Sintering and Mechanical Properties of Alumina-Yttrium Aluminate Composites
Total Page:16
File Type:pdf, Size:1020Kb
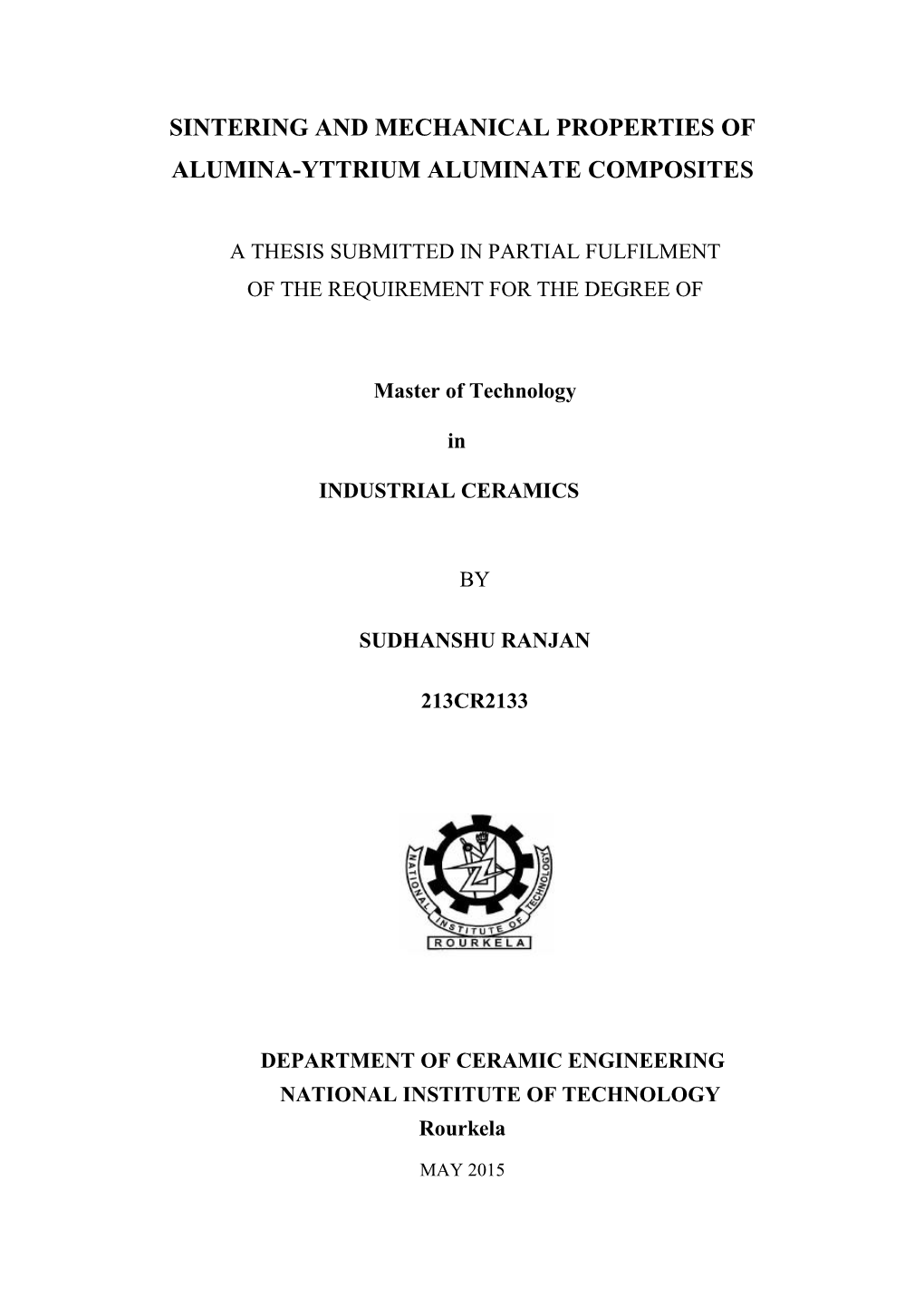
Load more
Recommended publications
-
(YAG) Laser Capsulotomy Reference Number: CP.VP.65 Coding Implications Last Review Date: 12/2020 Revision Log
Clinical Policy: Yttrium Aluminium Garnet (YAG) Laser Capsulotomy Reference Number: CP.VP.65 Coding Implications Last Review Date: 12/2020 Revision Log See Important Reminder at the end of this policy for important regulatory and legal information. Description This policy describes the medical necessity requirements for yttrium aluminium garnet (YAG) laser capsulotomy. Policy/Criteria I. It is the policy of health plans affiliated with Centene Corporation® (Centene) that YAG laser capsulotomy is medically necessary for the following indications: A. Posterior capsular opacification following cataract surgery resulting in best corrected visual acuity of 20/30 or worse associated with symptoms of blurred vision, visual distortion or glare affecting activities of daily living; B. Contraction of the posterior capsule with resulting displacement of the intraocular lens; C. Posterior capsular opacification resulting in best corrected visual acuity of 20/25 or worse, reducing the ability to evaluate and treat retinal detachment. Background YAG capsulotomy is the incision of an opaque posterior lens capsule in an aphakic or pseudophakic eye. This incision allows the capsule to retract and no longer serve as an obstruction to the passage of light through the media to the retina. The incision is performed with YAG laser. The eye examination must confirm the diagnosis of posterior capsular opacification and excludes other ocular causes of functional impairment by one of the following methods: The eye examination should demonstrate decreased light transmission (visual acuity worse than 20/30 or 20/25 if the procedure is performed to assist in the diagnosis and treatment of retinal detachment). Manifest refraction must be recorded with decrease in best-corrected visual acuity. -
Colourless Gemstones
GEMS THE gem DeteCTIVE: COLOURLess gemstONes superseded in the 1970s by a man-made gemstone called cubic zirconia that is still the most popular and common diamond imitation in modern jewellery due to its low cost, high dispersion and good hardness (8.5 on Mohs scale). Another man-made gemstone called synthetic Moissanite was introduced as a diamond simulant in the late 1990s. Although TED A synthetic Moissanite tests positive on a FFILI A diamond tester, it is easily distinguished from diamond by a property called double refraction, detected using a 10x loupe. This property is also displayed by zircon, a natural CCREESH, O’NEILS O’NEILS CCREESH, gemstone with a sub-adamantine lustre. M N N A Complicating the process of identification are treatments that may affect the value of gemstones. For example, a laser may be used to drill down to a dark diamond inclusion and remove it using acid in a process called GE COURTESY OF BREND OF COURTESY GE laser drilling. Also common is fracture filling, ma I where a high refractive-index lead glass is used to fill surface-reaching fractures to make Sparkling, colourless gemstones may People love to assume that their great ALTHOUGH them less visible. Fortunately, both of these appear similar to the naked eye but they grandma’s solitaire engagement ring SYNTHETIC treatments are easily identified using a loupe can vary significantly in identity, rarity contained a natural diamond by virtue MOISSANITE or microscope. TESTS POSITIVE and value. Making such distinctions of its age but they should think again. Some off-coloured diamonds may be ON A DIamOND requires the detective skills of a qualified Synthetically-produced sapphire, spinel and TESTER, IT CAN BE whitened using High Pressure High gemmologist. -
