Improve the Efficiency of a Plastic Film Capacitor Assembly Line by Use of Simulation Software: a Case Study of C Company
Total Page:16
File Type:pdf, Size:1020Kb
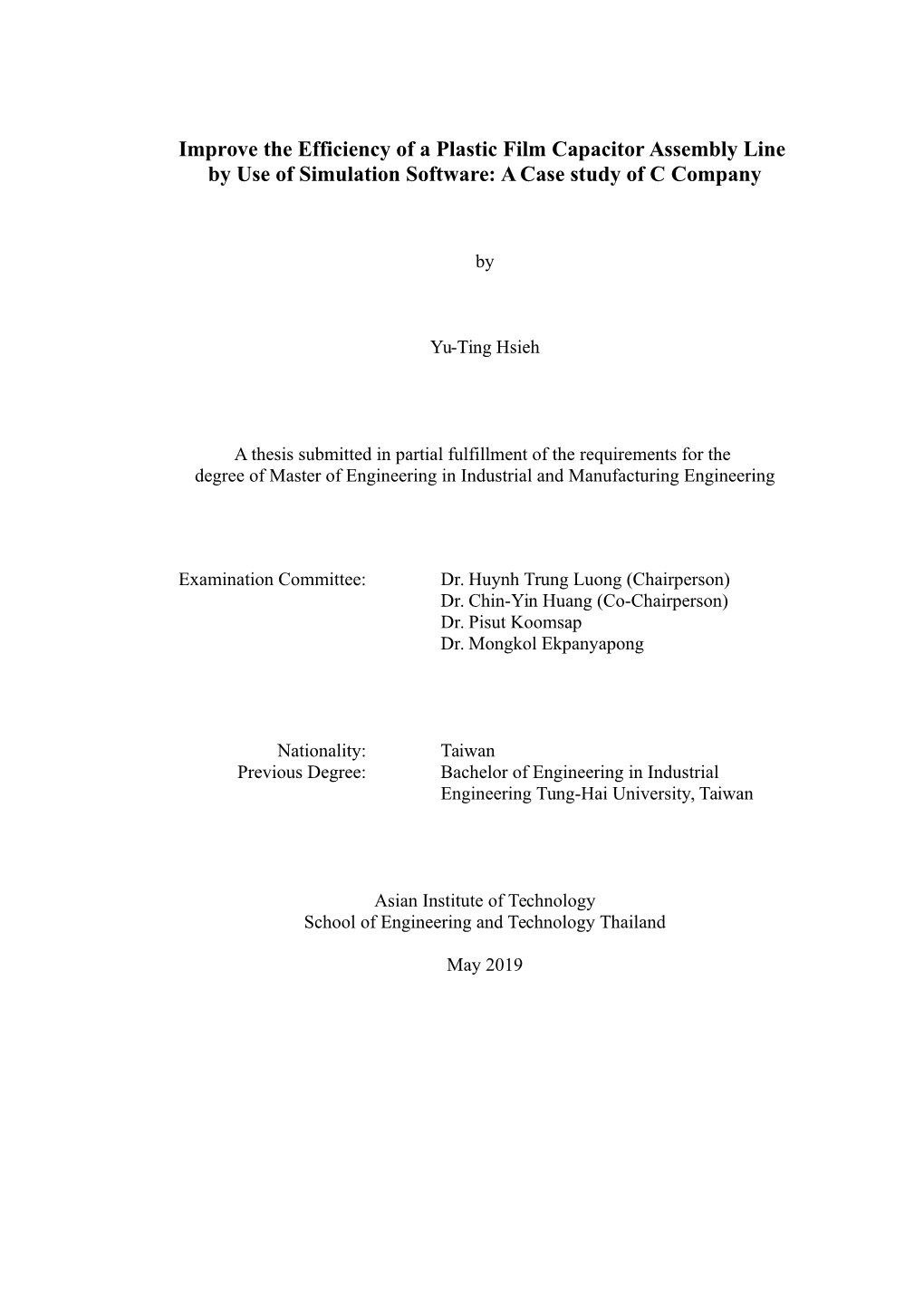
Load more
Recommended publications
-
A Review of Assembly Line Changes for Lean Manufacturing
IOSR Journal of Mechanical and Civil Engineering (IOSR-JMCE) ISSN: 2278-1684, PP: 01-05 www.iosrjournals.org A Review of Assembly Line Changes for Lean Manufacturing Awasare Anant Dattatray 1, M.V.Kavade 2 1 (Mechanical Engineering Department, Rajarambapu institute of Technology India) 2(Head Mechanical Engineering Department, Rajarambapu institute of Technology, India) ABSTRACT: The orientation towards an efficient mass customization confronts most companies with two opposing requirements: While the applied mass production system should be able to produce a huge product variety, the cost must be kept low. Therefore assembly lines have to be planned in a much more flexible way. The more complex the product, the more extensive the product mix—the more difficult the task. Shorter product life cycles also complicate the situation. Due to the volatile nature of market, companies cannot afford to manufacture same type of product for long period of time and neither can maintain high inventory level; to tackle this problem we propose a Continuous improvement tools and techniques are introduced to address these issues, allowing the manufacturing of superior quality products with efficient processes. The Lean tools and techniques is one of them. Keywords - production planning, Mixed-model assembly line balancing, Just-in-time scheduling, Lean tools, Product life cycle I. INTRODUCTION Assembly is an important manufacturing process for cost effective product variety. Significant research has been done in the Design and operations of assembly systems in support of high product variety, but many opportunities exist for future research. Assembly is the capstone process for product realization where component parts and subassemblies are integrated together to form the final products. -
Panel Assembly Line (PAL) for High Production Rates
2015-01-2492 Panel Assembly Line (PAL) for High Production Rates Michael Assadi, Sean Hollowell, Joseph Elsholz Electroimpact Inc. Samuel Dobbs, Brian Stewart Boeing Co. Copyright © 2015 SAE International Abstract Developing the most advanced wing panel assembly line for very The final solution was a coherent, streamlined and efficient assembly high production rates required an innovative and integrated solution, line capable of very high aircraft production rates (Figure 1). relying on the latest technologies in the industry. Looking back at over five decades of commercial aircraft assembly, a clear and singular vision of a fully integrated solution was defined for the new panel production line. The execution was to be focused on co-developing the automation, tooling, material handling and facilities while limiting the number of parties involved. Using the latest technologies in all these areas also required a development plan, which included pre-qualification at all stages of the system development. Planning this large scale project included goals not only for the final solution but for the development and implementation stages as well. The results: Design/build philosophy reduced project time and the number of teams involved. This allowed for easier communication and extended development time well into the project. All design teams (machine, tooling, automation, controls) Figure 1 PAL, automation cell, Line 4, Position 1 (L4P1) collocated and worked together on integration during all stages of development and implementation for the highest Introduction level of integration. Innovative integration of the tooling and the automated equipment evolved throughout project with the teams At the conception of the Panel Assembly Line (PAL), goals targeted working as one group. -
