Analytical Study of Microchannel and Passive Microvalve "Application to Micropump Simulator"
Total Page:16
File Type:pdf, Size:1020Kb
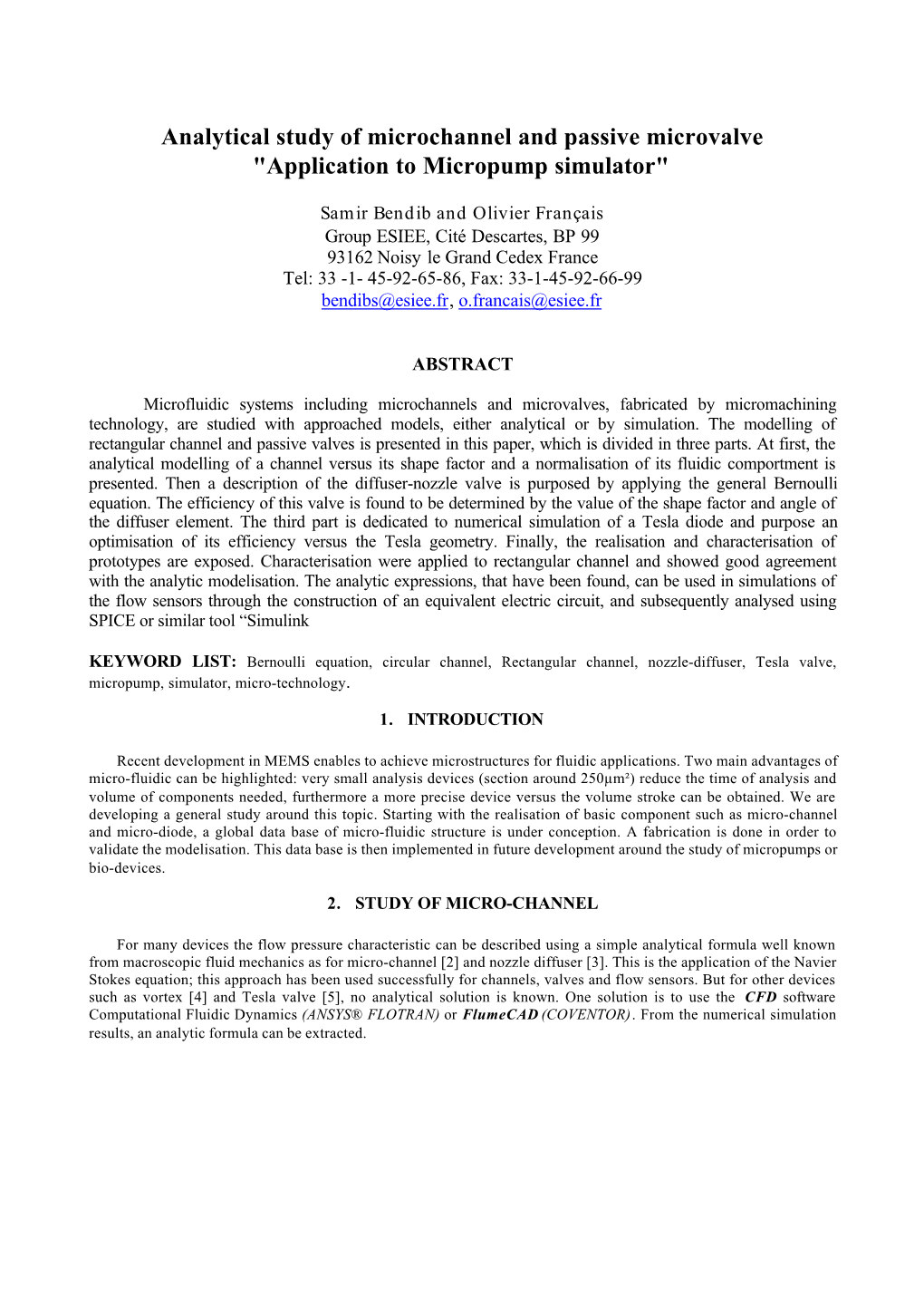
Load more
Recommended publications
-
Tesla's Fluidic Diode and the Electronic-Hydraulic Analogy Quynh M
Tesla's fluidic diode and the electronic-hydraulic analogy Quynh M. Nguyen, Dean Huang, Evan Zauderer, Genevieve Romanelli, Charlotte L. Meyer, and Leif Ristroph Citation: American Journal of Physics 89, 393 (2021); doi: 10.1119/10.0003395 View online: https://doi.org/10.1119/10.0003395 View Table of Contents: https://aapt.scitation.org/toc/ajp/89/4 Published by the American Association of Physics Teachers ARTICLES YOU MAY BE INTERESTED IN Euler's rigid rotators, Jacobi elliptic functions, and the Dzhanibekov or tennis racket effect American Journal of Physics 89, 349 (2021); https://doi.org/10.1119/10.0003372 Acoustic levitation and the acoustic radiation force American Journal of Physics 89, 383 (2021); https://doi.org/10.1119/10.0002764 How far can planes and birds fly? American Journal of Physics 89, 339 (2021); https://doi.org/10.1119/10.0003729 A guide for incorporating e-teaching of physics in a post-COVID world American Journal of Physics 89, 403 (2021); https://doi.org/10.1119/10.0002437 Gravitational Few-Body Dynamics: A Numerical Approach American Journal of Physics 89, 443 (2021); https://doi.org/10.1119/10.0003728 Frequency-dependent capacitors using paper American Journal of Physics 89, 370 (2021); https://doi.org/10.1119/10.0002655 Tesla’s fluidic diode and the electronic-hydraulic analogy Quynh M. Nguyen,a) Dean Huang, Evan Zauderer, Genevieve Romanelli, Charlotte L. Meyer, and Leif Ristrophb) Applied Math Lab, Courant Institute of Mathematical Sciences, New York University, New York, New York 10012 (Received 9 March 2020; accepted 10 October 2020) Reasoning by analogy is powerful in physics for students and researchers alike, a case in point being electronics and hydraulics as analogous studies of electric currents and fluid flows. -
A Laminar Flow-Based Microfluidic Tesla Pump Via Lithography
sensors Article A Laminar Flow-Based Microfluidic Tesla Pump via Lithography Enabled 3D Printing Mohammed-Baker Habhab, Tania Ismail and Joe Fujiou Lo * Department of Mechanical Engineering, Bioengineering Program, University of Michigan at Dearborn, 2088 IAVS Building, 4901 Evergreen Rd., Dearborn, MI 48128, USA; [email protected] (M.-B.H.); [email protected] (T.I.) * Correspondence: [email protected]; Tel.: +1-313-593-0913; Fax: +1-313-593-3851 Academic Editors: Amine Miled and Jesse Greener Received: 20 September 2016; Accepted: 18 November 2016; Published: 23 November 2016 Abstract: Tesla turbine and its applications in power generation and fluid flow were demonstrated by Nicholas Tesla in 1913. However, its real-world implementations were limited by the difficulty to maintain laminar flow between rotor disks, transient efficiencies during rotor acceleration, and the lack of other applications that fully utilize the continuous flow outputs. All of the aforementioned limits of Tesla turbines can be addressed by scaling to the microfluidic flow regime. Demonstrated here is a microscale Tesla pump designed and fabricated using a Digital Light Processing (DLP) based 3D printer with 43 µm lateral and 30 µm thickness resolutions. The miniaturized pump is characterized by low Reynolds number of 1000 and a flow rate of up to 12.6 mL/min at 1200 rpm, unloaded. It is capable of driving a mixer network to generate microfluidic gradient. The continuous, laminar flow from Tesla turbines is well-suited to the needs of flow-sensitive microfluidics, where the integrated pump will enable numerous compact lab-on-a-chip applications. Keywords: Tesla turbine; Tesla valve; microfluidic; DLP; 3D printing 1. -
