Review on Friction Stir Welding
Total Page:16
File Type:pdf, Size:1020Kb
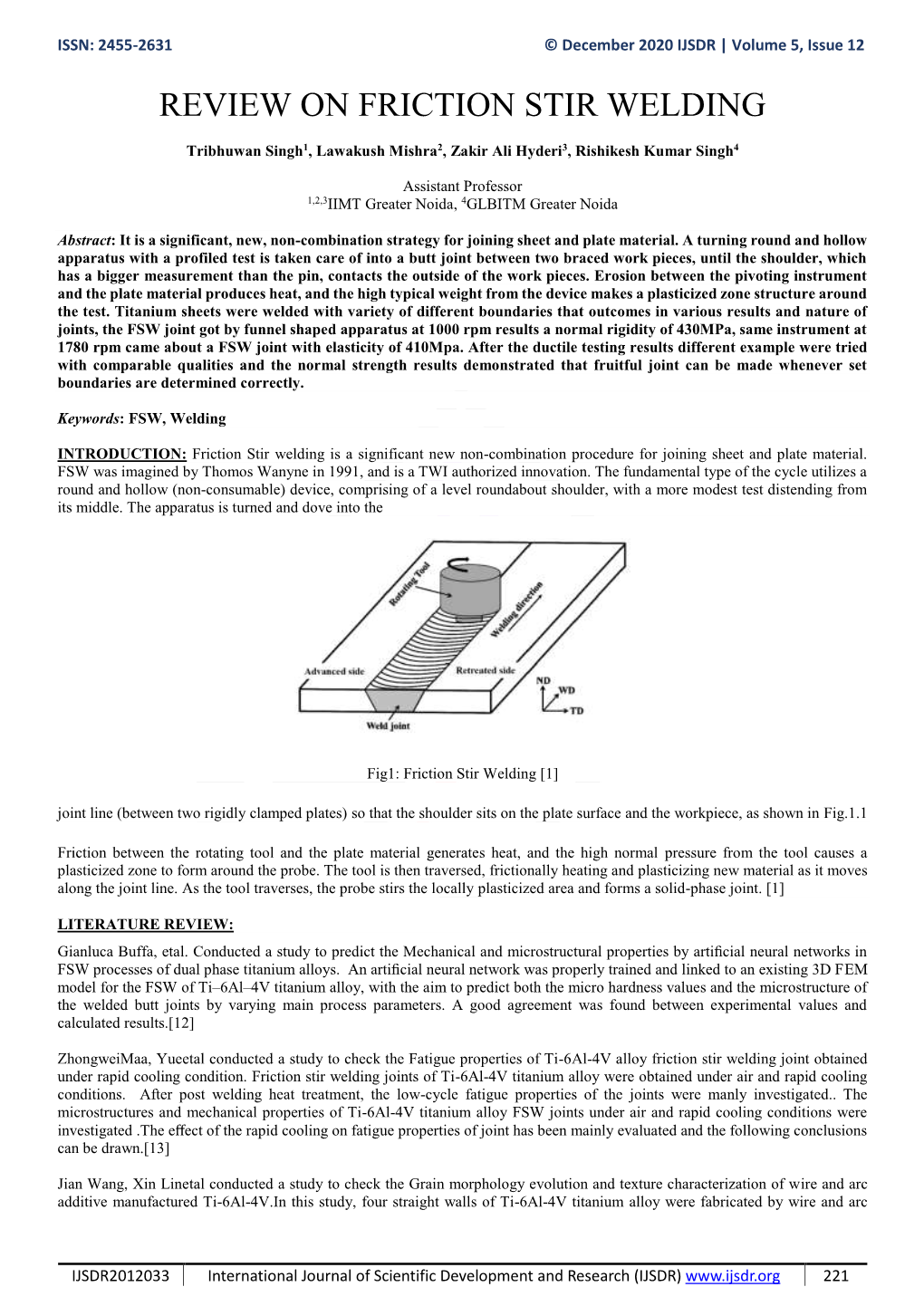
Load more
Recommended publications
-
Solid State Welding
EAA Aluminium Automotive Manual – Joining 7. Solid state welding Content: 7. Solid state welding 7.0 Introduction 7.1 Friction welding 7.1.1 Friction welding of components 7.1.1.1 Rotational friction welding 7.1.1.2 Linear friction welding 7.1.1.3 Orbital and multi-orbital friction welding 7.1.2 Linear friction stir welding 7.1.2.1 The linear friction stir welding process 7.1.2.2 Application of linear friction stir welding 7.1.2.3 Variants of the linear friction stir welding technique 7.1.3 Friction stir spot welding 7.1.3.1 The friction stir spot welding technique 7.1.3.2 Further developments of the friction stir spot welding technique 7.1.4 Friction stud welding 7.1.5 Friction element welding 7.2 Pressure welding processes 7.2.1 Contact and cold pressure welding 7.2.2 Diffusion and hot pressure welding 7.2.3 Explosion welding 7.2.4 Electromagnetic pulse welding 7.2.5 Roll bonding 7.2.6 Co-extrusion welding 7.3 Ultrasonic welding Version 2015 ©European Aluminium Association ([email protected]) 1 7.0 Introduction Solid-state welding describes a group of joining techniques which produces coalescence at temperatures below the melting point of the parent materials without the addition of third material. External pressure and relative movement may or may not be used to enhance the joining process. This group of joining techniques includes e.g. friction (stir) welding, cold pressure welding, diffusion welding, explosion welding, electromagnetic pulse welding, , and ultrasonic welding. -
The Use of Friction Welding for Corrosion Control in the Offshore Oil and Gas Industry Proserv UK To: Icorr, Aberdeen Branch 27.01.2015
The Use of Friction Welding for Corrosion Control in the Offshore Oil and Gas Industry Proserv UK To: Icorr, Aberdeen Branch 27.01.2015 Dave Gibson - Technical Authority, Friction Welding [email protected] Our Evolution What We Do: Life of Field Services Business Division What We Offer Solutions & Services • BOP Services Drilling Control Products and services • Drilling Control Systems Assurance & Performance Systems (DCS) focussed on operational • After-market & Lifecycle Management assurance Production Equipment Products and services • Flow Assurance & Sampling Solutions Systems (PES) focussed on production • Production Control & Safety Solutions optimisation • Asset Performance & Operational Integrity Products, services and • Subsea Marginal Field Development Subsea Production system design focused on • Subsea Brownfield Extension, Upgrade & Optimisation Systems (SPS) production enhancement • Obsolescence Management • Subsea Life of Field Services & Support • Subsea Infrastructure, Repair & Maintenance Products and services • Emergency Pipeline Repair Marine Technology focused on intervention and • Diverless Intervention Services (MTS) remediation to assure asset • Wellhead Abandonment & Decommissioning integrity • Friction Welding Summary 1. Why use Friction Welding Chosen for Corrosion Control ? 2. The Portable Friction Welding Process 3. Fatigue Strength of Friction Welds 4. Subsea Friction Welding Tooling 5. Subsea applications of Friction Welding for Cathodic Protection 6. Topside friction welding tooling 7. Topside applications of Friction welding for corrosion control 8. Corrosion Sensor Attachment Why is Friction Welding Chosen for Corrosion Control? Subsea • Welded, low electrical resistance, low maintenance connection • Suitable for large flat surfaces where clamps can’t be used (e.g. FPSO hulls, large diameter jacket legs and wind farm piles) • Better fatigue strength than arc welds in the “as welded” condition • When used with an ROV lower vessel costs and rapid installation. -
