Ducted Fan VTOL Aircraft with a Low Drag Profile, Efficient Wing, and Pusher Propeller for High Speed Flight
Total Page:16
File Type:pdf, Size:1020Kb
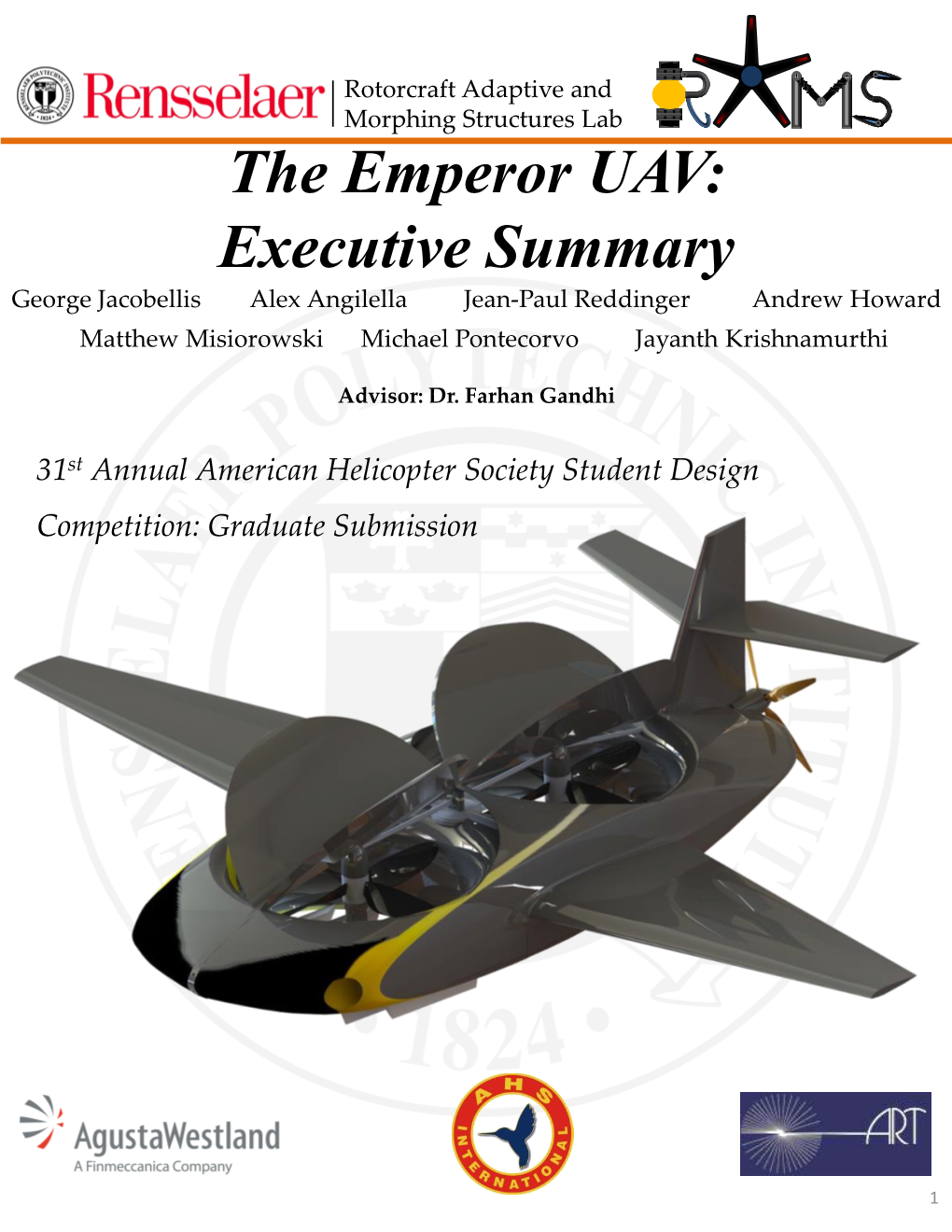
Load more
Recommended publications
-
Open LMM MS Thesis.Pdf
The Pennsylvania State University The Graduate School Department of Aerospace Engineering AERODYNAMIC EXPERIMENTS ON A DUCTED FAN IN HOVER AND EDGEWISE FLIGHT A Thesis in Aerospace Engineering by Leighton Montgomery Myers 2009 Leighton Montgomery Myers Submitted in Partial Fulfillment of the Requirements for the Degree of Master of Science December 2009 The thesis of Leighton Montgomery Myers was reviewed and approved* by the following: Dennis K. McLaughlin Professor of Aerospace Engineering Thesis Advisor Joseph F. Horn Associate Professor of Aerospace Engineering Michael Krane Research Associate PSU Applied Research Laboratory George A. Lesieutre Professor of Aerospace Engineering Head of the Department of Aerospace Engineering *Signatures are on file in the Graduate School ii ABSTRACT Ducted fans and ducted rotors have been integrated into a wide range of aerospace vehicles, including manned and unmanned systems. Ducted fans offer many potential advantages, the most important of which is an ability to operate safely in confined spaces. There is also the potential for lower environmental noise and increased safety in shipboard operations (due to the shrouded blades). However, ducted lift fans in edgewise forward flight are extremely complicated devices and are not well understood. Future development of air vehicles that use ducted fans for lift (and some portion of forward propulsion) is currently handicapped by some fundamental aerodynamic issues. These issues influence the thrust performance, the unsteadiness leading to vehicle instabilities and control, and aerodynamically generated noise. Less than optimum performance in any of these areas can result in the vehicle using the ducted fan remaining a research idea instead of one in active service. -
United States Patent (19) 11 Patent Number: 4,996,839 Wilkinson Et Al
United States Patent (19) 11 Patent Number: 4,996,839 Wilkinson et al. 45 Date of Patent: Mar. 5, 1991 54 TURBOCHARGED COMPOUND CYCLE FOREIGN PATENT DOCUMENTS DUCTED FAN ENGINE SYSTEM 3330315 3/1985 Fed. Rep. of Germany ........ 60/624 75) Inventors: Ronald Wilkinson; Ralph Benway, 916985 9/1946 France .......................... both of Mobile, Ala. 437018 10/1935 United Kingdom .................. 60/612 Primary Examiner-Michael Koczo 73 Assignee: Teledyne Industries, Inc., Los Attorney, Agent, or Firm-Gifford, Groh, Sprinkle, Angeles, Calif. Patmore and Anderson (21) Appl. No.: 329,661 (57) ABSTRACT A turbocharged, compounded cycle ducted fan engine (22 Filed: Mar. 29, 1989 system includes a conventional internal combustion engine drivingly connected to a fan enclosed in a duct. Related U.S. Application Data The fan provides propulsive thrust by accelerating air 63 Divisional Ser. No. 17,825, Feb. 24, 1987, Pat. No. through the duct and out an exhaust nozzle. A turbo 4,815,282. charger is disposed in the duct and receives a portion of the air compressed by the fan. The turbocharger com 51) Int. Cli................................................ F02K 5/02 pressor further pressurizes the air and directs it to the 52 U.S. Cl. ............ ... 60/247; 60/263; internal combustion engine where it is burned and exits 60/269; 60/605 as exhaust gas to drive the turbine. A power turbine also 58) Field of Search ................. 60/598, 605, 606, 612, driven by exhaust gas is also drivingly connected 60/624, 226.1, 247, 263, 269 through the engine to the fan to provide additional power. The size and weight of the turbocharger are (56) References Cited reduced since the compressor's work is partially U.S. -
