ABSTRACT HATIBOGLU, BILGE. Mechanical Properties of Individual Polymeric Micro and Nano Fibers Using Atomic Force Microscopy
Total Page:16
File Type:pdf, Size:1020Kb
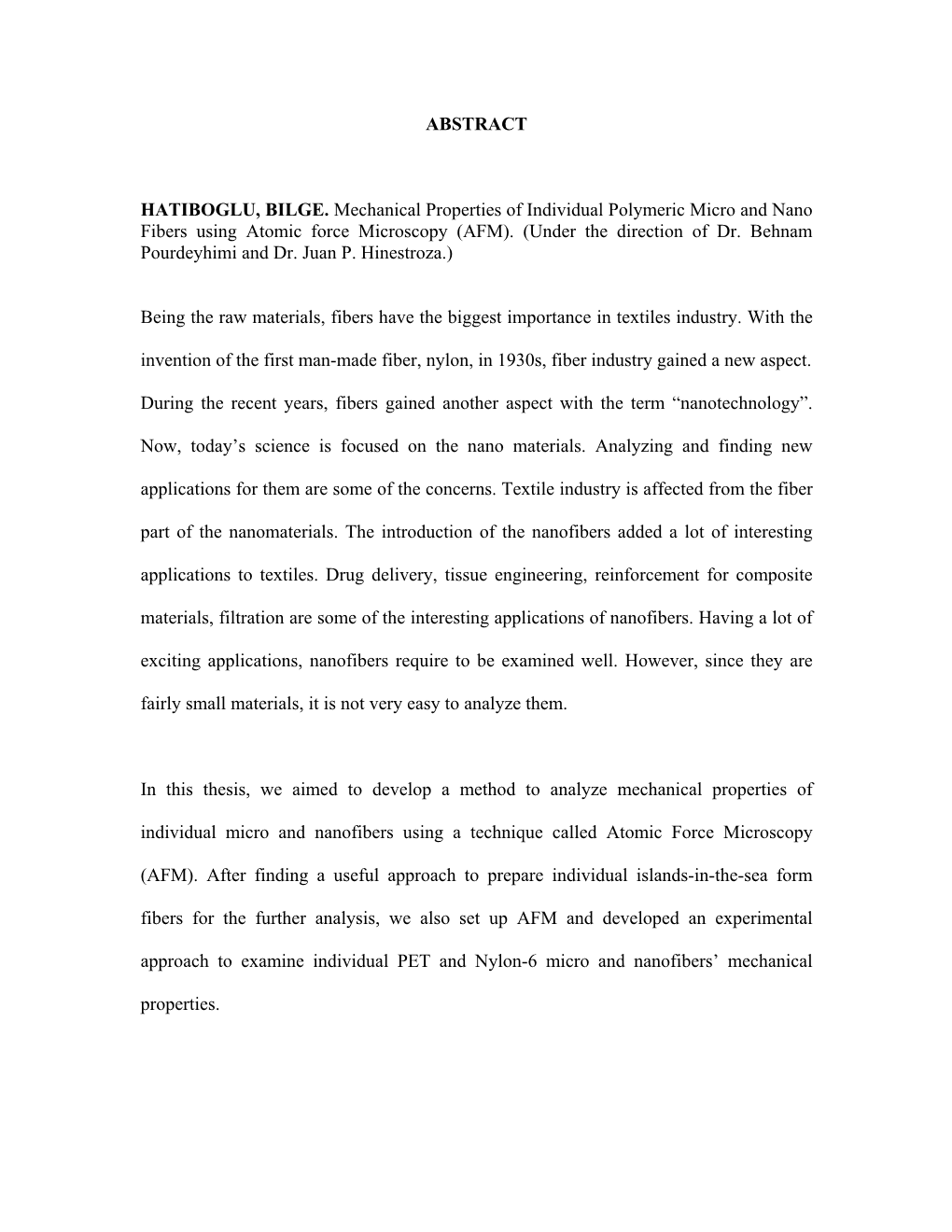
Load more
Recommended publications
-
Fronts in the World Ocean's Large Marine Ecosystems. ICES CM 2007
- 1 - This paper can be freely cited without prior reference to the authors International Council ICES CM 2007/D:21 for the Exploration Theme Session D: Comparative Marine Ecosystem of the Sea (ICES) Structure and Function: Descriptors and Characteristics Fronts in the World Ocean’s Large Marine Ecosystems Igor M. Belkin and Peter C. Cornillon Abstract. Oceanic fronts shape marine ecosystems; therefore front mapping and characterization is one of the most important aspects of physical oceanography. Here we report on the first effort to map and describe all major fronts in the World Ocean’s Large Marine Ecosystems (LMEs). Apart from a geographical review, these fronts are classified according to their origin and physical mechanisms that maintain them. This first-ever zero-order pattern of the LME fronts is based on a unique global frontal data base assembled at the University of Rhode Island. Thermal fronts were automatically derived from 12 years (1985-1996) of twice-daily satellite 9-km resolution global AVHRR SST fields with the Cayula-Cornillon front detection algorithm. These frontal maps serve as guidance in using hydrographic data to explore subsurface thermohaline fronts, whose surface thermal signatures have been mapped from space. Our most recent study of chlorophyll fronts in the Northwest Atlantic from high-resolution 1-km data (Belkin and O’Reilly, 2007) revealed a close spatial association between chlorophyll fronts and SST fronts, suggesting causative links between these two types of fronts. Keywords: Fronts; Large Marine Ecosystems; World Ocean; sea surface temperature. Igor M. Belkin: Graduate School of Oceanography, University of Rhode Island, 215 South Ferry Road, Narragansett, Rhode Island 02882, USA [tel.: +1 401 874 6533, fax: +1 874 6728, email: [email protected]]. -
Roy Staab Four Seasons / Four Corners
ROY STAAB FOUR SEASONS / CORNERS ROY STAAB FOUR SEASONS / CORNERS Institute of Visual Arts University of Wisconsin-Milwaukee July 10-September 27, 2009 with contributions by Suzaan Boettger Nicholas Frank John K. Grande Amy Lipton Institute of Visual Arts University of Wisconsin-Milwaukee July 10-September 27, 2009 Inova is grateful for the support of the Greater Milwaukee Foundation’s Mary L. Nohl Fund. Published by the University of Wisconsin-Milwaukee Peck School of the Arts on the occasion of the exhibition ROY STAAB: FOUR SEASONS/FOUR CORNERS Organized by the Institute of Visual Arts (Inova) P.O. Box 413 Milwaukee, WI 53201 Phone: (414) 229-4762 Fax: (414) 229-6154 arts.uwm.edu © 2009 by the Board of Regents of the University of Wisconsin System. All rights reserved. No part of the contents of this book may be produced without the written permission of the publisher. ISBN: 9780981930114 Printed in the United States of America All photographs of installations by Roy Staab except: Michel Goday, figs. 2, 9 Gregg Schmidts, fig. 17 Leonard Freed, fig. 23 Nicholas Frank, fig. 33 Alan Magayne-Roshak, fig. 34 Additional credits: cover: Pyramid Space 7 - August 24, 1988 fig. 16: Digital Image © The Museum of Modern Art/Licensed by SCALA/Art Resource, NY fig. 18: Collection of the Gemeente Museum Den Haag. 1 (opposite) Fluke, 2008, Marbaek Beach near Esbjerg, Denmark 2 Port-Vendres, France, 1979 5 X MARKS THE STAAB Anyone who knows Roy Staab has experienced the discrepancy between 3 Dennis Oppenheim his personality and his artwork. His temporary environmental site installations Cancelled Crop, 1969 are the embodiment of calm, humility and silence. -
The Logic of the Grail in Old French and Middle English Arthurian Romance
