Colloidal Synthesis of Hollow Cobalt Sulfide Nanocrystals
Total Page:16
File Type:pdf, Size:1020Kb
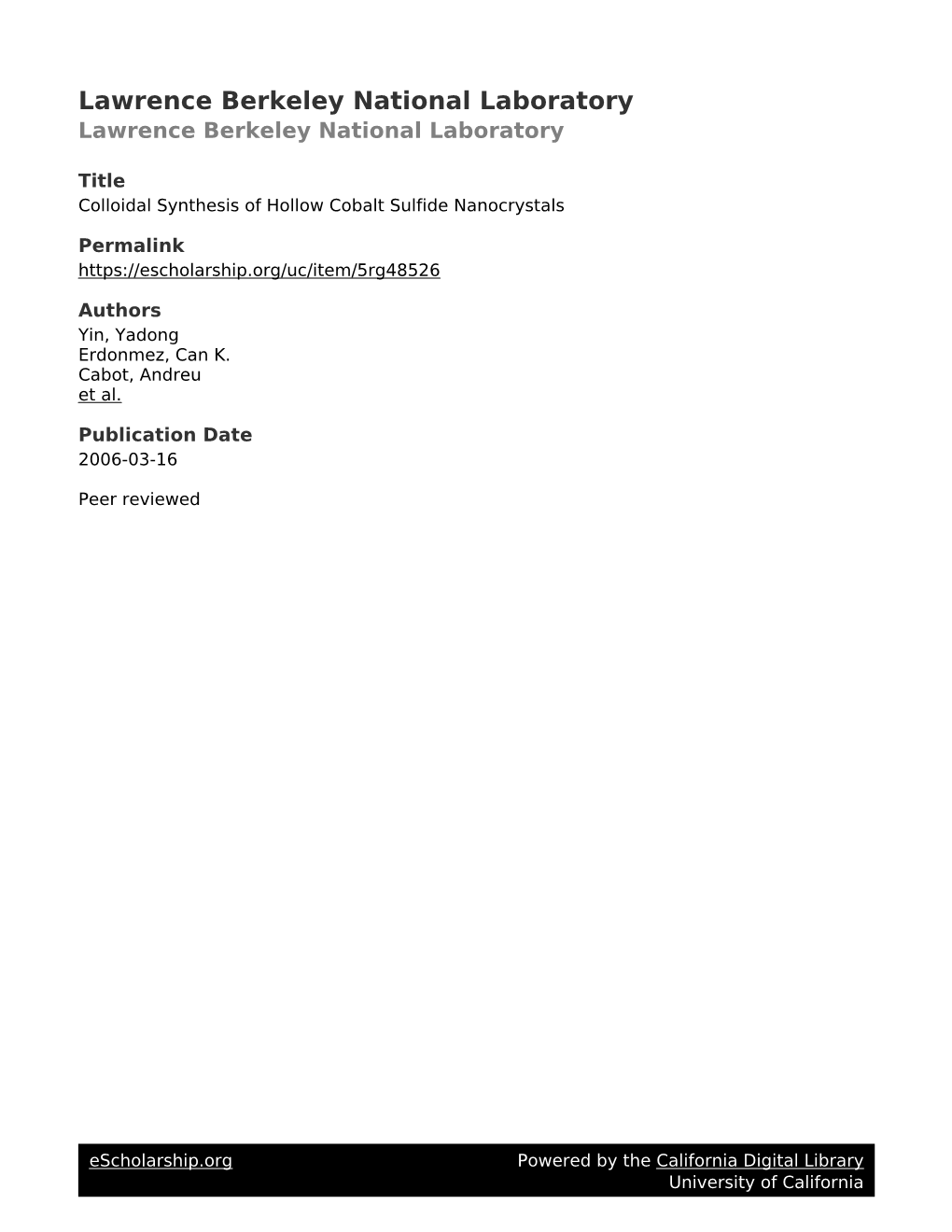
Load more
Recommended publications
-
Atomic Force Microscopy Studies on Sulfur-, Selenium- and Tellurium-Based Metal Chalcogenide Thin Films: a Review
Vol. 11(5), pp. 42-49, November 2017 DOI: 10.5897/AJPAC2017.0739 Article Number: BEB18A566732 African Journal of Pure and Applied ISSN 1996 - 0840 Copyright © 2017 Chemistry Author(s) retain the copyright of this article http://www.academicjournals.org/AJPAC Review Atomic force microscopy studies on sulfur-, selenium- and tellurium-based metal chalcogenide thin films: A review Ho Soonmin Centre for Green Chemistry and Applied Chemistry, INTI International University, Putra Nilai, 71800, Negeri Sembilan, Malaysia. Received 5 October, 2017; Accepted 16 November, 2017 Sulfur, selenium and tellurium-based metal chalcogenide films have been prepared using various deposition methods. Investigation of morphological properties of the generated surface structures on chalcogenide thin films using atomic force microscopy technique was reported. The purpose of this work is to describe past important research findings that are related to atomic force microscopy technique. Key words: Atomic force microscopy, surface roughness, film thickness, grain size. INTRODUCTION Sulfur-based films (Ho et al., 2013; Saravanan et al., epitaxy, metal organic vapor phase epitaxy, pulsed laser 2010; Mohd et al., 2011; Abdullah et al., 2010; deposition, spray pyrolysis, successive ionic layer Dhandayuthapani et al., 2017; Huse et al., 2017; Ahmad adsorption, and reaction. There are a number of papers et al., 2010; Garcia et al., 2017), selenium based films that report the results of morphological, structural, (Ham et al., 2008; Xue et al., 2006; Rajesh et al., 2013; compositional, functional group, and optical Kassim et al., 2010; Wen et al., 2017), and tellurium- characterization of thin films. These films were based metal chalcogenide films (Laxman et al., 2012; characterized using range of characterization techniques Pandiaraman et al., 2011; Camacho-Espinosa et al., such as X-ray photoelectron spectroscopy (Lisco et al., 2014; Chen et al., 2009; Yang et al., 2017) possess 2015; Meng et al., 2015; Zhang et al., 2001; useful electrical, optical and physical properties. -
Metal-Sulfur Compounds in N2 Reduction and Nitrogenase-Related Chemistry
Metal-Sulfur Compounds in N2 Reduction and Nitrogenase-Related Chemistry Kazuki Tanifuji1 and Yasuhiro Ohki 2* 1 Department of Molecular Biology and Biochemistry, University of California, Irvine, Irvine, CA 92697-3900, United States 2 Department of Chemsitry, Graduate School of Science, Nagoya University, Furo-cho, Chikusa-ku, Nagoya 464-8602, Japan e-mail: [email protected] Abstract Transition metal-sulfur (M-S) compounds are an indispensable means for biological systems to convert N2 into NH3 (biological N2 fixation), and these may have emerged by chemical evolution from a pre-biotic N2 fixation system. With a main focus on synthetic species, this article provides a comprehensive review of the chemistry of M-S compounds related to the conversion of N2 and