Optimal Integration of Steam Turbines in Industrial Process Plants
Total Page:16
File Type:pdf, Size:1020Kb
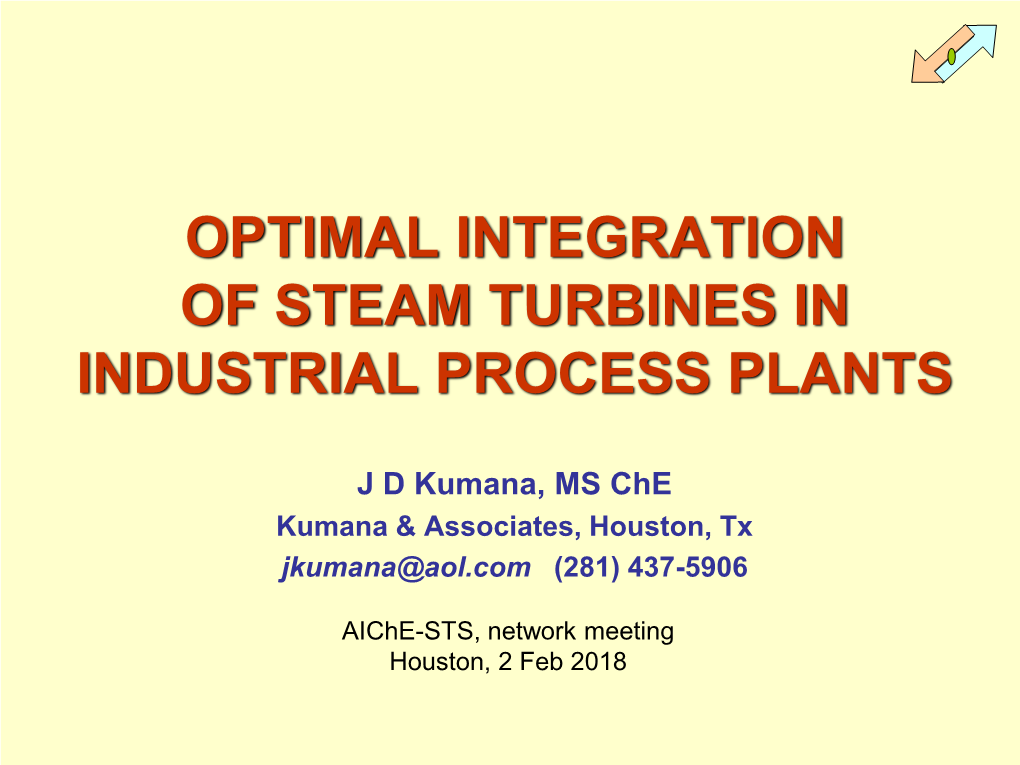
Load more
Recommended publications
-
Combustion Turbines
Section 3. Technology Characterization – Combustion Turbines U.S. Environmental Protection Agency Combined Heat and Power Partnership March 2015 Disclaimer The information contained in this document is for information purposes only and is gathered from published industry sources. Information about costs, maintenance, operations, or any other performance criteria is by no means representative of EPA, ORNL, or ICF policies, definitions, or determinations for regulatory or compliance purposes. The September 2017 revision incorporated a new section on packaged CHP systems (Section 7). This Guide was prepared by Ken Darrow, Rick Tidball, James Wang and Anne Hampson at ICF International, with funding from the U.S. Environmental Protection Agency and the U.S. Department of Energy. Catalog of CHP Technologies ii Disclaimer Section 3. Technology Characterization – Combustion Turbines 3.1 Introduction Gas turbines have been in use for stationary electric power generation since the late 1930s. Turbines went on to revolutionize airplane propulsion in the 1940s, and since the 1990s through today, they have been a popular choice for new power generation plants in the United States. Gas turbines are available in sizes ranging from 500 kilowatts (kW) to more than 300 megawatts (MW) for both power-only generation and combined heat and power (CHP) systems. The most efficient commercial technology for utility-scale power plants is the gas turbine-steam turbine combined-cycle plant that has efficiencies of more than 60 percent (measured at lower heating value [LHV]35). Simple- cycle gas turbines used in power plants are available with efficiencies of over 40 percent (LHV). Gas turbines have long been used by utilities for peaking capacity. -
Forces on Large Steam Turbine Blades RWE Npower Mechanical and Electrical Engineering Power Industry
Forces on Large Steam Turbine Blades RWE npower Mechanical and Electrical Engineering Power Industry INTRODUCTION RWE npower is a leading integrated UK energy company and is part of the RWE Group, one of Europe's leading utilities. We own and operate a diverse portfolio of power plant, including gas- fired combined cycle gas turbine, oil, and coal fired power stations, along with Combined Heat and Power plants on industrial site that supply both electrical power and heat. RWE npower also has a strong in-house operations and engineering capability that supports our existing assets and develops new power plant. Our retail business, npower, is one of the UK's largest suppliers of electricity and gas. In the UK RWE is also at the forefront of producing energy through renewable resources. npower renewables leads the UK wind power market and is a leader in hydroelectric generation. It developed the UK's first major off- shore wind farm, North Hoyle, off the North Wales Figure 1: Detailed view of turbine blades coast, which began operation in 2003. With blades (see Figure 1) rotating at such Through the RWE Power International brand, speeds, it is important that the fleet of steam RWE npower sells specialist services that cover turbines is managed to ensure safety and every aspect of owning and operating a power continued operation. If a blade were to fail in- plant, from construction, commissioning, service, this could result in safety risks and can operations and maintenance to eventual cost £millions to repair and, whilst the machine is decommissioning. not generating electricity, it can cost £hundreds of SCENARIO thousands per day in lost revenue. -
Use of Cogeneration in Large Industrial Projects
COGENERATION USE OF COGENERATION IN LARGE INDUSTRIAL PROJECTS (RECENT ADVANCES IN COGENERATION?) PRESENTER: JIM LONEY, PE [email protected] 281-295-7606 COGENERATION • WHAT IS COGENERATION? • Simultaneous generation of electricity and useful thermal energy (steam in most cases) • WHY COGENERATION? • Cogeneration is more efficient • Rankine Cycle – about 40% efficiency • Combined Cycle – about 60% efficiency • Cogeneration – about 87% efficiency • Why doesn’t everyone use only cogeneration? COGENERATION By Heinrich-Böll-Stiftung - https://www.flickr.com/photos/boellstiftung/38359636032, CC BY-SA 2.0, https://commons.wikimedia.org/w/index.php?curid=79343425 COGENERATION GENERATION SYSTEM LOSSES • Rankine Cycle – about 40% efficiency • Steam turbine cycle using fossil fuel • Most of the heat loss is from the STG exhaust • Some