Shaft Sinking
Total Page:16
File Type:pdf, Size:1020Kb
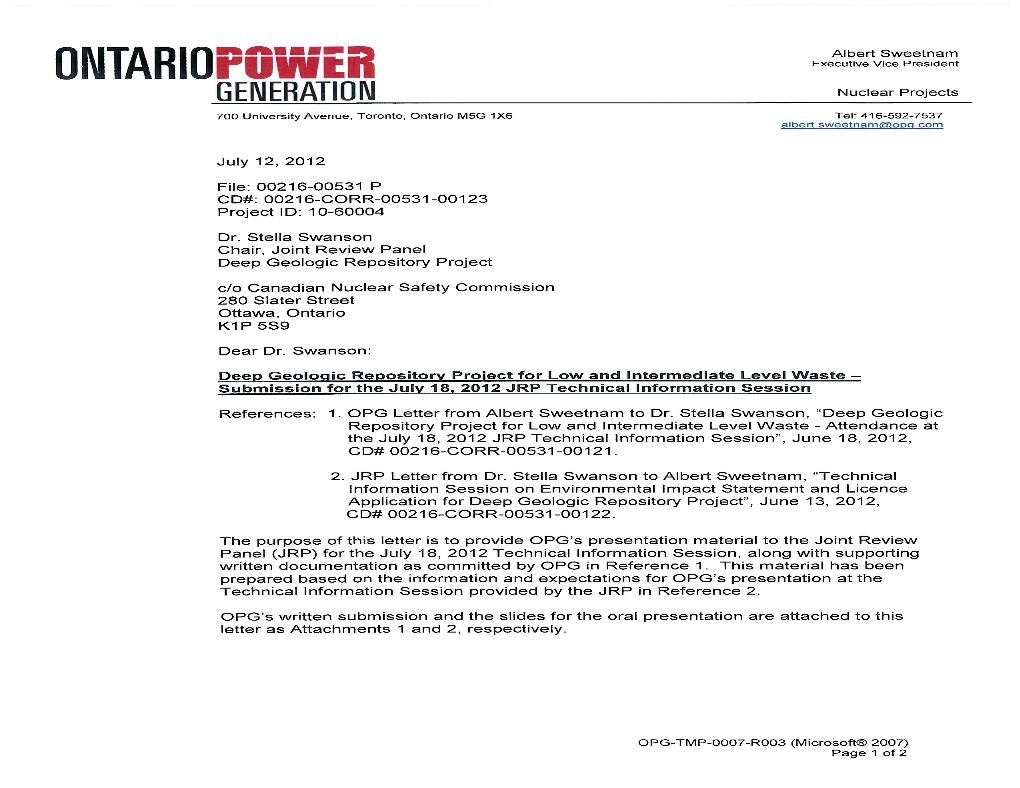
Load more
Recommended publications
-
Practical Shaft Sinking
PRA C T I C AL SH A FT SI N KI N G B Y D NAL CI O DSO M . E. FRAN S N , l C IfiEF ENGI NEER THE T . A. GI LLESPI E COM PANY SEC’OND EDITION Corrected with two new Appendices M cG R AW — H I L L B OOK C OM PA N Y 239 WEST 39TH STREET NEW YORK , T E T L ND N E 6 S R E O O C . BOUVERIE , , 1 91 2 Co ri ht 19 10 1912 b the C RAW- I L B oox COMPANY py g , , , y M G H L The Plimton Press Norwood Ma . p ss U. S. A. PREFACE TO THE FIRST ED I TI ON THE subject matter of this book was published as a Min s and Mimrals u 1909 series of articles in e , d ring and 1 s i 1 9 0. It is reproduced , with ome alterations and add n u Mr. tio s , thro gh the courtesy of Rufus J Foster, manager, M d Min r ine an als. r B . v s e and M . Eugene Wilson , editor of The writer also wishes to acknowledge his indebtedness to t Mines and Mine mls r H H . Soe M . k, who was editor of when most of the articles came out . e e 1 910. S ptemb r, PREFACE TO SECOND EDI TI ON SINCE the text of the fi rst edition of Practical Shaft ” o n u Sinking was written , cement gr ut has bee sed in several American shafts to cut off flows of water encountered in sinking , and its further use for this purpose will undoubtedly i become more common . -
Project Management, and the Design of Shaft-Sinking Projects
I Project management, and the design of shaft-sinking projects by H.W. Read* and L.G.D. Napierf Synopsis Introduction Astute corporate executives, under constant pressure of changing and challenging economic Change is endemic in our Traditionally, shaft-sinking projects have been constraints, are re-evaluating their mission society. Future change managed by conventional operational will be aa:elerated by an statements, and in many cases are becoming explosion in technology, techniques, and have often involved large cost more sharply focused in what their business communication, and and time overruns. This paper proposes that the activity should be. 'What are we actually political thought. To project-management system has a better chance required to produce?' is the question that is meet these challenges, of success. The characteristics, techniques, and being asked. Activities that are not in the main rapid structural changes application of project management are examined. stream are being pruned and, under the severe have been taking place Experience gained on numerous shaft-sinking in mining organizations strain of capital budgeting requirements, they projects has increased confidence in the efficacy both here and abroad. have started looking for better and more cost- The management qf of the project-management concept. effective ways of creating and expanding their shqft-sinking prqjects is Shaft sinking in South Africa is as old as the production facilities. a case in point. Shqft mining industry itself!. For over one hundred In addition, organizations now operate in an sinking is a seminal years, mining houses have been involved in the environment that is even more turbulent than element in the sustained sinking of shafts. -
Guidance Note QGN 30.2 Shaft Construction Metalliferous Mines
