System Design and Controller Interface of Spacecraft Reaction Wheels
Total Page:16
File Type:pdf, Size:1020Kb
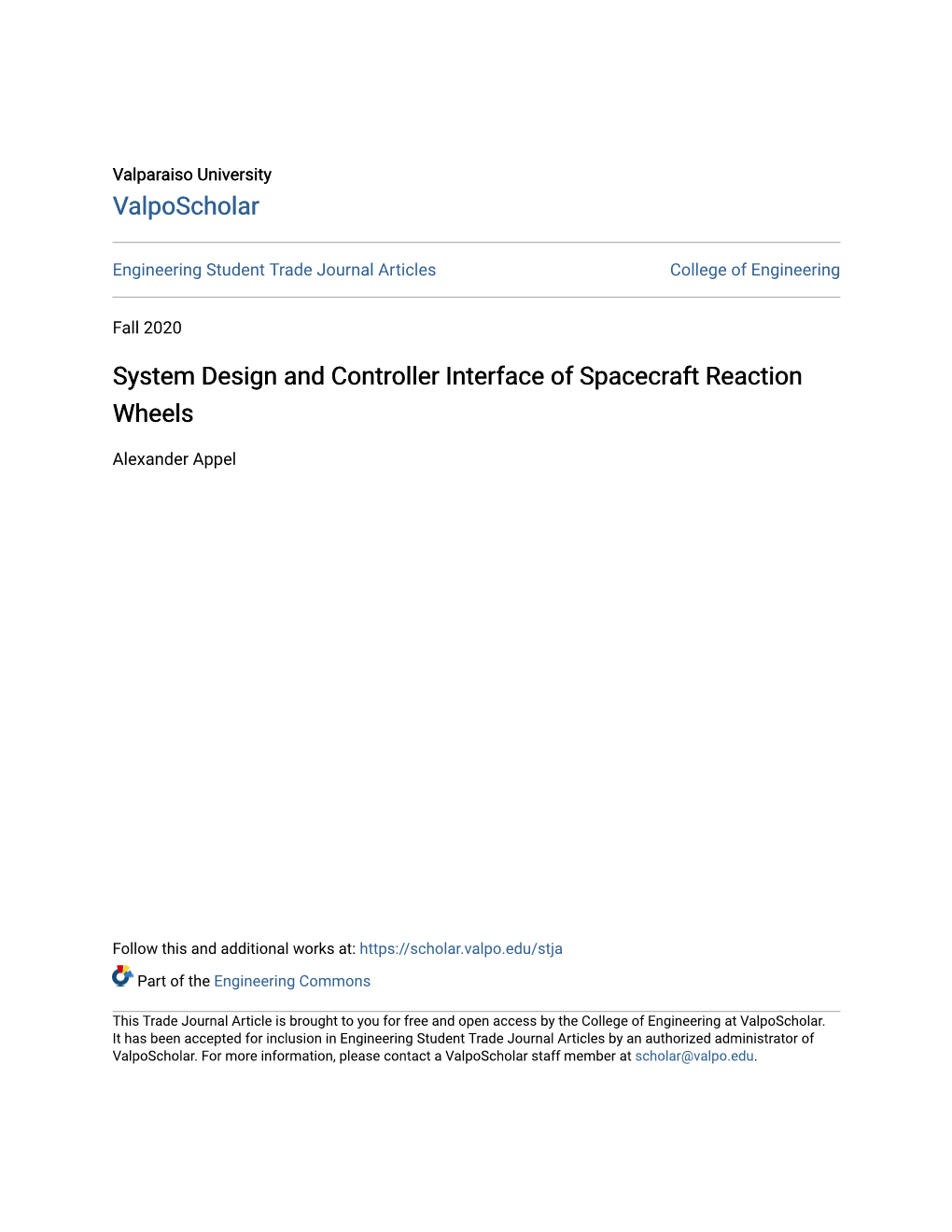
Load more
Recommended publications
-
Some Basic Response Felations for Reaction
SOME BASIC RESPONSE FELATIONS FOR REACTION-WHEEL ATTITUDE CONTROL Robert H. Cannon, Jr. Stanford University SOME BASIC FESPONSE RELATIONS * FOR FEACTION-WHEEL ATTITUDE CONTROL ** Robert H. Cannon, Jr. In many space vehicles, attitude control is best accomplished with combination systems using reaction wheels for momentum exchange and storage, plus jets for periodic momentum expulsion. Design of the reaction-wheel control involves evaluating the time history of system response to disturbances, many of which are either sinusoidal or impul- sive As an aid to such evaluation, this paper developes basic response relations--vehicle attitude, control torque, wheel motion, mechanical power, and energy consumption--for a vehicle subjected to both types of disturbance. Limiting values are calculated, assuming no standby losses. (The possibility of exchanging momentum with minimum energy loss is dis- cussed. ) The resulting normalized numerical relations are intended to li serve as an order-of magnitude basis for preliminary design estimates (r ‘.* and comparisons. c The response relations are derived first for a single-axis model. 2. Then their applicability to three-axis design is discussed. A control system is postulated which decouples vehicle dynamics so that vehicle motions are exactly single axis. (Some advantages of such control are discussed in References (2) and (3).) T’le resulting control-wheel motions may be complicated by gyroscopic coupling due to the spinning wheels. In control to a rotating reference extra power is consumed also because the spin momentum of the roll and yaw wheels must be passed back and forth from one to the other., Control systems which merely damp the natural motions of stable, local-vertical satellites can be smaller and simpler and use less power but, of course, furnish less precise control. -
Managing Momentum on the Dawn Low Thrust Mission. Brett A
Managing Momentum on the Dawn Low Thrust Mission. Brett A. Smith, Charles A. Vanelli, and Edward R. Swenka Jet Propulsion Laboratory, California Institute of Technology, Pasadena, CA 91109 [email protected], [email protected], [email protected] Abstract—Dawn is low-thrust interplanetary spacecraft en- 1. INTRODUCTION route to the asteroids Vesta and Ceres in an effort to better un- Dawn is NASA’s ninth Discovery class mission on a journey derstand the early creation of the solar system. After launch to orbit two asteroids in the region between Mars and Jupiter. in September 2007, the spacecraft will flyby Mars in February Scientists believe the asteroid belt provides similar conditions 2009 before arriving at Vesta in summer of 2011 and Ceres in as those found during the formation of Earth. Dawn will in- early 2015. Three solar electric ion-propulsion engines are vestigate Vesta and Ceres, which are two of the larger objects used to provide the primary thrust for the Dawn spacecraft. in the region, and each provides a unique view into the forma- Ion engines produce a very small but very efficient force, and tion of planet like objects. The Dawn mission is also unique therefore must be thrusting almost continuously to realize the as it will be the first spacecraft to orbit two extraterrestrial necessary change in velocity to reach Vesta and Ceres. planetary bodies [1]. Momentum must be carefully managed to ensure the space- Launching on September 27, 2007, the Dawn spacecraft be- craft has enough control authority to perform necessary turns gan its 8-year journey. -
