Wireless Power Transfer for Gas Pipe Inspection Robots
Total Page:16
File Type:pdf, Size:1020Kb
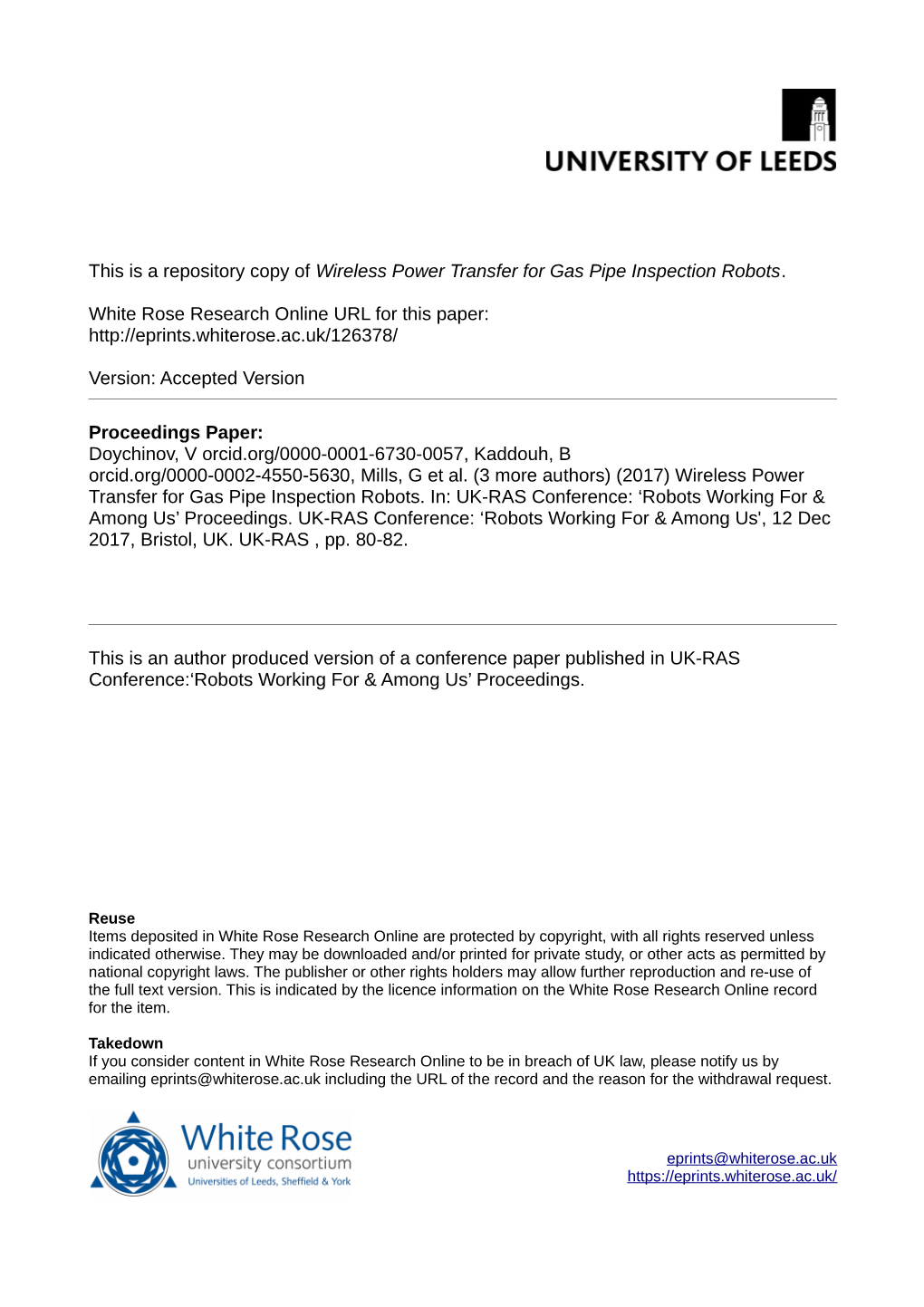
Load more
Recommended publications
-
A Brief History of Microwave Engineering
A BRIEF HISTORY OF MICROWAVE ENGINEERING S.N. SINHA PROFESSOR DEPT. OF ELECTRONICS & COMPUTER ENGINEERING IIT ROORKEE Multiple Name Symbol Multiple Name Symbol 100 hertz Hz 101 decahertz daHz 10–1 decihertz dHz 102 hectohertz hHz 10–2 centihertz cHz 103 kilohertz kHz 10–3 millihertz mHz 106 megahertz MHz 10–6 microhertz µHz 109 gigahertz GHz 10–9 nanohertz nHz 1012 terahertz THz 10–12 picohertz pHz 1015 petahertz PHz 10–15 femtohertz fHz 1018 exahertz EHz 10–18 attohertz aHz 1021 zettahertz ZHz 10–21 zeptohertz zHz 1024 yottahertz YHz 10–24 yoctohertz yHz • John Napier, born in 1550 • Developed the theory of John Napier logarithms, in order to eliminate the frustration of hand calculations of division, multiplication, squares, etc. • We use logarithms every day in microwaves when we refer to the decibel • The Neper, a unitless quantity for dealing with ratios, is named after John Napier Laurent Cassegrain • Not much is known about Laurent Cassegrain, a Catholic Priest in Chartre, France, who in 1672 reportedly submitted a manuscript on a new type of reflecting telescope that bears his name. • The Cassegrain antenna is an an adaptation of the telescope • Hans Christian Oersted, one of the leading scientists of the Hans Christian Oersted nineteenth century, played a crucial role in understanding electromagnetism • He showed that electricity and magnetism were related phenomena, a finding that laid the foundation for the theory of electromagnetism and for the research that later created such technologies as radio, television and fiber optics • The unit of magnetic field strength was named the Oersted in his honor. -
Microwave Engineering and Systems Applications
Microwave Engineering and Systems Applications Edward A. Wolff Roger Kaul WILEY A WILEY-INTERSCIENCE PUBLICATION JOHN WILEY & SONS New York • Chichester • Brisbane • Toronto • Singapore Contributors J. Douglas Adam (Chapter 10, co-author), Westinghouse Research Labo ratories, Pittsburgh, Pennsylvania David Blough (Chapter 22, co-author), Westinghouse Electric Co., Balti more, Maryland Michael C. Driver (Chapter 16), Westinghouse Research Laboratories, Pittsburgh, Pennsylvania Albert W. Friend (Chapter 5), Space and Naval Warfare Systems Com mand, Washington, D.C. Robert V. Garver (Chapters 6, 9, and 12; Chapter 10, co-author), Harry Diamond Laboratories, Adelphi, Maryland William E. Hosey (Chapter 17; Chapter 22, co-author), Westinghouse Elec tric Co., Baltimore, Maryland Roger Kaul (Chapters 2, 3, 4, 8, 11, 13, 14, 18, 19, 20, 21; Chapters 7, 15 co-author), Litton Amecom, College Park, Maryland (Presently at Harry Diamond Laboratories) David A. Leiss (Chapters 7 and 15, co-author), EEsof Inc., Manassas, Virginia Preface This book had its beginnings when Richard A. Wainwright, Cir-Q-Tel Pres ident, asked Washington area microwave engineers to create a course to interest students in microwave engineering and prepare them for positions industry was unable to fill. Five of these microwave engineers, H. Warren Cooper, Albert W. Friend, Robert V. Garver, Roger Kaul, and Edward A. Wolff, responded to the request. These engineers formed the Washington Microwave Education Committee, which designed and developed the mi crowave course. Financial support to defray course expenses was provided by Bruno Weinschel, President of Weinschel Engineering. The course was given for several years to seniors at the Capitol Institute of Technology in Laurel, Maryland. -