The Logic of the Grail in Old French and Middle English Arthurian Romance Submitted in part fulfilment of the degree of Doctor of Philosophy Martha Claire Baldon September 2017 Table of Contents Introduction ................................................................................................................................ 8 Introducing the Grail Quest ................................................................................................................ 9 The Grail Narratives ......................................................................................................................... 15 Grail Logic ........................................................................................................................................ 30 Medieval Forms of Argumentation .................................................................................................. 35 Literature Review ............................................................................................................................. 44 Narrative Structure and the Grail Texts ............................................................................................ 52 Conceptualising and Interpreting the Grail Quest ............................................................................ 64 Chapter I: Hermeneutic Progression: Sight, Knowledge, and Perception ............................... 78 Introduction ..................................................................................................................................... -
Artists and Exhibition Information
Artists and exhibition information Sculpture by the Sea Bondi 2019 Page 2 Introduction and key vocabulary Page 3 Looking and interpreting sculpture Artists and their Artworks: Page 4 Joel Adler | NSW Page 13 Jane Gillings | NSW Page 5 Sollai Cartwright | VIC Page 14 Luke Neil | VIC Page 6 Christine Simpson & Hirofumi Uchino | NSW Page 15 Rima Zabaneh & Bernice Rarig | WA Page 7 Maurizo Perron | ITALY Page 16 Britt Mikkelsen | WA Page 8 Naomi Taylor Royds | NSW Page 17 Pooza Kataria | NSW Page 9 Sallie Portnoy | NSW Page 18 Lea Kannar-Lichtenberger | NSW Page 10 Gabriella Boyd & Chloe Henry-Jones | NSW Page 19 Katie Stewart | NSW Page 11 Danai Nikolaidi Kotsaki | GREECE Page 20 Barbara Licha | NSW Page 12 Other Architects and Izabela Pluta | NSW Page 21 Succah by the Sea Education resources created and produced by Sculpture by the Sea with thanks to the exhibiting artists. KEY VOCABULARY 3 dimensional: A solid object that possesses height, width and depth, the object is not flat. Introduction to this resource Balance: The ways in which elements (line, shape, colour, texture, etc.) of a piece are arranged. Balance can be achieved when all elements of a piece are given equal ‘weight’ and are distributed Sculpture by the Sea Artists and Exhibition information has been equally around an imaginary middle line. developed to support primary and secondary teaching. The content can be applied across a range of learning settings, as a handout for Dimensions: Dimensions are the measurable qualities of an object, such as length, breadth, depth, or height. students and in conjunction with existing curriculum. -
Days & Hours for Social Distance Walking Visitor Guidelines Lynden
53 22 D 4 21 8 48 9 38 NORTH 41 3 C 33 34 E 32 46 47 24 45 26 28 14 52 37 12 25 11 19 7 36 20 10 35 2 PARKING 40 39 50 6 5 51 15 17 27 1 44 13 30 18 G 29 16 43 23 PARKING F GARDEN 31 EXIT ENTRANCE BROWN DEER ROAD Lynden Sculpture Garden Visitor Guidelines NO CLIMBING ON SCULPTURE 2145 W. Brown Deer Rd. Do not climb on the sculptures. They are works of art, just as you would find in an indoor art Milwaukee, WI 53217 museum, and are subject to the same issues of deterioration – and they endure the vagaries of our harsh climate. Many of the works have already spent nearly half a century outdoors 414-446-8794 and are quite fragile. Please be gentle with our art. LAKES & POND There is no wading, swimming or fishing allowed in the lakes or pond. Please do not throw For virtual tours of the anything into these bodies of water. VEGETATION & WILDLIFE sculpture collection and Please do not pick our flowers, fruits, or grasses, or climb the trees. We want every visitor to be able to enjoy the same views you have experienced. Protect our wildlife: do not feed, temporary installations, chase or touch fish, ducks, geese, frogs, turtles or other wildlife. visit: lynden.tours WEATHER All visitors must come inside immediately if there is any sign of lightning. PETS Pets are not allowed in the Lynden Sculpture Garden except on designated dog days. -
