Powder Build-Up in Detergent Packing Lines
Total Page:16
File Type:pdf, Size:1020Kb
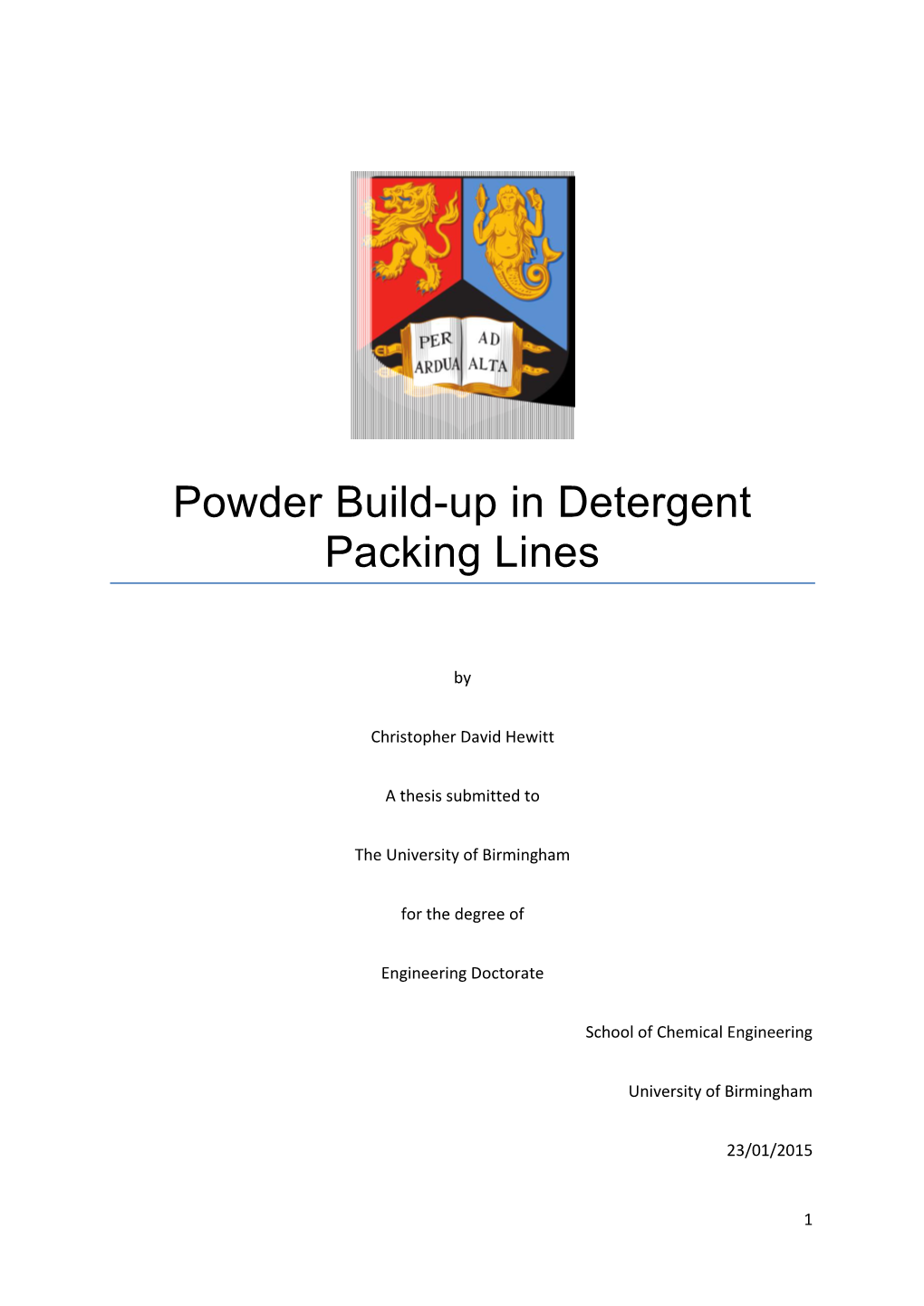
Load more
Recommended publications
-
MG HE Liquid Laundry Is Specially Formulated for Front Load High Efficiency Washing Machines
MGMG HEHE LiquidLiquid LaundryLaundry Highly-Effective Laundry Detergent MG HE Liquid Laundry is specially formulated for front load high efficiency washing machines. Standard detergents can cause over-sudsing when less water is used, and using less detergent sacrifices cleaning power. MG HE Liquid Laundry provides excellent cleaning with optimal level of sudsing. It is specifically formulated with powerful ingredients to suspend more significant levels of soil. This helps leave your clothes looking bright. • Controlled Foam • Effective in Hard Water • Effective in Cold or Hot Water • Removes Oils, Grease & Fat • Prevents Soil Re-deposition • Easy Rinsing Usage Directions: Sort laundry into similar color, type of fabric and soil condition. When laundering items for the first time, test for colorfastness in a solution of laundry detergent and cold water. Add 2 - 8 ounces of MG HE Liquid Laundry per 100-pound load as the washing machine is filling with water. Clothing and machine manufacturer’s instructions should always take precedence over these recommendations. If desired, MG ChlorSan bleach may be added approximately two minutes after wash cycle begins or MG 7% Fabric Softener may be added to the final rinse. Quantity of MG HE Liquid Laundry used will vary depending on local water conditions, water temperature selected and the amount and type of soils to be removed. Cold water rinsing is recommended for all wash loads. Safety & Hazards MG HE Liquid Laundry Dilution Guidelines Usage Dilution Whites Colorfast Fabrics & 2-8 Oz / 100 Lb Load (Hot Heavy Soils Water) Wear Protective Eye Glasses and Chemical-Resistant Gloves While Using MG HE Liquid Laundry Permanent Press & Special 2-8 Oz / 100 Lb Load (Warm Care Fabrics Water Consult SDS for Further Safety Precautions Colored or Sensitive Fabrics 2-8 Oz / 100 Lb Load (Cold DOT Shipping Name: Not Regulated. -
Revision of Ecolabel Criteria for Laundry Detergents 2008-2010
European Ecolabel ENV.G.2/SER2007/0073rl Commission Decision of 28 April 2011 Revision of Ecolabel Criteria for Laundry Detergents 2008-2010 Background report Prepared by Ecolabelling Denmark This document was last updated February 2011 INDEX 1. SUMMARY ....................................................................... 2 2. MARKET REVIEW ............................................................. 4 2.1. EUROPEAN MARKET FOR LAUNDRY DETERGENTS AND ADDITIVES .................................... 4 2.1.1. Laundry detergents .............................................................................................. 4 2.1.2. Fabric softeners ..................................................................................................... 5 2.1.3. Stain Removers ...................................................................................................... 6 2.2. WASHING HABITS IN EUROPE ............................................................................................. 6 2.3. ECOLABEL LICENSES AND PRODUCTS TODAY ..................................................................... 6 3. PRODUCT GROUP DEFINITION ........................................ 8 4. INTRODUCTION TO REVISED ECOLABEL CRITERIA ....... 10 5. REVISED ECOLABEL CRITERIA ...................................... 13 5.1. REVISED CRITERIA ............................................................................................................. 13 5.1.1. General remarks ................................................................................................. -