Microwave Photonic Signal Processing and Sensing Based on Optical Filtering
applied sciences Review Microwave Photonic Signal Processing and Sensing Based on Optical Filtering Liwei Li , Xiaoke Yi *, Shijie Song, Suen Xin Chew, Robert Minasian and Linh Nguyen School of Electrical and Information Engineering, The University of Sydney, NSW 2006, Australia; [email protected] (L.L.); [email protected] (S.S.); [email protected] (S.X.C.); [email protected] (R.M.); [email protected] (L.N.) * Correspondence: [email protected]; Tel.: +61-2-9351-2110 Received: 30 November 2018; Accepted: 27 December 2018; Published: 4 January 2019 Abstract: Microwave photonics, based on optical filtering techniques, are attractive for wideband signal processing and high-performance sensing applications, since it brings significant benefits to the fields by overcoming inherent limitations in electronic approaches and by providing immunity to electromagnetic interference. Recent developments in optical filtering based microwave photonics techniques are presented in this paper. We present single sideband modulation schemes to eliminate dispersion induced power fading in microwave optical links and to provide high-resolution spectral characterization functions, single passband microwave photonic filters to address the challenges of eliminating the spectral periodicity in microwave photonic signal processors, and review the approaches for high-performance sensing through implementing microwave photonics filters or optoelectronic oscillators to enhance measurement resolution. Keywords: Microwave photonics; photonic signal processing; photonic filtering; single sideband modulation; single passband microwave photonic filter; optical sensors 1. Introduction The low-loss and large available time-bandwidth product capability of fiber optic systems makes them attractive, not only for transmission of signals, but also for processing of high-speed signals [1–6]. -
ECE PROGRAMME ELECTIVES (PE)* OFFERED for LEVEL 5-6 of M
BIRLA INSTITUTE OF TECHNOLOGY- MESRA, RANCHI NEWCOURSE STRUCTURE M.Tech Microwave Engineering- To be effective from academic session 2018- 19 Based on CBCS & OBE model Recommended scheme of study for M.Tech. in Microwave Engineering Total Mode of delivery & credits SEMESTER / Course Credits Course Category L-Lecture; T-Tutorial;P-Practicals Session of Study Code Courses C- Credits Level of course (Recomended) L T P C (Periods/week ) (Periods/week ) (Periods/week ) Microwave & Mm-wave Integrated Circuits and EC501 3 0 0 3 Programme Core Applications (PC) EC503 Antennas and Diversity 3 0 0 3 EC505 Advanced Electromagnetic Engineering 3 0 0 3 Programme FIRST / PE-I 3 0 0 3 Monsoon FIFTH Elective (PE) Open elective OE-I 3 0 0 3 (OE) LABORATORIES Programme Core EC502 Microwave Measurement Lab 0 0 4 2 (PC) EC504 Antenna Lab. 0 0 4 2 TOTAL 19 EC550 Microwave Semiconductor Devices 3 0 0 3 Programme Core EC551 RF Circuit Design 3 0 0 3 (PC) EC553 Numerical Techniques in Electromagnetics 3 0 0 3 Programme PE-II 3 0 0 3 SECOND / Elective (PE) FIFTH Spring Open elective OE-II 3 0 0 3 (OE) LABORATORIES Programme Core EC552 Microwave Integrated Circuit Lab 0 0 4 2 (PC) EC554 Computational Electromagnetics Lab 0 0 4 2 TOTAL 19 TOTAL FOR FIFTH LEVEL 38 Programme Core EC600Thesis (Part I) 8 (PC) EC602 Microwave Imaging 3 0 0 3 THIRD / SIXTH Programme PE-III 3 0 0 3 Monsoon Elective (PE) Massive Open MOOC 2 Online Course TOTAL 16 Programme Core SIXTH EC650Thesis (Part II) 0 0 16 16 FOURTH / (PC) Spring TOTAL 16 TOTAL FOR SIXTH LEVEL 32 GRAND TOTAL FOR -
