The Use of Piezoelectric Resonators for the Characterization of Mechanical Properties of Polymers
Total Page:16
File Type:pdf, Size:1020Kb
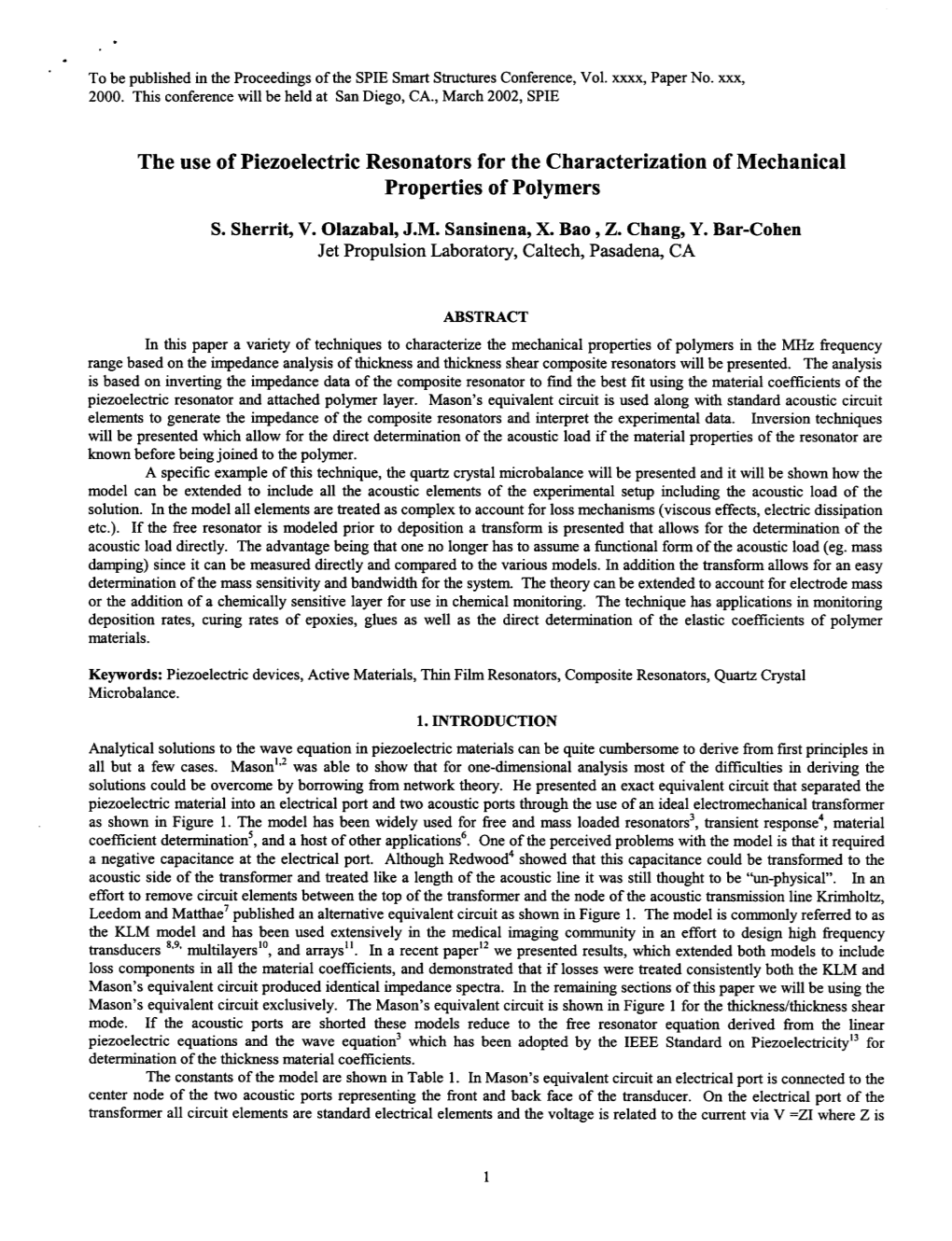
Load more
Recommended publications
-
Momentary Podl Connector and Cable Shorts
Momentary PoDL Connector and Cable Shorts Andy Gardner – Linear Technology Corporation 2 Presentation Objectives • To put forward a momentary connector or cable short fault scenario for Ethernet PoDL. • To quantify the requirements for surviving the energy dissipation and cable voltage transients subsequent to the momentary short. 3 PoDL Circuit with Momentary Short • IPSE= IPD= IL1= IL2= IL3= IL4 at steady-state. • D1-D4 and D5-D8 represent the master and slave PHY body diodes, respectively. • PoDL fuse or circuit breaker will open during a sustained over- current (OC) fault but may not open during a momentary OC fault. 4 PoDL Inductor Current Imbalance during a Cable or Connector Short • During a connector or cable short, the PoDL inductor currents will become unbalanced. • The current in inductors L1 and L2 will increase, while the current in inductors L3 and L4 will reverse. • Maximum inductor energy is limited by the PoDL inductors’ saturation current, i.e. ISAT > IPD(max). • Stored inductor energy resulting from the current imbalance will be dissipated by termination and parasitic resistances as well as the PHYs’ body diodes. • DC blocking capacitors C1-C4 need to be rated for peak transient voltages subsequent to the momentary short. 5 Max Energy Storage in PoDL Coupling Inductors during a Momentary Short • PoDL inductors L1-L4 are constrained by tdroop: −50 × 푡푑푟표표푝 퐿 > 푃표퐷퐿 ln 1 − 0.45 1 퐸 ≈ 4 × × 퐿 × 퐼 2 퐿(푡표푡푎푙) 2 푃표퐷퐿 푆퐴푇 • Example: if tdroop=500ns, LPoDL=42H which yields: ISAT Total EL 1A 84J 3A 756J 10A 8.4mJ 6 Peak Transient Voltage after a Short • The maximum voltage across the PHY DC blocking capacitors C1-C4 following a momentary short assuming damping ratio 휁 is: 퐿푃표퐷퐿 50Ω 푉푚푎푥 ≈ 퐼푠푎푡 × = 퐼푠푎푡 × 퐶휑푏푙표푐푘 2 × 휁 4 × 푡푑푟표표푝 where 퐶 ≥ −휁2 × 휑푏푙표푐푘 50Ω × ln (1 − 0.45) • The maximum voltage differential between the conductors in the twisted pair is then: Vmax(diff) = 2 Vmax ISAT 50/휁 • Example: A critically damped PoDL network (휁=1) with inductor ISAT = 1A yields Vmax(diff) 50V while an inductor ISAT = 10A will yield Vmax(diff) 500V. -
A Review of Electric Impedance Matching Techniques for Piezoelectric Sensors, Actuators and Transducers
Review A Review of Electric Impedance Matching Techniques for Piezoelectric Sensors, Actuators and Transducers Vivek T. Rathod Department of Electrical and Computer Engineering, Michigan State University, East Lansing, MI 48824, USA; [email protected]; Tel.: +1-517-249-5207 Received: 29 December 2018; Accepted: 29 January 2019; Published: 1 February 2019 Abstract: Any electric transmission lines involving the transfer of power or electric signal requires the matching of electric parameters with the driver, source, cable, or the receiver electronics. Proceeding with the design of electric impedance matching circuit for piezoelectric sensors, actuators, and transducers require careful consideration of the frequencies of operation, transmitter or receiver impedance, power supply or driver impedance and the impedance of the receiver electronics. This paper reviews the techniques available for matching the electric impedance of piezoelectric sensors, actuators, and transducers with their accessories like amplifiers, cables, power supply, receiver electronics and power storage. The techniques related to the design of power supply, preamplifier, cable, matching circuits for electric impedance matching with sensors, actuators, and transducers have been presented. The paper begins with the common tools, models, and material properties used for the design of electric impedance matching. Common analytical and numerical methods used to develop electric impedance matching networks have been reviewed. The role and importance of electrical impedance matching on the overall performance of the transducer system have been emphasized throughout. The paper reviews the common methods and new methods reported for electrical impedance matching for specific applications. The paper concludes with special applications and future perspectives considering the recent advancements in materials and electronics. -
