Volume 10, Issue 3, March 2021
Total Page:16
File Type:pdf, Size:1020Kb
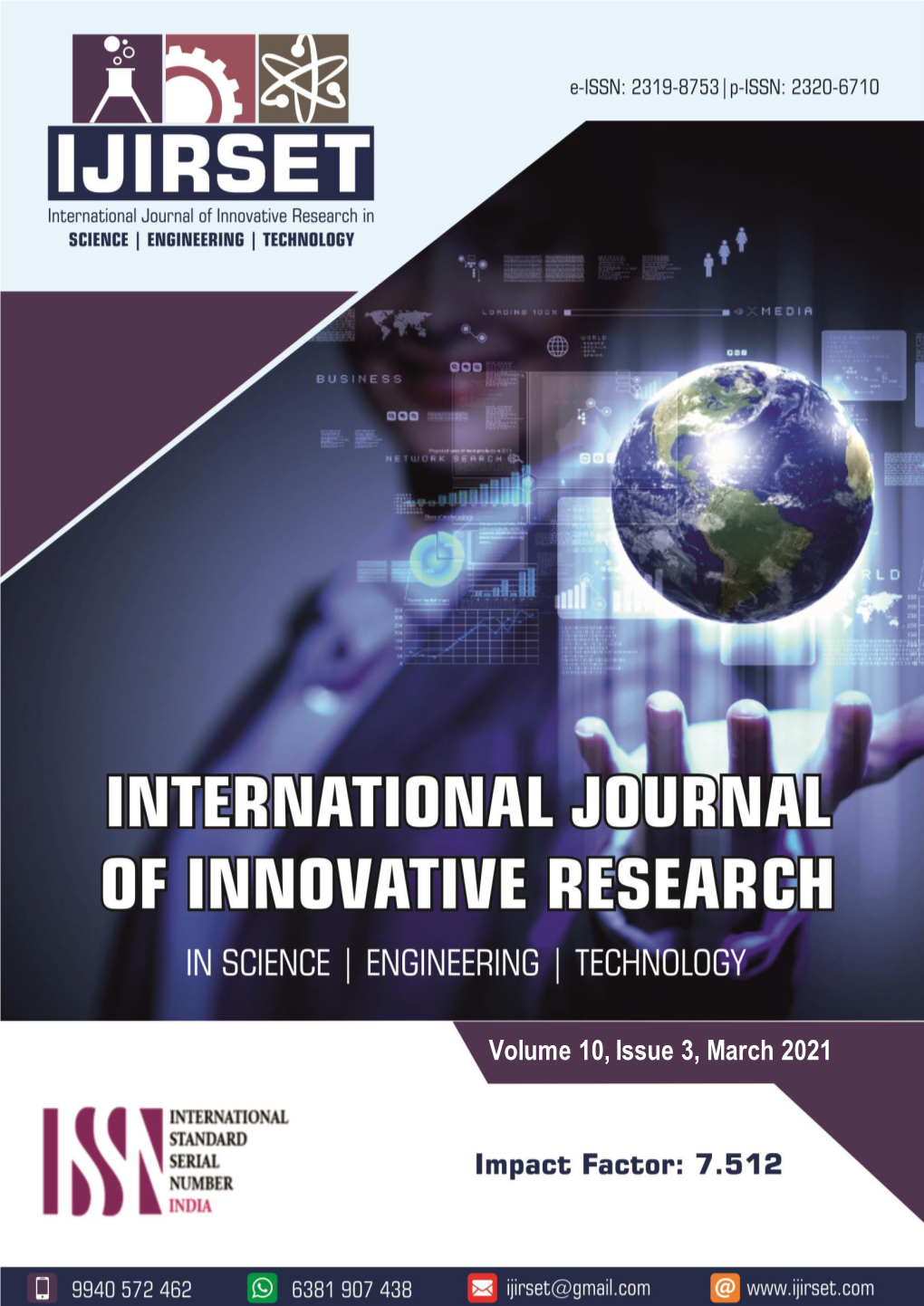
Load more
Recommended publications
-
The Use of Trend Forecasting in the Product Development Process
THE USE OF TREND FORECASTING IN THE PRODUCT DEVELOPMENT PROCESS C TWINE PhD 2015 THE USE OF TREND FORECASTING IN THE PRODUCT DEVELOPMENT PROCESS CHRISTINE TWINE A thesis submitted in partial fulfilment of the requirements of the Manchester Metropolitan University for the degree of Doctor of Philosophy Department of Apparel / Hollings Faculty the Manchester Metropolitan University 2015 Acknowledgements The completion of this research project owes a great deal of support and encouragement of my supervisory team, Dr. David Tyler, Dr. Tracy Cassidy as my adviser and the expert guidance of my Director of Studies Dr. Ji-Young Ruckman and Dr. Praburaj Venkatraman. Their experience and commitment provided inspiration and guidance throughout those times when direction was much needed. I am also indebted to all those who participated in the interviewing process which aided the data collection process and made this research possible. These included personnel from the trend forecasting agencies Promostyl, Mudpie, Trend Bible and the senior trend researchers from Stylesight, and Trendstop. The buyers and designers from the retailers Tesco, Shop Direct, Matalan, River Island, Mexx, Puma, Bench, Primark, H&M, ASOS and Boohoo. Thank you to my lovely family, David and Florence for their support and encouragement when I needed it most. i Declaration No portion of the work referred to in this thesis has been submitted in support of an application for another degree or qualification of this or any other university or institution of learning. Copyright© 2014 All rights reserved No part of this thesis may be reproduced, stored in a retrieval system, or transmitted in any form or by any means, electronic, mechanical, photocopying, recording or otherwise, without prior permission of the author. -
TTIP and Financial Services
EPRS | European Parliamentary Research Service TTIP and Financial Services Keysource by Baeverstroem, Jan | Posting date: 15/06/2015 According to a study from the Congressional Research Service: EU-U.S. Economic Ties: Framework, Scope, and Magnitude , February 2014, total EU foreign direct investments in the United States amounted to $1,647.6 billion at the end of 2012 (62.2% of total). Out of this, $356.8 billion (21.7%) was in banking and other financial services. While the EU has supported financial services inclusion in TTIP, in the US, Members of the Congress disagree whether or not to include financial services in these negotiations. Business groups on both sides of the Atlantic, including the Trans-Atlantic Business Council (TABC), support the inclusion of financial services in the negotiations. Against it are consumer organisations, like Transatlantic Consumer Dialogue (TACD) who have voiced fears that TTIP would deregulate the financial services or harmonise rules towards the lowest common denominator. In June 2014, Commissioner Barnier reiterated the need for a framework within the TTIP to handle differences between the EU and the US, but later the same month, U.S. Treasury Secretary restated that "financial regulatory cooperation should continue in existing and appropriate global fora". US fears a dilution of safeguards created with the 2010 Dodd-Frank Act . In July 2014 US financial services associations published a statement underlining the importance of including financial services in TTIP. In June a restricted document from 5 March was leaked: Regulatory Co-operation on Financial Regulation in TTIP (to be included to the EU proposal for services and investment chapter, Section VI – Financial services). -
