Kelvin-Helmholtz
Total Page:16
File Type:pdf, Size:1020Kb
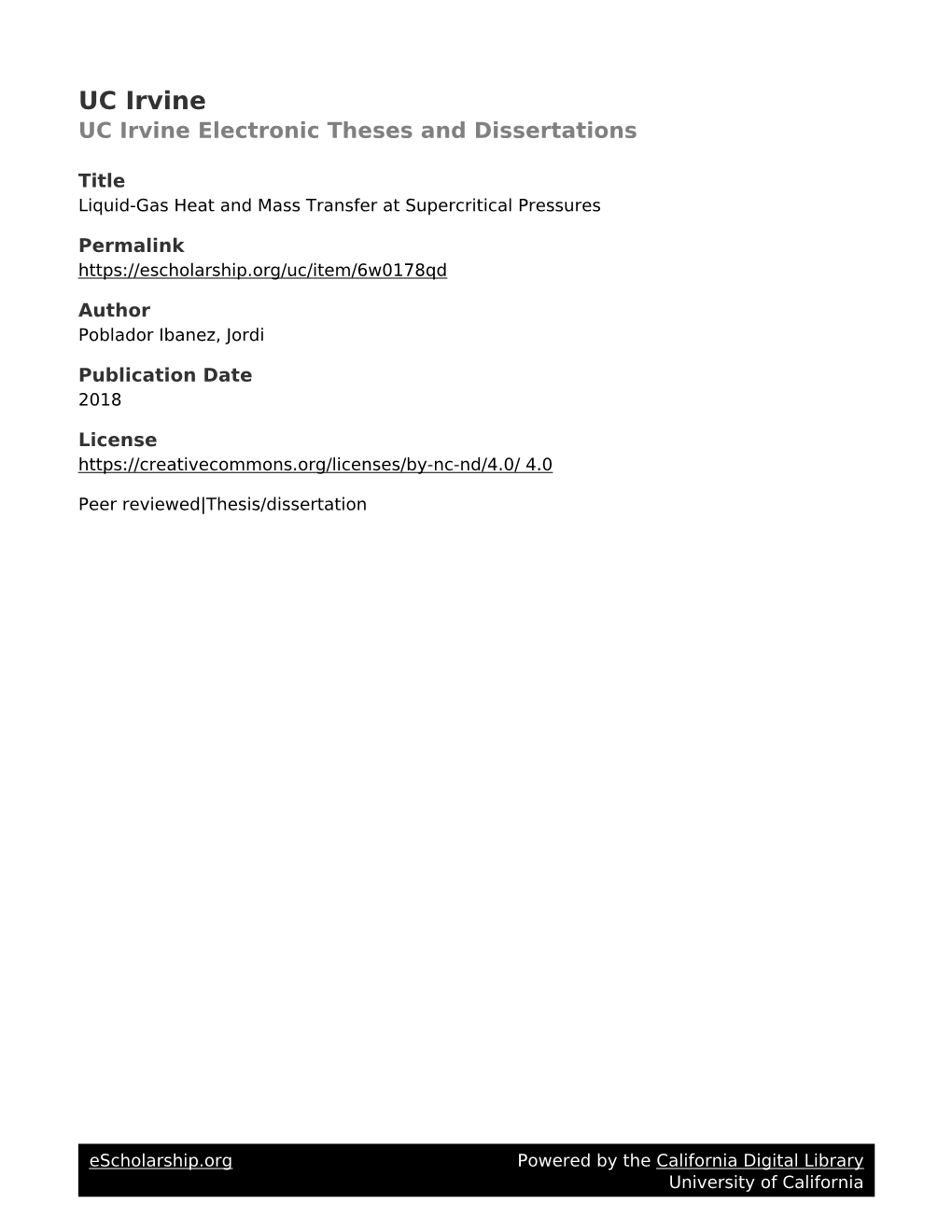
Load more
Recommended publications
-
Physical Model for Vaporization
Physical model for vaporization Jozsef Garai Department of Mechanical and Materials Engineering, Florida International University, University Park, VH 183, Miami, FL 33199 Abstract Based on two assumptions, the surface layer is flexible, and the internal energy of the latent heat of vaporization is completely utilized by the atoms for overcoming on the surface resistance of the liquid, the enthalpy of vaporization was calculated for 45 elements. The theoretical values were tested against experiments with positive result. 1. Introduction The enthalpy of vaporization is an extremely important physical process with many applications to physics, chemistry, and biology. Thermodynamic defines the enthalpy of vaporization ()∆ v H as the energy that has to be supplied to the system in order to complete the liquid-vapor phase transformation. The energy is absorbed at constant pressure and temperature. The absorbed energy not only increases the internal energy of the system (U) but also used for the external work of the expansion (w). The enthalpy of vaporization is then ∆ v H = ∆ v U + ∆ v w (1) The work of the expansion at vaporization is ∆ vw = P ()VV − VL (2) where p is the pressure, VV is the volume of the vapor, and VL is the volume of the liquid. Several empirical and semi-empirical relationships are known for calculating the enthalpy of vaporization [1-16]. Even though there is no consensus on the exact physics, there is a general agreement that the surface energy must be an important part of the enthalpy of vaporization. The vaporization diminishes the surface energy of the liquid; thus this energy must be supplied to the system. -
Corollary from the Exact Expression for Enthalpy of Vaporization
Hindawi Publishing Corporation Journal of Thermodynamics Volume 2011, Article ID 945047, 7 pages doi:10.1155/2011/945047 Research Article Corollary from the Exact Expression for Enthalpy of Vaporization A. A. Sobko Department of Physics and Chemistry of New Materials, A. M. Prokhorov Academy of Engineering Sciences, 19 Presnensky Val, Moscow 123557, Russia Correspondence should be addressed to A. A. Sobko, [email protected] Received 14 November 2010; Revised 9 March 2011; Accepted 16 March 2011 Academic Editor: K. A. Antonopoulos Copyright © 2011 A. A. Sobko. This is an open access article distributed under the Creative Commons Attribution License, which permits unrestricted use, distribution, and reproduction in any medium, provided the original work is properly cited. A problem on determining effective volumes for atoms and molecules becomes actual due to rapidly developing nanotechnologies. In the present study an exact expression for enthalpy of vaporization is obtained, from which an exact expression is derived for effective volumes of atoms and molecules, and under certain assumptions on the form of an atom (molecule) it is possible to find their linear dimensions. The accuracy is only determined by the accuracy of measurements of thermodynamic parameters at the critical point. 1. Introduction 1938 [2] with the edition from 1976 [3], we may find them actually similar. we may come to the same conclusion if In the present study, the relationship is obtained that we compare [2] with recent monograph by Prigogine and combines the enthalpy of vaporization with other thermody- Kondepudi “Modern Thermodynamics” [4]. The chapters namic evaporation parameters from the general expression devoted to first-order phase transitions in both monographs for the heat of first-order phase transformations. -
