. – Altadena, CA, USA Kris Zacny,3 Philip Chu, Jack Craft Honeybee Robotics Spacecraft Mechanisms Corporation – Pasadena, CA, USA This paper presents the results from the nine-month, Phase 1 investigation for the Robotic Asteroid Prospector (RAP). This project investigated several aspects of developing an asteroid mining mission. It conceived a Space Infrastructure Framework that would create a demand for in space-produced resources. The resources identified as potentially feasible in the near-term were water and platinum group metals. The project’s mission design stages spacecraft from an Earth Moon Lagrange (EML) point and returns them to an EML. The spacecraft’s distinguishing design feature is its solar thermal propulsion system (STP) that provides two functions: propulsive thrust and process heat for mining and mineral processing. The preferred propellant is water since this would allow the spacecraft to refuel at an asteroid for its return voyage to Cis- Lunar space thus reducing the mass that must be launched from the EML point. The spacecraft will rendezvous with an asteroid at its pole, match rotation rate, and attach to begin mining operations. The team conducted an experiment in extracting and distilling water from frozen regolith simulant. Nomenclature C-Type = Carbonaceous Asteroid EML = Earth-Moon Lagrange Point ESL = Earth-Sun Lagrange Point IPV = Interplanetary Vehicle M-Type = Metallic Asteroid NEA = Near Earth Asteroid NEO = Near Earth Object PGM = Platinum Group Metal STP = Solar Thermal Propulsion S-Type = Stony Asteroid I. -
The Lunar Orbital Prospector
THE LUNAR ORBITAL PROSPECTOR FrankJ. Redd, James N. Cantrell, and Greg McCurdy N 9 _ " 174 6 Center for Space Engineering Utah State University Logan UT 84322 The establishment of lunar bases will not end the need for remote sensing of the lunar surface by orbiting ldatforms. Human and robotic surface exploration u_ necessarily be limited to some proximate distance from the _ base..Near real-time, higlvresolulior_ global characterization of the lunar surface by orOiting sensing systems will continue to be essential to the understaru_'ng of the Moon's geophysical structure and the location of exploitable minerals and deposits of raw materials. 7be Lunar OrM'tal Prospector (LOP) is an orbiting sensing platforra capable of supIxgt_ng a varleO_ of modular sensing packages. Serviced by a lunarbased shuttle, the LOP will permit the exchange of instrument packages to meet evolving mission needs. The ability to recover, modify, and rotate sensing pack, ages allows their reuse in varying combinations. Combining this _'OJ u_th robust orbit moa_'fication capabilities and near real-time telemetry links provides considerable system responsiveness. Maintenance and mo_'fication of the LOP orbit are accomplished through use of an onboard propuL_n system that burns lunar-supplied oxygen and aluminum. The relatively low performance of such a system is more than comlxomated for by the elimination of the need for Earth-supplied prolx, liants. The LOP concept envisions a continuous expansion of capability through the incorporation of new instrument technologies and the addition of ptatforms. INTRODUCTION surface (Hood et aL, 1985). A long-term remote-sensing mission, in conjunction with a manned lunar base, can expand the LGO's Human and robotic exploration of the Moon during the last geophysical and geochemical database and serve as the "eyes and two decades has greatly increased our knowledge of the Moon's ears" of the manned base by searching for hmar transient events geophysical and geochemical nature. -
The Scientific Legacy of Apollo
The Scientific Legacy of Apollo Ian A. Crawford, Department of Earth and Planetary Sciences, Birkbeck College, University of London ([email protected]). Article published in the December 2012 issue of the Royal Astronomical Society’s journal Astronomy and Geophysics (Vol. 53, pp. 6.24-6.28). Abstract On the 40th anniversary of the last human expedition to the Moon, I review the scientific legacy of the Apollo programme and argue that science would benefit from a human return to the Moon. Introduction This December marks 40 years since the last human beings to set foot on the Moon, Gene Cernan and Harrison “Jack” Schmitt of Apollo 17, left the lunar surface and returned safely to Earth. This anniversary alone would have justified a retrospective look at the legacy of the Apollo project, but it has been given additional poignancy by the death earlier this year of Neil Armstrong, the first man to set foot on the lunar surface with Apollo 11 in July 1969. The history of the Apollo project, and its geopolitical motivation within the context of the Cold War, is of course well documented (e.g. Chaiken 1994; Burrows 1998; Orloff and Harland 2006) and need not be repeated here. However, although the scientific legacy of Apollo has also been well-documented (e.g. Heiken et al. 1991; Wilhelms 1993; Beattie 2001), and is generally well-known within the lunar science community, I have found that it is still underappreciated by many astronomers, and even some planetary scientists who are not directly involved in lunar studies. -
Development of the Moon Michael B
