Selection of Safe Roadside Cross Sections
Total Page:16
File Type:pdf, Size:1020Kb
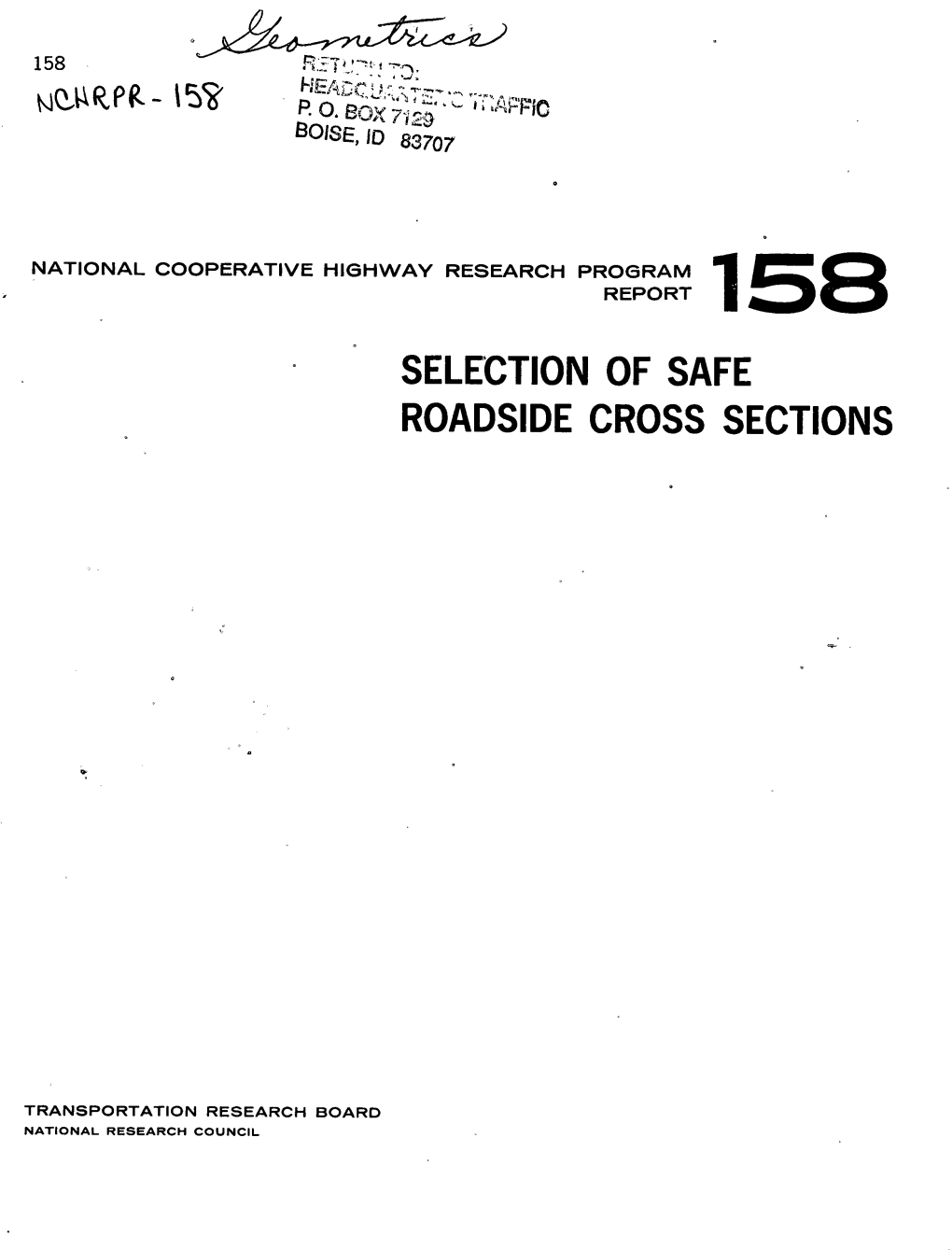
Load more
Recommended publications
-
Fws–R2–Es–2019–0061; Ff09e21000 Fxes11110900000 212]
This document is scheduled to be published in the Federal Register on 08/26/2021 and available online at Billing Code 4333–15 federalregister.gov/d/2021-18012, and on govinfo.gov DEPARTMENT OF THE INTERIOR Fish and Wildlife Service 50 CFR Part 17 [FWS–R2–ES–2019–0061; FF09E21000 FXES11110900000 212] RIN 1018–BD16 Endangered and Threatened Wildlife and Plants; Endangered Species Status with Critical Habitat for Guadalupe Fatmucket, Texas Fatmucket, Guadalupe Orb, Texas Pimpleback, and False Spike, and Threatened Species Status with Section 4(d) Rule and Critical Habitat for Texas Fawnsfoot AGENCY: Fish and Wildlife Service, Interior. ACTION: Proposed rule. SUMMARY: We, the U.S. Fish and Wildlife Service (Service or USFWS), propose to list six Central Texas mussel species: the Guadalupe fatmucket (Lampsilis bergmanni), Texas fatmucket (Lampsilis bracteata), Texas fawnsfoot (Truncilla macrodon), Guadalupe orb (Cyclonaias necki), Texas pimpleback (Cyclonaias (=Quadrula) petrina), and false spike (Fusconaia (=Quincuncina) mitchelli) as endangered or threatened under the Endangered Species Act of 1973, as amended (Act). After review of the best available scientific and commercial information, we find that listing Guadalupe fatmucket, Texas fatmucket, Guadalupe orb, Texas pimpleback, and false spike as endangered species is warranted, and listing Texas fawnsfoot as a threatened species is warranted. We propose a rule issued under section 4(d) of the Act (“4(d) rule”) for the Texas fawnsfoot. If we finalize this rule as proposed, it would add these species to the List of Endangered and Threatened Wildlife and extend the Act’s protections to the species. We also propose to designate critical habitat for all six species under the Act. -
Proposed Rule
Billing Code 4333–15 DEPARTMENT OF THE INTERIOR Fish and Wildlife Service 50 CFR Part 17 [FWS–R2–ES–2019–0061; FF09E21000 FXES11110900000 212] RIN 1018–BD16 Endangered and Threatened Wildlife and Plants; Endangered Species Status with Critical Habitat for Guadalupe Fatmucket, Texas Fatmucket, Guadalupe Orb, Texas Pimpleback, and False Spike, and Threatened Species Status with Section 4(d) Rule and Critical Habitat for Texas Fawnsfoot AGENCY: Fish and Wildlife Service, Interior. ACTION: Proposed rule. SUMMARY: We, the U.S. Fish and Wildlife Service (Service or USFWS), propose to list six Central Texas mussel species: the Guadalupe fatmucket (Lampsilis bergmanni), Texas fatmucket (Lampsilis bracteata), Texas fawnsfoot (Truncilla macrodon), Guadalupe orb (Cyclonaias necki), Texas pimpleback (Cyclonaias (=Quadrula) petrina), and false spike (Fusconaia (=Quincuncina) mitchelli) as endangered or threatened under the Endangered Species Act of 1973, as amended (Act). After review of the best available scientific and commercial information, we find that listing Guadalupe fatmucket, Texas fatmucket, Guadalupe orb, Texas pimpleback, and false spike as endangered species is warranted, and listing Texas fawnsfoot as a threatened species is warranted. We propose a rule issued under section 4(d) of the Act (“4(d) rule”) for the Texas fawnsfoot. If we finalize this rule as proposed, it would add these species to the List of Endangered and Threatened Wildlife and extend the Act’s protections to the species. We also propose to designate critical habitat for all six species under the Act. In total, approximately 1,944 river miles (3,129 river kilometers) in Texas fall within the boundaries of the proposed critical habitat designations. -
