Lecture 2014
Total Page:16
File Type:pdf, Size:1020Kb
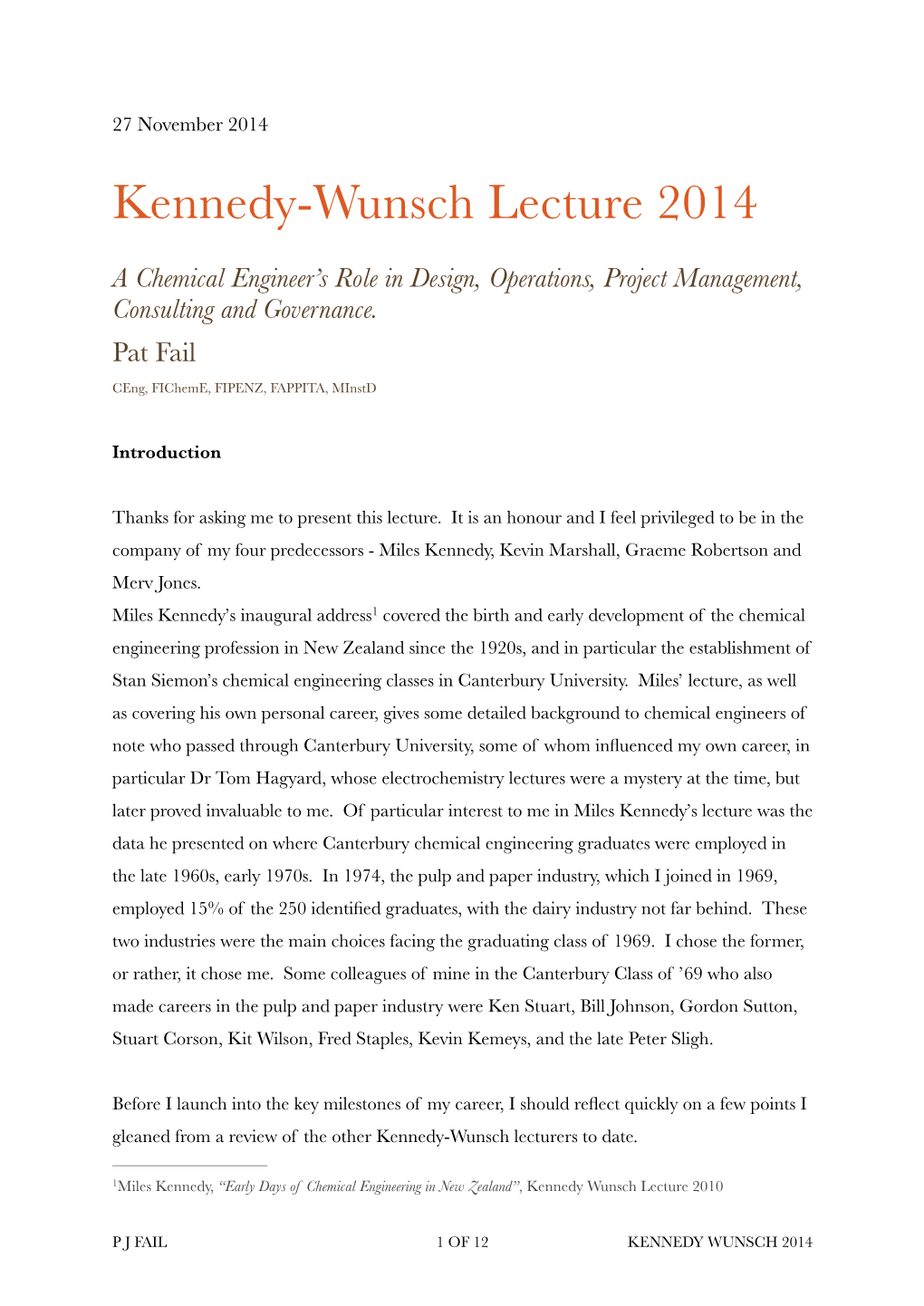
Load more
Recommended publications
-
Lack of Estrogenic and Endocrine Disrupting Effects in Juvenile Rainbow Trout Exposed to a New Zealand Pulp and Paper Mill Efflu
R. J. ELLIS URS New Zea/and Umited, Auckland, New Zea/and M. R. VAN DEN HEUVEL AND T. R. STUTHRIDGE Forest Research, Rotorua, New Zea/and N. L1NG University of Waikato, Hamilton, New Zea/and D. R. DIETRICH University ofKonstanz, Konstanz, Germany Abstract - Previous studies have noted effects of pulp and paper effluents on the physiology offishes including; smaller gonads, increased age to maturation, alterations in secondary sex characteristics, reduced plasma sex steroid levels, and the induction of vitellogenin (Vtg) in males and juveniles. A program to determine the potential impacts of a modem New Zealand pulp and paper mill effluent on fishes employed a combination of long- and short-term exposures of the juvenile (1+) rainbow trout, Oncorhynchus mykiss, to the effluent. Juvenile (1 + aged) rainbow trout were exposed to a mixed thermomechanical pulp/bleached kraft (TMP/BK) mill effluent at a range of concentrations from environmentally relevant (10%) to 70% (effluent by volume) in three exposure studies. During 21-,56- and 320-day exposures to 10% and 30% (viv) effluent, no significant impacts on circulating testosterone, and pregnenolone levels were observed. No significant induction of liver MFO activity was observed at any exposure concentration. Vitellogenin induction or expression of the estrogen receptor in juvenile males was not observed in fish from either experiment. High experimental mortality was observed in fish exposed to 70% (viv) secondary treated effluent compared to a reference treatment during the 2l-d exposure and was linked to an atypically high suspended solids load. Thus, the combined data from these experiments demonstrated a lack of estrogenicity or impacts on steroidogenesis following exposure to TMP/BK mill effluent. -
Sustainability Report 2015
SUSTAINABILITY REPORT 2015 A COMPANY OF REAL FIBRE ABOUT THIS REPORT DATA This Environmental Sustainability Report is our Data are collected and presented in accordance first report as Oji Fibre Solutions and continues with the following GRI Core Environmental our previous environmental performance reporting Performance Indicators: (since 2007) under different ownership. EN1 Materials used by weight or volume EN3 Direct energy consumption by primary SCOPE energy source EN4 Indirect energy consumption by primary This report covers the calendar year 2015 and energy source includes environmental performance data for the EN8 Total water withdrawal by source manufacturing operations of Oji Fibre Solutions. EN16 Total direct and indirect greenhouse gas Manufacturing operations are defined as Kinleith emissions by weight (Scope 1 and Scope 2) Mill, Tasman Mill, Penrose Mill, Packaging AUS EN21 Total water discharge by quality and Packaging NZ. Environmental performance and destination data are not presented for the service-focused EN22 Total weight of waste by type and sectors: Corporate Offices, Fullcircle and Lodestar. disposal method People and safety data covers manufacturing Due to shared wastewater treatment infrastructure, operations and the service-focused sectors. People certain effluent data presented for the Tasman Mill data includes permanent full-time and part-time include those from the neighbouring newsprint employees only. operation owned and operated by Norske Skog Tasman. These are identified in the notes to the REPORTING STANDARDS data tables. Greenhouse gas (GHG) emissions are reported according to the GHG Protocol(1), published by the DATA TRENDS AND RESTATEMENTS World Resources Institute and the World Business No adjustments to the bases were required in 2015. -