MSL Engineering Limited Platinum Blue House 1St Floor, 18 the Avenue Egham, Surrey, TW20 9AB
SMR Final Report 121404 Purpose of Issue Rev Date of Issue Author Agreed Approved Issued for information 0 Aug 2004 SM Issued for internal comment 1 November 2004 AFD DJM JB Issued as Final Report 2 December 2004 AFD DJM JB This Final report has been reviewed and approved by the Mineral Management Service. Approval does not signify that the contents necessarily reflect the views and policies of the Service, nor does mention of trade names or commercial products constitute endorsement or recommendation for use. This study was funded by the Mineral Management Service, U.S. Department of the Interior, Washington, D.C., under Contract Number 1435-01-04-CT-35320 ASSESSMENT OF REPAIR TECHNIQUES FOR AGEING OR DAMAGED STRUCTURES Project #502 DOC REF C357R001 Rev 1 NOV 2004 MSL Engineering Limited Platinum Blue House 1st Floor, 18 The Avenue Egham, Surrey, TW20 9AB Tel: +44 (0)1784 439194 Fax: +44 (0)1784 439198 E-mail: [email protected] C357R001Rev 2, December 2004 MMS Project #502 NUMBER DETAILS OF REVISION 0 Issued for information, August 2004 1 Issued for comment, November 2004. Extensive revisions throughout, including restructuring of report. 2 Issued as Final Report, December 2004. Conversion table added, Figure showing clamp details to avoid added, and general editorial revisions. C357R001Rev 2, December 2004 MMS Project #502 Assessment of Repair Techniques for Ageing or Damaged Structures By Dr. Adrian F Dier MSL Services Corporation Final Project Report: ASSESSMENT OF REPAIR TECHNIQUES FOR AGEING OR DAMAGED STRUCTURES MMS Project Number 502 November 2004 C357R001Rev 2, December 2004 i This Final report has been reviewed a nd approved by the Mineral Management Service. -
Experimental Investigation of Ti-6Al-4V Titanium Alloy and 304L
HOSTED BY Available online at www.sciencedirect.com ScienceDirect Defence Technology 11 (2015) 65e75 www.elsevier.com/locate/dt Experimental investigation of Tie6Ale4V titanium alloy and 304L stainless steel friction welded with copper interlayer R. KUMAR a,*, M. BALASUBRAMANIAN b a Mechanical Engineering, SKP Institute of Technology, Tiruvannamalai, Tamilnadu 606611, India b RMK College of Engineering and Technology, Tiruvallur, Tamilnadu 601206, India Received 3 August 2014; revised 28 September 2014; accepted 17 October 2014 Available online 5 January 2015 Abstract The basic principle of friction welding is intermetallic bonding at the stage of super plasticity attained with self-generating heat due to friction and finishing at upset pressure. Now the dissimilar metal joints are especially popular in defense, aerospace, automobile, bio-medical, refinery and nuclear engineerings. In friction welding, some special alloys with dual phase are not joined successfully due to poor bonding strength. The alloy surfaces after bonding also have metallurgical changes in the line of interfacing. The reported research work in this area is scanty. Although the sound weld zone of direct bonding between Tie6Ale4V and SS304L was obtained though many trials, the joint was not successful. In this paper, the friction welding characteristics between Tie6Ale4V and SS304L into which pure oxygen free copper (OFC) was introduced as interlayer were investigated. BoxeBehnken design was used to minimize the number of experiments to be performed. The weld joint was analyzed for its mechanical strength. The highest tensile strength between Tie6Ale4V and SS304L between which pure copper was used as insert metal was acquired. Micro-structural analysis and elemental analysis were carried out by EDS, and the formation of intermetallic compound at the interface was identified by XRD analysis. -
