Influence of Fabric Structure Parameters on Seam Slippage
Total Page:16
File Type:pdf, Size:1020Kb
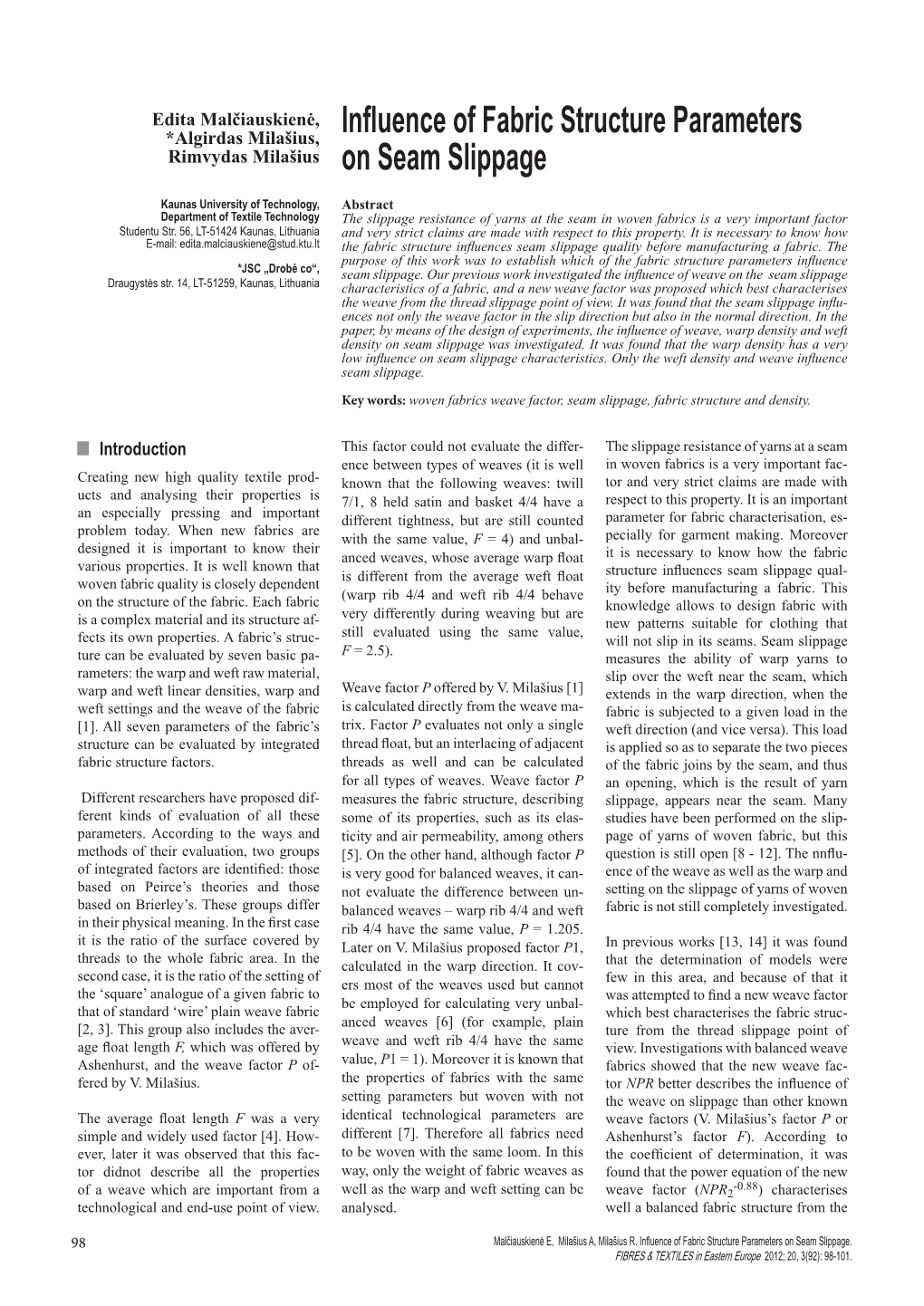
Load more
Recommended publications
-
Advanced Silk Shading
ROYAL SCHOOL OF NEEDLEWORK 2019-2020 ACADEMIC YEAR DIPLOMA ADVANCED SILK SHADING Traditionally worked with silk thread on silk or linen fabric, but now more usually worked in stranded cotton thread. Silk is still the most usual background fabric but a variety of other fabrics may be used. For Advanced Silk Shading you may work EITHER an animal, bird, fish or reptile; OR a tapestry shaded human figure. SILK SHADED ANIMAL OR BIRD AIM – To demonstrate an advanced level of technical skill by working a realistic and naturally shaded embroidery of an animal, fish, reptile or bird using Long and Short Stitch with one strand of stranded cotton (or fine silk thread). To utilise shading and stitch direction to accurately depict musculature, fur, scales and clearly defined feathers as appropriate. Please note: All preparatory work (e.g. outlines, drawings, stitch plans, original source material) MUST be handed in for assessment or the work will not be marked. DESIGN Try to come with some ideas for a design and bring along some photographs. The photograph must be printed a similar size to the embroidery size otherwise it is very difficult to work. It is essential to work from a crisp, clear, well-focused photograph where you can see the individual colours and changes from dark to light. Illustrations can sometimes be harder to follow, and you should be wary of images from the Internet, which are often poor quality and may not print sufficiently well. However there are many places online from which you can purchase high quality images. The tutor will be able to make suggestions and help you bring your ideas together. -
Altar Guild Handbook, Rev
HANDBOOK FOR ALTAR GUILDS Revised 2014 (Former versions entitled “Altar Guild Manual”) The Episcopal Diocese of Texas i The National Altar Guild Association (NAGA) The purpose of the National Altar Guild Association (NAGA) is to assist parish, diocesan, and provincial altar guilds through information, resources, and communication, including a quarterly newsletter—the EPISTLE www.nationalaltarguildassociation.org National Altar Guild Prayer Most gracious Father Who has called me Your child to serve in the preparation of Your Altar, so that it may be a suitable place for the offering of Your Body and Blood; Sanctify my life and consecrate my hands so that I may worthily handle Those Sacred Gifts which are being offered to You. As I handle holy things, grant that my whole life may be illuminated and blessed by You, in whose honor I prepare them, and grant that the people who shall be blessed by their use, May find their lives drawn closer to Him Whose Body and Blood is our hope and our strength, Jesus Christ our Lord. AMEN. Oh Padre bondadosa, que has llamado a tu hija(o) a sevir en la preparación