Experiences with a Vacuum Type Air-Driven Centrifuge for Use in Short Nuclear Life Time Measurements
Total Page:16
File Type:pdf, Size:1020Kb
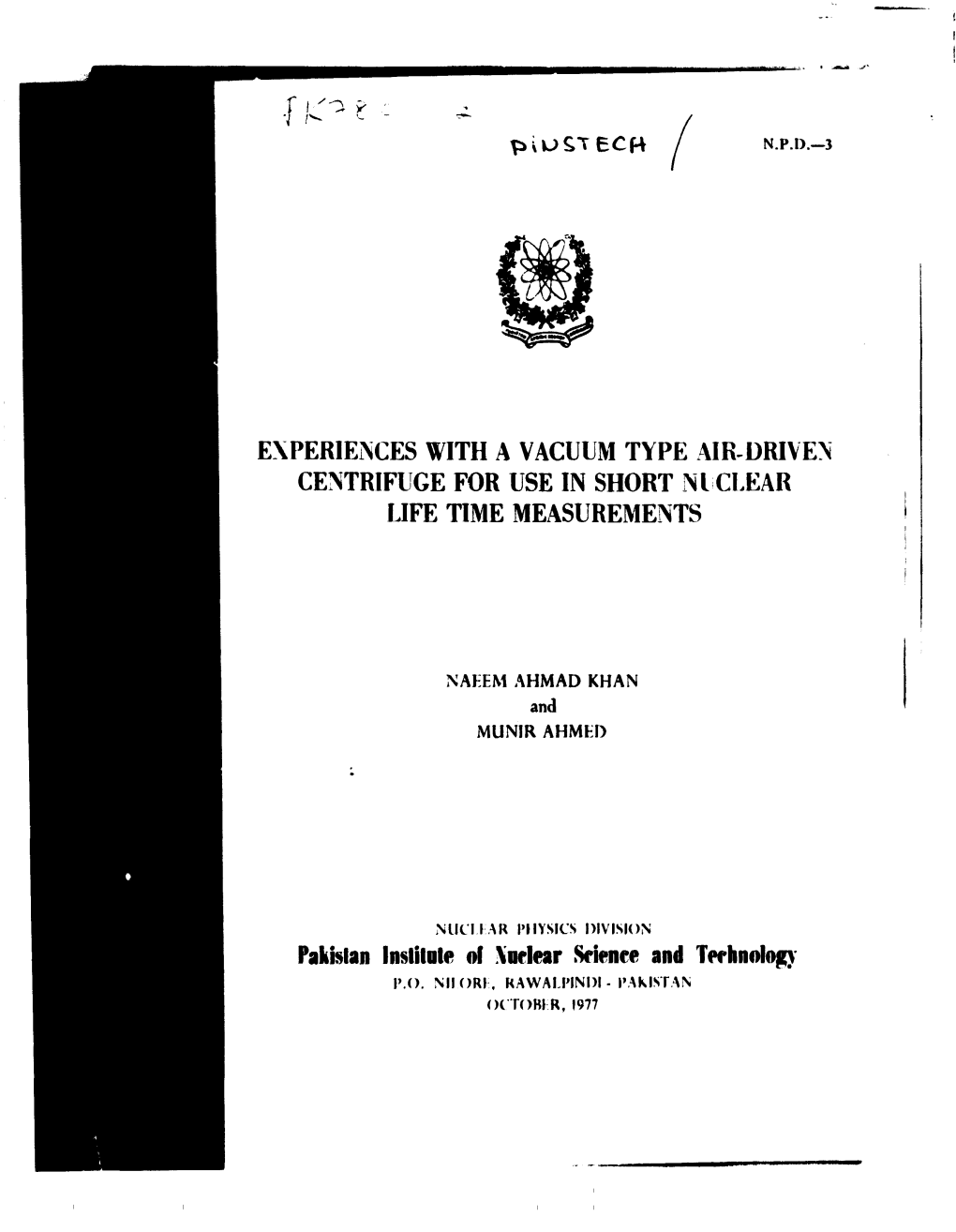
Load more
Recommended publications
-
Information Technology in Libraries. a Pakistani Perspective. ISBN ISBN-969-8133-21-6 PUB DATE 1998-00-00 NOTE 255P.; Introduction by Aris Khurshid
DOCUMENT RESUME ED 425 749 IR 057 248 AUTHOR Mahmood, Khalid TITLE Information Technology in Libraries. A Pakistani Perspective. ISBN ISBN-969-8133-21-6 PUB DATE 1998-00-00 NOTE 255p.; Introduction by Aris Khurshid. AVAILABLE FROM Pak Book Corporation, 2825 Wilcrest, Suite 255, Houston, TX 77042; e-mail: [email protected] (Rs. 395). PUB TYPE Books (010)-- Information Analyses (070)-- Reports Descriptive (141) EDRS PRICE MF01/PC11 Plus Postage. DESCRIPTORS Cataloging; *Computer Software; Developing Nations; Foreign Countries; Higher Education; *Information Technology; Integrated Library Systems; Librarians; *Libraries: *Library Automation; *Library DeveloiInent; Library Education; Library Services; Literature Reviews; Online Catalogs; Professional Continuing Education IDENTIFIERS *Library Computer Systems; Library Security; *Pakistan ABSTRACT This book presents an overview of the present status of the use of library automation hardware and software in Pakistan. The following 20 articles are included: (1) "The Status of Library Automation in Pakistan"; (2) "Promoting Information Technology in Pakistan: the Netherlands Library Development Project"; (3) "Library Software in Pakistan"; (4) "The Best Library Software for Developing Countries: More than 30 Plus Points of Micro CDS/ISIS [Computerized Documentation System/Integrated Set of Information Systems]"; (5) "Micro CDS/ISIS: What's New in Version 3.0"; (6) "Use of Micro CDS/ISIS in Pakistan: A Survey"; (7) "Do You Need a Lamp To Enlighten Your Library: An Introduction to Library Automation -
Received Applications (Lecturer)
RECEIVED APPLICATIONS (LECTURER) Depositing Slip / Challan Date of Depositing SR.# Name of the applicant Discipline / Bank Name Slip / Challan / Amount B D # B D # Mr. Rafaqat Ali HBL, Model Town Br. 1 Medicine 2193886 13-07-2018 3000 S/o: Liaqat Ali Khanpur Dist. R.Y. Khan Mr. Hafeez-ur-Rehman Ali Khera HBL, Nishtar Medical 2 Medicine 309350 17-07-2018 3000 S/o: Ch. Atta-ur-Rehman College, Multan Mr. Tawaf Ali Shah 3 Microbiology 41529606 HBL, Gufishan Colony, 09-07-2018 3000 S/o: Noor Ali Shah Mr. Fayyaz Yasin 4 Microbiology 8110208 HBL, Cavalry Ground, LHR 16-07-2018 3000 S/o: Muhammad Yasin Ms. Nousheen Arshad HBL, Main Bazar Toba Tak 5 Poultry Sciences 40025445 13-07-2018 3000 D/o: Muhammad Arshad Singh Mr. Muhammad Shakeel Ashraf 6 Animal Nutrition 6817397 HBL, Kot Rahda Kishan 12-07-2018 3000 S/o: Muhammad Ashraf Mr. Muhammad Arif Rizwan 7 Veterinary Science 4248097 HBL, Main Br. D.G. Khan 18-07-2018 3000 S/o: Malik Jammat Ali Ms. Sidra Maryam در ا دو Anatomy & Histology 36295660 HBL, Karor Lal Easan, Layyah 18-07-2018 3000 8 D/o: Abdul Basit Mr. Muhammad Arif Rizwan 9 Medicine 4248094 HBL, Main Br. D.G. Khan 18-07-2018 3000 S/o: Malik Jammat Ali Ms. Laiba Shafique HBL, Kutchery Chowk Br. 10 Zoology 40899908 16-07-2018 3000 D/o: Muhammad Shafique Wazirabad Mr. Shahzada Muhammad Zeeshan 11 Hayder Animal Nutrition 74102 HBL, Ahmadpur Sial 17-07-2018 3000 S/o: Ubaid Ullah Mr. Abid Ahmad 12 Animal Nutrition 8529676 HBL, Sher garh Br. -