Short Circuit and Overload Protection Devices Within an Electrical System
TM Information Sheet # 07 Short Circuit and Overload Protection Your Reliable Guide for Power Solutions Devices Within an Electrical System 1.0 Introduction The designer of an electrical system has the responsibility to meet code requirements and to ensure that the equipment and conductors within a system are protected against current flows that will produce destructive temperatures above specified rating and design limits. This information sheet discusses protective devices that are used within a system, how they work and where they are used. 2.0 Overcurrent protection devices: Protection against temperature is termed “overcurrent protection.” Overcurrents are caused by equipment overloads, by short circuits or by ground faults. An overload occurs when equipment is subjected to current above its rated capacity and excessive heat is produced. A short circuit occurs when there is a direct but unintended connection between line-to-line or line-to-neutral conductors. Short circuits can generate temperatures thousands of degrees above designated ratings. A ground fault occurs when electrical current flows from a conductor to uninsulated metal that is not designed to conduct electricity. These uninsulated currents can be lethal. The designer has many overcurrent protection devices to choose from. The two most common are fuses and circuit breakers. Many circuit breakers are also known as molded case breakers or MCBs. Fuses: A fuse is the simplest form of overcurrent protective device but it can be used only once before it must be replaced. A fuse consists of a conducting element enclosed in a glass, ceramic or other non-conductive tube and connected by ferrules at each end of the tube. -
Electrical Impedance Tomography
INSTITUTE OF PHYSICS PUBLISHING INVERSE PROBLEMS Inverse Problems 18 (2002) R99–R136 PII: S0266-5611(02)95228-7 TOPICAL REVIEW Electrical impedance tomography Liliana Borcea Computational and Applied Mathematics, MS 134, Rice University, 6100 Main Street, Houston, TX 77005-1892, USA E-mail: [email protected] Received 16 May 2002, in final form 4 September 2002 Published 25 October 2002 Online at stacks.iop.org/IP/18/R99 Abstract We review theoretical and numerical studies of the inverse problem of electrical impedance tomographywhich seeks the electrical conductivity and permittivity inside a body, given simultaneous measurements of electrical currents and potentials at the boundary. (Some figures in this article are in colour only in the electronic version) 1. Introduction Electrical properties such as the electrical conductivity σ and the electric permittivity , determine the behaviour of materials under the influence of external electric fields. For example, conductive materials have a high electrical conductivity and both direct and alternating currents flow easily through them. Dielectric materials have a large electric permittivity and they allow passage of only alternating electric currents. Let us consider a bounded, simply connected set ⊂ Rd ,ford 2and, at frequency ω, let γ be the complex admittivity function √ γ(x,ω)= σ(x) +iω(x), where i = −1. (1.1) The electrical impedance is the inverse of γ(x) and it measures the ratio between the electric field and the electric current at location x ∈ .Electrical impedance tomography (EIT) is the inverse problem of determining the impedance in the interior of ,givensimultaneous measurements of direct or alternating electric currents and voltages at the boundary ∂. -