TABLE OF CONTENTS 1 Introduction............................................................................................................................. 2 2 Why Go to the Moon? Exploration Rationales and Motivations............................................ 3 2.1 Expansion of humans into space..................................................................................... 3 2.2 The Search for Energy Alternatives................................................................................ 6 2.2.1 Solar Power Satellites ............................................................................................. 6 2.2.2 Lunar Power System............................................................................................... 8 2.2.3 3He......................................................................................................................... 10 2.3 The industrialization of space ....................................................................................... 12 2.4 Exploration and development of the Solar System....................................................... 13 2.5 The Moon as a planetary science laboratory................................................................. 15 2.6 Astronomical observatories on the Moon..................................................................... 17 2.7 Maintenance of human health on long-duration missions ............................................ 20 3 Transportation by rocket in the Earth-Moon system ........................................................... -
Case Study: Lunar Mobility • Overview of Past Lunar Rover Missions • Design Review of NASA Robotic Prospector (RP) Rover for Lunar Exploration
Case Study: Lunar Mobility • Overview of past lunar rover missions • Design review of NASA Robotic Prospector (RP) rover for lunar exploration © 2020 David L. Akin - All rights reserved http://spacecraft.ssl.umd.edu U N I V E R S I T Y O F Slopes and Static Stability ENAE 788X - Planetary Surface Robotics MARYLAND 1 Lunar Motorcycle in KC-135 Testing U N I V E R S I T Y O F Slopes and Static Stability ENAE 788X - Planetary Surface Robotics MARYLAND 8 Lunar Motorcycle in Suspension Testing U N I V E R S I T Y O F Slopes and Static Stability ENAE 788X - Planetary Surface Robotics MARYLAND 9 National Aeronautics and Space Administration RP Rover Tiger Team Mission Overview The Lunar Resource Prospector (RP) rover was an earlier version of what became Volatiles Investigating Polar Exploration Rover (VIPER), which will be launched to the Moon in 2023. The technical details are not necessarily representative of the final VIPER design. Level-1 Mission Requirements 1.1 RP SHALL LAND AT A LUNAR POLAR REGION TO ENABLE PROSPECTING FOR VOLATILES • Full Success Criteria: Land at a polar location that maximizes the combined potential for obtaining a high volatile (hydrogen) concentration signature and mission duration within traverse capabilities • Minimum Success Criteria: Land at a polar location that maximizes the potential for obtaining a high volatile (hydrogen) concentration signature 1.2 RP SHALL BE CAPABLE OF OBTAINING KNOWLEDGE ABOUT THE LUNAR SURFACE AND SUBSURFACE VOLATILES AND MATERIALS • Full Success Criteria: Take both sub-surface measurements -
Application of CFS to a Lunar Rover: Resource Prospector (RP)
https://ntrs.nasa.gov/search.jsp?R=20180000800 2019-08-30T13:42:14+00:00Z National Aeronautics and Space Administration Application of CFS to a Lunar Rover: Resource Prospector (RP) Howard Cannon RP Rover Software Lead NASA-Ames Research Center FSW Workshop 2017 2017-12-07 The Hunt for Lunar Volatiles Clementine (1994): Curious bi-static radar LCROSS/LRO (2009): findings at the poles... Yes! Water-ice. How is it Water-ice? distributed? Lunar Prospector (1998): RP (2022): Shadowed craters contain Prospect for water-ice elevated Hydrogen levels… on human scales and Water-ice? demo ISRU processing 11/12/2015 Information contained in this presentation is not subject to Export Controls (ITAR/EAR) 2 Resource Prospector • Mission to Lunar Pole to search for and characterize the water ice – What form (eg. Snow or Ice lens?) – How much water is there? – How deep is it? • Lunar Rover with: – Prospecting instruments to search for ice deposits – Drill to extract samples from the subsurface – Oven to bake the samples and scientific instruments to study its contents • Developed and demonstrated a first prototype in 2015 • Currently scheduled to launch in 2022 11/12/2015 Information contained in this presentation is not subject to Export Controls (ITAR/EAR) 3 RP Storyboard 11/12/2015 Information contained in this presentation is not subject to Export Controls (ITAR/EAR) 4 RP15 Distributed Operations Test testing 2015-08-21 NASA-ARC Mission Control room driving RP15 rover RP15 rover @ NASA-JSC Rock Yard NIRVSS Payload Operations NASA-KSC Payload Control -
Physics of Solar Wind and Terrestrial Magnetospheric Plasma Interactions with the Moon
