Is Process Simulation Effectively Utilized in Chemical Engineering Courses
Total Page:16
File Type:pdf, Size:1020Kb
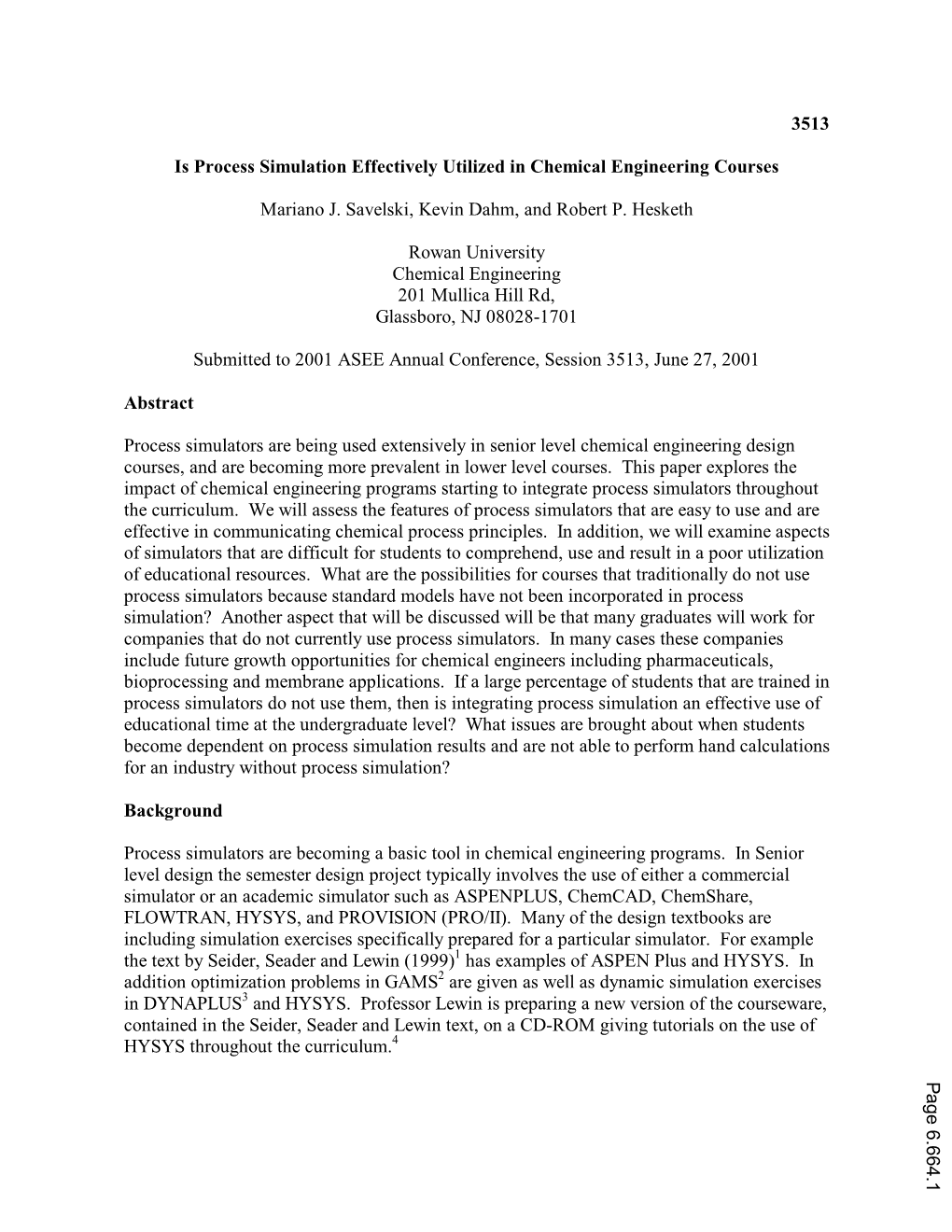
Load more
Recommended publications
-
1. Define: Unit Operation. Useful Physical Changes Occur in the Chemical Industry Is Known As a Unit Operation
INTREVIEW QUESTIONS 1. Define: Unit operation. Useful Physical changes occur in the chemical industry is known as a Unit Operation. Example: Distillation, Filtration, Drying, Extraction, Gas absorption, Crystallization, etc. 2. Define: Unit process. Useful Chemical changes with or without physical change occur in chemical industry are known as a Unit Process. Example: - Oxidation, Reduction, Alkylation, Sulfonation, Chlorination, etc. 3. Define: Boiling Point and Bubble Point. Boiling Point: -It is a temperature of a liquid at which the vapour pressure of the liquid is equal to atmospheric pressure. Bubble Point: -It is a temperature at which first bubble of vapour is formed. 4. When does liquid boil? When the vapour pressure of the liquid is equal to atmospheric pressure at that time liquid is boil. 5. Define: - Volatile Liquid. It is a tendency of a liquid to vaporize. 6. Acetone and water out of this which is more volatile and why? Acetone is more volatile than water because of boiling point of acetone (56.7 °C) is low compa re to boiling point of water (100° C) 7. What is the Relative Volatility? It is a ratio of concentration of more volatile component in vapour phase to liquid phase is called Relative Volatility 8. What is important of Relative Volatility? For separation of liquid mixture using distillation, Relative volatility should be more than 1. 9. Why is Reflux done in distillation column? and Define Reflux Ratio. For Increasing product purity. Reflux: -It is amount of distillate which is resend to distillation column is known as a reflux. Reflux Ratio: -Reflux ratio is the ratio of the portion of the overhead liquid product from a distillation column that is returned to the upper part of column to the portion of liquid collected as distillate. -
Opportunities for Catalysis in the 21St Century
Opportunities for Catalysis in The 21st Century A Report from the Basic Energy Sciences Advisory Committee BASIC ENERGY SCIENCES ADVISORY COMMITTEE SUBPANEL WORKSHOP REPORT Opportunities for Catalysis in the 21st Century May 14-16, 2002 Workshop Chair Professor J. M. White University of Texas Writing Group Chair Professor John Bercaw California Institute of Technology This page is intentionally left blank. Contents Executive Summary........................................................................................... v A Grand Challenge....................................................................................................... v The Present Opportunity .............................................................................................. v The Importance of Catalysis Science to DOE.............................................................. vi A Recommendation for Increased Federal Investment in Catalysis Research............. vi I. Introduction................................................................................................ 1 A. Background, Structure, and Organization of the Workshop .................................. 1 B. Recent Advances in Experimental and Theoretical Methods ................................ 1 C. The Grand Challenge ............................................................................................. 2 D. Enabling Approaches for Progress in Catalysis ..................................................... 3 E. Consensus Observations and Recommendations.................................................. -