Crystal Preferred Orientations of Garnet
Journal of Structural Geology 26 (2004) 2089–2102 www.elsevier.com/locate/jsg Crystal preferred orientations of garnet: comparison between numerical simulations and electron back-scattered diffraction (EBSD) measurements in naturally deformed eclogites David Mainpricea,*,Je´roˆme Bascoua, Patrick Cordierb, Andre´a Tommasia aLaboratoire de Tectonophysique, CNRS & Universite´ Montpellier II, France bLaboratoire de Structure et Proprie´te´s de l’Etat Solide, CNRS & Universite´ Lille I, France Received 26 March 2003; received in revised form 8 April 2004; accepted 24 April 2004 Available online 10 July 2004 Abstract Observations of dislocations, sub-grains and elongated crystal shapes support plastic deformation of garnet in laboratory experiments and naturally deformed eclogites. To evaluate the crystal preferred orientations (CPO) of garnet formed in axial shortening, pure shear and simple shear, we performed numerical simulations of CPO development during plastic flow using the visco-plastic self-consistent model. As input for the models we use the slip systems determined by transmission electron microscopy using experimentally deformed specimens. Although in garnet 66 slip systems are available, slip on the k111l{110} system provides over 86% of the total strain in the simulations. Characteristic CPO distributions are produced for the three deformation paths, with the CPO being strongest for axial shortening and weakest for simple shear. Compared with low-symmetry minerals, the pole figure densities of garnet, which has cubic symmetry, are weak. k100l axes tend to align with the shortening direction in all three deformation modes. The simulations are compared with CPO of naturally deformed garnet from nine eclogite samples from the Alps, Norway, and Mali, which contain 20–40% garnet. -
Pulsed Laser Deposition of High-Quality Μm-Thick YIG Films on YAG
Pulsed laser deposition of high-quality μm-thick YIG films on YAG A. Sposito,1,* T. C. May-Smith,1 G. B. G. Stenning,2 P. A. J. de Groot,2 and R. W. Eason1 1Optoelectronics Research Centre, University of Southampton, SO17 1BJ, Southampton, United Kingdom 2Physics and Astronomy, University of Southampton, SO17 1BJ, Southampton, United Kingdom *[email protected] Abstract: We report the epitaxial growth of high-quality μm-thick yttrium iron garnet (YIG) films on yttrium aluminium garnet (YAG) substrates by pulsed laser deposition (PLD). The effects of substrate temperature and oxygen pressure on composition, crystallinity, optical transmission and ferromagnetic resonance (FMR) linewidth have been investigated. An FMR linewidth as low as 1.75 mT at 6 GHz was achieved by depositing YIG on YAG substrates with (100) orientation at a substrate temperature of ~1600 K and with oxygen pressure of ~1 Pa. ©2013 Optical Society of America OCIS codes: (160.3820) Magneto-optical materials; (310.1860) Deposition and fabrication. References and links 1. R. W. Eason, Pulsed Laser Deposition of Thin Films – Applications-led Growth of Functional Materials (Wiley Interscience, 2007). 2. N. A. Vainos, C. Grivas, C. Fotakis, R. W. Eason, A. A. Anderson, D. S. Gill, D. P. Shepherd, M. Jelinek, J. Lancok, and J. Sonsky, “Planar laser waveguides of Ti:sapphire, Nd:GGG and Nd:YAG grown by pulsed laser deposition,” Appl. Surf. Sci. 127-129, 514–519 (1998). 3. H. Dötsch, N. Bahlmann, O. Zhuromskyy, M. Hammer, L. Wilkens, R. Gerhardt, P. Hertel, and A. F. Popkov, “Applications of magneto-optical waveguides in integrated optics: review,” J. -