COURSES DESCRIPTION SEM CR EE 414 Microwave Engineering F 4
APPROVED TECHNICAL ELECTIVES FOR ELECTRICAL ENGINEERS You are required to complete eighteen (18 or 19) semester credit hours of Technical Electives. You need 19 credits if your CORE Electives total 6 credits ● Twelve (12 or 13) credits of electives must be from the lists of EE/CprE electives below, including one approved sequence. ● The remaining six (6) credits required can be chosen from the lists of EE/CprE or Non-EE/CprE technical electives. Courses not on these lists may be counted as technical electives only if approved by the ECpE Curriculum Committee. A written request must be submitted IMPORTANT NOTATIONS (Please Read): 1. @ EE 422 and EE 423 must be take at the same time. 2. * Course is cross-listed (same course). Can only apply one towards graduation EE, CprE, SE, ComS, BME, etc. 3. ✔ Will need to check "Schedule of Classes" at http://classes.iastate.edu/ for class availability. 4. Math 489 & ME 484 are not allowed as EE or Non-EE Technical Electives - They can be used as a general education course. 5. ENGR/EE/CprE 467, EE 442 & EE 448 cannot be used to fulfill any elective requirements. 6. EE 351 and EE 388 may be used to fulfill International Perspective requirements - You must choose if you want the course applied to either a general education OR technical elective requirement but not both 7. Only one course of the following sets of courses may be applied as a technical elective: either MatE273 or MatE392; either ComS207 or ComS227; either ComS208 or ComS 228. 8. ComS 227 may be used either to fulfill the EE 285 course requirement OR applied to technical elective credit, but not both. -
Rf and Microwave Engineering Elective Course with a Co-Requisite in the Electromagnetics Course
AC 2007-2549: RF AND MICROWAVE ENGINEERING ELECTIVE COURSE WITH A CO-REQUISITE IN THE ELECTROMAGNETICS COURSE Ernest Kim, University of San Diego Page 12.1248.1 Page © American Society for Engineering Education, 2007 RF and Microwave Engineering Elective Course with a Co-Requisite in the Electromagnetics Course Abstract The requirement of a completed engineering electromagnetics course in order to register for an undergraduate RF and microwave engineering course has been eliminated for the last two years in our Electrical Engineering Program at the University of _____________. Instead, the requirement to register for the RF and microwave engineering elective has been change to concurrent registration in engineering electromagnetics. The completion of an electromagnetics course is, at first glance, seemingly desirable for students wishing to study RF and microwave engineering. However, it has become evident that when students are concurrently registered in both courses, there is a bridging of concepts between the two courses. Fundamental concepts are emphasized in the electromagnetics course. In the RF and microwave engineering, emphasis has been placed on design using the concepts introduced in the electromagnetics course. Extensive use of electronic design tools and laboratory experiences in the RF and microwave engineering course creates a synergistic relationship between the two courses and allows solidification of concepts introduced in each course. Curricular design of both courses as well as assessments of concurrent registration in the courses is presented. Specific laboratory design, fabrication, and measurement experiments conducted in the RF and microwave engineering course that helps emphasize concepts introduced in the engineering electromagnetics course are outlined. Introduction Radio frequency (RF) and microwave engineering courses are commonly taught as an electrical engineering elective in the senior or graduate years of study. -
