Nuclear Thermal Propulsion
Total Page:16
File Type:pdf, Size:1020Kb
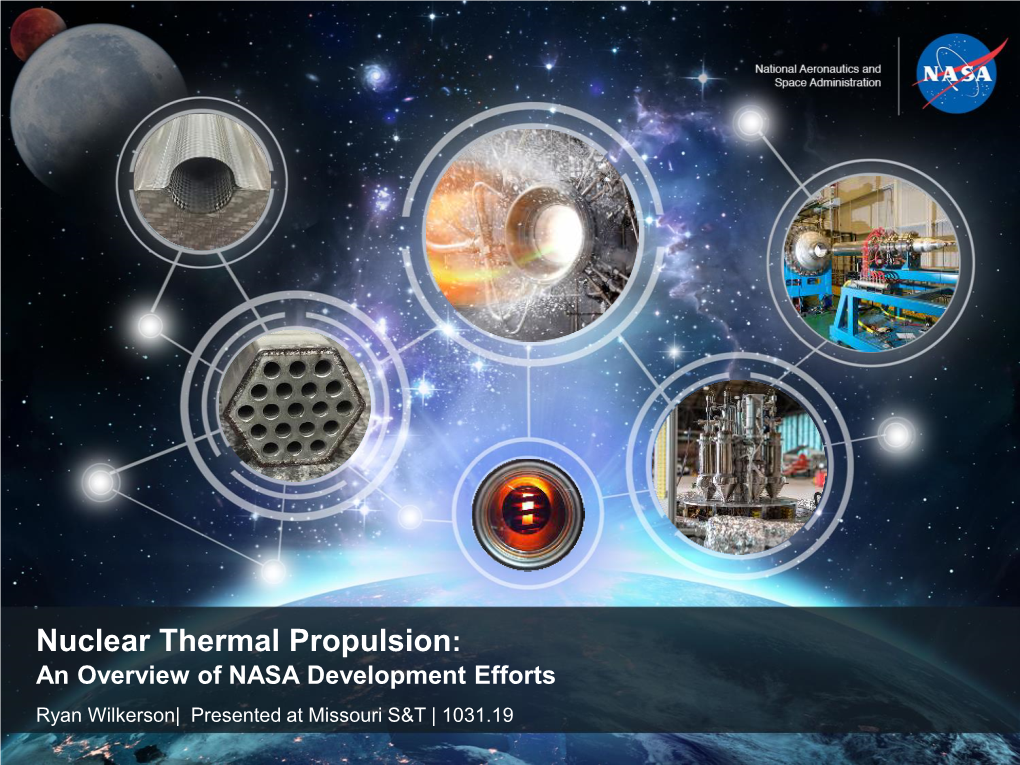
Load more
Recommended publications
-
Back to the the Future? 07> Probing the Kuiper Belt
SpaceFlight A British Interplanetary Society publication Volume 62 No.7 July 2020 £5.25 SPACE PLANES: back to the the future? 07> Probing the Kuiper Belt 634089 The man behind the ISS 770038 Remembering Dr Fred Singer 9 CONTENTS Features 16 Multiple stations pledge We look at a critical assessment of the way science is conducted at the International Space Station and finds it wanting. 18 The man behind the ISS 16 The Editor reflects on the life of recently Letter from the Editor deceased Jim Beggs, the NASA Administrator for whom the building of the ISS was his We are particularly pleased this supreme achievement. month to have two features which cover the spectrum of 22 Why don’t we just wing it? astronautical activities. Nick Spall Nick Spall FBIS examines the balance between gives us his critical assessment of winged lifting vehicles and semi-ballistic both winged and blunt-body re-entry vehicles for human space capsules, arguing that the former have been flight and Alan Stern reports on his grossly overlooked. research at the very edge of the 26 Parallels with Apollo 18 connected solar system – the Kuiper Belt. David Baker looks beyond the initial return to the We think of the internet and Moon by astronauts and examines the plan for a how it helps us communicate and sustained presence on the lunar surface. stay in touch, especially in these times of difficulty. But the fact that 28 Probing further in the Kuiper Belt in less than a lifetime we have Alan Stern provides another update on the gone from a tiny bleeping ball in pioneering work of New Horizons. -
Aerospace Engine Data
AEROSPACE ENGINE DATA Data for some concrete aerospace engines and their craft ................................................................................. 1 Data on rocket-engine types and comparison with large turbofans ................................................................... 1 Data on some large airliner engines ................................................................................................................... 2 Data on other aircraft engines and manufacturers .......................................................................................... 3 In this Appendix common to Aircraft propulsion and Space propulsion, data for thrust, weight, and specific fuel consumption, are presented for some different types of engines (Table 1), with some values of specific impulse and exit speed (Table 2), a plot of Mach number and specific impulse characteristic of different engine types (Fig. 1), and detailed characteristics of some modern turbofan engines, used in large airplanes (Table 3). DATA FOR SOME CONCRETE AEROSPACE ENGINES AND THEIR CRAFT Table 1. Thrust to weight ratio (F/W), for engines and their crafts, at take-off*, specific fuel consumption (TSFC), and initial and final mass of craft (intermediate values appear in [kN] when forces, and in tonnes [t] when masses). Engine Engine TSFC Whole craft Whole craft Whole craft mass, type thrust/weight (g/s)/kN type thrust/weight mini/mfin Trent 900 350/63=5.5 15.5 A380 4×350/5600=0.25 560/330=1.8 cruise 90/63=1.4 cruise 4×90/5000=0.1 CFM56-5A 110/23=4.8 16 -
Development of Turbopump for LE-9 Engine
Development of Turbopump for LE-9 Engine MIZUNO Tsutomu : P. E. Jp, Manager, Research & Engineering Development, Aero Engine, Space & Defense Business Area OGUCHI Hideo : Manager, Space Development Department, Aero Engine, Space & Defense Business Area NIIYAMA Kazuki : Ph. D., Manager, Space Development Department, Aero Engine, Space & Defense Business Area SHIMIYA Noriyuki : Space Development Department, Aero Engine, Space & Defense Business Area LE-9 is a new cryogenic booster engine with high performance, high reliability, and low cost, which is designed for H3 Rocket. It will be the first booster engine in the world with an expander bleed cycle. In the designing process, the performance requirements of the turbopump and other components can be concurrently evaluated by