Design of Special Plastic Bearings and Their Application in Renewable Energy Conversion System Yongjun Dong1,2, Wanqiang Zhu1,2, Xueming Zhang1,2 and Jingfu Guo*,1,2
Total Page:16
File Type:pdf, Size:1020Kb
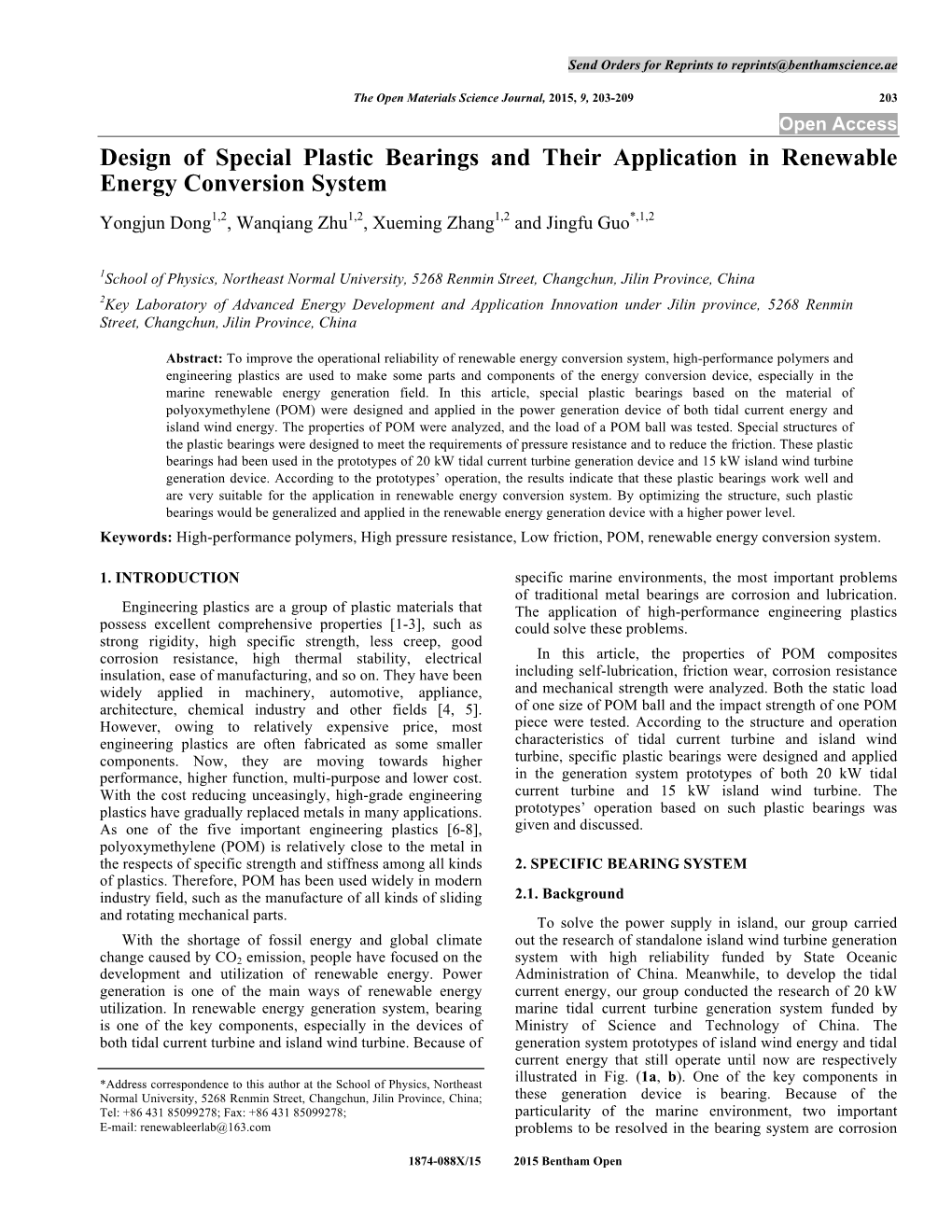
Load more
Recommended publications
-
Mounting and Dismounting of Rolling Bearings
Mounting and Dismounting of Rolling Bearings Schaeffler Technologies AG & Co. KG Every care has been taken to ensure the Georg-Schäfer-Straße 30 correctness of the information contained 97421 Schweinfurt in this publication but no liability can be Germany accepted for any errors or omissions. We Internet www.fag.com reserve the right to make technical changes. E-Mail [email protected] In Germany: © Schaeffler Technologies AG & Co. KG Phone 0180 5003872 Issued: 2012, June Fax 0180 5003873 This publication or parts thereof may not be From other countries: Phone +49 9721 91-0 reproduced without our permission. WL 80100/3 EA / 2012062 / Printed in Germany by kraus by 80100/3 EA / 2012062 Printed in Germany WL Fax +49 9721 91-3435 WL 80 100/3 EA Bearings Rolling of and Dismounting Mounting 80 100/3 EA WL Selection of FAG Publications The following publications are selected from the numerous FAG publications available. Further information on request. Catalogue WL 41520 FAG Rolling Bearings Publ. No. WL 00106 W.L.S. Rolling Bearing Learning System Publ. No. WL 80102 How to Mount and Dismount Rolling Bearings Hydraulically Publ. No. WL 80103 FAG Hydraulic Nuts Publ. No. WL 80107 FAG Induction Heating Equipment Publ. No. WL 80111 Rolling Bearing Mounting Cabinet and Mounting Sets – A fundamental course for vocational training Publ. No. WL 80123 All about the Rolling Bearing – FAG Training Courses on Rolling Bearings Theory and Practice Publ. No. WL 80134 FAG Video: Mounting and Dismounting of Rolling Bearings Publ. No. WL 80135 FAG Video: Hydraulic Methods for the Mounting and Dismounting of Rolling Bearings Publ. -
Hybrid Ceramic Ball Bearings
BEARING SPECIFIC BSA website Follow us on TOPICS BEARING BRIEFS Bearing Installation & Fitting Hybrid Ceramic Ball Bearings Bearing Repair Hybrid Ceramic Ball Bearings Linear Bearings Plane Bearings Seal Selection Spherical Plain Bearings Vibration Analysis Wear Sleeves and Other Shaft Repair Options Planetary Roller Screws The term “hybrid ceramic ball bearing” normally refers to a bearing assembly consisting of inner and outer rings of standard bearing steel, with silicon nitride (Si3N4) ceramic Bearings for the Food & balls. For some applications, the properties of the bearing with ceramic balls offer Beverage Industry functional improvements in several different areas over a conventional all-steel bearing. Split Roller Bearing There is a very significant cost penalty for the hybrid ceramic design that largely limits Technology its present-day use to certain high-end applications. However, this cost gap is expected to shrink over time with advances in ceramic ball manufacturing technology. Bearing Mounting Tools Bearings for Machine Tool Spindles BEARING INDUSTRY One of the predominant present-day applications for hybrid bearings is angular INFORMATION contact sets for high-speed machine tool spindles. This application utilizes some of the key properties of the ceramic balls compared to steel: Bearing Standards Organizations • Lower mass. The mass of a ceramic ball is about 40% of that of a steel ball of the same size. This Brief History of Bearings means the hybrid ceramic bearing operates with The Domestic Bearing less friction, less ball skidding, lower moment Industry: Investing in the from gyro-spin, and therefore, lower operating Future temperature for a given speed, and higher limiting History of Adhesives speed for a given size – by a margin of 20% or more. -
Rolling Bearings and Seals in Electric Motors and Generators
