106 Subpart C—Track Geometry V E D . = +3 0 0007
Total Page:16
File Type:pdf, Size:1020Kb
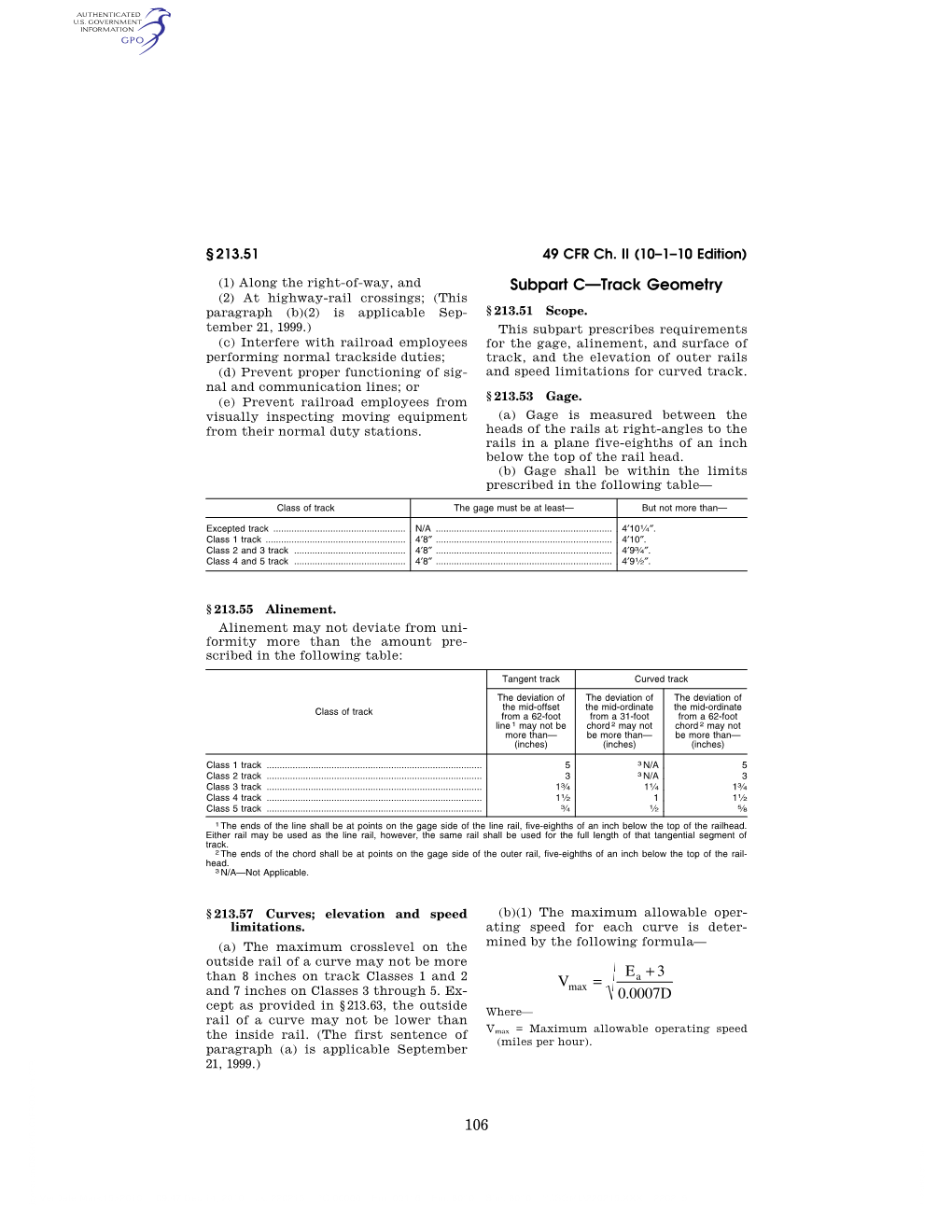
Load more
Recommended publications
-
Track Geometry
Track Geometry Track Geometry Cost effective track maintenance and operational safety requires accurate and reliable track geometry data. The Balfour Beatty Rail Digital Track Geometry System is a combined hardware and software application that derives track geometry parameters compliant with EN 13848-1:2003 and is an enhanced version of the original BR and LU systems, with a rationalised transducer layout using modern sensor technology. The system can be installed on a variety of vehicles, from dedicated test trains, service vehicles and road rail plant. Unlike some systems, our solution is designed such that voids and other vertical track defects are identified through the wheel/rail interface when the track is fully loaded. The compromise of taking measurements away from the wheel could produce under-measurement of voided track with an error that increases the further the measurement point is away from the influences of the wheel. The system uses bogie mounted non-contacting inertial sensors complemented by an optional image based sub-system, to measure rail vertical and lateral displacement. The system is designed to operate over a speed range of approx. 5 to 160 mph (8-250km/h). However, safety critical parameters such as gauge and twist will function at zero. Geometry parameters are calculated in real time and during operation real time exception and statistical reports are generated. Principal measurements consist of: • Twist • Dynamic Cross-level • Cant and Cant deficiency • Vertical Profile • Alignment • Curvature • Gauge • Dipped Joints • Cyclic Top Vehicle Ride Measurement As an accredited testing organisation we are well versed in capturing and processing acceleration measurements to national/international standards in order to obtain Ride Quality information in accordance with, for example ENV 12299 “Railway applications – Ride comfort for passengers – Measurement and Evaluation”. -
Coverrailway Curves Book.Cdr
RAILWAY CURVES March 2010 (Corrected & Reprinted : November 2018) INDIAN RAILWAYS INSTITUTE OF CIVIL ENGINEERING PUNE - 411 001 i ii Foreword to the corrected and updated version The book on Railway Curves was originally published in March 2010 by Shri V B Sood, the then professor, IRICEN and reprinted in September 2013. The book has been again now corrected and updated as per latest correction slips on various provisions of IRPWM and IRTMM by Shri V B Sood, Chief General Manager (Civil) IRSDC, Delhi, Shri R K Bajpai, Sr Professor, Track-2, and Shri Anil Choudhary, Sr Professor, Track, IRICEN. I hope that the book will be found useful by the field engineers involved in laying and maintenance of curves. Pune Ajay Goyal November 2018 Director IRICEN, Pune iii PREFACE In an attempt to reach out to all the railway engineers including supervisors, IRICEN has been endeavouring to bring out technical books and monograms. This book “Railway Curves” is an attempt in that direction. The earlier two books on this subject, viz. “Speed on Curves” and “Improving Running on Curves” were very well received and several editions of the same have been published. The “Railway Curves” compiles updated material of the above two publications and additional new topics on Setting out of Curves, Computer Program for Realignment of Curves, Curves with Obligatory Points and Turnouts on Curves, with several solved examples to make the book much more useful to the field and design engineer. It is hoped that all the P.way men will find this book a useful source of design, laying out, maintenance, upgradation of the railway curves and tackling various problems of general and specific nature. -
