A Study of the Shift in the Temperature of Maximum Density of Water And
Total Page:16
File Type:pdf, Size:1020Kb
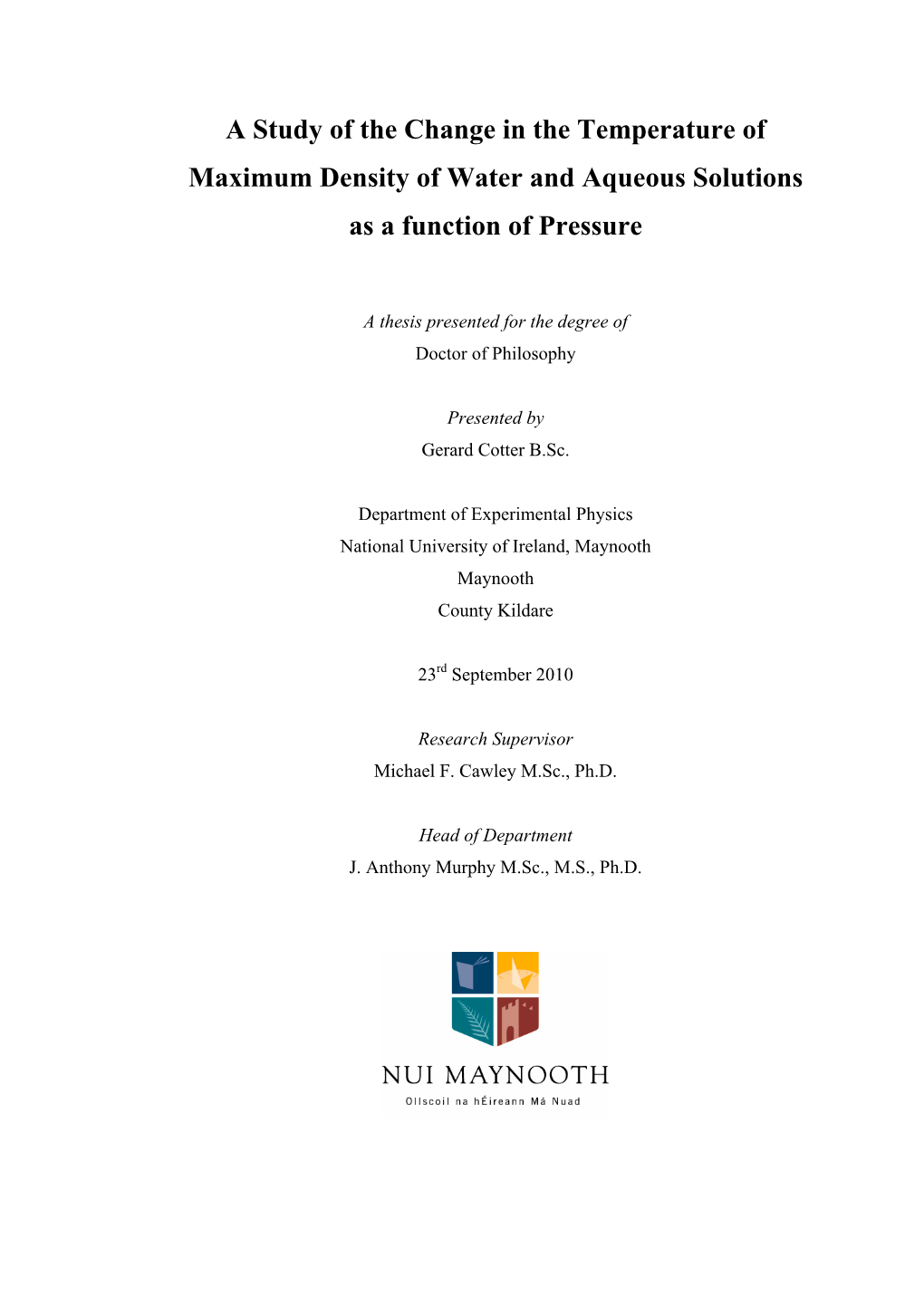
Load more
Recommended publications
-
Pr Rediction N of Rel Refere M Ative De Ence to C Master O Civil E Ensity Of
View metadata, citation and similar papers at core.ac.uk brought to you by CORE provided by ethesis@nitr Prediction of Relative Density of Sand with Particular Reference to Compaction Energy A Thesis Submitted in Partial Fulfillment of the Requirements for the Degree of Master of Technology in Civil Engineering Shuvranshu Kumar Rout DEPARTMENT OF CIVIL ENGINEERING NATIONAL INSTITUTE OF TECHNOLOGY ROURKELA August, 2009 Prediction of Relative Density of Sand with Particular Reference to Compaction Energy A Thesis Submitted in Partial Fulfillment of the Requirements for the Degree of Master of Technology in Civil Engineering By Shuvranshu Kumar Rout Under the Guidance of Prof. C. R. Patra Department of Civil Engineering National Institute of Technology Rourkela August 2009 National Institute of Technology Rourkela CERTIFICATE This is to certify that the thesis entitled, “Prediction of relative density of sand with particular reference to compaction energgy” submitted by Mr Shuvranshu Kumar Rout in partial fulfillment of the requirements for the award of Master of Technology in Civil Engineering at National Institute of Technology, Rourkela is an authentic work carried out by him under my supervision and guidance. To the best of my knowledge, the matter embodied in the thesis has not been submitted to any other University / Institute for the award of any Degree or Diploma. Date: Dr. C. R Patra Professor Dept. of Civil Engg. National Institute of Technologgy Rourkela – 769008 ACKNOWLEDGEMENT I sincerely express my deep sense of gratitude to my thesis supervisor, Prof. Chittaranjan Patra for his expert guidance, continuous encouragement and inspiration throughout the course of thesis work. -
Relation Between the Melting Temperature and the Temperature of Maximum Density for the Most Common Models of Water ͒ C
THE JOURNAL OF CHEMICAL PHYSICS 123, 144504 ͑2005͒ Relation between the melting temperature and the temperature of maximum density for the most common models of water ͒ C. Vegaa and J. L. F. Abascal Departamento de Química Física, Facultad de Ciencias Químicas, Universidad Complutense, 28040 Madrid, Spain ͑Received 22 June 2005; accepted 16 August 2005; published online 11 October 2005͒ Water exhibits a maximum in density at normal pressure at 4° above its melting point. The reproduction of this maximum is a stringent test for potential models used commonly in simulations of water. The relation between the melting temperature and the temperature of maximum density for these potential models is unknown mainly due to our ignorance about the melting temperature of these models. Recently we have determined the melting temperature of ice Ih for several commonly used models of water ͑SPC, SPC/E, TIP3P, TIP4P, TIP4P/Ew, and TIP5P͒. In this work we locate the temperature of maximum density for these models. In this way the relative location of the temperature of maximum density with respect to the melting temperature is established. For SPC, SPC/E, TIP3P, TIP4P, and TIP4P/Ew the maximum in density occurs at about 21–37 K above the melting temperature. In all these models the negative charge is located either on the oxygen itself or on a point along the H–O–H bisector. For the TIP5P and TIP5P-E models the maximum in density occurs at about 11 K above the melting temperature. The location of the negative charge appears as a geometrical crucial factor to the relative position of the temperature of maximum density with respect to the melting temperature. -