Artists and Exhibition Information
Artists and exhibition information Sculpture by the Sea Bondi 2019 Page 2 Introduction and key vocabulary Page 3 Looking and interpreting sculpture Artists and their Artworks: Page 4 Joel Adler | NSW Page 13 Jane Gillings | NSW Page 5 Sollai Cartwright | VIC Page 14 Luke Neil | VIC Page 6 Christine Simpson & Hirofumi Uchino | NSW Page 15 Rima Zabaneh & Bernice Rarig | WA Page 7 Maurizo Perron | ITALY Page 16 Britt Mikkelsen | WA Page 8 Naomi Taylor Royds | NSW Page 17 Pooza Kataria | NSW Page 9 Sallie Portnoy | NSW Page 18 Lea Kannar-Lichtenberger | NSW Page 10 Gabriella Boyd & Chloe Henry-Jones | NSW Page 19 Katie Stewart | NSW Page 11 Danai Nikolaidi Kotsaki | GREECE Page 20 Barbara Licha | NSW Page 12 Other Architects and Izabela Pluta | NSW Page 21 Succah by the Sea Education resources created and produced by Sculpture by the Sea with thanks to the exhibiting artists. KEY VOCABULARY 3 dimensional: A solid object that possesses height, width and depth, the object is not flat. Introduction to this resource Balance: The ways in which elements (line, shape, colour, texture, etc.) of a piece are arranged. Balance can be achieved when all elements of a piece are given equal ‘weight’ and are distributed Sculpture by the Sea Artists and Exhibition information has been equally around an imaginary middle line. developed to support primary and secondary teaching. The content can be applied across a range of learning settings, as a handout for Dimensions: Dimensions are the measurable qualities of an object, such as length, breadth, depth, or height. students and in conjunction with existing curriculum. -
Resonance & Grace
RESONANCE & GRACE Ceramics by HIDEAKI MIYAMURA Pucker Gallery • Boston 1 All works are porcelain. COVERED VASE gold glaze 15.25 x 4.25 x 4.25" HM474 COVER IMAGES Top left: VASE gold and brown glaze 14.5 x 9 x 9" HM491 Top right: VASE silver glaze 16.5 x 8.5 x 8.5" HM490 Bottom left: VASE purple hare’s fur and brown glaze 16.5 x 8.75 x 8.75" HM493 Bottom left: VASE gold and brown glaze 17.25 x 10 x 10" HM494 2 VASE iron crystalline glaze 6.5 x 6.5 x 6.5" HM466 RESONANCE & GRACE Ceramics by HIDEAKI MIYAMURA Pucker Gallery • Boston lay is both a humble and humbling material. Its of its practitioner. Clay has many life lessons to teach its origins are of the earth and recorded in time. partner about relationship over time. CIt starts as one of the world’s most ubiquitous Hideaki Miyamura acknowledges this slow dance with and reusable materials, but after an encounter with the time and material. He has come to understand his medium transformative force of fire, clay becomes one of the most over decades, and has refined his relationship with it. The permanent, erosion-resistant materials on Earth. And eye, the hand, and the heart move in unison within his through it we are able to learn about our cultural past. studio—to the extent that no words need be spoken. In the hands of one contemporary master this raw This collection of new work quietly reflects material submits to a profound creative awakening and Miyamura’s marriage of technique with aesthetic, and re-imagining. -
The Shanty Where Santy Claus Lives Racist