CHEMICALS Laundry Detergent/Bleach
Laundry Detergent/Bleach A A. INSTITUTIONAL HEAVY-DUTY DETERGENT CCP A concentrated blend of cleaning agents which will emulsify grease and dirt in either hard or soft water with excellent results. This synthetic detergent formula contains water softening, fabric brighteners, grease emulsifiers and soil suspending agents. 27600119 P550262 50 lb. 1/bx. B. ALL® POWDER LAUNDRY DETERGENT JOHNSON DIVERSEY ALL uses Stainlifters™ to safely lift dirt and stains. All Ultra® Powder Laundry Detergent 15200115 2979267 (100) 2 oz. Box 100/cs. B 15200176 2979304 150 Use 1/ea. All® Concentrated Powder Laundry Detergent 15200112 2979216 50 lb. Concentrated 1/ea. C C. SURF ULTRA® POWDER JOHNSON DIVERSEY LAUNDRY DETERGENT Surf® with Active Oxygen formula lifts dirt and odors while leaving laundry smelling fresh. 15200158 2979814 2 oz. 100/cs. D. TIDE® POWDER LAUNDRY DETERGENT PROCTER & GAMBLE Tide with bleach cleans so well…it’s the only detergent that kills 99.9% of bacteria, including Staphylococcus Aureus, Klebsiella Pneumoniae, E. coli and Salmonella Choleraesuis. Use D one full scoop as directed. Contains a unique activated bleaching system. Removes many tough stains and whitens whites. Helps keep colors bright. Non-phosphate. Harmless to septic tanks. EPA Registration No. 3573-56. 16902370 32370 33 oz. 15/cs. CHEMICALS w/Bleach Contains a unique active bleaching system. Removes many tough stains and whitens whites. Helps keep colors bright. No phosphate. Harmless to septic tanks. Kills 99.9% of bacteria (effective against Staphylococcus Aurius and Klebsiella Pneumoniae; use as directed). 16901801 02370 4 oz. 100/cs. 16900095 40026 8 oz. 14/cs. 16907330 84907330 33 oz. -
Second Time Moms & the Truth About Parenting
Second Time Moms & The Truth About Parenting Summary Why does our case deserve an award? In the US, and globally, every diaper brand obsesses about the emotion and joy experienced by new parents. Luvs took the brave decision to focus exclusively on an audience that nobody was talking to: second time moms. Planning made Luvs the official diaper brand of experienced moms. The depth of insights Planning uncovered about this target led to creative work that did a very rare thing for the diaper category: it was funny, entertaining and sparked a record amount of debate. For the first time these moms felt that someone was finally standing up for them and Luvs was applauded for not being afraid to show motherhood in a more realistic way. And in doing so, we achieved the highest volume and value sales in the brand’s history. 2 Luvs: A Challenger Facing A Challenge Luvs is a value priced diaper brand that ranks a distant fourth in terms of value share within the US diaper category at 8.9%. Pampers and Huggies are both premium priced diapers that make up most of the category, with value share at 31, and 41 respectively. Private Label is the third biggest player with 19% value share. We needed to generate awareness to drive trial for Luvs in order to grow the brand, but a few things stood in our way. Low Share Of Voice Huggies spends $54 million on advertising and Pampers spends $48 million. In comparison, Luvs spends only $9 million in media support. So the two dominant diaper brands outspend us 9 to 1, making our goal of increased awareness very challenging. -