Rolling bearings and seals in electric motors and generators ® SKF, @PTITUDE, BAKER, CARB, DUOFLEX, DURATEMP, ICOS, INSOCOAT, MARLIN, MICROLOG, MONOFLEX, MULTILOG, SEAL JET, SKF EXPLORER, SYSTEM 24 and WAVE are registered trademarks of the SKF Group. © SKF Group 2013 The contents of this publication are the copyright of the publisher and may not be reproduced (even extracts) unless permission is granted. Every care has been taken to ensure the accuracy of the information contained in this publication but no liability can be accepted for any loss or damage whether direct, indirect or consequential arising out of the use of the information contained herein. PUB 54/P7 13459 EN · August 2013 This publication supersedes publication 5230 E and 6230 EN. Certain image(s) used under license from Shutterstock.com. 1 Rolling bearings in electric machines 1 2 Bearing systems 2 3 Seals in electric machines 3 4 Tolerances and fits 4 5 Lubrication 5 6 Bearing mounting, dis mounting and motor testing 6 7 Bearing damage and corrective actions 7 8 SKF solutions 8 Rolling bearings and seals in electric motors and generators A handbook for the industrial designer and end-user 2 Foreword This SKF applications, lubrication and maintenance handbook for bearings and seals in electric motors and generators has been devel oped with various industry specialists in mind. For designers of electric machines1), this handbook provides the information needed to optimize a variety of bearing arrangements. For specialists working in various industries using electric machines, there are recommendations on how to maximize bearing service life from appropriate mounting, mainten ance and lubrication. -
Rolling Bearing Failure Analysis
Rolling Bearing Failure Analysis Contents 1. BEARING FAILURE ANALYSIS 3 1.1 DETERMINATION OF OPERATING DATA 3 1.2 LUBRICANT SAMPLING 4 1.3 INSPECTION OF THE BEARING ENVIRONMENT 4 1.4 ASSESSMENT OF BEARING IN MOUNTED CONDITION 5 1.5 DISMOUNTING THE DAMAGED BEARING 5 1.6 ASSESSMENT OF THE COMPLETE BEARING 5 1.7 ASSESSMENT OF BEARING COMPONENTS 6 1.8 ROLLING BEARING DAMAGE SYMPTOMS AND THEIR CAUSES 7 2. ROLLING BEARING DAMAGE 9 2.1 DAMAGE RELATING TO BEARING RINGS 9 2.1.1 FRETTING CORROSION 10 2.1.2 TRACKS IN THE CASE OF INADEQUATE LUBRICATION 11 2.1.3 TRACKS IN THE CASE OF CONTAMINATION IN BEARING OR LUBRICANT 12 2.1.4 UNUSUAL TRACKS WITH DETRIMENTAL RADIAL PRELOAD 13 2.1.5 TRACKS WITH OVAL DEFORMATION 14 2.1.6 DETRIMENTAL AXIAL PRE-LOAD 15 2.1.7 TRACKS WITH MISALIGNMENT 16 2.1.8 FATIGUE OF ROLLING BEARINGS DUE TO MISALIGNMENT 17 2.1.9 FATIGUE AS A RESULT OF POOR LUBRICATION 18 2.1.10 CORROSION 19 2.1.11 FALSE BRINELLING 20 2.1.12 PASSAGE OF ELECTRIC CURRENT 21 2.1.13 RING FRACTURES 22 2.1.14 SLIPPAGE TRACKS 24 2.1.15 SCORE MARKS 25 2.1.16 DAMAGE DUE TO OVERHEATING 26 2.1.17 ASSESSMENT OF LIP CONTACT 27 2.2 DAMAGE RELATING TO BEARING CAGES 28 2.2.1 CAGE WEAR DUE TO STARVED LUBRICATION AND CONTAMINATION 28 2.2.2 WEAR DUE TO EXCESS SPEED 28 2.2.3 WEAR DUE TO ROLLER SKEWING 29 2.2.4 WEAR IN BALL BEARING CAGES DUE TO TILTING 30 2.2.5 CAGE FRACTURE 31 2.2.6 DAMAGE DUE TO INCORRECT MOUNTING 31 Rolling Bearing Failure Analysis 1. -
Plastic Bearings That Revolve Around Your Needs
NON-CORROSIVE n NON-MAGNETIC n LIGHTWEIGHT Plastic bearings that revolve around your needs. FROM MAGNUS MOBILITY SYSTEMS ISO 9001-2008 Certified Plastic bearings that revolve around your needs We go to extremes to make things move. As suppliers of the highest quality plastic bearings and housings, we offer the largest selection of in-stock items and the ability to custom fabricate to your exact specifications – in quantities as low as one to over one million! A perfect fit Our business revolves around our customers’ needs. We have lit- erally thousands of standard and non-standard parts in-stock – in both inch and metric sizes. That means quick delivery – and less downtime for your equipment. Available inventory isn’t the only thing that sets us apart. Our experience and reliability is unmatched in the industry – from finding the perfect replacement part…to custom engineering a new design for an OEM…to selecting the right material for your environment - our people have the knowledge to keep your equipment running smoothly. Not all bearings are created equal It takes tough bearings to withstand a wet, corrosive environment – and we’ve got ‘em! Our plastic bearings are lightweight and will go where no conventional bearing can. Jilson bearings are engineered using materials specially matched to your application, to keep your equipment running at optimal performance. When combined with stainless steel or non-metallic balls, made of polymer or glass, they are completely non-magnetic. A great alternative when magnetic distortion must be avoided. Self-Lubricating = Maintenance Free! Jilson plastic ball bearings need no lubrication. -