de Tu Altar, para que sea un lugar digno para la Ofrenda de Tu Cuerpo y de Tu Sangre; Santifica mi vida y consagra mis manos para que de esta manera yo pueda encargarme dignamente de estos Dones Sagrados que te ofrecemos. Mientras sujeto estos santos objetos, concede que mi vida sea iluminada y santificada por Ti, en cuyo honor los preparo, y permite también que el pueblo bendecido por su participación, se una más a Él, Cuyo Cuerpo y Sangre son nuestra esperanza y nuestra fortaleza, Jesucristo nuestro Señor. -
How to Needlepoint
How to Needlepoint A quick guide for the on the go learner to get started stitching By Casey Sheahan What is needlepoint? Needlepoint is a type of embroidery where wool, cotton or silk is threaded through an open weave canvas. Needlepoint can be used to create many different objects, crafts or art canvases. Sources : Colorsheets, Viviva, and Shovava. “What Is Needlepoint? Learn the DIY Basics to Begin This Fun and Colorful Craft.” My Modern Met, 9 Sept. 2018, https://mymodernmet.com/what-is-needlepoint/. The Editors of Encyclopaedia Britannica. “Needlepoint.” Encyclopædia Britannica, Encyclopædia Britannica, Inc., 4 Sept. 2019, https://www.britannica.com/art/needlepoint#:~:targetText=Needlepoint as it is known,the foundation for the embroidery Needlework has been around for centuries. Throughout history we have seen a variety of different types History of of stitching. Tapestries have been found dating back to the 15th century Needlepoint and needlepoint was even found in the cave of a Pharaoh. In the 17th century when upholstered furniture became pooular. Source: “The English Needlepoint.” Ghorbany, https://ghorbany.com/inspiration/the-english-needlepoint. Getting Started Now that you know a little more about the history of needlepoint, you will start collecting your materials to begin stitching. Getting Started Material Options: Threads and Yarns Althea DeBrule outlines some of the most common types of threads used in needlepoint. Persian Yarn: By far the most popular yarn used for needlepoint. Persian wool can be be purchased in hundreds of colors from delicate hues to bold shades. Tapestry Yarn: Tapestry wool is a single strand thread that cannot be separated for fine stitching. -
De Laudibus Legum Angliae
This is a reproduction of a library book that was digitized by Google as part of an ongoing effort to preserve the information in books and make it universally accessible. https://books.google.com UNIVE NFORD UBRAR School of Law ह பல UL PREMY . JSN LFO XKD 1874 DE LAUDIBUS LEGUM ANGLIÆ A TREATISE IN COMMENDATION OF THE LAWS OF ENGLAND BY CHANCELLOR SIR JOHN FORTESCUE WITH TRANSLATION BY FRANCIS GREGOR NOTES BY ANDREW AMOS AND A LIFE OF THE AUTHOR BY THOMAS ( FORTESCUE ) LORD CLERMONT . CINCINNATI : ROBERT CLARKE & CO . 1874 Entered , according to act of Congress , in the year 1874 , By ROBERT CLARKE & CO . , In the office of the Librarian of Congress , at Washington . Stereotyped by OGDEN , CAMPBELL & Co. , Cin . , o . 