Thermodynamics Guide Definitions, Guides, and Tips Definitions What Each Thermodynamic Value Means Enthalpy of Formation
Thermodynamics Guide Definitions, guides, and tips Definitions What each thermodynamic value means Enthalpy of Formation Definition The enthalpy required or released during formation of a molecule from its elements. H2(g) + ½O2(g) → H2O(g) ∆Hºf(H2O) Sign: ∆Hºf can be positive or negative. Direction: From elements to product. Phase: The phase of the product being formed can be anything, but the elemental starting materials must be in their elemental standard phase. Notes: • RC&O Appendix 1 collects these values. • Limited by what values are experimentally available. • Knowing the elemental form of each atom is helpful. Ionization Enthalpy (IE) Definition The enthalpy required to remove one electron from an atom or ion. Li(g) → Li+(g) + e– IE(Li) Sign: IE is always positive — removing electrons from proximity of nucleus requires enthalpy input Direction: IE goes from atom to ion/electron pair. Phase: IE is a gas phase property. Reactants and products must be gas phase. Notes: • Phase descriptors are not generally given to an electron. • Ionization energy is taken to be identical to ionization enthalpy. • The first IE of Li(g) is shown above. A second, third, or higher IE can also be determined. Removing each additional electron costs even more enthalpy. Electron Affinity (EA) Definition How much enthalpy is gained when an electron is added to an atom or ion. (How much an atom “wants” an electron). Cl(g) + e– → Cl–(g) EA(Cl) Sign: EA is always positive, but the enthalpy is negative: ∆Hºrxn < 0. This is because of how we describe the property as an “affinity”. -
Chapter 1 INTRODUCTION and BASIC CONCEPTS
CLASS Third Units PURE SUBSTANCE • Pure substance: A substance that has a fixed chemical composition throughout. • Air is a mixture of several gases, but it is considered to be a pure substance. Nitrogen and gaseous air are pure substances. A mixture of liquid and gaseous water is a pure substance, but a mixture of liquid and gaseous air is not. 2 PHASES OF A PURE SUBSTANCE The molecules in a solid are kept at their positions by the large springlike inter-molecular forces. In a solid, the attractive and repulsive forces between the molecules tend to maintain them at relatively constant distances from each other. The arrangement of atoms in different phases: (a) molecules are at relatively fixed positions in a solid, (b) groups of molecules move about each other in the liquid phase, and (c) molecules move about at random in the gas phase. 3 PHASE-CHANGE PROCESSES OF PURE SUBSTANCES • Compressed liquid (subcooled liquid): A substance that it is not about to vaporize. • Saturated liquid: A liquid that is about to vaporize. At 1 atm and 20°C, water exists in the liquid phase (compressed liquid). At 1 atm pressure and 100°C, water exists as a liquid that is ready to vaporize (saturated liquid). 4 • Saturated vapor: A vapor that is about to condense. • Saturated liquid–vapor mixture: The state at which the liquid and vapor phases coexist in equilibrium. • Superheated vapor: A vapor that is not about to condense (i.e., not a saturated vapor). As more heat is transferred, At 1 atm pressure, the As more heat is part of the saturated liquid temperature remains transferred, the vaporizes (saturated liquid– constant at 100°C until the temperature of the vapor mixture). -
A Theoretical Analysis on Enthalpy of Vaporization: Temperature- Dependence and Singularity at the Critical State