Guidance Note QGN 30.2 Shaft construction metalliferous mines – Shaft sink – Engineering and design Mining and Quarrying Safety and Health Act 1999 March 2018 Reference is made to the following legislation as applicable to a Mine or Quarry in Queensland: • Mining and Quarrying Safety and Health Act 1999 • Mining and Quarrying Safety and Health Regulation 2017 This Guidance Note has been issued by the Mines Inspectorate of the Department of Natural Resources, Mines and Energy (DNRME) to provide guidance and instruction to the SSE and those involved in the engineering design of shaft sinking and proposed winding equipment. This Guidance Note is not a Guideline as defined in the Mining and Quarrying Safety and Health Act 1999 (MQSHA) or a Recognised Standard as defined in the Coal Mining Safety and Health Act 1999 (CMSHA). In some circumstances, compliance with this Guidance Note may not be sufficient to ensure compliance with the requirements in the legislation. Guidance Notes may be up-dated from time to time. To ensure you have the latest version, check the DNRME website: https://www.business.qld.gov.au/industry/mining/safety-health/mining-safety-health/legislation- standards-guidelines or contact your local Inspector of Mines. Mineral mines & quarries - North Mineral mines & quarries - North Mineral mines & quarries - South Region - Townsville West Region – Mount Isa Region - Woolloongabba PO Box 1752 PO Box 334 PO Box 1475 MC Townsville Q 4810 Mount Isa Q 4825 Coorparoo Q 4151 P (07) 4447 9248 P (07) 4747 2158 P (07) 3330 4272 Fax (07) 4447 9280 Fax (07) 4743 7165 Fax (07) 3405 5345 [email protected] [email protected] [email protected] Coal mines - South Region - Coal mines - North Region - Mackay Rockhampton PO Box 1801 PO Box 3679 Mackay Q 4740 Red Hill Q 4701 P (07) 4999 8512 P (07) 4936 0184 Fax (07) 4999 8519 Fax (07) 4936 4805 [email protected] [email protected] This publication has been compiled by the Mines Inspectorate, Department of Natural Resources, Mines and Energy. -
Mines Regulations, 2003
1 MINES O-1.1 REG 2 The Mines Regulations, 2003 being Chapter O-1.1 Reg 2 (effective July 16, 2003). NOTE: This consolidation is not official. Amendments have been incorporated for convenience of reference and the original statutes and regulations should be consulted for all purposes of interpretation and application of the law. In order to preserve the integrity of the original statutes and regulations, errors that may have appeared are reproduced in this consolidation. 2 O-1.1 REG 2 MINES Table of Contents PART I PART VI Preliminary Matters Design of Mines 1 Title DIVISION 1 2 Interpretation General 3 Application of these regulations 37 Change and shower facilities 4 Application of OHS regulations to mines 38 Fixed ladders underground 39 Wire rope or chain ladders PART II General Notice Requirements 40 Stairways 5 Commencement of work, intended installation DIVISION 2 6 Dangerous occurrences Underground Mines 41 Application of Division PART III Plans and Records 42 Design of mine 7 Preparation of plans 43 Tailings containing cyanide prohibited 8 Marking current progress 44 Exits to surface 9 Annual submission of certified copies 45 Exits underground 10 Monthly statistics 46 Marking exits, etc. 11 Entries in log books, records 47 Emergency means of exit during power failure 12 Record retention 48 Procedure where exit from underground restricted PART IV 49 Underground electrical system Supervision of Workers 50 Boundary pillars 13 Interpretation of Part DIVISION 3 14 Qualifications of direct supervisor Open Pit Mines 15 Suspension of -
Sinking and Equipping Inclined Shafts of More Than 60 Degree Dip