Prodigal Genius BIOGRAPHY of NIKOLA TESLA 1994 Brotherhood of Life, Inc., 110 Dartmouth, SE, Albuquerque, New Mexico 87106 USA
Prodigal Genius BIOGRAPHY OF NIKOLA TESLA 1994 Brotherhood of Life, Inc., 110 Dartmouth, SE, Albuquerque, New Mexico 87106 USA "SPECTACULAR" is a mild word for describing the strange experiment with life that comprises the story of Nikola Tesla, and "amazing" fails to do adequate justice to the results that burst from his experiences like an exploding rocket. It is the story of the dazzling scintillations of a superman who created a new world; it is a story that condemns woman as an anchor of the flesh which retards the development of man and limits his accomplishment--and, paradoxically, proves that even the most successful life, if it does not include a woman, is a dismal failure. Even the gods of old, in the wildest imaginings of their worshipers, never undertook such gigantic tasks of world- wide dimension as those which Tesla attempted and accomplished. On the basis of his hopes, his dreams, and his achievements he rated the status of the Olympian gods, and the Greeks would have so enshrined him. Little is the wonder that so-called practical men, with their noses stuck in profit-and-loss statements, did not understand him and thought him strange. The light of human progress is not a dim glow that gradually becomes more luminous with time. The panorama of human evolution is illumined by sudden bursts of dazzling brilliance in intellectual accomplishments that throw their beams far ahead to give us a glimpse of the distant future, that we may more correctly guide our wavering steps today. Tesla, by virtue of the amazing discoveries and inventions which he showered on the world, becomes one of the most resplendent flashes that has ever brightened the scroll of human advancement. -
Nikola Tesla's Life and Work
1 Nikola Tesla’s Life And Work This brief, systematic summary, designed as a map, will familiarize the reader through quotations with one of the greatest minds of our history; Nikola Tesla's life and work. Like the cognition of every human life, Tesla's also starts with the cognition of his parents, since one's genetic endowments are a key determinant of one's future life and opportunities. Beyond the genetic determination we can also get to know his unique, mechanical world view that was created by the extraordinary upbringing of his and the potential of his outstanding talents, whose correctness are entirely confirmed by the results of today's neuroscience, human perception and examination of mental functions. However mention will be made of his life's events that belong clearly to a more advanced, universal consciousness, that is evidence of the interventions of the Creator. The genetic capabilities, the constant development of exceptional abilities, widespread literacy, technical studies, as well as logical thinking and common sense and due to the unquenchable desire to truly understand Nature, Nikola Tesla became a researcher, who always verified through experiments the findings that lay beneath his theories, thus making him a true naturalist, a cultivator of positive science. As a result of this, figuratively speaking he soon found the thread of knowledge, and furling it up systematically he became an outstanding figure and a founder of fields such as the AC power supply, electric lighting, high- voltage high-frequency technology, resonant power conversion, single wire or "wireless" power and information transmission, remote control and robotics, particle physics, electro therapy, harnessing renewable energy sources, radio-astronomy, tele-geodynamics, fluid mechanics, interstellar transmission of information and energy, transmutation of elements and the creation of the unified theory of natural forces. -