City of Missouri City, Texas
City of Missouri City, Texas COMPREHENSIVE ANNUAL FINANCIAL REPORT For the Fiscal Year Ended June 30, 2014 Edward Broussard, City Manager Prepared by: Wes Vela, Director of Finance Michael Higgins, Assistant Finance Director City of Missouri City, Texas COMPREHENSIVE ANNUAL FINANCIAL REPORT Year Ended June 30, 2014 TABLE OF CONTENTS Exhibit Page INTRODUCTORY SECTION Letter of Transmittal i-xiv GFOA Certificate of Achievement xv Organizational Chart xvi List of Principal Officials xvii-xix FINANCIAL SECTION Independent Auditors’ Report 1-2 Management’s Discussion and Analysis 4-13 Basic Financial Statements: Government-Wide Financial Statements: Statement of Net Position A-1 17 Statement of Activities A-2 18-19 Fund Financial Statements: Balance Sheet - Governmental Funds A-3 20 Statement of Revenues, Expenditures, and Changes in Fund Balance - Governmental Funds A-4 21 Reconciliation of the Statement of Revenues, Expenditures, and Changes in Fund Balances of Governmental Funds to the Statement of Activities A-5 22 Statement of Net Position - Proprietary Funds A-6 23 Statement of Revenues, Expenses and Changes in Fund Net Position - Proprietary Funds A-7 24 Statement of Cash Flows - Proprietary Funds A-8 25-26 Notes to the Financial Statements A-9 28-64 Required Supplementary Information: General Fund - Schedule of Revenues, Expenditures, and Changes in Fund Balance - Budget and Actual B-1 66 Notes to Required Supplementary Information B-2 67-69 Texas Municipal Retirement System - Schedule of Funding Progress B-3 70 City of Missouri City, -
SIENNA PLANTATION LEVEE IMPROVEMENT DISTRICT of FORT BEND COUNTY, TEXAS (A Political Subdivision of the State of Texas, Located Within Fort Bend County)
OFFICIAL STATEMENT DATED SEPTEMBER 23, 2020 In the opinion of The Muller Law Group, PLLC, Bond Counsel, based upon an analysis of existing laws, regulations, rulings and court decisions, and assuming, among other matters, the accuracy of certain representations and compliance with certain covenants, interest on the Bonds (herein defined) is excluded from gross income for federal income tax purposes under Section 103 of the Internal Revenue Code of 1986. In the further opinion of Bond Counsel, interest on the Bonds is not a specific preference item for purposes of the federal alternative minimum tax. Bond Counsel expresses no opinion regarding any other tax consequences related to the ownership or disposition of, or the amount, accrual or receipt of interest on, the Bonds. See “TAX MATTERS.” The Bonds are NOT designated “qualified tax-exempt obligations” for financial institutions. See “TAX MATTERS – NOT Qualified Tax-Exempt Obligations.” NEW ISSUE – Book-Entry-Only S&P Global Ratings (AGM Insured) ......................................................... “AA” Moody’s Investors Service, Inc. (Underlying) (AGM Insured) ....... “A1” SIENNA PLANTATION LEVEE IMPROVEMENT DISTRICT OF FORT BEND COUNTY, TEXAS (A Political Subdivision of the State of Texas, located within Fort Bend County) $37,900,000 Unlimited Tax Levee Improvement Bonds Series 2020 Dated: October 1, 2020 Due: September 1, as shown on the inside cover The $37,900,000 Sienna Plantation Levee Improvement District of Fort Bend County, Texas, Unlimited Tax Levee Improvement Bonds, Series 2020 (the "Bonds") are obligations of Sienna Plantation Levee Improvement District of Fort Bend County, Texas (the "District") and are not obligations of the State of Texas (“Texas”); the City of Missouri City, Texas (the “City”); the City of Alvin, Texas; Fort Bend County, Texas (the “County”); or any political subdivision or entity other than the District. -