the structures/functions of the nitrogenase cofactors. Three classes of M-S compounds are highlighted here: multi-nuclear M-S clusters structurally or functionally relevant to the nitrogenase cofactors; mono- and di-nuclear transition metal complexes supported by sulfur-containing ligands in N2 and N2Hx (x = 2, 4) chemistry; metal sulfide-based solid materials employed in the reduction of N2. Fair assessments on these classes of compounds revealed that our understanding is still limited in N2 reduction and related substrate reductions. Our aims of this review are to compile a collection of studies performed at atomic to mesoscopic scales and to present potential opportunities for elucidating the roles of metal and sulfur atoms in the biological N2 fixation that might be helpful -
The Use Op Cobalt-60 As a Radiotracer in a Study Op
THE USE OP COBALT-60 AS A RADIOTRACER IN A STUDY OP THE ANALYTICAL CHEMISTRY OF COBALT DISSERTATION Presented in Partial Fulfillment of the Requirements for the Degree Doctor of Philosophy in the Graduate School of the Ohio State University By DARNELL SALYER, B. S. The Ohio State University 1956 Approvec by: Adv^rer Department of Chemistry ACKNOWLEDGMENT The author would like to express his sincere appre ciation to Dr. T. R. Sweet for his guidance and advice during the period of this research. The author’s wife, Octavia Elizabeth Salyer, has been a source of help and encouragement during the con clusion of this work and the oreparation of the manuscript. Most of this work was completed while the author held graduate fellowships from the Cincinnati Chemical vVorks (1954-55) and the Central Division of the Allied Chemical and Dye Corporation (1955-56). The aid provided by these fellowsnips is gratefully acknowledged. ii Table of Contents Page INTRODUCTION ................................................ 1 THE ANODIC DEPOSITION PROBLEM........................... 9 Theory of Anodic Deposition ...................... 9 Conditions for the Deposition of C o b a l t ......... 13 Promising Methods, A Qualitative Study........... 16 Reproducibility, A Quantitative Study ........... 17 Nature of the Deposits................. ........... 27 Ignition of Deposits............................... 33 Summary of Optimum Conditions for Plating and Weighing...................................... 34 Preparation of the Standard Curve ................ 37 Interference Study.................................. 41 DETERMINATION OF SMALL AMOUNTS OF COBALT BY THE ISOTOPE DILUTION-ANODIC DEPOSITION' METHOD . 4 6 Separation of Cobalt from Iron............... 49 Conclusion................................... 49 A STUDY OF THE CATHODIC ElECTRODEPOSITION METHOD FOR oOBALT »»»»»••••»»»..»»•».»• 31 Previous W o r k ...................................... 53 Experimental. -
Formation of Hollow Nanocrystals Through the Nanoscale Kirkendall
