Rail Accident Report
Total Page:16
File Type:pdf, Size:1020Kb
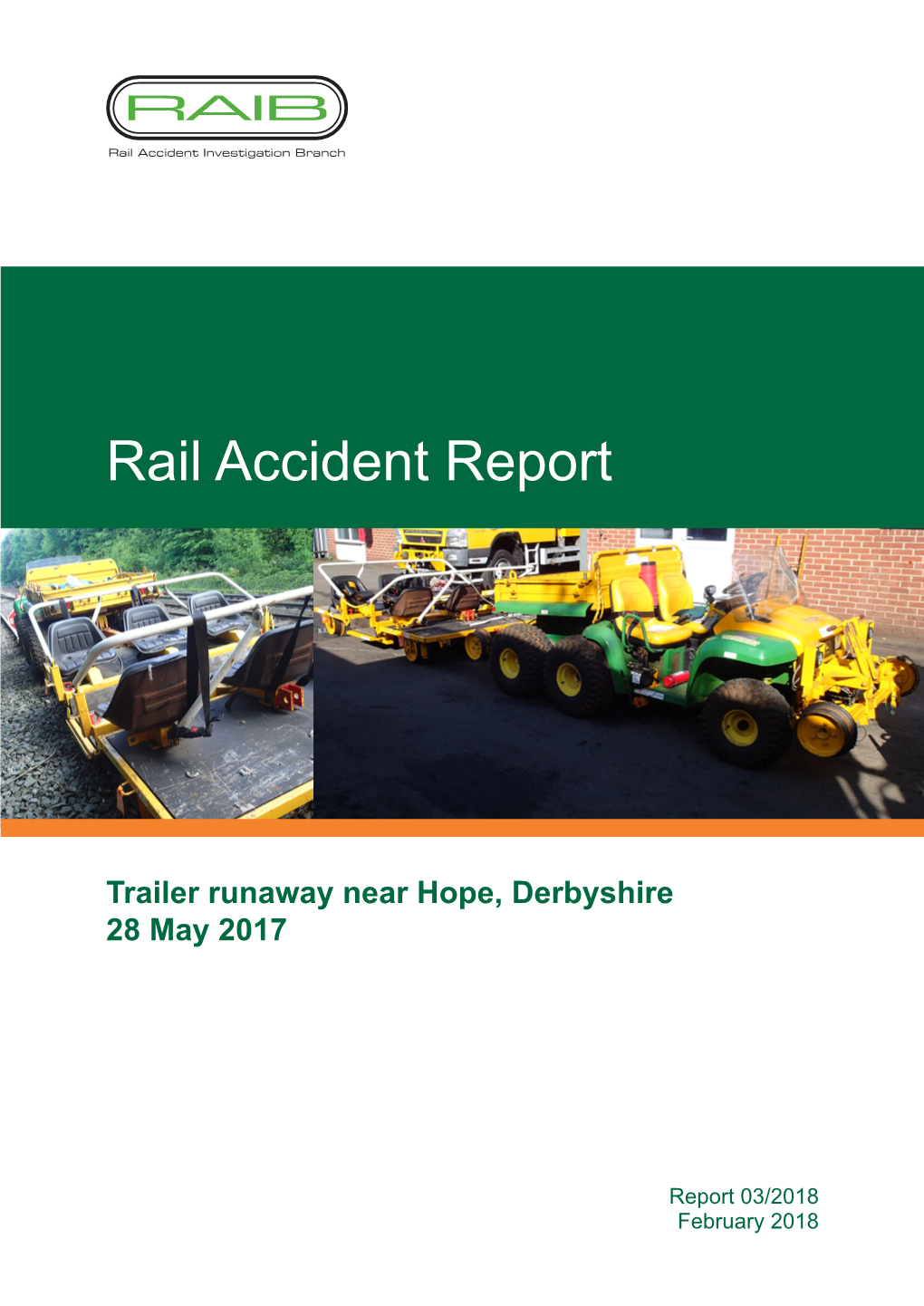
Load more
Recommended publications
-
Download from Our Website Or Pick One up When You Thrilling Mix of Sheffield Bands Including Dead Like Pop Down for a Coffee at Our Coffee Mornings
TOTLEY INDEPENDENT PUBLISHED BY THE TOTLEY RESIDENTS ASSOCIATION CONTINUOUSLY SINCE 1977 JULY/AUGUST 2010 No. 335 20p. I enclose a very old picture of The Fleur De Lys. This was passed on to my son Gary by and old Totley resident no longer living in the village. I would speculate after speaking to a few older and former residents it would be approximately early 1900. Pubs were often known by the owner or landlord’s name hence Greens. Similarly in my younger days The Peacock at Owler Bar was known locally as Johnny Braughm’s. I would think the present Fleur was completed around 1930. J W Abson. Totley Residents Association Update Success at last!! After countless phone calls over several years, we have finally won. The “new” bus shelter at the Baslow Road / Glover Road corner is now operational, it only took 5 months to complete the tarmac and put in the glass! The same week as this was done, the other two bus shelters were finally turned round. Instead of sheltering the wall, waiting passengers are now protected from splashing by speeding traffic by the shelter. It has taken a combined effort by disgruntled residents writing to The Star, many complaints by suffering residents to Highways, Streetforce and South Yorkshire Passenger Transport Executive and a continual regular stream of phone calls by yours truly to win the day. We did not give up and eventually we have won. Good news followed by bad. I expect you are all aware that Abbeydale Garden Centre has been sold to make way for a car park. -
The Edale Circular Walk a Cloudy Day in the Peak District Is Better Than a Sunny Day in the Office
The Edale circular walk A cloudy day in the Peak District is better than a sunny day in the office. The Edale circular walk is a great walk and takes you via: Edale, the start of the Pennine Way, Upperbooth, Jacob’s ladder, Browne Knoll trig point, Rushop edge, Mam Tor, Hollins Cross and then back to Edale. Plan your day for this Edale Circular hike: Start/Parking: I always start at Edale car park. Grid ref 125854 (OS Explorer SL1). Enter S33 7ZA into your Sat Nav. As you reach Hope you should turn onto Edale road, after a few miles you’ll find the car park on the right just before you turn right into Edale village. The last time I visited (Nov 2013) the parking costs were £3.00 for 2 – 4 hours and £5 for over 4 hours - don't forget your £1 coins. Walk summary: I started the walk at 9.30am and got back to the car park at 2pm (4 ½ hours). I stopped a couple of times for a cuppa and a little lunch at Hollins Cross. The walk starts at 231m and the highest point is around 569m. There are a number of stys, rough tracks, steep hill climbs and steep descents - you have to be fit to attempt this walk. Guided walks: We have guides available for this edale circular walk to escort you on your walk. Our guides are very friendly, experienced hill walkers. They are also highly qualified first aiders. Obviously there is a charge for their time; the more there are of you the cheaper it will be. -
Edale: a Study of a Pennine Dale
Scottish Geographical Magazine ISSN: 0036-9225 (Print) (Online) Journal homepage: http://www.tandfonline.com/loi/rsgj19 Edale: A study of a Pennine Dale C. B. Fawcett B.Litt., M.Sc. To cite this article: C. B. Fawcett B.Litt., M.Sc. (1917) Edale: A study of a Pennine Dale , Scottish Geographical Magazine, 33:1, 12-25, DOI: 10.1080/00369221708734256 To link to this article: http://dx.doi.org/10.1080/00369221708734256 Published online: 28 Jun 2010. Submit your article to this journal Article views: 27 View related articles Full Terms & Conditions of access and use can be found at