Process Intensification in the Synthesis of Organic Esters : Kinetics
PROCESS INTENSIFICATION IN THE SYNTHESIS OF ORGANIC ESTERS: KINETICS, SIMULATIONS AND PILOT PLANT EXPERIMENTS By Venkata Krishna Sai Pappu A DISSERTATION Submitted to Michigan State University in partial fulfillment of the requirements for the degree of DOCTOR OF PHILOSOPHY Chemical Engineering 2012 ABSTRACT PROCESS INTENSIFICATION IN THE SYNTHESIS OF ORGANIC ESTERS: KINETICS, SIMULATIONS AND PILOT PLANT EXPERIMENTS By Venkata Krishna Sai Pappu Organic esters are commercially important bulk chemicals used in a gamut of industrial applications. Traditional routes for the synthesis of esters are energy intensive, involving repeated steps of reaction typically followed by distillation, signifying the need for process intensification (PI). This study focuses on the evaluation of PI concepts such as reactive distillation (RD) and distillation with external side reactors in the production of organic acid ester via esterification or transesterification reactions catalyzed by solid acid catalysts. Integration of reaction and separation in one column using RD is a classic example of PI in chemical process development. Indirect hydration of cyclohexene to produce cyclohexanol via esterification with acetic acid was chosen to demonstrate the benefits of applying PI principles in RD. In this work, chemical equilibrium and reaction kinetics were measured using batch reactors for Amberlyst 70 catalyzed esterification of acetic acid with cyclohexene to give cyclohexyl acetate. A kinetic model that can be used in modeling reactive distillation processes was developed. The kinetic equations are written in terms of activities, with activity coefficients calculated using the NRTL model. Heat of reaction obtained from experiments is compared to predicted heat which is calculated using standard thermodynamic data. The effect of cyclohexene dimerization and initial water concentration on the activity of heterogeneous catalyst is also discussed. -
Chemical Process Modeling in Modelica
Chemical Process Modeling in Modelica Ali Baharev Arnold Neumaier Fakultät für Mathematik, Universität Wien Nordbergstraße 15, A-1090 Wien, Austria Abstract model creation involves only high-level operations on a GUI; low-level coding is not required. This is the Chemical process models are highly structured. Infor- desired way of input. Not surprisingly, this is also mation on how the hierarchical components are con- how it is implemented in commercial chemical process nected helps to solve the model efficiently. Our ulti- simulators such as Aspen PlusR , Aspen HYSYSR or mate goal is to develop structure-driven optimization CHEMCAD R . methods for solving nonlinear programming problems Nonlinear system of equations are generally solved (NLP). The structural information retrieved from the using optimization techniques. AMPL (FOURER et al. JModelica environment will play an important role in [12]) is the de facto standard for model representation the development of our novel optimization methods. and exchange in the optimization community. Many Foundations of a Modelica library for general-purpose solvers for solving nonlinear programming (NLP) chemical process modeling have been built. Multi- problems are interfaced with the AMPL environment. ple steady-states in ideal two-product distillation were We are aiming to create a ‘Modelica to AMPL’ con- computed as a proof of concept. The Modelica source verter. One could use the Modelica toolchain to create code is available at the project homepage. The issues the models conveniently on a GUI. After exporting the encountered during modeling may be valuable to the Modelica model in AMPL format, the already existing Modelica language designers. software environments (solvers with AMPL interface, Keywords: separation, distillation column, tearing AMPL scripts) can be used. -