Formation of Hollow Nanocrystals through the Nanoscale Kirkendall Effect Yadong Yin, Robert M. Rioux, Can K. Erdonmez, Steven Hughes, Gabor A. Somorjai, A. Paul Alivisatos* Department of Chemistry, University of California at Berkeley, and Materials Science Division, Lawrence Berkeley National Laboratory, Berkeley, CA 94720, USA. *To whom correspondence should be addressed. Email: [email protected] Abstract We demonstrate that hollow nanocrystals can be synthesized through a mechanism analogous to the Kirkendall Effect, in which pores form due to the difference in diffusion rates between two components in a diffusion couple. Cobalt nanocrystals are chosen as a primary example to show that their reaction in solution with oxygen, sulfur or selenium leads to the formation of hollow nanocrystals of the resulting oxide and chalcogenides. This process provides a general route to the synthesis of hollow nanostructures of large numbers of compounds. A simple extension of this process yields platinum-cobalt oxide yolk-shell nanostructures which may serve as nanoscale reactors in catalytic applications. Porous solid materials are important in many areas of modern science and technology, including ion exchange, molecular separation, catalysis, chromatography, microelectronics, and energy storage (1-3). Notable examples are microporous (< 2 nm) zeolites and mesoporous (2-50 nm) silicate and carbonaceous materials. The ability to manipulate the structure and morphology of porous solids on a nanometer scale would enable greater control of local chemical environment (4-6). Here, we demonstrate that nanoscale pores can develop inside nanocrystals with a mechanism analogous to void formation in the Kirkendall Effect, where the mutual diffusion rates of two components in a diffusion couple differ by a considerable amount (7). -
EICG-Hot Spots: EICG Appendix C
INFORMAL REVIEW DRAFT [Note: The pre-existing regulation text is set forth below in normal type. The original proposed amendments are shown in underline to indicate additions and strikeout to indicate deletions. Additional proposed modifications are shown in double-underline to indicate additions and double-strikeout to indicate deletions. The square brackets “[ ]” are used to indicate minor adjustments to text (e.g., page numbers and adoption dates) that will be updated upon adoption of the proposed amendments.] APPENDIX C FACILITY GUIDELINE INDEX (FACILITY "LOOK-UP" TABLE) INFORMAL REVIEW DRAFT This Page Intentionally Left Blank INFORMAL REVIEW DRAFT APPENDIX C - I RESPONSIBILITIES OF ALL FACILITIES INFORMAL REVIEW DRAFT NOTES FOR APPENDIX CFACILITY GUIDELINE INDEX APPENDIX C-I RESPONSIBILITIES OF ALL FACILITIES NOTHING IN THIS APPENDIX SHALL BE CONSTRUED AS REQUIRING THAT SOURCE TESTING BE CONDUCTED FOR SUBSTANCES SET FORTH IN THIS APPENDIX. FURTHER, IN CASES WHERE A SUBSTANCE SET FORTH HEREIN IS NOT PRESENT AT A PARTICULAR FACILITY, THE FACILITY OPERATOR SHALL NOT ATTEMPT TO QUANTIFY THE EMISSIONS OF SUCH SUBSTANCE, BUT SHALL PROVIDE ADEQUATE DOCUMENTATION TO DEMONSTRATE TO THE DISTRICT THAT THE POSSIBLE PRESENCE OF THE SUBSTANCE AT THE FACILITY HAS BEEN ADDRESSED AND THAT THERE ARE NO EMISSIONS OF THE SUBSTANCE FOR SPECIFIED REASONS. Substances emitted by a particular device or process may not be limited to those listed in this Facility Guideline Index. THIS APPENDIX IS NOT AN EXHAUSTIVE LIST. ALL FACILITIES ARE RESPONSIBLE FOR IDENTIFYING AND ACCOUNTING FOR ANY LISTED SUBSTANCE USED, MANUFACTURED, FORMULATED, OR RELEASED. This Facility Guideline Index is arranged in alphabetical order. The first part of the index, Appendix C-I, lists devices common to many industries and the second part of the index, Appendix C-II, lists industry types. -