The Water Molecule
Seawater Chemistry: Key Ideas Water is a polar molecule with the remarkable ability to dissolve more substances than any other natural solvent. Salinity is the measure of dissolved inorganic solids in water. The most abundant ions dissolved in seawater are chloride, sodium, sulfate, and magnesium. The ocean is in steady state (approx. equilibrium). Water density is greatly affected by temperature and salinity Light and sound travel differently in water than they do in air. Oxygen and carbon dioxide are the most important dissolved gases. 1 The Water Molecule Water is a polar molecule with a positive and a negative side. 2 1 Water Molecule Asymmetry of a water molecule and distribution of electrons result in a dipole structure with the oxygen end of the molecule negatively charged and the hydrogen end of the molecule positively charged. 3 The Water Molecule Dipole structure of water molecule produces an electrostatic bond (hydrogen bond) between water molecules. Hydrogen bonds form when the positive end of one water molecule bonds to the negative end of another water molecule. 4 2 Figure 4.1 5 The Dissolving Power of Water As solid sodium chloride dissolves, the positive and negative ions are attracted to the positive and negative ends of the polar water molecules. 6 3 Formation of Hydrated Ions Water dissolves salts by surrounding the atoms in the salt crystal and neutralizing the ionic bond holding the atoms together. 7 Important Property of Water: Heat Capacity Amount of heat to raise T of 1 g by 1oC Water has high heat capacity - 1 calorie Rocks and minerals have low HC ~ 0.2 cal. -
Glossary of Hazardous Materials Terms
GLOSSARY OF CHEMICAL HAZARD TERMS ACGIH - The American Conference of Governmental Industrial Hygienists consists of occupational safety and health professionals who recommend occupational exposure limits for many substances. Action Level - An OSHA concentration calculated as an 8-your time-weighted average, which initiates certain required activities such as exposure monitoring and medical surveillance. Acute Health Effect - A severe effect which occurs rapidly after a brief intense exposure to a substance. ANSI - American National Standards Institute is a private group that develops consensus standards. Acute toxicity -Acutely toxic substances cause adverse effects by any of the following exposure methods: 1. Oral or dermal administration of a single dose of a substance. 2. Multiple oral or dermal doses within a 24-hour period 3. An inhalation exposure of 4 hours. Asphyxiant - A chemical (gas or vapor) that can cause death or unconsciousness by suffocation. Aspiration hazard - A liquid or solid chemical that causes severe acute effects if it infiltrates into the trachea and lower respiratory tract. Possible effects include chemical pneumonia, pulmonary injury, or death Autoignition Temperature - The lowest temperature at which a substance will burst into flames without a source of ignition like a spark or flame. The lower the ignition temperature, the more likely the substance is going to be a fire hazard. Boiling Point - The temperature of a liquid at which its vapor pressure is equal to the gas pressure over it. With added energy, all of the liquid could become vapor. Boiling occurs when the liquid's vapor pressure is just higher than the pressure over it. Carcinogen - A substance that causes cancer in humans or, because it has produced cancer in animals, is considered capable of causing cancer in humans. -
REFPROP Documentation Release 10.0