Investigation of Glued Insulated Rail Joints with Special Fiber-Glass Reinforced Synthetic Fishplates Using in Continuously Welded Tracks
CORE Metadata, citation and similar papers at core.ac.uk Provided by Repository of the Academy's Library POLLACK PERIODICA An International Journal for Engineering and Information Sciences DOI: 10.1556/606.2018.13.2.8 Vol. 13, No. 2, pp. 77–86 (2018) www.akademiai.com INVESTIGATION OF GLUED INSULATED RAIL JOINTS WITH SPECIAL FIBER-GLASS REINFORCED SYNTHETIC FISHPLATES USING IN CONTINUOUSLY WELDED TRACKS 1 Attila NÉMETH, 2 Szabolcs FISCHER 1,2 Department of Transport Infrastructure, Széchenyi István University Győr, Egyetem tér 1 H-9026 Győr, Hungary, email: [email protected], [email protected] Received 29 December 2017; accepted 9 March 2018 Abstract: In this paper the authors partially summarize the results of a research on glued insulated rail joints with fiber-glass reinforced plastic fishplates (brand: Apatech) related to own executed laboratory tests. The goal of the research is to investigate the application of this new type of glued insulated rail joint where the fishplates are manufactured at high pressure, regulated temperature, glass-fiber reinforced polymer composite plastic material. The usage of this kind of glued insulated rail joints is able to eliminate the electric fishplate circuit and early fatigue deflection and it can ensure the isolation of rails’ ends from each other by aspect of electric conductivity. Keywords: Glued insulated rail joint, Fiber-glass reinforced fishplate, Polymer composite plastic material, Laboratory test 1. Introduction The role of the rail connections (rail joints) is to ensure the continuity of rails without vertical and horizontal ‘step’, as well as directional break. The opportunities to connect rails are the fishplate joints, welding, and dilatation structure (rail expansion device) [1]. -
Track, Wheel and Engineering Data and Drawings
DEERFIELD AND ROUNDABOUT RAILWAY LAKE FOREST LIVE STEAMERS RAILWAY MUSEUM INCORPORATED Track, Wheel and Engineering Data and Drawings Produced and Edited by Jeffrey G. Hook NOTICE: Any and all information, data, images or drawings published as part of this document have been prepared solely for the non-commercial amateur engineering use of designers, builders, maintainers or operators of one-eighth scale model railway track, locomotives or rolling stock. It has been compiled from information sources believed by Lake Forest Live Steamers Railway Museum Incorporated and any author credited to be competent. However, recognizing that each component of any system must be designed and installed to meet the particular circumstances, Lake Forest Live Steamers Railway Museum Incorporated and any author credited assumes no responsibility or liability of any kind in connection with the information, data, images or drawings published as part of this web site that are used in any way by any person or organization and makes no representations or warranties of any kind hereby. Definitions of Terms Relating to Track Work. Document DRTRK1 Current Revision 02-21-2013 Standard Dimensions, Tolerances and Data for Railway Wheels, Wheel Mounting, Unguarded Track Gage and Track Gage and Flangeways at Frogs and Crossings. Drawings DRTRK3-A Current Revision 04-16-2019 Drawing DRTRK3-B Current Revision 06-04-2021 DRTRK3 Table No. 1: Track and Wheel Set Standard Dimensions, Maximum Limits, Minimum Limits and Minimum Clearance Allowed Between Associated Track and Wheel Set Limits. Current Revision 04-04-2019 Drawing DRTRK3 Figure D: Plan view of guarded track at typical crossing. Current Revision 09-01-2004 Drawing DRTRK3 Figure E: Plan view of guarded track at typical turnout frog. -