93144 PUBLISHERS ' NOTICE . In carrying out our plans for the republication of some of the most noted “ Legal Classics , ” Sir John Fortescue's “ De Laudibus Legum Angliæ ” was selected as the third of our series , and the edition by Amos , published in 1825 , was fixed upon for republication . Just as we were about putting it into the printers ' hands , we fortunately heard of Lord Clermont's privately printed edition of Fortescue's Life and Works , in 2 vols . royal 4to , printed in 1869 , a detailed description of which will be found on page liv . After some correspondence we learned that the edition was a limited one - 120 copies — designed for family friends and important public libraries . On being informed of our in tended republication , and of our desire to refer to it for comparison , Lord Clermont generously sent to us a copy of this sumptuous work , for our use in the preparation of this edition , and then to be presented to the Public Library of Cincinnati . -
Sewing Fun! Feather
Sewing Fun! Feather. Blanket. Straight. Cross. Satin. Zig-zag. Chain. Running. Back. Whip. Slip. Knotting. These are not yoga poses! These are stitches that you can learn as you become a sewing master! Sewing is an essential skill that is practical and fun! Lose a button? No need to ask mom for help! You can fix it yourself! Want to create a personalized gift for someone? Sew it! Make your own bedroom accessories, stuffed animals, pencil cases, tote bags, blankets, pillows, doll clothes, design your own fashion. Dream it! Sew it! How to earn the Summer Reading patch the Girl Scout way: Steps: 1. Discover—Gather the materials you need and practice a few stitches. 2. Connect—Complete your first sewing project. 3. Take Action—Put your new skill to use! Materials Needed: In order to complete this patch, you’ll need a few things: • basic sewing supplies (See Step 1 for list or purchase an embroidery kit) • fabric: scraps or embroidery cloth • sewing resources: You can either go online with an adult, ask a professional, or visit your public library • a box or basket to use as your sewing kit • a quilting hoop • buttons STEP 1 Discover the basics of sewing. Before you start a project, it’s important to have all the tools you may need on hand. An easy way to gather everything is to create a sewing kit. Here are some items that you might want to have before you begin: • needles • thread • embroidery floss • needle threader • scissors • seam ripper • pins Optional: • measuring tools 800-248-3355 • marking tools gswpa.org • painter’s tape/colored tape (This is great for learning to sew straight lines!) Use your resources wisely to learn about hand sewing—you can find books about different kinds of stitches at your local library, or with the help of an adult, go online! There are websites and videos that can show you how to do easy, intermediate, and complicated stitches. -
What Are Fabric Scissors?