heat losses via boiler flue gas • Simple Cycle Gas Turbine– about 40% efficiency • The heat loss is from the gas turbine exhaust • Combined Cycle – about 60% efficiency • Recover the heat from the gas turbine exhaust and run a Rankine cycle • Cogeneration – about 87% efficiency COGENERATION • What is the problem with cogeneration? • Reality Strikes • In order to get to 87% efficiency, the heating load has to closely match the thermal energy left over from the generation of electricity. • Utility electricity demand typically follows a nocturnal/diurnal sine pattern • Steam heating loads follow a summer/winter cycle • With industrial users, electrical and heating loads are typically more stable COGENERATION • What factors determine if cogeneration makes sense? • ECONOMICS! • Not just the economics of the cogeneration unit, but the impact on the entire facility. • Fuel cost • Electricity cost, including stand-by charges • Operational flexibility including turndown ability • Reliability impacts • Possibly the largest influence • If the cogeneration unit has an outage then this may (will?) bring the entire facility down. -
Wind Energy Glossary: Technical Terms and Concepts Erik Edward Nordman Grand Valley State University, [email protected]
Grand Valley State University ScholarWorks@GVSU Technical Reports Biology Department 6-1-2010 Wind Energy Glossary: Technical Terms and Concepts Erik Edward Nordman Grand Valley State University, [email protected] Follow this and additional works at: http://scholarworks.gvsu.edu/bioreports Part of the Environmental Indicators and Impact Assessment Commons, and the Oil, Gas, and Energy Commons Recommended Citation Nordman, Erik Edward, "Wind Energy Glossary: Technical Terms and Concepts" (2010). Technical Reports. Paper 5. http://scholarworks.gvsu.edu/bioreports/5 This Article is brought to you for free and open access by the Biology Department at ScholarWorks@GVSU. It has been accepted for inclusion in Technical Reports by an authorized administrator of ScholarWorks@GVSU. For more information, please contact [email protected]. The terms in this glossary are organized into three sections: (1) Electricity Transmission Network; (2) Wind Turbine Components; and (3) Wind Energy Challenges, Issues and Solutions. Electricity Transmission Network Alternating Current An electrical current that reverses direction at regular intervals or cycles. In the United States, the (AC) standard is 120 reversals or 60 cycles per second. Electrical grids in most of the world use AC power because the voltage can be controlled with relative ease, allowing electricity to be transmitted long distances at high voltage and then reduced for use in homes. Direct Current A type of electrical current that flows only in one direction through a circuit, usually at relatively (DC) low voltage and high current. To be used for typical 120 or 220 volt household appliances, DC must be converted to AC, its opposite. Most batteries, solar cells and turbines initially produce direct current which is transformed to AC for transmission and use in homes and businesses. -
Hydroelectric Power -- What Is It? It=S a Form of Energy … a Renewable Resource
INTRODUCTION Hydroelectric Power -- what is it? It=s a form of energy … a renewable resource. Hydropower provides about 96 percent of the renewable energy in the United States. Other renewable resources include geothermal, wave power, tidal power, wind power, and solar power. Hydroelectric powerplants do not use up resources to create electricity nor do they pollute the air, land, or water, as other powerplants may. Hydroelectric power has played an important part in the development of this Nation's electric power industry. Both small and large hydroelectric power developments were instrumental in the early expansion of the electric power industry. Hydroelectric power comes from flowing water … winter and spring runoff from mountain streams and clear lakes. Water, when it is falling by the force of gravity, can be used to turn turbines and generators that produce electricity. Hydroelectric power is important to our Nation. Growing populations and modern technologies require vast amounts of electricity for creating, building, and expanding. In the 1920's, hydroelectric plants supplied as much as 40 percent of the electric energy produced. Although the amount of energy produced by this means has steadily increased, the amount produced by other types of powerplants has increased at a faster rate and hydroelectric power presently supplies about 10 percent of the electrical generating capacity of the United States. Hydropower is an essential contributor in the national power grid because of its ability to respond quickly to rapidly varying loads or system disturbances, which base load plants with steam systems powered by combustion or nuclear processes cannot accommodate. Reclamation=s 58 powerplants throughout the Western United States produce an average of 42 billion kWh (kilowatt-hours) per year, enough to meet the residential needs of more than 14 million people. -