Ceramic Bearings
FOR EXTREME SPECIAL ENVIRONMENTS CERAMIC BEARINGS Japan Quality CAT. NO. B1013E Ceramic Bearing Development Story Introduction to Application Examples 1 Machine tools 3 World’s first successful practical application of ceramic bearings 2 Film manufacturing equipment 3,4 3 Power generation equipment 4 4 Industrial furnaces 5,6 “Aren’t there any bearings that can be used in seawater?” 5 Production equipment 7,8 …One of our customers asked this question, 6 Semiconductor manufacturing equipment 9,10,11 7 Motor, Industrial machinery 12 triggering our efforts to develop the ceramic bearing. 8 Medical equipment 13 Initially, we attempted to use alumina as the raw material, 9 Home electrical appliances 13,14 but it split quickly and cracks developed… 10 Outer space, Leisure 14 11 Automobiles, Motorcycles 15,16 Following this, research stalled and ended after approximately five years. Research resumed again in 1978; Features this time with the development team consisting of five members. Cooperation Properties of ceramic materials Additionally, a material manufacturer known for 1 Material characteristics 17 leading ceramics research was invited to join the effort. 2 Rolling fatigue of ceramic materials 18 3 Ceramic materials suitable for rolling bearings 19 Starting with silicon nitride as the raw material, 4 Composition of ceramic bearings 19 strength was reinforced using a sintering additive and a hot pressing process eliminated cracking. As a result, the first ceramic bearings were commercialized in 1984. Production Process Some of our customers had doubts about strength in the beginning, Ceramics Production Process stating “If ceramic cracks, it will surely split in two!” 1 Production Process 20 At that time, customers would hit the bearings with a hammer to test their strength. -
IKO Needle Roller Bearing Series General Info
Nippon Thompson Co., Ltd. is a bearing manufacturer that launched the technical development of needle roller bearings for the first time in Japan and is proud of the high quality level and abundant varieties of its products. Needle roller bearings are bearings for rotary motion that incorporate needle- shaped thin rollers instead of ordinary bearing balls or rollers. Compared with other rolling bearings, they are small-sized and lightweight but have a large load capacity. They are widely used with high reliability in the fields of automobiles, industrial machinery, OA equipment, etc. as resource-saving type bearings that make the whole machine compact. A1 A2 A Characteristics of Needle Roller Bearings Bearings can be classified into two main types, namely rolling bearings and sliding bearings. Rolling bearings can be subdivided further into ball bearings and roller bearings according to the rolling elements. Classification of bearings B Needle Roller Bearings are high-precision rolling bearings with a low sectional height, incorporating needle rollers as the rolling element. They have the following features. Deep groove ball bearings C Merits of Rolling Bearings Merits of Needle Roller Bearings Angular contact ball bearings Radial ball bearings Self-aligning ball bearings Compared with sliding bearings, rolling bearings Compared with other rolling bearings, Needle D have the following merits: Roller Bearings have the following advantages: Others With a low sectional height, they can Thrust ball bearings with flat back face Static and -
Bearing Self Study Guide Expanding Your Knowledge of Bearings and Related Components