Draft Screening Assessment for the Challenge
Screening Assessment for the Challenge Cobalt (Elemental cobalt) Chemical Abstracts Service Registry Number 7440-48-4 Cobalt chloride Chemical Abstracts Service Registry Number 7646-79-9 Sulfuric acid, cobalt (2+) salt (1:1) (Cobalt sulfate) Chemical Abstracts Service Registry Number 10124-43-3 Sulfuric acid, cobalt salt (Cobalt sulfate) Chemical Abstracts Service Registry Number 10393-49-4 Environment Canada Health Canada January 2011 Screening Assessment CAS RN 7440-48-4, 7646-79-9, 10124-43-3, 10393-49-4 Synopsis Pursuant to section 74 of the Canadian Environmental Protection Act, 1999 (CEPA 1999), the Ministers of the Environment and of Health have conducted a screening assessment of elemental cobalt, Chemical Abstracts Service Registry Number (CAS RN) 7440-48-4, cobalt chloride, CAS RN 7646-79-9, and cobalt sulfate, CAS RN 10124-43-3 and CAS RN 10393-49-4. The substances elemental cobalt, cobalt chloride and cobalt sulfate (CAS RN 10124-43-3) were identified in the categorization of the Domestic Substances List as high priorities for action under the Challenge. Elemental cobalt and cobalt sulfate (CAS RN 10124-43-3) were considered to pose greatest potential for exposure of individuals in Canada whereas cobalt chloride was considered to pose intermediate potential for exposure. All of these substances are classified by other agencies on the basis of carcinogenicity. These substances all met the ecological categorization criteria for persistence; cobalt chloride and cobalt sulfate also met the categorization criteria for inherent toxicity to aquatic organisms. Therefore this assessment considers both human health and ecological risks. The substances were assessed together as they generate a common moiety of concern, Co2+, under physiological and environmental conditions, and are thus considered to be toxicologically equivalent. -
Commercialization of Cobalt Promoted Molybdenum Disulfide
University of Texas at El Paso DigitalCommons@UTEP Open Access Theses & Dissertations 2016-01-01 Commercialization Of Cobalt Promoted Molybdenum Disulfide yH drodesulfurization Unsupported Catalyst Juan Hilario Leal University of Texas at El Paso, [email protected] Follow this and additional works at: https://digitalcommons.utep.edu/open_etd Part of the Petroleum Engineering Commons Recommended Citation Leal, Juan Hilario, "Commercialization Of Cobalt Promoted Molybdenum Disulfide yH drodesulfurization Unsupported Catalyst" (2016). Open Access Theses & Dissertations. 