Welding Titanium a Designers and Users Handbook Tig the Titanium Information Group
- Guide to best practice - WELDING TITANIUM A DESIGNERS AND USERS HANDBOOK TIG THE TITANIUM INFORMATION GROUP WORLD CENTRE FOR MATERIALS JOINING TECHNOLOGY Electronic copyright in this document as follows: Copyright TWI and the Titanium Information Group, 1999 £25.00 TITANIUM INFORMATION GROUP The TITANIUM INFORMATION GROUP, (TIG) is an association of European suppliers, design engineers, and fabricators of titanium formed with the intention of promoting the use of titanium. The aim of the Group is to influence the initial selection of materials so that titanium is given the consideration merited by its unique combination of physical and mechanical properties, outstanding resistance to corrosion and cost effectiveness in a wide range of demanding applications. Regular publications and literature available from the Group present detailed and up-to-date technical and commercial information to materials engineers, plant and equipment designers and buyers, and provide the answers to everyday questions about cost, availability, fabrication and use of titanium and its alloys. Members of the Group are available to give presentations about titanium on either general or specific topics to companies or at seminars. A list of member companies of TIG appears on pages 32 and 33 Copies of the TIG video, ‘Titanium Today’ and the data diskette ‘Titanium and Its Alloys’ are available for use in educational and training establishments to provide an introduction to the metal its applications and properties. Further information on TIG publications can be found on the web: www.titaniuminfogroup.co.uk TWI TWI is based at Abington, near Cambridge, UK and is one of Europe’s largest independent contract research and technology organisations. -
Chapter 6 Arc Welding
Revised Edition: 2016 ISBN 978-1-283-49257-7 © All rights reserved. Published by: Research World 48 West 48 Street, Suite 1116, New York, NY 10036, United States Email: [email protected] Table of Contents Chapter 1 - Welding Chapter 2 - Fabrication (Metal) Chapter 3 - Electron Beam Welding and Friction Welding Chapter 4 - Oxy-Fuel Welding and Cutting Chapter 5 - Electric Resistance Welding Chapter 6 - Arc Welding Chapter 7 - Plastic Welding Chapter 8 - Nondestructive Testing Chapter 9 - Ultrasonic Welding Chapter 10 - Welding Defect Chapter 11 - Hyperbaric Welding and Orbital Welding Chapter 12 - Friction Stud Welding Chapter 13 WT- Welding Joints ________________________WORLD TECHNOLOGIES________________________ Chapter 1 Welding WT Gas metal arc welding ________________________WORLD TECHNOLOGIES________________________ Welding is a fabrication or sculptural process that joins materials, usually metals or thermoplastics, by causing coalescence. This is often done by melting the workpieces and adding a filler material to form a pool of molten material (the weld pool) that cools to become a strong joint, with pressure sometimes used in conjunction with heat, or by itself, to produce the weld. This is in contrast with soldering and brazing, which involve melting a lower-melting-point material between the workpieces to form a bond between them, without melting the workpieces. Many different energy sources can be used for welding, including a gas flame, an electric arc, a laser, an electron beam, friction, and ultrasound. While often an industrial process, welding can be done in many different environments, including open air, under water and in outer space. Regardless of location, welding remains dangerous, and precautions are taken to avoid burns, electric shock, eye damage, poisonous fumes, and overexposure to ultraviolet light. -