Configuration Design and Optimization of Ducted Fan Using Parameter Based Design
DOI: 10.13009/EUCASS2017-373 7TH EUROPEAN CONFERENCE FOR AERONAUTICS AND SPACE SCIENCES (EUCASS) Configuration Design and Optimization of Ducted Fan Using Parameter Based Design Yun Ki Jung*, Kwon-Su Jeon, Cheol-Kyun Choi, Tyan Maxim, Sangho Kim, and Jae-Woo Lee ** * Konkuk University Seoul, Republic of Korea ** Konkuk University Seoul, Republic of Korea Abstract In this study, ducted fan configuration design and optimization program is developed. With this program, configuration design and optimization of ducted fan which improves hovering performance is performed. First, the configuration parameters that have effects on performance of ducted fan are selected. Based on these parameters, baseline of ducted is constructed by the program. Optimization problem is formulated based on baseline configuration. Ducted Fan Design Code is used to generate design points. With the baseline configuration, optimization is performed. After optimization, optimum configuration is obtained, and 3D modelling of optimized ducted fan is generated automatically by optimum configuration parameters. 1. Introduction Lift fan aircraft is the one of compound aircraft which is combining conventional and vertical take-off & landing (VTOL). Lift fan aircraft has many advantage than conventional type aircraft. First advantage of lift fan is that lift fan aircraft can vertically take-off and land. Second is that ducted fan is adequate to install into wing or fuselage. Third is that runway is not required. Last is that it is faster than existing rotorcraft when it is in cruise state. [1] Chao verifies that the influences of ducted fan’s inlet and exit on its figure of merit and thrust. [2][3] By optimizing configuration of inlet and exit, ducted fan’s performance can be changed. -
Optimization and Analysis of an Elite Electric Propulsion System
International Journal of Aviation, Aeronautics, and Aerospace Volume 6 Issue 5 Article 5 2019 Optimization and Analysis of an Elite Electric Propulsion System Mehakveer Singh Punjab Engineering College (Deemed to be University)., [email protected] Kapil Yadav [email protected] Satnam Singh [email protected] Vikas Chumber [email protected] Harikrishna Chavhan [email protected] Follow this and additional works at: https://commons.erau.edu/ijaaa Part of the Aeronautical Vehicles Commons, Propulsion and Power Commons, and the Systems Engineering and Multidisciplinary Design Optimization Commons Scholarly Commons Citation Singh, M., Yadav, K., Singh, S., Chumber, V., & Chavhan, H. (2019). Optimization and Analysis of an Elite Electric Propulsion System. International Journal of Aviation, Aeronautics, and Aerospace, 6(5). https://doi.org/10.15394/ijaaa.2019.1419 This Concept Paper is brought to you for free and open access by the Journals at Scholarly Commons. It has been accepted for inclusion in International Journal of Aviation, Aeronautics, and Aerospace by an authorized administrator of Scholarly Commons. For more information, please contact [email protected]. Singh et al.: OPTIMIZATION AND ANALYSIS OF AN ELITE ELECTRIC PROPULSION SYSTEM Introduction This paper is envisioned to serve the general impression of the modern technology of electric-based propulsion, its application, and scope. The aeronautics industries have been challenged to enhance efficiency, reduce noise, emission, and decrease dependency on carbon-based fuel aircraft. The aircraft of the future will be simpler to operate and more capable than today’s combustion engine due to a convergence of technologies, mainly Electric Propulsion (Rezende, Barros, & Perez 2018). An aircraft propulsion technology is mainly depended on the use of petroleum-based internal combustion engines, in the form of either aviation turbine fuel or aviation gasoline. -