Chapter 2 Track
CALTRAIN DESIGN CRITERIA CHAPTER 2 - TRACK CHAPTER 2 TRACK A. GENERAL This Chapter includes criteria and standards for the planning, design, construction, and maintenance as well as materials of Caltrain trackwork. The term track or trackwork includes special trackwork and its interface with other components of the rail system. The trackwork is generally defined as from the subgrade (or roadbed or trackbed) to the top of rail, and is commonly referred to in this document as track structure. This Chapter is organized in several main sections, namely track structure and their materials including civil engineering, track geometry design, and special trackwork. Performance charts of Caltrain rolling stock are also included at the end of this Chapter. The primary considerations of track design are safety, economy, ease of maintenance, ride comfort, and constructability. Factors that affect the track system such as safety, ride comfort, design speed, noise and vibration, and other factors, such as constructability, maintainability, reliability and track component standardization which have major impacts to capital and maintenance costs, must be recognized and implemented in the early phase of planning and design. It shall be the objective and responsibility of the designer to design a functional track system that meets Caltrain’s current and future needs with a high degree of reliability, minimal maintenance requirements, and construction of which with minimal impact to normal revenue operations. Because of the complexity of the track system and its close integration with signaling system, it is essential that the design and construction of trackwork, signal, and other corridor wide improvements be integrated and analyzed as a system approach so that the interaction of these elements are identified and accommodated. -
Track Report 2006-03.Qxd
DIRECT FIXATION ASSEMBLIES The Journal of Pandrol Rail Fastenings 2006/2007 1 DIRECT FIXATION ASSEMBLIES DIRECT FIXATION ASSEMBLIES PANDROL VANGUARD Baseplate Installed on Guangzhou Metro ..........................................pages 3, 4, 5, 6, 7 PANDROL VANGUARD Baseplate By L. Liu, Director, Track Construction, Guangzhou Metro, Guangzhou, P.R. of China Installed on Guangzhou Metro Extension of the Docklands Light Railway to London City Airport (CARE project) ..............pages 8, 9, 10 PANDROL DOUBLE FASTCLIP installation on the Arad Bridge ................................................pages 11, 12 By L. Liu, Director, Track Construction, Guangzhou Metro, Guangzhou, P.R. of China PANDROL VIPA SP installation on Nidelv Bridge in Trondheim, Norway ..............................pages 13,14,15 by Stein Lundgreen, Senior Engineer, Jernbanverket Head Office The city of Guangzhou is the third largest track form has to be used to control railway VANGUARD vibration control rail fastening The Port Authority Transit Corporation (PATCO) goes High Tech with Rail Fastener............pages 16, 17, 18 in China, has more than 10 million vibration transmission in environmentally baseplates on Line 1 of the Guangzhou Metro by Edward Montgomery, Senior Engineer, Delaware River Port Authority / PACTO inhabitants and is situated in the south of sensitive areas. Pandrol VANGUARD system has system (Figure 1) in China was carried out in the country near Hong Kong. Construction been selected for these requirements on Line 3 January 2005. The baseplates were installed in of a subway network was approved in and Line 4 which are under construction. place of the existing fastenings in a tunnel on PANDROL FASTCLIP 1989 and construction started in 1993. Five the southbound track between Changshoulu years later, the city, in the south of one of PANDROL VANGUARD TRIAL ON and Huangsha stations. -