Dry Cleaning Calculator Guide
Guide to calculations for ChemTRAC reporting: Dry cleaning facilities Version 1.1 February 2013 Contents How do I use this guide? Part 1 of this guide will help you understand the ChemTRAC program, collect information about your facility, use the ChemTRAC calculator for dry cleaning facilities, and report to ChemTRAC, if needed. Part 2 of this guide will help you reduce your facility’s environmental impact. The Appendices provide additional information about emissions calculations. Part 1: Gathering data, using the calculator, and reporting to ChemTRAC Introduction to the ChemTRAC program ............................................................ 1 The Dry Cleaning Sector ................................................................................... 2 Identifying ChemTRAC substances in dry cleaning facilities .............................. 3 Calculating emissions ........................................................................................ 6 Worksheets for collecting information ................................................................ 7 Interpreting results........................................................................................... 22 Reporting to ChemTRAC ................................................................................. 24 Part 2: Reducing your facility’s environmental impact Pollution prevention strategies ......................................................................... 31 Control technologies for reducing emissions................................................... -
Pediatric Exposure to Laundry Detergent Pods Abstract
ARTICLE Pediatric Exposure to Laundry Detergent Pods AUTHORS: Amanda L. Valdez, BS,a,b Marcel J. Casavant, WHAT’S KNOWN ON THIS SUBJECT: Case studies, abstracts, and MD,c,d Henry A. Spiller, MS, D.ABAT,c,d Thiphalak small-sample research studies have shown that laundry Chounthirath, MS,a Huiyun Xiang, MD, MPH, PhD,a,d and detergent pods pose important poisoning risks to young children. Gary A. Smith, MD, DrPHa,d,e aCenter for Injury Research and Policy at Nationwide Children’s WHAT THIS STUDY ADDS: From 2012 through 2013, 17 230 Hospital, Columbus, Ohio; bUniversity of Washington School of children exposed to laundry detergent pods were reported to US c Medicine, Seattle, Washington; Central Ohio Poison Center, poison control centers. Among children exposed, 4.4% were Columbus, Ohio; dThe Ohio State University College of Medicine, Columbus, Ohio; and eChild Injury Prevention Alliance, Columbus, hospitalized and 7.5% experienced a moderate or major medical Ohio outcome, including 1 confirmed death. KEY WORDS detergent pod, ingestion, NPDS, poisoning, poison control center ABBREVIATIONS AAPCC—American Association of Poison Control Centers NPDS—National Poison Data System abstract PCC—Poison Control Center OBJECTIVE: Mrs Valdez conducted the data analysis, and drafted and revised Laundry detergent pods are a new product in the US mar- the manuscript; Dr Casavant contributed to conceptualization of ketplace. This study investigates the epidemiologic characteristics and the study, assisted in data access and analysis, and critically outcomes of laundry detergent pod exposures among young children in reviewed the manuscript; Drs Spiller and Xiang contributed to the United States. -