Scholars' Mine Professional Degree Theses Student Theses and Dissertations 1938 Sinking and equipping inclined shafts of more than 60 degree dip Wilford Stillman Wright Follow this and additional works at: https://scholarsmine.mst.edu/professional_theses Part of the Mining Engineering Commons Department: Recommended Citation Wright, Wilford Stillman, "Sinking and equipping inclined shafts of more than 60 degree dip" (1938). Professional Degree Theses. 259. https://scholarsmine.mst.edu/professional_theses/259 This Thesis - Open Access is brought to you for free and open access by Scholars' Mine. It has been accepted for inclusion in Professional Degree Theses by an authorized administrator of Scholars' Mine. This work is protected by U. S. Copyright Law. Unauthorized use including reproduction for redistribution requires the permission of the copyright holder. For more information, please contact [email protected]. SINKING AND EQ,UIPPING INaLIlrED SHAFl'S OF MORE THAN 60 DEGREE DI P by Wilford Stillman Wright A THE SIS submi tted to the faoul ty of the SCHOOL OF MINES AND METALLURGY OF THE UNIVElRSITY OF MISSOURI in partial fulfillment of the work required for the DEGREE OF ENGI NEER OF MI NEB Rolla, Mo. 1938 - Approved by __~~~~ professor of Mining. TABLE OF OONTENTS. The I ncIined Shaft •• •• • • • • · • 1 Merlts and Demerite Locati on . • • • •• • • • 3 Size and Shape of Shaft • • • • •• • , Equipnent ••••• • • •• · • 6 The Collar. • ••••• •• • • • • • 18 Dri IIing and Blasting • • ••• • • • 20 Mucking • • • • • •• • •• •• • • • 2, Timbering • •• •••• • • •• •• 27 Shaft Station a.nd Ore pockets •• • 34 organi z8.ti on • • · .. • • •• • •• • • 3, Ooste • • ••• • •• 37 Speed • • • • •• • • • • • • •• • • 40 Liibliography • • • ••• • • • •• • • 40-A Index • • • • • • • • •• • • • ••• 41 -- - LIST OF ILLUS'fRATIONS. Fig. 1 Headframe and Ore ~in for Sinking••• lO-A Fig. -
Idaho Mining and Exploration, 2013
Idaho Mining and Exploration, 2013 Virginia S. Gillerman Earl H. Bennett Idaho Geological Survey Morrill Hall, Third Floor University of Idaho 875 Perimeter Drive MS 3014 Moscow, Idaho 83844-3014 Staff Report S-15-2 Phone 208-885-7991 August 2015 IdahoGeology.org Idaho Mining and Exploration, 2013 Virginia S. Gillerman Earl H. Bennett Staff Reports present timely information for public distribution. This report may not conform to the agency’s publication standards. Idaho Geological Survey Morrill Hall, Third Floor University of Idaho 875 Perimeter Drive MS 3014 Moscow, Idaho 83844-3014 Staff Report S-15-2 Phone 208-885-7991 August 2015 IdahoGeology.org Contents Introduction ……………………………………………………………………………… 1 Metal Mining …………………………………………………………………………… 5 Phosphate Mining ……………………………………………………………………… 9 Other Industrial Minerals ……………………………………………………………… 14 Energy ………………………………………………………………………………… 18 Exploration …………………………………………………………………………… 19 State Activities ………………………………………………………………………… 30 Illustrations Figure 1. Location of 2013 mining areas in Idaho ………………………………………… 2 Figure 2. Idaho non-fuel mineral production by year ……………………………………… 3 Figure 3. Idaho’s 2013 mineral production by commodity ………………………………… 4 Figure 4. Hecla’s Lucky Friday mine and the Silver Shaft ………………………………… 6 Figure 5. The #4 shaft sinking, Lucky Friday mine ……………………………………… 7 Figure 6. Longitudinal section of the Galena complex …………………………………… 8 Figure 7. View of Thompson Creek mine and high wall ………………………………… 9 Figure 8. Map of the Idaho Phosphate District ………………………………………… 10 Figure 9. Ultimate pit at South Rasmussen mine ………………………………………… 11 Figure 10. Overview of Monsanto’s new Blackfoot Bridge mine ……………………… 12 Figure 11. Panel F at Smoky Canyon mine with road to panel G on right ……………… 13 Figure 12. Placing backfill in panel A at North Rasmussen Ridge mine ………………… 13 Figure 13. Map of industrial mineral operations ……………………………………… 15 Figure 14. -
Precise Mine Surveying