Characterization of Cubesat Reaction Wheel
Shields, J. et al. (2017): JoSS, Vol. 6, No. 1, pp. 565–580 (Peer-reviewed article available at www.jossonline.com) www.DeepakPublishing.com www. JoSSonline.com Characterization of CubeSat Reaction Wheel Assemblies Joel Shields, Christopher Pong, Kevin Lo, Laura Jones, Swati Mohan, Chava Marom, Ian McKinley, William Wilson and Luis Andrade Jet Propulsion Laboratory, California Institute of Technology Pasadena, California Abstract This paper characterizes three different CubeSat reaction wheel assemblies, using measurements from a six- axis Kistler dynamometer. Two reaction wheels from Blue Canyon Technologies (BCT) with momentum capac- ities of 15 and 100 milli-N-m-s, and one wheel from Sinclair Interplanetary with 30 milli-N-m-s were tested. Each wheel was tested throughout its specified wheel speed range, in 50 RPM increments. Amplitude spectrums out to 500 Hz were obtained for each wheel speed. From this data, the static and dynamic imbalances were calculated, as well as the harmonic coefficients and harmonic amplitudes. This data also revealed the various structural cage modes of each wheel and the interaction of the harmonics with these modes, which is important for disturbance modeling. Empirical time domain models of the exported force and torque for each wheel were constructed from water- fall plots. These models can be used as part of pointing simulations to predict CubeSat pointing jitter, which is currently of keen interest to the small satellite community. Analysis of the ASTERIA mission shows that the reaction wheels produce a jitter of approximately 0.1 arcsec RMS about the payload tip/tilt axes. Under the worst- case conditions of three wheels hitting a lightly damped structural resonance, the jitter can be as large as 8 arcsec RMS about the payload roll axis, which is of less importance than the other two axes. -
Development and Validation of Empirical and Analytical Reaction Wheel Disturbance Models by Rebecca A
Development and Validation of Empirical and Analytical Reaction Wheel Disturbance Models by Rebecca A. Masterson S.B. Mechanical Engineering (1997) Massachusetts Institute of Technology Submitted to the Department of Mechanical Engineering in partial fulfillment of the requirements for the degree of Master of Science in Mechanical Engineering at the MASSACHUSETTS INSTITUTE OF TECHNOLOGY June 1999 @ Massachusetts Institute of Technology 1999. All rights reserved. A uthor .. .. .............................. A r Department of Mechanical Engineering May 24, 1999 C ertified by ......... ................................... David W. Miller Associate Professor Thesis Supervisor C ertified by ................................ Warren P. Seering Professor/Director Departmental Reader A ccepted by .............. .. .................. Am A. Sonin Chairman, Department Committee on Graduate Students pg 999 ENG LIBRARIES 2 Development and Validation of Empirical and Analytical Reaction Wheel Disturbance Models by Rebecca A. Masterson Submitted to the Department of Mechanical Engineering on May 24, 1999, in partial fulfillment of the requirements for the degree of Master of Science in Mechanical Engineering Abstract Accurate disturbance models are necessary to predict the effects of vibrations on the perfor- mance of precision space-based telescopes, such as the Space Interferometry Mission (SIM) and the Next-Generation Space Telescope (NGST). There are many possible disturbance sources on such a spacecraft, but the reaction wheel assembly (RWA) is anticipated to be the largest. This thesis presents three types of reaction wheel disturbance models. The first is a steady-state empirical model that was originally created based on RWA vibration data from the Hubble Space Telescope (HST) wheels. The model assumes that the disturbances consist of discrete harmonics of the wheel speed with amplitudes proportional to the wheel speed squared. -