the mathematical model of the total engine system including evaluation with the simulated performance characteristic model of turbopump. This paper reports the design requirements of the LE-9 turbopump and their latest development status. Liquid oxygen 1. Introduction turbopump Liquid hydrogen The H3 rocket, intended to reduce cost and improve turbopump reliability with respect to the H-II A/B rockets currently in operation, is under development toward the launch of the first H3 test rocket in FY 2020. In rocket development, engine is an important factor determining reliability, cost, and performance, and as a new engine for the H3 rocket first stage, an LE-9 engine(1) is under development. A rocket engine uses a turbopump to raise the pressure of low-pressure propellant supplied from a tank, injects the pressurized propellant through an injector into a combustion chamber to combust it under high-temperature and high- pressure conditions. -
6. Chemical-Nuclear Propulsion MAE 342 2016
2/12/20 Chemical/Nuclear Propulsion Space System Design, MAE 342, Princeton University Robert Stengel • Thermal rockets • Performance parameters • Propellants and propellant storage Copyright 2016 by Robert Stengel. All rights reserved. For educational use only. http://www.princeton.edu/~stengel/MAE342.html 1 1 Chemical (Thermal) Rockets • Liquid/Gas Propellant –Monopropellant • Cold gas • Catalytic decomposition –Bipropellant • Separate oxidizer and fuel • Hypergolic (spontaneous) • Solid Propellant ignition –Mixed oxidizer and fuel • External ignition –External ignition • Storage –Burn to completion – Ambient temperature and pressure • Hybrid Propellant – Cryogenic –Liquid oxidizer, solid fuel – Pressurized tank –Throttlable –Throttlable –Start/stop cycling –Start/stop cycling 2 2 1 2/12/20 Cold Gas Thruster (used with inert gas) Moog Divert/Attitude Thruster and Valve 3 3 Monopropellant Hydrazine Thruster Aerojet Rocketdyne • Catalytic decomposition produces thrust • Reliable • Low performance • Toxic 4 4 2 2/12/20 Bi-Propellant Rocket Motor Thrust / Motor Weight ~ 70:1 5 5 Hypergolic, Storable Liquid- Propellant Thruster Titan 2 • Spontaneous combustion • Reliable • Corrosive, toxic 6 6 3 2/12/20 Pressure-Fed and Turbopump Engine Cycles Pressure-Fed Gas-Generator Rocket Rocket Cycle Cycle, with Nozzle Cooling 7 7 Staged Combustion Engine Cycles Staged Combustion Full-Flow Staged Rocket Cycle Combustion Rocket Cycle 8 8 4 2/12/20 German V-2 Rocket Motor, Fuel Injectors, and Turbopump 9 9 Combustion Chamber Injectors 10 10 5 2/12/20 -
Combustion Tap-Off Cycle
College of Engineering Honors Program 12-10-2016 Combustion Tap-Off Cycle Nicole Shriver Embry-Riddle Aeronautical University, [email protected] Follow this and additional works at: https://commons.erau.edu/pr-honors-coe Part of the Aeronautical Vehicles Commons, Other Aerospace Engineering Commons, Propulsion and Power Commons, and the Space Vehicles Commons Scholarly Commons Citation Shriver, N. (2016). Combustion Tap-Off Cycle. , (). Retrieved from https://commons.erau.edu/pr-honors- coe/6 This Article is brought to you for free and open access by the Honors Program at Scholarly Commons. It has been accepted for inclusion in College of Engineering by an authorized administrator of Scholarly Commons. For more information, please contact [email protected]. Honors Directed Study: Combustion Tap-Off Cycle Date of Submission: December 10, 2016 by Nicole Shriver [email protected] Submitted to Dr. Michael Fabian Department of Aerospace Engineering College of Engineering In Partial Fulfillment Of the Requirements Of Honors Directed Study Fall 2016 1 1.0 INTRODUCTION The combustion tap-off cycle is also known as the “topping cycle” or “chamber bleed cycle.” It is an open liquid bipropellant cycle, usually of liquid hydrogen and liquid oxygen, that combines the fuel and oxidizer in the main combustion chamber. Gases from the edges of the combustion chamber are used to power the engine’s turbine and are expelled as exhaust. Figure 1.1 below shows a picture representation of the cycle. Figure 1.1: Combustion Tap-Off Cycle The combustion tap-off cycle is rather unconventional for rocket engines as it has only been put into practice with two engines. -