HANDLING and ASSEMBLY Technologysubject to Change Without Notice
INDUSTRY GUIDE HANDLING AND ASSEMBLY TECHNOLOGY EFFICIENT APPLICATIONS SOLUTIONS HANDLING AND ASSEMBLY TECHNOLOGYSubject to change without notice TABLE OF CONTENTS 2 HANDLING AND ASSEMBLY TECHNOLOGY | SICK 8019952/2016-05-13 Subject to change without notice TABLE OF CONTENTS Challenges Challenges in handling and assembly technology 4 Applications in focus The application graphics shown are not binding, they are no substitute for the need to seek expert technical advice. Small part assembly: Example of pre-assembly involving an optics module 6 Small part assembly: Example of pre-assembly involving a housing assembly 14 Small part assembly: Example of final assembly involving a sensor 28 Products Product overview 42 Special pages We simply detect any object 118 IO-Link 120 Software Tool Sopas 122 Smart Sensor Solutions 124 4Dpro 126 Expertise in machines safety 128 Safe control solutions 130 Safety controller Flexi Soft 132 Safe networking: Flexi Line 134 Safe sensor cascade: Flexi Loop 135 Safe motion monitoring 136 Encoder and Motor feedback systems 138 General information Company 140 Industries 142 SICK LifeTime Services 144 Versatile product range for industrial automation 146 Industrial communication and device integration 150 Services 155 8019952/2016-05-13 HANDLING AND ASSEMBLY TECHNOLOGY | SICK 3 Subject to change without notice HANDLING AND ASSEMBLY TECHNOLOGYSubject to change without notice CHALLENGES Challenges in handling and assembly technology Many industries such as automotive, electronics, metal, machine tools, and medical engineering can be identified as the driving force behind handling and assembly technology. They rely heavily on automated han- dling and assembly processes that in turn contribute to streamlining high quality and accuracy and improving productivity and PSDI times. -
High Volume Automated Spar Assembly Line (SAL) 2017-01-2073 Published 09/19/2017
High Volume Automated Spar Assembly Line (SAL) 2017-01-2073 Published 09/19/2017 Rick Calawa Electroimpact Inc. Gavin Smith Boeing Co CITATION: Calawa, R. and Smith, G., "High Volume Automated Spar Assembly Line (SAL)," SAE Technical Paper 2017-01-2073, 2017, doi:10.4271/2017-01-2073. Copyright © 2017 SAE International Abstract build process and an exercise of the lean principles. As is typical, relatively good data was available from the automated equipment, but The decision to replace a successful automated production system at analyzing it showed that machine run time was only a fraction of the the heart of a high volume aircraft factory does not come easily. A point overall build time. Numerous manual interactions required frequent is reached when upgrades and retrofits are insufficient to meet machine stops. All maintenance required production stops or late increasing capacity demands and additional floor space is simply night and weekend work. Build times varied widely. unavailable. The goals of this project were to increase production volume, reduce floor space usage, improve the build process, and The wish list for a new spar production system was ambitious: smooth factory flow without disrupting today’s manufacturing. Two decades of lessons learned were leveraged along with advancements in • No large production disruptions. the aircraft assembly industry, modern machine control technologies, and maturing safety standards to justify the risk and expense of a • Increase production capacity. ground-up redesign. This paper will describe how an automated wing ◦ Create a single flow line and reduce buffer requirements by spar fastening system that has performed well for 20 years is analyzed matching the takt time of the wing lines. -