http://www.tandfonline.com/action/journalInformation?journalCode=rsgj20 Download by: [University of California Santa Barbara] Date: 18 June 2016, At: 02:09 12 SCOTTISH GEOGRAPHICAL MAGAZINE. EDALE: A STUDY OF A PENNINE DALE.1 By C. B. FAWCETT, B.Litt., M.Sc. (With Sketch-Map and Figures.) THE dale marked on the large-scale maps of the High Peak District as the "Vale of Edale" is the high-lying valley along the south- eastern side of the Peak. From the heights above Dalehead to Edale End the valley stretches for nearly five miles in a line from west-south- west to east-north-east. In its widest parts the breadth from crest to crest reaches three miles ; but most of this is moorland, and the width of the habitable portion nowhere exceeds one mile, and averages little more than half that distance. The total area of the civil parish of Edale is eleven square miles, of which the greater part is uncultivated and uninhabited moorland. -
Summer 1994 Issn 0965-8912
'DOOR DORE VILLAGE SOCIETY No. 34 SUMMER 1994 ISSN 0965-8912 Review of Acute Services- Sheffield Health Authority For some months Sheffield Health Authority has been considering the future provision of acute services for the people of Sheffield. In order to meet financial constraints and offer a service appropriate to the needs of the population, various options were considered. A proposal to close Nether Edge Hospital was announced. This was met with some dismay by those who have personally, or have family/friends, who benefited from the quality rehabilitation service offered in such pleasant surroundings. Some services will be relocated, albeit on a smaller scale and the resultant saving from the closure will allow for development of services in the Community. New facilities to replace the ageing Jessop Hospital are required. The desirability of easy access to the Children's Hospital favour the Royal Hallamshire/Stonegrove site as an option. It is the future location of the Accident and Emergency services that should be of Full steam ahead. Local dignatries are shown Totley Tunnel shortly before its official opening to particular concern to the people of Dore. It is regular passenger traffic in 1894. Work on coordinating a celebration of the tunnel's opening is very easy to be emotional about the possibility now well advanced with exhibitions, a fete and steam hauled trains planned. of having a single site Accident and Emergency Department at the Northern experts in facial injuries ~- all based at the General Hospital. Royal Hallamshire? Council Elections The big questions are:- • Has full consultation been made with other • Is it essential to opt for a single site hospitals such as Chesterfield, which are Following the Local Elections on 5th May, provision? more accessible to many Sheffield Dore has a new councillor - Colin Ross of • Can we be sure that the implications for residents than Northern General. -
Guided Walks and Folk Trains in the High Peak and Hope Valley
High Peak and Hope Valley January – April 2020 Community Rail Partnership Guided Walks and Folk Trains in the High Peak and Hope Valley Welcome to this guide It contains details of Guided Walks and Folk Trains on the Hope Valley, Buxton and Glossop railway lines. These railway lines give easy access to the beautiful Peak District. Whether you fancy a great escape to the hills, or a night of musical entertainment, let the train take the strain so you can concentrate on enjoying yourself. High Peak and Hope Valley This leaflet is produced by the High Peak and Hope Valley Community Rail Partnership. Community Rail Partnership Telephone: 01629 538093 Email: [email protected] Telephone bookings for guided walks: 07590 839421 Line Information The Hope Valley Line The Buxton Line The Glossop Line Station to Station Guided Walks These Station to Station Guided Walks are organised by a non-profit group called Transpeak Walks. Everyone is welcome to join these walks. Please check out which walks are