Turboelectric Distributed Propulsion Test Bed Aircraft
ROLLING HILLS RESEARCH CORPORATION Turboelectric Distributed Propulsion Test Bed Aircraft LEARN Phase I FINAL REPORT Contract Number NNX13AB92A Principal Investigator: Michael Kerho Rolling Hills Research Corporation th November 11 , 2013 Any opinions, findings, and conclusions or recommendations expressed in this material are those of the author(s) and do not necessarily reflect the views of the National Aeronautics and Space Administration. 420 North Nash Street, El Segundo, CA 90245 www.RollingHillsResearch.com [email protected] (310) 640-8781 (310) 640-0031 fax ROLLING HILLS RESEARCH CORPORATION 1 PROJECT SUMMARY In order to meet future goals for aircraft efficiency for proposed large reductions in fuel burn, emissions, and noise, next generation aircraft will have to employ new technologies for both the aerodynamics and propulsion. One configuration which shows significant promise is the Hybrid Blended Wing Body (HBWB) coupled with a turboelectric distributed propulsion (TeDP) system. The revolutionary TeDP propulsion concept uses electric motor driven fans to provide propulsive thrust, with the gas turbine generators providing electric power for the system. The TeDP concept has several distinct advantages, including boundary layer ingestion (BLI), re- energizing the wake of the airframe with the fan thrust stream, decoupling the propulsion from the power source, a very high effective bypass ratio, ultimate redundancy for increased safety, and differential thrust control for directional stability and trim. There are also significant challenges associated with TeDP, including increased inlet distortion due to BLI. The TeDP concept also leads to very close coupling between the aerodynamics and propulsion of the airframe. Significant interactions exist between the sectional aero performance and thrust level. -
Introduction to Airbreathing Propulsion Systems
Introduction to airbreathing propulsion systems Integrated project: AIAA aircraft design competition 1er master Aerospace 2020 Koen Hillewaert, Université de Liège Design of Turbomachines, A&M [email protected] Remy Princivalle, Principal Engineer, Safran Aero Boosters [email protected] 1. Balances, thrust and performance Drag / thrust definition 1. Balances, thrust and performance Airbreathing engines: acceleration of (clean) air mass flow ● Thrust = acceleration force of engine mass flow from flight vf to jet velocity vj ● Powers – Propulsive power → airplane acceleration : – Mechanical power → fluid acceleration : – Lost power ● Propulsive efficiency: ● Increasing propulsive efficiency for constant thrust – increase mass flow, decrease jet velocity – Ingest flow at speed lower than flight speed 1. Balances, thrust and performance Airbreathing engines: Boundary Layer Ingestion ● ● 1. Balances, thrust and performance Airbreathing engines: classical performance parameters ● Thermal energy ! = mf Δhf – Fuel mass flow rate: – Fuel to air ratio: – Fuel lower heating value: ● "verall efficiency propulsive power Pp versus thermal energy ! – Propulsive efficiency: – Thermal efficiency: ● Efficiency $ Thrust specific fuel consumption (TSFC) ● Compacity $ Specific thrust 2. Jet engines Generation of high” speed "et through e#pansion over no%%le Snecma/'' (lympus 593 Afterburning ,urbo"et -./ Leap -i$il ,urbofan Snecma /88 Afterburning Turbofan 2. Jet engines Generation of high” speed "et through e#pansion over no%%le ● Ingestion of ma air at flight speed in nacelle – Ram effect: increased total T and p due to relative Mach num!er Mf ● Increase total pressure and temperature – Mechanical : fan – Thermal : gas generator " #rayton – $fter!urning ● #(pansion over e(haust noz)le to ambient pressure – %ho&ed – $dapted 2. Jet engines -ore flow: Brayton thermodynamic cycle ● Thermodynamic cycle – $dia!atic compression ' → ( : – %om!ustion ( → ) : – $dia!atic e*pansion )+, : 2. -
