An Increased Reliability Male
Total Page:16
File Type:pdf, Size:1020Kb
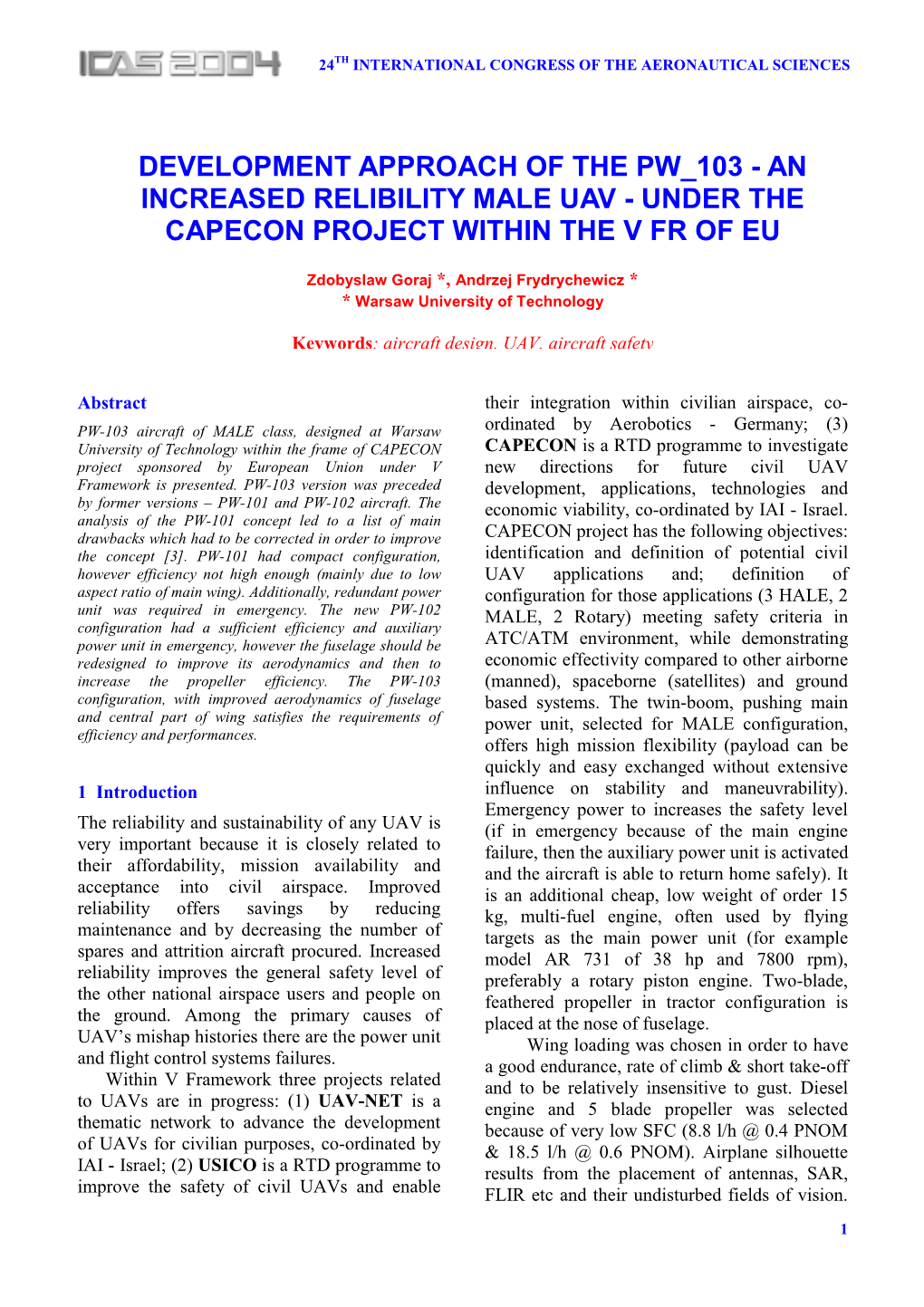
Load more
Recommended publications
-
A Numerical Approach for Implementing Air Intakes in a Canard Type Aircraft for Engine Cooling Purposes
https://doi.org/10.1590/jatm.v13.1192 ORIGINAL PAPER A Numerical Approach for Implementing Air Intakes in a Canard Type Aircraft for Engine Cooling Purposes Odenir de Almeida1,* , Pedro Correa Souza1 , Erick Cunha2 1.Universidade Federal de Uberlândia – Faculdade de Engenharia Mecânica – Centro de Pesquisa em Aerodinâmica Experimental – Uberlândia/MG – Brazil. 2.Fábrica Brasileira de Aeronaves – Uberlândia/MG – Brazil *Corresponding author: [email protected] ABSTRACT This work presents selected results of an unconventional aircraft development campaign. Engine installation at the rear part of the fuselage imposed design constraints for air intakes that should be used for cooling purposes. Trial and error flight tests increased the development cost and time which required a more sophisticated analysis through computational fluid dynamics (CFD) techniques and robust semiempirical approach. The carried-out investigation of the air intakes started with an empirical approach from guidelines for designing NACA and scoops. Numerical studies via computational fluid dynamics were performed with the air intakes installed in the aircraft fuselage. An analysis based on the air intake efficiency, drag and the effect of angle of attack are detailed in this work. Different air intakes designs, such as scoops of different shapes, were evaluated seeking for improved air intake efficiency and low drag while providing enough air for cooling the engine compartment. The results showed that the numerical approach used herein decreased the development cost and time of the aircraft, providing a reasonable low-cost approach and leading to a design selection more easily. Based on the current approach the canard airplane geometry was changed to account for the new selected air intake for engine cooling purposes. -
The Design and Development of a Human-Powered
THE DESIGN AND DEVELOPMENT OF A HUMAN-POWERED AIRPLANE A THESIS Presented to the Faculty of the Graduate Division "by James Marion McAvoy^ Jr. In Partial Fulfillment of the Requirements for the Degree Master of Science in Aerospace Engineering Georgia Institute of Technology June _, 1963 A/ :o TEE DESIGN AND DETERMENT OF A HUMAN-POWERED AIRPLANE Approved: Pate Approved "by Chairman: M(Ly Z7. /q£3 In presenting the dissertation as a partial fulfillment of the requirements for an advanced degree from the Georgia Institute of Technology, I agree that the Library of the Institution shall make it available for inspection and circulation in accordance with its regulations governing materials of this type. I agree that permission to copy from, or to publish from, this dissertation may he granted by the professor under whose direction it was written, or, in his absence, by the dean of the Graduate Division when such copying or publication is solely for scholarly purposes and does not involve potential financial gain. It is under stood that any copying from, or publication of, this disser tation which involves potential financial gain will not be allowed without written permission. i "J-lW* 11 ACKNOWLEDGMENTS The author wishes to express his most sincere appreciation to Pro fessor John J, Harper for acting as thesis advisor, and for his ready ad vice at all times. Thanks are due also to Doctor Rohin B. Gray and Doctor Thomas W. Jackson for serving on the reading committee and for their help and ad vice . Gratitude is also extended to,all those people who aided in the construction of the MPA and to those who provided moral and physical sup port for the project. -