Microwave Engineering Lecture Notes B.Tech (Iv Year – I Sem)
MICROWAVE ENGINEERING LECTURE NOTES B.TECH (IV YEAR – I SEM) (2018-19) Prepared by: M SREEDHAR REDDY, Asst.Prof. ECE RENJU PANICKER, Asst.Prof. ECE Department of Electronics and Communication Engineering MALLA REDDY COLLEGE OF ENGINEERING & TECHNOLOGY (Autonomous Institution – UGC, Govt. of India) Recognized under 2(f) and 12 (B) of UGC ACT 1956 (Affiliated to JNTUH, Hyderabad, Approved by AICTE - Accredited by NBA & NAAC – ‘A’ Grade - ISO 9001:2015 Certified) Maisammaguda, Dhulapally (Post Via. Kompally), Secunderabad – 500100, Telangana State, India MALLA REDDY COLLEGE OF ENGINEERING & TECHNOLOGY IV Year B. Tech ECE – I Sem L T/P/D C 5 -/-/- 4 (R15A0421) MICROWAVE ENGINEERING OBJECTIVES 1. To analyze micro-wave circuits incorporating hollow, dielectric and planar waveguides, transmission lines, filters and other passive components, active devices. 2. To Use S-parameter terminology to describe circuits. 3. To explain how microwave devices and circuits are characterized in terms of their “S” Parameters. 4. To give students an understanding of microwave transmission lines. 5. To Use microwave components such as isolators, Couplers, Circulators, Tees, Gyrators etc.. 6. To give students an understanding of basic microwave devices (both amplifiers and oscillators). 7. To expose the students to the basic methods of microwave measurements. UNIT I: Waveguides & Resonators: Introduction, Microwave spectrum and bands, applications of Microwaves, Rectangular Waveguides-Solution of Wave Equation in Rectangular Coordinates, TE/TM mode analysis, Expressions -
A Brief Introduction to Microwave Engineering and to EE 433 the Microwave Region Is Typically Defined As Those Frequencies Between 300 Mhz and 300 Ghz
EE433-08 Planer Microwave Circuit Design Notes A Brief Introduction To Microwave Engineering and To EE 433 The microwave region is typically defined as those frequencies between 300 MHz and 300 GHz. (Recall 1 MHz = 1x106 Hz and 1 GHz = 1x109 Hz.) These frequencies include free-space wavelengths between 1 m and 1 mm. Here’s a look at a few important regions in the electromagnetic spectrum… Region Frequency range Wavelength range Microwave 300 MHz – 300 GHz 1 m – 1 mm Millimeter-Wave 30 GHz – 300 GHz 1 cm – 1 mm Infrared 1000 GHz – 10000 GHz 0.3 mm – 30 μm Visible light 430000 GHz – 750000 GHz 700 nm – 400 nm Note: 1000 GHz = 1 THz = 1x1012 Hz Why are microwave frequencies of interest? Perhaps the best way of answering this is to consider a primary application of microwaves -- wireless communication The first application of microwaves that often comes to mind is wireless transmission of information. As we go higher in frequency, fractional bandwidth increases. For example, let’s assume that we wish to transmit a number of 4 kHz wide voice signals through a wireless link. Further let’s assume that we have two wireless systems to chose from, one operating at 500 MHz and the second at 4 GHz, each with a 10 % bandwidth around its center frequency. In theory, the 500 MHz system could carry: Operating frequency x percent BW 0.5 GHz x 0.1 Number of channels = = = 12,500 BW per channel 4 kHz In theory, the 4 GHz system could carry: 4GHzx0.1 Number of channels = = 100,000 4kHz From the above, we see that as the system’s operating frequency increases, ideally its capacity increases. -