Synthesis and Characterization of Yttrium Aluminium Garnet (YAG
Processing and Application of Ceramics 1 [1–2] (2007) 69–74 Synthesis and characterization of yttrium aluminium garnet (YAG) powders Magdalena Zarzecka-Napierala*, Krzystof Haberko AGH-University of Science and Technology, Faculty of Materials Science and Ceramics, Al. Mickiewicza 30, 30–059 Kraków, Poland Received 17 September 2007; received in revised form 20 November 2007; accepted 24 November 2007 Abstract In this paper synthesis and characterization of YAG powders, prepared by a process based on complexing properties of citric acid, was reported. Infl uence of citric acid estrifi cation induced by 2-propanol or ethylene glycol on the system homogeneity was investigated. These reagents were introduced to aqueous solution of yt- trium and aluminium nitrates. A variety of powders from Al2O3-Y2O3 system with different phase composition were obtained by altering the citrate to nitrate ratio. Evolution of the powders phase composition vs. tempera- ture was investigated using DTA/TG, XRD, and FT-IR methods. The most interesting results were observed in case of the citric acid – propanol – relative nitrates system. The mole ratio of these reagents equal to 1: 2.5: 2.5 (nitrates (Al,Y): citric acid: 2-propanol) allowed to synthesize pure YAG phase powders at temperature as low as 950°C. Keywords: YAG, citric acid, citrate gel method I. Introduction homogeneous YAG or Nd: YAG powder have been ad- opted. YAG powders have been prepared traditionally In the Y2O3 – Al2O3 system, apart from the end-mem- ber phases, three compounds stable at ambient pressure by a solid state reaction [6] from the corresponding ox- ides, which requires prolonged mechanical mixing and are known: Y3Al5O12 (YAG), YAlO3 (YAP) and Y2Al4O9 (YAM), having cubic garnet, orthorombic or hexagonal extensive heat treatment at high temperature to elimi- perovskite and monoclinic symmetry structure, respec- nate intermediate phases. -
Transparent Yttrium Aluminium Garnet Obtained by Spark Plasma Sintering of Lyophilized Gels
Hindawi Publishing Corporation Journal of Nanomaterials Volume 2009, Article ID 138490, 5 pages doi:10.1155/2009/138490 Research Article Transparent Yttrium Aluminium Garnet Obtained by Spark Plasma Sintering of Lyophilized Gels M. Suarez,´ 1 A. Fernandez,´ 2 J. L. Menendez,´ 1 and R. Torrecillas1 1 Departamento de Materials Nanoestructurados, Centro de Investigacion´ en Nanomateriales y Nanotecnolog´ıa (CINN), Principado de Asturias—Consejo Superior de Investigaciones Cient´ıficas (CSIC), Universidad de Oviedo (UO), Parque Tecnologico´ de Asturias, 33428 Llanera, Asturias, Spain 2 Fundacion´ ITMA, Parque Tecnologico´ de Asturias, 33428 Llanera, Spain Correspondence should be addressed to M. Suarez,´ [email protected] Received 18 March 2009; Revised 22 May 2009; Accepted 26 June 2009 Recommended by Wanqin Jin Lyophilized YAG gel, synthesized by the coprecipitation technique, has been sintered to transparency by spark plasma sintering method at 1500◦C. Whereas conventionally dried gels show large agglomerates, over 1 μm, powders from lyophilized gels show no agglomeration with an average particle size below 100 nm. The absence of agglomerates affects on the optical properties of the sintered materials: conventionally dried powders are opaque after sintering, whereas 0.8 mm thick transparent YAG materials with in-line transmittances close to 60% at 680 nm and over 80% in the infrared range have been obtained for the lyophilized gels. Copyright © 2009 M. Suarez´ et al. This is an open access article distributed under the Creative Commons Attribution License, which permits unrestricted use, distribution, and reproduction in any medium, provided the original work is properly cited. 1. Introduction in order to obtain the pure YAG phase, but it often leads to large powders with a broad grain size distribution. -