Design Study of Technology Requirements for High Performance Single-Propeller- Driven Business Airplanes
3 1176 01346 2362 ! NASA Contractor Report 3863 NASA-CR-386319850007383 Design Study of Technology Requirements for High Performance Single-Propeller- Driven Business Airplanes David L. Kohlman and James Hammer CONTRACT NAS1-16363 JANUARY 1985 N/ A NASA Contractor Report 3863 Design Study of Technology Requirements for High Performance Single-Propeller- Driven Business Airplanes David L. Kohlman and James Hammer Flight Research Laboratory University of Kansas Center for Research, Inc. Lawrence, Kansas Prepared for Langley Research Center under Contract NAS1-16363 N/ A National Aeronautics and Space Administration Scientific and Technical InformationBranch 1985 TABLE OF CONTENTS Page i. INTRODUCTION .............................................. 1 2. NOMENCLATURE .............................................. 5 3. BASELINE CONFIGURATION ANALYSIS ........................... 7 3.1 Description of Baseline Configuration ................ 7 3.2 Effect of Aspect Ratio ............................... ii 3.3 Effect of Wing Loading ............................... 12 3.4 Effect of Wing Natural Laminar Flow .................. 15 3.5 Effect of Fuselage Drag .............................. 19 4. PROPULSION SYSTEM ANALYSIS ................................. 31 4.1 GATE Engine ........................................... 32 4.1.1 Description of Engine .......................... 32 4.1.2 GASP Engine Routine ............................ 33 4.2 Very Advanced Reciprocating Engine (Spark Ignited), (SIR) ............................... 36 4.3 Very Advanced Diesel -
Design and Development of a Multi- Mission UAS Through Modular Component Integration and Additive Manufacturing
Design and Development of a Multi- Mission UAS through Modular Component Integration and Additive Manufacturing A project present to The Faculty of the Department of Aerospace Engineering San Jose State University in partial fulfillment of the requirements for the degree Master of Science in Aerospace Engineering By Kim Lau August, 2018 approved by Dr. Nikos Mourtos Faculty Advisor 2 Table of Contents 1. Introduction ........................................................................................................................5 1.1. Motivation .................................................................................................................5 1.2. Literature Review .....................................................................................................5 1.2.1. UAV Design and Development Trends ...........................................................5 1.2.2. Push for Modularity .........................................................................................7 1.2.3. Additive Manufacturing ...................................................................................8 1.3. Project Proposal ........................................................................................................11 1.4. Methodology .............................................................................................................11 2. Design Process ...................................................................................................................12 2.1. Mission Specification and -
