Fate of Noble Metals During the Pyroprocessing of Spent Nuclear Fuel
Total Page:16
File Type:pdf, Size:1020Kb
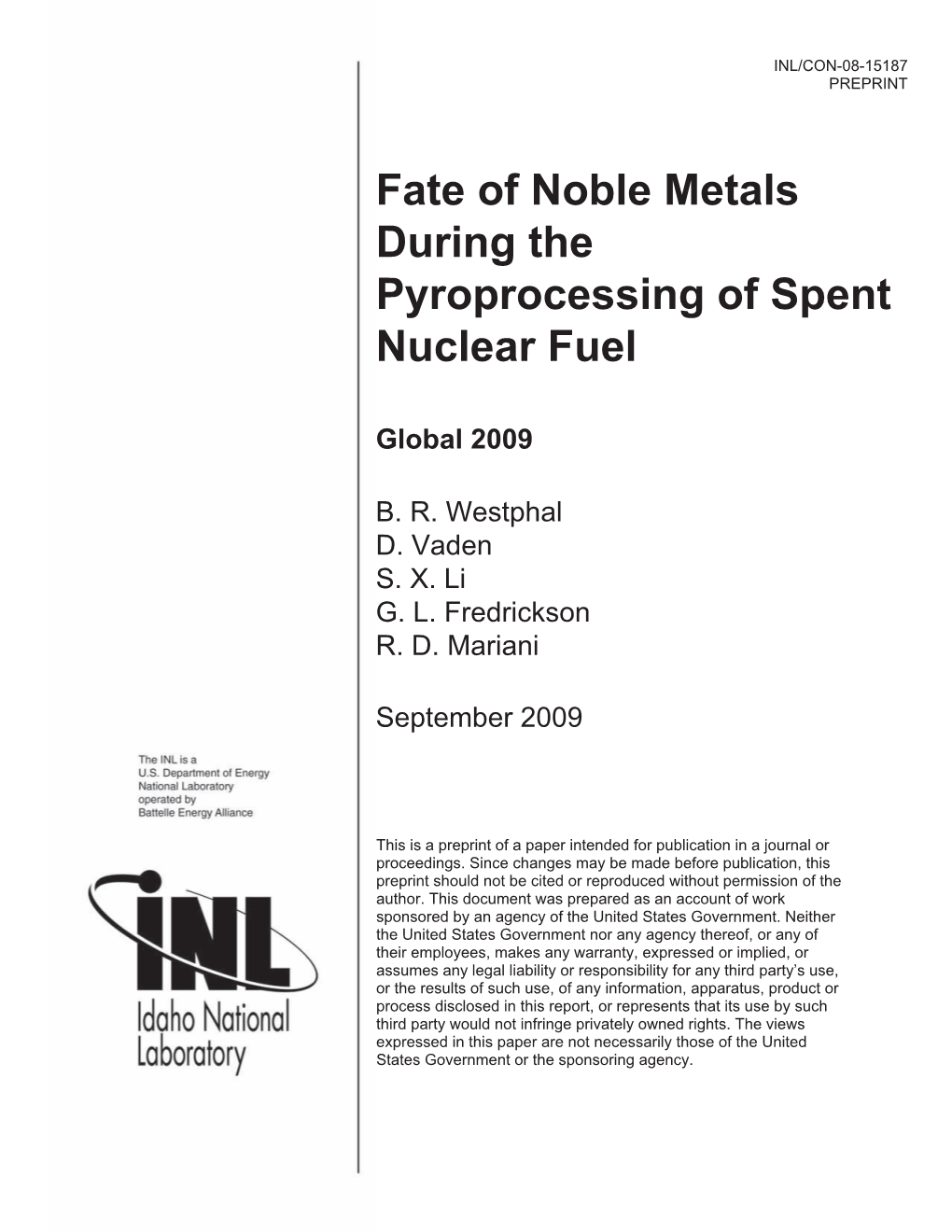
Load more
Recommended publications
-
Recent Advancements and Future Prospects of Noble Metal-Based Heterogeneous Nanocatalysts for Oxygen Reduction and Hydrogen Evolution Reactions
applied sciences Review Recent Advancements and Future Prospects of Noble Metal-Based Heterogeneous Nanocatalysts for Oxygen Reduction and Hydrogen Evolution Reactions Dinesh Bhalothia 1, Lucky Krishnia 2, Shou-Shiun Yang 1, Che Yan 1 , Wei-Hao Hsiung 1, Kuan-Wen Wang 3 and Tsan-Yao Chen 1,4,5,6,* 1 Department of Engineering and System Science, National Tsing Hua University, Hsinchu 30013, Taiwan; [email protected] (D.B.); [email protected] (S.-S.Y.); [email protected] (C.Y.); [email protected] (W.-H.H.) 2 Amity Centre of Nanotechnology, Amity University Haryana, Panchgaon, Gurugram-122413, India; [email protected] 3 Institute of Materials Science and Engineering, National Central University, Taoyuan City 32001, Taiwan; [email protected] 4 Institute of Nuclear Engineering and Science, National Tsing Hua University, Hsinchu 30013, Taiwan 5 Hierarchical Green-Energy Materials (Hi-GEM) Research Centre, National Cheng Kung University, Tainan 70101, Taiwan 6 Department of Materials Science and Engineering, National Taiwan University of Science and Technology, Taipei 10617, Taiwan * Correspondence: [email protected]; Tel.: +886-3-5715131 or +885-3-5720724 Received: 28 September 2020; Accepted: 28 October 2020; Published: 30 October 2020 Abstract: The oxygen reduction reaction (ORR) and hydrogen evolution reaction (HER) both are key electrochemical reactions for enabling next generation alternative-power supply technologies. Despite great merits, both of these reactions require robust electrocatalysts for lowering the overpotential and promoting their practical applications in energy conversion and storage devices. Although, noble metal-based catalysts (especially Pt-based catalysts) are at the forefront in boosting the ORR and HER kinetics, high cost, limited availability, and poor stability in harsh redox conditions make them unfit for scalable use. -
United States Patent Office Patented Feb
3,644,486 United States Patent Office Patented Feb. 22, 1972 2 acid, isobutyric acid, and preferably acetic acid. The car 3,644,486 boxylic acids are advantageously used in as concentrated PROCESS FOR THE MANUEFACTURE OF OX a form as possible, for example, acetic acid in the form of ACYLATION PRODUCTS AND OPTIONALLY HYDROXYLATON PRODUCTS OF CONDENSED glacial acetic acid. Small contents of water of up to about AROMATIC COMPOUNDS 10% of the carboxylic acids used are tolerable, however. Manfred Boldt and Hans-Jurgen Arpe, Fischbach, Taunus, It is also possible to use mixtures of the carboxylic acids and Lothar Hornig, Frankfurt am Main, Germany, as with the corresponding anhydrides in amounts of, for signors to Farbwerke Hoechst Aktiengesellschaft example, up to 30%. vormals Meister Lucius & Bruning, Frankfurt am Main, The oxygen may be introduced in an elementary form Germany O or in the form of air. No Drawing. Filed Sept. 19, 1968, Ser. No. 760,964 As noble metals the elements rhodium, iridium, plati Claims priority, application Germany, Sept. 23, 1967, num, ruthenium and advantageously palladium may be F 53,564 used in a finely divided form. As noble metal compounds Ent, CI, C07c69/14, 69/24, 69/62 there may be used salts of the noble metals with inorganic U.S. C. 260-479 R 6 Claims acids or advantageously with aliphatic Saturated carboxylic acids or complex compounds thereof with unsaturated or aromatic compounds. Examples of suitable noble metal ABSTRACT OF THE DISCLOSURE compounds are palladium chloride, palladium sulfate, Catalytic manufacture of oxacylation products and palladium acetate, the complex of benzene and palladium optionally hydroxylation products of condensed aromatic 20 acetate, and compounds of alkali metal acylates with cmpounds from condensed aromatic compounds and palladium acetate. -