An Exploratory Study
OCTOBER 2016 Physical Disengagement and Ideological Reorientation Among Militants in Kashmir: An Exploratory Study NIKHIL RAYMOND PURI Physical Disengagement and Ideological Reorientation Among Militants in Kashmir: An Exploratory Study NIKHIL RAYMOND PURI ABOUT THE AUTHOR Nikhil Raymond Puri is a Visiting Fellow at Observer Research Foundation, New Delhi. An independent researcher and risk analyst, Nikhil's research interests include religious education and state-led madrasa reform efforts, and militant radicalisation and disengagement in South Asia. He has conducted extensive fieldwork across India and Bangladesh. He consults in the area of operational and political risk management, and publishes widely on security-related developments in South Asia. He holds a BA in South Asian Studies from the University of Virginia and obtained his MPhil and PhD degrees in Politics from the University of Oxford. © 2016 Observer Research Foundation. All rights reserved. No part of this publication may be reproduced or transmitted in any form or by any means without permission in writing from ORF. Physical Disengagement and Ideological Reorientation Among Militants in Kashmir: An Exploratory Study ABSTRACT This qualitative study employs semi-structured interviews to explore the phenomenon of militant disengagement as experienced by six former militants in Jammu and Kashmir. The paper seeks to understand how and why individuals who enthusiastically joined the militant campaign against the Indian state beginning in the late 1980s subsequently moved away – physically – from armed violence. The study also aims to shed light on the nature and extent of ideological evolution experienced by the same individuals before and/or after their physical departures from militancy. The paper attends closely to the interplay between these physical and ideological aspects of disengagement, asking – in the case of each interviewee – how one relates to the other. -
Autumn News Letter2013-Xv.Cdr
ISSUE: AUTUMN 2013 VOL - XV INSIDE THIS ISSUE *QUARTERLY PERFORMANCE *NEW DEVELOPMENTS *RAMZAN ACTIVITIES *RI ANNUAL GENERAL MEETING *UN HIGH LEVEL MEETING ON DISABILITY & DEVELOPMENT *VISITORS & THEIR VIEWS *FUTURE EVENTS *MAJOR DONORS THE PAKISTAN SOCIETY FOR THE REHABILITATION OF THE DISABLED REGD. 1957 111 Ferozepur Road, Lahore, Pakistan Tel: 0092 42 - 37578253 , 37582860 Fax: 0092 - 42 - 37574936 Email: [email protected] Web: www.psrd.org.pk www.facebook.com/psrd.org.pk |PSRD SUFFERS ANOTHER LOSS| Occupational Therapy and Speech Therapy Unit Chairperson, Orthotics & 288 patients attended by Occupational Therapist 837 treatment sessions given. Prosthetics Centre, Brig. Abdul 115 patients attended