Fluid Phase Equilibria 516 (2020) 112611 Contents lists available at ScienceDirect Fluid Phase Equilibria journal homepage: www.elsevier.com/locate/fluid A theoretical analysis on enthalpy of vaporization: Temperature- dependence and singularity at the critical state * Dehai Yu , Zheng Chen BIC-ESAT, SKLTCS, CAPT, Department of Mechanics and Engineering Science, College of Engineering, Peking University, Beijing, 100871, China article info abstract Article history: Accurate evaluation of enthalpy of vaporization and its dependence upon temperature is crucial in Received 4 November 2019 studying phase transition and liquid fuel combustion. The theoretical calculation of enthalpy of vapor- Received in revised form ization based on Clapeyron equation involves the vapor-pressure-temperature correlation and the 14 April 2020 equation of state, and hence an explicit formula is unavailable. The formula for enthalpy of vaporization Accepted 14 April 2020 derived from the corresponding state principle, although in explicit form, is not valid over the entire Available online 19 April 2020 temperature range. The fitting formulas for enthalpy of vaporization involves various fluid-dependent coefficients and hence are lack of theoretical generality. In this study, the formulas for enthalpy of Keywords: Enthalpy of vaporization vaporization are rigorously derived at both the reference and critical states. By appropriate weighing, we Temperature dependence propose a composite formula for enthalpy of vaporization that has an elegant and compact form and is Critical exponent free of fitting parameters. Compared to the calculation based on equation of state, the composite formula Heat capacity predicts the evaluation of enthalpy with comparable or improved accuracy. The composite formula Coordination number implies a unified relationship between normalized enthalpy of vaporization and normalized tempera- ture, which substantiates the appropriateness of the function form of the composite formula. -
(12) United States Patent (10) Patent No.: US 7,935,450 B2 Preidel Et Al
US00793545OB2 (12) United States Patent (10) Patent No.: US 7,935,450 B2 Preidel et al. (45) Date of Patent: May 3, 2011 (54) METHOD FOR OPERATION OF AN ENERGY (56) References Cited SYSTEM, ASWELLAS AN ENERGY SYSTEM U.S. PATENT DOCUMENTS (75) Inventors: Walter Preidel, Erlangen (DE); Bernd Wacker, Herzogenaurach (DE); Peter 4,617,801 A 10/1986 Clark, Jr. Van Hasselt, Erlangen (DE) FOREIGN PATENT DOCUMENTS DE 36 34.936 C1 5, 1988 (73) Assignee: Siemens Aktiengesellschaft, Munich DE 39 08573 C2 3, 1992 (DE) WO WO O2, 14736 * 2/2OO2 WO WO O2, 1473.6 A1 2, 2002 (*) Notice: Subject to any disclaimer, the term of this WO WOO2,24523 A2 3, 2002 patent is extended or adjusted under 35 * cited by examiner U.S.C. 154(b) by 1079 days. Primary Examiner — Ula C. Ruddock (21) Appl. No.: 11/723,268 Assistant Examiner — Thomas H. Parsons (22) Filed: Mar 19, 2007 (74) Attorney, Agent, or Firm — Harness, Dickey & Pierce, P.L.C. (65) Prior Publication Data US 2007/O248849 A1 Oct. 25, 2007 (57) ABSTRACT An energy system, in at least one embodiment, includes an (30) Foreign Application Priority Data energy production device for production of energy for the Mar. 20, 2006 (DE) ......................... 10 2006 O12 679 energy system with the aid of an working medium, a Super conductor for low-loss conduction of electrical energy in the (51) Int. Cl. energy system, and a cooling device for cooling of the Super HOLM 8/04 (2006.01) conductor with the aid of a liquid phase of a cooling medium. -
Enthalpy of Mixing and Heat of Vaporization of Ethyl Acetate with Benzene and Toluene at 298.15 K and 308.15 K