REFPROP Documentation Release 10.0 EWL, IHB, MH, MML May 21, 2018 CONTENTS 1 REFPROP Graphical User Interface3 1.1 General Information...........................................3 1.2 Menu Commands.............................................6 1.3 DLLs................................................... 26 2 REFPROP DLL documentation 27 2.1 High-Level API............................................. 27 2.2 Legacy API................................................ 55 i ii REFPROP Documentation, Release 10.0 REFPROP is an acronym for REFerence fluid PROPerties. This program, developed by the National Institute of Standards and Technology (NIST), calculates the thermodynamic and transport properties of industrially important fluids and their mixtures. These properties can be displayed in Tables and Plots through the graphical user interface; they are also accessible through spreadsheets or user-written applications accessing the REFPROP dll. REFPROP is based on the most accurate pure fluid and mixture models currently available. It implements three models for the thermodynamic properties of pure fluids: equations of state explicit in Helmholtz energy, the modified Benedict-Webb-Rubin equation of state, and an extended corresponding states (ECS) model. Mixture calculations employ a model that applies mixing rules to the Helmholtz energy of the mixture components; it uses a departure function to account for the departure from ideal mixing. Viscosity and thermal conductivity are modeled with either fluid-specific correlations, an ECS method, or in some cases the friction theory method. CONTENTS 1 REFPROP Documentation, Release 10.0 2 CONTENTS CHAPTER ONE REFPROP GRAPHICAL USER INTERFACE 1.1 General Information 1.1.1 About REFPROP REFPROP is an acronym for REFerence fluid PROPerties. This program, developed by the National Institute of Standards and Technology (NIST), calculates the thermodynamic and transport properties of industrially important fluids and their mixtures. -
DENSITY TESTING and INSPECTION MANUAL 2003 EDITION Revised December 2020
DENSITY TESTING AND INSPECTION MANUAL 2003 EDITION Revised December 2020 CONSTRUCTION FIELD SERVICES DIVISION FOREWORD This manual provides guidance to administrative, engineering, and technical staff. Engineering practice requires that professionals use a combination of technical skills and judgment in decision making. Engineering judgment is necessary to allow decisions to account for unique site-specific conditions and considerations to provide high quality products, within budget, and to protect the public health, safety, and welfare. This manual provides the general operational guidelines; however, it is understood that adaptation, adjustments, and deviations are sometimes necessary. Innovation is a key foundational element to advance the state of engineering practice and develop more effective and efficient engineering solutions and materials. As such, it is essential that our engineering manuals provide a vehicle to promote, pilot, or implement technologies or practices that provide efficiencies and quality products, while maintaining the safety, health, and welfare of the public. It is expected when making significant or impactful deviations from the technical information from these guidance materials, that reasonable consultations with experts, technical committees, and/or policy setting bodies occur prior to actions within the timeframes allowed. It is also expected that these consultations will eliminate any potential conflicts of interest, perceived or otherwise. MDOT Leadership is committed to a culture of innovation to optimize engineering solutions. The National Society of Professional Engineers Code of Ethics for Engineering is founded on six fundamental canons. Those canons are provided below. Engineers, in the fulfillment of their professional duties, shall: 1. Hold paramount the safety, health, and welfare of the public. -