Development of the Noble Metal/Oxide Coated Titanium Electrode PART 111: COATED TITANIUM ANODES in WIDELY RANGING OXYGEN EVOLVING SITUATIONS by €? C
Development of the Noble Metal/Oxide Coated Titanium Electrode PART 111: COATED TITANIUM ANODES IN WIDELY RANGING OXYGEN EVOLVING SITUATIONS By €? C. S. Hayfield Bickenhill, West Midlands, England The first two parts of this paper on titanium-based electrodes concentrated on the development of coatings comprising noble metals and their oxides suitable for use in chloride-bearing electrolytes. This concluding part deals with simi- lar types of electrodes which act as counter electrodes in commercial processes where the product is made on the cathode. Many electrolytes in this category involve sulfuric acid, which means that oqgen evolves at the anodes. Applications for which these electrodes are used range from those operating at very high current density, such as electrogalvanising, to others at much lower current densitr, such as impressed current cathodic protection of rebar in concrete. When platinised titanium-type electrodes were type chlorine cell technology. first envisaged for commercial use, manufac- The electrolyte is usually strong sulfuric acid turers fixed their sights almost exclusively on (- 150 g 1.') at a temperature above ambient, using them as a possible replacement for graphite usually - 40°C, but at a significantly lower tem- in high current density chlor-alkali processes, perature than the electrolyte in chlor-alkali cells. in order to effect a lowering of the cell voltage The electrolyte is more likely to have an and therefore produce cost savings (26).In the organic content. author's experience, other applications, for There may be a high manganese level (10 instance replacing lead-based anodes in elec- to 15 g 1.'). trowinning, were not initially considered. -
Page 1 of 27 RSC Advances
RSC Advances This is an Accepted Manuscript, which has been through the Royal Society of Chemistry peer review process and has been accepted for publication. Accepted Manuscripts are published online shortly after acceptance, before technical editing, formatting and proof reading. Using this free service, authors can make their results available to the community, in citable form, before we publish the edited article. This Accepted Manuscript will be replaced by the edited, formatted and paginated article as soon as this is available. You can find more information about Accepted Manuscripts in the Information for Authors. Please note that technical editing may introduce minor changes to the text and/or graphics, which may alter content. The journal’s standard Terms & Conditions and the Ethical guidelines still apply. In no event shall the Royal Society of Chemistry be held responsible for any errors or omissions in this Accepted Manuscript or any consequences arising from the use of any information it contains. www.rsc.org/advances Page 1 of 27 RSC Advances Hydrodeoxygenation of phenol as a bio-oil model compound on intimate contact noble metal-Ni 2P/SiO 2 catalyst Yunhua Li *, Xin Yang, Linhui Zhu, Hua Zhang, Binghui Chen Department of Chemical and Biochemical Engineering, College of Chemistry and Chemical Engineering, National Engineering Laboratory for Green Chemical Productions of Alcohols-Ethers-Esters, Xiamen University, Xiamen 361005, PR China. Abstract: This study investigates phenol hydrodeoxygenation on supported Ni 2P from the sol-gel and TPR method and noble metal (Pd, Pt and Ru)-Ni 2P catalysts from Ni 2P partially in-situ reducing noble metal precursor. -