2019-20 Kkpsi Southwest District Constitution and Policy Guide
KAPPA KAPPA PSI SOUTHWEST DISTRICT CONSTITUTION AND POLICY GUIDE 2019-20 KAPPA KAPPA PSI SOUTHWEST DISTRICT CONSTITUTION & POLICY GUIDE 2019-20 Table of Contents p. 1 SOUTHWEST DISTRICT CONSTITUTION Preamble p. 5 Article I. Organization p. 5 Article II. Governance p. 6 Article III. Officers p. 8 Article IV. Finance p. 10 Article V. Meetings p. 11 Article VI. Delegates and Proxies p. 12 Article VII. Committees p. 13 Article VIII. Publications and Communications p. 14 Article IX. Awards and Traditions p. 14 SOUTHWEST DISTRICT POLICY GUIDE Section 1. Purpose p. 17 Section 2. Governance p. 17 Section 3. Officers p. 18 Section 4. Elections p. 19 Section 5. Finance p. 20 Section 6. Meetings p. 21 Section 7. Delegates and Proxies p. 23 Section 8. Committees p. 24 Section 9. Publications and Communications p. 26 Section 10. Awards p. 27 Section 11. Grants and Funding p. 31 Section 12. Traditions p. 32 SOUTHWEST DISTRICT CONSTITUTION 2019-20 CONSTITUTION of the SOUTHWEST DISTRICT of KAPPA KAPPA PSI PREAMBLE Be it known: that to fulfill the Purposes of Kappa Kappa Psi, to promote the ideals of the Fraternity, and to help our fellows to do the same, the Brothers of the Southwest District, in accordance with the Kappa Kappa Psi National Constitution, do hereby establish this Southwest District Constitution. ARTICLE 1. ORGANIZATION 1.01 Name The name of this District shall be the Southwest District of Kappa Kappa Psi, National Honorary Band Fraternity for College and University Bandmembers. 1.02 Membership The Southwest District shall comprise all the chapters and colonies of Kappa Kappa Psi located within the states of Arkansas, Louisiana, New Mexico, Oklahoma, and Texas, unless assigned elsewhere by the Kappa Kappa Psi National Council; as well as any chapters or colonies assigned to the District by the National Council. -
Corflu 37 Progress Report 0
CORFLU 37 / CORFLU HEATWAVE 37º C C orflu Heatwave College Station, Texas Spring 2020 CORFLU 37 / CORFLU HEATWAVE How I got into this mess. “Okay. Fine. I’ll think about it.” I do believe those were my exact words when Pablo Miguel Alberto Vazquez – hereafter referred to as simply Pablo to save space and avoid unnecessary spelling errors – approached me about the idea of bringing Corflu, the fanzine fan’s annual gathering, back to Texas. It has been twelve years since Corflu Quire (#24 in the series: collect them all, like Ted White) was held in Austin, Texas (expertly handled by that human dynamo called Pat Virzi), and I agreed that it had indeed been awhile. I had a grand time at Corflu Quire, and marveled at not only seeing old friends again, but meeting new friends that I had known through their fanzines for practically decades. I even still have pictures of that affair, and wrote up the event in the first issue of Askance (March 2007) in “A Full-Voiced Quire,” which I thought was a clever title for that con report. About a week later I wrote back to Pablo, stating that the idea was worth looking into, but noting that we needed a venue that was accessible to me as I offered to research the idea while Pablo was off in England working on his graduate degree. Sheesh! The things people will do to duck out of their responsibilities… Anyway. I started asking some people here in Texas who might be willing to help out, and got some cautious responses. -