Third Report on Potentially Trade Restrictive Measures
Report on potentially trade restrictive measures 12 June 2009 Introduction and main findings This is the third report on new potentially trade restrictive measures planned or implemented by our trading partners in the face of the economic crisis. The information used in this report has been primarily gathered by European Commission Delegations / Market Access Teams in G-20 countries and other key markets through their local monitoring exercises1, as well as from business sources providing specific contributions. The report provides an overview of the data received since mid-March 2009. It shows that trade restrictive measures continue to be on the rise, including in some G20 members. Moreover, the types of measures identified have become more complex and diversified, notably when they are part of broader stimulus packages. Therefore, increased alertness, as well as political determination to use all opportunities to address the measures put in place so far, remains all the more necessary at this stage. The world-wide economic downturn has been dramatic since the start of the financial crisis last autumn. 2009 seems set to be the first year in which global trade will decline year-on-year since the early 1980s. Although more indications continue to emerge pointing to the gradual stabilisation of the financial sector (stock market indices, lower risk spread), the signals from the real economy continue to be at best mixed. Despite some evidence of a slowdown in the pace of decline, the evolution of exports and imports of all the major trading countries remains very negative. Moreover, the fact that unemployment continues to rise in most major economies, means that the global recovery is still not fully underway. -
Summary of April 13, 2000, Meeting Between the Nrc Staff And
UNITED STATES * NUCLEAR REGULATORY COMMISSION WASHINGTON, D.C. 20555-0001 NIay 1, 20000 MEMORANDUM TO: Cynthia A. Carpenter, Chief Generic Issues, Environmental, Financial and Rulemaking Branch Division of Regulatory Improvement Programs, NRR FROM: Joseph L. Birmingham, Project Manager Generic Issues, Environmental, Fi1ancial and Rulemaking Branchd -< - . Division of Regulatory Improvement Programs, NRR SUBJECT: SUMMARY OF APRIL 13, 2000, MEETING BETWEEN THE NUCLEAR REGULATORY COMMISSION STAFF AND THE NUCLEAR ENERGY INSTITUTE On April 13, 2000, staff members of the Nuclear Regulatory Commission (NRC) met with representatives of the Nuclear Energy Institute (NEI) and industry to discuss NEI's draft of their probabilistic post-fire safe shutdown fire-induced circuit failure analysis methodology. Meeting attendees are listed in Attachment 1. Handouts used by NEI during the meeting are included in Attachment 2. ,Leon Whitney and Eric Weiss (NRC) began the meeting by stating that the purpose of the meeting was to discuss NEI's draft probabilistic post-fire safe shutdown fire-induced circuit failure analysis methodology. This opening statement was followed with introductions of those in attendance. David Modeen and Fred Emerson (NEI) then began a discussion by identifying the industry objectives and summarizing the industry actions since the last meeting. They described the NEI probabilistic methodology and its intended application, and indicated that the methodology was to be part of an "integrated" industry approach (i.e., the NEI method used the Boiling Water Reactors Owners Group (BWROG) deterministic methodology as a guidance document "template"), but that the deterministic BWROG methodology would remain a "stand alone" document. NRC asked how the various pieces of the methodology were integrated with the BWROG document. -