PRECISE KLINE SURVEYING DONALD LI3UE MASSON A T}tESIS submitted to ORkON STATE COLLEGE in partial f ulfi.11nient of the requirements for the degree of MflI ENGINEIE June 1947 Appaova: Redacted for Privacy Prof 88 sor of Mining Ñ*gineering Redacted for Privacy flea of Department of Mining Engineering Redacted for Privacy Chairman of School Graduate Committee Redacted for Privacy (7 Associate Dean, Graduate Division TALZ OF CONTJNTS Page Introduction 3. General 2 Equipnnt 4 Method of Procedure 8 Surface Leve1ir 9 Underground Leveling 11 Shaft Measurennts 13 Triangulation 15 Underground Survey 20 Standardization of Tapes 26 Orientation 28 Monterrey Shaft Data 35 Galculat.i 0fl8 35 Bibliography 38 LLT or ius Table Page I Surface Levele lo .11 Unciergrond Levele, 300 Level Dolores ir* 12 III Un,erground Levels, 400 Level Dolores iii 12 1V Shaft &eaeuremonte 14 V Copariaon of Taping 24 VI Coipri*ozt of Taped Distances - arUer Trsverees 24 VU Mea'anante dth the tandrd Tape 27 VIII Doloree Shaft PlwMng 32 lx ngineering Data ¿3eee 300, 301, 302 33 X Monterrey Shaft Data Plat.e I Triangulation Net of tl* Iónt.my Shaft Survey 39 11 Prinary 'rraveraeø in the aeai dal Monte Aines 40 IiI Traveree for the Monterrey Shaft Connection 43. ?RßCISE MINE SUIWEYING INTRODUCTION The field of preoiee mine surveying ja one that i o! interest to e.0 mine surveyors. Standard text booke describe methods and practices suitable for routine mine surreying and acknowledge that refinements of these thods are desirable for precise work (1). Engineering departments of large mining companies make irnprov4a to and adaptations of existing methods to raeet local conditions and special problems. -
REPORT of INVESTIGATION Shaft Construction for Underground Mine Fatal Fall of Persons August 10, 2007
CAI-2007-12-14 UNITED STATES DEPARTMENT OF LABOR MINE SAFETY AND HEALTH ADMINISTRATION COAL MINE SAFETY AND HEALTH REPORT OF INVESTIGATION Shaft Construction for Underground Mine Fatal Fall of Persons August 10, 2007 Frontier-Kemper Constructors Inc. (A01) Evansville, Indiana at Gibson Mine Gibson County Coal, LLC Princeton, Gibson County, Indiana ID No. 12-02215 Accident Investigators Charles H. Grace, P.E. Assistant District Manager, Technical Programs, District 7, Barbourville, KY Michael G. Kalich, CMSP Senior Mining Engineer, Headquarters Safety Division J. Jarrod Durig, P.E. Civil Engineer, Technical Support, Pittsburgh, PA Michael P. Snyder, P.E. Mining Engineer, Technical Support, Triadelphia, WV Kevin L. Doan Roof Control and Ventilation Specialist, District 7 Originating Office Mine Safety and Health Administration Office of the Administrator Coal Mine Safety and Health 1100 Wilson Boulevard Arlington, VA 22209 Kevin G. Stricklin, Administrator TABLE OF CONTENTS VIEW OF SHAFT SINKING OPERATION.................................................................. ii OVERVIEW........................................................................................................................1 GENERAL INFORMATION ...........................................................................................1 DESCRIPTION OF ACCIDENT......................................................................................2 INVESTIGATION OF ACCIDENT ................................................................................4 DISCUSSION.....................................................................................................................5 -
Using an Integrated Model for Shaft Sinking Method Selection