Brazilian Journal of Chemical ISSN 0104-6632 Printed in Brazil Engineering www.abeq.org.br/bjche Vol. 25, No. 01, pp. 167 - 174, January - March, 2008 ENTHALPY OF MIXING AND HEAT OF VAPORIZATION OF ETHYL ACETATE WITH BENZENE AND TOLUENE AT 298.15 K AND 308.15 K K. L. Shivabasappa1*, P. Nirguna Babu1 and Y. Jagannadha Rao2 1Department of Chemical Engineering, Siddaganga Institute of Technology, Phone: (91) 984-5768784, Fax: (91) 816-2282994, Tumkur, 572103, India. 2Department of Chemical Engineering, MVJ College of Engineering, Bangalore - 560067, India E-mail: [email protected] (Received: June 4, 2007 ; Accepted: November 5, 2007) Abstract - The present work was carried out in two phases. First, enthalpy of mixing was measured and then the heat of vaporization for the same mixtures was obtained. The data are useful in the design of separation equipments. From the various designs available for the experimental determination of enthalpy of mixing, and heat of vaporization, the apparatus was selected, modified and constructed. The apparatus of enthalpy of mixing was tested with a known system Benzene – i-Butyl Alcohol and the data obtained was in very good agreement with literature values. Experiments were then conducted for mixtures of Ethyl Acetate with Benzene and Toluene. The experimental data was fitted to the standard correlations and the constants were evaluated. Heat of vaporization data were obtained from a static apparatus and tested for accuracy by conducting experiments with a known system Benzene – n-Hexane and the data obtained were found to be in agreement with literature values. Experiments were then conducted to measure heat of vaporization for the mixtures of Ethyl Acetate with Benzene and Toluene. -
THERMODYNAMICS PROPERTIES of PURE SUBSTANCES Pure Substance a Substance That Has a Fixed Chemical Composition Throughout Is Called Pure Substance
Thermodynamics THERMODYNAMICS PROPERTIES OF PURE SUBSTANCES Pure Substance A substance that has a fixed chemical composition throughout is called pure substance. Water, helium carbon dioxide, nitrogen are examples. It does not have to be a single chemical element just as long as it is homogeneous throughout, like air. A mixture of phases of two or more substance is can still a pure substance if it is homogeneous, like ice and water (solid and liquid) or water and steam (liquid and gas). Vapor Vapor Liquid Liquid Water Air (Pure substance) (Not a pure substance because the composition of liquid air is different from the composition of vapor air) Phases of a Pure Substance There are three principle phases – solid, liquid and gas, but a substance can have several other phases within the principle phase. Examples include solid carbon (diamond and graphite) and iron (three solid phases). Nevertheless, thermodynamics deals with the primary phases only. In general: - Solids have strongest molecular bonds. - Solids are closely packed three dimensional crystals. - Their molecules do not move relative to each other - Intermediate molecular bond strength - Liquid molecular spacing is comparable to solids but their molecules can float about in groups. - There is molecular order within the groups - Weakest molecular bond strength. - Molecules in the gas phases are far apart, they have no ordered structure - The molecules move randomly and collide with each other. - Their molecules are at higher energy levels, they must release large amounts of energy to condense or freeze. THERMODYNAMICS 1 PROPERTIES OF PURE SUBSTANCES Thermodynamics Phase – Change Processes Of Pure Substances At this point, it is important to consider the liquid to solid phase change process. -
Extraction by Subcritical and Supercritical Water, Methanol, Ethanol and Their Mixtures