878. https://digitalcommons.utep.edu/open_etd/878 This is brought to you for free and open access by DigitalCommons@UTEP. It has been accepted for inclusion in Open Access Theses & Dissertations by an authorized administrator of DigitalCommons@UTEP. For more information, please contact [email protected]. COMMERCIALIZATION OF COBALT PROMOTED MOLYBDENUM DISULFIDE HYDRODESULFURIZATION UNSUPPORTED CATALYST JUAN HILARIO LEAL Doctoral Program in Materials Science and Engineering APPROVED: Russell R. Chianelli, Ph.D., Chair Devesh Misra, Ph.D. Felicia Manciu, Ph.D. Binata Joddar, Ph.D. Charles Ambler, Ph.D. Dean of the Graduate School Copyright © by Juan Hilario Leal 2016 Dedication I dedicate this to my family and especially my daughter, Caroline. The people of El Paso, including UTEP faculty and friends have made this a memorable experience. Thank you to all my friends, which I will not name, but you know who you are. I would not have made it without your support. COMMERCIALIZATION OF COBALT PROMOTED MOLYBDENUM DISULFIDE HYDRODESULFURIZATION UNSUPPORTED CATALYST by JUAN HILARIO LEAL, M.S., B.S. DISSERTATION Presented to the Faculty of the Graduate School of The University of Texas at El Paso in Partial Fulfillment of the Requirements for the Degree of DOCTOR OF PHILOSOPHY Material Science and Engineering THE UNIVERSITY OF TEXAS AT EL PASO May 2016 ACKNOWLEDGEMENTS I would like to take this opportunity to thank everyone who has helped me. -
Ti Magnetite Tailings Using Flotation Process
Recovering Cobalt and Sulfur in Low Grade Cobalt-Bearing V?Ti Magnetite Tailings Using Flotation Process Authors: Junhui Xiao, Yushu Zhang Date Submitted: 2019-11-05 Keywords: flotation, cobalt pyrite, V–Ti magnetite tailings, linneite, cobalt, pyrite Abstract: There is 0.032% cobalt and 0.56% sulfur in the cobalt-bearing V?Ti tailings in the Panxi Region, with the metal sulfide minerals mainly including FeS2, Fe1?xS, Co3S4, and (Fe,Co)S2, and the gangue minerals mainly including aluminosilicate minerals. The flotation process was used to recover cobalt and sulfur in the cobalt-bearing V?Ti tailings. The results showed that an optimized cobalt?sulfur concentrate with a cobalt grade of 2.08%, sulfur content of 36.12%, sulfur recovery of 85.79%, and cobalt recovery and 84.77% were obtained by flotation process of one roughing, three sweeping, and three cleaning under roughing conditions, which employed pulp pH of 8, grinding fineness of <0.074 mm occupying 80%, flotation concentration of 30%, and dosages of butyl xanthate, copper sulfate, and pine oil of 100 g/t, 30 g/t, and 20 g/t, respectively. Optimized one sweeping, two sweeping, and three sweeping conditions used a pulp pH of 9, and dosages of butyl xanthate, copper sulfate, and pine oil of 50 g/t, 15 g/t, 10 g/t; 25 g/t, 7.5 g/t, 5 g/t; 20 g/t, 5 g/t, 5 g/t, respectively. Optimized one cleaning, two cleaning, and three cleaning condition dosages of sodium silicate of 200 g/t, 100 g/t, 50 g/t, respectively. -
Characterization of Cobalt Sulfide Thin Films Synthesized from Acidic Chemical Baths
Hindawi Advances in Materials Science and Engineering Volume 2020, Article ID 2628706, 9 pages https://doi.org/10.1155/2020/2628706 Research Article Characterization of Cobalt Sulfide Thin Films Synthesized from Acidic Chemical Baths Tizazu Abza ,1 Dereje Gelanu Dadi,1 Fekadu Gashaw Hone,1 Tesfaye Chebelew Meharu,1 Gebremeskel Tekle,1 Eyobe Belew Abebe,2 and Kalid Seid Ahmed2 1Hawassa University, Department of Physics, Hawassa, Ethiopia 2Adama Science and Technology University, Department of Materials Science and Engineering, Adama, Ethiopia Correspondence should be addressed to Tizazu Abza; [email