Effect of Noble Metals (Ag, Pd, Pt) Loading Over the Efficiency of Tio2
chemengineering Article Effect of Noble Metals (Ag, Pd, Pt) Loading over the Efficiency of TiO2 during Photocatalytic Ozonation on the Toxicity of Parabens † João F. Gomes 1,*, Ana Lopes 1, Katarzyna Bednarczyk 2, Marta Gmurek 3, Marek Stelmachowski 2, Adriana Zaleska-Medynska 4 ID , M. Emília Quinta-Ferreira 5, Raquel Costa 1, Rosa M. Quinta-Ferreira 1 and Rui C. Martins 1 1 CIEPQPF—Chemical Engineering Processes and Forest Products Research Center, Department of Chemical Engineering, Faculty of Sciences and Technology, University of Coimbra, Rua Sílvio Lima, 3030-790 Coimbra, Portugal; [email protected] (A.L.); [email protected] (R.C.); [email protected] (R.M.Q.-F.); [email protected] (R.C.M.) 2 Faculty of Process and Environmental Engineering, Department of Safety Engineering Lodz University of Technology, Wolczanska 213, 90-924 Lodz, Poland; [email protected] (K.B.); [email protected] (M.S.) 3 Faculty of Process and Environmental Engineering, Department of Bioprocess Engineering Lodz University of Technology, Wolczanska 213, 90-924 Lodz, Poland; [email protected] 4 Faculty of Chemistry, Department of Environmental Technology, University of Gdansk, ul. Wita Stwosza 63, 80-308 Gda´nsk,Poland; [email protected] 5 CNC—Center for Neuroscience and Cell Biology and Department of Physics, Faculty of Sciences and Technology, University of Coimbra, Rua Larga, P-3004-516 Coimbra, Portugal; [email protected] * Corresponding author: [email protected]; Tel: +35-123-979-8723; Fax: +35-123-979-8703 † This article belongs to the Special Issue Selected Papers from ICEER 2017: 2017 the 4th International Conference on Energy and Environment Research. -
Noble Metal Nanoparticles Stabilized by Hyper-Cross-Linked Polystyrene As Effective Catalysts in Hydrogenation of Arenes
molecules Article Noble Metal Nanoparticles Stabilized by Hyper-Cross-Linked Polystyrene as Effective Catalysts in Hydrogenation of Arenes Elena S. Bakhvalova 1, Arina O. Pinyukova 2, Alexey V. Mikheev 2, Galina N. Demidenko 2, Mikhail G. Sulman 2, Alexey V. Bykov 2, Linda Z. Nikoshvili 2,* and Lioubov Kiwi-Minsker 1,3,* 1 Regional Technological Centre, Tver State University, Zhelyabova Str., 33, 170100 Tver, Russia; [email protected] 2 Department of Biotechnology, Chemistry and Standardization, Tver State Technical University, A.Nikitina Str., 22, 170026 Tver, Russia; [email protected] (A.O.P.); [email protected] (A.V.M.); [email protected] (G.N.D.); [email protected] (M.G.S.); [email protected] (A.V.B.) 3 Department of Basic Sciences, Ecole Polytechnique Fédérale de Lausanne (GGRC-ISIC-EPFL), CH-1015 Lausanne, Switzerland * Correspondence: [email protected] (L.Z.N.); lioubov.kiwi-minsker@epfl.ch (L.K.-M.); Tel.: +7-904-005-7791 (L.Z.N.); +41-21-693-3182 (L.K.-M.) Abstract: This work is addressing the arenes’ hydrogenation—the processes of high importance for petrochemical, chemical and pharmaceutical industries. Noble metal (Pd, Pt, Ru) nanoparticles (NPs) stabilized in hyper-cross-linked polystyrene (HPS) were shown to be active and selective catalysts in hydrogenation of a wide range of arenes (monocyclic, condensed, substituted, etc.) in a batch mode. HPS effectively stabilized metal NPs during hydrogenation in different medium (water, organic Citation: Bakhvalova, E.S.; Pinyukova, A.O.; Mikheev, A.V.; solvents) and allowed multiple catalyst reuses. Demidenko, G.N.; Sulman, M.G.; Bykov, A.V.; Nikoshvili, L.Z.; Keywords: polymeric catalysts; hydrogenation of arenes; noble metals; hyper-cross-linked Kiwi-Minsker, L. -
