Cement-Based Piezoelectric Ceramic Composites for Sensing Elements: a Comprehensive State-Of-The-Art Review
Total Page:16
File Type:pdf, Size:1020Kb
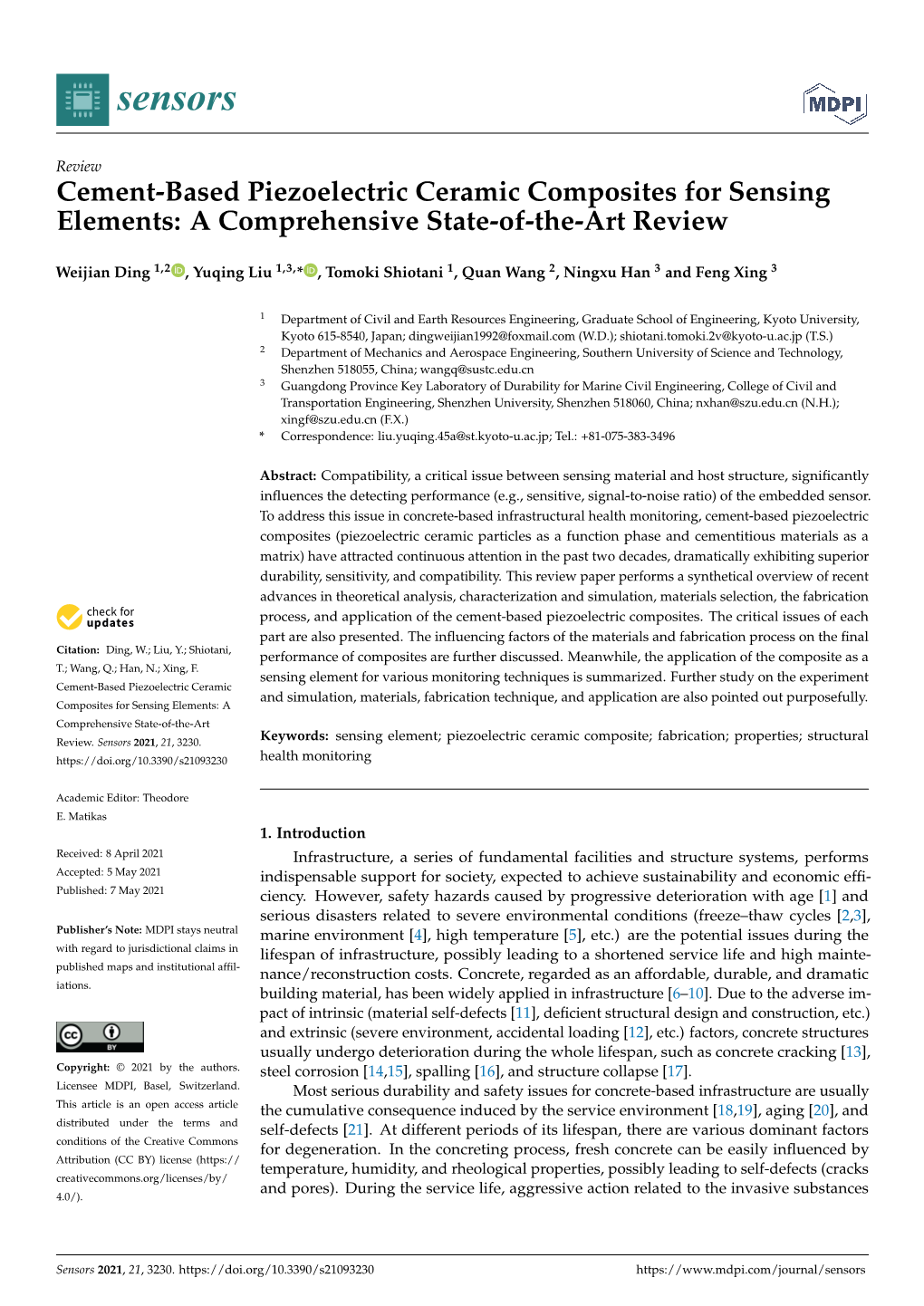
Load more
Recommended publications
-
Piezoelectric Pressure Sensor Based on Enhanced Thin-Film PZT Diaphragm Containing Nanocrystalline Powders
Chapter 6 Piezoelectric Pressure Sensor Based on Enhanced Thin-Film PZT Diaphragm Containing Nanocrystalline Powders Vahid Mohammadi, Saeideh Mohammadi and Fereshteh Barghi Additional information is available at the end of the chapter http://dx.doi.org/10.5772/54755 1. Introduction During recent years, the study of micro-electromechanical systems (MEMS) has shown that there are significant opportunities for micro sensors and microactuators based on various physical mechanisms such as piezoresistive, capacitive, piezoelectric, magnetic, and electro‐ static. In addition, specialized processes, novel materials, and customized packaging meth‐ ods are routinely used. MEMS themes include miniaturization, multiplicity, and microelectronic manufacturing and integration. Huge technology opportunities for MEMS are present in automotive applications, medicine, defense, controls, and communications. Other applications include biomedical pressure sensors and projection displays. For several excellent MEMS overviews of both core technologies and emerging applications, the readers are encouraged to consult references [1–4]. MEMS can be classified in two major categories: sensors and actuators. MEMS sensors, or microsensors, usually rely on integrated microfabrication methods to realize mechanical structures that predictably deform or respond to a specific physical or chemical variable. Such responses can be observed through a variety of physical detection methods including electronic and optical effects. Structures and devices are designed to be sensitive to changes in resistance (piezoresistivity), changes in capacitance, and changes in charge (piezoelectrici‐ ty), with an amplitude usually proportional to the magnitude of the stimulus sensed. Exam‐ ples of microsensors include accelerometers, pressure sensors, strain gauges, flow sensors, thermal sensors, chemical sensors, and biosensors. MEMS actuators, or microactuators, are usually based on electrostatic, piezoelectric, magnetic, thermal, and pneumatic forces. -
Piezoelectric Chemical Sensors
Pure Appl. Chem., Vol. 76, No. 6, pp. 1139–1160, 2004. © 2004 IUPAC INTERNATIONAL UNION OF PURE AND APPLIED CHEMISTRY ANALYTICAL CHEMISTRY DIVISION* PIEZOELECTRIC CHEMICAL SENSORS (IUPAC Technical Report) Prepared for publication by RICHARD P. BUCK1, ERNO˝ LINDNER2,‡, WLODZIMIERZ KUTNER3, AND GYÖRGY INZELT4 1Department of Chemistry, University of North Carolina at Chapel Hill, Chapel Hill, NC 27599-3290, USA; 2Department of Biomedical Engineering, The University of Memphis, Herff College of Engineering, Memphis, TN 38512, USA; 3Institute of Physical Chemistry, Polish Academy of Sciences, Kasprzaka 44/52, PL-01 224 Warszawa, Poland; 4Department of Physical Chemistry, Eötvös Loránd University, Budapest, Pázmány Péter sétány 1/A, H-1117, Hungary *Membership of the Analytical Chemistry Division during the final preparation of this report (2002–2003) was as follows: President: D. Moore (USA); Titular Members: F. Ingman (Sweden); K. J. Powell (New Zealand); R. Lobinski (France); G. G. Gauglitz (Germany); V. P. Kolotov (Russia); K. Matsumoto (Japan); R. M. Smith (UK); Y. Umezawa (Japan); Y. Vlasov (Russia); Associate Members: A. Fajgelj (Slovenia); H. Gamsjäger (Austria); D. B. Hibbert (Australia); W. Kutner (Poland); K. Wang (China); National Representatives: E. A. G. Zagatto (Brazil); M.-L. Riekkola (Finland); H. Kim (Korea); A. Sanz-Medel (Spain); T. Ast (Yugoslavia). ‡Corresponding author Republication or reproduction of this report or its storage and/or dissemination by electronic means is permitted without the need for formal IUPAC permission on condition that an acknowledgment, with full reference to the source, along with use of the copyright symbol ©, the name IUPAC, and the year of publication, are prominently visible. Publication of a translation into another language is subject to the additional condition of prior approval from the relevant IUPAC National Adhering Organization. -