Friction Surfacing of Stainless Steel on Mild Steel with a Robot
Friction Surfacing of Stainless Steel on Mild Steel with a Robot Annemiek van Kalken MSc Thesis Delft University of Technology Laboratory of Material Science and Engineering Section: Welding Technology and Non-destructive Testing Supervisors: Dr. Ir. M.J.M. Hermans Dipl. Ing. A. Meyer (GKSS, Forschungszentrum Geesthacht, Germany) Prof. Dr. G. den Ouden Dr. J.F. dos Santos (GKSS, Forschungszentrum Geesthacht, Germany) CONTENTS 1 INTRODUCTION ............................................................................................................................... 2 2 FRICTION SURFACING - REVIEW .................................................................................................. 4 2.1 THE FRICTION SURFACING PROCESS ................................................................................................ 4 2.2 PROCESS PARAMETERS ................................................................................................................... 5 2.2.1 Effect of Surfacing Parameters on Process Behaviour ........................................................ 6 2.3 PROCESS CHARACTERISTICS ........................................................................................................... 8 2.4 CHARACTERISTICS OF THE DEPOSITED LAYER ................................................................................. 11 2.4.1 Layer Dimensions ............................................................................................................... 11 2.4.2 Hardness ............................................................................................................................ -
Friction Welding
Capability Presentation Friction Welding Stephen Booth Product Manager Overview 120 45% Proserv has executed over 120 projects Friction welding is 45% lower in cost globally using friction welding technology. than traditional electric arc welding. 30 430 We have 30 years experience in the For the Sheringham Shoal development of friction welding windfarm project, our technology performed 430 welds. 1470m 1 Our technology has operated in Proserv is the market leader in the depths up to 1470m. provision of friction welding services – the only provider to offer a subsea solution. Overview Proserv is a global market-leader in the provision of friction welding technology solutions, a unique process for maintaining the integrity of assets in explosive atmospheres and subsea environments. With a proven track record, and due to the significant cost and operational efficiencies it offers over more traditional methods, friction welding has become an essential part of many asset owners corrosion and integrity management programmes. Friction Welding Process What is Friction Welding? Friction welding is a form of solid phase welding e.g. when a blacksmith puts two pieces of metal into a furnace, heats them up until they are glowing hot then places them together onto an anvil before striking them with a hammer 1. Rotate the stud at high speed 2. Apply pressure forcing the stud onto the substrate 3. Friction between the stud tip and the substrate causes the metal surfaces to heat and a thin layer of metal to flow plastically under pressure (without melting) to the periphery of the weld, removing impurities from the interface 4. -
Comparison of Friction Welding Technologies