Transuranic Material Recovery in the Integral Fast Reactor Fuel Cycle Demonstration
TRANSURANIC MATERIAL RECOVERY IN THE INTEGRAL FAST REACTOR FUEL CYCLE DEMONSTRATION. R. W. Benedict and K. M. Goff, *Argonne National Labordtory, P.O. Box 2528, Idaho Falls, ID 83403. 208-533-7166 or 7084. Fax 208-533-7151. Argonne National Laboratory is operated by the University of Chicago for the United States Department of Energy under Contract W-3I-109-Eng-38. ANL/FC/CP—77545 TIM utmttM iMNHcnm r>M twn wttand by • contrmu. of in* U.S. Gowmnwit d No. W'3M0(-ENG-3S. tin U. S. Oowrnmwit mm • DE93 009213 nonuckim. -waiv-fn* ikmm n puWiMi or nproauct m suMMiM form rt BHI contnbutun, or aMow otters lo do n. for ABSTRACT U. s. Gowrniiwit Burpom. The Integral Fast Reactor is an innovative liquid metal reactor concept that is being developed by Argonne National Laboratory. It takes advantage of the properties of metallic tiiei and liquid metal cooling to offer significant improvements in reactor safety, operation, fuel cycle economics, environmental protection, and safeguards. The plans for demonstrating the IFR fuel cycle, including its waste processing options, by processing irradiated fuel from the Experimental Breeder Reactor-H fuel in its associated Fuel Cycle Facility have been developed for the first lenning series. This series has been designed to provide the data needed for the further development of the IFR program. An important piece of the data needed is the recovery of TRU material during the reprocessing and waste operations. INTRODUCTION The Integral Fast Reactor is an innovative liquid metal reactor concept that is being developed by Argonne National Laboratory. -
Layered Ternary and Quaternary Transition Metal Chalcogenide Based Catalysts for Water Splitting
catalysts Review Layered Ternary and Quaternary Transition Metal Chalcogenide Based Catalysts for Water Splitting Anand P. Tiwari 1,†, Travis G. Novak 1,†, Xiuming Bu 2, Johnny C. Ho 2,* and Seokwoo Jeon 1,* 1 Department of Materials Science and Engineering, KAIST Institute for the Nanocentury, Advanced Battery Center, KAIST, Daejeon 305-701, Korea; [email protected] (A.P.T.); [email protected] (T.G.N.) 2 Department of Materials Science and Engineering, City University of Hong Kong, 83 Tat Chee Avenue, Kowloon, Hong Kong; [email protected] * Correspondence: [email protected] (J.C.H.); [email protected] (S.J.); Tel.: +82-42-350-3342 (S.J.) † These authors contributed equally. Received: 30 October 2018; Accepted: 13 November 2018; Published: 16 November 2018 Abstract: Water splitting plays an important role in the electrochemical and photoelectrochemical conversion of energy devices. Electrochemical water splitting by the hydrogen evolution reaction (HER) is a straightforward route to producing hydrogen (H2), which requires an efficient electrocatalyst to minimize energy consumption. Recent advances have created a rapid rise in new electrocatalysts, particularly those based on non-precious metals. In this review, we present a comprehensive overview of the recent developments of ternary and quaternary 6d-group transition metal chalcogenides (TMCs) based electrocatalysts for water splitting, especially for HER. Detailed discussion is organized from binary to quaternary TMCs including, surface engineering, heterostructures, chalcogen substitutions and hierarchically structural design in TMCs. Moreover, emphasis is placed on future research scope and important challenges facing these electrocatalysts for further development in their performance towards water splitting. -
Microstructure Characterization of Noble Metal–Silica Nanocomposites M