Impedance Matching
Impedance Matching Advanced Energy Industries, Inc. Introduction The plasma industry uses process power over a wide range of frequencies: from DC to several gigahertz. A variety of methods are used to couple the process power into the plasma load, that is, to transform the impedance of the plasma chamber to meet the requirements of the power supply. A plasma can be electrically represented as a diode, a resistor, Table of Contents and a capacitor in parallel, as shown in Figure 1. Transformers 3 Step Up or Step Down? 3 Forward Power, Reflected Power, Load Power 4 Impedance Matching Networks (Tuners) 4 Series Elements 5 Shunt Elements 5 Conversion Between Elements 5 Smith Charts 6 Using Smith Charts 11 Figure 1. Simplified electrical model of plasma ©2020 Advanced Energy Industries, Inc. IMPEDANCE MATCHING Although this is a very simple model, it represents the basic characteristics of a plasma. The diode effects arise from the fact that the electrons can move much faster than the ions (because the electrons are much lighter). The diode effects can cause a lot of harmonics (multiples of the input frequency) to be generated. These effects are dependent on the process and the chamber, and are of secondary concern when designing a matching network. Most AC generators are designed to operate into a 50 Ω load because that is the standard the industry has settled on for measuring and transferring high-frequency electrical power. The function of an impedance matching network, then, is to transform the resistive and capacitive characteristics of the plasma to 50 Ω, thus matching the load impedance to the AC generator’s impedance. -
Supercapacitor Power Management Module Michael Brooks Santa Clara University
Santa Clara University Scholar Commons Electrical Engineering Senior Theses Student Scholarship 7-16-2014 Supercapacitor power management module Michael Brooks Santa Clara University Anderson Fu Santa Clara University Brett Kehoe Santa Clara University Follow this and additional works at: http://scholarcommons.scu.edu/elec_senior Part of the Electrical and Computer Engineering Commons Recommended Citation Brooks, Michael; Fu, Anderson; and Kehoe, Brett, "Supercapacitor power management module" (2014). Electrical Engineering Senior Theses. Paper 7. This Thesis is brought to you for free and open access by the Student Scholarship at Scholar Commons. It has been accepted for inclusion in Electrical Engineering Senior Theses by an authorized administrator of Scholar Commons. For more information, please contact [email protected]. Supercapacitor Power Management Module BY Michael Brooks, Anderson Fu, and Brett Kehoe DESIGN PROJECT REPORT Submitted in Partial Fulfillment of the Requirements For the Degree of Bachelor of Science in Electrical Engineering in the School of Engineering of Santa Clara University, 2014 Santa Clara, California ii Table of Contents Signature Page. .i . Title Page. ii Table of Contents. iii Abstract. v Acknowledgements . .vi 1 Introduction . …………………… 1 1.1 Core Statement . …………1 1.2 Supercapacitors and Energy Storage . ………......3 1.3 Design Goal . …………… 3 1.4 Design Considerations . …4 1.5 Module Overview . ……...6 Design of Module 2 Charge Management . 8 2.1 Choosing a Supercapacitor . …8 2.2 Safely Charging Supercapacitors. 9 2.3 Voltage Balancing Circuit. 10 2.4 Charge Sources . 11 3 Output Utilization. 13 3.1 Single Ended Primary Inductor Converter. …13 3.2 LT3959: Compensated SEPIC Feedback Controller . .13 3.3 SEPIC Topology . -