Third Quarter 2020
THIRD QUARTER 2020 - QUARTERLY REPORT - PRESENTATION - PRESS RELEASES NORSKE SKOG QUARTERLY REPORT – THIRD QUARTER 2020 (UNAUDITED) 2 ││││││││││││││││││││││││││││││││││││││││││││││││││││││││││││││││││││││││││││││││││││││││││││││││││││││││││││││││││││││││││││││││││││││││││││││││││││││││││││││││││││││││││││││││││││││││││││││││││││││││││││││││││││││││││││││││││││││││││││││││││││││││││││││││││││ INTRODUCTION Norske Skog is a world leading producer of publication paper with Of the four mills in Europe, two will produce recycled containerboard strong market positions in Europe and Australasia. Publication paper following planned conversion projects. In addition to the traditional includes newsprint and magazine paper. Norske Skog operates six publication paper business, Norske Skog aims to further diversify its mills in five countries, with an annual production capacity of 2.3 million operations and continue its transformation into a growing and high- tonnes. Four of the mills are located in Europe, one in Australia and margin business through a range of exciting fibre projects. one in New Zealand. The group also operates a pellet facility in New Zealand. Newsprint and magazine paper is sold through sales offices The parent company, Norske Skog ASA, is incorporated in Norway and and agents to over 80 countries. The group has approximately 2 300 has its head office at Skøyen in Oslo. The company is listed on Oslo employees. Stock Exchange with the ticker NSKOG. KEY FIGURES NOK MILLION Q3 2020 Q2 2020 Q3 2019 YTD 2020 YTD 2019 INCOME STATEMENT -
Press Release Norske Skog to Close the Tasman Mill in New Zealand
Press release 9 June 2021 Norske Skog to close the Tasman mill in New Zealand and sell mill assets Reference is made to the stock exchange release dated 9 October 2020 regarding a strategic review of the Tasman mill in New Zealand. Norske Skog today announces the closure of the Tasman mill in New Zealand and a sales process for the mill’s assets. Production will cease by 30 June 2021, permanently reducing Norske Skog’s newsprint capacity by approximately 150,000 tonnes. Since the initiation of the strategic review process in New Zealand in October 2020, a process made necessary by the secular decline of the publication paper industry and the impact of COVID-19, Norske Skog has explored a range of alternatives for the Tasman mill. Following a careful review, this process has resulted in a decision to close the Tasman mill and a sale of the mill’s assets. Production will cease by 30 June 2021, reducing Norske Skog’s newsprint capacity by approximately 150,000 tonnes per annum. The Tasman mill has only produced very limited volumes during 2021. Norske Skog will honour all redundancy and contractual obligations to the mill’s approximately 160 employees as the workforce is progressively reduced during the third quarter. - The decision to close the Tasman mill follows a detailed review over the past eight months. It will address the substantial imbalance between newsprint production capacity and customer demand in the Australasian region. The Tasman mill has been an important contributor to the regional economy in New Zealand for the past 66 years, producing more than 15 million tonnes of publication paper over its lifetime. -