Mars Reconnaissance Orbiter's High Resolution Imaging Science
JOURNAL OF GEOPHYSICAL RESEARCH, VOL. 112, E05S02, doi:10.1029/2005JE002605, 2007 Click Here for Full Article Mars Reconnaissance Orbiter’s High Resolution Imaging Science Experiment (HiRISE) Alfred S. McEwen,1 Eric M. Eliason,1 James W. Bergstrom,2 Nathan T. Bridges,3 Candice J. Hansen,3 W. Alan Delamere,4 John A. Grant,5 Virginia C. Gulick,6 Kenneth E. Herkenhoff,7 Laszlo Keszthelyi,7 Randolph L. Kirk,7 Michael T. Mellon,8 Steven W. Squyres,9 Nicolas Thomas,10 and Catherine M. Weitz,11 Received 9 October 2005; revised 22 May 2006; accepted 5 June 2006; published 17 May 2007. [1] The HiRISE camera features a 0.5 m diameter primary mirror, 12 m effective focal length, and a focal plane system that can acquire images containing up to 28 Gb (gigabits) of data in as little as 6 seconds. HiRISE will provide detailed images (0.25 to 1.3 m/pixel) covering 1% of the Martian surface during the 2-year Primary Science Phase (PSP) beginning November 2006. Most images will include color data covering 20% of the potential field of view. A top priority is to acquire 1000 stereo pairs and apply precision geometric corrections to enable topographic measurements to better than 25 cm vertical precision. We expect to return more than 12 Tb of HiRISE data during the 2-year PSP, and use pixel binning, conversion from 14 to 8 bit values, and a lossless compression system to increase coverage. HiRISE images are acquired via 14 CCD detectors, each with 2 output channels, and with multiple choices for pixel binning and number of Time Delay and Integration lines. -
Enabling Reaction Wheel Technology for High-Performance Nanosatellite
SSC07-X-3 ENABLING REACTION WHEEL TECHNOLOGY FOR HIGH PERFORMANCE NANOSATELLITE ATTITUDE CONTROL Doug Sinclair Sinclair Interplanetary 268 Claremont Street, Toronto, Ontario, Canada, M6J 2N3 Tel: 647-286-3761; Fax: 775-860-5428; Web: www.sinclairinterplanetary.com [email protected] C. Cordell Grant, Robert E. Zee Space Flight Laboratory University of Toronto Institute for Aerospace Studies 4925 Dufferin Street, Toronto, Ontario, Canada, M3H 5T6 Tel: 416-667-7700; Fax: 416-667-7799; Web: www.utias-sfl.net [email protected], [email protected] ABSTRACT To date nanosatellites have primarily relied on magnetic stabilization which is sufficient to meet thermal and communications needs but is not suited for most payloads. The ability to put one, or even three, reaction wheels on a spacecraft in the 2-20 kg range enables new classes of mission. With reaction wheels and an appropriate sensor suite a nanosatellite can point in arbitrary directions with accuracies on the order of a degree. Sinclair Interplanetary, in collaboration with the University of Toronto Space Flight Laboratory (SFL), has developed a reaction wheel suitable for very small spacecraft. It fits within a 5 x 5 x 4 cm box, weighs 185 g, and consumes only 100 mW of power at nominal speed. No pressurized enclosure is required, and the motor is custom made in one piece with the flywheel. The wheel is in mass production with sixteen flight units delivered, destined for the CanX series of nanosatellites. The first launch is expected in 2007. Future missions that will make use of these wheels include CanX-3 (BRITE), which will make astronomical observations that cannot be duplicated by any existing terrestrial facility, and CanX-4 and -5, which will demonstrate autonomous precision formation flying. -