by Speech Therapist. Qayyum Sher (Retd), passed 285 treatment sessions given. away on Sunday, 25th August, 2013. He was 94. Upright and Skill Development Unit principled, he had served PSRD 18 trainees trained in various Arts & Craft unit. for over 29 years with great dedi- Rs. 340,035/- income generated from Arts & Craft Section. cation, sincerity and enthusiasm. His services, 17 trainees trained in Tailoring Section. Rs. 570,050/- income generated from Tailoring Section. particularly in the Orthotics & Prosthetics Centre, were 64 students trained in Computer Training Courses. outstanding, and resulted in making it a professional 15 students completed Cell Phone Repairing Course. set up which not only provides services at PSRD but also in areas outside Lahore. He was so devoted to the Orthotic and Prosthetic Unit cause of people with disabilities that, despite his frailty, 936 patients attended. he worked steadfastly to the end. His absence will be 1166 appliances manufactured. deeply felt. 905 appliances delivered A brave and courageous soldier, he served in the army with distinction and will be remembered for his heroics Vocational Rehabilitation Centre in the recapture of the Wagah position occupied by the 7 disabled persons given loan of RS. -
Vol 18 Issue 03
JAIMC PATRON Prof. Arif Tajammul The Journal of Allama Iqbal Medical College Principal Allama Iqbal Medical College/ July - September 2020, Volume 18, Issue 03 Jinnah Hospital Editorial i CHIEF EDITOR Coronaconomy – Health Verses Economy In The Time Of Corona iii Dr. Rubina Aslam Muhamamd Imran Head of Department of Psychiatry Original Articles i ASSOCIATE EDITORS Sub-Conjunctival Versus Intracameral Dexamethasone Injection Afteri 334 Sana Iftikhar Phacoemmulsifiction, A Comparative Study About Immediate Mehwish Akhtar Anterior Uveitis Sabeen Irshad Fiza Azhar, Shamshad Ali, Saqib Siddiq, Muhammad Moeen Bhatti, Ather Touseef, M. Abrar Ahmad, Khalid Waheed MANAGING EDITOR Muhammad Imran Leading Causes of Morbidities in Children under Five Years Age: 339 Knowledge and Practices Regarding Risk Factors in CMH Lahore STATISTICAL EDITORS Tahira Raza, M Asharaf Chaudhry, Ahsan Masud, Hira Kalsoom, Maheen Omer, Mamoon Akbar Qureshi Khawaja Rafay Ghazanfar, Inoshia Inam, Hamza Alvi, Jannat Sardar Sheikh Zarabia Pervaiz Butt The Prevalence of Dry Eye Disease Among Professional Computer Users 344 M. Nausherwan Adil, M. Abrar Ahmad, Usama Javaid,M.Rashid Yaseen, Ather PHOTOGRAPHY & GRAPHICS Touseef, Muhammad Moeen Bhatti Syed Ali Hassan Rizvi Knowledge, Attitudes and Practices of Hospital Waste Management amongst 349 the Paramedics of a Teaching Hospital in Lahore DESIGNING & COMPOSING Khawar Abbas Chaudhry, Amina Yousaf, Mujtaba Hasan Siddiqui, Muhammad Talal Publishers Ismaeel Tariq, Surya Fazal Hashmi, Muhammad Azhar Shah I.T MANAGER Awareness and Knowledge of PAP Smear as a Screening Test for Cervical 355 Muhamamd Shujat Ali Cancer Among Women Attending Gynaecological OPD of Services Hospital Madeeha Rashid, Kiren Khurshid Malik, Asma Mushtaq, Rubina Sohail INTERNATIONAL ADVISORY BOARD The Impact of Pterygium Surgical Excision on Corneal Astigmatism 361 Shoaib Khan (Finland) M. -