MATERIAL BALANCE NOTES Revision 3 Irven Rinard Department
MATERIAL BALANCE NOTES Revision 3 Irven Rinard Department of Chemical Engineering City College of CUNY and Project ECSEL October 1999 © 1999 Irven Rinard CONTENTS INTRODUCTION 1 A. Types of Material Balance Problems B. Historical Perspective I. CONSERVATION OF MASS 5 A. Control Volumes B. Holdup or Inventory C. Material Balance Basis D. Material Balances II. PROCESSES 13 A. The Concept of a Process B. Basic Processing Functions C. Unit Operations D. Modes of Process Operations III. PROCESS MATERIAL BALANCES 21 A. The Stream Summary B. Equipment Characterization IV. STEADY-STATE PROCESS MODELING 29 A. Linear Input-Output Models B. Rigorous Models V. STEADY-STATE MATERIAL BALANCE CALCULATIONS 33 A. Sequential Modular B. Simultaneous C. Design Specifications D. Optimization E. Ad Hoc Methods VI. RECYCLE STREAMS AND TEAR SETS 37 A. The Node Incidence Matrix B. Enumeration of Tear Sets VII. SOLUTION OF LINEAR MATERIAL BALANCE MODELS 45 A. Use of Linear Equation Solvers B. Reduction to the Tear Set Variables C. Design Specifications i VIII. SEQUENTIAL MODULAR SOLUTION OF NONLINEAR 53 MATERIAL BALANCE MODELS A. Convergence by Direct Iteration B. Convergence Acceleration C. The Method of Wegstein IX. MIXING AND BLENDING PROBLEMS 61 A. Mixing B. Blending X. PLANT DATA ANALYSIS AND RECONCILIATION 67 A. Plant Data B. Data Reconciliation XI. THE ELEMENTS OF DYNAMIC PROCESS MODELING 75 A. Conservation of Mass for Dynamic Systems B. Surge and Mixing Tanks C. Gas Holders XII. PROCESS SIMULATORS 87 A. Steady State B. Dynamic BILIOGRAPHY 89 APPENDICES A. Reaction Stoichiometry 91 B. Evaluation of Equipment Model Parameters 93 C. Complex Equipment Models 96 D. -
Chemical Process Modeling in Modelica
Chemical Process Modeling in Modelica Ali Baharev Arnold Neumaier Fakultät für Mathematik, Universität Wien Nordbergstraße 15, A-1090 Wien, Austria Abstract model creation involves only high-level operations on a GUI; low-level coding is not required. This is the Chemical process models are highly structured. Infor- desired way of input. Not surprisingly, this is also mation on how the hierarchical components are con- how it is implemented in commercial chemical process nected helps to solve the model efficiently. Our ulti- simulators such as Aspen PlusR , Aspen HYSYSR or mate goal is to develop structure-driven optimization CHEMCAD R . methods for solving nonlinear programming problems Nonlinear system of equations are generally solved (NLP). The structural information retrieved from the using optimization techniques. AMPL (FOURER et al. JModelica environment will play an important role in [12]) is the de facto standard for model representation the development of our novel optimization methods. and exchange in the optimization community. Many Foundations of a Modelica library for general-purpose solvers for solving nonlinear programming (NLP) chemical process modeling have been built. Multi- problems are interfaced with the AMPL environment. ple steady-states in ideal two-product distillation were We are aiming to create a ‘Modelica to AMPL’ con- computed as a proof of concept. The Modelica source verter. One could use the Modelica toolchain to create code is available at the project homepage. The issues the models conveniently on a GUI. After exporting the encountered during modeling may be valuable to the Modelica model in AMPL format, the already existing Modelica language designers. software environments (solvers with AMPL interface, Keywords: separation, distillation column, tearing AMPL scripts) can be used. -