Efficiency, Reliability, Friendship
3/24/2021 Nd:YAG Crystal Laser Rod & Slab,Yttrium Aluminium Garnet - China Bluebean HOME | ABOUT US | CONTACT US | English Efficiency, Reliability, Friendship Polarization Optics Crystal Products Optical Elements Material Data Nd: YAG Crystal UV & IR Optics Nd:YAG(Neodymiumdoped Yttrium Aluminium Garnet) laser crystal provides the laser system designer with the most versatile solid state laser source in use today. With thousands of systems in NLO Crystals daily use, Nd:YAG continues as the best of the rare earth garnet laser materials characterised by four level laser operation, permitting low threshold pulse or CW operation. Nd:YAG laser rods Laser Crystals produce efficient laser output at 1064nm. The systems designer can select from several levels of dopant concentration to optimize laser performance. Sapphire Products Nd: YAG Crystal Properties: Beamsplitters Polarizers Chemical Formula Y3Al5O12 Crystal structure Cubic Waveplates Lattice constant 12.01Å Melting point 1970°C Laser Glass Density 4.5g/cm3 Pockels Cells Reflective Index 1.82 Thermal Expansion Coefficient 7.8x106 /K <111> Faraday Rotator Crystal 14 W/m/K, 20°C Thermal Conductivity 10.5 W/m/K, 100°C High power fiber optics Mohs hardness 8.5 Stimulated Emission Cross Section 19 2 2.8x10 cm Relaxation Time of Terminal Lasing Level 30 ns +86 21 51012729 Radiative Lifetime 550 us +86 21 51685837 Spontaneous Fluorescence 230 us [email protected] Linewidth 0.6 nm Loss Coefficient 0.003 cm1 @ 1064nm Nd:YAG Specifications: Dopant 0.3~2.0(±0.1)atm% Crystal Orientation <111> -
Effects of Lasers and Their Delivery Characteristics on Machined
bioengineering Article Effects of Lasers and Their Delivery Characteristics on Machined and Micro-Roughened Titanium Dental Implant Surfaces Thomas Fenelon 1, Mahmoud M. Bakr 1 , Laurence J. Walsh 2 and Roy George 1,* 1 School of Dentistry and Oral Health, Queensland, Griffith University, Queensland 4215, Australia; [email protected] (T.F.); m.bakr@griffith.edu.au (M.M.B.) 2 School of Dentistry, The University of Queensland, Queensland 4006, Australia; [email protected] * Correspondence: r.george@griffith.edu.au; Tel.: +61-0756780751 Received: 15 June 2020; Accepted: 5 August 2020; Published: 11 August 2020 Abstract: The aim of the study was to investigate the effects of neodymium: yttrium aluminium garnet (Nd:YAG) (1064 nm) and erbium: yttrium aluminium garnet (Er:YAG) (2940 nm) laser energy on titanium when delivered with conventional optics (focusing handpieces or plain ended optical fibres) or with a conical tip. Machined and micro-roughened implant discs were subjected to laser irradiation under a variety of energy settings either dry (without water) or wet (with water). Samples were scanned using a 3D non-contact laser profilometer and analysed for surface roughness, volume of peaks and the maximum diameter of the ablated area. Conical tip designs when used with both lasers showed no surface effect at any power setting on both machined and micro-roughened implant surfaces, regardless of the irrigation condition. When used with conventional delivery systems, laser effects on titanium were dose related, and were more profound with the Nd:YAG than with the Er:YAG laser. High laser pulse energies caused surface fusion which reduced the roughness of micro-roughened titanium surfaces. -