JOURNAL OF CIVIL ENGINEERING AND MANAGEMENT ISSN 1392-3730 print/ISSN 1822-3605 online 2011 Volume 17(4): 569–580 http://dx.doi.org/10.3846/13923730.2011.628687 USING AN INTEGRATED MODEL FOR SHAFT SINKING METHOD SELECTION 1 2 3 Ali Lashgari , Mohamad Majid Fouladgar , Abdolreza4 Yazdani-Chamzini , Miroslaw J. Skibniewski 1 Tarbiat Modares University, Tehran, Iran 2, 3 Fateh Research Group, No. 5 Block. 3 Milad Complex Artesh Blvd. Aghdasieh Tehran, Iran 4 Visiting Professor, Department of Management, Bialystok University of Technology, 16-001 Kleosin, Poland 1 2 3 E-mails: [email protected]; [email protected]; [email protected]; 4 [email protected] (corresponding author) Received 21 Jun. 2011; accepted 30 Aug. 2011 Abstract. Shafts have critical importance in deep mines and underground constructions. There are several traditional and mechanized methods for shaft sinking operations. Using mechanized excavation technique is an applicable alternative to improve project performance, although impose a huge capital cost. There are a number of key parameters for this selection which often are in conflict with each other and decision maker should seek a balance between these parameters. There- fore, shaft sinking method selection is a multi criteria decision making problem. This paper intends to use the combination of analytical hierarchy process and TOPSIS (Technique for Order Performance by Similarity to Ideal Solution) methods under fuzzy environment in order to select a proper shaft sinking method. A real world application is conducted to illus- trate the utilization of the model for the shaft sinking problem in Parvadeh Coal Mine. The results show that using raise boring machine is selected as the most appropriate shaft sinking method for this mine. -
I Sub: - Underground Coal Mining Chapter – Shaft Sinking
NARAYANI INSTITUTE OF ENGINEERING & TECHNOLOGY ARAHAT, ANGUL 4th Semester, Mining Engineering Theory – I Sub: - Underground Coal Mining Chapter – Shaft Sinking Definition Shaft: A vertical or inclined opening from surface for the conveyance of men, materials, hoisting ore, pumping water and providing ventilation. Sinking: The work in excavating a shaft. SHAFT SINKING It may be described as an excavation of vertical or inclined opening from surface for conveyance of men, materials, ventilation, pumping water, in addition to hoisting ore and waste rock. It is also called Shaft Construction or Shaft Mining. AIM OF THE PROJECT To study conventional and advanced techniques of shaft sinking. To increase the production and productivity in method of working adopted to win the ore or mineral deposit by selecting appropriate and suitable available technologies for shaft sinking in Indian mines. OBJECTIVE OF PROJECT . Increasing the safety during sinking. The conditions inside the mine is needed to be improved . The safe transport of the waste/ material/men. Increasing the production, efficiency and productivity of underground mine. To improve the ventilation arrangement of a mine. For this we require the construction of a new, sufficiently dimensioned shaft. PURPOSE OF SHAFT SINKING: - Shaft sinking is used for many purposes. To transport men and materials to and from underground Workings. For hoisting ore and waste from underground. To serve as intake and return airways for the mine (ventilation shaft). To access an ore body These shafts are used in applications such as hydro electric projects, water supply, waste water shafts and tunnel projects. Drilled shaft machine is used in such process, where it consists of special type of units that are used in both stable and unstable soils. -
SHAFT SINKING COST ANALYSIS by John Edward Dowis a Thesis