Bearing self study guide Expanding your knowledge of bearings and related components. $10.00 Table of contents Introduction ............................................................. 2 Chapter 8 Chapter 1 Installation ......................................................................38 History of bearings ......................................................... 3 Pre-installation ................................................................38 The parts of a bearing..................................................... 3 Press fitting, mounting ..................................................39 Review ................................................................................. 5 Clutch release bearing: Special mounting procedures .......................................40 Chapter 2 Installation checklist ........................................................41 The bearing ...................................................................... 7 Review ...............................................................................42 Review ................................................................................. 9 Chapter 9 Chapter 3 Bearing adjustment......................................................44 Operation conditions ....................................................11 Review ...............................................................................46 Internal bearing clearance ............................................11 Shaft and housing conditions .......................................12 Chapter -
Rolling Element Bearing Methodology Application Guide Bently Nevada Machinery Condition Monitoring
Rolling Element Bearing Methodology Application Guide Bently Nevada Machinery Condition Monitoring Objective This document is intended to be the complete source for understanding Bently Nevada’s methodology on monitoring/managing rolling element bearings. The intention is to reduce the number of sources/locations where such information is stored. Deliverables and CTQs This document describes in detail Bently Nevada’s methodology for managing Rolling Element Bearings which has been proven over the past years using Trendmaster Pro, 1900/65A, vbX/SCOUT instruments along with Ascent software and System 1 Evolution. This methodology is accepted throughout Bently Nevada and multiple industries. Introduction This document is intended to be the master document for Bently Nevada’s methodology for management of rolling element bearings (REB’s). To avoid the repetitive reworking and releasing of multiple documents, all other documents that require mention of Bently Nevada’s REB management methodology should simply refer to this document rather than duplicating parts of it. Bently Nevada’s REB management methodology includes the important aspects of transducer types/usage, transducer mounting, monitor and software configuration and processing techniques. It is based on both the principles of rotating machinery behavior and the vibration characteristics of rolling element bearings. It combines traditional strategies for detecting rotor-related problems (such as unbalance and misalignment) with specialized methodologies (such as enveloping or demodulation) for identifying rolling-element bearing defects. The monitoring system must provide data for detecting and preventing rotor and bearing related problems and give adequate advanced warning of these problems so corrective action may be initiated. The system must be capable of discriminating among bearing faults, and give an early warning when a lubrication problem is present. -
Timken® Fafnir® Super Precision Bearings for Machine Tool Applications
TIMKEN® FAFNIR® SUPER PRECISION BEARINGS FOR MACHINE TOOL APPLICATIONS INDEX A ENGINEERING Bearing Selection Process ......................................... 9 Determination of Applied Loads and Bearing Analysis ............... 32 Bearing Reactions, Load Ratings and Life .......................... 38 Permissible Operating Speed ..................................... 49 Lubrication ...................................................... 52 Run-In Procedures ............................................... 57 Heat Generation and Dissipation ................................... 60 Tolerances ...................................................... 63 Fitting Practices ................................................. 76 Shaft and Housing Considerations ................................. 84 Mounting Designs ................................................ 88 Setting and Preloading Guidelines ................................. 