Microwave Engineering Programme Course 6 Credits Mikrovågsteknik TNE071 Valid From: 2018 Spring Semester
1(9) Microwave Engineering Programme course 6 credits Mikrovågsteknik TNE071 Valid from: 2018 Spring semester Determined by Board of Studies for Electrical Engineering, Physics and Mathematics Date determined LINKÖPING UNIVERSITY FACULTY OF SCIENCE AND ENGINEERING LINKÖPING UNIVERSITY MICROWAVE ENGINEERING FACULTY OF SCIENCE AND ENGINEERING 2(9) Main field of study Electrical Engineering Course level Second cycle Advancement level A1X Course offered for Communication Systems, Master's Programme Electronics Engineering, Master's Programme Electronics Design Engineering, M Sc in Engineering Applied Physics and Electrical Engineering - International, M Sc in Engineering Applied Physics and Electrical Engineering, M Sc in Engineering Entry requirements Note: Admission requirements for non-programme students usually also include admission requirements for the programme and threshold requirements for progression within the programme, or corresponding. Prerequisites Electromagnetism, RF Electronics, RF System Design Intended learning outcomes The aim of the course is to provide a through coverage of fundamental principles of microwave engineering with focus on wireless communication system and high-speed data transmission. Besides enhancing general radio frequency circuit theory covered in previous courses, it introduces the fundamental of microwave circuit analysis and design, from electromagnetic theory to radar systems. Starting with a concise presentation of the electromagnetic theory, the course leads to passive and active microwave circuit -
RF Measurement Concepts
Published by CERN in the Proceedings of the CAS-CERN Accelerator School: Advanced Accelerator Physics, Trondheim, Norway, 19–29 August 2013, edited by W. Herr, CERN-2014-009 (CERN, Geneva, 2014) RF Measurement Concepts F. Caspers1 and P. Kowina2 1CERN, Geneva, Switzerland 2GSI, Darmstadt, Germany Abstract For the characterization of components, systems and signals in the radiofre- quency (RF) and microwave ranges, several dedicated instruments are in use. In this article the fundamentals of the RF signal techniques are discussed. The key element in these front ends is the Schottky diode which can be used either as a RF mixer or as a single sampler. The spectrum analyser has become an absolutely indispensable tool for RF signal analysis. Here the front end is the RF mixer as the RF section of modern spectrum analyses has a rather complex architecture. The reasons for this complexity and certain working principles as well as limitations are discussed. In addition, an overview of the develop- ment of scalar and vector signal analysers is given. For the determination of the noise temperature of a one-port and the noise figure of a two-port, basic concepts and relations are shown as well as a brief discussion of commonly used noise-measurement techniques. In a further part of this article the oper- ating principles of network analysers are shown. A distinction can be made between scalar and vector network analysers and their methods of measuring the transmission or reflection coefficients are explained. As digital signal pro- cessing has become cheap and easily available over the last 30 years, these instruments have become extremely versatile and powerful. -