Taking Reactive Distillation to the Next Level of Process Intensification, Chemical Engineering Transactions, 69, 553-558 DOI: 10.3303/CET1869093 554
553 A publication of CHEMICAL ENGINEERING TRANSACTIONS VOL. 69, 2018 The Italian Association of Chemical Engineering Online at www.aidic.it/cet Guest Editors: Elisabetta Brunazzi, Eva Sorensen Copyright © 2018, AIDIC Servizi S.r.l. ISBN 978-88-95608-66-2; ISSN 2283-9216 DOI: 10.3303/CET1869093 Taking Reactive Distillation to the Next Level of Process Intensification Anton A. Kissa,b,*, Megan Jobsona a The University of Manchester, School of Chemical Engineering and Analytical Science, Centre for Process Integration, Sackville Street, The Mill, Manchester M13 9PL, United Kingdom b University of Twente, Sustainable Process Technology, PO Box 217, 7500 AE Enschede, The Netherlands [email protected] Reactive distillation (RD) is an efficient process intensification technique that integrates catalytic chemical reaction and distillation in a single apparatus. The process is also known as catalytic distillation when a solid catalyst is used. RD technology has many key advantages such as reduced capital investment and significant energy savings, as it can surpass equilibrium limitations, simplify complex processes, increase product selectivity and improve the separation efficiency. But RD is also constrained by thermodynamic requirements (related to volatility differences and heat of reaction), overlapping of the reaction and distillation operating conditions, and the availability of catalysts that are active, selective and with sufficient longevity. This paper is the first to provide insights into novel reactive distillation technologies that combine RD principles with other intensified distillation technologies – e.g. dividing-wall columns, cyclic distillation, HiGee distillation, and heat integrated distillation column – potentially leading to new processes and applications. 1. Introduction Reactive distillation (RD) is one of the best success stories of process intensification technology – developed since the early 1920s – that made a strong positive impact in the chemical process industry (CPI). -
CHEMICAL REACTION ENGINEERING* Current Status and Future Directions
[eJij9iviews and opinions CHEMICAL REACTION ENGINEERING* Current Status and Future Directions M. P. DUDUKOVIC and petrochemical industry provided a fertile ground Washington University for further development of reaction engineering con St. Louis, MO 63130 cepts. The final cornerstone of this new discipline was laid in 1957 by the First Symposium on Chemical HEMICAL REACTIONS have been used by man Reaction Engineering [3] which brought together and C kind since time immemorial to produce useful synthesized the European point of view. The Amer products such as wine, metals, etc. Nevertheless, the ican and European schools of thought were not identi unifying principles that today we call chemical reac cal, but in time they converged into the subject matter tion engineering were not developed until relatively a that we know today as chemical reaction engineering, short time ago. During the decade of the 1940's (not or CRE. The above chronology led to the establish even half a century ago!) a transition was made from ment of CRE as an accepted discipline over the span descriptive industrial chemistry to the conceptual un of a decade and a half. This does not imply that all the ification of reaction processes and reactor types. The principles important in CRE were discovered then. pioneering work in this area of industrial practice was The foundation for CRE had already been established done by Denbigh [1] in England. Then in 1947, by the early work of Frank-Kamenteski, Damkohler, Hougen and Watson [2] published the first textbook Zeldovitch, etc., but at that time they represented in the U.S. -