IJISET - International Journal of Innovative Science, Engineering & Technology, Vol. 2 Issue 12, December 2015. www.ijiset.com ISSN 2348 – 7968 Comparison of Friction Welding Technologies D. Rakesh Raghavendra1, Dr.Sethuram2.Dr.V.P.Raghupathy3 1 student at pes institute of technology, ([email protected]) 2 professor at pes institute of technology,([email protected]) 3 professor at pes institute of technology. PES Institute Of Technology, Bengaluru Abstract such as what are the friction welding parameters that govern effective coalescence have to be arrived Linear friction welding is a solid state joining at. These require elaborate computations of the process in which a joint between two metals can be parameter ranges that have to be set in the machine. formed through the contact of a plasticised layer at One also should understand the consequences of the interface of the adjoining specimens. This welding outside the range in each parameter. plasticised layer is created through a combination of frictional heating, which occurs as a result of After going through the science and engineering pushing a stationary work piece against one that is aspects, it is imperative to have a thorough moving, in a linear reciprocating manner, and knowledge of different types of friction welding applied force. The process is currently employed as technologies and where these can be applied. Each a niche technology for the fabrication of titanium type of technology is unique and require an in-depth alloy bladed disk (blisk) assemblies in aero- study of the benefits and limitations of each so that engines,. However, interest is growing in utilising best results can be obtained. -
Joining of Hybrid AA6063-6Sicp-3Grp Composite and AISI 1030 Steel by Friction Welding
Accepted Manuscript Joining of hybrid AA6063-6SiCp-3Grp composite and AISI 1030 steel by friction welding N. Rajesh Jesudoss Hynes, Associate Professor, M. Vivek Prabhu, Assistant Professor, P. Nagaraj, Senior Professor PII: S2214-9147(16)30162-3 DOI: 10.1016/j.dt.2017.05.014 Reference: DT 251 To appear in: Defence Technology Received Date: 26 December 2016 Revised Date: 5 May 2017 Accepted Date: 24 May 2017 Please cite this article as: Rajesh Jesudoss Hynes N, Vivek Prabhu M, Nagaraj P, Joining of hybrid AA6063-6SiCp-3Grp composite and AISI 1030 steel by friction welding, Defence Technology (2017), doi: 10.1016/j.dt.2017.05.014. This is a PDF file of an unedited manuscript that has been accepted for publication. As a service to our customers we are providing this early version of the manuscript. The manuscript will undergo copyediting, typesetting, and review of the resulting proof before it is published in its final form. Please note that during the production process errors may be discovered which could affect the content, and all legal disclaimers that apply to the journal pertain. ACCEPTED MANUSCRIPT Joining of Hybrid AA6063-6SiC p-3Gr pComposite and AISI 1030 steel by Friction Welding N.Rajesh Jesudoss Hynes 1*, M. Vivek Prabhu 2, P.Nagaraj 3 1* Associate Professor, Department of Mechanical Engineering, Mepco Schlenk Engineering College, Sivakasi, Tamilnadu, India-626005. 2Assistant Professor, Department of Mechanical Engineering, Velammal College of Engineering and Technology,Madurai – 625009 3Senior Professor, Department of Mechanical Engineering, Mepco Schlenk Engineering College, Sivakasi, Tamilnadu, India-626005. Email Id: [email protected] , [email protected] , [email protected] MANUSCRIPT ABSTRACT Joining of metals and aluminium hybrid metal matrix composites has significant applications in aviation, ship building and automotive industries. -