97 B PRECISION TAPERED ROLLER BEARINGS Part Numbering Systems ......................................... 103 Introduction .................................................... 106 TS Style – Metric, Inch .......................................... 108 TSF Style – Metric, Inch ......................................... 112 TXR Style – Metric, Inch ......................................... 116 TSHR Style – Metric, Inch ........................................ 118 C SUPER PRECISION BALL BEARINGS Part Numbering Systems ......................................... 125 Introduction .................................................... 130 -
Design of a Test Rig for Conductive Ball Bearing Greases
Design of a Test Rig for Conductive Ball Bearing Greases A Major Qualifying Project Report Submitted to the Faculty of WORCESTER POLYTECHNIC INSTITUTE in Partial Fulfillment of the Requirements for the Degree of Bachelor of Science by: __________________________ Samantha E. Robinson With co-authors at Kungliga Tekniska Högskolan: Gabriel Benjamin Calderon Salmeron Siddharth Ramakrishnan Vignesh Nagarajan Nikhil Marharshi Ruben Noya Professor Holly K. Ault, Advisor Submitted on May 19, 2018 This report represents the work of a WPI undergraduate student. It has been submitted to the faculty as evidence of completion of a degree requirement. WPI publishes these reports on its website without editorial or peer review. 1 ABSTRACT Modern electric machinery requires the use of conductive ball bearing greases. The project sponsor, Axel Christiernsson International AB, has outlined requirements for a device to test grease under simulated conditions of an electric motor. The machine combines all of the requirements, including operating at speeds above 10,000rpm, measuring milli-Newton- meter range torques, and isolating an electric current to the test bearing. This report outlines the process to design a test rig to be constructed in August 2018. The final design consists of a belt transmission, ceramic support bearings, cantilevered test bearing in custom housing, an electric circuit, nut and screw loading, PT100 temperature sensor, and friction torque measurement by load cells. 2 ACNOWLEDGMENTS This project would not be possible without the help from many different individuals. First, I would like to thank Worcester Polytechnic Institute (WPI) and the Interdisciplinary and Global Studies Division for allowing me the opportunity to complete this project in Stockholm, Sweden. -
Design of a Variable Compression Internal Combustion Engine
Design of a Variable Compression Internal Combustion Engine A Major Qualifying Project Report Submitted to the faculty of Worcester Polytechnic Institute In partial fulfillment of the requirements for the Degree of Bachelor of Science In Mechanical Engineering By: Liam Finnegan Quinton Schimmel Submitted On: May 18, 2020 Project Advisor: Robert Daniello 2 Design of a Variable Compression Internal Combustion Engine Acknowledgements We would like to primarily thank Professor Daniello for advising us on this project. He was always well-informed regarding the topics and provided helpful feedback in a timely manner. We would also like to thank Ian Anderson, a member of the Washburn Shops Laboratory Staff for his help with understanding the manufacturability and tolerances of the components we were designing. 3 Design of a Variable Compression Internal Combustion Engine Abstract The purpose of this project is to design a single cylinder internal combustion engine to be used by the Mechanical Engineering Department at WPI to aid in class demonstrations. The engine must be reconfigurable for different operating parameters, and durable enough to withstand sub-optimal operating conditions. It must be able to function with a compression ratio and ignition timing that can be adjusted from 4:1 to 25:1 and able to operate using both gasoline and diesel fuels. The design focuses on the components that are unique to this engine: Acme threading around the cylinder that allows the compression ratio to be varied while the engine is running, a unique crankcase, and a valve train that maintains consistent valve timing as the compression ratio is varied.