City of Missouri City, Texas
City of Missouri City, Texas COMPREHENSIVE ANNUAL FINANCIAL REPORT For the Fiscal Year Ended June 30, 2007 Frank Simpson, City Manager Prepared by: City of Missouri City Finance Department Wes Vela, Director of Finance Michael Higgins, Assistant Director of Finance Cynthia Conley, Budget and Financial Reporting Manager City of Missouri City, Texas COMPREHENSIVE ANNUAL FINANCIAL REPORT Year Ended June 30, 2007 TABLE OF CONTENTS Exhibit Page INTRODUCTORY SECTION Letter of Transmittal i-vii GFOA Certificate of Achievement viii Organizational Chart ix List of Principal Officials x-xii FINANCIAL SECTION Independent Auditors’ Report 5 Management’s Discussion and Analysis 9-18 Basic Financial Statements: Government-Wide Financial Statements: Statement of Net Assets A-1 21 Statement of Activities A-2 22-23 Fund Financial Statements: Balance Sheet - Governmental Funds A-3 24-25 Statement of Revenues, Expenditures, and Changes in Fund Balances - Governmental Funds A-4 26-27 Reconciliation of the Statement of Revenues, Expenditures, and Changes in Fund Balance of Governmental Funds to the Statement of Activities A-5 29 Statement of Net Assets - Proprietary Funds A-6 30-31 Statement of Revenues, Expenses and Changes in Fund Net Assets - Proprietary Funds A-7 32-33 Statement of Cash Flows - Proprietary Funds A-8 34-35 Statement of Fiduciary Net Assets A-9 37 Notes to the Financial Statements A-10 40-70 Required Supplementary Information: General Fund - Schedule of Revenues, Expenditures, and Changes in Fund Balances – Budget and Actual (Non-GAAP Budgetary -
Official Statement
OFFICIAL STATEMENT DATED APRIL 4, 2019 In the opinion of The Muller Law Group PLLC, Bond Counsel, based upon an analysis of existing laws, regulations, rulings and court decisions, and assuming, among other matters, the accuracy of certain representations and compliance with certain covenants, interest on the Bonds is excluded from gross income for federal income tax purposes under Section 103 of the Internal Revenue Code of 1986. In the further opinion of Bond Counsel, interest on the Bonds is not a specific preference item for purposes of the federal alternative minimum tax. Bond Counsel expresses no opinion regarding any other tax consequences related to the ownership or disposition of, or the amount, accrual or receipt of interest on, the Bonds. See “TAX MATTERS” herein. The Bonds are NOT designated “qualified tax-exempt obligations” for financial institutions. See “TAX MATTERS – Not Qualified Tax-Exempt Obligations.” NEW ISSUE – Book Entry Only RATINGS: Moody’s Investors Service, Inc. (Underlying) ................. “A2” S&P Global Ratings (BAM Insured) ......................“AA/Stable” See “MUNICIPAL BOND INSURANCE” and “MUNICIPAL BOND RATINGS” $10,725,000 FORT BEND COUNTY LEVEE IMPROVEMENT DISTRICT NO. 19 (A Political Subdivision of the State of Texas, located within Fort Bend County) UNLIMITED TAX LEVEE IMPROVEMENT BONDS, SERIES 2019 Dated: April 1, 2019 Due: September 1, as shown on inside cover The $10,725,000 Fort Bend County Levee Improvement District No. 19 Unlimited Tax Levee Improvement Bonds, Series 2019 (the “Bonds”) are obligations of Fort Bend County Levee Improvement District No. 19 (the “District”) and are not obligations of the State of Texas; the City of Missouri City, Texas; Fort Bend County, Texas; or any political subdivision or entity other than the District. -