protected] Received 13 December 2019; Accepted 26 March 2020; Published 30 April 2020 Academic Editor: Isabel J. Ferrer Copyright © 2020 Tizazu Abza et al. ,is is an open access article distributed under the Creative Commons Attribution License, which permits unrestricted use, distribution, and reproduction in any medium, provided the original work is properly cited. Cobalt sulfide thin films were synthesized from acidic chemical baths by varying the deposition time. ,e powder X-ray diffraction studies indicated that there are hexagonal CoS, face-centered cubic Co3S4, and cubic Co9S8 phases of cobalt sulfide. ,e crystallite size of the hexagonal CoS phase decreased from 52.8 nm to 22.5 nm and that of the cubic Co9S8 phase increased from 11 nm to 60 nm as the deposition time increased from 2 hrs to 3.5 hrs. ,e scanning electron microscopic images revealed crack and pinhole free thin films with uniform and smooth background and few large polygonal grains on the surface. ,e band gap of the cobalt sulfide thin films decreased from 1.75 eV to 1.3 eV as the deposition time increased from 2 hrs to 3.5 hrs. -
Beneficiation Research on a Low Grade Linnaeite Ore with Hema-Tite-Pyrite Type
E3S Web of Conferences 136, 02008 (2019) https://doi.org/10.1051/e3sconf/2019136020 08 ICBTE 2019 Beneficiation research on a low grade linnaeite ore with hema- tite-pyrite type Xinfang Zhang, Qinqin Wang, Chengdong Wang, Lang Zhu, Shujie Shi, Niao Wang, Chunying Li and Guiming Shi* College of Chemistry Biology and Environment, Yuxi Normal University, Yuxi, Yunnan, 653100, China Abstract. Mineralogy and separation experiments were carried out for a low-grade linnaeite ore (0.052%), which belonged to limonite-hematite-pyrite type complex mineral. Under the grinding fineness of 80% - 0.074 mm, linnaeite concentrate which contained cobalt grade of 0.51%, recovery rate of 80.99%, sulfur grade of 23.79%, recovery of 88.03% was obtained by closed-circuit processes of one roughing, two scaenging and one cleaning, which used sulfate acid (4500 g/t) and copper sulfate (300 g/t) as activator, so- dium silicate (1000 g/t) and CMC (30 g/t) as inhibitor, ethyl xanthate(100 g/t)and butyl xanthate (100 g/t) as collector, 2# oil (40 g/t) as forther in roughing, no agent in cleaing and first scavenging, used ethyl xan- thate(50 g/t)and butyl xanthate (50 g/t) as collector, 2# oil (20 g/t) as forther in second scavenging. 1 Introduction must be pyrite, but the content of cobalt in pyrite is low and it is difficult to obtain qualified cobalt sulfide Cobalt is one of the important strategic mineral in the concentrate. Therefore, this paper mixed the cobalt world, it has high temperature resistance, corrosion sulfide mineral with other sulphides to obtain mixed resistance, high strength and strong magnetic etc, which concentrate. -
Cobalt Alloys (Including Cobalt-Containing Medical Implants) and (C) Cobalt Compounds