most suitable for you. Under 16s must be accompanied by an adult. It is essential to have strong footwear, appropriate clothing, and a packed lunch. Dogs on a short leash are allowed at the discretion of the walk leader. Please book your place well in advance. All walks are subject to change. Please check nearer the date. For each Saturday walk, bookings must be made by 12:00 midday on the Friday before. For more information or to book, please call 07590 839421 or book online at: www.transpeakwalks.co.uk/p/book.html Grades of walk There are three grades of walk to suit different levels of fitness: Easy Walks Are designed for families and the occasional countryside walker. -
Derbyshire Gritstone Way
A Walker's Guide By Steve Burton Max Maughan Ian Quarrington TT HHEE DDEE RRBB YYSS HHII RREE GGRRII TTSS TTOONNEE WW AAYY A Walker's Guide By Steve Burton Max Maughan Ian Quarrington (Members of the Derby Group of the Ramblers' Association) The Derbyshire Gritstone Way First published by Thornhill Press, 24 Moorend Road Cheltenham Copyright Derby Group Ramblers, 1980 ISBN 0 904110 88 5 The maps are based upon the relevant Ordnance Survey Maps with the permission of the controller of Her Majesty's Stationery Office, Crown Copyright reserved CONTENTS Foreward.............................................................................................................................. 5 Introduction......................................................................................................................... 6 Derby - Breadsall................................................................................................................. 8 Breadsall - Eaton Park Wood............................................................................................ 13 Eaton Park Wood - Milford............................................................................................... 14 Milford - Belper................................................................................................................ 16 Belper - Ridgeway............................................................................................................. 18 Ridgeway - Whatstandwell.............................................................................................. -
NOTICE of POLL and SITUATION of POLLING STATIONS Election of A
NOTICE OF POLL and SITUATION OF POLLING STATIONS High Peak Borough Council Election of a Derbyshire County Councillor for Chapel & Hope Valley Division Notice is hereby given that: 1. A poll for the election of a County Councillor for Chapel & Hope Valley Division will be held on Thursday 6 May 2021, between the hours of 7:00 am and 10:00 pm. 2. The number of County Councillors to be elected is one. 3. The names, home addresses and descriptions of the Candidates remaining validly nominated for election and the names of all persons signing the Candidates nomination paper are as follows: Names of Signatories Name of Candidate Home Address Description (if any) Proposers(+), Seconders(++) & Assentors BANN 31 Beresford Road, Independent Barton Sarah L(+) Barton Michael(++) Paddy Chapel-en-le-Frith, High Peak, SK23 0NY COLLINS 9 Hope Road, The Green Party Wight Jeremy P(+) Farrell Charlotte N(++) Joanna Wiehe Edale, Hope Valley, S33 7ZF GOURLAY Ashworth House, The Conservative and Sizeland Kathleen(+) Gourlay Sara M(++) Nigel Wetters Long Lane, Unionist Party Chapel-en-le-Frith, High Peak, SK23 0TF HARRISON Castleton Hall, Labour Party Cowley Jessica H(+) Borland Paul J(++) Phil Castle Street, Castleton, Hope Valley, S33 8WG PATTERSON (Address in High Peak) Liberal Democrats Rayworth Jayne H(+) Foreshew-Cain James Robert Stephen J(++) 4. The situation of Polling Stations and the description of persons entitled to vote thereat are as follows: Station Ranges of electoral register numbers of Situation of Polling Station Number persons entitled -
Our Edale Meeting Point, Peak District