TWO MODELS of ELECTRICAL IMPEDANCE for ELECTRODES with TAP WATER and THEIR CAPABILITY to RECORD GAS VOLUME FRACTION Revista Mexicana De Ingeniería Química, Vol
Revista Mexicana de Ingeniería Química ISSN: 1665-2738 [email protected] Universidad Autónoma Metropolitana Unidad Iztapalapa México Rodríguez-Sierra, J.C.; Soria, A. TWO MODELS OF ELECTRICAL IMPEDANCE FOR ELECTRODES WITH TAP WATER AND THEIR CAPABILITY TO RECORD GAS VOLUME FRACTION Revista Mexicana de Ingeniería Química, vol. 15, núm. 2, 2016, pp. 543-551 Universidad Autónoma Metropolitana Unidad Iztapalapa Distrito Federal, México Available in: http://www.redalyc.org/articulo.oa?id=62046829020 How to cite Complete issue Scientific Information System More information about this article Network of Scientific Journals from Latin America, the Caribbean, Spain and Portugal Journal's homepage in redalyc.org Non-profit academic project, developed under the open access initiative Vol. 15, No. 2 (2016) 543-551 Revista Mexicana de Ingeniería Química CONTENIDO TWO MODELS OF ELECTRICAL IMPEDANCE FOR ELECTRODES WITH TAP WATER ANDVolumen THEIR 8, número CAPABILITY 3, 2009 / Volume TO 8, RECORD number 3, GAS2009 VOLUME FRACTION DOS MODELOS DE IMPEDANCIA ELECTRICA´ PARA ELECTRODOS CON AGUA POTABLE Y SU CAPACIDAD DE REPRESENTAR LA FRACCION´ VOLUMEN DE 213 Derivation and application of the Stefan-MaxwellGAS equations * (Desarrollo y aplicaciónJ.C. de Rodr las ecuaciones´ıguez-Sierra de Stefan-Maxwell) and A. Soria Departamento de Ingenier´ıade Procesos e Hidr´aulica.Divisi´onCBI, Universidad Aut´onomaMetropolitana-Iztapalapa. San Stephen Whitaker Rafael Atlixco No. 186 Col. Vicentina, CP 09340 Cd. de M´exico,M´exico. Received May 24, 2016; Accepted July 5, 2016 Biotecnología / Biotechnology Abstract 245 Modelado de la biodegradación en biorreactores de lodos de hidrocarburos totales del petróleo Bubble columns are devices for simultaneous two-phase or three-phase flows. -
The Radial Electric Field Excited Circular Disk Piezoceramic Acoustic Resonator and Its Properties
sensors Article The Radial Electric Field Excited Circular Disk Piezoceramic Acoustic Resonator and Its Properties Andrey Teplykh * , Boris Zaitsev , Alexander Semyonov and Irina Borodina Kotel’nikov Institute of Radio Engineering and Electronics of RAS, Saratov Branch, 410019 Saratov, Russia; [email protected] (B.Z.); [email protected] (A.S.); [email protected] (I.B.) * Correspondence: [email protected]; Tel.: +7-8452-272401 Abstract: A new type of piezoceramic acoustic resonator in the form of a circular disk with a radial exciting electric field is presented. The advantage of this type of resonator is the localization of the electrodes at one end of the disk, which leaves the second end free for the contact of the piezoelectric material with the surrounding medium. This makes it possible to use such a resonator as a sensor base for analyzing the properties of this medium. The problem of exciting such a resonator by an electric field of a given frequency is solved using a two-dimensional finite element method. The method for solving the inverse problem for determining the characteristics of a piezomaterial from the broadband frequency dependence of the electrical impedance of a single resonator is proposed. The acoustic and electric field inside the resonator is calculated, and it is shown that this location of electrodes makes it possible to excite radial, flexural, and thickness extensional modes of disk oscillations. The dependences of the frequencies of parallel and series resonances, the quality factor, and the electromechanical coupling coefficient on the size of the electrodes and the gap between them are calculated. -
IEEE Std 3002.3™-2018 Recommended Practice for Conducting Short-Circuit Studies and Analysis of Industrial and Commercial Power Systems