COBALT AND COBALT COMPOUNDS The agents considered herein include (a) metalIc cobalt, (b) cobalt alloys (including cobalt-containing medical implants) and (c) cobalt compounds. Organic cobalt-containing agents (e.g., vitamin B12) are not covered comprehensively in this monograph. 1. Chemical and Physical Data 1.1 Synonyms, trade narnes and molecular rormulae Synonyms, trade names and molecular formulae for cobalt, cobalt alloys and cobalt compounds are presented in Table 1. The cobalt alloys and compounds given in Table 1 are not an exhaustive list, nor are they necessarily the most commercially important cobalt-containing substances; the list indicates the range of cobalt alloys and compounds available. Table 1. Synonyms (Chemical Abstracts Service names are given in bold type), trade names and atomic or molecular rormulae or cobalt and cobalt compounds Chemical name Chem. Abstr. Synonyms and trade names Formulae Servces Reg. a No. Metale cobal Cobalt 74448-4 c.I. 77320; cobalt element; Co cobalt-59 Cobalt alloys Cobalt-chromium 11114-92-4 Cobalt alloy (nonbase), Co, Co.Cr alloyb (91700-55-9) Cr; chromium alloy (nonbas), Co, Cr Nickel-based cobalt 1106-91-0 Nickel alloy (base), Ni 47-59, CAI-Co'Cr-Fe.MoNi' alloyb (126261; Co 17-20, Cr 13-17, Mo Ti 12616-603; 4.5-5.7, AI 3.7-4.7, Ti 3-4, Fe 12616-61-4; 0-1, C 0-0.1 (AISI 687) 1262482-7; 12630-37-4; APK 1; Astroloy; Cabot 700; 12636-2-1; NiCo18Cr15MoAlTi; Nimonic 12672-01-4; AP 1; NK17CADT; PM-ATS 12774-12-8; 380; PWA 1013; R 77; Rene 37323-85-l; 77; U 700; U 700m; U700PM; 64941-39-5) Udimet 700 -363- L., 364 lARe MONOGRAHS VOLUME 52 Table i (contd) Chemical name Chem. -
Synthesis and Characterization of Cobalt Sulfide/Fnbr Nanocomposites by Silar Method
Journal of Ovonic Research Vol. 12, No. 6, November - December 2016, p. 267 - 273 SYNTHESIS AND CHARACTERIZATION OF COBALT SULFIDE/FNBR NANOCOMPOSITES BY SILAR METHOD O. O. BALAYEVAa*, A. A. AZIZOVa, M. B. MURADOVb, A. M. MAHARRAMOVa, G. M. EYVAZOVAb aDepartment of Chemistry, Baku State University, Z. Khalilov str., 23, AZ-1148 Baku, Azerbaijan bDepartment of Physics, Baku State University, Z. Khalilov str., 23, AZ-1148 Baku, Azerbaijan We have prepared cobalt sulfide (CoxSy) nanoparticles through a successive ionic layer adsorption and reaction (SILAR) method at room temperature. Co(NO3)2 × 6H2O aqueous solution was used as a cobalt precursor, Na2S × 9H2O and thiourea [(NH2)2CS] aqueous solutions were used as sulfur precursors. Functionalized nitrile butadiene rubber (FNBR) was used as a stabilizing agent for the formation of nanoparticles and contains –PO(OH)2 and –(O)PO(OH)2 acid groups. Obtained CoxSy/FNBR nanocomposites were annealed at 100ºC in a vacuum for 6 h. The prepared nanocomposites were characterized by XRD, SEM, EDX, UV-Vis and FT-IR spectrometer. In case thiourea is used as asulfur source, mixed phases of Co3S4, CoS1.097 and CoS2 were obtained with the dominance of Co3S4 phase. A possible formation mechanism, physical and chemical stabilization into the functional polymer matrix (FNBR) for the growth processes have been discussed. (Received August 1, 2016; Accepted November 10, 2016) Keywords: Cobalt sulfide, Functionalized polymer, Nanocomposites, Optical properties 1. Introduction Cobalt sulfide has potential applications in solar selective coatings, IR detectors and as a storage electrode in photoelectrochemical storage device [1]. Due to its band gap and good adsorption properties, CoS can be used as a photocatalyst.