Data Collection Survey on Investment Promotion and Export Promotion in the Republic of the Union of Myanmar
The Republic of the Union of Myanmar Data Collection Survey on Investment Promotion and Export Promotion in the Republic of the Union of Myanmar Final Report May 2019 Japan International Cooperation Agency (JICA) Koei Research & Consulting Inc. IL JR 19-041 The Republic of the Union of Myanmar Data Collection Survey on Investment Promotion and Export Promotion in the Republic of the Union of Myanmar Final Report May 2019 Japan International Cooperation Agency (JICA) Koei Research & Consulting Inc. Project Photo Gallery (1/2) Meeting for SOP Formulation Training of DICA Personnel Myanmar Investment Seminar in Tokyo Investment Promotion Mission to Japan MIPP Consultation Meeting in Nay Pyi Taw MIPP Launching Ceremony (Yangon) Project Photo Gallery (2/2) Potential Industry Study Myantrade Export Promotion Workshop Myantrade Pilot Project (Overseas Market Study) Myantrade Pilot Project (Trade Fair Management) Workshop on Branding for Export Promotion Executive Summary 1. Outline of the Project Background Since the inauguration of the civilian government in March 2011, the Government of Myanmar has been promoting open-economy policy aimed at transition to a market economy and developing infrastructure. It has attached much importance onto foreign direct investment (FDI) in order to spur job creation and income growth. In Myanmar, the Directorate of Investment and Company Administration (DICA) is in charge of investment promotion and investment application. The Japan International Cooperation Agency (JICA) supported DICA to formulate the Long-term Foreign Direct Investment Promotion Plan (FDIPP). DICA requested JICA’s assistance for institutional capacity development of DICA and enhancement of one-stop service (OSS) at DICA. JICA supported the Ministry of Commerce (MoC) for export development. -
Alternative Animal Welfare Responses: Options and Implications for Producers and Industry at Large
AlternativeAlternative AnimalAnimal WelfareWelfare Responses:Responses: OptionsOptions andand ImplicationsImplications forfor ProducersProducers andand IndustryIndustry atat LargeLarge Glynn Tonsor Dept. of Agricultural, Food, and Resource Economics Michigan State University State-Wide Pork Industry Information Meetings March 23-26, 2009 OverviewOverview QuickQuick overviewoverview ofof consumerconsumer researchresearch OutlineOutline ofof industryindustry && producerproducer optionsoptions Consumer Group Sourced Articles 800 ConsumerLexis Group Sourced Articles 700 600 -Nexis Media Indices: 500 Nexis Media Indices: 400 Pork Consumer Group - LN-Media Indices (2003- Poultry 300 Beef 200 Westland/Hallmark; Chino, CA Event: 100 0 2003 2003 2003 2008) 2003 2004 2004 2004 2004 2005 2005 2005 2005 2006 2006 2006 2006 2007 2007 2007 2007 2008 2008 2008 2008 LexisLexis--NexisNexis MediaMedia Indices:Indices: IndustryIndustry SourcedSourced ArticlesArticles Industry Source (2003-2008) 40 35 30 Pork Poultry Beef 25 20 15 10 5 0 2003 2003 2003 2003 2004 2004 2004 2004 2005 2005 2005 2005 2006 2006 2006 2006 2007 2007 2007 2007 2008 2008 2008 2008 PerceivedPerceived AnimalAnimal WelfareWelfare InformationInformation AccuracyAccuracy (1=Very(1=Very Inaccurate,Inaccurate, ……,, 7=Very7=Very Accurate)Accurate) The Humane Society of the U.S. (HSUS) 4.93 University Scientists/Researchers 4.47 People for the Ethical Treatment of Animals (PETA) 4.22 National Milk Producers Federation (NMPF) 4.20 U.S. Poultry & Egg Association 4.18 National Cattlemen's Beef Association (NCBA) 4.11 United Egg Producers (UEP) 4.10 National Pork Producers Council (NPPC) 4.07 State Governmental Agencies 4.00 Federal Governmental Agencies 4.00 PerceivedPerceived AbilityAbility toto InfluenceInfluence andand AssureAssure AnimalAnimal WelfareWelfare (1=Very(1=Very LowLow Ability,Ability, ……,, 7=Very7=Very HighHigh Ability)Ability) Farmer/Grower 5.33 Government Inspectors/Regulators 5.16 The Humane Society of the U.S. -