Historical Variations in the Specialized Subjects of the Elected Fellows of the Pakistan Academy of Sciences
Historical Variations in the Specialized Subjects of the Elected Fellows 251 Proceedings of the Pakistan Academy of Sciences, 48 (4): 251-260 (2011) Pakistan Academy of Sciences Copyright © Pakistan Academy of Sciences ISSN: 0377 - 2969 Review Article Historical Variations in the Specialized Subjects of the Elected Fellows of the Pakistan Academy of Sciences Shafiq Ahmad Khan1 and M.M. Qurashi2 1 4-A, PCSIR, ECHS, Phase-1, Canal Bank Road, Lahore 2 Pakistan Association for History & Philosophy of Sciences, c/o Pakistan Academy of Sciences, Sector G-5/2, Constitution Avenue, Islamabad Abstract: The Pakistan Academy of Sciences (PAS) was inaugurated on 16th February 1953 by the then Prime Minister of Pakistan, Khawaja Nazim-ud-Din. The Academy is a non-governmental and non-political supreme body of distinguished scientists, to which the Government has entrusted the consultative and advisory status. The affairs of the Academy are regulated by its Charter and the Bye- Laws approved by its Fellows who are elected through the prescribed procedure. Since its establishment, the Academy has elected 162 scientists belonging to all branches of science as its Fellows during a period of 58 years (i.e., 1953-2010) at an average of 2.8 Fellows per year. However, no Fellows were elected for 10 years (i.e., 1955, 1960, 1962, 1963, 1965, 1969, 1975, 1981, 1985 and 1987) and, therefore, the average induction-rate works out to be about 3.5 Fellows per year during a period of 48 years. A comparison of the number of Fellows elected per decade during 50 years (i.e.,1961-2010) in physical and bio-sciences is provided and depicted graphically, showing the variation trend regarding the specialized fields of the elected Fellows for the studied five decades. -
Hippocratic Journal of Unani Medicine
HIPPOCRATIC JOURNAL OF UNANI MEDICINE Volume 8, Number 4, October – December 2013 Hippocratic J. Unani Med. 8(4): 1–182, 2013 CENTRAL COUNCIL FOR RESEARCH IN UNANI MEDICINE Department of Ayurveda, Yoga & Naturopathy, Unani, Siddha and Homoeopathy (AYUSH) Ministry of Health & Family Welfare, Government of India Hippocratic Journal of Unani Medicine Chief Patron Minister for Health & Family Welfare, Government of India Patron Secretary, Department of AYUSH Ministry of Health & Family Welfare, Government of India International Advisory Board Prof. Ranjit Roy Chaudhary, New Delhi, INDIA Hakim Syed Khaleefathullah, Chennai, INDIA Hakim Saifuddin Ahmad, Meerut, INDIA Dr. Suraiya H. Hussein, Kuala Lumpur, MALAYSIA Dr. Fabrezio Speziale, Rome, ITALY Prof. Sami K. Hamarneh, Washington D.C. USA Dr. M. Abdullah, Lund. SWEDEN Dr. Saleem Khan, London, ENGLAND Mrs. Sadia Rashid, Karachi, PAKISTAN Dr. Marteen Bode, Amsterdam, THE NETHERLANDS Prof. S.G. Marketos, Cos, GREECE Mr. Rafiqul Islam, Dhaka, BANGLADESH Prof. Ikhlas A. Khan, USA