Ducted Fan Aerodynamics and Modeling, with Applications of Steady and Synthetic Jet Flow Control
Ducted Fan Aerodynamics and Modeling, with Applications of Steady and Synthetic Jet Flow Control Osgar John Ohanian III Dissertation submitted to the faculty of the Virginia Polytechnic Institute and State University in partial fulfillment of the requirements for the degree of Doctor of Philosophy In Mechanical Engineering Daniel J. Inman, Committee Chair Kevin B. Kochersberger Andrew J. Kurdila William H. Mason Sam B. Wilson May 4th, 2011 Blacksburg, VA Keywords: ducted fan, shrouded propeller, synthetic jets, flow control, aerodynamic modeling, non-dimensional, unmanned aerial vehicle, micro air vehicle Copyright 2011, Osgar John Ohanian III Ducted Fan Aerodynamics and Modeling, with Applications of Steady and Synthetic Jet Flow Control Osgar John Ohanian III ABSTRACT Ducted fan vehicles possess a superior ability to maximize payload capacity while minimizing vehicle size. Their ability to both hover and fly at high speed is a key advantage for information-gathering missions, particularly when close proximity to a target is essential. However, the ducted fans aerodynamic characteristics pose difficulties for stable vehicle flight and therefore require complex control algorithms. In particular, they exhibit a large nose-up pitching moment during wind gusts and when transitioning from hover to forward flight. Understanding ducted fan aerodynamic behavior and how it can be altered through flow control techniques are the two prime objectives of this work. This dissertation provides a new paradigm for modeling the ducted fans nonlinear behavior and new methods for changing the duct aerodynamics using active flow control. Steady and piezoelectric synthetic jet blowing are employed in the flow control concepts and are compared. The new aerodynamic model captures the nonlinear characteristics of the force, moment, and power data for a ducted fan, while representing these terms in a set of simple equations. -
Air Breathing Propulsion.Pdf
AERONAUTICAL ENGINEERING_MRCET (AUTONOMOUS INSTITUTION) AIR BREATHING PROPULSION (R18A2109) COURSE FILE II B. Tech II Semester (2019-2020) Prepared By Prof Vedantam Ravi Department of Aeronautical Engineering MALLA REDDY COLLEGE OF ENGINEERING & TECHNOLOGY (Autonomous Institution – UGC, Govt. of India) Affiliated to JNTU, Hyderabad, Approved by AICTE - Accredited by NBA & NAAC – ‘A’ Grade - ISO 9001:2015 Certified) Maisammaguda, Dhulapally (Post Via. Kompally), Secunderabad – 500100, Telangana State, India. 1 AERONAUTICAL ENGINEERING_MRCET (AUTONOMOUS INSTITUTION) MRCET VISION To become a model institution in the fields of Engineering, Technology and Management. To have a perfect synchronization of the ideologies of MRCET with challenging demands of International Pioneering Organizations. MRCET MISSION To establish a pedestal for the integral innovation, team spirit, originality and competence in the students, expose them to face the global challenges and become pioneers of Indian vision of modern society. MRCET QUALITY POLICY To pursue continual improvement of teaching learning process of Undergraduate and Post Graduate programs in Engineering & Management vigorously. To provide state of art infrastructure and expertise to impart the quality education. 1 AERONAUTICAL ENGINEERING_MRCET (AUTONOMOUS INSTITUTION) PROGRAM OUTCOMES Engineering Graduates will be able to: 1. Engineering knowledge: Apply the knowledge of mathematics, science, engineering fundamentals, and an engineering specialization to the solution of complex engineering problems. 