Value in the Aboriginal and Torres Strait Islander Souvenir Art Sector
Value in the Aboriginal and Torres Strait Islander Souvenir Art Sector Brendan Mahoney Doctorate of Philosophy University of Western Sydney 2011 © Brendan Mahoney, 2011 Abstract The Aboriginal and Torres Strait Islander souvenir art sector with its wide range of products has a long and significant history and is economically important within the industry. However, the full scope of this significance has not been adequately recognised in the academic literature. While the sector’s substantial economic contribution is acknowledged in some policy documents, these considerations are generally brief, with little analysis of any value the sector might generate in the social and cultural spheres. This neglect of souvenir art is driven by two key factors: its low status in the social hierarchy of the arts (Bourdieu, 1984), and the difficulty of finding analytical tools capable of assessing the complexities of the sector without falling into assumptions about the cultural value and ‘authenticity’ of souvenir art. In an attempt to redress this, the thesis develops both a theoretical framework that aims to adequately capture the social, cultural and economic significance of the sector, and analytical tools that cover the broad set of discourses that comprise the subject. As such, I have adapted the insights of modern and critical political economy theories to analyse the distribution of economic capital, and broadened these theories to encompass Pierre Bourdieu’s (1984) concepts of social and cultural capital. This combination of theories forms a broad-ranging theoretical framework that accommodates economic capital and the qualitative discursive constructions that inform amounts of social and cultural capital within the same system. -
Boctor of ^F)Flo)B;Opi)P^ \\
A STUDY OF GOVERNMENT POLICY AND STRUCTURAL CHANGES IN TOURISM SECTOR SINCE 1991 ABSTRACT . THesis Suomittedfor the award of the degree of Boctor of ^f)flo)B;opi)p^ \\ P^^ COMMERCE*^ (By SAJWRCENA ATHAR UNDER THE SUPERVISION OF Prof. NAFEES BAIG r- h^s) DEPARTMENT OF COMMERCE ALIGARH MUSLIM UNIVERSITY AUGARH (INDIA) 2003 V' *'"'•/ 'b 'C.-' ABSTRACT "A study of Governme"* Policy and Structural Changes in Tourism Sector Since 1991" The present studv entitled "A study of Government Policy and Structural Changes ir' Tourism Sector since 1991", is a modest attempt to examine tl^® limitations in the policy and plans of the Government of India \0 relation to the Tourism industry, and to study the structural changes that are required for the development of tourism industry in Ind'^- Tourism as a ph^^iomenon has been in existence since ancient times. But the trave' ^^ early days was largely unconscious and rather a simple affair ^^^^ ^^^ sophisticated travel of the modern days. The main moti^® ^^i" ^^® travel in the ancient time was trade and commerce but in ^^^ present scenario, recreation, enjoyment, relaxation have taken ^he place of trade and commerce. The invention o^ money and the increased development of trade and commerce i^ about 4000 B.C. marks the beginning of the modern era of travel a""^ tourism. Romans have the honour of being the first ones to start ^^^ phenomenon of travel, as they had good communication systeni a"d their empire was highly secured and they had very good netwo'''^ ^^ roads. Besides this Romans even had 1 tourist literature giving details about the routes, distance and journey time on horses. -