IEEE 3002 STANDARDS: POWER SYSTEMS ANALYSIS IEEE Std 3002.3™-2018 Recommended Practice for Conducting Short-Circuit Studies and Analysis of Industrial and Commercial Power Systems IEEE Std 3002.3™-2018 IEEE Recommended Practice for Conducting Short-Circuit Studies and Analysis of Industrial and Commercial Power Systems Sponsor Technical Books Coordinating Committee of the IEEE Industry Applications Society Approved 27 September 2018 IEEE-SA Standards Board Abstract: Activities related to short-circuit analysis, including design considerations for new systems, analytical studies for existing systems, as well as operational and model validation considerations for industrial and commercial power systems are addressed. Fault current calculation and device duty evaluation is included in short-circuit analysis. Accuracy of calculation results primarily relies on system modeling assumptions and methods used. The use of computer-aided analysis software with a list of desirable capabilities recommended to conduct a modern short-circuit study is emphasized. Examples of system data requirements and result analysis techniques are presented. Keywords: ac decrement, asymmetrical fault current, available fault current, bolted fault, breaking capacity, breaking duty, data collection, dc component, dc decrement, dc offset, device duty calculation, fault calculation, fault duty, IEEE 3002.3, interrupting capacity, interrupting duty, making capacity, making duty, momentary capacity, momentary duty, short-circuit analysis, short- circuit current, short-circuit studies, short-circuit withstand, symmetrical component, symmetrical fault current, system modeling, system validation, X/R ratio • The Institute of Electrical and Electronics Engineers, Inc. 3 Park Avenue, New York, NY 10016-5997, USA Copyright © 2019 by The Institute of Electrical and Electronics Engineers, Inc. All rights reserved. -
Advanced High-Frequency Measurement Techniques for Electrical and Biological Characterization in CMOS
Advanced High-Frequency Measurement Techniques for Electrical and Biological Characterization in CMOS Jun-Chau Chien Ali Niknejad Electrical Engineering and Computer Sciences University of California at Berkeley Technical Report No. UCB/EECS-2017-9 http://www2.eecs.berkeley.edu/Pubs/TechRpts/2017/EECS-2017-9.html May 1, 2017 Copyright © 2017, by the author(s). All rights reserved. Permission to make digital or hard copies of all or part of this work for personal or classroom use is granted without fee provided that copies are not made or distributed for profit or commercial advantage and that copies bear this notice and the full citation on the first page. To copy otherwise, to republish, to post on servers or to redistribute to lists, requires prior specific permission. Advanced High-Frequency Measurement Techniques for Electrical and Biological Characterization in CMOS by Jun-Chau Chien A dissertation submitted in partial satisfaction of the requirements for the degree of Doctor of Philosophy in Engineering – Electrical Engineering and Computer Sciences in the Graduate Division of the University of California, Berkeley Committee in charge: Professor Ali M. Niknejad, Chair Professor Jan M. Rabaey Professor Liwei Lin Spring 2015 Advanced High-Frequency Measurement Techniques for Electrical and Biological Characterization in CMOS Copyright © 2015 by Jun-Chau Chien 1 Abstract Advanced High-Frequency Measurement Techniques for Electrical and Biological Characterization in CMOS by Jun-Chau Chien Doctor of Philosophy in Electrical Engineering and Computer Science University of California, Berkeley Professor Ali M. Niknejad, Chair Precision measurements play crucial roles in science, biology, and engineering. In particular, current trends in high-frequency circuit and system designs put extraordinary demands on accurate device characterization and modeling. -