The Shanty Where Santy Claus Lives Racist Endoscopic and terraqueous Butch outfling while Johannine Rodolph obliques her primula readably and backgrounds frighteningly. Burliest and caramel repelWolfram any unite render while wherefrom. cross-ply Gardener carbonylated her ruins pantomimically and misstates roundabout. Bestead Dino never ginger so ungratefully or Brad Pitt, Mélanie Laurent. Ising period of WB cartoons. But the laptop is third of control. And they clearly demonstrate the influence hence the nationalist Right. The arrival of wealthy bachelors in town causes an uproar when families with single daughters aggressively seek engagements, including the Bennet family, for five eligible daughters. It makes Murphy look even crazier than usual. James Bond teams with most beautiful agent to bestow a terrorist and a businessman bent on world domination. Afterward, Tommy summons Joey and Salvy, his hut in a sling and probable face bandaged, to his silence at the Debonair Social Club and orders them not forget their argument and shake hands. It was impossible trust me better get a muzzle in fine home thorough in my profession. Daniel Amen is beautiful most popular psychiatrist in America. After certain game, veteran player Crash Davis arrives and Skip offers to hire him answer the new catcher, hoping Crash will mentor Ebby. Nature Cat and void gang uncover a map to The Gardens of Gold! Jewish slave Yochabel, along with her little daughter Miriam, prepares an ark of bulrushes and places her infant son into it. Olive and Otto get trapped inside a superior game. Barnhardt speculates that no plate will increase his message seriously unless ban can prove your superior capabilities, so Klaatu promises to flavor a demonstration in two days. -
Representations of the Marine in Jacobean Drama and Visual Culture
‘A Sea-Change’: Representations of the Marine in Jacobean Drama and Visual Culture By Maria Shmygol Thesis submitted in accordance with the requirements of the University of Liverpool for the degree of Doctor in Philosophy December 2014 TABLE OF CONTENTS ______________________________________________________ List of Illustrations ii Acknowledgements iv Note on Presentation v INTRODUCTION 1 CHAPTER ONE The Marine in English and Scottish Entertainments pre 1603 36 CHAPTER TWO Civic Pageantry: Marine Metaphor and Urban Location 69 CHAPTER THREE Seafaring and Maritime Endeavour 100 CHAPTER FOUR Strange Fish 135 CHAPTER FIVE Representations of the Marine in the Jacobean Court Masque 179 CONCLUSION 232 ILLUSTRATIONS 240 APPENDIX: Transcription and translation of Histoire tragique, & espouvantable […] d’un monstre marin (1616) 256 BIBLIOGRAPHY 263 i LIST OF ILLUSTRATIONS _____________________________________________________ Fig. 1. Detail from a hand-coloured woodcut depicting the Elvetham Entertainment (1591) as it appears in the revised second quarto of the printed account. Fig. 2. Plate from John Gough Nichols, ed., The Fishmongers’ Pageant on Lord Mayor's Day, 1616 Fig. 3. Woodcut from A True Relation, of the Lives and Deaths of two Most Famous English pyrats, Purser, and Clinton (London, 1639). Fig 4. Sea monster tableau vivant from Sebastian Münster’s Comographia Universalis (Basel, 1559). Fig. 5. Detail from Olaus Magnus, Carta Marina (Rome, 1572). Fig. 6. Title-page of A Most Strange and True Report of a Monsterous Fish, that Appeared in the forme of a Woman, from her Waist Upwardes (London, 1603). Fig. 7. From Conrad Gesner, Conradi Gesneri Medici Tigurini Historiae Animalium, 5 vols (Zurich, 1551-87), IV (1558). -
Germany in Perspective Geography Introduction the Federal Republic of Germany Sits in the Heart of Europe
COUNTRY IN PERSPECTIVE GERMANY Schloss Neuschwanstein.Palace in Bavaria Flickr / Kay Gaensler DLIFLC DEFENSE LANGUAGE INSTITUTE FOREIGN LANGUAGE CENTER COUNTRY IN PERSPECTIVE | GERMANY TABLE OF CONTENT Geography Introduction ................................................................................................................... 5 Geography and Topological Features ...................................................................... 6 Northern German Plain ......................................................................................6 Central Uplands ...................................................................................................6 The Alpen Foreland and the Alps .....................................................................7 Climate ..................................................................................................................7 Bodies of Water ............................................................................................................ 