Environmentalism Contained: a History of Corporate Responses to the New Environmentalism
ENVIRONMENTALISM CONTAINED: A HISTORY OF CORPORATE RESPONSES TO THE NEW ENVIRONMENTALISM Joe Greene Conley II A DISSERTATION PRESENTED TO THE FACULTY OF PRINCETON UNIVERSITY IN CANDIDACY FOR THE DEGREE OF DOCTOR OF PHILOSOPHY RECOMMENDED FOR ACCEPTANCE BY THE PROGRAM IN HISTORY OF SCIENCE NOVEMBER 2006 UMI Number: 3236171 UMI Microform 3236171 Copyright 2006 by ProQuest Information and Learning Company. All rights reserved. This microform edition is protected against unauthorized copying under Title 17, United States Code. ProQuest Information and Learning Company 300 North Zeeb Road P.O. Box 1346 Ann Arbor, MI 48106-1346 © Copyright by Joe Greene Conley II, 2006. All rights reserved. Abstract This dissertation describes how affected industries responded to the new environmentalism that emerged as a potent political and cultural force in late-twentieth- century America. Through a series of case studies, it traces how large corporations linked to pollution or toxics problems sought to contain the broad environmental agenda embodied in the landmark environmental laws of the 1970s. These companies and trade associations used public relations and advertising campaigns to shape popular perceptions of industrial environmental impacts. They also employed a variety of tactics to strategically manage scientific information on alleged harms, to inject cost and feasibility considerations into federal environmental laws and the regulatory process, and to challenge the policies used by federal regulators to estimate environmental risks. Drawing on internal corporate documents, records of public relations and advertising campaigns, as well as more traditional sources, this dissertation argues that affected industries were a driving force in moving the discourse of environmental politics toward an increasingly narrow, more technical language of cost-benefit analysis, risk assessment, and risk-benefit balancing. -
University of Southern Denmark Branding an Industry? Bajde, Domen
University of Southern Denmark Branding an Industry? Bajde, Domen Published in: The Journal of Brand Management DOI: 10.1057/s41262-019-00152-y Publication date: 2019 Document version: Accepted manuscript Citation for pulished version (APA): Bajde, D. (2019). Branding an Industry? The Journal of Brand Management, 26(5), 497-504. https://doi.org/10.1057/s41262-019-00152-y Go to publication entry in University of Southern Denmark's Research Portal Terms of use This work is brought to you by the University of Southern Denmark. Unless otherwise specified it has been shared according to the terms for self-archiving. If no other license is stated, these terms apply: • You may download this work for personal use only. • You may not further distribute the material or use it for any profit-making activity or commercial gain • You may freely distribute the URL identifying this open access version If you believe that this document breaches copyright please contact us providing details and we will investigate your claim. Please direct all enquiries to [email protected] Download date: 25. Sep. 2021 This is a post-peer-review, pre-copyedit version of an article published in Journal of Brand Management. The final authenticated version is available online at: http://dx.doi.org/10.1057/s41262-019-00152-y Branding an Industry? Conceptual development and relevance “The food industry is under full scale assault. The crisis is global.” (Rotten, Netflix documentary series) “Drones mean innovation, new services for citizens, new business models and a huge potential for economic growth. We need the EU to be in the driving seat...” (Violeta Bulc, European Commissioner for transport) An established industry is struggling to defend its image in the aftermath of a “full scale assault”. -