Anderson & Steinssen
Anderson & Steinssen, Inc. Crystalline Products Company Overview Anderson & Steinssen, Inc. (Abbreviation: ANS) is one of the most reputable and largest laser crystal manufacturers in the world. Our main optical crystal products include the YAG series, which we supply to our cooperative research centers and universities. We have also successfully expanded to manufacturing NLO crystal, BIBO, LBO, KTP, etc, which are widely used in industrial, military, medical, cosmetic and other fields. ANS has a long-term commitment to improvement of and research in growth technology. At ANS, we have crystal growth technology including induction heating and resistance heating, which can meet different customers’ requirements. We are now serving customers throughout America, Korea, Canada, Japan and Germany. Crystal Products Product Name Formula Yttrium aluminium garnet YAG Neodymium-doped yttrium aluminium garnet Nd:YAG Ytterbium-doped yttrium aluminium garnet Yb:YAG Neodymium-cerium double-doped yttrium aluminium garnet (Nd,Ce):YAG Chromium (IV)-doped yttrium aluminium garnet Cr4:YAG Erbium-doped yttrium aluminium garnet Er:YAG Holmium-doped yttrium aluminium garnet Ho:YAG Samarium-doped yttrium aluminium garnet Sm:YAG Dysprosium-doped yttrium aluminium garnet Dy:YAG Holmium-chromium-thulium triple-doped yttrium aluminium Ho:Cr:Tm:YAG garnet Terbium-doped yttrium aluminium garnet Tb:YAG Thulium-doped yttrium aluminium garnet Tm:YAG Cerium(III)-doped yttrium aluminium garnet Ce:YAG Neodymium-doped yttrium lithium fluoride Nd:YLF Calcium gadolinium aluminum -
2876.Full.Pdf
[CANCER RESEARCH 43, 2876-2879, June 1983] 0008-5472/83/0043-0000$02.00 Neodymium-Yttrium Aluminium Garnet Laser Destruction of Nonsensitized and Hematoporphyrin Derivative-sensitized Tumors1 Thierry Patrice, Marie-Françoise Le Bodic,2 Louis Le Bodic, Thierry Spreux, GérardDabouis, and Luc Hervouet DéparlementLaser CHU Nantes [T. P., L L B., T. S., G. D., L H.] and Laboratoires d'Anatomie Pathologique A et B [M-F. L. B.], Facultéde Médecine,1 rue Gaston Veil, 44035 Nantes, France ABSTRACT in darkness. The solution for injection was prepared by mixture of one part of HPD and 50 parts of 0.1 N soda solution left at room temperature The injection of hematoporphyrin derivative (5 mg/kg ¡.v.) for 1 hr. The pH was adjusted at 7.2 to 7.4 with the addition of followed 24 hr later by a neodymium-yttrium aluminium garnet hydrochloric acid solution and made isotonic by the addition of sodium laser irradiation shows the destruction of CX1 tumors grafted on chloride. The final 5-mg/ml solution was sterilized by filtration through a Millipore filter and kept in darkness at -20° until used. nude mice. This acidophilic necrosis occurred with a significantly The energy was produced by a Nd-YAG laser (Cilas-Marcoussis increased frequency in tumors treated by hematoporphyrin de rivative injection and irradiated with the neodymium-yttrium alu Laboratory, 91460, France) emitting in the near IR (1.06 //m). This laser is a solid-state laser commonly used in our medical applications of laser minium garnet laser as compared with noninjected but irradiated therapy. -
Hilger Crystals