Military Railways
PROFESSIONAL PAPERS, No. 32 CORPS OF ENGINEERS, U. S. ARMY MILITARY RAILWAYS BY MAJ. W. D. CONNOR CORPS OF ENGINEERS V REVISED EDITION :916 Reviewed and Approved by the Board on Engineer Troops WASHINGTON GOVERNMENT PRINTING OFFICE 1916 WAR DEPARTMENT Document No 539 Office 0/the Chief of Engineers WAR DEPARTMENT, OFFICE 05' THE CHIEF OP STAFF, Washington, May 5, 1915. The following Manual of Military Railways, prepared by Maj. William D. Connor, Corps of Engineers, is approved and published for the information and government of the Regular Army and the Organized Militia of the United States.It is intended to supplement Part IV, Military Railways, of the Engineer Field Manual (Pro- fessional Papers No. 29, Corps of Engineers). By order of the Secretary of War: TASKER H. BLISS, Major General, Acting Chief of Sf aff. 3 . MILITARY RAILROADS. COMBAT RAILWAYS. 1. The subject of military railroads as here treated willinclude the location, construction, operation, and maintenance of railroads in the theaterof war under military auspices and for military purposes; that is, with apersonnel consisting of officers, enlisted men, and civilian employees, and for the main purposeof facilitat- ing the movements and supply of the Army. The difference between war and peace conditions will cause awide departure of military from civil railroad practice.Some of the conditions of military railroad earvice are: (a) Quick results for a short period are of the first consideration. (t) The mechanical possibilities of the property can not befully developed by reason of an untrained personnel. Speed requirements are moderate and practically uniform for alltraffic. -
Track Report 2009 V1:G 08063 PANDROLTEXT
The Journal of Pandrol Rail Fastenings 2009 DIRECT FIXATION ASSEMBLIES Pandrol and the Railways in China................................................................................................page 03 by Zhenping ZHAO, Dean WHITMORE, Zhenhua WU, RailTech-Pandrol China;, Junxun WANG, Chief Engineer, China Railway Construction Co. No. 22, P. R. of China Korean Metro Shinbundang Project ..............................................................................................page 08 Port River Expressway Rail Bridge, Adelaide, Australia...............................................................page 11 PANDROL FASTCLIP Pandrol, Vortok and Rosenqvist Increasing Productivity During Tracklaying...................................................................................page 14 PANDROL FASTCLIP on the Gaziantep Light Rail System, Turkey ...............................................page 18 The Arad Tram Modernisation, Romania .....................................................................................page 20 PROJECTS Managing the Rail Thermal Stress Levels on MRS Tracks - Brazil ...............................................page 23 by Célia Rodrigues, Railroad Specialist, MRS Logistics, Juiz de Fora, MG-Brazil Cristiano Mendonça, Railroad Specialist, MRS Logistics, Juiz de Fora, MG-Brazil Cristiano Jorge, Railroad Specialist, MRS Logistics, Juiz de Fora, MG-Brazil Alexandre Bicalho, Track Maintenance Manager, MRS Logistics, Juiz de Fora, MG-Brazil Walter Vidon Jr., Railroad Consultant, Ch Vidon, Juiz de Fora, MG-Brazil -
Network Rail Infrastructure Limited – Annual Return 2011 3 MB