What are fabric scissors? Fabric scissors or fabric shears as they are more commonly referred to are the main tool used for cutting out your fabric. There are various different types of fabric shears on the market which range from general purpose to a traditional tailors shears. Shears should cut cleanly and smoothly so the type you choose usually depends on what material you need to cut and what you find comfortable to use. If you are buying hand crafted shears, your choice will also be influenced by the shear manufacturers skill and the quality of steel used. Heavy fabrics such as leather and denim are easier to cut using shears that have longer handles or sharper blades. Synthetic fabrics tend to slip on smooth blades so a serrated pair for better control would be the answer. Elastic or pivoted shears offer precision cutting right to the tip of the blades. Most dressmakers shears are angled (or bent) to keep the blades flat on the table reducing disruption to your lay. But very angled shears can be awkward to use if you need to stretch across a table. Lightweight shears are recommended for occasional use where as drop forged shears are for more prolonged use. The size you choose should depend largely on what you find comfortable to use. If possible try to borrow a pair to handle them and see if they suit you before buying. They mustn’t be to heavy for comfort. If you are in doubt, then go for the larger size. The maintenance of scissors and shears is very important, yet often neglected. -
Blackwork Journey
Blackwork Journey © 1 'Sublime Stitches' Aida Part 6 Patterns 75 - 85 Full Design Area: 16.07 x 29.57 inches worked on 14 count AIDA 225 x 414 stitches Material: Minimum size - 26 x 40 inches to allow for embroidery frame and mounting Suggested fabric: Zweigart 14 count Aida, white, antique white or cream The sample was worked on Zweigart 14 count Aida, white Over dyed or space dyed fabrics may detract from the design - select carefully! There are 12 pages of patterns. One page will be placed in 'Freebies' in Blackwork Journey every month. Each pattern or group of patterns have their: Individual numbers, Technique, Threads and beads used, Chart, Picture and Method. Each month join a printout of the chart to the one before. The final chart will consist of 12 pages arranged in the order as shown above. Please follow the main chart carefully to place and work the different patterns. The embroidery may differ slightly. Where patterns overlap between the pages do not start the pattern. The part patterns are there to help in the placing of the design. As additional pages are added the part patterns will be complete. Do not add beads to the design until all 12 pages have been worked. The sample was worked in DMC and Anchor floss in four shades including DMC 310 as the base colour. Cross stitch is worked in TWO strands over two threads, back stitch is worked in ONE strand over two threads. Threads used: DMC 310 Black, three skeins Anchor 1206 variegated, or DMC 815 Garnet, three skeins DMC 415 Pearl grey, one skein DMC 414 Steel grey, one skein Metallic threads used: Rainbow Gallery Petite Treasure Braid PB01, one card or DMC Lights Effects E3852 Dark Gold, one skein DMC Lights Effects E317 DMC 996 electric blue is used on the chart to show ONE strand of 415 and ONE strand 414 together to make two strands for pulled thread work stitches. -
A Live Documentary by Sam Green and Kronos Quartet