American University Department of Economics
American University Department of Economics ECON-200-09 Microeconomics Spring 2009 Tuesday-Friday 9:55-11:10 AM, Ward 3 Dr. Robert Lerman Office Hours: Room 115, Roper Hall Tuesday 5:30-7:00 PM Telephone: x3761, (202) 261-5676 Friday 11:30 AM-1:00 PM, [email protected] and by appointment General Education: Econ-200, Microeconomics, is a second level course that, when taken together with Econ-100 (Macroeconomics), satisfies the General Education requirement for Curricular Area 4, Social Institutions and Behavior. Course Objectives: This course presents an economic approach to thinking about how and why modern economies work and about making rational decisions about scarce resources. Microeconomics provides a disciplined way to think about tradeoffs, about the outcomes of interactions among economic actors, and about how incentives affect behavior. The focus is on the operations of a market economy as well as the interaction between markets and government. Microeconomic analysis offers a framework for judging the effectiveness of alternative policies and institutions and provides guidelines for thinking about personal financial decisions. It yields answers to “big-think” and “little-think” questions, such as: Big think What are the microeconomic elements driving the financial crisis? In what ways does the financial and economic crisis call into question the effectiveness of the market? In what ways do markets yield socially optimal results? What corrections to market outcomes yield improved economic outcomes? What difficulties are mortgage and housing markets facing? What caused gas prices to rise and fall sharply in 2008? Does the expanding international trade help or hurt U.S. -
Data Collection and Confirmation Study on Private Sector Development in Nepal
Data Collection and Confirmation Study on Private Sector Development in Nepal FINAL REPORT March 2013 JAPAN INTERNATIONAL COOPERATION AGENCY UNICO INTERNATIONAL CORPORATION 4R JR 13-022 Data Collection and Confirmation Study on Private Sector Development in Nepal FINAL REPORT March 2013 JAPAN INTERNATIONAL COOPERATION AGENCY UNICO INTERNATIONAL CORPORATION Table of Contents Introduction Summary of Recommendation Chapter 1 Socioeconomic Conditions in Nepal 1.1 General Background ................................................................................................... 1-1 1.1.1 Current Status ..................................................................................................... 1-1 1.1.2 Central and Local Government Organizations ................................................... 1-5 1.1.3 Educational System and the Current State of Education .................................... 1-8 1.2 Economic and Social Conditions ............................................................................. 1-11 1.2.1 Macroeconomic Trend ..................................................................................... 1-11 1.2.2 Changes in Industrial Structure ........................................................................ 1-12 1.2.3 Labor Market and Social Development ............................................................ 1-14 1.3 Issues identified from Macroeconomic Indicators ................................................... 1-20 1.3.1 Macroeconomic and Development Issues .......................................................