Shaft sinking cost analysis Item Type text; Thesis-Reproduction (electronic) Authors Dowis, John Edward, 1940- Publisher The University of Arizona. Rights Copyright © is held by the author. Digital access to this material is made possible by the University Libraries, University of Arizona. Further transmission, reproduction or presentation (such as public display or performance) of protected items is prohibited except with permission of the author. Download date 07/10/2021 15:22:50 Link to Item http://hdl.handle.net/10150/318302 SHAFT SINKING COST ANALYSIS by John Edward Dowis A Thesis Submitted to the Faculty of the DEPARTMENT OF MINING AND GEOLOGICAL ENGINEERING In Partial Fulfillment of the Requirements For the Degree of MASTER OF SCIENCE WITH A MAJOR IN MINING ENGINEERING In the Graduate College THE UNIVERSITY OF ARIZONA 1 9 7 2 STATEMENT BY AUTHOR This thesis has been submitted in partial fulfillment of requirements for an advanced degree at The University of Arizona and is deposited in the University Library to be made available to borrowers under rules of the Library. Brief quotations from this thesis are allowable,without special permission, provided that accurate acknowledgment of source is made. Requests for permission for extended quotation from or reproduction of this manuscript in whole or in part may be granted by the head of the major department or the Dean of the Graduate College when in his judgment the proposed use of the material is in the interests of scholarship. In all other instances, however, permission must be obtained from the author. APPROVAL BY THESIS DIRECTOR This thesis has been approved on the date shown below: WILLARD C. -
Tunnels, Shaft and Development Headings Blast Design
TUNNELS, SHAFT AND DEVELOPMENT HEADINGS BLAST DESIGN INTRODUCTION Tunnels, shafts, and raises are developed for a variety of purposes. In mines development headings provide; mine access for men and materials, ore and waste hoisting, and ventilation paths. Shafts are also used in civil construction projects. In hydroelectric projects, shafts and tunnels are used to build spillways around dams, and penstocks for water feed to underground power plants. Large tunnels are also used to build underground rail and roadways. Design principles for shaft, tunnel, and raise rounds are reviewed and demonstrated in this section. Hanging Lake Tunnels on Interstate 70, Glenwood Springs, CO REVEY Associates, Inc. 2005 Page 1 Underground Blasting Technology ______________________________________________________________ DEFINING REQUIREMENTS AND CONDITIONS In an ideal situation, designers would have unlimited choices regarding explosives selection, and drilling equipment. However in most situations, blast designers do not have complete control over all of the variables affecting blast design. Round dimensions are usually pre-set, and designers must often accept the limitations that come with using existing drilling equipment drilling equipment. Despite some limitations, many other design elements can be adjusted to improve round design. Drill patterns and explosive loads can be modified, and within drilling equipment limits, hole-size can be changed. Following, is a list of typical considerations that designers should define when they develop new, or attempt improvement to existing, heading rounds. HEADING ROUND DESIGN CONSIDERATIONS 1. Heading production goals; advance rates, and schedule. 2. Ground conditions; rock strength and structure. 3. Shaft or tunnel excavation dimensions. 4. Overbreak limitations, and perimeter loading specifications. 5. Vibration and airblast limits.