SUSTAINABILITY REPORT 2020 We Create Green Value Contents
SUSTAINABILITY REPORT 2020 We create green value Contents SUMMARY Key figures 6 Norske Skog - The big picture 7 CEO’s comments 8 Short stories 10 SUSTAINABILITY REPORT About Norske Skog’s operations 14 Stakeholder and materiality analysis 15 The sustainable development goals are an integral part of our strategy 16 Compliance 17 About the sustainability report 17 Sustainability Development Goals overview 20 Prioritised SDGs 22 Our response to the TCFD recommendations 34 How Norske Skog relates to the other SDGs 37 Key figures 50 GRI standards index 52 Independent Auditor’s assurance report 54 Design: BK.no / Print: BK.no Paper: Artic Volum white Editor: Carsten Dybevig Cover photo: Carsten Dybevig. All images are Norske Skog’s property and should not be used for other purposes without the consent of the communication department of Norske Skog Photo: Carsten Dybevig SUMMARY BACK TO CONTENTS > BACK TO CONTENTS > SUMMARY Key figures NOK MILLION (UNLESS OTHERWISE STATED) 2015 2016 2017 2018 2019 2020 mills in 5 countries INCOME STATEMENT 7 Total operating income 11 132 11 852 11 527 12 642 12 954 9 612 Skogn, Norway / Saugbrugs, Norway / Golbey, France / EBITDA* 818 1 081 701 1 032 1 938 736 Bruck, Austria / Boyer, Australia / Tasman, New Zealand / Operating earnings 19 -947 -1 702 926 2 398 -1 339 Nature’s Flame, New Zealand Profit/loss for the period -1 318 -972 -3 551 1 525 2 044 -1 884 Earnings per share (NOK)** -15.98 -11.78 -43.04 18.48 24.77 -22.84 CASH FLOW Net cash flow from operating activities 146 514 404 881 602 549 Net cash flow -
Kinleith Transformation
Improving Maintenance Operation through Transformational Outsourcing Jacqueline Ming-Shih Ye MIT Sloan School of Management and the Department of Engineering Systems 50 Memorial Drive, Cambridge, Massachusetts 02142 408-833-0345 [email protected] Abstract Outsourcing maintenance to third-party contractors has become an increasingly popular option for manufacturers to achieve tactical and/or strategic objectives. Though simple in concept, maintenance outsourcing is difficult in execution, especially in a cost-sensitive environment. This project examines the Full Service business under ABB Ltd to understand the key factors that drive the success of an outsourced maintenance operation. We present a qualitative causal loop diagram developed based on the case study of Kinleith Pulp and Paper Mill in New Zealand. The diagram describes the interconnections among various technical, economic, relationship, and humanistic factors and shows how cost-cutting initiatives can frequently undermine labor relationship and tip the plant into the vicious cycle of reactive, expensive work practices. The model also explains how Kinleith achieved a remarkable turnaround under ABB, yielding high performance and significant improvements in labor relations. A case study of Tasman Pulp and Paper Mill provides a contrasting case where success has been more difficult. Results point to the importance of creating sufficient resources (“slack”) to implement improvement activities and pace implementation based on pre-existing dynamics on site. Introduction From multi-million dollar IT systems and Lean methodology to smaller-scale initiatives around organizational design or human resource development, companies continue to search for ways to better performance. Outsourcing, once seen as pure cost-reduction, is increasingly viewed as an option with considerable strategic value. -