Vol. 130 (2016) ACTA PHYSICA POLONICA A No. 4 Proceedings of the XXIII Conference on Applied Crystallography, Krynica Zdrój, Poland, September 20–24, 2015 Microstructure Characterization of Noble Metal–Silica Nanocomposites M. Zienkiewicz-Strzałkaa;∗ and S. Pikusb aDepartment of Physicochemistry of Solid Surface, Faculty of Chemistry, Maria Curie-Skłodowska University, Lublin, Poland bDepartment of Crystallography, Faculty of Chemistry, Maria Curie-Skłodowska University, Lublin, Poland The presence of highly dispersed metal particles on solid supports with well-defined microstructure is important in the field of functional materials, active catalysts as well as bionanomaterials for medical applications. Noble metal nanostructures, in particular silver, palladium, and platinum nanoparticles were formed from ammine complexes ([Pt(NH3)4]Cl2, [Ag(NH3)2]OH, and [Pd(NH3)4]Cl2) and supported on high ordered mesoporous silica (SBA-15) and aluminosilica matrix. In this work, the distribution, composition and crystal structure of supported noble metal nanoparticles were determined and characterized. Finally the stability of incorporated nanostructures was confirmed. The microstructures of the obtained samples were analyzed by high resolution transmission electron microscopy. Obtained results indicated that developed procedures of synthesis and modification of mesoporous ordered silica or their derivate by proposed nanostructures are effective and allow to obtain new nanocomposites and nanocatalysts in repeatable and controlled way. DOI: 10.12693/APhysPolA.130.972 PACS/topics: 61.46.Df 1. Introduction is directly related to chemical activity. Microstructural characterization of noble metal nanoparticles is impor- Nanotechnology and materials with new and unique tant for understanding their unique structures and prop- structural properties are an essential part of modern sci- erties [12, 13]. -
Coupled Reduction with Platinum Group Metals
Coupled Reduction with Platinum Group Metals THE PREPARATION OF HIGH PURITY RARE METALS By U. Berndt, B. Erdriianii and C. Keller Institute for Radiochemistry, Karlsruhe Nuclear Research Centre presence of noble metals (platinum, palladium, Very pure metals of the actinide, rhodium, iridium) can be applied to prepare lanthanide and alkaline earth series can very pure noble metal alloys with actinide, be prepared from their oxides by lanthanide and alkaline earth elements, coupled reduction by hydrogen in the titanium, zirconium, hafnium, vanadium, presence of platinum group metals. niobium, tantalum, and even with lithium During the process the platinum group (2-6). metals form intermetallic phases with The direct synthesis of alloy phases of the metals from the oxides. These noble metals with base metals involves many phases are decomposed to yield the pure serious problems caused by the relatively metals in gaseous form and the platinum high vapour pressure of the base metals. In group metals in solid form. The pure addition, the choice of the crucible material gaseous metals condense to produce and of the gas atmosphere affects the results. pure solid specimens. Furthermore, ordered phases are obtained only by repeated homogenising and by pro- longed and careful annealing. Also the usual In the course of our investigations dealing methods of preparation of highly radioactive with phase equilibria in uranium oxide-rare metals are somewhat difficult, and in some earth oxide systems, we made the following cases the elements, such as protoactinium unexpected observations (I) : (islPa) and curium (244Cm),are only prepared (I) In fluorite phases with a high content of in milligram quantities and have not yet been rare earth oxides it is not possible to investigated sufficiently. -
A Repertoire of Biomedical Applications of Noble Metal Nanoparticles Mohammad Azharuddin, Geyunjian H