Our Edale Meeting Point, Peak District Don’t leave home without these instructions Please use the following details to arrive at the meeting point 15 minutes prior to your course start time to enable us to make a prompt start. While the course is held in a rural location the nearby cities of Manchester and Sheffield, and the surrounding motorways can cause significant traffic congestion at times so please allow plenty of time for your journey. Setting Our navigation course takes place within the stunning Peak District National Park and we use the Kinder Scout area as our training ground. Set in the beautiful hills of Derbyshire there is no better venue to learn Navigation. Our starting point is a short walk from the centre of Edale village. Participants have the option of booking into one of many local B&B’s or joining the instructors at Coopers camping and caravan site. Running late? If you are delayed at all please contact us at the earliest possible moment on 07843064114 so we can try and plan logistically to get an instructor back to the meeting point. However, please note due to the rural setting there is no phone signal in Edale so if it is the morning of the course we will not be able to assist you so a late arrival may mean that we cannot wait for you at the meeting point and you may not be able to take part in the course – In these situations late arrivals will be considered a cancellation on your part. On arrival On the first morning of your 2 day course you will be met by a Woodland Ways instructor at 09:30 outside the Old Nags Head pub, S33 7ZD which is in the centre of Edale village. -
Moorland Marathons Philip Brockbank 71
( ~~~~~~-T-------t--14 BURNLE IIIIIII11 '11111111111 '11/ BRAQFORD LEEDS I ~---+------+-- 3 I i . 1\\\\11 \ HUD~ERSFIELD'-+-II---12 RTHDALE IIIIII ' ~RSDEN 'f - I BURY!JIIIll!IC-..~~+--=:-=- - BARNSLEY BOLTON --I [11111 1 l OPENISTONE OLANGSETT' MANCHESTER Land above 1000' 30Sm 70 Moorland marathons Philip Brockbank Though the Pennine moors lack much of the beauty of the Lakeland fells and the splendour of the Welsh mountains, the more strenuous walks across them have given pleasure and not a little sport-especially in winter-to many an Alpine and even Himalayan climber. For the moorland lover based on Man chester, the only part of the Pennine worth serious consideration begins at a point 6 miles SSW of Skipton on the crest of the Colne-Keighley road, or, as easier of access, at Colne itself, and after a crow's flight of 37 miles roughly SSE ends at the foot of the steep slopes of Kinder Scout a mile N of Edale. We can also include the moors which towards the end of that range extend E and SE to nurse the infant Derwent as far as Ladybower on the main road from Glossop to Sheffield. For about the first 28 miles of that Colne to Edale flight the moors are of the conventional type. Their surface consists mainly of coarse grass with bil berry and heather in various states of roughness, culminating in the robust tussocks known as Scotchmen's heads, or (more politely) Turks' heads, which when spaced apart at a critical distance slightly less than a boot's width, thereby tending to twist the boot when inserted between them, constitute the worst going in the Kingdom apart from the rock-and-heather mixture of the Rhinogs of North Wales. -
Moors for the Future Edale Route