Diodicity Investigation of Tesla Valve
TURBO, vol. VII (2020), no. 2 DIODICITY INVESTIGATION OF TESLA VALVE Cosmin Petru SUCIU1, Razvan Edmond NICOARA1, Madalin-Constantin DOMBROVSCHI1, Emilia PRISACARIU1, Ioana Octavia BUCUR1 ABSTRACT: The Tesla valve is a NMP (no moving parts) component that facilitates the flow in one direction and inhibits the flow in the other direction. This paper studies the diodicity of two different geometries for such a component. Numerical CFD simulations are presented and the results are discussed. 3D printed parts for each geometry have been printed for an experimental campaign. The inlet and outlet pressure are measured for computing the diodicity. The results are post-processed and the geometries compared. A high diodicity Tesla Valve can be used in many applications as an upgrade, given the fact that there are no moving parts that can be damaged by high temperature or stress. KEYWORDS: fluidic diode, no-moving-parts, valvular conduit, Nikola Tesla. 1. INTRODUCTION The Tesla valve was named by its inventor (Nikola Tesla) valvular conduit. It is a unidirectional valve with fixed geometry, that allows the fluid to flow in a preferential direction. Nikola Tesla has received a patent for his invention in 1920. Tesla`s invention presents various channels, that are disposed in a way that allows the flow to pass freely in one direction, but when the direction changes, the stream is subject to rapid reversals of direction thus blocking the flow through friction and mass resistance [1]. The specific efficiency of this valvular pipe can be controlled through the number of elements (nodes). This type of valve does not block entirely the flow, but can provide a resistance dependent on direction. -
Omnipresence of Tesla's Work and Ideas
Omnipresence of Tesla’s Work and Ideas Milosˇ D. Ercegovac Abstract— Tesla made several of the most significant discover- II. MENTAL MODELS,VISUALIZATION, AND CREATIVE ies in electric power systems and wireless signal transmission. PROCESS These contributions were crucial in enabling economic and technological progress leading to our modern world. In his Tesla’s way of visualizing problems and discovering solu- long creative life, he impacted many other areas in engineering, tions in his mind before committing time and effort to the sciences, medicine, and art. This paper discusses examples of Tesla’s work as it influenced others in diverse areas over a long physical realization anticipates amazingly well the modern period of time, continuing to the present day. approach of using computer-based visualization in discovery, creation and exploration of solutions to complex problems in Index Terms— lighting, mental models, microfluidics, neu- roimaging, resonant circuits, sensors, telerobotics, thermomag- science and engineering. Without it, progress in many vital netic generators, transducers, turbines, visualization. areas such as molecular biology, design of aircraft and com- plex mechanical systems, would be hampered or impossible. I. INTRODUCTION West [33], [32] gives a fascinating account of exceptionally HIS paper discusses several examples of the continuing creative people including Faraday, Tesla, Poincare,´ and da T presence of Tesla’s work in science, engineering, and Vinci who had the ability to visualize solutions to a desired other areas. We analyze papers and patents over an extensive level of perfection. West develops a convincing argument about period of time that cite directly Tesla’s work and comment on the power of learning in ”one’s mind” with the help of ever his ideas. -