On the Design of a MEMS Piezoelectric Accelerometer
www.nature.com/scientificreports OPEN On the design of a MEMS piezoelectric accelerometer coupled to the middle ear as an Received: 8 January 2018 Accepted: 19 February 2018 implantable sensor for hearing Published: xx xx xxxx devices A. L. Gesing1, F. D. P. Alves2, S. Paul1 & J. A. Cordioli1 The presence of external elements is a major limitation of current hearing aids and cochlear implants, as they lead to discomfort and inconvenience. Totally implantable hearing devices have been proposed as a solution to mitigate these constraints, which has led to challenges in designing implantable sensors. This work presents a feasibility analysis of a MEMS piezoelectric accelerometer coupled to the ossicular chain as an alternative sensor. The main requirements of the sensor include small size, low internal noise, low power consumption, and large bandwidth. Diferent designs of MEMS piezoelectric accelerometers were modeled using Finite Element (FE) method, as well as optimized for high net charge sensitivity. The best design, a 2 × 2 mm2 annular confguration with a 500 nm thick Aluminum Nitride (AlN) layer was selected for fabrication. The prototype was characterized, and its charge sensitivity and spectral acceleration noise were found to be with good agreement to the FE model predictions. Weak coupling between a middle ear FE model and the prototype was considered, resulting in equivalent input noise (EIN) lower than 60 dB sound pressure level between 600 Hz and 10 kHz. These results are an encouraging proof of concept for the development of MEMS piezoelectric accelerometers as implantable sensors for hearing devices. Over 10% of the world’s population is afected by hearing losses1, a disability which incurs in lower quality life and even reduced income. -
Charge Amplifier Type 5050B
Electronics and Software Charge Amplifier Type 5050B... In-line TEDS Charge Amplifier Module A signal processing device that converts the charge signal from a high impedance piezoelectric sensor into a voltage signal at a low impedance level. Used with high impedance acceleration sensors for performing dynamic measurements in a wide variety of applications. • Two-wire, single-ended device • Rugged, stainless steel case • Wide frequency response • Five gain versions • ä conforming • IEPE compatibility • TEDS option available 2.79 Description 0.17 0.47 The 5050B... in-line TEDS charge amplifier series contains ø0.625 miniature charge amplifiers that convert the charge signal from a stand-alone high impedance piezoelectric sensor into a high level voltage signal at a low impedance output. This two-wire, single-ended device is in five fixed gain settings 0.1, 0.5, 1, 10, and 25 mV/pC with a frequency response of KIAG 10-32 neg. Connector BNC neg. Connector 0.5 Hz ... 50 kHz. Type 5050B... T-version includes a TEDS (sensor input) (output) (Transducer Electronic Data Sheet) chip for storage and retrieval of information. The charge converters can be powered by several Kistler Piezotron power supply couplers or any industry standard IEPE (Integrated Electronic Piezo-Electric) compatible power source. Installation Application Typically, the sensor is placed in a high temperature environment The combination of Type 5050B... in-line TEDS charge amplifier and the charge converter is located some distance away at a and power supply/coupler is a less expensive alternative to location within its operating temperature range. laboratory style charge amplifiers. The charge amplifier is inserted in the signal line between a high impedance sensor and follow- High temperature cable such as the Type 1635Csp is used to on signal conditioning. -