Prof. R.D. Kulkarni, Mumbai, INDIA Dr. V.K. Gupta, New Delhi, INDIA Dr. G.N. Qazi, New Delhi, INDIA Dr. Rashid Bhikha, Industria, SOUTH AFRICA Prof. Khan Usmanghani, Karachi, PAKISTAN Editorial Board Unani Medicine: Botany: Prof. Hakim Jameel Ahmad, New Delhi, INDIA Prof. Wazahat Husain, Aligarh, INDIA Prof. A. Hannan, Karachi, PAKISTAN Dr. Rajeev Kr. Sharma, Ghaziabad, INDIA Prof. Anis A. Ansari, Aligarh, INDIA Chemistry: Modern Medicine: Dr. Sajid Husain, Hyderabad, INDIA Prof. C.M. Habibullah, Hyderabad, INDIA Pharmacology: Prof. Badri N. Saxena, New Delhi, INDIA Prof. K.M.Y. Amin, Aligarh Prof. V.H. Talib, Dehradun, INDIA Prof. A. Ray, New Delhi, INDIA Dr. (Mrs.) Rajbala Yadav, New Delhi, INDIA Prof. -
Vol 19 Issue 02.Pdf
JAIMC PATRON Prof. Arif Tajammul The Journal of Allama Iqbal Medical College Principal Allama Iqbal Medical College/ April - June 2021, Volume 19, Issue 02 Jinnah Hospital Editorial i CHIEF EDITOR Kidney Diseases Rising in Pakistan iii Dr. Rubina Aslam Muhammad Imran Head of Department of Psychiatry Original Articles i ASSOCIATE EDITORS Sana Iftikhar Diagnostic Accuracy of Transrectal Power Doppler Ultrasound in Diagnosing 253 Mehwish Akhtar Prostate Cancers Sabeen Irshad Naeem Ahmad Khan, Tanweer Ahmad, Adnan Ahmad Sattar, Irfan Masood, Arslan Masood Fatima Iqbal, Javed Iqbal, Basma Khan, Aamer Nadeem Chaudhary Frequency of Diabetes Mellitus and Impaired Fasting Glucose in Patients with 260 MANAGING EDITOR Lichen Planus Muhammad Imran Aisha Chaudhry, Lamees Mahmood Malik, Zartaj Liaqat, Ambreen Ashraf, Amna Rasul, Maheen Irfan STATISTICAL EDITORS Mamoon Akbar Qureshi Comparison of Functional Outcome of Unipolar Versus Bipolar Uncemented 264 Zarabia Pervaiz Butt Hemiarthroplasty in Patients with Displaced Intracapsular Femoral Neck Fractures PHOTOGRAPHY & GRAPHICS Aamir Shabab, Muhammad Zubair Farooq, Muhammad Imran, Waqar Ahmed Syed Ali Hassan Rizvi Siddiqui, Fatima Arshad, Zahid Akhtar Role of Vitamin-D Along with Pregabalin for the Treatment of Painful 269 DESIGN & PRINTING Diabetic Neuropathy Talal Publishers Mohsin Masud, Lala Rukh Bangash, Shaheer Nayyar, Faridah Suhail, Muhammad [email protected] Rizwan Ahmed, Anam Fatima Bangash Association of Mean Serum Magnesium Levels in Patients Having Non-Insulin 273 INTERNATIONAL ADVISORY -
The Profile Updated June, 2017
The Profile Updated June, 2017 Omeed Ki Kiran Foundation (A Ray of Hope) Gynae Welfare Hospital & Thalassaemia Center Mardan Head Office: House #73, Street #01, Sector K, Sheikh Maltoon Town, Mardan. Gynae Welfare Hospital & Thalassaemia Center: House No.03, Near Bilal, Masjid Canal Road Bijli Ghar Mardan Phone: +92-937-876329 +92-937-862789 +92-300-5723523 Email: [email protected] [email protected] www.okkf.org Message by Chairman, The Founder,Chairman Omeed Ki Kiran Foundation (A Ray of Hope) Our aim and vision is to bring hope of life among thalasseamia children, and to serve humanity and bring hope of life among deprived people who are in sufferings. To achieve the aim and vision Omeed Ki Kiran Foundation has been established as a welfare hospital & thalasseamia center, which provide free and safe blood transfusion to thalasseamia children without any discrimination. We appeal to all people who belong to different spheres of life to come forward and help us generously for this noble and pious cause and to play best role for spreading happiness among thalasseamia children and render the world Thalassaemia free. Imran A. Khan Founder, Chairman “The enjoyment of the highest attainable standard of health is one of the fundamental rights of every human being” “To serve humanity and bring a hope of life among deprived people who are in sufferings” “To ensure free & standard health services for poor & vulnerable people with kidney failures and deadly disease of Thalassaemia” “May Allah give us the strength to serve the humanity” The Profile Omeed Ki Kiran Foundation (A Ray of Hope) Updated June, 2017 Back Ground of Omeed Ki Kiran Foundation Omeed Ki Kiran Foundation is a social, non-Profitable and non-governmental Organization in the field of Health, established by Mr. -
Years 1953 2013 of Pakistan Academy of Sciences Milestones and Salient Activities
Years 1953 2013 of PAKISTAN ACADEMY OF SCIENCES MILESTONES AND SALIENT ACTIVITIES Dr. Abdul Rashid PAKISTAN ACADEMY OF SCIENCES SIXTY YEARS OF PAKISTAN ACADEMY OF SCIENCES (1953–2013) Milestones and Salient Activities Dr. Abdul Rashid Fellow, Pakistan Academy of Sciences Pakistan Academy of Sciences 2014 Pakistan Academy of Sciences Mission Statement “Promoting Science, Technology and Innovation for Socio-economic Development” ADVISORY COMMITTEE Prof. Dr. M. D. Shami, S.I. Vice President, Pakistan Academy of Sciences Dr. Anwar Nasim, S.I. Secretary General, Pakistan Academy of Sciences Prof. Dr. N. M. Butt, S.I. Treasurer, Pakistan Academy of Sciences © 2014 Pakistan Academy of Sciences ISBN: 978-969-8223-13-7 Composed by: Engr. Adnan Bashir Printer: PanGraphics (Ptv) Ltd., Islamabad 60 YEARS of PAkiStAn AcAdEmY of SciEncES (1953–2013)Years 1953 2013 FOREWORD The Pakistan Academy of Sciences was inaugurated by the Prime minister of Pakistan, khwaja nazimuddin, on 16th february 1953, during 5th Pakistan Science conference at Lahore. The Government of Pakistan has bestowed a consultative and advisory status to the Academy “on all problems relating to the development of scientific efforts in the country”, and “generally on such matters of national and international importance in the field of science as may be referred to the Academy”. The land for the construction of the Academy building was allotted at the Silver Jubilee celebrations in 1978 by General Zia-ul-Haq and a grant of Rs. 7.00 million was also provided for that purpose. The building was constructed when Dr. m.A. kazi was President and Dr. Raziuddin Siddiqi was Secretary. -
W Ebsite: Www .Paspk.Org