Wexner Center for the Arts School Programs Resources A Thousand Thoughts: a Live Documentary by Sam Green and Kronos Quartet “I've always wanted the string quartet to be vital, and energetic, and alive, and cool, and not afraid to kick ass and be absolutely beautiful and ugly if it has to be. But it has to be expressive of life. To tell the story with grace and humor and depth. And to tell the whole story, if possible." –David Harrington, Kronos Quartet ABOUT THE PERFORMANCE: After 45 years since their inception the ever-forward thinking Kronos Quartet embrace a moment of reflection with this special Wexner Center commissioned collaboration with filmmaker Sam Green, for which they have won an Artist Residency Award at the Wexner. A live cinema documentary about Kronos’ past, present, and future, A Thousand Thoughts--conceptualized and directed by Green--will take on an expansive exploration of form as it tells the story of Kronos’ history through live narration, archival footage, interviews with Kronos collaborators such as Philip Glass, Terry Riley, Tanya Tagaq, and Wu Man among others, and live music performed by Kronos. Sam Green’s insightful narration will highlight telling moments from Kronos’ early days in San Francisco as upstarts in the world of classical music seeking new ways to perform chamber music with a hip edge while championing music from Jimi Hendrix and Astor Piazzolla to their place today as widely acclaimed artists and trailblazers of the vibrant indie chamber scene. The meta quality of this work—a live documentary about Kronos as Kronos performs the soundtrack—allows audiences to reflect on the nature of liveness, presence, and the collective experience of art, while also deepening their understanding of Kronos’ music, story, and legacy. -
Issue36january2014v4.Pdf
1 A Bustle & Sew Publication Copyright © Bustle & Sew Limited 2013 The right of Helen Dickson to be identified as the author of this work has been asserted in accordance with the Copyright, Designs and Patents Act 1988. All rights reserved. No part of this publication may be reproduced, stored in a retrieval system or transmitted in any form, or by any means, without the prior written permission of the author, nor be otherwise circulated in any form of binding or cover other than that in which it is published and without a similar condition being imposed on the subsequent purchaser. Every effort has been made to ensure that all the information in this book is accurate. However, due to differing conditions, tools and individual skills, the publisher cannot be responsible for any injuries, losses and other damages that may result from the use of the information in this book. First published 2013 by: Bustle & Sew Coombe Leigh Chillington Kingsbridge Devon TQ7 2LE UK www.bustleandsew.com Farewell to the Old Year 2 Hello, Welcome to the first issue of 2014! This promises to be a most exciting year here for us all at Coombe Leigh as Rosie’s wedding to Dan takes place in June, so now Christmas is over our preparations are really getting underway! Inspired by this happy event, and of course looking forward to Valentine’s Day next month, there are two love heart patterns in this issue. The first is an old favourite, “Made for each other” featuring a turtle and hedgehog who find true love in each other’s arms, whilst the second is a brand new design - a lovely summery floral heart inspired by one of Shakespeare’s love sonnets. -
Extinct Embroidery: Lost Sunflower
EXTINCT EMBROIDERY: LOST SUNFLOWER WITH SolsTice HandMade SETTING UP SET UP THE HOOP 1. Loosen the outer ring of your embroidery hoop by spinning the silver knob. 2. Separate the hoops and set the smaller inside hoop on a flat surface. 3. Lay your fabric across the smaller hoop. 4. Take the larger hoop and fit it onto the fabric and smaller hoop. 5. Spin the Knob to tighten the outer hoop, stretching the fabric taunt. Smooth out any wrinkles. SPLIT YOUR THREAD 1. Measure out apx 36 in of embroidery floss. Refer to example photo, as well as stitch guide, to guide your color decision. 2. Notice that embroidery floss is made of 6 threads. Split the cut length in half, into two strands of 3 threads each. 2 THREAD THE NEEDLE 1. Take the cut end of your embroidery floss and feed it through the eye of the needle. HAVING TROUBLE? 1. Give the end of your floss a fresh trim. 2. Wet the end of the floss. 3. Pinch the end of the floss to flatten it. 4. Slip the floss through the eye of the needle. STILL STRUGGLING? 1. Apply chapstick to the end of floss and pinch between your fingers. This should help the fibers stick together and stiffen to slip through the needle. As an alternative, pull thread through beeswax. 2. Find a needle threader. 3 SETTING UP CREATE AN ANCHOR KNOT 1. Hold both cut ends of floss next to each other so the ends align between thumb and forefinger. 2. Wrap doubled floss around thumb and forefinger, then tuck the cut ends under this wrap. -