Iot Integrated Assembly Line - a Conceptual Model Development for Car Toys Assembly Line
Advances in Intelligent Systems Research, volume 173 1st International Conference on Engineering and Management in Industrial System (ICOEMIS 2019) IoT Integrated Assembly Line - a conceptual model development for car toys assembly line I Kurniawan,1, S Awibowo,1 and A T Pratama1 1 Department of Industrial Engineering, Swiss German University, Alam Sutera, Tangerang, Banten, Indonesia Keywords: Lean Manufacturing, Cloud Manufacturing (CMfg), Internet of Things (IoT) Abstract. Lean manufacturing is a common methodology widely used by manufacturers around the world. The keys in order to apply lean manufacturing are efficiency and continuous improvement. Efficiency can be achieved towards the utilization of technology between shopfloor and supporting business layers occurs in a system. One of the technologies that can be used is IoT (Internet of Things) and Cloud Manufacturing (CMfg) in specific. This paper contains the concept design of IoT technologies that will be applied in a car toys assembly line. Technology such as RFID, Sensors, and Android-based cloud services will be included in the assembly line system design. RFID and sensors are used to capture a number of components & subassembly parts that occur in the assembly line and the data captured will be forwarded to the ERP Systems. Android-based cloud services are used to monitor and control the systems especially for the shop floor area. Introduction Nowadays, all manufacturers around the world are trying to achieve efficiency as high as possible that being driven by global competition and the fast changing of market demand and needs. Efficiency becomes one of the most critical factors in order to reduce resources usage such as labours, materials, and machines which all leading to cost reduction and productivity increases. -
Automated High Speed Assembly Machine Design
AUTOMATED HIGH SPEED ASSEMBLY MACHINE DESIGN Murat Demirci Zheng Jeremy Li, PhD Graduate Student Associate Professor School of Engineering School of Engineering University of Bridgeport University of Bridgeport Abstract Recent years, automation is still important for industrial world and in the global economy. Because of the global competition, industries started to look for new technologies and designs in automation field. There is no more enough time, energy and material to catch people needs for industries in nowadays. Thus, automated systems are becoming more interesting and important. The potential benefits of automated systems are reducing the cost of product, labor and waste; increasing the production quality, repeatability, work safety. In this paper, I describe the design steps of an automated high speed machine which is assembling the parts of a pen, according to manufacturing and production specifications. In the design project, automated system perform different kinds of process in assembly line, such as cartridge loading, point fitting, ink filling, plug fitting, gas charging and cap installing and final sealing. Furthermore, as our goals in project, automated machine must be cheaper, easier to maintain and working at “high speed” repeatedly. Working on the design project, it was really good experience to solve major design problems and to understand of engineering technology limitations in today’s world. I concluded my paper with a description designing of an automated high speed system and its distinguished advantages. Introduction In current world, the population of humanity is increasing day by day. Simultaneously, people needs are increasing, as well. In order to catch this trend and to meet the people needs; design engineers created automated machines to produce more products in short times. -