ISSN Print : 0377 - 2969 ISSN Online : 2306 - 1448 Vol. 50(4), December 2013 OF THE PAKISTAN ACADEMY OF SCIENCES C O N T E N T S Volume 50, No. 4, December 2013 Page Research Articles Engineering Sciences A Scrum Framework for Requirement Engineering Practices 263 – Asma Batool, Yaser Hafeez, Sohail Asghar, Muhammad, A. Abbas and Muhammad S. Hassan Earth Retention Systems Disasters: Causes and Prevention 271 – Ammad Hassan Khan Novel Photo-Neutron Oriented Dynamic Modeling and Synthesis of Robust Global Power 285 Controllers for CANDU-6 Nuclear Reactor using Modern Optimization Techniques – Arshad H Malik and Feroza Arshad Life Sciences Identification of Neotectonics using DEM-based Local Base-level Approach in Pothowar Plateau 299 – Syed Amer Mahmood, Jahanzeb Qureshi, Sajid Rashid Ahmad, Javed Sami, Amer Masood and Hafiz Muhammad Rafique Medical Sciences Verification of Absorbed Radiation Dose for X-rays through Lagrange's Interpolation Method 309 – Saeed Ahmad Buzdar, Qurat-ul-Ain Shamsi, M. Afzal, Aalia Nazir, Muhammad Altaf Hussain Nizamani and Muhamad Asghar Gadhi Can We Really Treat Thalassemia Major? 315 – Rashid A. Seyal, Siraj M. Tareen and Hayat M. Awan Physical Sciences W Statistical Analysis of Cloud Cover at Pakistan Coastal Regions 327 ebsite: www – Faisal Ahmed Khan Afridi, M. Ayub Khan Yousuf Zai and Khusro Mian 65 67 69 71 Calculation of ng(9/2)+ Isomers in Ni, Zn, Ge, and Se Nuclei 335 – Nik N.A.M.A. Ghani, Imam Hossain, Mohammad A. Saeed, Hewa Y. Abdullah and Magdy Hussein Borel Summability for Fractional Differential Equation in the Unit Disk 339 – Rabha W. Ibrahim and Maslina Darus Obituaries .paspk.org Prof. -
Dr. Naeem Ahmad Khan, FPAS
Proceedings of the Pakistan Academy of Sciences 50 (4): 347–348 (2013) Pakistan Academy of Sciences Copyright © Pakistan Academy of Sciences ISSN: 0377 - 2969 (print), 2306 - 1448 (online) Obituary Dr. Naeem Ahmad Khan, FPAS It is with great sorrow to share that we have lost Pakistan Council of Scientific and Industrial an eminent Fellow of the Pakistan Academy of Research (PCSIR) where he made outstanding Sciences, Dr. Naeem Ahmad Khan, who left us on contributions by developing laboratories of 29th September 2013 for his eternal life in the world PCSIR and in greatly enhancing the work culture beyond us. by promoting scientists on merit. In 1989, he was Dr. Khan was born on April 12, 1928 in appointed Advisor (Technical), COMSTECH, Hoshiarpur (East Punjab). He did BA (Hons) form where he served for seven years. St. Stephen’s College, Delhi (1946); MA from Sind Dr. Khan had more than 100 scientific University (1950); MSc from Karachi University publications, 69 scientific reports and 28 general (1955); and PhD from University of Manchester articles, to his credit. He participated in 75 (1958). He worked as a post-doctoral Fellow at the conferences and seminars and presented 37 papers. Atomic Energy Research Establishment, Harwell, Besides teaching Meteorology at the PAF College, England (1961-1962), and as a Research Fellow Risalpur, Dr. Khan taught post-graduate courses at the Bartol Research Foundation of the Franklin in Physics at Karachi and Punjab Universities. Institute, Philadelphia, USA (1964-1965). Five PAEC scientists earned their PhD from the He joined Indian Meteorological Department University of Punjab under his supervision.