Hilger Crystals State-of-the-art scintillation and detection solutions FS 613925 EMS 694354 OHS 718450 for security, defence, and medical industries ABOUT Hilger Crystals is an ISO 9001:2015, ISO 14001:2015, and ISO 45001:2018 certified company with a long-established history and proven reputation producing high-quality synthetic crystals for infrared spectroscopy and X- and gamma-ray detection. Products can be built to custom design requirements and supplied within short lead times. COLLABORATE TO CREATE Hilger Crystals prides itself in developing crystal materials in conjunction with its customers requirements. This ensures that customers receive product that is optimized for their specific application. This collaboration has been proven successful for both academic projects and commercial engagements. SCINTILLATION CRYSTALS We produce an extensive range of scintillation crystals chosen for their high density, excellent light output and short decay constants. Our scintillation crystals are used in X- and gamma-ray detectors and other non-destructive testing, such as baggage scanning systems, medical applications, and academic research. High-quality raw materials and a strictly controlled growth environment ensure that all Hilger scintillation crystals achieve the highest standard required for low-background applications in research and critical commercial applications. Our crystals can be supplied as a single unit or as a complete assembly. IMAGING ARRAYS Our linear and two-dimensional arrays vary in size from 5mm to 200mm, and can be coupled directly to a position sensitive PMT, CCD array, SiPM, or linear photodiode to form a complete assembly. +44(0) 1843-231166 hilger.dynasil.com Hilger Crystals State-of-the-art scintillation and detection solutions FS 613925 EMS 694354 OHS 718450 for security, defence, and medical industries INFRARED MATERIALS The various optical materials available from Hilger Crystals are utilized as windows and beamsplitters for infrared spectroscopy. -
YTTRIUM ALUMINIUM GARNET OPTICAL CRYSTAL According to Regulation (EC) No.1907/2006 (REACH) Revision 2016 : Issued 30Th August 2016 1
SAFETY DATA SHEET YTTRIUM ALUMINIUM GARNET OPTICAL CRYSTAL According to Regulation (EC) No.1907/2006 (REACH) Revision 2016 : Issued 30th August 2016 1. IDENTIFICATION OF THE SUBSTANCE AND THE COMPANY 1.1. PRODUCT IDENTIFIERS: Product Name: Yttrium Aluminium Oxide (Pentaaluminium triyttrium dodecaoxide) Synonyms, Trade Names: YAG, Yttrium Aluminium Garnet, Yttorgarnet, Y3Al5O12 1.2. RELEVANT IDENTIFIED USES OF THE SUBSTANCE OR MIXTURE AND USES ADVISED AGAINST Identified Uses: Optical Material for manufacture of Optical Components. 1.3. DETAILS OF THE SUPPLIER OF THE SAFETY DATA SHEET Company: CRYSTRAN LTD, 1 Broom Road Business Park, Poole, Dorset UK BH12 4PA +44 1202 307650 1.4. EMERGENCY TELEPHONE NUMBER Emergency Phone: +44 1202 307650 (Monday to Friday 08:30 to 17:00 GMT) Emergency Action: In the event of a medical enquiry involving this product, please contact your doctor or local hospital accident and emergency department. The attending health professional will be able to contact the National Poisons Information Service. 2. HAZARDS IDENTIFICATION 2.1. CLASSIFICATION OF THE SUBSTANCE OR MIXTURE No Hazardous Product as specified in Directive 67/548/EEC. 2.2. LABEL ELEMENTS Precautionary Statements: P262 Do not breathe dust/fume/gas/mist/vapours/spray. 2.3. OTHER HAZARDS None 3. COMPOSITION/INFORMATION ON INGREDIENTS 3.1. SUBSTANCES Component Name CAS number % EC number (EINECS) EU index UN number Yttrium Aluminium Oxide 12005-21-9 100% 234-465-8 - - 4. FIRST AID MEASURES 4.1. DESCRIPTION OF FIRST AID MEASURES GENERAL: Consult a doctor for specific advice. EYES: Irrigate thoroughly with water for at least 15 minutes. If discomfort persists obtain medical attention.