Grade: Easy/Moderate Map: Explorer OL01 The Peak District - Dark Peak Area Allow: 1-1.5 hours Nearest Town: Edale Terrain: The route is generally good under foot but with a steep ascent from Billy’s Cote to The Nab. Moors for the Future Audio Trails Edale – The start of the Pennine Way 1.Edale Train Station 6.The Nab Edale is accessed by train from either Sheffield or Follow the steps as they initially run parallel with the Manchester by train, or by road from Hope or Chapel-en- plantation on the right and then veer, firstly left, then right le-Frith. until the path flattens out within a couple of minutes. A small rocky outcrop will be visible 10 metres on the right. 2.The Moorland Centre Exit the train station on the left, or by leaving the main 7.Ollerbrook Clough visitor car park by the toilets and turning right. Head up Ignoring the rockier paths to your left, follow the path as the road (past The Rambler public house) and after 300 it descends around towards Ollerbrook Clough in the metres you will reach the Moorland Centre. west. Stop at the first tree you encounter (a beech), by a gate on this side of the river. 3.The Old Nags Head Continue up the road for a further 400 metres. 8.Ollerbrook Head through the small wicket gate, down the sunken 4.Billy’s Cote lane and through4 more gates until you reach a lane with Continue along the road and take the footpath signed a post box, just past the buildings. -
Dore and Totley Golf Club's Centenary Year
TOTLEY INDEPENDENT PUBLISHED CONTINUOUSLY SINCE 1977 www.totleyindependent.co.uk FEBRUARY/MARCH 2013 No. 360 20p. Chapel Fields One of Bob Warburton’s slides. Photo taken from Strawberry Lee Lane with The Cricket in the lower right and Baslow Road running left to right, with Chapel Fields in between. The fields are almost clear of bushes and the sledging run that we enjoyed as youngsters shows beautifully in this colour shot. The challenge was to clear the path and get as far as Needham’s Dyke at the bottom. Great memories. The Cricket was sporting it’s ‘Ward’s Brewery’ livery in those days – probably about 30 years ago. Totley Residents Association Update We had our first meeting of 2013 on Wednesday, January 9th, and were joined by Councillors Colin Ross and Keith Hill. We would like to thank them for their continuing support. Roger Hart also attended and spoke to us about Traffic and Parking Issues; he informed us of The Streets Ahead Roadshow which was held at Abbeydale Sports Club on 15th January. A TRA Committee Member also attended. Our next Farmers’ Market/Spring Fair will take place on Sunday, 17th March 2013 from 11am – 3pm at Totley Rise. We have a very broad Database of Stallholders; however, we are always looking for new ones. If you are interested in being involved, a Booking Form will be available to download from the Totley Independent website, or contact Hetty Moran on [email protected]. If anyone is able to help deliver flyers for this event around the Community please let us know. -
South Yorkshire
INDUSTRIAL HISTORY of SOUTH RKSHI E Association for Industrial Archaeology CONTENTS 1 INTRODUCTION 6 STEEL 26 10 TEXTILE 2 FARMING, FOOD AND The cementation process 26 Wool 53 DRINK, WOODLANDS Crucible steel 27 Cotton 54 Land drainage 4 Wire 29 Linen weaving 54 Farm Engine houses 4 The 19thC steel revolution 31 Artificial fibres 55 Corn milling 5 Alloy steels 32 Clothing 55 Water Corn Mills 5 Forging and rolling 33 11 OTHER MANUFACTUR- Windmills 6 Magnets 34 ING INDUSTRIES Steam corn mills 6 Don Valley & Sheffield maps 35 Chemicals 56 Other foods 6 South Yorkshire map 36-7 Upholstery 57 Maltings 7 7 ENGINEERING AND Tanning 57 Breweries 7 VEHICLES 38 Paper 57 Snuff 8 Engineering 38 Printing 58 Woodlands and timber 8 Ships and boats 40 12 GAS, ELECTRICITY, 3 COAL 9 Railway vehicles 40 SEWERAGE Coal settlements 14 Road vehicles 41 Gas 59 4 OTHER MINERALS AND 8 CUTLERY AND Electricity 59 MINERAL PRODUCTS 15 SILVERWARE 42 Water 60 Lime 15 Cutlery 42 Sewerage 61 Ruddle 16 Hand forges 42 13 TRANSPORT Bricks 16 Water power 43 Roads 62 Fireclay 16 Workshops 44 Canals 64 Pottery 17 Silverware 45 Tramroads 65 Glass 17 Other products 48 Railways 66 5 IRON 19 Handles and scales 48 Town Trams 68 Iron mining 19 9 EDGE TOOLS Other road transport 68 Foundries 22 Agricultural tools 49 14 MUSEUMS 69 Wrought iron and water power 23 Other Edge Tools and Files 50 Index 70 Further reading 71 USING THIS BOOK South Yorkshire has a long history of industry including water power, iron, steel, engineering, coal, textiles, and glass.