Network Rail Annual Return 2011 “More trains would take the pressure off at busy times. They nearly all seem to be crowded.” The railways have never been more popular. The result is that we need more capacity. More trains. Longer trains. We spent £1.7bn in the year on capacity enhancements and plan to invest £12bn over the five years to 2014 *Passenger comment, December 2010 Helping Britain run better Contents 1 Executive Summary 8 Introduction 11 Section 1 – Operational performance and stakeholder relationships 25 Section 2 – Network capability and network availability 37 Section 3 – Asset management 75 Section 4 – Activity volumes 89 Section 5 – Safety and environment 98 Section 6 – Enhancement Programme “Projects designed to increase capacity and improve services range from the new Airdrie-Bathgate rail link in Scotland to Thameslink across London, from platform lengthening on the East Coast to the redevelopment of Reading and entirely new stations such as Newport.” Contents Executive Summary 1 Track failures 50 Overall performance in 2010/11 1 Condition of asset temporary speed restriction sites (M4) 51 Operational performance and stakeholder relationships 2 Track geometry faults (M5) 54 Network capability and network availability 3 Earthwork failures (M6) 57 Asset management 4 Earthwork condition (M33) 58 Safety and environment 5 Tunnel condition 59 Expenditure and efficiency 6 Bridge condition (M8) 61 Enhancements schemes 7 Signalling failures (M9) 64 Signalling asset condition (M10) 64 Introduction 8 Alternating current traction -
Rail Transit Track Inspection and Maintenance
APTA STANDARDS DEVEL OPMENT PROGRAM APTA RT-FS-S-002-02, Rev. 1 STANDARD First Published: Sept. 22, 2002 American Public Transportation Association First Revision: April 7, 2017 1300 I Street, NW, Suite 1200 East, Washington, DC 20006 Rail Transit Fixed Structures Inspection and Maintenance Working Group Rail Transit Track Inspection and Maintenance Abstract: This standard provides minimum requirements for inspecting and maintaining rail transit system tracks. Keywords: fixed structures, inspection, maintenance, qualifications, rail transit system, structures, track, training Summary: This document establishes a standard for the periodic inspection and maintenance of fixed structure rail transit tracks. This includes periodic visual, electrical and mechanical inspections of components that affect safe and reliable operation. This standard also identifies the necessary qualifications for rail transit system employees or contractors who perform periodic inspection and maintenance tasks. Scope and purpose: This standard applies to transit systems and operating entities that own or operate rail transit systems. The purpose of this standard is to verify that tracks are operating safely and as designed through periodic inspection and maintenance, thereby increasing reliability and reducing the risk of hazards and failures. This document represents a common viewpoint of those parties concerned with its provisions, namely operating/ planning agencies, manufacturers, consultants, engineers and general interest groups. The application of any standards, recommended practices or guidelines contained herein is voluntary. In some cases, federal and/or state regulations govern portions of a transit system’s operations. In those cases, the government regulations take precedence over this standard. The North American Transit Service Association (NATSA) and its parent organization APTA recognize that for certain applications, the standards or practices, as implemented by individual agencies, may be either more or less restrictive than those given in this document. -
Mechanical Track Deterioration Due Tolateral Geometry Irregularities