Industrial Vibration Accelerometer Performance Considerations: Shear Versus Compression Designs
Industrial Vibration Accelerometer Performance Considerations: Shear versus Compression Designs By: David A. Corelli Category IV Vibration Analyst Director of Application Engineering IMI Sensors Molly Bakewell Global PR, Advertising & Image Manager PCB Piezotronics, Inc. www.pcb.com The implementation of industrial vibration monitoring sensors and associated signal conditioning as an integral part of industrial predictive maintenance programs has proven for many maintenance and plant engineers to be an effective strategy for reducing downtime and improving overall machinery health. Vibration monitoring technology is widely used because of its ability to detect and diagnose a wide variety of machinery faults, such as bearing faults, gear problems, misalignment, looseness, mass imbalance, and others, on a wide variety of rotating machinery, and its relative ease of integration with portable data collectors, online vibration monitoring systems, PLC’s, qne SCADA and Plant Information (PI) systems. For the proper implementation of sensors into a vibration monitoring program, one must first understand the differences in the two most common designs of industrial piezoelectric sensors, as well as various considerations in selection and mounting. A piezoelectric accelerometer produces a measurable electrical signal when an inertial mass stresses, or applies a force to, its integral crystal sensing element. The two main types of piezoelectric sensor designs most typically used for industrial vibration monitoring applications are shear and compression, which define the actual mode, or crystal axis, in which an inertial mass stresses the piezoelectric crystal. While both types operate in a similar fashion, one of these designs provides much more reliable and repeatable performance when acted upon by certain external influences within the demanding industrial application environment. -
Velocity Measurements Using a Piezoelectric Plate As a Sensor
University of Texas at El Paso ScholarWorks@UTEP Open Access Theses & Dissertations 2020-01-01 Velocity Measurements Using A Piezoelectric Plate As A Sensor Paul Perez University of Texas at El Paso Follow this and additional works at: https://scholarworks.utep.edu/open_etd Part of the Mechanical Engineering Commons Recommended Citation Perez, Paul, "Velocity Measurements Using A Piezoelectric Plate As A Sensor" (2020). Open Access Theses & Dissertations. 3020. https://scholarworks.utep.edu/open_etd/3020 This is brought to you for free and open access by ScholarWorks@UTEP. It has been accepted for inclusion in Open Access Theses & Dissertations by an authorized administrator of ScholarWorks@UTEP. For more information, please contact [email protected]. VELOCITY MEASUREMENTS USING A PIEZOELECTRIC PLATE AS A SENSOR PAUL ALFREDO PEREZ ITURRALDE Master’s Program in Mechanical Engineering APPROVED: Norman Love, Ph.D., Chair Yirong Lin, Ph.D. Tzu-Liang (Bill) Tseng, Ph.D. Stephen L. Crites, Jr., Ph.D. Dean of the Graduate School Copyright © by Paul Alfredo Perez Iturralde 2020 Dedication I dedicated this work to my parents and siblings because they are the main foundation of my values, they laid my foundations of responsibility and desires for professional improvement. EXPERIMENTAL SET UP FOR THE TESTING OF A PIEZOELECTRIC MASS FLOW RATE SENSOR by PAUL ALFREDO PEREZ ITURRALDE THESIS Presented to the Faculty of the Graduate School of The University of Texas at El Paso in Partial Fulfillment of the Requirements for the Degree of MASTER OF SCIENCE Department of Mechanical Engineering THE UNIVERSITY OF TEXAS AT EL PASO May 2020 Acknowledgements This thesis has been funded by National Energy Technology Laboratory (NETL). -