A repertoire of biomedical applications of noble metal nanoparticles Mohammad Azharuddin, Geyunjian H. Zhu, Debapratim Das, Erdogan Ozgur, Lokman Uzun, Anthony P. F. Turner and Hirak Kumar Patra The self-archived postprint version of this journal article is available at Linköping University Institutional Repository (DiVA): http://urn.kb.se/resolve?urn=urn:nbn:se:liu:diva-158861 N.B.: When citing this work, cite the original publication. Azharuddin, M., Zhu, G. H., Das, D., Ozgur, E., Uzun, L., Turner, A. P. F., Patra, H. K., (2019), A repertoire of biomedical applications of noble metal nanoparticles, Chemical Communications, 55(49), 6964-6996. https://doi.org/10.1039/c9cc01741k Original publication available at: https://doi.org/10.1039/c9cc01741k Copyright: ROYAL SOC CHEMISTRY Publisher URL Missing Please do not adjust margins ARTICLE A repertoire of biotechnological applications of noble metal nanocomposites a b c d d Received 00th January 20xx, Mohammad Azharuddin , Geyunjian H. Zhu , Debapratim Das , Erdogan Ozgur , Lokman Uzun , Accepted 00th January 20xx Anthony P.F. Turner*e and Hirak K Patra*a,b,f DOI: 10.1039/x0xx00000x Noble metals comprise any of several metallic chemical elements that are outstandingly resistant to corrosion and oxidation, even at elevated temperatures. This group is not strictly defined, but the tentative list includes ruthenium, rhodium, palladium, silver, osmium, iridium, platinum and gold, in order of atomic number. The emergence of noble metal nanotechnology is attracting huge interest from the scientific community and has led to an unprecendented expansion of research and exploration of applications in electrochemistry, catalysis and biomedicine. Noble metal nanocomposites can be synthesised both by top-down and bottom up approches, as well as via organism-assisted routes, and subsequently modified appropriately for the field of use. -
Cobalt Discovery Replaces Precious Metals As Industrial Catalyst
Cobalt discovery replaces precious metals as industrial catalyst November 26, 2012 Novel cobalt system supports less expensive hydrogenation and the creation of everyday products HIGHLIGHTS • Cobalt may substitute as industrial catalyst for energy-related technologies • Catalysts are integral to thousands of industrial, synthetic, and renewable energy processes • Common cobalt may replace pricier, rare metal relatives • Potential applications: biofuel production, carbon dioxide reduction, basic necessary chemistry LOS ALAMOS, N.M., November 26, 2012—Cobalt, a common metal, holds promise as an industrial catalyst with potential applications in such energy-related technologies - 1 - such as the production of biofuels and the reduction of carbon dioxide. That is, provided the cobalt is captured in a complex molecule so it mimics the precious metals that normally serve this industrial role. In work published Nov. 26 in the international edition of the chemistry journal Angewandte Chemie, Los Alamos National Laboratory scientists report the possibility of replacing the normally used noble metal catalysts with cobalt. (http:// onlinelibrary.wiley.com/doi/10.1002/anie.201208739/full) Efficient and reusable catalysts essential elements for commodity chemicals Catalysts are the parallel of the Philosopher’s Stone for chemistry. They cannot change lead to gold, but they do transform one chemical substance into another while remaining unchanged themselves. Perhaps the most familiar example of catalysis comes from automobile exhaust systems that change toxic fumes into more benign gases, but catalysts are also integral to thousands of industrial, synthetic, and renewable energy processes where they accelerate or optimize a mind-boggling array of chemical reactions. It’s not an exaggeration to say that without catalysts, there would be no modern industry.