TRANSACTION COST LIMITS to ECONOMIES of SCALE Cotton M
DO RATE AND VOLUME MATTER? TRANSACTION COST LIMITS TO ECONOMIES OF SCALE Cotton M. Lindsay & Michael T. Maloney Department of Economics Clemson University In the traditional treatment, economies of scale are attributed to a hodgepodge of sources. A typical list might include Adam Smith's famous "division of labour," economies of large machines, the integration of processes, massed reserves, and standardization. The list can be partly systematized because, when considered in detail, these various economies are themselves the result of various other more basic and occasionally overlapping principles. For example, both economies of massed reserves and economies of standardi- zation are to a certain extent the product of the statistical “law of large numbers.” However, even this analysis fails to strike to the heart of the matter because the technological factors however described that reduce costs with scale do not in themselves imply that large firms can produce at lower cost than small firms. The possible presence of such technological scale economies does not give us adequate knowledge to predict the structure of industry. These forces of nature may combine to make it cheaper to get things done in big chunks. However, this potential will be economically important only in the presence of transactions costs. Firms can specialize their production processes and hire out the jobs that require large scale. Realistically all firms hire out some portion of the production process regard- less of their size. General Motors ships many of its automobiles by rail, but does not own a railroad for this purpose. Anaconda uses a great deal of fuel oil in its production of copper, but it does not own oil wells or refineries. -
Cost Concepts the Cost Function
(Largely) Review: Cost concepts The Cost Function • Cost function C(q): minimum cost of producing a given quantity q • C(q) = F + V C(q), where { Fixed costs F : cost incurred regardless of output amount. Avoidable vs. sunk: crucial for determining shut-down decisions for the firm. { Variable costs V C(q); vary with the amount produced. C(q) { Average cost AC(q) = q @C(q) { Marginal cost MC(q) = @q V C(q) F { AV C(q) = q ; AF C(q) = q ; AC(q) = AV C(q) + AF C(q). Example • C(q) = 125 + 5q + 5q2 • AC(q) = • MC(q) = • AF C(q) = 125=q • AV C(q) = 5 + 5q q AC(q) MC(q) 1 135 15 • 3 61.67 35 5 55 55 7 57.86 75 9 63.89 95 • AC rises if MC exceeds it, and falls if MC is below it. Implies that MC intersects AC at the minimum of AC. Short-run vs. long-run costs: • Short run: production technology given • Long run: can adapt production technology to market conditions • Long-run AC curve cannot exceed short-run AC curve: its the lower envelope Example: \The division of labor is limited by the extent of the market" (Adam Smith) • Division of labor requires high fixed costs (for example, assembly line requires high setup costs). • Firm adopts division of labor only when scale of production (market demand) is high enough. • Graph: Price-taking firm has \choice" between two production technologies. Opportunity cost The opportunity cost of a product is the value of the best forgone alternative use of the resources employed in making it. -
What Was the Assembly Line ?