2. Problem analysis: Identify, formulate, review research literature, and analyze complex engineering problems reaching substantiated conclusions using first principles of mathematics, natural sciences, and engineering sciences. 3. Design / development of solutions: Design solutions for complex engineering problems and design system components or processes that meet the specified needs with appropriate consideration for the public health and safety, and the cultural, societal, and environmental considerations. -
Review on Ducted Fans for Compound Rotorcraft
\ Zhang, T. and Barakos, G. N. (2020) Review on ducted fans for compound rotorcraft. Aeronautical Journal, 124, pp. 941-974. (doi: 10.1017/aer.2019.164) The material cannot be used for any other purpose without further permission of the publisher and is for private use only. There may be differences between this version and the published version. You are advised to consult the publisher’s version if you wish to cite from it. http://eprints.gla.ac.uk/206001/ Deposited on 16 December 2019 Enlighten – Research publications by members of the University of Glasgow http://eprints.gla.ac.uk Review on Ducted Fans for Compound Rotorcraft Tao Zhang 1 and George N. Barakos 2 CFD Laboratory, School of Engineering, University of Glasgow, G12 8QQ, Scotland, UK www.gla.ac.uk/cfd Abstract This paper presents a survey of published works on ducted fans for aeronautical ap- plications. Early and recent experiments on full- or model-scale ducted fans are reviewed. Theoretical studies, lower-order simulations and high-fidelity CFD simulations are also summarised. Test matrices of several experimental and numerical studies are compiled and discussed. The paper closes with a summary of challenges for future ducted fan research. Nomenclature A Propeller disk area Ae Duct exit area AoA Duct angle of attack cduct Duct profile chord length Din Duct inner diameter FoM Figure of Merit Ma Mach number Pdf Ducted fan power Pop Open propeller power Re Reynolds number (Re = V∞cduct/ν∞) RPM Revolutions Per Minute Tdf Duct fan thrust 1PhD Candidate - [email protected] -
Airplane Flying Handbook (FAA-H-8083-3B) Chapter 15
Chapter 15 Transition to Jet-Powered Airplanes Introduction This chapter contains an overview of jet powered airplane operations. The information contained in this chapter is meant to be a useful preparation for, and a supplement to, formal and structured jet airplane qualification training. The intent of this chapter is to provide information on the major differences a pilot will encounter when transitioning to jet powered airplanes. In order to achieve this in a logical manner, the major differences between jet powered airplanes and piston powered airplanes have been approached by addressing two distinct areas: differences in technology, or how the airplane itself differs; and differences in pilot technique, or how the pilot addresses the technological differences through the application of different techniques. For airplane-specific information, a pilot should refer to the FAA-approved Airplane Flight Manual for that airplane. 15-1 Jet Engine Basics Although the propeller-driven airplane is not nearly as efficient as the jet, particularly at the higher altitudes and cruising A jet engine is a gas turbine engine. A jet engine develops speeds required in modern aviation, one of the few advantages thrust by accelerating a relatively small mass of air to very the propeller-driven airplane has over the jet is that maximum high velocity, as opposed to a propeller, which develops thrust is available almost at the start of the takeoff roll. Initial thrust by accelerating a much larger mass of air to a much thrust output of the jet engine on takeoff is relatively lower slower velocity. and does not reach peak efficiency until the higher speeds. -