Physics of Solar Wind and Terrestrial Magnetospheric Plasma Interactions With the Moon R.P. Lin Physics Dept & Space Sciences Laboratory University of California, Berkeley with help from J. Halekas, M. Oieroset, & M. Fillingim Plasma Interaction with the Moon and Dust Plasma Physics of the Distant Magnetotail Plasma Interaction with Mini-Magnetospheres The Lunar Environment Dipolar E-Fields? Extreme Surface Charging Surface potentials of up to several kV (negative) found: • In the terrestrial plasmasheet, where 4 KeV Beam we encounter high plasma temperature. • During Solar Energetic Particle events Frequency of Extreme Charging Events During the Entire Lunar Prospector Mission • Green in color bar indicates magnetospheric tail passages, red indicates major SEP events The Earth’s magnetic shield DuringBefore reconnectionreconnection Dungey, Philos. Mag. 55, (1953) Wind observed 10 hours of reconnection flows at lunar distance (XGSE=-60 RE) lobe NP plasma Wind alternately inside plasma sheet sheet and lobe High speed reconnection flows always TP observed when the spacecraft was in the plasma sheet → 10 hours of continuous reconnection VX High speed Reconnection flows Bx Bz B (GSM) (Oieroset et al., 2000) By Wind satellite observations in distant magnetotail, 60RE • Measurements within the ion diffusion region reveal: Strong anisotropy in fe. Log(f) M. Øieroset et al. Nature 412, (2001) M. Øieroset et al. PRL 89, (2002) A trapped electron in the magnetotail mv 2 m(v2 - v 2 ) The magnetic moment: µ = ! = || 2B 2B Drift kinetic modeling of Wind data • Applying f(x0,v0) = f∞(|v1|) to an X-line geometry consistent with the Wind measurements • A potential,Φ∞ needed for trapping at low energies • Ion outflow: 400 km/s, consistent with acceleration in Φ ∞ ~ -300V Φ∞ Theory Wind Φ∞~ -800V Φ∞~ -1150V J. -
The Ladee Mission: the Next Step After the Discovery of Water on the Moon
41st Lunar and Planetary Science Conference (2010) 2459.pdf THE LADEE MISSION: THE NEXT STEP AFTER THE DISCOVERY OF WATER ON THE MOON. G. T. Delory1,2, R. C. Elphic1, A. Colaprete1, P. Mahaffy3, and M. Horanyi4 1NASA Ames Research Center, Moffett Field, CA 94035-1000, 2Space Sciences Laboratory, University of California, Berkeley CA 94720 gde- [email protected].) 3NASA Goddard Space Flight Center, Greenbelt, MD, 20771 4Laboratory for Atmospheric and Space Physics, University of Colorado, Boulder, CO 80309. Introduction: The recent discovery of significant amounts of water on the lunar surface and within a permanently shadowed region of the southern lunar pole has re-ignited the debate regarding the sources and dynamics of lunar volatiles. Whether lunar volatile deposits are primordial and static over periods as long as several Ga or are engaged in active processes in- volving present-day source and loss mechanisms re- mains a key question. The answer to this question bears directly on what volatile stratigraphy can reveal regarding the evolution of the Moon and the condi- tions in the early solar system. Volatiles may be found in the tenuous lunar atmosphere, a surface boundary exosphere whose composition and variability may Fig. 1: Volatile cycling on the Moon (From [1]) provide direct insight into their transport and evolu- trapping processes. While LCROSS represents a single tion. The Lunar Atmosphere and Dust Environment point measurement, the presence of at least 100 kg of Explorer (LADEE), a small, low-cost lunar orbiter water in a ~20m diameter region within Cabeus, to- currently planned for a launch in 2012, carries an in- gether with the hydrogen measurements from LP, ar- strument payload specifically designed to study the gue strongly that there are likely significant volatile lunar exosphere, and is thus an important and timely deposits within PSRs. -
A Reanalysis of Apollo 15 and 17 Surface and Subsurface Temperature Series
Lunar and Planetary Science XXXVII (2006) 1682.pdf 1 A REANALYSIS OF APOLLO 15 AND 17 SURFACE AND SUBSURFACE TEMPERATURE SERIES. M. A. Wieczorek and S. Huang2, 1Institut de Physique du Globe de Paris, France ([email protected]), 2University of Michigan ([email protected]). Introduction: Geophysical packages were The goal of this project is twofold. First, a deployed on the lunar surface as part of the Apollo reanalysis of the Apollo Heat Flow Experiment data program that continuously transmitted data to the using improved modeling techniques will offer a Earth until 1978. The Apollo Lunar Surface more precise estimate of the heat flow in the Experiment Package (ALSEP) at the Apollo 15 and Procellarum KREEP Terrane and Feldspathic 17 sites contained a heat flow experiment that both Highlands Terrane. Such measurements will help monitored surface and subsurface temperatures and constraint the total abundance of heat-producing conducted thermal conductivity measurements. elements in the crust at these two sites, and will be Analyses of these data placed constraints on the heat crucial for understanding the asymmetric thermal flow of the Moon and the near-surface thermal evolution of the Moon (the magmatic activity of the conductivity profile [1, 2]. Moon is largely confined to the Procellarum KREEP One important result obtained from these analyses Terrane). Secondly, as a byproduct of analyzing the is that the heat flow at the Apollo 15 site is surface temperatures, we will attempt to constrain apparently significantly greater than at the Apollo 17 variations in the Sun’s total irradiance. Satellite site [1] (21 vs.