The Voisin Biplane by Robert G
THE VOISIN BIPLANE BY ROBERT G. WALDVOGEL A single glance at the Voisin Biplane reveals exactly what one would expect of a vintage aircraft: a somewhat ungainly design with dual, fabric-covered wings; a propeller; an aerodynamic surface protruding ahead of its airframe; and a boxy, kite-resembling tail. But, by 1907 standards, it had been considered “advanced.” Its designer, Gabriel Voisin, son of a provincial engineer, was born in Belleville, France, in 1880, initially demonstrating mechanical and aeronautical aptitude through his boat, automobile, and kite interests. An admirer of Clement Ader, he trained as an architect and draftsman at the Ecole des Beaux-Arts in Lyon, and was later introduced to Ernest Archdeacon, a wealthy lawyer and aviation enthusiast, who subsequently commissioned him to design a glider. Using inaccurate and incomplete drawings of the Wright Brothers’ 1902 glider published in L’Aerophile, the Aero-Club’s journal, Voisin constructed an airframe in January of 1904 which only bore a superficial resemblance to its original. Sporting dual wings subdivided by vertical partitions, a forward elevating plane, and a two-cell box-kite tail, it was devoid of the Wright-devised wing- warping method, and therefore had no means by which lateral control could be exerted. Two-thirds the size of the original, it was 40 pounds lighter. Supported by floats and tethered to a Panhard-engined racing boat, the glider attempted its first fight from the Seine River on June 8, 1905, as described by Voisin himself. “Gradually and cautiously, (the helmsman) took up the slack of my towing cable…” he had written. -
The Modern Resurgence of a Misunderstood Machine
FEATURE THE MODERN RESURGENCE OF A MISUNDERSTOOD MACHINE STORY BY BETH E. STANTON PHOTOGRAPHY BY CHRIS MILLER AT FIRST GLANCE, GYROPLANES LOOK LIKE A FUNKY CROSS BETWEEN A HELICOPTER AND AN AIRPLANE. While sharing aspects of both, they combine a unique blend of flight characteristics into one exhilarating-to-fly package. There is a standard in the industry known as the Gyroplane Grin. After his first flight in a gyroplane at EAA AirVenture Oshkosh 2018, Jim Antes, EAA Lifetime 1170562, was hooked. 78 March 2019 Alvee has no pilot experience but loved his gyroplane ride. www.eaa.org 79 “ALL IT TOOK WAS ONE FLIGHT, AND I HAD TO BUY THAT GYRO,” HE SAID. “I COULDN’T GET THE SMILE OFF MY FACE.” Gyroplanes can take off and land in short distances and fly in wind and turbulence that keeps fixed-wing aircraft on the ground. They can fly low and slow or cruise along at around 100 mph. They are highly maneuverable, can- not stall or spin, and, since they’re always in auto-rotation, they gradually descend to a land- ing spot in the event of an engine failure. Gyroplanes are a niche within a niche of rotorcraft and have been the outcasts of general aviation for decades. “We’re always sort of outcasts anyway being a rotorcraft,” gyroplane pilot Paul Minear said. “Then“ flying this thing that’s really unusual, we’re reallyr on the fringe of things.” MISCONCEPTIONS MISCONCEPTIONS ABOUT GYROPLANES span GYROPLANEGYROPLANE GEMSGEMS ROTOR FLIGHT DYNAMICS DOMINATOR / N559RD opposite ends of the spectrum, from so easy you can teach yourself to fly to the notion that they are difficult and dangerous. -
Design of an Unmanned Aerial Vehicle for Long-Endurance Communication Support