Tackling Your Laundry: Let’S Talk Products! Welcome to the Ever Changing World of Laundry Detergents, Stain Removal Products, Fabric Softeners and Dryer Sheets
FRM-AP.017 Tackling Your Laundry: Let’s talk products! Welcome to the ever changing world of laundry detergents, stain removal products, fabric softeners and dryer sheets. Some of today’s choices can become overwhelming. Whatever the product choice, the information in this There are publication should help you keep your laundry room safe. three types of energy Choosing the right laundry detergent Laundry detergents come in many forms, each having its own benefits. needed for Select the form that meets your specific need. good cleaning General purpose detergents Full-strength detergents can be used with many types of fabrics/textiles. results: These products include: Chemical — • High Efficiency (HE) detergents provided by • Ultra detergents detergents • Single-use detergents (pods) and laundry • Fragrance or dye-free detergents • Bar soap aids; • Combination detergents Thermal — provided by Light duty detergents These detergents can be used when washing fabrics by hand or in your the water washing machine. They are used primarily for delicate fabrics, such as those temperature; requiring special care, or lightly-soiled items; ideal for hand washing baby Mechanical clothes. These products include: — provided • Liquid Detergents by the • Powdered Detergents machine agitation. All three need to be considered for best results! Liquid, powders and enzyme detergents Liquid detergents work at all temperatures and are easy to use for pretreating stains. Liquid detergents have an ingredient that helps soften hard water minerals. Ground in dirt and clay are best lifted from soiled laundry with powder detergents using warm to hot water. Protein and oil-based stains are best removed using enzyme detergents. -
Inspection Copy Inspection Copy
INSEAD Harv ard Business School Procter and Gamble Europe: Ariel Ultra’s Euroband Strategy INSPECTIONNot For Reproduction COPY 05/2000-4816 This case was written by Professor Christopher A. Bartlett at Harvard Business School, Ph.D. candidate Alice de Koning at INSEAD, and Professor Paul Verdin Affiliate Professor at INSEAD and at Catholic University of Leuven as the basis for class discussion rather than to illustrate either effective or ineffective handling of an administrative situation. Copyright © 1999 INSEAD-HBS, France-USA. N.B. PLEASE NOTE THAT DETAILS OF ORDERING INSEAD CASES ARE FOUND ON THE BACK COVER. COPIES MAY NOT BE MADE WITHOUT PERMISSION. INSPECTIONNot For Reproduction COPY Harvard Business School INSEAD 1 One Sunday night in July of 1989, Claude Meyer and his delivery team for Ariel Ultra were on a train speeding from Brussels to Paris. They had spent 18 months developing P&G’s first compact laundry detergent for the European market, and now, as they were finalizing the details of a meticulously planned pan-European launch, they learned that Unilever was about to launch a similar product in France—two months ahead of P&G. Meyer, European Regional Vice President for laundry products, and his team were brainstorming responses to their longtime rival’s pricing tactics, package sizes, and a premium-niche marketing strategy, all of which differed significantly from P&G’s European plan. As the train sped towards Paris, they debated whether to change their approach to the French market to meet Unilever’s challenge, or continue with their original intention to implement a consistent Europe-wide strategy. -