Hydropower Technologies Program — Harnessing America’S Abundant Natural Resources for Clean Power Generation
U.S. Department of Energy — Energy Efficiency and Renewable Energy Wind & Hydropower Technologies Program — Harnessing America’s abundant natural resources for clean power generation. Contents Hydropower Today ......................................... 1 Enhancing Generation and Environmental Performance ......... 6 Large Turbine Field-Testing ............................... 9 Providing Safe Passage for Fish ........................... 9 Improving Mitigation Practices .......................... 11 From the Laboratories to the Hydropower Communities ..... 12 Hydropower Tomorrow .................................... 14 Developing the Next Generation of Hydropower ............ 15 Integrating Wind and Hydropower Technologies ............ 16 Optimizing Project Operations ........................... 17 The Federal Wind and Hydropower Technologies Program ..... 19 Mission and Goals ...................................... 20 2003 Hydropower Research Highlights Alden Research Center completes prototype turbine tests at their facility in Holden, MA . 9 Laboratories form partnerships to develop and test new sensor arrays and computer models . 10 DOE hosts Workshop on Turbulence at Hydroelectric Power Plants in Atlanta . 11 New retrofit aeration system designed to increase the dissolved oxygen content of water discharged from the turbines of the Osage Project in Missouri . 11 Low head/low power resource assessments completed for conventional turbines, unconventional systems, and micro hydropower . 15 Wind and hydropower integration activities in 2003 aim to identify potential sites and partners . 17 Cover photo: To harness undeveloped hydropower resources without using a dam as part of the system that produces electricity, researchers are developing technologies that extract energy from free flowing water sources like this stream in West Virginia. ii HYDROPOWER TODAY Water power — it can cut deep canyons, chisel majestic mountains, quench parched lands, and transport tons — and it can generate enough electricity to light up millions of homes and businesses around the world. -
AP-42, Vol. I, 3.1: Stationary Gas Turbines
3.1 Stationary Gas Turbines 3.1.1 General1 Gas turbines, also called “combustion turbines”, are used in a broad scope of applications including electric power generation, cogeneration, natural gas transmission, and various process applications. Gas turbines are available with power outputs ranging in size from 300 horsepower (hp) to over 268,000 hp, with an average size of 40,200 hp.2 The primary fuels used in gas turbines are natural gas and distillate (No. 2) fuel oil.3 3.1.2 Process Description1,2 A gas turbine is an internal combustion engine that operates with rotary rather than reciprocating motion. Gas turbines are essentially composed of three major components: compressor, combustor, and power turbine. In the compressor section, ambient air is drawn in and compressed up to 30 times ambient pressure and directed to the combustor section where fuel is introduced, ignited, and burned. Combustors can either be annular, can-annular, or silo. An annular combustor is a doughnut-shaped, single, continuous chamber that encircles the turbine in a plane perpendicular to the air flow. Can-annular combustors are similar to the annular; however, they incorporate several can-shaped combustion chambers rather than a single continuous chamber. Annular and can-annular combustors are based on aircraft turbine technology and are typically used for smaller scale applications. A silo (frame-type) combustor has one or more combustion chambers mounted external to the gas turbine body. Silo combustors are typically larger than annular or can-annular combustors and are used for larger scale applications. The combustion process in a gas turbine can be classified as diffusion flame combustion, or lean- premix staged combustion. -
Horizontal Axis Water Turbine: Generation and Optimization of Green Energy