Solar Sail Attitude Control System for the NASA Near Earth Asteroid Scout Mission
Solar Sail Attitude Control System for the NASA Near Earth Asteroid Scout Mission Juan Orphee Ben Diedrich Brandon Stiltner Chris Becker Andy Heaton 1/19/2017 1 Introduction • Near Earth Asteroid (NEA) Scout mission uses an 86 m^2 sail for primary propulsion • The sail produces a significant solar disturbance torque • NEA Scout is a class D NASA payload in the form of a 6U cubesat • Limited volume and mass creates challenges • NEA Scout uses reaction wheels for primary attitude control • NEA Scout uses an Adjustable Mass Translator (AMT) to manage pitch and yaw momentum • NEA Scout uses a cold gas Reaction Control System (RCS) for initial de-tumble, a Trajectory Control Maneuver (TCM), roll momentum management, and safe mode • NEA Scout control software ensures all systems work smoothly together for successful mission 2 NEA Scout Spacecraft Configuration Spacecraft body axes and relative scale of sail to spacecraft 1 – BCT Star Tracker/Drive Control Electronics 1 2 2 2 – BCT Coarse Sun Sensors x 3 3 – BCT 15 milli-Nm Reaction Wheel x 4 4 3 6 4 – Sensonor MEMS IMU 5 5 – VACCO cold gas Reaction Control System (RCS) 6 – NASA in house Adjustable Mass Translator (AMT) 2 3 NEA Scout Control System Reaction wheel feedback control loop Reaction wheels are primary attitude controller Bode diagram for roll control System bandwidth is 0.067 Hz Stability margin 16 dB/67 deg 4 NEA Scout ACS Performance Meets attitude pointing requirements Meets science pointing requirement that is challenging for small sat 5 NEA Scout RCS Design VACCO cold gas RCS -
High-Performance Reaction Wheel
High-Performance Reaction Wheel Optimization for Fine-Pointing Space Platforms: Minimizing Induced Vibration Effects on Jitter Performance plus Lessons Learned from Hubble Space Telescope for Current and Future Spacecraft Applications Martin D. Hasha* Abstract The Hubble Space Telescope (HST) applies large-diameter optics (2.5-m primary mirror) for diffraction- limited resolution spanning an extended wavelength range (~100-2500 nm). Its Pointing Control System (PCS) Reaction Wheel Assemblies (RWAs), in the Support Systems Module (SSM), acquired an unprecedented set of high-sensitivity Induced Vibration (IV) data for 5 flight-certified RWAs: dwelling at set rotation rates. Focused on 4 key ratios, force and moment harmonic values (in 3 local principal directions) are extracted in the RWA operating range (0-3000 RPM). The IV test data, obtained under ambient lab conditions, are investigated in detail, evaluated, compiled, and curve-fitted; variational trends, core causes, and unforeseen anomalies are addressed. In aggregate, these values constitute a statistically-valid basis to quantify ground test-to-test variations and facilitate extrapolations to on-orbit conditions. Accumulated knowledge of bearing-rotor vibrational sources, corresponding harmonic contributions, and salient elements of IV key variability factors are discussed. An evolved methodology is presented for absolute assessments and relative comparisons of macro-level IV signal magnitude due to micro-level construction-assembly geometric details/imperfections stemming from both electrical drive and primary bearing design parameters. Based upon studies of same-size/similar-design momentum wheels’ IV changes, upper estimates due to transitions from ground tests to orbital conditions are derived. Recommended HST RWA choices are discussed relative to system optimization/tradeoffs of Line-Of-Sight (LOS) vector-pointing focal- plane error driven by higher IV transmissibilities through low-damped structural dynamics that stimulate optical elements. -