Design of a Piezoelectric Accelerometer with High Sensitivity and Low Transverse Effect
sensors Article Design of a Piezoelectric Accelerometer with High Sensitivity and Low Transverse Effect Bian Tian, Hanyue Liu *, Ning Yang, Yulong Zhao and Zhuangde Jiang State Key Laboratory for Mechanical Manufacturing Systems Egineering, Xi’an Jiaotong University, Xi’an 710049, China; [email protected] (B.T.); [email protected] (N.Y.); [email protected] (Y.Z.); [email protected] (Z.J.) * Correspondence: [email protected]; Tel.: +86-29-8339-5171 Academic Editor: Jörg F. Wagner Received: 19 July 2016; Accepted: 21 September 2016; Published: 26 September 2016 Abstract: In order to meet the requirements of cable fault detection, a new structure of piezoelectric accelerometer was designed and analyzed in detail. The structure was composed of a seismic mass, two sensitive beams, and two added beams. Then, simulations including the maximum stress, natural frequency, and output voltage were carried out. Moreover, comparisons with traditional structures of piezoelectric accelerometer were made. To verify which vibration mode is the dominant one on the acceleration and the space between the mass and glass, mode analysis and deflection analysis were carried out. Fabricated on an n-type single crystal silicon wafer, the sensor chips were wire-bonged to printed circuit boards (PCBs) and simply packaged for experiments. Finally, a vibration test was conducted. The results show that the proposed piezoelectric accelerometer has high sensitivity, low resonance frequency, and low transverse effect. Keywords: piezoelectric accelerometer; high sensitivity; low resonance frequency; low transverse effect 1. Introduction With the development of urbanization, cables have gradually been replacing overhead lines due to their merits of being a reliable power supply, having a simple operation, and being a less occupying area. -
Modelling and Trials of Pyroelectric Sensors for Improving Its Application for Biodevices
MODELLING AND TRIALS OF PYROELECTRIC SENSORS FOR IMPROVING ITS APPLICATION FOR BIODEVICES Andrés Díaz Lantada, Pilar Lafont Morgado, Héctor Hugo del Olmo, Héctor Lorenzo-Yustos Javier Echavarri Otero, Juan Manuel Munoz-Guijosa, Julio Muñoz-García and José Luis Muñoz Sanz Grupo de Investigación en Ingeniería de Máquinas – E.T.S.I. Industriales – Universidad Politécnica de Madrid C/ José Gutiérrez Abascal, nº 2. 28006 – Madrid, Spain Keywords: Pyroelectricity, Ferroelectric Polymers, Sensors Behaviour, Medical Devices. Abstract: Active or “Intelligent” Materials are capable of responding in a controlled way to different external physical or chemical stimuli by changing some of their properties. These materials can be used to design and develop sensors, actuators and multifunctional systems with a large number of applications for developing medical devices. Pyroelectric materials, with thermoelectrical properties coupling, can be used as temperature sensors with applications in the development of several biodevices, including the combination with other thermally active materials, whose actuation can be improved by means of precise temperature registration. This paper makes an introduction to pyroelectricity and its main applications in the development of biodevices, focusing also in the pyroelectric properties of polyvinylidene fluoride or PVDF and presenting some results related with sensors’ behaviour modelling and characterization. 1 INTRODUCTION TO During the last decades important progress has been made in creating artificial pyroelectric PYROELECTRICITY materials, usually in the form of a thin film, out of gallium nitride (GaN), caesium nitrate (CsNO3), Pyroelectricity is the ability of certain materials to polyvinylidene fluorides (PVDF and copolymers), generate an electrical potential when they are heated derivatives of phenylpyrazine cobalt phthalocyanine or cooled. -