International Journal of Applied Engineering Research ISSN 0973-4562 Volume 13, Number 5 (2018) pp. 9-14 © Research India Publications. http://www.ripublication.com Horizontal Axis Water Turbine: Generation and Optimization of Green Energy Disha R. Verma1 and Prof. Santosh D. Katkade2 1Undergraduate Student, 2Assistant Professor, Department of Mechanical Engineering, Sandip Institute of Technology & Research Centre, Nashik, Maharashtra, (India) 1Corresponding author energy requirements. Governments across the world have been Abstract creating awareness about harnessing green energy. The The paper describes the fabrication of a Transverse Horizontal HAWT is a wiser way to harness green energy from the water. Axis Water Turbine (THAWT). THAWT is a variant of The coastal areas like Maldives have also been successfully Darrieus Turbine. Horizontal Axis Water Turbine is a turbine started using more of the energy using such turbines. The HAWT has been proved a boon for such a country which which harnesses electrical energy at the expense of water overwhelmingly depends upon fossil fuels for their kinetic energy. As the name suggests it has a horizontal axis of electrification. This technology has efficiently helped them to rotation. Due to this they can be installed directly inside the curb with various social and economic crisis [2]. The water body, beneath the flow. These turbines do not require complicated remote households and communities of Brazil any head and are also known as zero head or very low head have been electrified with these small hydro-kinetic projects, water turbines. This Project aims at the fabrication of such a where one unit can provide up to 2kW of electric power [11]. -
Comparison of ORC Turbine and Stirling Engine to Produce Electricity from Gasified Poultry Waste
Sustainability 2014, 6, 5714-5729; doi:10.3390/su6095714 OPEN ACCESS sustainability ISSN 2071-1050 www.mdpi.com/journal/sustainability Article Comparison of ORC Turbine and Stirling Engine to Produce Electricity from Gasified Poultry Waste Franco Cotana 1,†, Antonio Messineo 2,†, Alessandro Petrozzi 1,†,*, Valentina Coccia 1, Gianluca Cavalaglio 1 and Andrea Aquino 1 1 CRB, Centro di Ricerca sulle Biomasse, Via Duranti sn, 06125 Perugia, Italy; E-Mails: [email protected] (F.C.); [email protected] (V.C.); [email protected] (G.C.); [email protected] (A.A.) 2 Università degli Studi di Enna “Kore” Cittadella Universitaria, 94100 Enna, Italy; E-Mail: [email protected] † These authors contributed equally to this work. * Author to whom correspondence should be addressed; E-Mail: [email protected]; Tel.: +39-075-585-3806; Fax: +39-075-515-3321. Received: 25 June 2014; in revised form: 5 August 2014 / Accepted: 12 August 2014 / Published: 28 August 2014 Abstract: The Biomass Research Centre, section of CIRIAF, has recently developed a biomass boiler (300 kW thermal powered), fed by the poultry manure collected in a nearby livestock. All the thermal requirements of the livestock will be covered by the heat produced by gas combustion in the gasifier boiler. Within the activities carried out by the research project ENERPOLL (Energy Valorization of Poultry Manure in a Thermal Power Plant), funded by the Italian Ministry of Agriculture and Forestry, this paper aims at studying an upgrade version of the existing thermal plant, investigating and analyzing the possible applications for electricity production recovering the exceeding thermal energy. A comparison of Organic Rankine Cycle turbines and Stirling engines, to produce electricity from gasified poultry waste, is proposed, evaluating technical and economic parameters, considering actual incentives on renewable produced electricity. -
Steam Turbine Corrosion and Deposits Problems and Solutions
STEAM TURBINE CORROSION AND DEPOSITS PROBLEMS AND SOLUTIONS by Otakar Jonas Consultant and Lee Machemer Senior Engineer Jonas, Inc. Wilmington, Delaware longer blades) resulted in increased stresses and vibration Otakar Jonas is a Consultant with Jonas, Inc., in Wilmington, problems and in the use of higher strength materials (Scegljajev, Delaware. He works in the field of industrial and utility steam cycle 1983; McCloskey, 2002; Sanders, 2001). Unacceptable failure corrosion, water and steam chemistry, reliability, and failure analysis. rates of mostly blades and discs resulted in initiation of numerous After periods of R&D at Lehigh University and engineering projects to investigate the root causes of the problems (McCloskey, practice at Westinghouse Steam Turbine Division, Dr. Jonas started 2002; Sanders, 2001; Cotton, 1993; Jonas, 1977, 1985a, 1985c, his company in 1983. The company is involved in troubleshooting, 1987; EPRI, 1981, 1983, 1995, 1997d, 1998a, 2000a, 2000b, 2001, R&D (EPRI, GE, Alstom), failure analysis, and in the production 2002b, 2002c; Jonas and Dooley, 1996, 1997; ASME, 1982, 1989; of special instruments and sampling systems. Speidel and Atrens, 1984; Atrens, et al., 1984). Some of these Dr. Jonas has a Ph.D. degree (Power Engineering) from the problems persist today. Cost of corrosion studies (EPRI, 2001a, Czech Technical University. He is a registered Professional Syrett, et al., 2002; Syrett and Gorman, 2003) and statistics (EPRI, Engineer in the States of Delaware and California. 