Materials for Liquid Propulsion Systems
https://ntrs.nasa.gov/search.jsp?R=20160008869 2019-08-29T17:47:59+00:00Z CHAPTER 12 Materials for Liquid Propulsion Systems John A. Halchak Consultant, Los Angeles, California James L. Cannon NASA Marshall Space Flight Center, Huntsville, Alabama Corey Brown Aerojet-Rocketdyne, West Palm Beach, Florida 12.1 Introduction Earth to orbit launch vehicles are propelled by rocket engines and motors, both liquid and solid. This chapter will discuss liquid engines. The heart of a launch vehicle is its engine. The remainder of the vehicle (with the notable exceptions of the payload and guidance system) is an aero structure to support the propellant tanks which provide the fuel and oxidizer to feed the engine or engines. The basic principle behind a rocket engine is straightforward. The engine is a means to convert potential thermochemical energy of one or more propellants into exhaust jet kinetic energy. Fuel and oxidizer are burned in a combustion chamber where they create hot gases under high pressure. These hot gases are allowed to expand through a nozzle. The molecules of hot gas are first constricted by the throat of the nozzle (de-Laval nozzle) which forces them to accelerate; then as the nozzle flares outwards, they expand and further accelerate. It is the mass of the combustion gases times their velocity, reacting against the walls of the combustion chamber and nozzle, which produce thrust according to Newton’s third law: for every action there is an equal and opposite reaction. [1] Solid rocket motors are cheaper to manufacture and offer good values for their cost. -
Enhancement of Volumetric Specific Impulse in HTPB/Ammonium Nitrate Mixed
Utah State University DigitalCommons@USU All Graduate Plan B and other Reports Graduate Studies 12-2016 Enhancement of Volumetric Specific Impulse in TPB/H Ammonium Nitrate Mixed Hybrid Rocket Systems Jacob Ward Forsyth Utah State University Follow this and additional works at: https://digitalcommons.usu.edu/gradreports Part of the Propulsion and Power Commons Recommended Citation Forsyth, Jacob Ward, "Enhancement of Volumetric Specific Impulse in TPB/AmmoniumH Nitrate Mixed Hybrid Rocket Systems" (2016). All Graduate Plan B and other Reports. 876. https://digitalcommons.usu.edu/gradreports/876 This Report is brought to you for free and open access by the Graduate Studies at DigitalCommons@USU. It has been accepted for inclusion in All Graduate Plan B and other Reports by an authorized administrator of DigitalCommons@USU. For more information, please contact [email protected]. ENHANCEMENT OF VOLUMETRIC SPECIFIC IMPULSE IN HTPB/AMMONIUM NITRATE MIXED HYBRID ROCKET SYSTEMS by Jacob W. Forsyth A report submitted in partial fulfillment of the requirements for the degree of MASTER OF SCIENCE in Aerospace Engineering Approved: ______________________ ____________________ Stephen A. Whitmore Ph.D. David Geller Ph.D. Major Professor Committee Member ______________________ Rees Fullmer Ph.D. Committee Member UTAH STATE UNIVERSITY Logan, Utah 2016 ii Copyright © Jacob W. Forsyth 2016 All Rights Reserved iii ABSTRACT Enhancement of Volumetric Specific Impulse in HTPB/Ammonium Nitrate Mixed Hybrid Rocket Systems by Jacob W. Forsyth, Master of Science Utah State University, 2016 Major Professor: Dr. Stephen A. Whitmore Department: Mechanical and Aerospace Engineering Hybrid rocket systems are safer and have higher specific impulse than solid rockets. However, due to large oxidizer tanks and low regression rates, hybrid rockets have low volumetric efficiency and very long longitudinal profiles, which limit many of the applications for which hybrids can be used. -
Validation of a Simplified Model for Liquid Propellant Rocket Engine Combustion Chamber Design