Allocated Earmarks Less Than 10% Obligated
Publication Date 3/7/2016 ALLOCATED EARMARK PROJECTS STATUS FOR FUND AVAILABLE IN FMIS DEMO by STATE or TERRITORY LESS THAN 10% OBLIGATED, As of December 18, 2015 State or Territory Demo ID Demo Description Allocated Amount* Obligated Amount Unobligated Balance % Obligated Comment ALABAMA AL019 Construct Decatur Southern Bypass $4,100,399.00 $0.00 $4,100,399.00 0.00% ALABAMA AL023 Construct repairs to viaducts connecting downtown and midtown areas, $461,295.00 $5,863.60 $455,431.40 1.27% Birmingham ALABAMA AL043 Capital costs associated with track relocation, construction and rehab, $4,989,000.00 $0.00 $4,989,000.00 0.00% hwy-rail separation construction activities incl ROW acquisition and utility relocation, and signal improvements in Muscle Shoals, Tuscumbia and Sheffield, AL ALABAMA AL077 Riverwalk, Montgomery, Alabama $136,612.06 $0.00 $136,612.06 0.00% ALABAMA AL081 Balch Road, Madison, Alabama $854,246.50 $0.00 $854,246.50 0.00% ALABAMA AL108 Construction of Valleydale Road Flyover and widening and $4,726,962.00 $0.00 $4,726,962.00 0.00% improvements from U.S. 31 to I65 (Shelby County Rd. 17) ALABAMA AL112 Pedestrian Improvements for Homewood, AL $320,472.00 $0.00 $320,472.00 0.00% ALABAMA AL114 I-20 widening and safety improvements in St. Clair County $4,005,900.00 $0.00 $4,005,900.00 0.00% ALABAMA AL116 Pedestrian Improvements for Morris, AL $106,823.67 $0.00 $106,823.67 0.00% ALABAMA AL117 To construct up to 2 interchanges on U.S. -
City of Bryan Community Wildfire Protection Plan
City of Bryan Community Wildfire Protection Plan 2013 A collaborative approach to protecting lives, property and natural resources in the City of Bryan This plan is dedicated to the memory of Lt. Eric Wallace, a member of the Community Wildfire Protection Plan working group, and Lt. Greg Pickard. The men valiantly gave their lives in the line of duty in February 2013. In accordance with Title I of the Healthy Forest Restoration Act of 2003 This document was prepared by the Bryan Fire Department and Texas A&M Forest Service and was completed on May 1, 2013. Jason Bienski Tom Boggus Mayor Director Bryan, Texas Texas A&M Forest Service Randy McGregor Mark Stanford Fire Chief Fire Chief Bryan, Texas Texas A&M Forest Service Jerry Henry Bruce Woods Emergency Management Coordinator Department Head, Mitigation and Prevention Bryan, Texas Texas A&M Forest Service Table of Contents Introduction ..................................................................................................................................................................................................... 6 Statement of Intent .......................................................................................................................................................................................... 6 Goals ................................................................................................................................................................................................................. 6 Objectives ........................................................................................................................................................................................................ -
CTCOG Community Profiles