Chemical Engineering (CHE) 1
Chemical Engineering (CHE) 1 CHE 3113 Rate Operations II CHEMICAL ENGINEERING Prerequisites: CHE 3013, CHE 3333, and CHE 3473 with grades of "C" or better. (CHE) Description: Development and application of phenomenological and empirical models to the design and analysis of mass transfer and CHE 1112 Introduction to the Engineering of Coffee (LN) separations unit operations. Description: A non-mathematical introduction to the engineering aspects Credit hours: 3 of roasting and brewing coffee. Simple engineering concepts are used Contact hours: Lecture: 3 Contact: 3 to study methods for roasting and processing of coffee. The course will Levels: Undergraduate investigate techniques for brewing coffee such as a drip coffee, pour-over, Schedule types: Lecture French press, AeroPress, and espresso. Laboratory experiences focus on Department/School: Chemical Engineering roasting and brewing coffee to teach introductory engineering concepts CHE 3123 Chemical Reaction Engineering to both engineers and non-engineers. Prerequisites: CHE 3013, CHE 3333, and CHE 3473 with grades of "C" or Credit hours: 2 better. Contact hours: Lecture: 1 Lab: 2 Contact: 3 Description: Principles of chemical kinetics rate concepts and data Levels: Undergraduate treatment. Elements of reactor design principles for homogeneous Schedule types: Lab, Lecture, Combined lecture and lab systems; introduction to heterogeneous systems. Course previously Department/School: Chemical Engineering offered as CHE 4473. General Education and other Course Attributes: Scientific Investigation, Credit hours: 3 Natural Sciences Contact hours: Lecture: 3 Contact: 3 CHE 2033 Introduction to Chemical Process Engineering Levels: Undergraduate Prerequisites: CHEM 1515, ENSC 2213, and ENGR 1412 with grades of "C" Schedule types: Lecture or better and concurrent enrollment in MATH 2233 or MATH 3263. -
Chemical Engineering Careers in the Bioeconomy
BioFutures Chemical engineering careers in the bioeconomy A selection of career profiles Foreword In December 2018, IChemE published the final report of its BioFutures Programme.1 The report recognised the need for chemical engineers to have a greater diversity of knowledge and skills and to be able to apply these to the grand challenges facing society, as recognised by the UN Sustainable Development Goals2 and the NAE Grand Challenges for Engineering.3 These include the rapid development of the bioeconomy, pressure to reduce greenhouse gas emissions, and an increased emphasis on responsible and sustainable production. One of the recommendations from the BioFutures report prioritised by IChemE’s Board of Trustees was for IChemE to produce and promote new career profiles to showcase the roles of chemical engineers in the bioeconomy, in order to raise awareness of their contribution. It gives me great pleasure to present this collection of careers profiles submitted by members of the chemical engineering community. Each one of these career profiles demonstrates the impact made by chemical engineers across the breadth of the bioeconomy, including water, energy, food, manufacturing, and health and wellbeing. In 2006, the Organisation for Economic Co-operation and Development (OECD) defined the bioeconomy as “the aggregate set of economic operations in a society that uses the latent value incumbent in biological products and processes to capture new growth and welfare benefits for citizens and nations”.4 This definition includes the use of biological feedstocks and/or processes which involve biotechnology to generate economic outputs. The output in terms of products and services may be in the form of chemicals, food, pharmaceuticals, materials or energy. -