IOP Conference Series: Materials Science and Engineering PAPER • OPEN ACCESS Validation of a simplified model for liquid propellant rocket engine combustion chamber design To cite this article: M Hegazy et al 2020 IOP Conf. Ser.: Mater. Sci. Eng. 973 012003 View the article online for updates and enhancements. This content was downloaded from IP address 170.106.33.14 on 25/09/2021 at 23:25 AMME-19 IOP Publishing IOP Conf. Series: Materials Science and Engineering 973 (2020) 012003 doi:10.1088/1757-899X/973/1/012003 Validation of a simplified model for liquid propellant rocket engine combustion chamber design M Hegazy1, H Belal2, A Makled3 and M A Al-Sanabawy4 1 M.Sc. Student, Rocket Department, Military Technical College, Egypt 2 Assistant Professor, Rocket Department, Military Technical College, Egypt 3 Associate Professor. Zagazig University, Egypt 4 Associate Professor. Rocket Department, Military Technical College, Egypt [email protected] Abstract. The combustion phenomena inside the thrust chamber of the liquid propellant rocket engine are very complicated because of different paths for elementary processes. In this paper, the characteristic length (L*) approach for the combustion chamber design will be discussed compared to the effective length (Leff) approach. First, both methods are introduced then applied for real LPRE. The effective length methodology is introduced starting from the basic model until developing the empirical equations that may be used in the design process. The classical procedure of L* was found to over-estimate the required cylindrical length in addition to the inherent shortcoming of not giving insight where to move to enhance the design. -
Cryogenic Technology & Rocket Engines
ISSN (O): 2393-8609 International Journal of Aerospace and Mechanical Engineering Volume 2 – No.5, August 2015 Cryogenic Technology & Rocket Engines AKHIL GARG KARTIK JAKHU KISHAN SINGH ABHINAV B.Tech – Aerospace B.Tech – Aerospace B.Tech – Aerospace MAURYA Engg. Engg. Engg. B.Tech – Aerospace PUNJAB PUNJAB PUNJAB Engg. TECHNICAL TECHNICAL TECHNICAL PUNJAB UNIVERSITY, UNIVERSITY, UNIVERSITY, TECHNICAL JALANDHAR JALANDHAR JALANDHAR UNIVERSITY, akhilgarg.313@g kartik.lphawk@g kishansngh1996 JALANDHAR mail.com mail.com @gmail.com abhinavguru123 @gmail.com ABSTRACT 3.2 What is Cryogenic Rocket Engine? This paper is all about the rocket engine involving the use of A cryogenic rocket engine is a rocket engine that cryogenic technology at a cryogenic temperature (123K). This uses a cryogenic fuel or oxidizer, that is, its fuel or basically uses the liquid oxygen and liquid hydrogen as an oxidizer (or both) is gases liquefied and stored at oxidizer and fuel, which are very clean and non-pollutant very low temperatures. Notably, these engines were fuels compared to other hydrocarbon fuels like petrol, diesel, one of the main factors of the ultimate success in gasoline, LPG, CNG, etc., sometimes, liquid nitrogen is also reaching the Moon by the Saturn V rocket. used as an fuel. During World War II, when powerful rocket engines were first considered by the German, American and Keywords Soviet engineers independently, all discovered that Rocket engine, Cryogenic technology, Cryogenic temperature, rocket engines need high mass flow rate of both Liquid hydrogen and Oxygen. oxidizer and fuel to generate a sufficient thrust. At that time oxygen and low molecular weight 1. -
Sidney Allan Ceng, Fraes 1909-1973
frustration caused him to tend to withdraw somewhat broader front. This made him very vulnerable and it was from the company of others and thus give an appearance in this respect that his wife (Tommy) was such a tower of of aloofness. Those of us who were privileged to know strength to him throughout their long married life. Her him better recognised this as mere illusion for he could be death just over three years ago was a great blow to him. the most warm and charming of companions. His very Though now gone he will live on for as long as people keen sense of humour could always be relied upon to en are concerned with the problems of flight in a way that is liven any conversation and often even shone through much aptly described by words that Barry himself used of of his technical writing, whilst in the right circumstance he another, could use a caustic wit with quite devastating effect Above all he loved the simple things of life—the beauty of nature "He is not dead. Still on my mortal breath and the countryside. Walking was a favourite pastime of Swells a low music from his heart's desire. his as was also working in his garden and it is not un I am most proud, and you most cheated, Death, natural that this part of him is reflected so well in a num Knowing in bis closed book this deathless fire". ber of his poems. A man of great sensitivity he always Poems, 1925 reacted vigorously to any suggestion of man's inhumanity to man whether on a person to person level or on a H. -