separations Review Extraction by Subcritical and Supercritical Water, Methanol, Ethanol and Their Mixtures Yizhak Marcus Institute of Chemistry, the Hebrew University of Jerusalem, Jerusalem 91904, Israel; [email protected] Received: 5 November 2017; Accepted: 27 December 2017; Published: 1 January 2018 Abstract: Hot, subcritical and supercritical water, methanol, ethanol and their binary mixtures have been employed to treat fuels (desulfurize coal and recover liquid fuels from coal and oil shales) and to extract valuable solutes from biomass. The properties of these solvents that are relevant to their extraction abilities are presented. Various extraction methods: accelerated solvent extraction (ASE), pressurized liquid extraction (PLE), supercritical fluid extraction (SFE, but excluding supercritical carbon dioxide) with these solvents, including microwave- and ultrasound-assisted extraction, are dealt with. The extraction systems are extensively illustrated and discussed. Keywords: ethanol; methanol; water; pressurized liquid; supercritical extraction; fuels; biomass 1. Introduction The concept of “green solvents” pertains to the wider area of “green chemistry”, for which several principles have been established. These include waste prevention, safety—no toxic or hazardous materials should be used or produced—maximization of energy efficiency, and minimization of the potential for accidents—explosion, fire, and pollution possibilities must be kept in mind. In view of these principles, the chemical community is proceeding in recent years towards sustainable industrial processes. Water is the “greenest solvent” imaginable: it is readily available at the required purity, it is cheap, it is readily recycled, non-toxic, non-flammable, and environmentally friendly. In its supercritical form, water is also considered as a “green solvent” [1]. Supercritical ethanol has also been mentioned as a “green solvent” and even supercritical methanol (although much less often). -
Enthalpy of Vaporization of Hypersaline Brine from 230 to 280 Bar
Enthalpy of Vaporization of Hypersaline Brine from 230 to 280 bar A thesis presented to the faculty of the Russ College of Engineering and Technology of Ohio University In partial fulfillment of the requirements for the degree Master of Science David D. Ogden May 2018 © 2018 David D. Ogden. All Rights Reserved. 2 This thesis titled Enthalpy of Vaporization of Hypersaline Brine from 230 to 280 bar by DAVID D. OGDEN has been approved for the Department of Mechanical Engineering and the Russ College of Engineering and Technology by Jason P. Trembly Associate Professor of Mechanical Engineering Dennis Irwin Dean, Russ College of Engineering and Technology 3 ABSTRACT OGDEN, DAVID D., M.S., May 2018, Mechanical Engineering Enthalpy of Vaporization of Hypersaline Brine from 230 to 280 bar Director of Thesis: Jason P. Trembly There is a need for thermodynamic data of mixed brine solutions in order to properly treat brines generated from oil/gas wells and CO2 sequestration. Thermodynamic properties of high concentration, multicomponent brine solutions are unknown, and limited to estimations based on single component solution data. Experimental data for mixed brine solutions at elevated temperatures and pressures does not exist due to the extreme operating conditions above the supercritical point of pure water. This study combines experimental results for mixed brine solutions, with thermodynamic models previously created for single component NaCl solutions to identify deviations resulting from additional dissolved species. Experiments were conducted using a Joule heated desalinator at pressures of 230 to 280 bar and temperatures of 387 to 406 ºC. 4 ACKNOWLEDGMENTS I would like to thank my advisor, Dr. -
Enthalpies of Vaporization and Sublimation of the Halogen- Substituted Aromatic Hydrocarbons at 298.15 K: Application of Solution Calorimetry Approach † † † † Boris N