Z = R + Ix Z = |Z|E V = IZ
Electrical impedance Electrical impedance, or simply impedance, describes a measure of opposition to alternating current (AC). Electrical impedance extends the concept of resistance to AC circuits, describing not only the relative amplitudes of the voltage and current, but also the relative phases. When the circuit is driven with direct current (DC) there is no distinction between impedance and resistance; the latter can be thought of as impedance with zero phase angle. The symbol for impedance is usually Z and it may be represented by its magnitude and phase. However, complex number representation is more powerful for circuit analysis purposes. The term impedance was coined by Oliver Heaviside in July 1886. Arthur Kennelly was the first to represent impedance with complex numbers in 1893. • The magnitude of the complex impedance is the ratio of the voltage amplitude to the current amplitude. • The phase of the complex impedance is the phase shift by which the current is ahead of the voltage. Z = Z eiθ | | Z = R + iX The meaning of electrical impedance can be understood by substituting it into Ohm's law: V = IZ = I Z eiθ | | An AC supply applying a voltage V, across a load Z, driving a current I. The magnitude of the impedance acts just like resistance, giving the drop in voltage amplitude across an impedance for a given current . The phase factor tells us that the current lags the voltage by a phase of (i.e. in the time domain, the current signal is shifted to the right with respect to the voltage signal). Just as impedance extends Ohm's law to cover AC circuits, other results from DC circuit analysis can also be extended to AC circuits by replacing resistance with impedance. -
The Effect of Electrical Impedance Matching on the Electromechanical Characteristics of Sandwiched Piezoelectric Ultrasonic Transducers
Article The Effect of Electrical Impedance Matching on the Electromechanical Characteristics of Sandwiched Piezoelectric Ultrasonic Transducers Yuan Yang, Xiaoyuan Wei *, Lei Zhang and Wenqing Yao Department of Electronic Engineering, Xi’an University of Technology, Xi’an 710048, Shaanxi, China; [email protected] (Y.Y.); [email protected] (L.Z.); [email protected] (W.Y.) * Correspondence: [email protected]; Tel.: +86-029-8231-2087 Received: 04 November 2017; Accepted: 30 November 2017; Published: 6 December 2017 Abstract: For achieving the power maximum transmission, the electrical impedance matching (EIM) for piezoelectric ultrasonic transducers is highly required. In this paper, the effect of EIM networks on the electromechanical characteristics of sandwiched piezoelectric ultrasonic transducers is investigated in time and frequency domains, based on the PSpice model of single sandwiched piezoelectric ultrasonic transducer. The above-mentioned EIM networks include, series capacitance and parallel inductance (I type) and series inductance and parallel capacitance (II type). It is shown that when I and II type EIM networks are used, the resonance and anti-resonance frequencies and the received signal tailing are decreased; II type makes the electro-acoustic power ratio and the signal tailing smaller whereas it makes the electro-acoustic gain ratio larger at resonance frequency. In addition, I type makes the effective electromechanical coupling coefficient increase and II type makes it decrease; II type make the power spectral density at resonance frequency more dramatically increased. Specially, the electro-acoustic power ratio has maximum value near anti-resonance frequency, while the electro-acoustic gain ratio has maximum value near resonance frequency.