How We Transform Industrial Organic Waste Into Vermicompost and Champion Environmental Sustainability
This paper is part of the Proceedings of the 8th International Conference on Waste Management and The Environment (WM 2016) www.witconferences.com How we transform industrial organic waste into vermicompost and champion environmental sustainability M. Quintern1, M. Morley2, B. Seaton2 & R. Hamilton3 1Quintern Innovation Ltd., Consulting, New Zealand 2MyNOKE Industrial Vermicomposting, Noke Ltd., New Zealand 2Oji Fibre Solutions Ltd., Kinleith Paper Mill, New Zealand 3Fonterra Co-operative Group Ltd., New Zealand Abstract The traditional means of disposing of processing waste to landfill is receiving close scrutiny due to high capex and opex costs and negative environmental impacts. Increasingly stringent legislation means communities and industries are seeking the security of alternative solutions when planning their long-term organic waste disposal strategies. Important to these are excellence in environmental performance, ecological sustainability and to cost effectiveness. Vermicomposting technologies achieve this through the conversion of wet organic waste to a nutrient rich, safe fertiliser for sustainable land utilisation. Vermicomposting is highly cost effective for industrial and municipal organic waste streams. MyNOKE is currently vermicomposting 30,000 tonnes per year of co-decanter dewatered waste activated sludge (WAS) and dissolved air flotation (DAF) sludge from Fonterra milk processing plants in New Zealand. The sludge is blended with 50,000 tonnes of several pulp and paper mill sludge’s from Oji Fibre Solutions Paper Mills for vermicomposting. The product, some 20,000 tonnes of vermicast, is land applied to dairy pasture and maize land. As a result, productivity, soil water efficiency, and nutrient uptake are increased. Plant available water holding capacity, root density, and root depth reduces the risk for nitrate nutrient leaching when applied as effluent or mineral fertiliser. -
IEA Bioenergy Task42 Biorefining Deals with Knowledge Building and Exchange Within the Area of Biorefining, I.E
IEA Bioenergy is an international collaboration set-up in 1978 by the International Energy Agency (IEA) to improve international co-operation and information exchange between national bioenergy RD&D programmes. Its Vision is that bioenergy is, and will continue to be a substantial part of the sustainable IEA BIOENERGY use of biomass in the BioEconomy. By accelerating the sustainable production and use of biomass, particularly in a Task42 Biorefining approach, the economic and environmental impacts will be optimised, resulting in more cost-competitive BIOREFINING bioenergy and reduced greenhouse gas emissions. Its Mission is facilitating the commercialisation and market deployment of environmentally sound, socially acceptable, and cost-competitive bioenergy systems and technologies, and to advise policy and industrial decision makers accordingly. Its Strategy is to provide platforms for international FOOD FEED collaboration and information exchange, including the development of networks, dissemination of information, and provision of science-based technology BIOENERGY (FUELS, POWER, HEAT) analysis, as well as support and advice to policy makers, involvement of industry, and encouragement of membership by countries with a strong bioenergy CHEMICALS MATERIALS infrastructure and appropriate policies. Gaps and barriers to deployment will be addressed to successfully promote sustainable bioenergy systems. The purpose of this brochure is to provide an unbiased, authoritative statement on biorefining in general, and of the specific activities -