Propylene Glycol
PROPYLENE GLYCOL Your patch test result indicates that you have a contact allergy to propylene glycol. This contact allergy may cause your skin to react when it is exposed to this substance although it may take several days for the symptoms to appear. Typical symptoms include redness, swelling, itching, and fluid-filled blisters. Where is propylene glycol found? Propylene glycol is used as a softening agent, preservative, humectants, and solvent in cosmetics, fragrances, topical medications, soaps and cleansers, hair care products, and deodorants. Propylene glycol is also found in oral treatments as well as many foods. It is also added during the manufacture of many industrial fluids, such as solvents, thinners, antifreeze, other de-icing fluids, desiccants, brake fluids, and polyester resins. How can you avoid contact with propylene glycol? Avoid products that list any of the following names in the ingredients: • Propylene glycol • 1,2-Dihydroxypropane • CASRN: 57-55-6 • Methylethyl glycol • 1,2-Propanediol • 2-Hydroxypropanol • Isopropylene glycol What are some products that may contain propylene glycol? Antiperspirants and Deodorants: • Old Spice High Endurance • Meguiars Vinyl/Rubber Cleaner/Condition • Adidas 24 Hour Deodorant Control Antiperspirant & Deodorant • Pennzoil Roadside Fix A Flat Tire Sealant & • Adidas 24 Hour Fragrance Clear Stick • Old Spice High Endurance Deodorant Flat Preventative Deodorant • Old Spice Red Zone Clear Gel • Rain-X De-Icer (Aerosol) • Adidas Action 3 Tech F • Old Spice Red Zone Deodorant Stick • Slime -
Wog Laundry Tips & Tricks
WOMEN OF GOLD: PRE-WASH LAUNDRY TIPS & TRICKS STAINS? Oil stains: Blue Dawn dish soap + scrub with a toothbrush (or other brush). Wait a few hours and then toss in the washer. Other stains (food, grass, etc.): Option 1: Bleach (e.g. OxiClean, Clorox, etc.) | Option 2: Bleach-free (e.g. Tide-to-go pen) Option 3: 1 part blue Dawn dish soap + 2 parts hydrogen peroxide. Pour mixture onto stain. Add baking soda for extra scrubbing element. Let it sit for an hour or so, and then toss in the washer. | Option 4: Natural (e.g. Puracy Natural Stain Remover) SORTING LAUNDRY By texture and/or fabric type and soil level: Cotton w/normal soil level, cotton w/heavy soil level Heavy pile: Jeans, thick fleece, etc. Towels, wash cloths, bedding, etc. TIP: Towel terry cloth is abrasive and thick, which agitates clothing fibers and creates pilling). Separate towels from clothing. By color: It’s really only for if you're trying to avoid dye transfer issues. Pre-treat and set the dyes by soaking the article of clothing for 30 minutes in water + ½ cup of vinegar + 2 tsp salt. OTHER MISC. TIPS Check pockets for coins, metal objects, pens, receipts, etc. to avoid washer damage. Flip clothes inside out (cleaner wash and keeps clothing newer longer) Tie hoodie strings to avoid slipping out. If clothes are smelly (from working out, sweating, etc.), use 1 part vinegar + 4 parts water and soak for half an hour WOMEN OF GOLD: WASH LAUNDRY TIPS & TRICKS DON'T OVERSTUFF! Clothes won't have room to "agitate" = clothes won't be as clean. -
Color Safe Bleach