Flow Visualization of Free Convection in a Vertical Cylinder of Water in the Vicinity of the Density Maximum M.F
CORE Metadata, citation and similar papers at core.ac.uk Provided by MURAL - Maynooth University Research Archive Library International Journal of Heat and Mass Transfer 47 (2004) 1175–1186 www.elsevier.com/locate/ijhmt Flow visualization of free convection in a vertical cylinder of water in the vicinity of the density maximum M.F. Cawley *, P. McBride Department of Experimental Physics, National University of Ireland, Maynooth, County Kildare, Ireland Received 24 February 2003; received in revised form 16 September 2003 Abstract Free convection in a vertical cylinder of water is studied in the vicinity of the density maximum at 4 °C. Results are presented both from cooling curve measurements (using a series of thermistors along the central axis of the cylinder) and from flow visualization experiments (using particle image velocimetry), and a comparison is made with simulations. The reversal of the overall flow direction as the temperature crosses the maximum density region gives rise to a plateau feature in the cooling curve, which may be explained by the formation of a rising toroidal structure along the column boundary. This feature effectively diverts flow away from the inner region of the cylinder, resulting in a temporary cessation of convective cooling within this region. Ó 2003 Elsevier Ltd. All rights reserved. 1. Introduction Hope [2]. Through a series of experiments, he proposed that water was at its most dense at a temperature be- Fluid density usually changes as a function of tem- tween 4.2 and 4.4 °C (Hope quoted his results using the perature in a reasonably linear manner. A notable Fahrenheit scale; he concluded that the density maxi- exception is liquid water. -
High-Pressure and High-Temperature Density Measurements of N- Pentane, N-Octane, 2,2,4-Trimethylpentane, Cyclooctane, N- Decane, and Toluene
Virginia Commonwealth University VCU Scholars Compass Theses and Dissertations Graduate School 2010 High-Pressure and High-Temperature Density Measurements of n- Pentane, n-Octane, 2,2,4-Trimethylpentane, Cyclooctane, n- Decane, and Toluene Yue Wu Virginia Commonwealth University Follow this and additional works at: https://scholarscompass.vcu.edu/etd Part of the Engineering Commons © The Author Downloaded from https://scholarscompass.vcu.edu/etd/2286 This Thesis is brought to you for free and open access by the Graduate School at VCU Scholars Compass. It has been accepted for inclusion in Theses and Dissertations by an authorized administrator of VCU Scholars Compass. For more information, please contact [email protected]. High-Pressure and High-Temperature Density Measurements of n-Pentane, n-Octane, 2,2,4-Trimethylpentane, Cyclooctane, n-Decane, and Toluene A thesis submitted in partial fulfillment of the requirements for the degree of Master of Science at Virginia Commonwealth University. by Yue Wu, Master of Science, Virginia Commonwealth University, 2010 Director: Mark A. McHugh, Professor, Department of Chemical and Life Science Engineering Virginia Commonwealth University Richmond, Virginia October, 2010 Acknowledgment I thank my advisor, Professor Mark A. McHugh for his guidance over the years. He will always be given my respect for guiding me through the ocean of chemical engineering. His devotion to the science, great personality, and sense of humor impress me a lot. I do enjoy working in Professor McHugh’s Lab. I acknowledge Dr. Kun Liu for helping me get familiar with the high-pressure view cell system and some density experiments. I thank my family and girlfriend for their support throughout my life. -