1985b, 1997d; NERC, 2002) determined that amelioration of turbine corrosion is urgently needed. Same problems exist in smaller industrial turbines and the same solutions apply Lee Machemer is a Senior Engineer at Jonas, Inc., in Wilmington, (Scegljajev, 1983; McCloskey, 2002; Sanders, 2001; Cotton, 1993; Delaware. -
Preliminary Design and Optimization of Axial Turbines Accounting for Diffuser Performance
International Journal of Turbomachinery Propulsion and Power Article Preliminary Design and Optimization of Axial Turbines Accounting for Diffuser Performance Roberto Agromayor * and Lars O. Nord Department of Energy and Process Engineering, NTNU—The Norwegian University of Science and Technology, Kolbj. Hejes v. 1B, NO-7491 Trondheim, Norway; [email protected] * Correspondence: [email protected] Received: 19 May 2019; Accepted: 11 September 2019; Published: 18 September 2019 Abstract: Axial turbines are the most common turbine configuration for electric power generation and propulsion systems due to their versatility in terms of power capacity and range of operating conditions. Mean-line models are essential for the preliminary design of axial turbines and, despite being covered to some extent in turbomachinery textbooks, only some scientific publications present a comprehensive formulation of the preliminary design problem. In this context, a mean-line model and optimization methodology for the preliminary design of axial turbines with any number of stages is proposed. The model is formulated to use arbitrary equations of state and empirical loss models and it accounts for the influence of the diffuser on turbine performance using a one-dimensional flow model. The mathematical problem was formulated as a constrained, optimization problem, and solved using gradient-based algorithms. In addition, the model was validated against two test cases from the literature and it was found that the deviation between experimental data and model prediction in terms of mass flow rate and power output was less than 1.2% for both cases and that the deviation of the total-to-static efficiency was within the uncertainty of the empirical loss models. -
Comparing Combined Gas Tubrine/Steam Turbine and Marine Low Speed Piston Engine/Steam Turbine Systems in Naval Applications
POLISH MARITIME RESEARCH 4(71) 2011 Vol 18; pp. 43-48 10.2478/v10012-011-0025-8 Comparing combined gas tubrine/steam turbine and marine low speed piston engine/steam turbine systems in naval applications Marek Dzida, Assoc. Prof. Wojciech Olszewski, M. Sc. Gdansk University of Technology ABSTRACT The article compares combined systems in naval applications. The object of the analysis is the combined gas turbine/steam turbine system which is compared to the combined marine low-speed Diesel engine/steam turbine system. The comparison refers to the additional power and efficiency increase resulting from the use of the heat in the exhaust gas leaving the piston engine or the gas turbine. In the analysis a number of types of gas turbines with different exhaust gas temperatures and two large-power low-speed piston engines have been taken into account. The comparison bases on the assumption about comparable power ranges of the main engine. Key words: marine power plants, combined systems, piston internal combustion engine, gas turbine, steam turbine INTRODUCTION being the combination of a Diesel engine and a gas turbine (CODAG, CODOG) or gas turbines (COGOG, COGAG). The In recent years combined systems consisting of a gas turbine propulsion applied in the passenger liner Millenium makes and a steam turbine have started to be used as marine propulsion use of a COGES system which increases the efficiency and systems. In inland applications the efficiency of these systems operating abilities of the ship by combining the operation of can exceed 60%. In naval applications such a system was a gas turbine with a steam turbine which drives the electric used in Millenium, a passenger liner.