Nikola Tesla: Mechanical Oscillator
archived as http://www.stealthskater.com/Documents/Tesla_02.pdf more on Tesla is at http://www.stealthskater.com/Science.htm#Tesla Frequently "here today but gone tomorrow", the following was archived from http://www.rexresearch.com/teslamos/tmosc.htm on January 27, 2005 . This is NOT an attempt to divert readers from the aforementioned website. Indeed, the reader should only read this back-up copy if it cannot be found at the original author's site. Nikola Tesla: Mechanical Oscillator L. Anderson: Tesla's Teleforce & Tele-Geodynamics Proposals D. Pond & W. Baumgartner: Nikola Tesla's Earthquake Machine J. O'Neill: Prodigal Genius: The Life and Times of Nicola Tesla M. Cheney: Tesla: Man Out of Time Miscellanies N. Tesla: US Patent # 514,169 ~ Reciprocating Engine N. Tesla: US Patent # 517,900 ~ Steam Engine 1 Nikola Tesla's Teleforce & Telegeodynamics Proposals Leland Anderson ISBN: 0-9636012-8-8 2 important papers -- hidden for more than 60 years -- are presented for the first time. The principles behind teleforce (the particle-beam weapon) and telegeodynamics (the mechanical earth-resonance concept for seismic exploration) are fully addressed. In addition to copies of the original documents typed on Tesla's official stationery, this work also includes 2 "Reader's Aid" sections that guide the reader through the more technical aspects of each paper. The papers are followed by "Commentary" sections which provide historical background and functional explanations of the 2 devices. Significant newspaper articles and headline accounts are provided to document the first mention of these proposals. A large "Appendix" provides a wealth of related material and background information, followed by a "Bibliography" section and "Index". -
Design and Operation of a Tesla-Type Valve for Pulsating Heat Pipes
Design and operation of a Tesla-type valve for pulsating heat pipes Citation for published version (APA): de Vries, S. F., Florea, D., Homburg, F. G. A., & Frijns, A. J. H. (2017). Design and operation of a Tesla-type valve for pulsating heat pipes. International Journal of Heat and Mass Transfer, 105, 1-11. https://doi.org/10.1016/j.ijheatmasstransfer.2016.09.062 DOI: 10.1016/j.ijheatmasstransfer.2016.09.062 Document status and date: Published: 01/02/2017 Document Version: Publisher’s PDF, also known as Version of Record (includes final page, issue and volume numbers) Please check the document version of this publication: • A submitted manuscript is the version of the article upon submission and before peer-review. There can be important differences between the submitted version and the official published version of record. People interested in the research are advised to contact the author for the final version of the publication, or visit the DOI to the publisher's website. • The final author version and the galley proof are versions of the publication after peer review. • The final published version features the final layout of the paper including the volume, issue and page numbers. Link to publication General rights Copyright and moral rights for the publications made accessible in the public portal are retained by the authors and/or other copyright owners and it is a condition of accessing publications that users recognise and abide by the legal requirements associated with these rights. • Users may download and print one copy of any publication from the public portal for the purpose of private study or research. -