59 WHAT WAS THE ASSEMBLY LINE ? DAVID E. NYE INTRODUCTION Today, ”assembly line” immediately suggests Asian or Latin-American factories where poorly-paid workers make consumer goods for export to the West. For example, many US corporations shifted jobs to northern Mexico beginning in 1965 as part of the Border Industrialization Program. This process accelerated dramatically after January 1, 1994, when the North American Free Trade Agreement (NAFTA) went into effect. It abolished tariffs and made re-importation of assembly line goods easy. By 2000, 1.2 million US jobs had been relocated to Mexico. Most of the Mexicans hired were semi-skilled women, preferred both for their manual dexterity and their willingness to accept low wages.1 Corporations built factories where environmental legislation was lax and unions were weak or non-existent. In such places, “the danger is that repression rather than innovation becomes a competitive advantage.”2 Yet if the assembly line of today is often part of a global production system for offshore, semi-skilled work, at its inception in 1913 the Americans saw the assembly line as the guarantor of high wages and domestic prosperity. This essay reviews the origins of the assembly line, what exactly it was as a technology, and how it was initially understood. In hindsight, it was less a beginning than a mid-point in long- term developments that are still underway. Historians frequently refer to the assembly line as an historical stage, in a sequence from Taylorism to Fordism to “post-Fordism,” with additional stages sometimes included such as “lexible production,” “lean production” and most recently “post- lean production.”3 As convenient as these historical stages once seemed, their proliferation suggests that the whole notion of a sequence was mistaken to begin with. -
The Industrial Revolution in Services *
The Industrial Revolution in Services * Chang-Tai Hsieh Esteban Rossi-Hansberg University of Chicago and NBER Princeton University and NBER May 12, 2021 Abstract The U.S. has experienced an industrial revolution in services. Firms in service in- dustries, those where output has to be supplied locally, increasingly operate in more markets. Employment, sales, and spending on fixed costs such as R&D and man- agerial employment have increased rapidly in these industries. These changes have favored top firms the most and have led to increasing national concentration in ser- vice industries. Top firms in service industries have grown entirely by expanding into new local markets that are predominantly small and mid-sized U.S. cities. Market concentration at the local level has decreased in all U.S. cities but by significantly more in cities that were initially small. These facts are consistent with the availability of a new menu of fixed-cost-intensive technologies in service sectors that enable adopters to produce at lower marginal costs in any markets. The entry of top service firms into new local markets has led to substantial unmeasured productivity growth, particularly in small markets. *We thank Adarsh Kumar, Feng Lin, Harry Li, and Jihoon Sung for extraordinary research assistance. We also thank Rodrigo Adao, Dan Adelman, Audre Bagnall, Jill Golder, Bob Hall, Pete Klenow, Hugo Hopenhayn, Danial Lashkari, Raghuram Rajan, Richard Rogerson, and Chad Syverson for helpful discussions. The data from the US Census has been reviewed by the U.S. Census Bureau to ensure no confidential information is disclosed. 2 HSIEH AND ROSSI-HANSBERG 1. -
Mechanization and Automation by the Manufacturing of Removable Modular Buildings
Mechanization and Automation by the Manufacturing of Removable Modular Buildings Frans van Gassel Eindhoven University of Technology, Faculty of Building and Architecture, P.O. BOX 513, NL 5600 MB Eindhoven, The Netherlands. ABSTRACT During the last ten years Removable Modular Building Systems in the Netherlands have made remarkable progress by using mechanization and automation. These are not the only techniques, as logistic techniques, design according to a modular system and standardization of joints, are also used. An interesting question is what designers of permanent buildings and building processes can learn from these techniques. To get insight into the manufacturing of Removable Modular Buildings this system has been described. The problems related to the production of permanent buildings are mentioned too. The answer to the question: "What can we learn about mechanization and automation by the production of Removable Modular Buildings for the construction of permanent buildings?", is: - Reducing the construction processes on the site to simple transport and assembly processes allows mechanization and robotization to become less complex. - It is possibly to develop components with standard joints (design by construction). - All information about the product and its production process can be stored in one data-base. 1. INTRODUCTION The Advisory Committee for Technological Policy in the Building Industry (Adviesraad Technologiebeleid Bouwnijverheid ARTB) predicts two strategies for the coming years in its publication Building Outlook for 2010 (Bouwvisie 2010): - Optional standardization: to standardize industrially manufactured, not project-depend vent, components to make individual buildings. - Flexible production organization: to manufacture standardized components with a series of one piece [1]. -1019- 13th ISARC The manufacturing of Removable Modular Buildings in the Netherlands already involved these strategies. -
The Domestic System Vs. the Factory System by Sarah Collinge
The Domestic System vs. the Factory System By Sarah Collinge The Domestic System Before the 1700s, people manufactured products in their own homes. These people were considered artisans. They made products by hand, often taking a long time to make each object. While this work was slow, the finished products were of high quality. During the time of the domestic system, it took a great deal of time to produce fabric that could be made into clothing. First, wool was sheared from the sheep and cleaned. It was then spun by spinners and made into yarn. Finally, a skilled weaver wove the yarn using a handloom. It took a significant amount of time and skill to make a single piece of fabric. With the population growing, the need for a large production of goods, especially textiles, was needed. The domestic system was no longer able to provide enough goods to meet the demand. The Factory System In the late 1700s, machines were invented that allowed textiles to be made faster and in larger quan- tities. These new machines replaced hand weavers. The new machines were too large to be housed in one’s home. They also required a power source to make them run. Factories, or mills, were built along rivers, which supplied power. Workers now had to leave their homes each day and travel to a factory to work. Some workers lived too far away from a factory to trav- el back and forth each day. They stayed in tenements or apartments in order to be close to their work.