2020 ELECTRICAL ENGINEERING: RF and Microwaves Track DEGREE
2020 ELECTRICAL ENGINEERING: RF and Microwaves Track DEGREE REQUIREMENT CHECKSHEET COLLEGE OF ENGINEERING & COMPUTER SCIENCE UNIVERSITY OF CENTRAL FLORIDA GENERAL EDUCATION PROGRAM LOWER AND JUNIOR LEVEL REQUIRED COURSES SH Grd Trans Equiv * Indicates "C-" minimum required by the Gordon Rule EGS 1006C Introduction to the Engineering Profession 1 # ** Indicates minimum "C" or better grade EGN 1007C Engineering Concepts and Methods 1 # COMMUNICATION (9 SEM HRS) SH Grd Trans Equiv STA 3032 Probability & Statistics for Engineers GEP ENC 1101 3 * PHY 3101 General Physics Using Calculus III 3 ENC 1102 3 * EEL 3926L Junior Design 1 EGN 3211 Engineering Analysis & Computation 3 ** SPC 1603C 3 EEL 3004C Linear Circuits I 3 ** CULTURAL & HISTORICAL (9 SEM HRS) EEL 3123C Linear Circuits II 3 ** Select 2: AMH 2010, EUH 2000, EUH 2001, HUM EEE 3307C Electronics I 4 2211, HUM 2230, WOH 2012, WOH 2022 6 * EEE 3342C Digital Systems 3 ** Approved Cultural Foundations course: 3 EEL 3801C Computer Organization 4 ** SOCIAL FOUNDATION - (6 SEM HRS) EEL 3470 Electromagnetic Fields 3 ANT 2000/ PSY 2012/ SYG 2000 3 JUNIOR LEVEL ELECTIVE COURSES (CHOOSE 2) SH Grd Trans Equiv ECO 2013 or ECO 2023 3 EEE 3350 Semiconductor Devices 3 SCIENCE - 6 SH EEL 3552C Signal Analysis & Analog Communication 4 GEO 1200 or GEO 2370 (either GEO is preferred) EEL 3657 Linear Control Systems 3 or BSC 1050C or BSC 1005C or GLY 1030 3 PHY 2048C General Physics Using Calculus I 4 SENIOR LEVEL REQUIRED COURSES SH Grd Trans Equiv MATHEMATICAL - 6 SH EEE 4309C Electronics II 4 MAC 2311C -
Journal of Rf/Microwave Engineering, Photonics and Communications
FREQUENZ JOURNAL OF RF/MICROWAVE ENGINEERING, PHOTONICS AND COMMUNICATIONS EDITOR-IN-CHIEF Franko Küppers, Darmstadt Rolf Jakoby, Darmstadt Thomas Kürner, Braunschweig Wolfgang Menzel, Ulm EDITORIAL ASSISTANTS David Pouhè, Reutlingen Andreas Penirschke, Darmstadt Hermann Rohling, Hamburg Eleonore Titow, Darmstadt Lorenz-Peter Schmidt, Erlangen Reiner S. Thomä, Ilmenau EDITORIAL BOARD Martin Vossiek, Erlangen Axel Bangert, Kassel Robert Weigel, Erlangen Georg Böck, Berlin Thomas Weiland, Darmstadt Ranjan Bose, New Delhi Abdelhak Zoubir, Darmstadt Ivan B. Djordjevic, Tucson Philippe Ferrari, Grenoble EDITORIAL ADVISORY BOARD Rüdiger Follmann, Kamp-Lintfort Jürgen Detlefsen, München Ingo Gaspard, Darmstadt Günter Fuchs, IImenau Spartak Gevorgian, Göteborg Hans Hartnagel, Darmstadt Klaus Hofmann, Darmstadt Erich Kasper, Stuttgart Friedrich Jondral, Karlsruhe Hans-Peter Kuchenbecker, Hannover Kira Kastell, Frankfurt Gerhard Mönich, Berlin Anja Klein, Darmstadt Bernhard Rembold, Aachen Reinhard Knöchel, Kiel Klaus Schünemann, Hamburg Rolf Kraemer, Frankfurt (Oder) FREQUENZ was first published in 1947 with an circulation of 7000 copies, focusing on Telecommunications. Today, the major aim of Frequenz is to highlight current research activities and development efforts in RF/Microwave Engineering, Photonics and Communications throughout a wide frequency spectrum ranging from radio and microwave frequencies via THz and the infrared up to optical frequencies. All information regarding notes for contributors, subscriptions, Open access, back volumes