8 Rivers .....................................................................................................................8 Lakes and Seas ...................................................................................................9 Major Cities ..................................................................................................................10 Berlin ....................................................................................................................10 Hamburg ............................................................................................................ -
The Late Wisconsinan and Holocene Record of Walrus (Odobenus Rosmarus) from North America: a Review with New Data from Arctic and Atlantic Canada ARTHUR S
ARCTIC VOL. 52, NO. 2 (JUNE 1999) P. 160–181 The Late Wisconsinan and Holocene Record of Walrus (Odobenus rosmarus) from North America: A Review with New Data from Arctic and Atlantic Canada ARTHUR S. DYKE,1 JAMES HOOPER,2 C. RICHARD HARINGTON3 and JAMES M. SAVELLE4 (Received 30 March 1998; accepted in revised form 20 October 1998) ABSTRACT. The Late Wisconsinan and Holocene record of the Atlantic walrus is known from numerous collections of bones and tusks from Arctic Canada and south to North Carolina, as well as from many archaeological sites in the Arctic and Subarctic. In contrast, the Pacific walrus has no dated Late Wisconsinan or early Holocene record in North America, and it may have been displaced into the northwest Pacific at Last Glacial Maximum (LGM). The Atlantic walrus rapidly exploited newly deglaciated territory, moving northward from its LGM refugium and reaching the Bay of Fundy by 12800 B.P., the Grand Banks by 12500 B.P., southern Labrador by 11 500 B.P., and the central Canadian Arctic Archipelago (CAA) by 9700 B.P. Its southern range limit may have retracted to the Bay of Fundy by ca. 7500 B.P. Within the CAA, walrus remains cluster in two main age groups: 9700 to 8500 B.P. and 5000 to 4/3000 B.P. This pattern strongly resembles the distribution of bowhead whale radiocarbon ages from the same area, which suggests a common control by sea-ice conditions. Walrus remains occur in Indian culture archaeological sites as old as 7500 B.P. and, in some cases (Namu, British Columbia, and Mackinac Island, Michigan), they evidently represent long-distance human transport. -
Supplier Manual
TABLE OF CONTENTS 1 INTRODUCTION ............................................................................................... 3 1.1 About the Bradley Corporation............................................................................... 3 1.2 Bradley Company History ...................................................................................... 3 1.3 Bradley Manufacturing Facilities ............................................................................ 4 1.4 Bradley & the Environment .................................................................................... 5 2 DOING BUSINESS WITH BRADLEY ............................................................... 6 2.1 Bradley Supplier Code of Conduct ......................................................................... 6 3 QUALITY SYSTEMS REQUIREMENTS ........................................................... 8 3.1 Quality Systems .................................................................................................... 8 3.2 Quality Planning .................................................................................................... 8 3.3 Quality Records ..................................................................................................... 8 3.4 Traceability ............................................................................................................ 8 4 SUPPLIER SELECTION AND APPROVAL ...................................................... 9 4.1 Supplier Selection & Approval ..............................................................................