Fluid Diodes Design by Using Topology Optimization Method
FLUID DIODES DESIGN BY USING TOPOLOGY OPTIMIZATION METHOD Bruno Caldas de Souza Prof. Dr. Emílio Carlos Nelli Silva Dept. Mechatronics Engineering University of São Paulo, Brazil RCGI intern Workshop August 20th, 2018 Outline • Introduction to Fluid Diodes • Motivation of the Project • Objective • Problem Formulation • Topology Optimization Method • Results • Conclusions RESEARCH CENTRE FOR GAS INNOVATION 2 Introduction – Fluid Diodes • A fluid diode is a device without moving parts which causes smaller flow resistance in one direction compared to the opposite. • The basic concept is shown on the right and it was patented by Nikola Tesla in 1916. • A special kind of fluid diodes applied to turbines is the labyrinth seal. RESEARCH CENTRE FOR GAS INNOVATION 3 Labyrinth Seal Application Example Turbo parts steam turbine advanced sealing system (Link: https://www.youtube.com/watch?v=942gtbwBmcw) RESEARCH CENTRE FOR GAS INNOVATION 4 Introduction – Motivation • Labyrinth Seals are used extensively in machines • The factors influencing this fluid loss include the with high pressure and temperature, like turbines design and their maintenance. The first is the and pumps [1], even with their inherent leakage. most effective in combating gas emissions. • 60% of methane emissions are caused by leaks in • The shape of these kind of devices are so relevant pumps, turbines or pneumatic devices, coming to that there are patents [4] exploring design. leak about 4m³ a day, which amount to about 3,965 m³ per year for each device [2]. • Supercritical Carbon Dioxide (S-CO2) is a promising working fluid for future high efficiency power cycles, but the leakage from compressors may be considered. -
Determination Whether a Large Scale Tesla Valve Could Be Applicable As a Fish Passage
Determination whether a large scale Tesla valve could be applicable as a fish passage Additional Thesis K. Keizer Supervisor: N.C. van de Giesen Delft University of Technology, Department of Civil Engineering, Stevinweg 1, 2628CN Delft, PO-Box 5048, The Netherlands October, 2016 1 Special thanks to: Prof. dr. ir. Nick van de Giesen - Water Resources Management Prof. dr. ir. Wim Uijttewaal - Experimental Hydraulics Sander de Vree - Coordinator Laboratory Hans Tas - Research Assistants & Arno - Research Assistants (Trainee) Frank Kalkman - Technician & Jaap van Duin - Technician Jasper Arntz - Specialist at Arcadis 2 Table of contents Abstract……………………….………….……………………………………………………… 4 1. Introduction………………...………………………………………………………………… 4 2. Background information.......………………………………………………………………… 5 3. Materials and Methods………………………………………………………………………. 7 3.1 Experiment I……...………………………………………………………………… 7 3.2 Experiment II……..………………………………………………………………… 7 3.3 Experiment III…….………………………………………………………………… 8 4. Results and discussion……...………………………………………………….…..………… 11 4.1 Experiment I……………………………………………………………….……….. 11 4.2 Experiment II……...……..….……………………………………………………… 11 4.2.1 Flow depth…...…………………………………………………………... 11 4.2.2 Flow velocity…...………………………………………………………... 13 4.2.3 Energy dissipation...……………………………………………………... 14 4.3 Experiment III…….………………………………………………………………… 15 4.3.1 Energy dissipation………...…..…..……………………………………… 16 4.3.2 Critical flow velocity……..……………………………………………… 18 4.3.3 Pond depth………………...……………………………………………… 19 5. Conclusion and recommendations…………….………………………………………….…. -
2.Ijmperddec20192