AIAA 2017-4148 AIAA AVIATION Forum 5-9 June 2017, Denver, Colorado 18th AIAA/ISSMO Multidisciplinary Analysis and Optimization Conference Design of an Unmanned Aerial Vehicle for Long-Endurance Communication Support Berk Ozturk,∗ Michael Burton,∗ Ostin Zarse,y Warren Hoburg,z Mark Drela,x John Hansmanx A long-endurance, medium-altitude unmanned aerial vehicle (UAV) was designed to provide communication support to areas lacking communication infrastructure. Current solutions involve larger, more costly aircraft that carry heavier payloads and have maximum flight durations of less than 36 hours. The presented design would enable a 5.6 day mission with a 10 lb, 100 W communications payload, providing coverage over an area 100 km in diameter. A geometric program was used to size the aircraft, which is a piston-engine unmanned aircraft with a 24 ft wingspan, and a takeoff weight of 147 lbs. The airframe is designed to be modular, which allows for fast and easy transportation and assembly for an operating crew of four to six. The aircraft can station-keep in 90% of global wind conditions at an altitude of 15,000 ft. Nomenclature ADS-B Automatic Dependent LOS line-of-sight Surveillance-Broadcast MSL mean sea level BLOS beyond line-of-slight MTOW maximum takeoff weight BSFC brake specific fuel consumption PMU power management unit CG center of gravity RC remote control GP geometric program RPM revolutions per minute ECU engine control unit STP standard temperature and pressure FAA Federal Aviation Administration UAV unmanned aerial vehicle FAR Federal Aviation Regulations UHF ultra-high frequency GPS Global Positioning System IC internal combustion I. -
Conceptual and Preliminary Design of a Long Endurance Electric UAV
Conceptual and Preliminary Design of a Long Endurance Electric UAV Luís Miguel Almodôvar Parada Thesis to obtain the Master of Science Degree in Aerospace Engineering Supervisor: Prof. André Calado Marta Examination Committee Chairperson: Prof. Filipe Szolnoky Ramos Pinto Cunha Supervisor: Prof. André Calado Marta Member of the Committee: Dr. José Lobo do Vale November 2016 ii Pela minha fam´ılia, por ter permanecido. iii iv Acknowledgments First of all, I would like to express my gratitude to my thesis supervisor, professor Andre´ Calado Marta, for all technical guidance, patience and moral support throughout the period of time it took me to write this document. Moving on to the extracurricular plan, a word of appreciation is due to the Autonomous Section of Applied Aeronautics (S3A). It was thanks to the work developed at this hands-on organization of students that I started gaining interest in model aircraft, which made me look at this thesis subject twice. Furthermore, I want to thank a few friends and acquaintances that helped me through my academic life. Borrowed class notes, car rides, sleepless nights working for course projects, miraculous pieces of code, etc... all genuine contributions mattered. Finally, I must dedicate this work to my family, the foundation that allowed me to harvest a higher education level. To my parents, for supporting me financially and emotionally, while respecting my decisions and daily struggles. To my grandparents, for diligently nurturing me over the years with all the resilience they could possibly seed. And last but not least, to my brother and to my sister, for being the best distractions of my life. -
Airplane Design(Aerodynamic) Prof. EG Tulapurkara Chapter-1