Article pubs.acs.org/jced Enthalpies of Vaporization and Sublimation of the Halogen- Substituted Aromatic Hydrocarbons at 298.15 K: Application of Solution Calorimetry Approach † † † † Boris N. Solomonov,*, Mikhail A. Varfolomeev, Ruslan N. Nagrimanov, Vladimir B. Novikov, † † † ‡ Marat A. Ziganshin, Alexander V. Gerasimov, and Sergey P. Verevkin*, , † Department of Physical Chemistry, Kazan Federal University, Kremlevskaya str. 18, 420008 Kazan, Russia ‡ Department of Physical Chemistry, University of Rostock, Dr-Lorenz-Weg 1, 18059 Rostock, Germany *S Supporting Information ABSTRACT: Recently, the solution calorimetry has been shown to be a valuable tool for the indirect determination of vaporization or sublimation enthalpies of low volatile organic compounds. In this work we studied 16 halogen-substituted derivatives of benzene, naphthalene, biphenyl, and anthracene using a new solution calorimetry based approach. Enthalpies of solution at infinite dilution in benzene as well as molar refractions for the chlorine-, bromine-, and iodine-substituted aromatics were measured at 298.15 K. Vaporization and sublimation enthalpies of these compounds at 298.15 K were indirectly derived from the solution calorimetry data. In order to verify results obtained by using solution calorimetry, vaporization/sublimation enthalpies for 1,2-, 1,3-, 1,4-dibromobenzenes, 4-bromobiphenyl, and 4,4′-dibromobiphenyl were additionally measured by using the well established transpiration method. Experimental data available in the literature were collected and evaluated in this work for the sake of comparison with our own results. Vaporization and sublimation enthalpies of halogen-substituted aromatics under study derived by using solution calorimetry approach have been in a good agreement with those measured by conventional methods. This fact approves using of solution calorimetry for determination or validation of sublimation/vaporization enthalpies for different aromatic compounds at reference temperature 298.15 K, where the conventional experimental data are absent or in disarray. -
Evaluation and Prediction of Latent Heat of Vaporization at Various Temperatures for Pure Components and Binary Mixtures
Evaluation and Prediction of Latent Heat of Vaporization at Various Temperatures for Pure Components and Binary Mixtures A Thesis Submitted to the College of Engineering of Nahrain University in Partial Fulfillment of the Requirements for the Degree of Master of Science in Chemical Engineering by Mohammed Jabbar Ajrash B.Sc. in Chemical Engineering 2006 Jamad Al- awla 1430 May 2009 1 Abstract The prediction of latent heat of vaporization of pure compounds has at least sixteen methods to predict the latent heat of vaporization for pure compounds and three methods to predict the latent heat of vaporization for binary mixtures .All these methods has been evaluated in this work. There are at least nine methods available in literature for prediction of latent heat of vaporization at any temperature using either vapor pressure data or the law of corresponding states .These methods predict the latent heat of vaporization at various temperatures directly. The accuracy of these methods are different. Some of these methods have accurate results when dealing with non polar compounds but not so accurate when dealing with polar compounds . Halim and Stiel is the best method among these nine methods which is directly deal with polarity of compounds by introducing what is known polarity factor of polar compounds and it gives 1.552 absolute average deviation percent compared with experimental data for 18 pure non polar compounds with 446 data points .On the other hand it gives 2.8476 AAD% compared with experimental data for 6 polar compounds with 180 data points . The prediction of the latent heat of vaporization from normal boiling point have at least seven methods .