A Demiseable Reaction Wheel Assembly
National Aeronautics and Space Administration www.nasa.gov a e r o s p a c e opportunity A Demiseable Reaction Wheel Assembly ...lowering the cost, complexity, and risk of uncontrolled re-entry for LEO missions Benefits • Simplified space missions: Removes the need for special echnology propulsion systems, extra fuel, t and additional mission planning required of controlled re-entry • Modular design: Offers reduced complexity, providing for reduced manufacturing costs and simpler assembly and balancing as compared with traditional designs • Scalable: Momentum storage from 10 to 80 Nms and torque up to 0.5 Nm allow the RWA to be tailored to specific applica- tions on all sizes of spacecraft • Innovative: Combines materials that melt at relatively low temperatures with an archi- tecture that makes exposure NASA Goddard Space Flight Center invites companies to to heat very efficient, enabling license its new, patent-pending reaction wheel assembly (RWA) that is complete demise designed to melt or burn up (demise) upon re-entry to Earth’s atmos- • Low risk: Helps to lower phere, making it ideal for low Earth orbit (LEO) missions. The simple, the risk of re-entry for LEO modular design also makes it a good option for small and large missions by making uncon- trolled, demiseable re-entry spacecraft in other orbits. possible Goddard’s RWA assembly helps make uncontrolled re-entry to Earth’s atmosphere possible. Because controlled re-entry (in which the spacecraft is disposed of into the ocean) can be more costly, complex, and risky, uncontrolled re-entry is an attractive option. It also greatly reduces debris (the remains of the spacecraft itself) left in orbit or deposited into the ocean. -
Fuel-Free Attitude Control of Bias-Momentum Solar Sail
Fuel-free Attitude Control of Bias-momentum Solar Sail By Yuya MIMASU1), Go ONO1), Yuichi TSUDA1) 1)The Institute of Space and Astronautical Science, JAXA, Sagamihara, Japan (Received 1st Dec, 2016) Solar sail is the fuel-free thrust system. Its trajectory can be changed without fuel by using the solar radiation pressure (SRP) induced by the sail. In general, however, the direction and the magnitude of the photon acceleration are controlled by the attitude of the sail, and the attitude control fuel is required. That is why, it is necessarily to reduce the fuel consumption of the attitude control in order to realize a real fuel-free solar sail. This research is one solution for this issue. The SRP is affected not only to the orbit, but also to the attitude of the spacecraft. This effect can be utilized to control the attitude of spacecraft. There is an appropriate example on Hayabusa2 case during coasting phase. The attitude dynamics model of the Hayabusa2 under the SRP had been studied. Especially, the attitude motion in the one-wheel bias-momentum control mode has been modeled in detail, and calibrated by using the actual flight data of Hayabusa2. The one-wheel bias-momentum control mode is the control mode in which the spacecraft is controlled by using only Z-axis reaction wheel. In this mode, the angular momentum vector precesses due to the SRP. According to the established model and flight result of Hayabusa2, the precession trajectory is changed by the body-phase angle with respect to the Sun direction. By utilizing this feature, the direction of angular momentum vector can be controlled by changing phase angle with respect to the Sun angle. -
Rocket Lab Expands Space Systems Footprint with New High Volume Reaction Wheel Production Facility