Piezoelectric Accelerometer with Improved Temperature Stability By
Title Page Piezoelectric Accelerometer with Improved Temperature Stability by Wenhao Huang B.E., University of Pittsburgh, 2019 Submitted to the Graduate Faculty of the Swanson School of Engineering in partial fulfillment of the requirements for the degree of Master of Science in Mechanical Engineering University of Pittsburgh 2021 Committee Page UNIVERSITY OF PITTSBURGH SWANSON SCHOOL OF ENGINEERING This thesis was presented by Wenhao Huang It was defended on April 8, 2021 and approved by Qing-Ming Wang, Ph.D., Professor Department of Mechanical Engineering and Materials Science Patrick Smolinski, Ph.D., Assosiate Professor Department of Mechanical Engineering and Materials Science Heng Ban, Ph.D., Professor Department of Mechanical Engineering and Materials Science Thesis Advisor: Qing-Ming Wang, Ph.D., Professor Department of Mechanical Engineering and Materials Science ii Copyright © by Wenhao Huang 2021 iii Abstract Piezoelectric Accelerometer with Improved Temperature Stability Wenhao Huang, M.S. University of Pittsburgh, 2021 Piezoceramic materials like PZT allow the manufacturing of piezoelectric sensors with advantages including high sensitivity, low price, and easy to shape. However, it is also featured with the pyroelectric effect, which brings extra charge generation with temperature variations. Those charges caused by the thermal effect contribute to errors in the sensor measurement result. Theoretically, the appropriate configuration of the sensor would neutralize the thermal effect. In this thesis, a triple layer piezoelectric sensor with a parallel connection would be used to check its thermal stability at elevated temperatures. The thesis begins with reviewing the fundamental concepts of piezoelectricity. The following section contains the analysis of the relationship between the different external inputs and the output of a triple layer sensor. -
Piezotron Coupler Type 5118B2 Piezoelectric Sensor Power Supply/Coupler
Pressure Piezotron coupler Type 5118B2 Piezoelectric sensor power supply/coupler A flexible, easy-to-use signal conditioner that provides excitation power, signal tailoring, and acts as an interface between voltage mode piezoelectric sensors and measuring instru ments. Single channel unit powered by internal AA bat- teries or an AC/DC adaptor. • Selectable gain and low-pass, plug-in filters • High-pass filtering, panel selectable • Monitor the condition of the sensors and cables • Exclusive “Rapid Zero” feature • AC, DC or battery powered • Conforming to ä Description Dimensions The signal conditioner provides the constant current 12,8 excitation required by low impedance, voltage mode sensors with 165 built-in electronics (i.e. Piezotron, PiezoBeam, K-Shear, and Ceramic Shear) or for high impedance sensors with an external impedance converter. Sensor power is supplied by the same 44,7 2-wire cable that provides the low impedance output signal. Type 5118B2 decouples the DC bias voltage from the output 25,4 signal and provides a 2 mA constant current source, which SIDE VIEW can also be factory adjusted from 2 ... 18 mA. Bias indicators display the condition of the sensor and cable. Amplifier gains TOP VIEW of 1x, 10x and 100x are selectable from a front panel switch. High-pass filter cutoff frequencies (–3 dB) 0.006 and 0.03 Hz are also selectable by a switch on the front panel. Plug-in, low-pass filters are available to limit the frequency response of the amplifier. These low-pass filters can be used to atten- 90,4 uate unwanted frequency and/or to improve signal-to-noise ratio. -