Solid Propellant Rocket Engines - V.M
THERMAL TO MECHANICAL ENERGY CONVERSION: ENGINES AND REQUIREMENTS – Vol. II - Solid Propellant Rocket Engines - V.M. Polyaev and V.A. Burkaltsev SOLID PROPELLANT ROCKET ENGINES V.M. Polyaev and V.A. Burkaltsev Department of Rocket engines, Bauman Moscow State Technical University, Russia. Keywords: Combustion chamber, solid propellant load, pressure, temperature, nozzle, thrust, control, ignition, cartridge, aspect ratio, regime. Contents 1. Introduction 2. Historical information 3. SPRE scheme and main units 4. SPRE operation 5. Parameter optimization, the approach and results 6. Transient regime 7. Service 8. Development prospects 9. Conclusions Acknowledgments Glossary Bibliography Biographical Sketches 1. Introduction Solid propellant rocket engines (SPRE) are called the direct reaction engines, in which chemical energy of the solid propellant being placed in the combustion chamber is transformed at first to thermal energy, and then to kinetic energy of the combustion products thrown away with high velocity in the environment. The momentum of combustion products discharging through the nozzle is equal to the impulse of reactive force being created by the engine. 2. Historical information First of rocketsUNESCO known to us were rockets – with EOLSS primitive powder rocket engines used in China near 5000 years ago for pleasure and military aims (so-called "fiery arrows", Figure 1). SAMPLE CHAPTERS The first rocket propellant was black smoky powder (potassium saltpetre with charcoal mixture). In Russia, powder rockets appeared in the beginning of XVII century. In 1680, Tsar Peter I founded "rocket institution" in Moscow for firework rockets making. In 1717 lighting signal rockets existed for 200 years without changes. In the beginning of XIX century, Englishman Kongrev improved the "fiery arrows" having been borrowed from Hindus. -
An Investigation of the Performance Potential of A
AN INVESTIGATION OF THE PERFORMANCE POTENTIAL OF A LIQUID OXYGEN EXPANDER CYCLE ROCKET ENGINE by DYLAN THOMAS STAPP RICHARD D. BRANAM, COMMITTEE CHAIR SEMIH M. OLCMEN AJAY K. AGRAWAL A THESIS Submitted in partial fulfillment of the requirements for the degree of Master of Science in the Department of Aerospace Engineering and Mechanics in the Graduate School of The University of Alabama TUSCALOOSA, ALABAMA 2016 Copyright Dylan Thomas Stapp 2016 ALL RIGHTS RESERVED ABSTRACT This research effort sought to examine the performance potential of a dual-expander cycle liquid oxygen-hydrogen engine with a conventional bell nozzle geometry. The analysis was performed using the NASA Numerical Propulsion System Simulation (NPSS) software to develop a full steady-state model of the engine concept. Validation for the theoretical engine model was completed using the same methodology to build a steady-state model of an RL10A-3- 3A single expander cycle rocket engine with corroborating data from a similar modeling project performed at the NASA Glenn Research Center. Previous research performed at NASA and the Air Force Institute of Technology (AFIT) has identified the potential of dual-expander cycle technology to specifically improve the efficiency and capability of upper-stage liquid rocket engines. Dual-expander cycles also eliminate critical failure modes and design limitations present for single-expander cycle engines. This research seeks to identify potential LOX Expander Cycle (LEC) engine designs that exceed the performance of the current state of the art RL10B-2 engine flown on Centaur upper-stages. Results of this research found that the LEC engine concept achieved a 21.2% increase in engine thrust with a decrease in engine length and diameter of 52.0% and 15.8% respectively compared to the RL10B-2 engine.