Oji Fibre Solutions Modern Slavery
Modern Slavery Statement 2020 Modern Slavery Statement 2020 About Us Oji Fibre Solutions is one of Australasia’s leading producers of market pulp, paper and fibre-based packaging. We are a vertically integrated OJI FIBRE SOLUTIONS’ FACILITIES business, employing around 1,800 people. Our operations include: • Three mills in New Zealand producing market pulp and containerboards. • Ten packaging operations across New Zealand and Australia providing BRISBANE paper-based packaging solutions – Foodservice boxes, multiwall bags, paper cups Yatala and specialty boards. • A logistics service providing national and international transport solutions. SYDNEY Lansvale • A paper and cardboard recycling service with 14 bailing sites across New Zealand, which supplies MELBOURNE recovered fibre to our paper mills Cardboard Carton Solutions Noble Park for reprocessing. AUCKLAND EMPLOYEE LOCATION Head Oice Northern 81.7% Paper Bag Penrose Mill 17.9% HAMILTON KAWERAU 0.4% Specialty Boards Tasman Mill TOKOROA LEVIN Kinleith Mill Central WELLINGTON Materials Recovery Facility Asia CHRISTCHURCH Australia Southern New Zealand DUNEDIN Materials Recovery Facility Head Office Mill Packaging Facility Materials Recovery Facility Distribution Centres Modern Slavery Statement 2020 This is our first public Modern Slavery Statement. It covers all the entities within Oji Oceania Management (NZ) Ltd 1, which are together known as Oji Fibre Solutions. OJI FIBRE SOLUTIONS’ STRUCTURE Oji Oceania Management (NZ) Ltd Oji Fibre Solutions (NZ) Ltd Oji Oceania PPP Operations Management (NZ) Ltd (AUS) Pty Ltd Oji Cardboard Oji Foodservice Oji Fibre Solutions XPACCAR Oji Fibre Solutions Oji Fibre Solutions Carton Solutions Packaging Solutions (QLD) Pty Ltd Pty Ltd (AUS) Pty Ltd (Malaysia) Sdn Bhd Pty Ltd (AUS) Pty Ltd XPACCAR Oji Fibre Solutions 2 Pty Ltd (HK) Ltd The main raw material input to the products made by Oji Fibre Solutions is wood-fibre grown in New Zealand. -
Norske Skog Annual Report 2020 / Norske Skog 7 SUMMARY BACK to CONTENTS > BACK to CONTENTS > SUMMARY
ANNUAL REPORT 2020 We create green value Contents SUMMARY Key figures 6 Norske Skog - The big picture 7 CEO’s comments 8 Share information 10 Board of directors 12 Corporate management 13 Short stories 14 SUSTAINABILITY REPORT About Norske Skog’s operations 18 Stakeholder and materiality analysis 19 The sustainable development goals are an integral part of our strategy 20 Compliance 21 About the sustainability report 21 Sustainability Development Goals overview 24 Prioritised SDGs 26 Our response to the TCFD recommendations 38 How Norske Skog relates to the other SDGs 41 Key figures 54 GRI standards index 56 Independent Auditor’s assurance report 58 Corporate governance 60 Report of the board of directors 68 CONSOLIDATED FINANCIAL STATEMENTS 73 Notes to the consolidated financial statements 78 FINANCIAL STATEMENTS NORSKE SKOG ASA 119 Notes to the financial statements 124 Statement from the board of directors and the CEO 132 Independent auditor’s report 133 Alternative performance measures 137 Design: BK.no / Print: BK.no Paper: Artic Volum white Editor: Carsten Dybevig Cover photo: Adobe Stock. All images are Norske Skog’s property and should not be used for other purposes without the consent of the communication department of Norske Skog Photo: Carsten Dybevig SUMMARY BACK TO CONTENTS > BACK TO CONTENTS > SUMMARY Key figures NOK MILLION (UNLESS OTHERWISE STATED) 2015 2016 2017 2018 2019 2020 mills in 5 countries INCOME STATEMENT 7 Total operating income 11 132 11 852 11 527 12 642 12 954 9 612 Skogn, Norway / Saugbrugs, Norway / Golbey, -