Classifications of Aircraft Engines
Aeronautic Techniques Engineering Assist lecturer: Ali H. Mutib Aircraft Engines 3rd Class Classifications of Aircraft Engines An aircraft engine (or aero engine) is a propulsion system for an aircraft. Aircraft engines are the key module or the heart in aviation progress. Aero engines must be: 1. Reliable, as losing power in an airplane, is a substantially greater problem than in road vehicles. 2. Operate at extreme temperature, pressure and speed. 3. Light weight as a heavy engine increases the empty weight of the aircraft and reduces its payload. 4. Powerful, to overcome the weight and drag of the aircraft. 5. Small and easily streamlined to minimize the created drag. 6. Field repairable to keep the cost of replacement down. Minor repairs should be relatively inexpensive and possible outside of specialized shops. 7. Fuel efficient to give the aircraft the range and maneuverability the design requires. 8. Capable of operating at sufficient altitude for the aircraft. 9. Generate the least noise. 10. Generates the least emission. Aero engines may be classified based on input power into three main categories, namely, internal combustion engines, external combustion engines, and other power sources (Fig. 1-1). 1.1 External Combustion External combustion engines are steam, stirling, or nuclear engines. In these types, all heat transfer takes place through the engine wall. This is in contrast to an internal combustion engine where the heat input is by combustion of a fuel within the body of the working fluid. 1.1.1 Steam Engines Steam aircraft are aircraft that are propelled by steam engines. They were unusual devices because of the difficulty in producing a power plant with a high enough power to weight ratio to be practical. -
Design and Optimization of a Ducted Fan VTOL MAV Controlled by Electric Ducted Fans
DOI: 10.13009/EUCASS2019-108 8TH EUROPEAN CONFERENCE FOR AERONAUTICS AND AEROSPACE SCIENCES (EUCASS) DOI: 108 Design and optimization of a ducted fan VTOL MAV controlled by Electric Ducted Fans Yacoubi Moaad?, Jlassi Alaaeddine, Karoun Jawad, Ben Kirane Tarik, Bekkali Lekman, Jhabli Hamza and Hendrick Patrick? Université Libre de Bruxelles (ULB) - Aero-Thermo-Mechanics department - School of Engineering (Polytechnic School)? Avenue F. D. Roosevelt 50 (CP165/41), 1050 Brussels, Belgium [email protected] Abstract In October 2013, we presented our ducted fan VTOL MAV prototype, Dulbema (see figure 1), in the Journal of Mechanic Engineering and Automation (JMEA).1 From an aerodynamic study carried out at the Université Libre de Bruxelles (ULB), in pursuit of the latest Minidrones competition issued by the French Aerospace Lab ONERA, the ULB decided to continue the development and optimization of a ducted fan MAV, that was built for this competition and for which VTOL capabilities and autonomous flight were mandatory. This paper explains how we want to increase the maneuverability of our drone. 1. Introduction Since the first flight of Sikorsky Aircraft Corporation’s Cypher UAV in 1992,2 several concepts of ducted fan have emerged and continue to emerge across the world. The two counter-rotating coaxial rotors, which allowed flight con- trol of the Cypher were giving up due mechanical complexity and replaced by a quadrant of vanes. In the years 2000s, a large number of ducted fan UAVs, equipped with this quadrant of vanes, made their first flights: the iStar (Allied Aerospace - 2000), the Hovereye (Bertin Technologies-2004), the T-Hawk (Honeywell - 2005), the Fantail (Singapore Technology Aerospace - 2006), and many more.