An Investigation Into the Friction Stir Welding of Aluminium Pipe with Stainless Steel Plate
AN INVESTIGATION INTO THE FRICTION STIR WELDING OF ALUMINIUM PIPE WITH STAINLESS STEEL PLATE A THESIS SUBMITTED IN PARTIAL FULFILMENT OF THE REQUIREMENTS FOR THE DEGREE OF Bachelor of Technology In Mechanical Engineering By SATYA PRAKASH PRADHAN 108ME049 Under the Guidance of Dr. C.K.BISWAS Department of Mechanical Engineering National Institute of Technology Rourkela 2012 AN INVESTIGATION INTO THE FRICTION STIR WELDING OF ALUMINIUM PIPE WITH STAINLESS STEEL PLATE A THESIS SUBMITTED IN PARTIAL FULFILMENT OF THE REQUIREMENTS FOR THE DEGREE OF Bachelor of Technology In Mechanical Engineering By SATYA PRAKASH PRADHAN 108ME049 Under the Guidance of Dr. C.K.BISWAS Department of Mechanical Engineering National Institute of Technology Rourkela 2012 National Institute of Technology Rourkela CERTIFICATE This is to certify that thesis entitled, “AN INVESTIGATION INTO THE FRICTION STIR WELDING OF ALUMINIUM PIPE WITH STAINLESS STEEL PLATE” submitted by Mr. SATYA PRAKASH PRADHAN in partial fulfillment of the requirements for the award of Bachelor of Technology Degree in Mechanical Engineering at National Institute of Technology, Rourkela is an authentic work carried out by him under my supervision and guidance. To the best of my knowledge, the matter included in this thesis has not been submitted to any other university/ institute for award of any Degree or Diploma. Date: Dr. C.K.BISWAS Place: Dept. of Mechanical Engineering National Institute of Technology Rourkela-769008 ACKNOWLEDGEMENT I express my deep sense of gratitude and ardent indebtedness to my supervisor Prof C.K.Biswas, Associate Professor, Mechanical Engineering for his excellent guidance, consistent encouragement and constant supervision throughout the course of this work. -
Survey of Joining, Cutting, and Allied Processes
CHAPTER 1 Prepared by the Welding Handbook Chapter Committee SURVEY OF on Joining and Cutting Processes: W. H. Kielhorn, Chair JOINING, LeTourneau University Y. Adonyi LeTourneau University CUTTING, R. L. Holdren Edison Welding Institute R. C. Horrocks, Sr. AND ALLIED Springfield & Clark Company N. E. Nissley PROCESSES The Ohio State University Welding Handbook Volume 1 Committee Member: T. D. Hesse Technical Welding Service Contents Introduction 2 Joining Processes 3 Cutting Processes 42 Thermal Spraying 47 Conclusion 49 Bibliography 49 Supplementary Reading List 50 2 SURVEY OF JOINING, CUTTING, AND ALLIED PROCESSES CHAPTER 1 SURVEY OF JOINING, CUTTING, AND ALLIED PROCESSES INTRODUCTION This chapter introduces the conventional and more spraying processes,1 the reader is encouraged to con- widely known joining, cutting, and thermal spraying duct a thorough investigation of the processes that processes. The distinguishing features of the various appear to have the best potential for the intended appli- processes are summarized and compared to one cations. This investigation should take into account another. Among the joining processes reviewed are the safety and health considerations such as those presented arc, resistance, and solid-state welding processes as well in the American National Standard Safety in Welding, as brazing, soldering, and adhesive bonding. The cut- Cutting, and Allied Processes, ANSI Z49.1,2, 3 and the ting processes examined include thermal and non- information provided in the manufacturers’ material thermal methods. The thermal spraying processes safety data sheets (MSDSs). Additional sources of infor- considered include flame and plasma arc spraying as mation about the joining, cutting, and allied processes well as arc and detonation flame spraying.