Paper Technology Journal
Paper Technology Journal ahead 2004: International Customer Conference for Board and Packaging Papers. News from the Divisions: Reading matter from 100 % recov- ered paper for the United Kingdom. Success in South Africa – Mondi relies once more on Voith Paper. Mission 2004 – Rebuild of StoraEnso’s Board Machine 3 at Baienfurt Mill. Minfeng PM 21 – Specialist for specialty papers. Paper Culture: With CD ROM: “A line of types” – 150th anniversary One Platform Concept 18 of the birth of Ottmar Mergenthaler. Contents EDITORIAL Front page: Ottmar Mergenthaler’s Foreword 1 Linotype was the breakthrough that ahead 2004 – International Customer Conference dramatically speeded up the setting for Board and Packaging Papers in Vienna from May 5 to 7, 2004 2 of type in the printing industry. It led to larger newspapers and thus NEWS FROM THE DIVISIONS to a greater demand for newsprint. Norske-Skog Parenco – Water management system secures fresh water savings 6 Hamburger Spremberg orders new recovered fibre plant 10 Reading matter from 100 % recovered paper for the United Kingdom 12 Success in South Africa – Mondi relies once more on Voith Paper 17 Peninsular PM 62 Newsprint machine ordered 20 Mission 2004 – Rebuild of StoraEnso’s Board Machine 3 at Baienfurt Mill 22 To the customer’s advantage – From One Platform Concept to Process Line Package 27 Ruzomberok PM 18 – First Single NipcoFlex Press operating successfully 32 Schongau PM 9 success story – Optimization completed 36 Minfeng PM 21 – Specialist for specialty papers 38 QualiFlex Press Sleeves – Innovative development of shoe press sleeves 42 Thirtieth anniversary of the Nipco system – Fitter than ever for the next thirty years 45 The new winder mathematics – one is more than two. -
Commerce Commission Decision No
Public Version ISSN NO. 0114-2720 J4434 Commerce Commission Decision No. 424 Determination pursuant to the Commerce Act 1986 in the matter of an application involving: CARTER HOLT HARVEY LIMITED and NORSKE SKOGINDUSTRIER ASA The Commission: M J Belgrave M N Berry Summary of Application: The acquisition by Carter Holt Harvey Limited of those business assets of Norske Skogindustrier ASA relating to the kraft pulp processing assets of Norske's Tasman Mill. Determination: Pursuant to section 66(3)(a) of the Commerce Act 1986, the Commission determines to give clearance for the proposed acquisition. Date of Determination: 21 March 2001 CONFIDENTIAL MATERIAL IN THIS REPORT IS CONTAINED IN SQUARE BRACKETS 2 THE PROPOSAL ..........................................................................................................................................4 THE PROCEDURES.....................................................................................................................................4 THE PARTIES...............................................................................................................................................5 CARTER HOLT HARVEY LIMITED ..................................................................................................................5 NORSKE SKOGINDUSTRIER ASA ...................................................................................................................5 OTHER PARTIES ...........................................................................................................................................5