THESIS FOR THE DEGREE OF LICENTIATE OF ENGINEERING IN SOLID AND STRUCTURAL MECHANICS Mechanical track deterioration due to lateral geometry irregularities KALLE KARTTUNEN Department of Applied Mechanics CHALMERS UNIVERSITY OF TECHNOLOGY G¨oteborg, Sweden 2012 Mechanical track deterioration due to lateral geometry irregularities KALLE KARTTUNEN c KALLE KARTTUNEN, 2012 Thesis for the degree of Licentiate of Engineering 2013:02 ISSN 1652-8565 Department of Applied Mechanics Chalmers University of Technology SE-412 96 G¨oteborg Sweden Telephone: +46 (0)31-772 1000 Cover: Predicted response of the outer wheel on the leading axle of a freight wagon with Y25- bogies negotiating a 438 metre radius curve. The solid line indicates predicted RCF damage (scale on the left axis) and the dotted line lateral position of wheel/rail contact point (scale on the right axis). Grey areas indicate predicted RCF (positive on the left vertical axis) or wear (negative) according to a wear number based criterion. Chalmers Reproservice G¨oteborg, Sweden 2012 Mechanical track deterioration due to lateral geometry irregularities Thesis for the degree of Licentiate of Engineering in Solid and Structural Mechanics KALLE KARTTUNEN Department of Applied Mechanics Chalmers University of Technology Abstract This thesis deals with how a degraded track geometry influences further degradation of the geometry and the formation of rolling contact fatigue (RCF) and wear of rails. The overall objective is optimisation of railway maintenance. For this, further understanding and quantification of the deterioration of track components are needed. Dynamic multibody simulations have been performed featuring different wagons, and a track with different curve radii and different levels of track geometry degradation. -
Principles of Track Geometry
1 Principles of Track Geometry Presented by: Gary Wolf Wolf Railway Consulting 2838 Washington Street Avondale Estates, Georgia 30002 404‐600‐2300 www.wolfrailway.com Insert logo here in first Master slide Individual Geometry Topics 2 • Gage • Curves and Curve Alignment • Superelevation • Crosslevel Variance and Deviation • Vertical Profile • Runoff from a Raise Insert logo here in first Master slide Gage, Alignment, Profile, and 3 Crosslevel Variations Insert logo here in first Master slide 4 Gage and Alignment Variations Insert logo here in first Master slide Crosslevel and Alignment Variations 5 Insert logo here in first Master slide Surface and Profile Deviations 6 Insert logo here in first Master slide §213.13 Measuring track not under load. 7 When unloaded track is measured to determine compliance with requirements of this part, the amount of rail movement, if any, that occurs while the track is loaded must be added to the measurements of the unloaded track. Dynamic Gage Widening of appx. 1” Insert logo here in first Master slide 8 Measuring Crosslevel Under Load Insert logo here in first Master slide For North American Freight Operations9 1. 2. Insert logo here in first Master slide 10 §213.53 Gage. (a) Gage is measured between the heads of the rails at right‐angles to the rails in a plane five‐eighths of an inch below the top of the rail head. (b) Gage shall be within the limits prescribed in the following table — Insert logo here in first Master slide 11 Gage Deviations Insert logo here in first Master slide 12 Gage Deviations Insert logo here in first Master slide 13 Gage – Distance between the rail heads measured 5/8” below top of rail ¼” dynamic movement on 56 ¾” base plate static shoulder 56 ¾” static gage ½” dynamic ¼” dynamic base movement lateral ½” dynamic plate movement movement of plate on tie 57 ½” total gage for FRA surface Compliance Insert logo here in first Master slide 14 Dynamic Gage Widening Insert logo here in first Master slide 15 Wide Gage Defect of 1.25” Insert logo here in first Master slide 16 Gage 56.5” Base Gage Rail Wt.