Community Profiles Bartlett Fast Facts: • Population: 2,243 • Total Area: 1.22 square miles • Median Household Income: $36,563 Population and Demographics Bartlett had a population density of 1,838.52 per square mile at the 2017 census. The racial makeup of the city was 70.3% White, 23.9% African American, 0% Native American, 3.5% from other races, and 3.2% from two or more races. Hispanic or Latino of any race were 39.8% of the population. Location Bartlett is a city in Bell and Williamson counties in the U.S. state of Texas. Bartlett lies in two counties as well as two metropolitan areas. The Bell County portion of the city is part of the Killeen–Temple–Fort Hood Metropolitan Statistical Area, while the Williamson County portion is part of the Austin–Round Rock Metropolitan Statistical Area Economic Assets Known for its late nineteenth and early twentieth century architecture, Bartlett was the site for the filming of movies including The Stars Fell on Henrietta and The Newton Boys, as well as the NBC television drama Revolution. Bartlett is 27 minutes from the Georgetown, TX Municipal Airport and 53 minutes from the Austin-Bergstrom International Airport. The city is also 44 minutes away from Fort Hood army base. DDCT Board Meeting January 9, 2020 Community Profiles Belton Fast Facts • Population: 24,684 • Total Area: 19.96 square miles • Median Household Income: $54,325 Population and Demographics Belton, TX is the 2,165th largest city in the United States. The population density is 1,007 per sq mi which is 938% higher than the Texas average and 1011% higher than the national average. -
Offering Memorandum
OFFERING MEMORANDUM WACO SHOPPING CENTER / Kelley Workman SHERMAN SHOPPING CENTER Vice President David H. Luther Executive Vice President Morgan Hansen Senior Associate INVESTMENT SALES INVESTMENT NON-ENDORSEMENT AND DISCLAIMER NOTICE CONFIDENTIALITY AND DISCLAIMER The information contained in the following marketing brochure is proprietary and strictly confidential. It is intended to be reviewed only buy the party receiving it from NewQuest Properties and should not be made available to any other person or entity without the written consent of NewQuest Properties. This Marketing Brochure has been prepared to provide summary, unverified information to prospective purchasers, and to establish only a preliminary level of interest in the subject property. The information contained herein is not a substitute for a thorough due diligence investigation. NewQuest Properties has not made any investigation, and makes no warranty or representation, with respect to the income or expenses for the subject property, the future projected financial performance of the property, the size square footage of the property and improvements, presence or absence of contaminating substances, PCB‘s or asbestos, the compliance with State and Federal regulations, the physical condition of the improvements thereon, or the financial condition or business prospects of any tenant, or any tenants plans or intentions to continue it’s occupancy of the subject property. The information contained in this Marketing Brochure has been obtained from sources we believe to be reliable; however, NewQuest Properties has not verified, and will not verify, any of the information contained herein, nor has NewQuest Properties conducted any investigation regarding these matters and makes no warrantee or representation whatsoever regarding the accuracy or completeness of the information provided.