SEWING for BEGINNERS a 4‐H Clothing Publication
SEWING FOR BEGINNERS A 4‐H Clothing Publication Pin Cushion Stuffed Toy Potholder Scarf Apron Tote Bag Knapsack UNH Cooperative Extension programs and policies are consistent with pertinent Federal and State laws and regulations, and prohibits discrimination in its programs, activities and employment on the basis of race, color, national origin, gender, religion, age, disability, political beliefs, sex, sexual orientation, or veteran’s, marital or family status. New Hampshire counties cooperating. SEWING FOR BEGINNERS Introduction We should all learn to sew. Sewing is a skill for people of all ages, in all occupations, and from all walks of life. From making small repairs to making complete wardrobes, sewing provides for our basic, and not so basic, clothing needs. Sewing can also produce knapsacks and stuffed toys, practical articles and gifts. Sewing is a fun, useful craft that you can be proud of doing. This manual is an introduction to sewing. It is designed to give you information quickly and easily. The drawings and descriptions will help you understand the most important steps and ideas. First, you will learn about the basic tools, terms, and techniques of sewing. You will then develop your skills by completing a few simple projects. Never hesitate to seek help from more experienced sewers. If you have a problem with a project, ask a friend, parent or your club leader for help. Refer often to this manual and other sewing guides. Practice and have fun! TOOLS People need tools for every hobby and job. You need special tools for sewing. These tools will make sewing easier, neater, and more enjoyable. -
Aviation & Tinner's Snips HVAC Tools Scissors & Shears Utility Knives
■ Aviation & Tinner’s Snips ■ HVAC Tools ■ Scissors & Shears ■ Utility Knives Wiss® products have been earning their reputation for craftsmanship and long life since 1848. One result: Wiss has been the market leading “call-out brand” for aviation snips for over 50 years. The wide product line includes scissors, industrial shears, utility knives, siding and HVAC tools… all with famous Wiss quality built in. TABLE OF CONTENTS Wiss® Table of Contents Contents Page No. Snips introduction 247 Aviation snips 248 - 250 All-purpose cutters 250 - 251 Tinners’ snips 252 - 254 Heating, ventilating and air conditioning tools (HVAC) 255 - 258 Ratcheting Pipe Cutters 258 Vinyl siding tools 259 Utility knives 260 - 261 Snap knife 261 Replacement utility knife blades 261 Shears and scissors introduction 262 Stainless steel scissors and shears 262 - 263 Solid steel trimmers 264 Industrial shears 264 - 267 Inlaid shears and trimmers 264 Belt and leather cutting scissors 267 Double rounded scissors and shears 267 Pinking shears 268 Sewing and embroidery scissors 268 Quick-Clip® lightweight speed cutters 269 Special purpose Industrial snips and shears 270 - 271 Electrician’s scissors 272 Wiss Numerical Index 273 Key to symbol Length of Cut Wiss 246 AVIATION SNIPS Wiss® Aviation Snips The Wiss® line of aviation snips is the most complete line on the market. Wiss® aviation snips are advanced metal cutting tools originally developed for cutting extremely tough alloys used in the aircraft industry. Wiss® snips are widely used in the construction trades by general contractors, HVAC professionals, sheet metal workers, drywallers, roofers, electricians, and siding contractors. They are common tools for maintenance specialists and industrial workers, and can be found in almost any industrial application.