"Signal Conditioning Piezoelectric Sensors"
Application Report SLOA033A - September 2000 Signal Conditioning Piezoelectric Sensors James Karki Mixed Signal Products ABSTRACT Piezoelectric elements are used to construct transducers for a vast number of different applications. Piezoelectric materials generate an electrical charge in response to mechanical movement, or vice versa, produce mechanical movement in response to electrical input. This report discusses the basic concepts of piezoelectric transducers used as sensors and two circuits commonly used for signal conditioning their output. Contents 1 Introduction . 1 2 Theory and Modeling . 2 3 Signal Conditioning . 2 3.1 Voltage Mode Amplifier. 3 3.2 Charge Mode Amplifier. 4 3.3 Signal Conditioning Made Easier. 4 Appendix A . 5 List of Figures 1 Sensor Models . 2 2 Voltage Mode Amplifier Circuit. 3 3 Charge Mode Amplifier Circuit. 4 1 Introduction The word piezo comes from the Greek word piezein, meaning to press or squeeze. Piezoelectricity refers to the generation of electricity or of electric polarity in dielectric crystals when subjected to mechanical stress and conversely, the generation of stress in such crystals in response to an applied voltage. In 1880, the Curie brothers found that quartz changed its dimensions when subjected to an electrical field and generated electrical charge when pressure was applied. Since that time, researchers have found piezoelectric properties in hundreds of ceramic and plastic materials. Many piezoelectric materials also show electrical effects due to temperature changes and radiation. This report is limited to piezoelectricity. More detailed information on particular sensors can be found by contacting the manufacturer. 2 Theory and Modeling The basic theory behind piezoelectricity is based on the electrical dipole. -
Piezotron Coupler Type 5114
Electronics & Software Piezotron Coupler Type 5114... Versatile voltage mode piezoelectric sensor power supply/coupler A self contained power source that provides excitation power and acts as an interface between voltage mode piezoelectric sensors and measuring instruments. Single channel unit pow- ered by internal 9 volt battery or an AC/DC adaptor. • Provides constant current excitation • Monitors condition of sensors and cables • 3.5 digit LCD display • AC, DC or battery powered • Conforming to CE Description Type 5114 is a single channel signal conditioner that provides- constant current excitation required by low impedance voltage mode sensors with built-in electronics (i.e. Piezotron, Piezo- Beam, K-Shear, and Ceramic Shear) or for high impedance sensors with an external impedance converter. Sensor power is supplied by the same two-wire cable that provides the low impedance, output signal. Type 5114 decouples the DC bias voltage from the output signal. A 3.5 digit LCD with 0.5 inch high digits indicates sensor DC bias voltage. Three light-emitting diode on the display panel indicate the basic status of the sensor circuit. Bias voltages in the range of 4 to 16 volts are normal and result in a “Normal” (green) indication; bias voltages below 4 volts (see model ex- ception note 2) produce a “Short” (red) indication; and, a volt- age above 16 volts will result in an “Open” (yellow) indication. The unit operates from a single 9 volt battery or DC power from an external AC/DC power adapter. “LOBAT” is indicated on the LCD readout when battery replacement is required. One 9 volt battery is installed in a compartment in the bottom of the case and operates 36 hours.