Density Standards for Field Compaction of Granular Bases and Subbases
172 Vk ~ MAR 7 1977 DEPT. OF HIGHWAYS BRIDGE SECTION NATIONAL COOPERATIVE HIGt-IWAY RESEARCH PROGRAM REPORT 172 DENSITY STANDARDS FOR FIELD COMPACTION OF GRANULAR BASES AND SUBBASES TRANSPORTATION RESEARCH BOARD NATIONAL RESEARCH COUNCIL TRANSPORTATION RESEARCH BOARD 1976 Officers HAROLD L. MICHAEL, Chairman ROBERT N. HUNTER, Vice Chairman W. N. CAREY, JR., Executive Director Executive Committee HENRIK E. STAFSETH, Executive Director, American Assn. of State Highway and Transportation Officials (ex officio) NORBERT T. TIEMANN, Federal Highway Administrator, U.S. Department of Transportation (ex officio) ROBERT E. PATRICELLI, Urban Mass Transportation Administrator, U.S. Department of Transportation (ex officio) ASAPH H. HALL, Federal Railroad Administrator, U.S.' Department of Transportation (ex officio) HARVEY BROOKS, Chairman, Commission on Sociotechnical Systems, National Research Council (ex officio) MILTON PIKARSKY, Chairman of the Board, Chicago Regional Transportation Authority (ex officio, Past Chairman 1975) WARREN E. ALBERTS, Vice President (Systems Operations Seivices), United Airlines GEORGE H. ANDREWS, Vice President (Transportation Marketing), Sverdrup and Parcel GRANT BASTIAN, State Highway Engineer, Nevada Department of Highst'ays KURT W. BAUER, Executive Director, Southeastern Wisconsin Regional Planning Commission LANGHORNE M. BOND, Secretary, Illinois Department of Transportation MANUEL CARBALLO, Secretary of Health and Social Services, State of Wisconsin L. S. CRANE, President, Southern Railway System JAMES M. DAVEY Consultant B. L. DEBERRY, Engineer-Director, Texas State Department of Highways and Public Transportation LOUIS J. GAMBACCINI, Vice President and General Manager, Port Authority Trans-Hudson Corporation HOWARD L. GAUTHIER, Professor of Geography, Ohio State University FRANK C. HERRINGER, General Manager, San Francisco Bay Area Rapid Transit District ANN R. HULL, Delegate, Maryland General Assembly ROBERT N. -
Precision Density Measurement of Silicon 1 2
JOURNAL O F RESEARCH of the National Bureau of Standards- A. Physics and Chemistry Vol. 68A, No.5, September- Odober 1964 Precision Density Measurement of Silicon 1 2 Ivars Henins 3 (June 10, 1964) The densit ies of 22 large h ighly perfect sil icon single crystals have been measured by hydrostatic weighing in water, yielding an aver age value of ds ;(25°C) = 2.329002 ± (7 X 10- 6) g/cm3. An experimental precision has been achieved which exceeds the accuracy with which t he absolute density of water is known. The effect of variations of the water surface t ens ion force on the suspension wire has been m imized by using a 0.001 in . suspension wire coated with platinum black, and by doin g a large number of r epeated weighings of each crystal. 1. Introduction [2. Experimental Procedure :Measurement of density is one of the most basic Accurate density measurement consists of a precise of physical measurements, and is often intrinsic in determination of the mass and the volume of an the determination of other physical constants. For object. The mass can be determined by direct instance, the density together with the lattice spacing weighing, but the volume must usually be determined and molecular weight of a crystal can be used to indirectly by determining the mass of water that the determine Avogadro's number [1 ].4 Similarly, it is object displaces. Kohlrausch [6] was the first to use possible to determine relative a,tomic or molecular this method for accurate density determination, weights from the densities and lattice co nstants of and it usually bears his name. -