Color Safe Bleach Clothesline Fresh Color Safe Bleach is a non-chlorinated, oxygen-based bleach that enhances the performance of Clothesline Fresh Laundry Detergents. Clothesline Fresh Color Safe Bleach is safe to use on most all machine-washable fabrics and colors, yet powerful enough to remove even the toughest stains. Providing Quality Maintenance and Chemical Specialty Solutions with Unparalleled Customer Service Spartan Chemical Company, Inc. 1110 Spartan Drive Maumee, OH 43537 1-800-537-8990 www.spartanchemical.com CONTEMPORARY CLEANING As a Laundry Bleach: As a Laundry Stain Pre-Treatment: TECHNOLOGY: 1. Always read and follow care directions. 1. Apply a small amount of Clothesline Fresh Clothesline Fresh Color Safe Bleach 2. If the care label on a garment states “no Color Safe Bleach directly to the stain as was formulated in partnership with bleach,” do not attempt to use Clothesline soon as possible. the Environmental Protection Agency’s Design Fresh Color Safe Bleach without first 2. Gently rub the stain and allow Clothesline for the Environment Program. Clothesline testing an inconspicuous area on the garment. Fresh Color Safe Bleach to penetrate the Fresh Color Safe Bleach brightens colors 3. Sort laundry by color and fabric type. stain for 3 – 5 minutes. and whitens whites much more than using 4. From care directions, choose proper wash 3. Wash pre-treated garment immediately detergent alone. Clothesline Fresh Color Safe cycle and water temperature. using Clothesline Fresh Laundry Detergent Bleach is formulated with the power of active 5. Do not overload washer with soiled laundry. and Clothesline Fresh Color Safe Bleach. oxygen, an effective oxidizing agent, for superior 6. -
2.2.9. Procter & Gamble
1 Dirty recyclables of a Procter & Gamble brand Credit: Les Stone P&G has made no commitments regarding collection, and neither calls for legislation in this area nor mentions support for DRS. It high- lights different targets on its US environmental sustainability webpage6 than on its UK equivalent.7 At the time of writing, there was no reference to the development of reuse-and-refill delivery models for P&G products on their UK site;8 on its US site, however, the company highlights its 2019 participation in test programmes with TerraCycle’s Loop project in New York and Paris,9 in which its brands Pantene, Gillette and Venus were included.10 When it comes to reduction of virgin-plastic use, P&G states alternative materials will only be used ‘when it makes sense’, and that lightweighting, increasing recycled content and moving towards more concentrated products will take priority.11 However, this does not appear to involve an absolute reduction in the total number of single-use plastic-packaging units. It is also unclear what instances the company will consider using alternative materials in, and which types of materials. In another document on the company’s brand criteria for 2030, it states it will achieve ‘a meaningful increase in responsibly-sourced bio-based, or recycled or more resource efficient materi- als’;12 however, this commitment is nebulous because it does not include an actual target, timeframe or more detail on what ‘responsi- bly-sourced’ means. When it comes to minimum recycled content, P&G talks about ‘continuously innovating with recycled plastic’,13 and, according to As You Sow, has a recycled-content target of 8% for 2025.14 This is a very modest increase – from 6.3% in 2018.