Unit Operations for Bioprocess Engineers
Unit Operations for Bioprocess Engineers Chenming (Mike) Zhang Department of Biological Systems Engineering Virginia Polytechnic Institute and State University Blacksburg, VA 24061 Abstract Unit Operations in Biological Systems Engineering was introduced into the curriculum at Virginia Tech in 2000. It is a lecture and laboratory combined course. The lectures and experiments covered in the course had a narrow focus before the author took over in 2002. To broaden the education for students selecting the Bioprocess Engineering option within the curriculum, the author has revised the content of the course to give the students an opportunity to understand that different unit operations can be applied in various industries, namely food, biochemical, and biotechnology. The experiments have been decreased from 14 to 8 so the students could have a better grasp of the theories and applications. Students’ responses showed that it is important to design the experiments in a way to stimulate their desire to learn and perform. The author found that it is possible to give the students a better view of the various unit operations in bioprocess engineering. Page 9.1342.1 Page 1 Introduction As defined by Shuler and Kargi (2002), “Bioprocess engineers are engineers working to apply the principles of various disciplines, such as chemical, mechanical, electrical, and industrial, to processes based on using living cells or subcomponents of such cells.” In other words, bioprocess engineers are engineers who process biological materials to produce useful goods for society. Without question, bioprocess engineering is a broad-based engineering discipline. As educators, it is our job to broaden the view of the students, so they can take advantage of numerous, diverse job opportunities presented to them when they finish their BS degree. -
Handbook of Chemical Engineering Calculations
Source: HANDBOOK OF CHEMICAL ENGINEERING CALCULATIONS SECTION 1 PHYSICAL AND CHEMICAL PROPERTIES Avinash Gupta, Ph.D. Senior Principal Chemical Engineer Chevron Lummus Global Bloomfield, NJ 1.1 MOLAR GAS CONSTANT 1.2 EQUATIONS AND LIQUID-LIQUID 1.2 ESTIMATION OF CRITICAL EQUILIBRIUM DATA 1.44 TEMPERATURE FROM EMPIRICAL 1.21 ACTIVITY-COEFFICIENT-CORRELATION CORRELATION 1.2 EQUATIONS AND VAPOR-LIQUID 1.3 CRITICAL PROPERTIES FROM EQUILIBRIUM DATA 1.46 GROUP-CONTRIBUTION METHOD 1.3 1.22 CONVERGENCE-PRESSURE 1.4 REDLICH-KWONG EQUATION VAPOR-LIQUID EQUILIBRIUM K OF STATE 1.5 VALUES 1.49 1.5 P-V-T PROPERTIES OF A GAS 1.23 HEAT OF FORMATION FROM MIXTURE 1.8 ELEMENTS 1.64 1.6 DENSITY OF A GAS MIXTURE 1.12 1.24 STANDARD HEAT OF REACTION, 1.7 ESTIMATION OF LIQUID STANDARD FREE-ENERGY CHANGE, AND EQUILIBRIUM CONSTANT 1.67 DENSITY 1.14 1.25 STANDARD HEAT OF REACTION FROM 1.8 ESTIMATION OF IDEAL-GAS HEAT HEAT OF FORMATION—AQUEOUS CAPACITY 1.15 SOLUTIONS 1.68 1.9 HEAT CAPACITY OF REAL GASES 1.20 1.26 STANDARD HEAT OF REACTION FROM 1.10 LIQUID HEAT CAPACITY— HEAT OF COMBUSTION 1.68 GENERALIZED CORRELATION 1.22 1.27 STANDARD HEAT OF FORMATION 1.11 ENTHALPY DIFFERENCE FOR IDEAL FROM HEAT OF COMBUSTION 1.70 GAS 1.24 1.28 HEAT OF ABSORPTION FROM 1.12 ESTIMATION OF HEAT OF SOLUBILITY DATA 1.71 VAPORIZATION 1.24 1.29 ESTIMATION OF LIQUID VISCOSITY 1.13 PREDICTION OF VAPOR AT HIGH TEMPERATURES 1.73 PRESSURE 1.27 1.30 VISCOSITY OF NONPOLAR AND 1.14 ENTHALPY ESTIMATION— POLAR GASES AT HIGH GENERALIZED METHOD 1.29 PRESSURE 1.73 1.15 ENTROPY INVOLVING A PHASE 1.31