Airplane design(Aerodynamic) Prof. E.G. Tulapurkara Chapter-1 Chapter 1 Lecture 2 Introduction - 2 Topics 1.5 Classification of airplanes according to configuration 1.5.1 Classification of airplanes based on wing configuration 1.5.2 Classification of airplanes based on fuselage 1.5.3 Classification of airplanes based on horizontal stabilizer 1.5.4 Classification of airplanes based on number of engines and their location 1.6 Factors affecting the configuration 1.6.1 Aerodynamic considerations – drag, lift and interference 1.6.2 Low structural weight 1.6.3 Layout peculiarities 1.6.4 Manufacturing processes 1.6.5 Cost and operational economics - Direct operating cost (DOC) and Indirect operating cost (IOC) 1.6.6 Interaction of various factors 1.7 Brief historical background 1.7.1 Early developments 1.5 Classification of airplanes according to configuration This classification is based on the following features of the configuration. a) Shape, number and position of wing. b) Type of fuselage. c) Location of horizontal tail. d) Location and number of engines. Dept. of Aerospace Engg., Indian Institute of Technology, Madras 1 Airplane design(Aerodynamic) Prof. E.G. Tulapurkara Chapter-1 The different types of configurations are shown in Fig.1.2. As an exercise the student is advised to study, at this stage, various types of airplanes from Jane's all the world aircraft (Ref.1.21). Fig.1.2 Types of airplanes(cont.) Dept. of Aerospace Engg., Indian Institute of Technology, Madras 2 Airplane design(Aerodynamic) Prof. E.G. Tulapurkara Chapter-1 Fig.1.2 Types of airplanes 1.5.1 Classification of airplanes based on wing configuration Early airplanes had two or more wings e.g. -
Delft University of Technology Aerodynamic Installation Effects Of
Delft University of Technology Aerodynamic installation effects of lateral rotors on a novel compound helicopter configuration Stokkermans, Tom; Soemarwoto, Bambang; Voskuijl, Mark; Fukari, Raphaël; Veldhuis, Leo; Eglin, Paul Publication date 2018 Document Version Accepted author manuscript Published in Annual Forum Proceedings - AHS International Citation (APA) Stokkermans, T., Soemarwoto, B., Voskuijl, M., Fukari, R., Veldhuis, L., & Eglin, P. (2018). Aerodynamic installation effects of lateral rotors on a novel compound helicopter configuration. Annual Forum Proceedings - AHS International, 2018-May. Important note To cite this publication, please use the final published version (if applicable). Please check the document version above. Copyright Other than for strictly personal use, it is not permitted to download, forward or distribute the text or part of it, without the consent of the author(s) and/or copyright holder(s), unless the work is under an open content license such as Creative Commons. Takedown policy Please contact us and provide details if you believe this document breaches copyrights. We will remove access to the work immediately and investigate your claim. This work is downloaded from Delft University of Technology. For technical reasons the number of authors shown on this cover page is limited to a maximum of 10. Aerodynamic Installation Effects of Lateral Rotors on a Novel Compound Helicopter Configuration Tom Stokkermans Mark Voskuijl Leo Veldhuis PhD Candidate Assistant Professor Full Professor Delft University of Technology Delft University of Technology Delft University of Technology Delft, the Netherlands Delft, the Netherlands Delft, the Netherlands Bambang Soemarwoto Raphael¨ Fukari Paul Eglin Senior Scientist Engineer Aeromechanics senior expert Netherlands Aerospace Centre NLR Airbus Helicopters Airbus Helicopters Amsterdam, the Netherlands Marignane, France Marignane, France ABSTRACT Installation effects of the lateral rotors for a compound helicopter were investigated by means of unsteady CFD sim- ulations. -