Rocket Lab Expands Space Systems Footprint with New High Volume Reaction Wheel Production Facility The new production facility comes as Rocket Lab secures contracts to supply major satellite constellations with reaction wheels Long Beach, California. September 1, 2021 – Rocket Lab USA, Inc. (Nasdaq: RKLB) (“Rocket Lab” or the “Company”), global leader in launch and space systems, today announced that construction is underway on a new production facility capable of supplying up to 2,000 reaction wheels per year to fulfil growing demand from satellite constellation customers. The new production facility, which joins Rocket Lab’s existing 380,000 sq/ft manufacturing footprint, comes as Rocket Lab signs deals to supply reaction wheels for a number of undisclosed satellite constellations. The production line incorporates advanced metal machining centers optimized for unattended operation, automated production tools, and automated environmental testing workstations. More than 16 new roles are expected to support the new production facility and the growing Space Systems operations at Rocket Lab by the end of the year. The new production facility is the latest expansion of Rocket Lab’s Space Systems business, which was strengthened in 2020 by the acquisition of Toronto-based Sinclair Interplanetary, a leading provider of high-quality, flight-proven satellite hardware including reaction wheels and star trackers. Sinclair Interplanetary pioneered high-reliability reaction wheels for small satellites and there are close to 200 wheels currently operating on orbit. Rocket Lab founder and Chief Executive Officer, Peter Beck, said the new production facility leverages Sinclair Interplanetary’s heritage and marries it with Rocket Lab’s extensive experience with high-rate manufacture of aerospace components for the Electron launch vehicle to make what the Company considers best-in-class satellite hardware available to customers at scale. -
The Deployment and Control of a Spinning Solar Sail Cubesat
Spinning Solar Sail: The Deployment and Control of a Spinning Solar Sail Satellite by Hendrik Willem Jordaan Dissertation presented for the degree Doctor of Philosophy in Faculty of Engineering at Stellenbosch University Promoter: Prof W.H. Steyn Department Electrical and Electronic Engineering March 2016 Stellenbosch University https://scholar.sun.ac.za Declaration By submitting this thesis electronically, I declare that the entirety of the work contained therein is my own, original work, that I am the sole author thereof (save to the extent explicitly otherwise stated), that reproduction and publication thereof by Stellenbosch University will not infringe any third party rights and that I have not previously in its entirety or in part submitted it for obtaining any qualification. March 2016 Date: ..................................................... Copyright © 2016 Stellenbosch University All rights reserved. ii Stellenbosch University https://scholar.sun.ac.za Abstract Solar sailing has become a viable and practical option for current satellite missions. A spinning solar sail has a number advantages above a 3-axis stabilised sail. A spinning sail is more resistant to disturbance torques and the misalignment of the centre of mass and centre of pressure. The spinning sail generates a constant centrifugal force, which reduces sail billowing and makes it possible to use wire booms. The new tri-spin solar sail and tri-spin Gyro satellite configurations are proposed that combines the advantages of the spinning and 3-axis stabilised sail designs. This study focuses on the deployment control of the sail and the orientation control of the satellite. Different deployment methods of a rotating structure are studied. The active deployment method makes use of a separate module with an actuator on the rotating system to deploy the structure.