International Journal of Mechanical and Production Engineering Research and Development (IJMPERD) ISSN (P): 2249-6890; ISSN (E): 2249-8001 Vol.9, Issue 6, Dec 2019, 13-24 © TJPRC Pvt. Ltd. STABILITY IMPROVEMENT IN NATURAL CIRCULATION LOOP USING TESLA VALVE – AN EXPERIMENTAL INVESTIGATION *U. C. ARUNACHALA 1, A. C. RAJAT 2, DHRUV SHAH 3 & UJJAWAL SUREKA 4 1,3,4 Department of Mechanical & Manufacturing Engineering, Manipal Institute of Technology, Manipal Academy of Higher Education, Manipal, India 2Department of Mechanical Engineering, National Institute of Technology Karnataka, India ABSTRACT Natural circulation loop works on the basic principle of thermosiphon effect, which doesn’t require any external force to drive the fluid in a loop. Hence they are highly applicable in power industries where there are a source and a sink. However, the flow pattern in a single-phase natural circulation loop is quite unstable especially the horizontal heater horizontal cooler configuration which results in lower loop effectiveness. A lot of research has been carried out to study these instabilities and find a way to curb them. Techniques such as tilting of loop, use of nanofluids, adding flow resistances etc. have shown promising results. But they have their own practical constraints. Hence in the present experimental study, a Tesla-type passive valve is incorporated in natural circulation loop. Due to its presence, not only Article Original stability period is reduced (at least 90 s compared to non-Tesla loop) but also unidirectional flow is achieved. The Tesla valve performed better for a broad range of heater power (90-170W) and was also able to provide noticeable resistance to the flow when the loop was inclined by 2.5° in the opposite direction. -
Development of a Low Cost Micro-Pump
University of Calgary PRISM: University of Calgary's Digital Repository Graduate Studies The Vault: Electronic Theses and Dissertations 2012-09-06 Development of a low cost micro-pump Khalilian, Sina Khalilian, S. (2012). Development of a low cost micro-pump (Unpublished master's thesis). University of Calgary, Calgary, AB. doi:10.11575/PRISM/25658 http://hdl.handle.net/11023/179 master thesis University of Calgary graduate students retain copyright ownership and moral rights for their thesis. You may use this material in any way that is permitted by the Copyright Act or through licensing that has been assigned to the document. For uses that are not allowable under copyright legislation or licensing, you are required to seek permission. Downloaded from PRISM: https://prism.ucalgary.ca UNIVERSITY OF CALGARY Development of a Low Cost Micro-pump by Sina Khalilian A THESIS SUBMITTED TO THE FACULTY OF GRADUATE STUDIES IN PARTIAL FULFILMENT OF THE REQUIREMENTS FOR THE DEGREE OF MASTER OF SCIENCE DEPARTMENT OF MECHANICAL AND MANUFACTURING ENGINEERING CALGARY, ALBERTA Aug, 2012 © Sina Khalilian 2012 i UNIVERSITY OF CALGARY FACULTY OF GRADUATE STUDIES The undersigned certify that they have read, and recommend to the Faculty of Graduate Studies for acceptance, a thesis entitled “ Development of a Low Cost Micro-pump” submitted by Sina Khalilian in partial fulfilment of the requirements for the degree of the degree of Master of Science. ________________________________________________ Supervisor, Dr. Theodor Freiheit Department of Mechanical & Manufacturing Engineering ________________________________________________ Dr. Robert W. Brennan Department of Mechanical & Manufacturing Engineering ________________________________________________ Dr. Alejandro Ramirez-Serrano Department of Mechanical & Manufacturing Engineering ________________________________________________ Dr.