Wind-Tunnel Investigation of the Flight Chasacteristics of a Canard
., , -. / ~ ,a ~ i t 1 1 / I -1 I' I , ,Wind-TunnelInvestigation of the Flight Chasacteristics of a Canard Genera1:Aviation Airplane Coniiguration - I Dale R. Satran j . iNA3A-22-2623 ) UIND- TUNKEL INVESTIGkTION OE 138 7 - 1 d 0 3 j IHZ ELIGHT Cii Ait ACiEiiI STILS C F A CANAtiD Fig32 AVI - G AL- A T iUN AIRP LANE CC NEPGUEATION I 60 [NASA) p csci 01A Ullcla s I H1/02 44247 , NASA NASA Technical Paper 2623 1986 Wind-Tunnel Investigation of the Flight Characteristics of a Canard General-Aviation Airplane Configuration Dale R. Satran Langley Research Center Hampton, Virginia National Aeronautics and Space Administration Scientific and Technical Information Branch Summary figuration. A 0.36-scale model was used in the free- flight investigation and was also used to obtain static A 0.36-scale model of a canard general-aviation and dynamic force data to aid in the interpretation airplane with a single pusher propeller and winglets of the free-flight test results. The free-flight tests was tested in the Langley 30- by 60-Foot Wind Tun- were conducted for angles of attack ranging from 7O nel to determine the static and dynamic stability and to 14O. The investigation included tests of the model control and free-flight behavior of the configuration. with high and low canard positions, three center-of- Model variables made testing of the model possible gravity locations, outboard wing leading-edge droop, with the canard in high and low positions, with in- winglets and a center vertical tail, and several roll- creased winglet area, with outboard wing leading- and yaw-control systems. -
Red Bull Air Racer
University of Tennessee, Knoxville TRACE: Tennessee Research and Creative Exchange Supervised Undergraduate Student Research Chancellor’s Honors Program Projects and Creative Work 5-2011 Senior Design II Final Report: Red Bull Air Racer Eric H. Kirchoff University of Tennessee - Knoxville, [email protected] Chad Sutton University of Tennessee - Knoxville Andrew Kail University of Tennessee - Knoxville Sydney Fears University of Tennessee - Knoxville Follow this and additional works at: https://trace.tennessee.edu/utk_chanhonoproj Part of the Other Aerospace Engineering Commons Recommended Citation Kirchoff, Eric H.; Sutton, Chad; Kail, Andrew; and Fears, Sydney, "Senior Design II Final Report: Red Bull Air Racer" (2011). Chancellor’s Honors Program Projects. https://trace.tennessee.edu/utk_chanhonoproj/1455 This Dissertation/Thesis is brought to you for free and open access by the Supervised Undergraduate Student Research and Creative Work at TRACE: Tennessee Research and Creative Exchange. It has been accepted for inclusion in Chancellor’s Honors Program Projects by an authorized administrator of TRACE: Tennessee Research and Creative Exchange. For more information, please contact [email protected]. Senior Design II Final Report: Red Bull Air Racer Chad H. Sutton, Eric Kirchoff, Andrew Kail, Sydney Fears Department of Mechanical, Aerospace and Biomedical Engineering University of Tennessee, Knoxville, TN, 37916 Submitted to Dr. Robert Bond May 2, 2011 1 Abstract The preliminary design process of modern aircraft is a very important process for aerospace engineers to learn. To expand on previous assignments, this capstone design project aims to be a full and in-depth analysis of the design process. The objective of this project was to design a theoretical, full-scale, pusher configuration air racer capable of competing in the Red Bull Air Race, specifically on the Budapest track.