Measurement of the Temperature of Density Maximum of Water Solutions Using a Convective flow Technique
View metadata, citation and similar papers at core.ac.uk brought to you by CORE provided by MURAL - Maynooth University Research Archive Library International Journal of Heat and Mass Transfer 49 (2006) 1763–1772 www.elsevier.com/locate/ijhmt Measurement of the temperature of density maximum of water solutions using a convective flow technique M.F. Cawley *, D. McGlynn, P.A. Mooney Department of Experimental Physics, National University of Ireland, Maynooth, County Kildare, Ireland Received 4 August 2005 Available online 7 February 2006 Abstract A technique is described which yields an accurate measurement of the temperature of density maximum of fluids which exhibit such anomalous behaviour. The method relies on the detection of changes in convective flow in a rectangular cavity containing the test fluid. The normal single-cell convection which occurs in the presence of a horizontal temperature gradient changes to a double cell configu- ration in the vicinity of the density maximum, and this transition manifests itself in changes in the horizontal temperature profile across the cavity. The method is applied to a variety of water solutions. Ó 2006 Elsevier Ltd. All rights reserved. Keywords: Free convection; Water; Density anomaly; Density maximum; Aqueous solutions 1. Introduction which is exploited in fine-detail casting. Hydrogen bonding plays no role in such elemental metals. It is not clear if The majority of substances expand when heated. A any of these substances exhibit a density maximum in the notable exception is water: when water at 0 °C and at a liquid state under normal pressure conditions. A density pressure of one atmosphere is heated, its density increases maximum has been reported for Gallium [6], but under to a maximum value of 999.972 kg mÀ3 at 3.98 °C. -
Lecture 3: Neutron Stars
Neutron Stars We now enter the study of neutron stars. Like black holes, neutron stars are very compact objects, so general relativity is important in their description. Unlike black holes, they have surfaces instead of horizons, so they are a lot more complicated than black holes. We’ll start with an overall description of neutron stars, then discuss their high densities and strong magnetic fields. Summary of Neutron Stars A typical neutron star has a mass of 1.5 − 2 M⊙ and a radius of ∼ 10 − 15 km. It can have a spin frequency up to ∼1 kHz and a magnetic field up to perhaps 1015 G or more. Its surface gravity is around 2 − 3 × 1014 cm s−2, so mountains of even perfect crystals can’t be higher than < 1 mm, meaning that these are the smoothest surfaces in the universe. They have many types of behavior, including pulsing (in radio, IR, optical, UV, X-ray, and gamma-rays, but this is rarely all seen from a single object), glitching, accreting, and possibly gravitational wave emission. They are the best clocks in the universe; the most stable are thousands of times more stable in the short term than the best atomic clocks. Their cores are at several times nuclear density, and may be composed of exotic matter such as quark-gluon plasmas, strange matter, kaon condensates, or other weird stuff. In their interior they are superconducting and superfluid, with transition temperatures around a billion degrees Kelvin. All these extremes mean that neutron stars are attractive to study for people who want to push the envelope of fundamental theories about gravity, magnetic fields, and high-density matter.